精密模锻工艺及模具设计
锻造工艺与模具设计-模锻成形工序分析

● 金属充满模膛后,多余金属由桥口流出,此 为第Ⅲ阶段。
13
一、开式模锻变形过程
●
第Ⅰ阶段:由开始模压到金属与模具侧壁接触为止
14
一、开式模锻变形过程
●
第Ⅱ阶段:第Ⅰ阶段结束到金属充满模膛为止
15
一、开式模锻变形过程
●
第Ⅲ阶段:金属充满模膛后,多余金属由桥口流出
16
二、开式模锻各阶段的应力应变分析
32
小飞边模锻
对某些形状的锻件,在模锻最后阶段,变形区集中 分布在分模面附近,远离分模面的部分不容易充满。
33
楔形飞边槽
主要依靠桥口斜面产生的水平分力阻止金属外 流,飞边部分金属消耗减少一倍;这种飞边与锻件 连接处较厚,切边较困难
34
扩张型飞边槽
在模锻的第一第二阶段,桥口部分对金属外流有一定阻力作用;而最 后阶段,对多余金属的外流无阻碍作用,可以较大程度的减小变形力,使 上下模压靠。
42
18
二、开式模锻各阶段的应力应变分析
●
第Ⅱ阶段
19
二、开式模锻各阶段的应力应变分析
第Ⅲ阶段: 主要是将多余金属排入飞边。此时流动界面已不存 在,变形仅发生在分模面附近的一个区域内,其它部位 则处于弹性状态;多于金属由桥口流出时阻力很大,使 变形抗力急剧增大
●
20
二、开式模锻各阶段的应力应变分析
6
控制金属的流动方向
各质点向着阻力最小方向移动, 因此依靠不同的工具,采取不同的加载方式在变形 体内建立不同的应力场实现对金属流动物体内方向的控 制
7
控制塑性变形区
主要靠利用不同工具在坯料内产生不同的应力状态, 使部分金属满足屈服准则,另一部分金属不满足屈服准 则,达到控制变形区的目的
锻造工艺与模具设计

锻造工艺与模具设计一、引言锻造是一种重要的金属加工方法,通过将金属材料加热至可塑状态后,使用力量施加在材料上,从而改变其形状和结构。
模具设计是锻造工艺中的关键环节,合理的模具设计可以提高锻造产品的质量和生产效率。
本文将全面、详细、完整且深入地探讨锻造工艺与模具设计的相关内容。
二、锻造工艺的分类根据加热方式和施加力量的方式,锻造工艺可分为以下几类:2.1 自由锻造在自由锻造中,加热后的金属材料放置在锻造台上,通过锤击或压力的施加来改变其形状。
自由锻造适用于简单形状的锻件制造,如棒状、环状等。
2.2 模具锻造在模具锻造中,金属材料通过模具的形状来决定其最终形态。
模具可以分为两部分:上模和下模。
金属材料在加热后放置在模具中,上下模通过压力施加力量,使金属材料按照模具的形状进行变形。
2.3 冷锻冷锻是在常温下进行的锻造过程,适用于对材料进行塑性变形的锻造工艺。
冷锻可以提高材料的成形性能,使其获得更高的强度和韧性。
2.4 热锻热锻是在高温下进行的锻造过程,通过加热金属材料可以提高其塑性,使其变形更容易。
热锻适用于制造复杂形状的锻件,如汽车曲轴、航空发动机零件等。
三、模具设计的要点模具设计在锻造工艺中起到了至关重要的作用,以下是模具设计的一些要点:3.1 材料的选择模具应选择适合锻造材料的耐热、耐磨损的材料。
常用的模具材料有优质碳素结构钢、合金结构钢等。
3.2 模具的结构设计模具的结构设计应尽可能简单,易于制造和维修。
同时,模具应具有足够的刚性和强度,以承受锻造过程中的力量和热应力。
3.3 模具的热处理模具在使用前需要进行热处理,以提高其硬度和耐磨性。
常见的热处理方法有淬火、回火等。
3.4 模具的涂层处理为了减少模具的磨损和增加其使用寿命,可以对模具进行涂层处理。
常见的涂层材料有硬质合金、陶瓷等。
四、锻造工艺与模具设计的应用锻造工艺与模具设计在各个领域都有广泛的应用,以下是几个常见的应用领域:4.1 汽车制造锻造工艺在汽车制造中有重要的地位,汽车的关键部件如曲轴、连杆等都是通过锻造工艺制造而成的。
模锻工艺与模具设计实用手册模锻工艺与模具设计实用手册
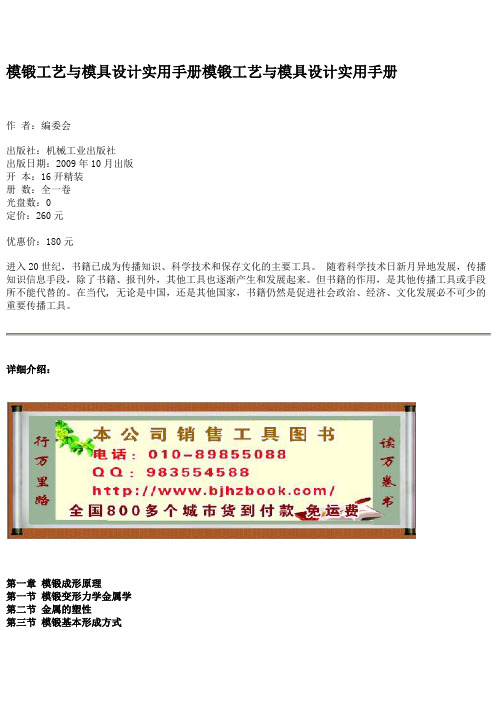
模锻工艺与模具设计实用手册模锻工艺与模具设计实用手册作者:编委会出版社:机械工业出版社出版日期:2009年10月出版开本:16开精装册数:全一卷光盘数:0定价:260元优惠价:180元进入20世纪,书籍已成为传播知识、科学技术和保存文化的主要工具。
随着科学技术日新月异地发展,传播知识信息手段,除了书籍、报刊外,其他工具也逐渐产生和发展起来。
但书籍的作用,是其他传播工具或手段所不能代替的。
在当代, 无论是中国,还是其他国家,书籍仍然是促进社会政治、经济、文化发展必不可少的重要传播工具。
详细介绍:第一章模锻成形原理第一节模锻变形力学金属学第二节金属的塑性第三节模锻基本形成方式第四节模锻变形流动的控制第二章模锻变形前工序第一节模锻原毛坯的制备第二节加热的目的、方法和质量第三节锻造加热规范第四节少无氧化加热第五节火焰加热炉与加热温度测量第三章模锻基本设备第一节锤类模锻设备第二节热模锻压力机第三节平锻机第四节螺旋压力机第五节模锻液压机第四章锤上模锻第一节锤上模锻概述第二节模锻件图设计第三节模锻模膛设计第四节制坯模膛设计第五节原毛坯计算与设备吨位第六节锤锻模结构设计第七节设计实例第五章其它设备上模锻第一节热模压力机上模锻第二节螺旋压力机上模锻第三节平锻机上模锻第六章模锻变形后工序第一节锻件冷却第二节切边和冲孔第三节模锻热处理第四节校正第五节精压第六节表面清理第七节模锻件质量检验第七章特殊金属模锻第一节不透钢的模锻第二节铝台金模锻第三节铜合金模锻第四节钛合金的模锻第五节高温合金的模锻第六节镁合金的模锻第八章特殊模锻第一节精密模锻第二节挤压第三节高速模锻第四节锟压锻第五节模轧第六节环形件辗压第七节径向锻造第八节粉末锻造第九节摆动辗压第十节液态模锻第十一节高温模锻第十二节超塑性模锻第九章模锻生产优化技术第一节模锻机械化与自动化第二节模锻成形过程模拟仿真第三节锻模cAD/CAM技术模锻工艺与模具设计实用手册模锻工艺与模具设计实用手册模锻工艺与模具设计实用手册模锻工艺与模具设计实用手册模锻工艺与模具设计实用手册模锻工艺与模具设计实用手册第一章模锻成形原理第一节模锻变形力学金属学第二节金属的塑性第三节模锻基本形成方式第四节模锻变形流动的控制第二章模锻变形前工序第一节模锻原毛坯的制备第二节加热的目的、方法和质量第三节锻造加热规范第四节少无氧化加热第五节火焰加热炉与加热温度测量第三章模锻基本设备第一节锤类模锻设备第二节热模锻压力机第三节平锻机第四节螺旋压力机第五节模锻液压机第四章锤上模锻第一节锤上模锻概述第二节模锻件图设计第三节模锻模膛设计第四节制坯模膛设计第五节原毛坯计算与设备吨位第六节锤锻模结构设计第七节设计实例第五章其它设备上模锻第一节热模压力机上模锻第二节螺旋压力机上模锻第三节平锻机上模锻第六章模锻变形后工序第一节锻件冷却第二节切边和冲孔第三节模锻热处理第四节校正第五节精压第六节表面清理第七节模锻件质量检验第七章特殊金属模锻第一节不透钢的模锻第二节铝台金模锻第三节铜合金模锻第四节钛合金的模锻第五节高温合金的模锻第六节镁合金的模锻第八章特殊模锻第一节精密模锻第二节挤压第三节高速模锻第四节锟压锻第五节模轧第六节环形件辗压第七节径向锻造第八节粉末锻造第九节摆动辗压第十节液态模锻第十一节高温模锻第十二节超塑性模锻第九章模锻生产优化技术第一节模锻机械化与自动化第二节模锻成形过程模拟仿真第三节锻模cAD/CAM技术作者:编委会出版社:机械工业出版社出版日期:2009年10月出版开本:16开精装册数:全一卷光盘数:0定价:260元优惠价:180元本店订购简单方便,可以选择货到付款、汇款发货、当地自取等方式全国货到付款,满200元免运费,更多请登陆文成图书。
材料成形工艺第六章 模锻工艺及锻模设计

(2)飞边槽尺寸的确定
1)吨位法。飞边槽具体尺寸根据锻锤吨位大小来选定(可查有关 手册),吨位法是从实际生产中总结出来的,应用简便,但未考 虑锻件形状复杂程度,因而准确性差。 2)计算法。计算法是采用经验公式计算飞边槽桥部高度,即 h=0.015A件或h=-0.09+23Q-0.01Q 式中,h是飞边桥部高度(mm);A件是锻件在分模面上的投影面 积(mm2);Q是锻件质量(kg)。然后根据计算得到的h值查相关 手册确定飞边槽其他尺寸。
第二节 锻件分类及锻件图设计
一、锻件的分类 二、表示锻件复杂程度的参数 三、锻件图的设计
第二节 锻件分类及锻件图设计
图6-2 拉臂锻件模锻工艺以及锻模的实例
一、锻件的分类
(1)短轴线类锻件 其特点是锻件高度方向的尺寸通常比其平面 图中的长、宽尺寸小,锻件平面图呈圆形、方形或近似圆形和 方形。 (2)长轴线类锻件 其特点是锻件的长度与宽度或高度的尺寸比 例较大。
一、开式模锻的变形特征 二、终锻模膛设计 三、预锻模膛设计
一、开式模锻的变形特征
1.开式模锻的变形过程分析 2.飞边槽的作用
1.开式模锻的变形过程分析
图6-10 开式模锻中金属变形过程及飞边槽的形式 a)开式模锻变形过程 b)飞边槽形式
1.开式模锻的变形过程分析
第Ⅰ阶段(镦粗变形) 毛坯在模膛中发生镦粗变形,对于某些 形状的锻件可能伴有局部压入变形。当被镦粗的毛坯与模膛侧 壁接触时,此阶段结束。这时变形金属处于较弱的三向压应力 状态,变形抗力也较小。
二、锻件的冷却方法
1.在空气中冷却 2.在干燥的灰砂中冷却 3.在炉内冷却
1.在空气中冷却
在空气中冷却的速度较快,适合合金化程度低、导热性及塑性 好的材料的中小锻件的锻后冷却。锻后一般是以单件直接散放 或成堆摆放在地面上,但不能放在潮湿地面上或金属板上,也 不要摆放在有穿堂风的地方,以免冷却不均匀或局部急冷引起 翘曲变形或开裂。
锻造工艺及模具设计
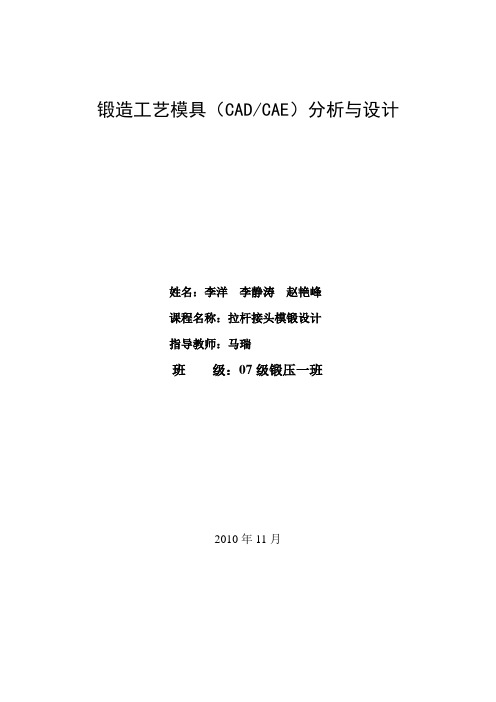
锻造工艺模具(CAD/CAE)分析与设计姓名:李洋李静涛赵艳峰课程名称:拉杆接头模锻设计指导教师:马瑞班级:07级锻压一班2010年11月拉杆接头模锻设计李洋李静涛赵艳峰(燕山大学机械工程学院)摘要:本次项目是通过锤上模锻成形生产制动器杠杆,锤上模锻主要用于锻件的大批量生产,是锻造生产中最基本的锻造方法。
主要设计步骤有制定锻件图;计算主要参数;确定设备吨位;作热锻件图,确定终锻模膛;确定飞边槽的形式和尺寸;计算毛坯图;选择制坯工步;确定坯料尺寸;设计滚压模膛;设计终锻模膛;绘制锻模图等。
前言:通过这次课程设计,我们掌握了基本的模锻设计理论,积累了一些设计经验,为以后的工作学习奠定了基础。
1.锻件图设计锻件图是根据零件产品图制定的,在锻件图中要规定:锻件的几何形状、尺寸;锻件公差和机械加工余量;锻件的材质及热处理要求以及其他技术条件等内容1.1 分模位置。
为便于锻件脱模,选拨杆锻件的最大投影面为分模面。
1.2 锻件质量锻件质量为2Kg,拨杆材料为45钢,即材质系数为M11.3 拔杆体积拔杆体积为2.68*106mm3 密度:7.85*10-6K g/ mm31.4 锻件复杂系数S=Vd/Vb=2000/(7.46×18.73×5.9×7.85)=0.309,为3级复杂系数S31.5 公差和余量查《锻压手册》表3-1-3[GB12362-1990]【普通级】长度公差为2.2(+1.5 -0.7),高度公差为1.6(+1.1 -0.5),宽度公差为1.6(+1.1 -0.5)错差公差0.5mm 残留边公差0.7mm1.6 机械加工余量余量的确定和锻件形状的复杂程度,成品零件的精度要求,锻件的材质,模锻设备,工艺条件等很多因素有关,为了将锻件的脱碳层和表面的细小裂纹去掉,留有一定的加工余量是必要的该零件的表面粗糙度为∨3(25-100um)查《锻压手册》表3-1-1[GB12362-1990]锻件内外表面的加工余量查得厚度方向1.5-2.0mm 水平方向1.5-2.0mm 取2mm1.7 模锻斜度为了使锻件容易从模膛中取出,一般锻件均有模锻斜度,附加的模锻斜度会增加金属的损耗和机械加工余量,因此在保证锻件出模的前提下,应选用较小的模锻斜度,拔模斜度应按锻件各部分高度和宽度之比值H/B和长度和宽度之比值L/B确定,根据上述原则,该锻件未标注斜率为7°。
6 精密模锻工艺及模具设计

3 精密模锻工艺及模具设计
内容简介
1 引言 2 国内外发展现状 3 基本概念 4 精密模锻成形过程的分析 5 精密模锻变形力的计算 6 影响精密模锻件尺寸精度的主要因素 7 闭式精密模锻工艺的制订 8 精密模锻的辅助工序 9 精密模锻模具设计 10 精密模锻实例分析
锻件的种类繁多,其几何形状复杂程度和相对尺寸的差别很大。 为了制订精密模锻工艺、确定合理的毛坯形状和尺寸,首先应 将锻件分类。目前比较一致的分类方法是按照锻件形状并参考 精密模锻时毛坯的轴线方向来分类的。精密模锻件的分类情况 见表。
第一类(饼盘类)锻件。其外形为圆形而高度较小。精密模锻时 毛坯轴线方向与模锻设备的作用力方向相同,金属沿高度和径 向同时流动。对于结构简单的饼盘类锻件,一般只需一个终锻 工步即可;对于结构复杂的,如编号为135、144和145所示齿 轮坯锻件,若在热模锻压力机上闭式模锻,在终锻工步前通常 还需镦粗制坯和预锻工步。编号为154、155所示圆锥齿轮锻件, 无论采用开式或闭式精密模锻,均能直接终锻出齿形。
(5)
C锻—回转体锻件轴向断面周长上的平方与其轴向断面积F之比; C外— 锻件外接圆柱体轴向断面周长的平方与外接圆柱体的轴向断面积Fc之 比。
横截面形状系数
(6)
Rg—对称轴至半个纵截面质心间的径向距离;Rc—锻件外接圆柱体半 径。
由式(5)可以看出,在锻件外接圆柱体的高度和直径不变的条件下,空 腔愈多、愈窄和愈深,则锻件的周长愈长、纵截面面积愈小,相应的 Lc2/Fc值愈大。这个比值没有完全考虑空腔在锻模上的位置:对于具有 相同宽度和深度的空腔,它们位于轴线附近或者位于外围,其 Lc2/Fc值 是相同的。
表示锻件复杂程度的参数
模锻成形工艺及模具设计特点

模锻成形工艺及模具设计特点锻锤的优点在于打击速度快,因而模具接触时间短,适合要求高速变形来填充模具的场合。
由于其快速、灵活的操作特性,其适应性非常强,有人成为“万能”设备,因而特别适用于多品种、小批量的生产。
模锻锤属于力大能小,能量可以累积,强冲击负荷和没有固定下死点的定能设备,锻锤的强冲击负荷和多次锻击成形特点,使金属在高度方向流动和填充良好,特别适用于生产薄平带筋的锻件。
锤锻主要工作特点(1)靠冲击力使金属变形,锤头在行程的最后,速度约4-9m/s(2)受力系统不是封闭的,冲击力通过下砧传给基础(3)单位时间内的打击次数多(1~10t模锻锤为40~100次/min)(4)锤头行程不固定(5)承受偏载能力和导向精度均较差(6)无顶出装置模锻工艺和模具设计特点(1)金属在各模膛中的变形是锤头的打击下逐步完成的,锤头的打击速度虽然快,但在打击中每一次的变形量较小(2)由于考冲击力使金属变形,可以利用金属的流动惯性,有利于金属填充模膛。
锻件上难充满的部分应尽量放在上模(3)在锤上可实现多种模锻工步,特别是对长轴类锻件进行滚压,拔长等制坯工步非常方便(4)由于模锻锤的导向精度不太高,工作时的冲击性质和锤头行程不固定等,因此模锻件的尺寸不太高(5)由于无顶出装置,锻件起模较困难,模锻斜度应适当大些(6)由于冲击力使金属变形,模具一般采用整体结构(7)由于靠冲击力使金属变形和锤头行程速度快,通常才用锁扣装置导向,较少采用导柱导套。
典型的锤模锻经过6个工序①镦粗:用来以减小坯料高度,增大横截面积(图中无镦粗工序)。
②拔长:将坯料绕轴线翻转并沿轴线送进,用来减小坯料局部截面,延长坯料长度。
③滚压:操作时只翻转不送进,可使坯料局部截面聚集增大,并使整个坯料的外表圆浑光滑。
④弯曲:用来改变坯料轴线形状。
⑤预锻:改善锻件成形条件,减少锻模膛的磨损。
⑥终锻:使锻件最终成形,决定锻件的形状和精度。
锻造工艺及模具设计资料
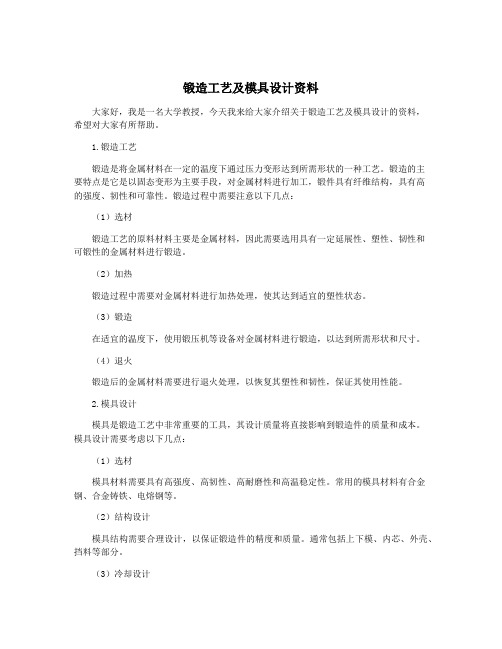
锻造工艺及模具设计资料大家好,我是一名大学教授,今天我来给大家介绍关于锻造工艺及模具设计的资料,希望对大家有所帮助。
1.锻造工艺锻造是将金属材料在一定的温度下通过压力变形达到所需形状的一种工艺。
锻造的主要特点是它是以固态变形为主要手段,对金属材料进行加工,锻件具有纤维结构,具有高的强度、韧性和可靠性。
锻造过程中需要注意以下几点:(1)选材锻造工艺的原料材料主要是金属材料,因此需要选用具有一定延展性、塑性、韧性和可锻性的金属材料进行锻造。
(2)加热锻造过程中需要对金属材料进行加热处理,使其达到适宜的塑性状态。
(3)锻造在适宜的温度下,使用锻压机等设备对金属材料进行锻造,以达到所需形状和尺寸。
(4)退火锻造后的金属材料需要进行退火处理,以恢复其塑性和韧性,保证其使用性能。
2.模具设计模具是锻造工艺中非常重要的工具,其设计质量将直接影响到锻造件的质量和成本。
模具设计需要考虑以下几点:(1)选材模具材料需要具有高强度、高韧性、高耐磨性和高温稳定性。
常用的模具材料有合金钢、合金铸铁、电熔钢等。
(2)结构设计模具结构需要合理设计,以保证锻造件的精度和质量。
通常包括上下模、内芯、外壳、挡料等部分。
(3)冷却设计在锻造过程中,模具需要耐受高温和高压的腐蚀和磨损,因此需要合理设计冷却系统,以提高模具的使用寿命和稳定性。
(4)应力分析在模具设计过程中需要进行应力分析,以确保模具在使用中不会破裂或变形,同时需要加强模具的强度和稳定性。
以上就是关于锻造工艺及模具设计的简单介绍,感谢大家的阅读。
除了以上介绍的基本知识外,我们还可以探讨一些更深入的问题和技术。
1.锻造工艺的分类锻造工艺可以根据材料的状态和加工方式进行分类。
常见的分类有:(1)按材料状态分类:①冷锻:在材料不加热或温度较低时进行的锻造。
②热锻:在材料加热到适宜温度时进行的锻造。
热锻可以分为碳素钢热锻、合金钢热锻、铝合金热锻、镁合金热锻等。
(2)按加工方式分类:①自由锻造:将金属材料置于锻造机上,通过锤击、撞击等方式进行锻造。
- 1、下载文档前请自行甄别文档内容的完整性,平台不提供额外的编辑、内容补充、找答案等附加服务。
- 2、"仅部分预览"的文档,不可在线预览部分如存在完整性等问题,可反馈申请退款(可完整预览的文档不适用该条件!)。
- 3、如文档侵犯您的权益,请联系客服反馈,我们会尽快为您处理(人工客服工作时间:9:00-18:30)。
– 二是精锻成品零件,不机加工,完全经过精锻而得到成品零件 的实例尚小。但对于一些关键零件,将其形状复杂难于切削加 工的部分进行精密模锻成形,而其余部分仍采用切削加工。如 齿轮的齿形、叶片的叶身等直接精锻成形或仅留抛光余量,而 花键槽、叶根等仍采用切削加工。这种精锻与切削加工相结合 的方法,其应用越来越广泛。精密模锻工艺的发展趋势是,由 接近形向净形发展。
第一节
精密模锻工艺的特点及应用
一、精密模锻工艺的特点
二、精密模锻的应用
一、精密模锻工艺的特点
• 与普通模锻相比,精密模锻的主要优点是:机械加工余量少甚至为零;尺寸 精度较高,即精密模锻件的尺寸公差比普通模锻件的尺寸公差小,一般仅为 普通模锻件公差的一半,甚至更小;表面质量好,即精密模锻件的表面粗糙 度较低,表面凹坑等缺陷和切边后留下的残余飞边宽度限制更严等。 • 与切削加工相比,精密模锻的主要优点:因锻件毛坯的形状和尺寸与成品零 件接近甚至完全一致,因而材料利用率高;因精密塑性成形,金属纤维的分 布与零件形状一致,因而使零件的力学性能有较大的提高等。所以,精密模 锻也称少无切屑工艺。 精密模锻与普通模锻一 样,同样分为开式精密 模锻和闭式精密模锻。 开式精密模锻(图7-1a) 时锻件沿分模面周围形 成横向小飞边,闭式精 密模锻(图7-1b)时不 形成横向飞边而仅形成 极小的纵向飞边。
9
第二节 闭式精密模锻工艺 一、常见闭式精密模锻锻件及成形工步选择
二、闭式镦粗模锻过程及成形力的计算
一、常见闭式精密模锻锻件及成形工步选择
•
•
第二类(法兰突缘类)锻件。其外形为回转体,带有圆形或长宽尺寸相差不大的法兰 或突缘。闭式模锻时,一般只需一个终锻工步。
第三类(轴杆类)锻件 其杆部为圆形,带有圆形或非圆形头部,或中间局部粗大的直 长杆类。这类锻件中,对于编号为313所示的杯杆形阶梯轴可采用闭式镦粗与反挤复 合成形工艺;其余的轴杆类锻件一般都采用闭式局部镦粗成形。
• 第六类(叉形类)锻件 包括带有空心或实心杆部、带有圆形或非圆形法兰等 多种结构形式。这类锻件常常需要两个工步以上的可分凹模模锻,即预成形 和终锻。
• 表7-1所示六种类型锻件的外形特点可以看出,前四类,即饼盘类、法兰突缘 类、轴杆类和杯筒类属于旋转体;后两类,即枝芽类和叉形类属于非旋转体。
11
第二节 闭式精密模锻工艺 一、常见闭式精密模锻锻件及成形工步选择
二、闭式镦粗模锻过程及成形力的计算
二、闭式镦粗模锻过程及成形力的计算
• • • •
1. 闭式模锻的变形过程 闭式模锻按变形金属充满模膛的方式可分为镦粗式和挤压式两类。 (1)镦粗式闭式模锻的变形过程 镦粗式闭式模锻也称闭式镦粗,其变形过程可以分为三个阶段(图7-2): – 镦粗阶段(图7-2a) – 充满角隙阶段(图7-2b) – 挤出端部飞边阶段(图7-2c),
•
第四类(杯筒类)锻件 这类锻件多采用闭式反挤、正反复合挤压或镦粗冲孔复合成形。 10
第二节 闭式精密模锻工艺 一、常见闭式精密模锻锻件及成形工步选择
二、闭式镦粗模锻过程及成形力的计算
一、常见闭式精密模锻锻件及成形工步选择
• 第五类(枝芽类)锻件 包括单枝芽、多枝芽的实心和空心类锻件。这类锻件 多采用可分凹模闭式模锻或多向闭式模锻。
1
第一节
精密模锻工艺的特点及应用
一、精密模锻工艺的特点
二、精密模锻的应用
一、精密模锻工艺的特点
• 闭式精密模锻比开式精密模锻具有更多的优点: – 锻件不产生飞边,模锻斜度更小甚至为零,可分凹模 闭式模锻还可锻出垂直于锻击方向的孔或凹坑,材料 利用率平均提高20%左右; – 坯料在封闭的模膛内成时,变形金属处于更加强大的 三向压力状态,有利于提高金属材料的塑性和产品的 机械性能;可分凹模闭式精锻常常可减少甚至取消制 坯工步,省去切边和辅助工序,平均提高生产率 25%~50%。 • 闭式模锻的主要问题是,对于一些大中型锻件,模具寿命 低,需采取多种措施逐步解决。国内外总的趋势是,闭式 精密模锻发展快,应用广。
– 二是采用专用设备,如机械式、液压式或机械—液压 联合式的单动、双动、三动和多向模锻压力机,实现 各种复杂锻件的闭式精密模锻。
7
双动液压机
第二节 闭式精密模锻工艺 一、常见闭式精密模锻锻件及成形工步选择
二、闭式镦粗模锻过程及成形力的计算
一、常见闭式精密模锻锻件及成形工步选择
• 常见的闭式精密模锻件,并按照锻件形状且参考精密模锻时毛坯的轴线方向 进行分类,如表7-1所示。
第一类(饼盘类)锻件 其外 形为圆形而高度较小。 闭式精密模锻时毛坯轴线方向 与模锻设备的作用力方向相同, 金属沿高度和径向同时流动。 对于结构简单的饼盘类锻件, 一般只需一个终锻工步即可; 对于结构复杂的,如编号为 135、144和145所示齿轮坯锻 件,若在热模锻压力机上闭式 模锻,在终锻工步前通常还需 镦粗制坯和预锻工步,编号为 154、155所示圆锥齿轮锻件, 无论采用开式或闭式精密模锻, 均能直接终锻出齿形。
12
第二节 闭式精密模锻工艺 一、常见闭式精密模锻锻件及成形工步选择
2
第一节
精密模锻工艺的特点及应用
一、精密模锻工艺的特点
二、精密模锻的应用
二、精密模锻的应用
• 目前,精密模锻主要应用在两个方面: – 一是精化毛坯,即利用精锻工艺取代粗切削加工工序,将精密 模锻件直接进行精加工而得到成品零件,如齿轮坯、叶片、小 型连杆、管接头、中小型阀体、中小型万向节叉、十字轴、轿 车等速万向节等锻件。是目前的主要应用方面。
3
典型的冷锻件实物图
5
应用实例:
轿 车安 全 气囊气体 发生器压 盖与壳体 (图片)
第二节 闭式精密模锻工艺 一、常见闭式精密模锻锻件及成形工步选择
二、闭式镦粗模锻过程及成形力的计算
第二节 闭式精密模锻工艺
• 闭式精密模锻分为整体凹模和可分凹模精密模锻。 • 当前,可分凹模精密模锻主要沿两条技术路线发展。 – 一是由通用模架和可更换的凸、凹模镶块构成可分凹 模组合结构,安装在通用锻压设备如热模锻压力机或 普通曲柄压力机、液压机和螺旋压力机上使用,实现 一些小型锻件的可分凹模精密模锻;