2019年注塑车间总结
注塑车间年度总结范文(3篇)

第1篇一、前言时光荏苒,岁月如梭。
转眼间,一年又即将过去。
在过去的一年里,注塑车间在公司领导的正确指导下,全体员工团结一心,克服种种困难,圆满完成了各项工作任务。
现将本年度工作总结如下:二、工作回顾1. 生产任务完成情况本年度,注塑车间共生产各类注塑产品XX万件,同比增长XX%;完成产值XX亿元,同比增长XX%。
在产量和产值上均创下了历史新高。
2. 产品质量情况通过加强质量管理,本年度注塑车间产品合格率达到XX%,较去年同期提高XX个百分点。
在产品性能、外观等方面得到了客户的一致好评。
3. 设备维护与保养本年度,注塑车间对设备进行了全面维护与保养,确保设备正常运行。
同时,对设备进行了技术改造,提高了生产效率和产品质量。
4. 安全生产本年度,注塑车间认真贯彻落实安全生产责任制,加强安全管理,严格执行各项安全规章制度。
全年无重大安全事故发生,员工安全意识明显增强。
5. 员工培训与素质提升本年度,注塑车间组织开展了各类培训活动,提高了员工的专业技能和综合素质。
同时,加强了团队建设,提升了团队凝聚力。
三、主要工作措施1. 优化生产流程本年度,注塑车间对生产流程进行了优化,缩短了生产周期,提高了生产效率。
同时,通过引入先进的生产设备和技术,提高了产品质量。
2. 加强质量管理注塑车间始终坚持“质量第一”的原则,严格执行质量管理体系,加强过程控制,确保产品质量稳定。
3. 严格设备管理注塑车间对设备进行了全面维护与保养,确保设备正常运行。
同时,加强设备操作人员的培训,提高设备利用率。
4. 强化安全管理注塑车间认真贯彻落实安全生产责任制,加强安全管理,严格执行各项安全规章制度。
定期开展安全检查,及时发现和消除安全隐患。
5. 提升员工素质注塑车间通过开展各类培训活动,提高员工的专业技能和综合素质。
同时,加强团队建设,提升团队凝聚力。
四、存在问题及改进措施1. 存在问题(1)生产效率仍有提升空间;(2)产品质量波动较大;(3)部分员工技能水平有待提高。
注塑车间工作总结范文(3篇)

第1篇一、前言在过去的一年里,注塑车间全体员工在公司的正确领导下,紧紧围绕年度工作目标,以“安全第一、质量至上、效率优先、创新驱动”为工作方针,扎实开展各项工作。
现将本年度工作总结如下:二、工作回顾(一)安全生产方面1. 安全教育培训:我们严格执行安全生产责任制,定期组织员工进行安全教育培训,提高员工的安全意识和操作技能。
本年度共组织安全培训20次,参与员工达200人次。
2. 安全隐患排查:车间每月开展一次全面的安全隐患排查,对发现的问题及时整改,确保车间安全生产。
本年度共排查安全隐患50余处,已全部整改完成。
3. 应急预案演练:为了提高应对突发事件的能力,我们定期开展应急预案演练,提高员工的应急处置能力。
本年度共开展应急演练4次,均取得了良好的效果。
(二)质量管理方面1. 质量控制体系:我们建立了完善的质量控制体系,从原材料采购、生产过程控制到成品检验,严格把关,确保产品质量。
2. 质量检测:本年度共进行产品质量检测1000余次,合格率达到99.8%。
3. 客户投诉处理:对客户投诉的问题,我们高度重视,及时进行调查处理,确保客户满意度。
本年度共处理客户投诉20起,客户满意度达到95%。
(三)生产效率方面1. 设备维护与保养:我们定期对生产设备进行维护和保养,确保设备运行稳定,提高生产效率。
2. 生产计划管理:通过优化生产计划,合理安排生产任务,提高生产效率。
本年度生产任务完成率达到了102%。
3. 员工技能培训:针对生产过程中出现的问题,我们组织员工进行技能培训,提高员工操作技能,从而提高生产效率。
(四)技术创新方面1. 工艺改进:通过不断优化生产工艺,降低生产成本,提高产品质量。
本年度共实施工艺改进5项,节约成本10万元。
2. 设备更新:根据生产需求,引进了3台先进的生产设备,提高了生产效率和产品质量。
3. 研发投入:本年度投入研发经费30万元,研发新产品3个,成功应用于市场。
三、工作亮点1. 安全生产零事故:通过加强安全管理,本年度实现安全生产零事故的目标。
注塑车间的工作总结5篇

注塑车间的工作总结5篇注塑车间的工作总结(篇1)一年的时间也过半了,回头看上半年,有收获,也是有自己做的还不够好的地方,但终究也是过去了,在此也是要来对自己的一个工作去反思,总结下。
参与工作的时间并不是很长,我也是始终都在学习之中,车间的工作跟着师傅,慢慢的熟悉了解,而今也是能独立的去做一些工作了,但是还是有挺多的方面需要去向师傅请教的才行,毕竟自己的阅历还是不足,一些新的问题消失,自己也是无法很好的解决,不过通过学习,我也是比之前好了许多,而我学习的进度也是得到了认可,个人来说其实也是有些焦急,期望能多学一些,自己能做得更好,不过也是清楚,工作是不断去积累才有的阅历,并非是一时半会就会有的,上半年虽然受到了疫情的影响,但是我们复工还是比较的早,公司也是做好了防控的工作,所以我们在车间其实也没有太多的影响,况且我们的工作和外部的关系没有那么的大,虽然事情少了一些,但是师傅也是每天带着我去看机器,去处理问题的同时也是慢慢的教我。
工作之中,跟随着师傅做下手,而且也是在做的过程之中对于我们要去维护的机器有了更多的了解,下班之后和师傅谈天或者自己找书籍来看,去更清楚自己要做的事情,师傅也是说了我们维护的工作是始终不停的,要去做好不简单,同时也是阅历不断地积累,要尽可能的熟悉了解机器,那么做起来就会更顺利,机器也是始终在运行,去做生产的工作,而维护也是不可避开,没有不需要维护的机器,同时我们的工作也是尽可能的让机器运行更快更好一些,不去耽搁了生产。
上半年虽然生产的任务少了一些,不过我们维护做的还是有许多事情,一些闲置的机器也是尽可能的多做保养,去让其在今后运行的时候没有问题消失才行的。
工作之中,我也是出过一些错误,一些事情做得有问题,也是让师傅操劳了,但是也是给予了我许多的鼓励,犯错的同时也是能更好的学会,去在今后不再犯错了。
下半年的生产任务也是恢复了正常,而我们的工作要连续的做下去,同时个人也是要跟着师傅乐观的去学,去让自己的阅历积累更多来做好工作。
注塑部年度总结范文(3篇)

第1篇一、前言时光荏苒,岁月如梭。
转眼间,一年又即将过去。
在这辞旧迎新之际,我部注塑部全体成员怀着激动的心情,对本年度的工作进行总结,以期为新一年的工作提供借鉴和指导。
二、年度工作回顾1. 生产与质量管理在过去的一年里,注塑部全体员工紧紧围绕公司生产计划和目标,紧密配合,攻坚克难,取得了显著的成绩。
(1)生产方面:全年累计生产各类注塑产品5182500件,同比增长10%。
其中,试模约1000副/次,削毛刺约3000000次。
生产效率得到了明显提升。
(2)质量管理:我们始终坚持“质量第一”的原则,严把质量关。
在质量奖惩制度执行后,我部高度重视产品质量,严把生产工序的每一个质量控制关。
通过例会、班前会及生产过程及时为操作工灌输质量理念,坚持操作工为第一质检员的观点。
同时,根据操作工的流动量,及时为新职工安排质量、操作技能方面基本的理论培训和现场操作实践,保证每一个新操作工在上机独立操作以前,都能了解基本的产品质量判别方法。
2. 技术创新与设备改进(1)技术创新:为了提高生产效率和产品质量,我部积极进行技术创新。
例如,引入了先进的注塑机控制系统,实现了生产过程的自动化和智能化;优化了注塑模具设计,降低了生产成本。
(2)设备改进:针对生产过程中出现的问题,我部对设备进行了多次改进。
例如,更换了部分老化设备,提高了设备运行稳定性;对关键设备进行了定期维护和保养,确保设备处于良好状态。
3. 团队建设与人才培养(1)团队建设:为了提高团队凝聚力,我部定期组织各类团队活动,如户外拓展、部门聚餐等。
通过这些活动,增强了员工之间的沟通与协作,提高了团队整体素质。
(2)人才培养:我部注重人才培养,为员工提供良好的学习和发展平台。
通过开展内部培训、外部进修等方式,提高了员工的专业技能和综合素质。
4. 安全环保与节能减排(1)安全环保:我部始终将安全环保放在首位,严格执行国家相关法律法规。
通过加强安全教育培训、完善安全管理制度、开展安全隐患排查等措施,确保了生产安全。
注塑车间工艺年度总结(3篇)
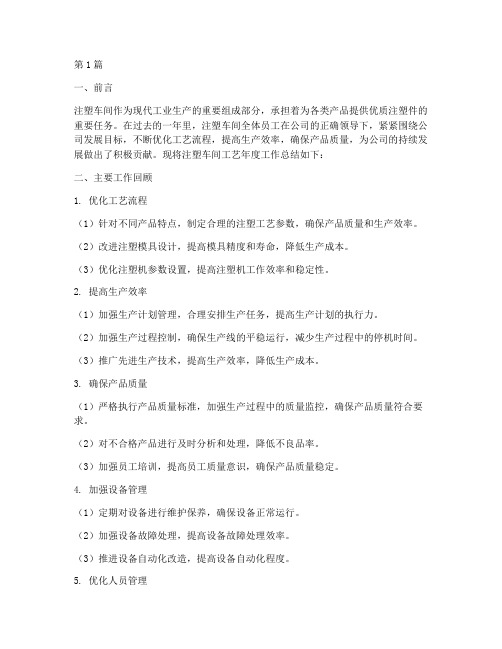
第1篇一、前言注塑车间作为现代工业生产的重要组成部分,承担着为各类产品提供优质注塑件的重要任务。
在过去的一年里,注塑车间全体员工在公司的正确领导下,紧紧围绕公司发展目标,不断优化工艺流程,提高生产效率,确保产品质量,为公司的持续发展做出了积极贡献。
现将注塑车间工艺年度工作总结如下:二、主要工作回顾1. 优化工艺流程(1)针对不同产品特点,制定合理的注塑工艺参数,确保产品质量和生产效率。
(2)改进注塑模具设计,提高模具精度和寿命,降低生产成本。
(3)优化注塑机参数设置,提高注塑机工作效率和稳定性。
2. 提高生产效率(1)加强生产计划管理,合理安排生产任务,提高生产计划的执行力。
(2)加强生产过程控制,确保生产线的平稳运行,减少生产过程中的停机时间。
(3)推广先进生产技术,提高生产效率,降低生产成本。
3. 确保产品质量(1)严格执行产品质量标准,加强生产过程中的质量监控,确保产品质量符合要求。
(2)对不合格产品进行及时分析和处理,降低不良品率。
(3)加强员工培训,提高员工质量意识,确保产品质量稳定。
4. 加强设备管理(1)定期对设备进行维护保养,确保设备正常运行。
(2)加强设备故障处理,提高设备故障处理效率。
(3)推进设备自动化改造,提高设备自动化程度。
5. 优化人员管理(1)加强员工培训,提高员工技能水平。
(2)完善绩效考核体系,激发员工工作积极性。
(3)加强团队建设,提高团队协作能力。
三、存在问题及改进措施1. 存在问题(1)部分员工对工艺流程的理解不够深入,导致生产过程中出现偏差。
(2)设备故障处理速度有待提高。
(3)生产计划执行力度不够。
2. 改进措施(1)加强员工培训,提高员工对工艺流程的理解和应用能力。
(2)优化设备故障处理流程,提高故障处理速度。
(3)加强生产计划管理,提高生产计划的执行力。
四、展望在新的一年里,注塑车间将继续秉承“质量第一、客户至上”的原则,不断优化工艺流程,提高生产效率,确保产品质量,为公司的发展贡献力量。
注塑成型车间年度总结(3篇)

第1篇一、前言在过去的一年里,注塑成型车间在公司领导的正确指导和全体员工的共同努力下,紧紧围绕公司年度目标,积极推进各项工作,取得了一定的成绩。
现将本年度工作总结如下:一、工作回顾1. 生产任务完成情况本年度,注塑成型车间共完成各类产品产量XX万件,同比增长XX%;产值XX亿元,同比增长XX%。
在完成生产任务的同时,产品质量稳定,不良品率控制在XX%以内。
2. 技术创新与改进(1)针对生产过程中存在的问题,车间组织技术攻关,对生产线进行优化改造,提高生产效率。
(2)引进先进设备,提高生产自动化水平,降低人工成本。
(3)开展技术培训,提高员工技能水平,为生产提供有力保障。
3. 节能减排与环保(1)加强能源管理,降低能源消耗,本年度能源消耗同比下降XX%。
(2)严格执行环保法规,确保生产过程中污染物达标排放。
(3)开展环保宣传教育,提高员工环保意识。
4. 安全生产(1)加强安全管理,严格执行安全操作规程,确保生产安全。
(2)开展安全教育培训,提高员工安全意识。
(3)定期进行安全检查,及时消除安全隐患。
二、存在问题1. 生产计划与实际需求存在一定差距,导致生产过程中出现断料、停机等现象。
2. 部分设备老化,维修保养不及时,影响生产效率。
3. 员工技能水平参差不齐,制约了生产水平的进一步提升。
三、下一步工作计划1. 优化生产计划,提高生产效率,确保生产任务按时完成。
2. 加大设备更新改造力度,提高生产自动化水平。
3. 加强员工培训,提高员工技能水平,打造一支高素质的员工队伍。
4. 深入开展节能减排工作,降低生产成本,提高企业竞争力。
5. 加强安全生产管理,确保生产安全。
总之,过去的一年,注塑成型车间在全体员工的共同努力下,取得了显著成绩。
在新的一年里,我们将继续努力,为实现公司年度目标,为我国注塑行业的发展贡献自己的力量。
第2篇一、工作回顾在过去的一年里,注塑成型车间在公司领导的正确指导和全体员工的共同努力下,圆满完成了公司下达的各项生产任务。
注塑车间个人工作总结

时光荏苒,转眼间我在注塑车间已经度过了几个月的时光。
这段时间里,我在工作中不断学习、成长,现将我的个人工作总结如下:一、工作回顾1. 安全生产自入职以来,我始终把安全生产放在首位,严格遵守各项安全操作规程,积极参加车间组织的安全生产培训。
在注塑生产过程中,我始终保持高度警惕,确保自身及同事的人身安全。
2. 产量提升为了提高生产效率,我积极学习并掌握注塑设备的操作技能,努力提高生产速度。
在保证产品质量的前提下,努力完成生产任务,为车间产量提升做出贡献。
3. 产品质量在注塑生产过程中,我注重细节,严格按照工艺要求进行操作。
对于出现的产品质量问题,我能及时发现并反馈给上级,确保产品质量达标。
4. 设备维护我熟悉注塑设备的结构及工作原理,能够对设备进行日常维护保养,确保设备正常运行。
在设备出现故障时,我能迅速排除,减少生产停机时间。
5. 团队协作我具备良好的团队协作精神,与同事之间相互学习、相互帮助,共同提高。
在完成本职工作的同时,积极参与车间组织的各项活动,为团队凝聚力贡献力量。
二、经验教训1. 安全意识在注塑生产过程中,安全意识至关重要。
我深刻认识到安全无小事,时刻保持警惕,避免因疏忽而导致安全事故的发生。
2. 操作技能为了提高生产效率,我深知自己需要不断学习新的操作技能。
在今后的工作中,我将努力学习,提高自己的业务水平。
3. 团队协作团队协作是提高生产效率的关键。
我将继续加强与同事之间的沟通与协作,共同为车间发展贡献力量。
三、未来展望1. 提高自身素质在今后的工作中,我将继续努力学习,提高自己的业务水平,为车间发展贡献更多力量。
2. 优化生产流程针对生产过程中存在的问题,我将积极提出改进建议,优化生产流程,提高生产效率。
3. 加强团队建设我将加强与同事之间的沟通与协作,共同为团队建设贡献力量,为车间创造更好的业绩。
总之,在注塑车间的工作经历让我收获颇丰。
在今后的工作中,我将继续努力,为车间发展贡献自己的一份力量。
注塑车间工作总结_注塑车间年终总结

注塑车间工作总结_注塑车间年终总结全文共四篇示例,供读者参考第一篇示例:注塑车间工作总结一、工作回顾2019年,注塑车间在公司领导的正确指引下,注塑车间全体员工团结一心,积极进取,尽心尽力,兢兢业业,勇于拼搏,将公司生产任务圆满完成。
一是生产质量得到稳步提升。
我们始终坚持“质量第一”的原则,严格按照相关标准和要求进行生产操作,注塑产品的合格率和产品质量受到了客户的高度认可,公司产品的退货率大幅度减少。
二是生产效率明显提高。
在注塑车间的管理上,我们强调了生产流程的精细化管理,合理的生产安排和班组间的密切合作,使得产品生产的周期明显缩短,效率明显提高。
三是设备维护保养得到加强。
我们加强了对注塑设备的日常检修,保养工作,及时消除了隐患,减少了机械设备的故障率,保证了生产的连续进行。
二、工作亮点1. 优秀员工的涌现。
在这一年中,注塑车间涌现了一批优秀的员工,他们用自己的实际行动诠释了专业的工作态度,在生产一线表现突出,体现出了较强的执行力和责任心。
2. 返修率大幅度下降。
我们加强了对产品质量的监控和检测,发现问题及时对产品进行改进,从而大幅度降低了产品的返修率。
3. 产品创新能力得到提升。
我们大力推动了产品研发和技术改进,通过不断的学习和实践,注塑车间在产品的外观设计、材料选择、工艺流程等方面都实现了较大突破,为公司产品附加值的提升打下了坚实的基础。
三、存在问题1. 人员流动大。
由于一些员工对工作环境不太适应或者其他原因,人员流动比较大,导致了生产中一些不稳定因素的出现。
2. 装备老化。
部分生产设备已经使用多年,存在一些老化现象,需要及时进行维修及更新升级。
3. 管理有待完善。
在生产管理过程中,发现部分班组间的协作还不够默契,工作流程还需要进一步优化。
四、改进措施1. 人员流动问题。
我们将优化薪酬福利政策,加强员工职业培训,提高员工的归属感,从而减少员工流动。
2. 设备更新。
公司计划在新的一年对注塑车间的设备进行全面更新和升级,以提高生产效率和产品质量。
- 1、下载文档前请自行甄别文档内容的完整性,平台不提供额外的编辑、内容补充、找答案等附加服务。
- 2、"仅部分预览"的文档,不可在线预览部分如存在完整性等问题,可反馈申请退款(可完整预览的文档不适用该条件!)。
- 3、如文档侵犯您的权益,请联系客服反馈,我们会尽快为您处理(人工客服工作时间:9:00-18:30)。
2009年产品质量控制情况
2009年12月份不良率高主要原因分析如下: 1、为降低产品成本铰链扶手本体使用PA66二次抽粒料生产(原使用
PA6G30原料),该料表面花银丝严重废品多。 2、加ABS二次料废品率高 3、震徳捷霸CJ320注塑机螺杆与螺筒配合间隙过大,设备压力不足产品缺
吨PA661.404吨、二次料6吨
。并对2019年材料消耗控制进行新的
规划。
追求卓越 永无止境
3、缩短非生产所用时间
千方百计地控制和缩短非生产时间:对调机、转 模、烘料、清洗螺杆与螺筒、试模、改模与修模、 修机与签样板等非生产所用时间进行了科学合理的 控制。调机15分钟、转模30分钟、烘料严格按照不 同种材料的烘料时间表来控制,其他按照标准作业 流程来进行时间控制。
09年 1月 2月 3月 4月 5月 6月 7月 8月 9月 10月 11月 12月
数量 91058
68613
352332 340223 333321 298766 285357 385073 386155 441886. 275631.5 434555 5
08年 1月 2月 3月 4月 5月 6月 7月 8月 9月 10月 11月 12月
补料退料和废料回收等环节上严格把关。坚持按定额用料,加强计量检测,
及时发现和解决用料不节约,出入库不计量,生产中超定额用料和废料率高
等问题。在保证质量的前提下,为控制原材料的消耗提倡对2次料与抽粒料
的使用,合理控制调机与洗机材料的浪费,达到减少原材料消耗的目的。
09年6至 12月共使用抽粒料与二次料 ABS16.89吨、PP18.75吨、PA61.38
对车间产品检验采取了专职检查员首件确认与末件的检验,主机手 自检、付机手互检、班长巡检与专职检查员抽检与终检相结合的产品控 制方式。
主机手对自己加工的产品首先进行自检,检验合格后再有付机手进 行互检,合格后方可装箱;班长对产品在开机前20分钟及每两个小时的 抽检;专职检查员随机抽检与终检,按照0过1退的品质抽查管理执行。
52.67% 其它 690 52.67%
追求卓越 永无止境
12月份注塑车间生产不合格率图
2009年1~12月份注塑车间生产不合格率趋图
不合格率
0.50% 0.45%
0.46%
0.40% 0.35% 0.30%
0.39%
0.34%
0.31%
0.25% 0.20% 0.15%
0.21% 0.16%
0.10%
2、配料区进行了重新规划。对两台烘箱、一台混料机及配料用操作台 进行了迁移与重新布置。
3、从新规划车间管理看板与6S改善看板。车间管理看板重新规划了车 间组织机构图、生产计划栏、质量专栏、光荣榜、公告栏、设备月度保养计 划、持续改善、员工素质矩阵图、员工学习园地等内容。6S看板规划了改善 前与改善后对比照片、车间6S管理小组、6S责任区域划分图、6S考核表等 内容。
为了保证生产过程中受控或保证产品入库合格,建议专职检查员在 产品入库前要进行全面检验。
产品外观检验:主要对产品表面的划伤、开裂、收坑、气丝、缺料、 飞边、烧焦、翘曲变形、色差及污渍等。
产品配合检验:配合件之间的间隙大小、零部件的尺寸公差等。 产品标识检验:对产品名称、编号、材料、数量、时间及责任人等。 产品包装检验:包装是否牢固,是否符合搬运要求等。
09年下半年,注塑车间将灯镜车间大小镜体装 卡子的工作主动承担下来,共装卡子106800个大小 镜体镜体,为灯镜车间节约了大量工作时间。
追求卓越 永无止境
三、生产计划完成情况
车间生产计划排程,是根据公司下达的生产计划与注塑半成品的 库存情况,结合注塑机的生产进度进行排程的。下面我将车间2019 年与2009年车间的产能对照及效益对比情况汇报如下:
料与气丝严重,废品率高。
12月份注塑不良品缺陷图
800 700 600 500 400 300 200 100
0
缺陷数量 不良比率
382
29.16% 气丝 382 29.16%
12月份注塑不良品缺陷汇总
206
15.73% 缺料 206 15.73%
32
2.44%
粘模
32 2.44%
690
缺陷数量 不良比率
0.05%
0.00% 1月 2月 3月 4月 5月 6月 7月 8月 9月 10月 11月 12月
不合格率
0.39% 0.34% 0.31% 0.21% 0.16% 具与设备管理及建议
◆■、模具管理 模具是企业中的一项重要的企业资产,模具的管理水平直接影响产品 的质量和产品的交货期,但它的管理在企业中依然属于一个被忽略的角落 不被重视。对我们生产塑胶产品而言,模具是成型塑胶产品之母,是成型 合格产品的保障。 注塑车间是与模具有密切关联的车间,产品的生产效率及品质与模具 有密切的联系。80%以上的质量及效率与模具有关,实际上注塑企业的工 程服务能力主要表现为模具。模具的重要性具体表现在如下2个方面: 1) 模具的成型周期和质量一一决定注塑生产的效率(成型快,模具维护时间 少): 2)注塑件的质量(外观、尺寸精度、强度等),主要取决于模具的质量, 好的模具保证生产的产品质量稳定,生产效率高。 所以我们要高度重视, 要在模具研发、设计与制造上下功夫,把问题消灭在制造前。现在我们企 业模具管理、设计与制造存在问题很多:应该根据TS/ 16949对产品开发 的要求产品在立项开发前,对产品与模具进行APOP策划及FMEA
数量 249355 215055 284036 241054 295147 280369 201954 89940
179496 99872
101560
36740
09年与08年全年完成注塑产品数为:3692971与2273778
3692971 X100%=162.4%
2273778
追求卓越 永无止境
四、产品质量控制
2009年注塑车间
总 结 与 不足
赵树育
追求卓越 永无止境
摘要:
一.车间现场管理 二.现场成本控制 三.计划完成情况 四.产品质量控制 五.模具与设备管理 六.注塑车间综合管理 七.存在不足
追求卓越 永无止境
一、车间现场管理
1、09年下半年车间对6D6S工作进行了较大的改善,首先对11台注塑机 从新规划与定置工作,按照事先设计好的规划图纸对新购的两台 PL4500/2900、PL2500/900注塑机及原有BOLE350/160D、 BOLE220/120C注塑机进行了迁移与重新布置。经过从新规划后的11台注塑 机10台排成一排,即方便管理又节约了生产时间。
追求卓越 永无止境
二、现场成本控制
1、劳动力消耗的控制
对生产过程中劳动力的消耗,控制定员、定额、出勤率及加班工时等。
及时发现安排不合理、派工不恰当、生产时松时紧、窝工与停工等问题。本
车间已采用定机台定责任人管理(每个机台平均1.5人),确定注塑车间人
员编制(全车间定员43人)。
2、物料消耗的控制
对主要原材料、辅助材料的消耗的管理,在领料、入库出库、投料用料、