商用车转向器支架疲劳寿命仿真分析
转向器疲劳试验台被动加载建模与仿真

转向器疲劳试验台被动加载建模与仿真刘杰;麦云飞【摘要】目前越来越多的汽车采用电动助力转向器(EPS)转向系统,因此搭建EPS 疲劳试验台对EPS转向管柱进行疲劳耐久性试验已成为行业热点.针对疲劳试验台液压控制系统进行建模与仿真,验证液压系统在高频情况下的可行性.通过对疲劳试验台液压系统各环节进行分析,以力为控制量,角度为干扰量建立阀控液压缸力伺服控制数学模型,对系统进行Simulink仿真.通过所得的阶跃响应图和伯德图对系统进行时域和频域分析,得出疲劳试验台液压系统闭环稳定,但系统在响应快速性方面尚有欠缺,这对后续试验台液压系统的改进有重要意义.【期刊名称】《电子科技》【年(卷),期】2017(030)007【总页数】4页(P55-57,61)【关键词】疲劳试验台;力伺服控制;角度干扰;Simulink仿真【作者】刘杰;麦云飞【作者单位】上海理工大学机械工程学院,上海200093;上海理工大学机械工程学院,上海200093【正文语种】中文【中图分类】TP391.9;TH137汽车转向器疲劳试验台是用于转向机开发过程中的疲劳试验,主要功能是在实验室环境下模拟转向器工作状态下的输入、负载及环境状态,使转向机总成在特定环境下连续高负荷工作,以求在较短时间评价转向机总成及总成各部件的耐久性能[1]。
现今许多大型汽车整车厂都搭建有汽车转向器疲劳试验台以供研发需要,但随着对疲劳测试对象——转向器性能要求的不断提高,EPS疲劳试验台性能参数也随之提高,原有液压控制系统频率低于50 Hz,现通过研究液压控制系统在高频下的动态特性以验证原有液压系统在高频下是否可行,并研究液压系统的可改进之处。
本文建立高频情况下的液压系统数学模型,对其进行仿真分析,通过调节放大系数,使系统达到闭环稳定。
EPS疲劳试验台以EPS转向器为试验对象,通过液压马达模拟方向盘转动,阀控液压缸活塞杆通过力传感器连接方向机模拟汽车轮胎进行阻力加载。
汽车转向拉杆的疲劳分析

汽车转向拉杆的疲劳分析Seung K. Koh机械与汽车工程学院,Kansan国立大学,Kansan,Chonbuk,573–701, 大韩民国摘要进行疲劳分析的目的是防止疲劳失效和估算汽车转向拉杆疲劳寿命,这对于车辆安全来说是非常重要的。
从拉杆管获取的单轴标本用于单项拉伸试验和受应变控制的低循环疲劳试验,这就形成了这种拉杆材料的单循环特性。
有限元方法用于确定局部应力和应变分布的联系。
利用应变计测定的重要部位的实验应力是为了验证有限元分析结果的准确性。
在拉杆的弯曲部分计算出的局部应力是接近于实验应力的,仅有8%的差别。
构成转向拉杆的一个STKM12C碳钢管表现出循环软化的特性。
循环屈服强度约为25%,低于单屈服强度。
正如预期的有限元应力分析的那样,裂纹发生在管式转向连杆弯曲地区,并从拉杆的反面向四周扩展,导致最后这个部位的断裂。
1.引言在运动中,汽车零部件受到循环载荷的作用,从而由于局部的的疲劳损伤扩展导致产生疲劳裂纹和裂缝。
由于疲劳失效,组件无法正常运行并引发了关于车辆安全的关键问题【1】。
因此为了保证能抑制汽车零部件的疲劳失效,在汽车产业中需要对零部件的耐用性进行测试。
近年来,在汽车发展初期,疲劳设计和耐用性分析被应用于如电力输送,悬架转向,底盘系统,制动等对车辆安全起至关重要的部分【2-4】在转向系统中的拉杆是一个能传输转向力的组件,这种转向力存在于转向轴中的皮特曼臂和转向节中的转向臂之间。
在如图1所示中,拉杆组件是由球节点和连杆组成。
在本文中,为了确保拉杆组件的可靠性,拉杆的疲劳分析是通过结合拉杆组件的有限元应力分析和拉杆材料的低循环疲劳试验来进行的。
通过对拉杆的疲劳寿命的预测和用实验来确定拉杆的疲劳寿命进行比较,从而来评估这种疲劳分析的准确性和有效性2.材料特征2.1.单调性质这种拉杆是由0.12%碳钢(STKM12C)制成的,这种碳钢被用作制造一些结构性管材和一些其他的管状物。
为了研究这种制作拉杆的3mm厚、8mm宽的平板试样的单向拉伸性能,就要进行拉伸或抗拉试验,试验是由具有100KN承载能力的液压材料试验机系统完成的,并通过0.2mm/min加载速率的位移控制模式来实现。
转向节疲劳寿命有限元分析和台架试验

2021年6月第49卷第11期机床与液压MACHINETOOL&HYDRAULICSJun 2021Vol 49No 11DOI:10.3969/j issn 1001-3881 2021 11 026本文引用格式:张鹏,袁文强.转向节疲劳寿命有限元分析和台架试验[J].机床与液压,2021,49(11):127-131.ZHANGPeng,YUANWenqiang.Finiteelementanalysisandbenchtestoffatiguelifeofsteeringknuckle[J].MachineTool&Hydraulics,2021,49(11):127-131.收稿日期:2021-02-26作者简介:张鹏(1984 ),男,硕士研究生,高级工程师,主要研究方向为汽车零部件耐久试验㊂E-mail:787593499@qq com㊂转向节疲劳寿命有限元分析和台架试验张鹏1,2,袁文强1,2(1 广州机械科学研究院有限公司,广东广州510700;2 中汽检测技术有限公司,广东广州510700)摘要:以某麦弗逊悬架中的转向节为研究对象,利用有限元分析的方法验证其是否满足设计要求,并采用台架试验验证分析结果的可靠性㊂结合转向节的疲劳试验条件,通过有限元分析的方法计算出转向节在规定工况下的静力学分析结果,再根据其材料属性,计算出其疲劳寿命㊂为验证分析结果,采用液压伺服疲劳试验系统进行转向节台架耐久试验㊂结果表明:有限元疲劳分析结果与台架试验结果相符合,验证了该分析方法对转向节的设计过程有参考作用,同时表明了该转向节结构需要进一步改进㊂关键词:转向节;疲劳寿命;有限元分析中图分类号:U463 1;U467 3FiniteElementAnalysisandBenchTestofFatigueLifeofSteeringKnuckleZHANGPeng1,2,YUANWenqiang1,2(1 GuangzhouMechanicalEngineeringResearchInstituteCo.,Ltd.,GuangzhouGuangdong510700,China;2 CRATTesting&CertificationCo.,Ltd.,GuangzhouGuangdong510700,China)Abstract:TakingthesteeringknuckleofaMcPhersonsuspensionastheresearchobject,thefiniteelementanalysismethodwasusedtoverifywhetheritmetthedesignrequirements,andbenchtestwasusedtoverifythereliabilityoftheanalysisresults.Thestaticanalysisresultsofthesteeringknuckleunderthefatiguetestconditionswerecalculatedbyusingfiniteelementanalysismethod,andthefatiguelifeofthesteeringknucklewascalculatedbycombiningwithitsmaterialproperties.Inordertoverifytheanalysisresults,thehydraulicservofatiguetestsystemwasusedtocarryoutthesteeringknucklebenchendurancetest.Theresultsshowthattheresultsoffiniteelementfatigueanalysisareingoodagreementwiththoseofbenchtest,whichindicatesthattheanalysismethodcanbeusedasareferenceforthedesignprocessofthesteeringknuckle,andthestructureofthesteeringknuckleneedstobefurtherimproved.Keywords:Steeringknuckle;Fatiguelife;Finiteelementanalysis0㊀前言转向节是麦弗逊悬架中的关键零件之一,连接轮毂轴承㊁卡钳㊁刹车盘㊁下摆臂㊁转向拉杆和减振器总成[1],传递来自轮胎的各种路面激励㊂转向节受力复杂,必须有足够的强度来保证驾驶的安全性[2]㊂疲劳破坏是转向节失效的主要形式之一,因此在转向节的设计和验证阶段,必须严格考虑它的疲劳耐久性能[3]㊂有限元分析技术是一种重要的设计和验证手段,可以在零件制造之前通过仿真计算分析其强度和性能是否满足要求[4]㊂有限元计算的方法需要设定边界条件㊁材料属性和载荷条件,尤其是疲劳寿命计算过程中需要设置表面状态,假设疲劳破坏判断条件㊂因此影响其准确性的因素众多,为了检验计算结果的可靠性,往往需要进行验证试验[5]㊂1㊀转向节疲劳寿命分析工况条件麦弗逊悬架的结构如图1所示,车轮通过轮毂轴承安装在转向节上,转向节下部通过球铰C连接下摆臂,下摆臂再通过衬套A和B连接在副车架上;转向节上部与减振器总成固定连接,减振器总成上端通过缓冲块D与车身连接;转向节的转向臂通过球铰E与转向拉杆连接,转向拉杆通过球铰F与转向机连接㊂其中,衬套A和B相当于转动副,球铰C㊁E和F相当于球副,缓冲块D能在各个方向摆动也相当于球副㊂车轮承受来自地面的激励,纵向载荷和横向载荷经过转向节,然后主要经过下摆臂和减振器传递到车身㊂转向拉杆对转向节的转向臂施加推拉载荷从而控制方向㊂图1㊀麦弗逊悬架结构[2]为了验证转向节的疲劳性能是否满足要求,需要根据转向节在实车上的载荷工况设计台架疲劳耐久试验或者进行有限元计算㊂转向节疲劳寿命分析以及台架试验的载荷输入,是通过道路载荷谱采集(RLDA)后计算伪损伤转化而来,或者根据车辆轴荷㊁满载质量㊁轴距等参数,采用经验公式计算得出㊂针对某型号的转向节,为了验证其疲劳性能,进行制动工况㊁侧向力工况疲劳试验及分析㊂根据经验公式计算得到的疲劳寿命以及台架试验的载荷输入如表1所示㊂在表中,纵向力以车身后方向为正,侧向力以朝向车身中轴线为正,垂向力以向上为正㊂2个工况中均施加了静态的垂向力,制动工况的1个载荷循环包括10次正向加载和1次负向加载;侧向力工况1个载荷循环包括1次正向加载和1次负向加载㊂进行制动工况试验的转向节经历10万次循环加载后,未出现裂纹破坏即判定为满足要求;进行侧向力工况试验的转向节经历20万次循环加载后,未出现裂纹破坏即判定为满足要求㊂表1㊀疲劳工况及载荷工况载荷名称载荷/N循环次数/次制动工况纵向力8200,-6800垂向力6800100000侧向力工况侧向力9200,-9200垂向力68002000002 静力学分析将转向节模型导入ABAQUS中,设置材料属性㊁装配部件㊁设置分析步㊁设置耦合㊁划分网格㊁添加边界条件,然后进行静力分析㊂2 1㊀边界条件为了能够实现正确的模拟计算,对零件的约束需要和其实际工作状态一致㊂对于转向节而言,转向节各个连接点的约束需要模拟实车状态㊂如图2所示,下摆臂连接点(图中RP⁃3参考点)仅约束球铰中心位置X㊁Y两个方向的位移,不约束Z方向的位移和绕3个方向的旋转,球销孔位置采用运动耦合的方式与球铰中心耦合㊂减振器上端安装点(图中RP⁃1参考点)约束X㊁Y和Z3个方向的位移,不约束绕3个方向的旋转,转向节上与减振器配合的安装面采用运动耦合的方式与减振器上端安装点耦合㊂转向臂球铰中心(图中RP⁃7参考点)仅约束Y方向的位移,不约束X㊁Z方向的位移以及绕3个方向的旋转,球销孔位置采用运动耦合的方式与球铰中心耦合㊂图2㊀转向节的约束和加载对零件施加载荷的作用点和方向也需要符合实际情况㊂如图2所示,垂向力㊁纵向力和侧向力的加载点为轮胎接地点(图中RP⁃3参考点),纵向力的加载是模拟刹车工况,轮胎接地点的载荷产生的扭矩会传递至卡钳,然后传递至转向节卡钳安装孔位㊂在纵向力计算过程中,为了简化模型,将轮胎接地点(RP⁃3)㊁轮胎中心(RP⁃2)和2个卡钳安装孔位(RP⁃4和RP⁃5)运动耦合,同时轮胎中心和主轴表面运动耦合,卡钳安装孔内表面分别和RP⁃4和RP⁃5运动耦合㊂2 2㊀材料属性和网格划分转向节材料为40Cr,材料属性如表2所示㊂表2㊀40Cr材料属性参数参数值抗拉强度/MPa980泊松比0.3弹性模量/GPa210㊀㊀在ABAQUS中划分网格时,因为转向节形状不规则,采用自由网格划分技术,并选择十节点二次四面体C3D10单元,采用该单元可以得到较高精度的分析结果,但是相比六面体单元需要消耗更多的计算时间㊂网格布点距离设置为1 5mm,转向节一共划分成50 6万个单元㊂2 3㊀静力分析结果在制动工况模拟计算时,X方向分步骤地加载峰㊃821㊃机床与液压第49卷值为+8200N和-6800N的载荷,Z方向加载6800N的静态载荷㊂当X方向加载+8200N时其静力分析结果如图3所示,当X方向加载-6800N时其静力分析结果如图4所示,当X方向加载0N㊁Z方向加载+6800N时其静力分析结果如图5所示㊂可知:3种受力状态下最大应力为556MPa,出现在减振器连接臂根部㊂图3㊀制动力工况下X方向加载+8200N时应力云图图4㊀制动力工况下X方向加载-6800N时应力云图图5㊀制动力工况下仅Z方向加载+6800N时应力云图在模拟侧向力工况时,Y方向分步骤地加载峰值为ʃ9200N的载荷,Z方向加载6800N的静态载荷㊂当Y方向加载+9200N时,其分析结果如图6所示,当Y方向加载-9200N时,其分析结果如图7所示㊂可以看出:最大应力出现在减振器连接臂的根部位置㊂在Y方向加载-9200N时,最大应力值达到459MPa㊂图6㊀侧向力工况下Y方向加载+9200N时应力云图图7㊀侧向力工况下Y方向加载-9200N时应力云图3 疲劳寿命分析零件在承受往复循环的载荷作用时,容易引起裂纹的萌生,随后裂纹逐渐扩展至破坏㊂疲劳破坏是零件破坏的主要形式之一,影响零件疲劳性能的因素也很多,包括材料性能㊁零件结构㊁载荷性能㊁表面质量以及环境等㊂采用模拟计算的方法求解零件的疲劳寿命需要合理设置相关的影响因素,才能获得可信的求解结果㊂nCodeDesignlife结合ABAQUS的静力计算结果㊁材料属性㊁载荷情况和零件表面状态可以计算得出疲劳寿命即载荷循环次数㊂计算流程如图8所示㊂将制动工况的静态分析结果导入Designlife中,按10次正向加载和1次负向加载为1个加载循环,计算得出的寿命为13 4万次循环,满足使用要求,疲劳寿命云图如图9所示㊂图8㊀疲劳寿命计算流程㊃921㊃第11期张鹏等:转向节疲劳寿命有限元分析和台架试验㊀㊀㊀图9㊀制动工况疲劳寿命将侧向力动工况的静态分析结果导入Designlife中,按1次正向加载和1次负向加载为1个加载循环,计算得出的寿命为10 3万次循环,不满足使用要求,疲劳寿命云图如图10所示㊂图10㊀侧向力工况疲劳寿命4 疲劳耐久台架试验为验证转向节的疲劳性能,进行疲劳耐久台架试验,台架试验一般采用作动器提供推拉力㊂为了反映转向节实车受力状态,在台架试验时需要对转向节施加合理约束㊂为避免下摆臂衬套㊁减振器顶端的弹性元件和弹簧在试验过程引起大位移,采用模拟减振器和模拟下摆臂进行代替,模拟下摆臂仅保留上下摆动的自由度,模拟下摆臂通过球铰和转向节连接,模拟减振器顶端通过球铰与铁平台连接㊂为空间布置方便,将横拉杆缩短,同时保留横拉杆内外球铰㊂制动工况台架如图11(a)所示,其载荷波形如图11(b)所示㊂侧向力工况台架如图12(a)所示,其载荷波形如图12(b)所示㊂侧向力工况中,载荷通过模拟轮胎的夹具传递至转向节的轮毂主销中,模拟轮胎的夹具仅与转向节轮毂轴承主销配合,并且作动器前后两端均有保护其自身不受侧向力的球铰㊂因此,在轮胎接地点还需要约束X方向的位移,即约束模拟轮胎转动,可以采用两端带有球铰的横拉杆沿着X方向固定轮胎接地点㊂图11㊀制动工况疲劳试验图12㊀侧向力工况疲劳试验㊃031㊃机床与液压第49卷制动工况中,转向节历经10万次载荷循环后未发生破坏,符合设计要求㊂侧向力工况下,2个转向节分别历经144879㊁146725次循环时发生破裂,破裂位置均为减振器连接臂根部,如图13所示㊂试验结果与有限元分析计算结果相吻合㊂图13㊀侧向力工况疲劳试验转向节断裂位置5㊀结论针对某型号的转向节,采用有限元计算分析的方法求出其疲劳失效位置和疲劳寿命㊂对比分析结果与试验结果,验证了有限元分析结果有一定的参考价值㊂在合理设置各个相关参数的前提下,其结果与试验结果一致性较好㊂该型号转向节的减振器连接臂根部是薄弱位置,在侧向力作用下会引发疲劳失效,需要进一步改进该结构㊂参考文献:[1]SIVANANTHV,VIJAYARANGANS,etal.Fatiguelifeanalysisandoptimizationofapassengercarsteeringknuckleunderoperatingconditions[J].InternationalJour⁃nalofAutomotiveandMechanicalEngineering,2015,11(1):2417-2429.[2]刘明余.基于麦弗逊结构汽车转向节的试验台架开发及验证[D].秦皇岛:燕山大学,2019.LIUMY.DevelopmentandverificationofsteeringknuckletestbasedonMacphersonstructure[D].Qinhuangdao:Yan⁃shanUniversity,2019.[3]杨苍禄,朱传敏,刘素,等.汽车转向节疲劳寿命分析和试验研究[J].机电工程,2015,32(7):950-953.YANGCL,ZHUCM,LIUS,etal.Fatiguelifeanalysisandexperimentalvalidationofautomobilesteeringknuckle[J].Mechanical&ElectricalEngineeringMagazine,2015,32(7):950-953.[4]蔚亚.基于有限元分析的新能源汽车底盘结构静强度分析[J].内燃机与配件,2019(24):44-45.[5]徐忠诚,张健,蒋雪文,等.某乘用车转向节疲劳分析及验证[J].汽车零部件,2018(9):23-27.XUZC,ZHANGJ,JIANGXW,etal.Fatigueanalysisandvalidationofknuckleofapassengercar[J].AutomobileParts,2018(9):23-27.(责任编辑:张楠)(上接第102页)[13]郭逸伦.基于OpenCV的边缘检测算法效率分析[J].科学技术创新,2019(1):87-88.[14]INGLEMA,TALMALEGR.Respiratorymaskselectionandleakagedetectionsystembasedoncannyedgedetec⁃tionoperator[J].ProcediaComputerScience,2016,78:323-329.[15]陈浩.图像经典边缘检测算子的研究与比较[J].电脑编程技巧与维护,2019(12):150-152.[16]ÖZTÜRKŞ,AKDEMIRB.Comparisonofedgedetectionalgorithmsfortextureanalysisonglassproduction[J].ProcediaSocialandBehavioralSciences,2015,195:2675-2682.[17]周莉莉,姜枫.图像分割方法综述研究[J].计算机应用研究,2017,34(7):1921-1928.ZHOULL,JIANGF.Surveyonimagesegmentationmeth⁃ods[J].ApplicationResearchofComputers,2017,34(7):1921-1928.[18]DHALKG,RAYS,DASA,etal.Fuzzymulti⁃levelcolorsatelliteimagesegmentationusingnature⁃inspiredoptimi⁃zers:acomparativestudy[J].JournaloftheIndianSocietyofRemoteSensing,2019,47(8):1391-1415.[19]冷建伟,沈芳婷.基于HSV色彩模型与区域生长法的水文图像分割[J].计算机工程,2017,43(7):223-228.LENGJW,SHENFT.HydrologicalimagesegmentationbasedonHSVcolormodelandregiongrowingalgorithm[J].ComputerEngineering,2017,43(7):223-228.[20]段康容,刘先勇.基于Blob算法的标记圆检测技术研究[J].传感器世界,2014,20(8):7-10.DUANKR,LIUXY.Researchonreferencepointdetec⁃tionbasedonBlobalgorithm[J].SensorWorld,2014,20(8):7-10.[21]ZHANGM,WUT,BEEMANSC,etal.Efficientsmallblobdetectionbasedonlocalconvexity,intensityandshapeinformation[J].IEEETransactionsonMedicalIma⁃ging,2016,35(4):1127-1137.(责任编辑:张楠)㊃131㊃第11期张鹏等:转向节疲劳寿命有限元分析和台架试验㊀㊀㊀。
商用车车架疲劳寿命仿真研究

商用车车架疲劳寿命仿真研究作者:张小雨来源:《科技信息·下旬刊》2018年第09期摘要:汽车车架是汽车的关键承载部件,易发生疲劳破坏。
商用车车架进行扭转台架疲劳试验时,不满足车架循环次数20 万次寿命要求;需要采用有限元法模拟车架扭转疲劳台架试验,以找出焊缝开裂原因并提出改进方案,比较不同焊缝建模方法计算所得车架扭转台架疲劳寿命,确定与台架试验结果吻合的焊缝建模方法;对车架焊缝开裂风险位置进行结构优化设计,提升纵梁横梁接头强度,先用有限元方法验证车架优化方案满足寿命要求后,再将优化后的车架进行台架试验,车架未发生开裂。
应用有限元方法预测台架疲劳耐久寿命,可以找出焊缝开裂原因并快速验证优化方案,缩短产品开发周期。
关键词:商用车;台架试验;疲劳寿命疲劳耐久性是汽车的主要性能指标之一。
汽车中大部分零部件的失效模式都表现为疲劳破坏。
对于非承载式车身的车型,车架是整车的装配基体和承载基体,承载着汽车各总成,并承受着各种力及力矩。
设计合理的车架是开发非承载式汽车重中之重,设计车架即不可过强,避免造成材料浪费,增加产品成本;又不可过弱,避免车辆寿命周期内发生开裂,对乘客造成伤害。
因此,对车架疲劳耐久寿命预估是车架开发的重要内容。
车架由不同厚度、不同形状的冲压钣金焊接而成,焊缝数量多且走势复杂,根据工程经验,车架疲劳失效主要发生在焊缝及其热影响区域,因此对焊缝及热影响区进行有限元模拟及寿命预测势在必行。
某商用车车架在进行扭转疲劳台架试验时,车架第三横梁与纵梁连接处焊缝发生开裂,不满足车架疲劳寿命要求,因此,对车架焊缝进行模拟,预测车架焊缝疲劳耐久寿命、找出焊缝开裂原因并快速提出有效改进措施。
一、车架扭转疲劳台架试验根据车架進行台架扭转疲劳试验,车架扭转疲劳台架试验模拟实车状态,把车架总成固定在台架试验台上,用专用夹具固定车架后弹簧座吊耳,可绕X 轴旋转加载装置与前弹簧座支架通过专用夹具连接,激振器作用通过加载装置Z 向加载,加载扭矩±2000N·m,加载频率3Hz,顺时针、逆时针各加载一次计一个循环。
新型货车转向架变刚度弹簧组的试验寿命估算及疲劳强度分析

校核结果与寿命估算所得的结果一致;转 K 型转向架弹簧的校核结果与其所采用的试验方案有关系,现行试验 4
方案下 ,校核所得 的转 K4型转向架减振外簧 的疲 劳强度 相对最弱 。分析认 为,应该 修正减振 内簧 的设计 参数 ,
从设计源头消除失稳及由此引发的其他问题;个别弹簧出现折断质量问题 ,主要原因是弹簧钢材质不够稳定,
部件 ,其主要失效形式为疲劳断裂。尽管制造单位
很注重产品制造质量 ,但实际运用中仍偶有断簧发
生[ 。为此 ,本文参照 目 1 ] 前的试验标准、试验结果 以及关于变刚度弹簧组的设计 方法 ,对转 K2 、 型 转 K 型、转 K 型转 向架的变刚度弹簧组 的疲劳 4 6
04 . ,要求寿命达到 3 0 次,不出现裂纹和折断 ×i
( +c)可 近似求 得 材料 的剪 切疲 劳 极 限 为 r b 50 3 a 5. 7MP 。采用两点法嘲作 出材料在双对 数坐
基金项 目:国家 自然科学基金 资助项 目 (0702 ;甘肃省 中青年科技基金 资助项 目 (Z 01 2— 4 5659) 3 S4 50 ) A 0 作者简介 :王 红 (98 ) 16一 ,男 ,青海乐都人 ,副教授 。
行计算分析。试验载荷下的寿命估算表明; 质量完好的这 3 种转向架变刚度弹簧组的各型弹簧的疲劳寿命均可 达到 3 0 次; ×1 其中, K 型转向架的减振内簧 、 K 型转向架的减振外簧、转 K 型转向架的承载外簧在 转 2 转 4 6
对应 的弹簧组 中相对寿命较短 。疲劳校核表明 ;转 K 2型、转 K 型转 向架各 型弹簧 能基本满足 疲劳强度 要求 , 6
承载外簧 承载内簧 减振外簧 5 5 2 2 6 1 8 1 8 12 2 7 0 9 8 4900 8 . 2 3918 8 . 5 1230 4 . 9 22 3 20 1 25 5 5 0 .5 7 7 .0 7 7 .0 6S2 r A 0i V T C 6 S2 r A 0I V T C 6 S2 r A 0i V T C 90 5 90 5 90 5
新型货车转向架变刚度弹簧组的试验寿命估算及疲劳强度分析

第28卷,第1期 中国铁道科学Vol 128No 11 2007年1月 C HINA RA IL WA Y SCIENCEJ anuary ,2007 文章编号:100124632(2007)0120071205新型货车转向架变刚度弹簧组的试验寿命估算及疲劳强度分析王 红,商跃进,孟广浦(兰州交通大学机电工程学院,甘肃兰州 730070) 摘 要:针对运用中偶有发生的转K2型、转K4型、转K6型3种货车转向架变刚度弹簧组的断簧问题进行计算分析。
试验载荷下的寿命估算表明:质量完好的这3种转向架变刚度弹簧组的各型弹簧的疲劳寿命均可达到3×106次;其中,转K2型转向架的减振内簧、转K4型转向架的减振外簧、转K6型转向架的承载外簧在对应的弹簧组中相对寿命较短。
疲劳校核表明:转K2型、转K6型转向架各型弹簧能基本满足疲劳强度要求,校核结果与寿命估算所得的结果一致;转K4型转向架弹簧的校核结果与其所采用的试验方案有关系,现行试验方案下,校核所得的转K4型转向架减振外簧的疲劳强度相对最弱。
分析认为,应该修正减振内簧的设计参数,从设计源头消除失稳及由此引发的其他问题;个别弹簧出现折断质量问题,主要原因是弹簧钢材质不够稳定,材料与产品的热处理工艺匹配不够完善。
建议立项研究60Si2CrVA T 材料的基础性能参数。
关键词:变刚度弹簧;试验寿命;疲劳强度;转向架;分析 中图分类号:U2721041;U2701331 文献标识码:A 收稿日期:2006202227;修订日期:2006208225 基金项目:国家自然科学基金资助项目(50675092);甘肃省中青年科技基金资助项目(3ZS0412A252004) 作者简介:王 红(1968—),男,青海乐都人,副教授。
为满足我国铁路货车提速和重载的要求,近年来,国内相关车辆工厂先后设计制造了运行速度为120km ・h -1的转K2型、转K4型、转K6型3种技术性能先进的新型货车转向架。
转向架构架疲劳计算方法的分析

转向架构架疲劳计算方法分析1112A.Cera ,G.Mancini ,V.Leonardi ,L.BertiniTrenitalia S.p.A, Florence,1Italy ; Pisa University - Mech. Engng. Dept., Pisa,2Italy摘要本文主要进行了转向架构架强度评定的关键分析,尤其着重于焊接节点。
特别分析了针对不同焊接节点的疲劳分析技术。
疲劳分析技术中包含的两种方法(疲劳极限和Goodman 曲线)是由欧洲标准EN 13749提出的。
通过分析,我们可以知晓方法的准确性和可行性,从而选择最合适的转向架构架分析方法。
通过成熟的商业有限元软件(ANSYS ),我们可以对挑选的标准的可靠性和安全性进行严格地比较。
本文研究调查了疲劳分析方法,关注了其中有限元方法的使用。
一、引言欧洲标准EN 13749,作为欧洲标准化进程的产物,于2005年4月由欧洲标准委员会CEN 提出。
规范制定的目的在于定义完整的转向架设计过程。
其中包括设计步骤、评定方法、验证以及加工质量要求。
EN 13749编撰了静态和疲劳下载荷的假设和计算。
同时标准也定义了转向架构架静态和疲劳阻抗的测试方法。
在转向架的章节中,标准针对疲劳预测特别定义了一系列的载荷工况和作用在构架上的不同类型的力。
随着新的数值计算方法的发展(有限元方法),疲劳完整性评估已经发展到较高的水平,尤其是在精确度和细节仿真方面。
即使在近期有了更新,标准仍未解决和定义某些重要部分。
仍需要研究的问题主要有两点。
首先缺少用于焊接节点的有限元仿真和疲劳评定方法。
其次尚未定义多轴应力状态下(特别在铁路应用)疲劳强度评估的标准计算方法。
由于上述未解决的问题,同样的转向架设计用不同的疲劳分析方法可能得到不一样的结果。
从2006年起,意大利铁路(意大利国有铁路运营商)的工程部门和比萨大学机械工程部展开了关于转向架疲劳行为的公共研究项目。
基于LMS Virtual.Lab的货车转向架疲劳性能仿真研究
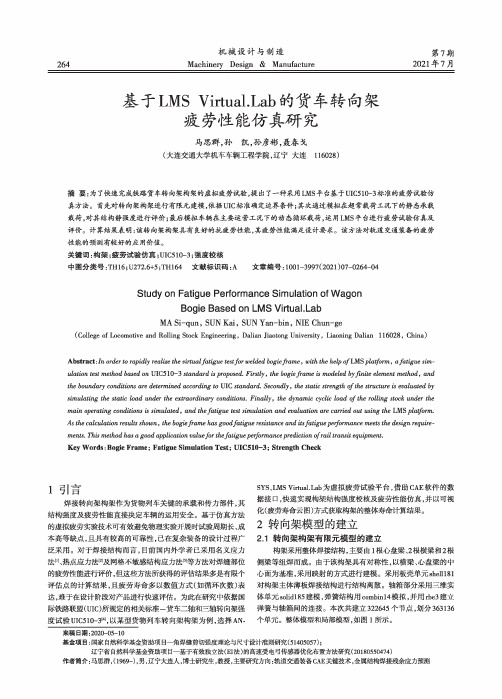
在心盘横端面,二者均以面压力载荷的形式加载,如图2所示;轨
道扭曲载荷作用在1、4位或2、3位线弹簧单元处,以14mm的垂 向抬高量施加。
3.1.3组合工况
为验证该货物列车在极限载荷共同作用的实际运营条件
下,转向架构架是否产生塑性永久变形,进行的超常载荷工况验
算,如表2所示。
表2超常载荷工况 Tab.2 Extraordinary Load Conditions
50%。基于运营安全性考虑,将上述边界条件同时施加到疲劳分 析的构架有限元模型中。UIC标准规定的动态载荷疲劳加载试 验分为三阶段,如图5所示。
Fig.5 Three-Stage Diagram of Fatigue Test Loading
5.2.2有限元计算结果的导入
该平台提供了广泛的数据接口,能够直接读取各类有限元 软件的模型和计算结果文件,并以此为基础进行疲劳分析。将经
度条件下材料的屈服强度应大于325 MPa。基于安全考虑,同时
依据EN12663标准冏,超常工况下非焊缝区安全系数取1.15,因此
其许用应力取值为282MPao
No.7
266
机械设计与制造
July.2021
4.2焊接构架静强度评价
在超常载荷工况下,转向架最大Von Mises应力出现在第四 工况,位置出现在轴箱上表面外侧与构架侧梁下盖板交界处 ,值
3.2.2约束条件
约束条件与静强度分析一致,强制位移约束都是施加在线 弹簧单元处。不同的是,将施加在线弹簧单元处的轨道扭曲载荷
更改为7mm的垂向抬高值。
4焊接构架的静强度评价
4.1焊接构架静强度标准
UIC规定,对由延展性较好的塑性材料组成的构架进行静强
- 1、下载文档前请自行甄别文档内容的完整性,平台不提供额外的编辑、内容补充、找答案等附加服务。
- 2、"仅部分预览"的文档,不可在线预览部分如存在完整性等问题,可反馈申请退款(可完整预览的文档不适用该条件!)。
- 3、如文档侵犯您的权益,请联系客服反馈,我们会尽快为您处理(人工客服工作时间:9:00-18:30)。
收稿日期:2010 04 10作者简介:赵卫艳(1978 ),女,山西运城人,陕西汽车集团有限责任公司汽车工程研究院工程师,长安大学工学博士研究生,E mail:zw y780906@ 。
第31卷 第1期2011年1月长安大学学报(自然科学版)Journal of Chang an University(Natural Science Edition)Vol.31 No.1Jan.2011文章编号:1671 8879(2011)01 0090 05商用车转向器支架疲劳寿命仿真分析赵卫艳1,2,谷雪松2,王 可3,魏 朗1,曹祖强2(1.长安大学汽车学院,陕西西安710064; 2.陕西汽车集团有限责任公司汽车工程研究院,陕西西安710200; 3.中国定远汽车试验场,安徽定远210028)摘 要:为了揭示转向器支架的破坏机理,在整车实际运行工况下计算转向器支架最大受力,并在此基础上建立了转向器支架的有限元模型,在转向器质量和最大转向力矩的共同作用下对转向器支架进行静强度分析;根据S N 曲线方法、正弦载荷谱和Radio ss 工具对转向器支架进行疲劳寿命分析;最后将仿真结果与实际破坏形式及理化分析结果进行对比。
结果表明:转向器支架满足静强度要求,但是存在局部寿命不足、一致性差的问题;仿真分析与工程实际具有较好的吻合性。
关键词:汽车工程;转向器支架;疲劳寿命;有限元分析;S N 曲线中图分类号:U 463.4 文献标志码:ASimulation for fatigue life of commercial vehicle steering gear bracketZH A O Wei yan 1,2,GU Xue song 2,WANG Ke 3,WEI Lang 1,CAO Zu qiang 2(1.Schoo l o f Automo bile,Chang an U niversit y,Xi an 710064,Shaanxi,China; 2.Institute of Auto mobile Engineer ing,Shaanx i A uto mobile G ro up Co L td,Xi an 710200,Shaanx i,China;3.China Dingy uan A ut omotive P rov ing G round,Ding yuan 210028,Anhui,China)Abstract:In order to reveal the dam ag e mechanism of the steering g ear bracket for a certain com m er cial vehicle,the maximum force w as com puted under actual w orking condition.The finite model of the bracket w as built based on the force analy sis,and the static streng th w as analyzed by sim ulation.The fatig ue life of the br acket w as analyzed by simulation,based on the S N method,the sine w ave lo ad spectrum and Radioss tool.In the end,the simulation analysis w as com pared w ith the real damage fo rms and physics chemical analysis.T he result show s that the static str ength o f the steering g ear bracket is adequate,but the local life is insufficient and the consistence is poor,the simulatio n and r eal damage results are uniform.2tabs,11figs,10refs.Key words:automobile engineering;steering g ear bracket;fatig ue life;finite element analy sis;S N curve0 引 言汽车零部件的破坏是涉及结构、材料、强度、动力学、制造装配工艺、质量保证体系以及车辆运用条件等诸多因素的复杂问题。
转向器支架,作为转向器的支撑件和地面转向阻力矩到转向器的传递机构,其结构强度及其疲劳寿命直接影响整个转向机构的稳定性和使用寿命。
对于重型商用车来说,由于轴荷加大,转向器支架承受的交变力矩更大,因此合理设计转向器支架,使其以尽量小的质量满足强度和使用寿命要求,将有利于整车减重和提高转向机构的稳定性。
目前,对于重型车辆的设计分析,主要集中在车架及各大总成的匹配性计算以及车架的静强度和刚度分析上,而对于小结构件的重视程度不够,因此经常会出现由于小结构件的破坏而影响整车性能[1 4]。
本文采用有限元分析方法,研究转向器支架在最恶劣转向条件下的静强度和疲劳行为,基于H y permesh/Radioss 平台进行静强度和疲劳寿命分析计算,同时将分析结果与实车问题及破坏件理化分析结果进行对比,分析结果与破坏件破坏形式完全吻合,真实可靠地反映了转向器支架的破坏机理。
这种分析方法是成熟且科学的,已得到较多的工程应用,而且可以为更多小构件的设计和破坏失效分析提供参考。
1 转向器支架破坏形式转向器支架是在车辆行驶约2.5 104km 后出现断裂,断裂件的断口锈蚀,锈蚀程度不一,锈蚀严重区域表面较为光滑,约1/3断口面粗糙,可见金属光泽,如图1、图2所示。
图1断裂件复原形貌图2 断裂件断口形貌根据图1、图2转向器支架的断口形貌,初步判断为疲劳断裂。
由于构件腔体矩形孔四角过渡圆角过小,造成应力集中点,在交变力矩作用下,逐渐在构件应力集中区域或铸造缺陷部位产生细微裂纹,形成疲劳源;随着循环次数的增加,裂纹逐渐扩展,两侧不断开合,类似研磨作用,形成了断口的光滑区;随着裂纹扩展,构件的截面不能承受所加载荷而突然发生脆性断裂,形成了断口区的粗糙区。
结合上述判断,根据转向器支架三维模型建立有限元模型,然后综合考虑工艺影响,对转向器支架进行静强度和疲劳寿命分析,同时与真实件断裂情况和理化分析报告进行对比,以此检验分析结果和指导产品优化及工艺改进。
2 受力分析转向器支架整车装配如图3所示,转向器支架通过8个螺栓固结在车架上,转向器安装在支架上。
转向器支架受力传递途径:转向轮转向过程中,克服地面摩擦阻力进行转动,转向轮的转动带动转向节臂(前桥上)绕转向主销转动,转向节臂拉动直拉杆前后运动,直拉杆带动转向摇臂转动,转向摇臂的转向力作用在转向器上,进而传递给转向器支架,因此转向器支架一方面承受转向器的重力,另一方面承受来自转向摇臂的转向力(或力矩,即此处转向力与转向摇臂的长度之乘积),受力如下页图4所示。
在此处进行力矩计算,转向器支架所受力矩来自于转向车轮的转向阻力矩。
图3 转向器的装配在最恶劣的转向条件下(在干而粗糙的转向轮支承面上作原地转向)进行力矩计算,转向车轮的转向阻力矩T r 由转向车轮相对于主销轴线的滚动阻力矩T 1、轮胎与地面接触部分的滑动摩擦力矩T 2以及转向车轮的稳定力矩或自动回转力矩所形成的阻力矩T 3组成。
即91第1期 赵卫艳,等:商用车转向器支架疲劳寿命仿真分析图4 受力分析T r =T 1+T 2+T 3T 1=G 1f a T 2=G 1xT 3=aG 1[ (sin ( 1)+sin ( 2))+ (cos ( 1)+cos ( 2))]式中:G 1为转向轴的载荷;a 为滚动阻力的力臂,或主销偏移距,本文取50m m;f 为车轮的滚动阻力系数,取0.015; 为主销内倾角; 为主销后倾角; 1、 2分别为内、外转向轮的平均转角,本文采用42 ; 为附着系数,计算时取0.86;x 为滑动摩擦力矩T 2的力臂:x =0.5r 2-r 21,r 、r 1分别为车轮的自由半径和静半径,取r 1=0.96r 。
将相关数据代入上式中,计算得到转向摇臂轴上的力矩为6730N m 。
3 仿真计算与结果分析3.1 静强度有限元分析根据三维模型和上述受力分析进行有限元建模,采用H ypermesh/Radioss 工具进行前处理和计算,本模型可以简化为8点约束、2点加载的计算工况。
用4节点四面体单元对转向器支架进行网格划分,建立好的有限元分析模型如图5所示。
在建立好的转向器支架有限元模型上施加约束条件。
约束条件为,通过建立转向器支架与车架螺栓连接处的多点约束单元(multi point constraint,MPC),在与车架连接的螺栓孔的中心节点上分别约束其在x 、y 、z 3个方向的平移自由度和转动自由度,模拟转向器支架被固结在车架上。
转向器支架所承受载荷包括转向器的质量和转向力矩,质量载荷定义为,在转向器质心处施加点质量44kg,质量点通过Rbe3单元与转向器支架连接在一起;力矩载荷定义为,在干而粗糙的支承面上,转向轮作原地图5 有限元分析模型转向时转向器支架所承受的力矩,在转向器支架与摇臂连接点处施加转向力矩6730N m,此点通过刚性Rigid 单元与转向器支架连在一起。
在计算过程中,涉及到转向器支架的材料及其固有力学性能参数见表1。
表1 转向器支架材料及其固有属性材 料密度/(t m -3)弹性模量/GPa 切变模量/GPa球墨铸铁QT450 107.315561计算出的应力分布如图6所示。
在质量和力矩载荷的共同作用下,转向器支架所受最大等效应力值为300MPa,发生于倒圆角处以及加强筋端部,应力值低于材料的屈服极限310M Pa 。
这说明,该转向器支架的静强度指标是合格的,但是存在局部应力集中,存在疲劳隐患,其他部位的应力水平相对较低。
图6 转向器支架应力分布3.2 疲劳寿命分析在静强度分析结果的基础上,根据S N 曲线对转向器支架进行疲劳寿命分析[5 10]。
S N 曲线试验测定十分耗资费力,因此,本文根据经验关系式进行疲劳极限的估算,从而确定S N 曲线。
对于标准材料试验的S N 曲线来说,根据材料103与106次循环的疲劳强度就可确定曲线,103次循环的疲劳强度,根据经验大约等于90%的拉伸极限S b ,106次92长安大学学报(自然科学版) 2011年循环的疲劳强度(疲劳极限)等于50%的拉伸极限S b 。