剪板机控制的PLC控制
剪板机的PLC控制系统设计

高 新 技 术7科技资讯 S CI EN CE & T EC HNO LO GY I NF OR MA TI ON 剪板机是机械行业的常用设备之一,主要用于金属板材的直线剪裁。
将P L C 技术用于剪板机的控制系统,改善了剪板机的自动化水平和性能,提高了企业的生产效率,降低了工人的劳动强度,减少了人工成本,增强了产品的竞争力。
1 剪板机简介按照工艺要求,设计的剪板机包括四个部分,即开卷取料、校直校平、定长取料和板料切断。
前三部分中,通过辊轴实现板料的前移,由电动机作为动力来实现驱动。
最后的板料切断部分为往复式直线运动,考虑到冲击与振动的存在,采用气动技术实现这部分的结构。
四个部分协调动作,实现板料的切断工作,并达到精度要求。
图1所示为剪板机结构简图。
开卷取料部分包括开卷和取料机构,开卷机构的幅度可以调节,满足不同板料剪切的要求。
取料机构是为了使得板料前移,通过辊轴夹紧板料并转动向前推进,其中取料机构的辊轴部分同样可以调节,以满足板料厚度规格的变化。
校直校平部分是通过外加压力达到板料由原来的卷式逐步变成需要的平板,由多级上下辊轴施压逐步实现。
在实现施压校直的同时,还要将板料传输向前给下一工作位置。
上下辊轴之间的间距同样可调,满足板料规格及所需压力所需。
定长取料部分的左右幅度、上下辊轴均可调,以满足剪切取料不同尺寸的要求。
这一部分是剪板机的剪切精度关键所在,最后切下来的板料尺寸精度由这里来决定,要求其精度高、效率高、运转平稳,综合考虑,在传动上采用了同步带的方案。
板料切断部分主要考虑剪切力的大小,当然必须结合切断时的特征,如冲击大、振动强等特征。
结合该运动为往复式直线运动,确定采取气压传动方式,具有清洁、安全、成本低等优点。
经计算选型,确定合适的气缸。
2 PLC 控制系统设计PLC因其适合于工业现场的控制,在现代制造业自动化领域得到了广泛的应用。
剪板机的控制系统采用P L C 来实现。
根据板料规格不同,对其工艺速度要求可调,所以在前三部分中的驱动电机采用变频器进行调速。
基于PLC实现对剪板机自动控制的设计

基于PLC实现对剪板机自动控制的设计剪板机是一种工业生产中常用的设备,用于加工各种金属板材。
随着自动化技术的不断发展,越来越多的企业开始使用PLC控制系统来实现对剪板机的自动化控制。
本文将介绍基于PLC实现对剪板机自动控制的设计方案。
一、PLC控制系统的基本原理PLC(Programmable Logic Controller)即可编程逻辑控制器,是一种专门用于工业自动化控制的计算机控制系统。
PLC控制系统由CPU、输入模块、输出模块、通信模块等组成。
它的工作原理是根据程序控制CPU的运行状态,从而控制输入和输出模块的状态。
PLC控制系统非常稳定可靠,而且易于安装和维护,因此在工业生产中被广泛应用。
二、剪板机自动控制系统的设计方案1. 系统框图设计剪板机自动控制系统的基本框图如下图所示:图中P为PLC,可以看到P的输入端通过探头检测工件、压力、位置等信号,输出端则连接着各种驱动元件,在PLC的控制下实现对剪板机的自动化操作。
其中,探头检测到的信号通过模拟输入模块进入PLC中,而PLC的输出信号则通过模拟输出模块输出到各种驱动元件中。
2. 硬件配置设计为实现对剪板机的自动化控制,我们需要对剪板机进行硬件改造。
具体的改造方案如下:(1)安装伺服电机,取代原有电机。
伺服电机是一种精度高、运行稳定的电机,适合用于精密控制。
通过PLC的控制,可以控制伺服电机的转速和运动方向,从而实现对剪板机的精确控制。
(2)添加探头传感器。
探头传感器用于检测工件的位置、大小、压力等参数。
当探头检测到信号时,PLC控制系统会根据预设程序进行对工件的切割。
(3)安装触控屏,取代原有的按钮控制方法。
触控屏操作简单,可以直观地显示加工工艺和状态,与PLC控制系统实现无缝对接。
通过触控屏,可以方便地对剪板机的工作模式、加工参数等进行设置和控制。
(4)添加安全保护装置,如急停开关、警示灯等。
在PLC控制系统运行期间,一旦出现异常情况,急停开关能够迅速切断电源保护设备和人员的安全。
基于PLC实现对剪板机自动控制的设计

基于PLC实现对剪板机自动控制的设计剪板机是一种常见的机械设备,广泛应用于金属加工行业。
传统的剪板机需要由操作员手动控制,存在操作繁琐、效率低下、安全风险高等问题。
为了提高剪板机的自动化程度,可以利用PLC(可编程逻辑控制器)对剪板机进行自动控制。
PLC是一种专门用于实现工业自动化控制的电子设备,具有可编程性、可靠性强、稳定性好的特点。
通过PLC控制系统,可以实现对剪板机的自动控制,提高生产效率和产品质量。
剪板机自动控制系统的设计首先需要确定控制策略,即确定剪切厚度、切割长度、切割速度等参数。
然后,根据控制策略设计PLC程序。
PLC程序主要包括输入模块、输出模块、中央处理器和编程软件。
输入模块负责读取外部信号,如传感器检测到的材料厚度、长度等信息;输出模块负责向执行机构发送控制信号,如控制剪刀的开合、工作台的前进后退等;中央处理器负责处理输入信号并执行控制算法,根据输入信号的变化改变输出信号,从而实现对剪板机的自动控制。
编程软件用于编写PLC程序,通常采用类似于 ladder diagram(梯形图)的图形化编程语言。
对于剪板机的自动控制,PLC程序的关键任务是根据输入信号实时监测剪板机的状态,并根据预先设定的控制策略做出相应的控制。
当传感器检测到材料厚度超过设定值时,PLC程序可以自动调整剪刀的压力,确保材料在剪切过程中不会变形或损坏。
PLC程序还可以根据实时输入信号调整切割速度,确保切割精度和效率的平衡。
在实际应用中,剪板机的自动控制还需要考虑安全因素。
PLC程序中需要加入安全控制逻辑,如急停装置、紧急切断装置等,以保障操作人员和机器的安全。
基于PLC实现对剪板机自动控制的设计可以大大提高剪板机的自动化程度,提高生产效率和产品质量,减少人工操作,降低安全风险。
随着科技的不断发展,PLC技术将在工业自动化控制领域中得到更广泛的应用。
基于PLC实现对剪板机自动控制的设计
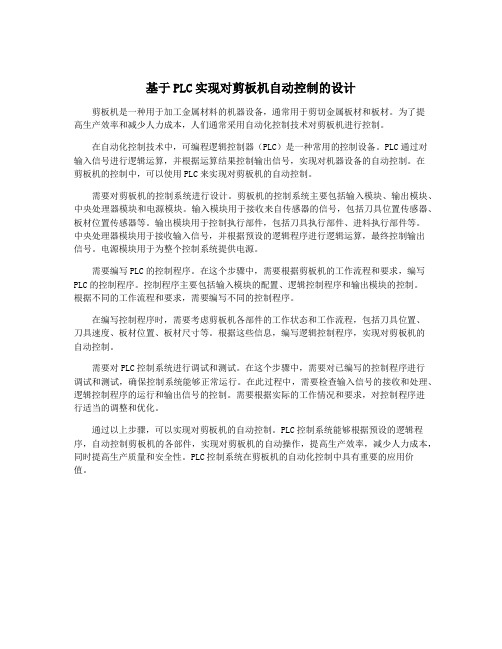
基于PLC实现对剪板机自动控制的设计剪板机是一种用于加工金属材料的机器设备,通常用于剪切金属板材和板材。
为了提高生产效率和减少人力成本,人们通常采用自动化控制技术对剪板机进行控制。
在自动化控制技术中,可编程逻辑控制器(PLC)是一种常用的控制设备。
PLC通过对输入信号进行逻辑运算,并根据运算结果控制输出信号,实现对机器设备的自动控制。
在剪板机的控制中,可以使用PLC来实现对剪板机的自动控制。
需要对剪板机的控制系统进行设计。
剪板机的控制系统主要包括输入模块、输出模块、中央处理器模块和电源模块。
输入模块用于接收来自传感器的信号,包括刀具位置传感器、板材位置传感器等。
输出模块用于控制执行部件,包括刀具执行部件、进料执行部件等。
中央处理器模块用于接收输入信号,并根据预设的逻辑程序进行逻辑运算,最终控制输出信号。
电源模块用于为整个控制系统提供电源。
需要编写PLC的控制程序。
在这个步骤中,需要根据剪板机的工作流程和要求,编写PLC的控制程序。
控制程序主要包括输入模块的配置、逻辑控制程序和输出模块的控制。
根据不同的工作流程和要求,需要编写不同的控制程序。
在编写控制程序时,需要考虑剪板机各部件的工作状态和工作流程,包括刀具位置、刀具速度、板材位置、板材尺寸等。
根据这些信息,编写逻辑控制程序,实现对剪板机的自动控制。
需要对PLC控制系统进行调试和测试。
在这个步骤中,需要对已编写的控制程序进行调试和测试,确保控制系统能够正常运行。
在此过程中,需要检查输入信号的接收和处理、逻辑控制程序的运行和输出信号的控制。
需要根据实际的工作情况和要求,对控制程序进行适当的调整和优化。
通过以上步骤,可以实现对剪板机的自动控制。
PLC控制系统能够根据预设的逻辑程序,自动控制剪板机的各部件,实现对剪板机的自动操作,提高生产效率,减少人力成本,同时提高生产质量和安全性。
PLC控制系统在剪板机的自动化控制中具有重要的应用价值。
基于PLC的自动剪板机控制系统设计

基于PLC的自动剪板机控制系统设计自动剪板机是一种广泛应用于工业领域的设备,其主要功能是对板材进行剪切加工。
随着工业自动化的不断发展,基于PLC的自动剪板机控制系统设计成为了一种常见且有效的解决方案。
本文将从系统设计的背景、系统结构、控制策略、硬件选型和软件开发等方面进行深入研究和探讨。
第一章:引言随着工业领域对高效、精确加工设备需求的不断增长,自动剪板机作为一种重要的生产设备,被广泛应用于钢铁、建筑等行业。
然而,在传统手动操作下,生产效率低下且存在安全隐患。
因此,基于PLC的自动剪板机控制系统设计成为了解决这些问题的有效手段。
第二章:系统结构设计基于PLC(可编程逻辑控制器)技术进行自动剪板机控制系统设计是目前较为常见和成熟的解决方案之一。
本章将介绍该系统结构设计中各个组成部分及其功能。
2.1 输入模块输入模块主要用于接收各种传感器信号,如压力传感器、光电传感器等,以实时监测剪板机工作状态和板材位置等信息。
2.2 输出模块输出模块用于控制剪板机的各个执行机构,如电动切割刀、送料装置等,以实现对板材的精确切割。
2.3 PLC控制器PLC控制器是整个系统的核心部件,负责接收输入模块的信号,并根据预设的控制策略进行逻辑运算和决策,并通过输出模块对执行机构进行精确控制。
2.4 人机界面人机界面是用户与系统进行交互和信息显示的接口设备,通过触摸屏或键盘等方式实现对系统参数设置、工作状态监测等功能。
第三章:控制策略设计自动剪板机需要根据具体需求进行不同的切割操作。
本章将介绍基于PLC的自动剪板机控制系统设计中常用的几种控制策略,并分析其优缺点。
3.1 定长切割策略定长切割策略是指根据预设参数对板材进行固定长度的切割操作。
该策略适用于需求相对固定的生产场景,具有操作简单、生产效率高的优点。
3.2 定宽切割策略定宽切割策略是指根据预设参数对板材进行固定宽度的切割操作。
该策略适用于对板材宽度要求较高的场景,可以保证切割出的板材具有一致的宽度。
基于PLC实现对剪板机自动控制的设计

基于PLC实现对剪板机自动控制的设计剪板机自动控制是现代工业生产中的一项重要技术,其实现是为了提高生产效率、降低成本、提升产品质量,本文将基于PLC实现对剪板机自动控制的设计进行详细介绍。
一、剪板机自动控制的意义剪板机是用于对金属板材进行切割加工的设备,传统的剪板机操作需要人工介入,存在劳动力成本高、操作复杂、效率低下等问题,而自动控制技术的引入可以解决这些问题,提高生产效率,降低成本,提升产品质量。
1. 系统框图设计剪板机的自动控制系统主要由PLC、传感器、执行器、人机界面等组成。
首先需要设计系统框图,明确各个部件之间的连接方式和信号传输路径,保证系统的稳定性和可靠性。
2. 传感器的选择剪板机自动控制系统需要使用液压传感器、接近开关、光电开关等多种传感器,用于实现对板材位置、板材厚度、压力等参数的检测和监控,因此传感器的选择至关重要。
3. PLC程序设计PLC作为剪板机自动控制系统的核心,需要编写相应的程序来实现对剪板机的自动控制。
程序设计需要考虑到各种工况下的情况,包括正常工作、异常情况、安全保护等,保证系统的稳定和安全。
4. 执行器控制执行器是剪板机自动控制系统中的重要部件,包括液压缸、电机等,通过对执行器的控制实现对刀具的移动、板材的压力等操作,需要设计相应的控制策略。
5. 人机界面设计人机界面是剪板机自动控制系统的操作界面,设计合理的人机界面可以方便操作人员对系统进行监控和操作,提高工作效率。
6. 安全保护设计在剪板机自动控制系统中,安全保护至关重要,需要设置相应的安全开关、紧急停止按钮等,保证在出现异常情况时能够及时停止系统运行,确保操作人员的安全。
三、基于PLC的剪板机自动控制系统的优势1. 提高生产效率通过自动控制,可以实现对剪板机的精确控制,减少人为操作中的误差,提高生产效率。
2. 降低成本自动控制可以减少人工成本,提高生产效率,降低生产成本。
3. 提升产品质量自动控制可以精确控制切割参数,保证产品质量的稳定性和一致性。
基于PLC实现对剪板机自动控制的设计
基于PLC实现对剪板机自动控制的设计剪板机是一种常用的机械设备,用于对板材进行切割,广泛应用于制造业中。
由于剪板机的切割过程需要高精度且操作人员需要长时间持续工作,因此需要自动化控制系统来实现自动控制。
本文基于PLC(可编程逻辑控制器)实现对剪板机的自动控制设计。
PLC是一种用于自动控制和工业自动化的专用电子设备,可以程序控制多个输入和输出,实现各种工业自动化应用。
PLC系统具有开放、灵活、易于编程和维护、可靠性高、抗干扰性强等特点。
本文将介绍基于PLC实现对剪板机的自动控制设计的过程和实现方式,包括硬件设计和软件编程实现。
具体包括以下几个方面:1. 硬件设计1)PLC选型:选择合适的PLC是关键。
根据剪板机的需求,可选用中小型PLC,如西门子S7-200、德尔TA等。
2)传感器选择和连接:在剪板机的自动控制系统中,需要选用多个传感器,如光电传感器、接近传感器等,用于检测工件的位置和状态。
一般将传感器放置在剪板机的进料口和出料口等位置进行控制。
3)电机驱动器:电机是剪板机的核心组成部分,需要选用合适的电机驱动器,如伺服驱动器、变频器等,用于控制电机的转速和运动方向。
4)控制面板:控制面板用于控制剪板机的启动、停止、调整等操作。
控制面板需要设计成符合人体工学的布局,易于操作。
2. 软件编程实现软件编程是实现自动控制系统的关键。
在剪板机的自动控制系统中,软件编程需要实现以下几个方面:1)输入和输出的配置:在PLC编程软件(如西门子的STEP 7等)中进行输入和输出的配置,确定输入输出信号的类型和地址,为后续程序的实现提供必要的条件。
2)梯形图程序的编写:在PLC编程软件中,根据剪板机的工作流程,编写相应的梯形图程序。
比如,程序需要检测工件的位置和状态,根据传感器的信号反馈,控制电机的启动和停止。
3)程序调试:在梯形图程序编写完成后,进行程序调试。
通过示波器、万用表等工具,对PLC的各个输入和输出信号进行检测,确保程序逻辑正确,可以正常运行。
自动剪板机的PLC控制系统设计
⾃动剪板机的PLC控制系统设计2010年05期(下)⾃动剪板机是⼀种精确控制板材加⼯尺⼨,将⼤块⾦属板材进⾏⾃动循环剪切加⼯,并由送料车运送下⼀⼯序的⾃动化加⼯设备,其结构原理如下图所⽰:1.⼯作过程1.1当系统启动时,输⼊板料的加⼯尺⼨、每车板料的加⼯数量等参数,按下⾃动开关,系统运⾏。
1.2检查限位开关SQ6的状态,若⼩车空载,起动送料⼩车,直⾄碰到SQ5,使其闭合,⼩车停车。
1.3起动送料结构,带动板料右移,直⾄碰到SQ1时,送料停⽌。
1.4压块电机启动,使压块B 压下,上限开关SQ2闭合。
当压块到位,板料压紧时,下限开关SQ3闭合。
1.5剪切⼑电动机起动,带动剪⼑下落。
SQ4闭合,直⾄剪断的板料落⼊⼩车并计数⼀次后,剪切⼑复位。
1.6当⼩车上的板料够数时,控制⼩车的电动机带动⼩车右⾏,将切好的板料送⾄下⼀⼯序。
卸下后,⼩车再左⾏到位,进⾏下⼀⼯作循环。
2.PLC 控制系统设计2.1I/O 端⼦分配图通过市场调研,该设计采⽤⽇本松下公司⽣产的FP1—C24系列PLC 系统作为主机。
2.2梯形图3.结束语⾃动剪板机的⼯艺过程很符合顺序控制的要求,所以采⽤PLC 对其进⾏控制,较好的解决了继电器控制系统中因⼤量接线使可靠性降低的问题。
因此应⽤PLC 控制系统,具有操作简单、运⾏可靠、编程⽅便,控制精度⾼的特点。
控制过程中,每车板料数及加⼯板料的尺⼨可根据实际需要修改,⽽且利⽤光电接近开关检测板料状态⾮常准确。
【参考⽂献】[1]PLC 应⽤技术(三菱).中国劳动社会保障出版社.[2]王炳实.机床电⽓控制[M].机械⼯业出版社.[3]潘新民,王燕芳.微型计算机实⽤系统设计[M].⼈民邮电出版社.科●⾃动剪板机的PLC 控制系统设计张玲(滨州技术学院⼭东滨州256603)【摘要】当前我国机械制造业⼤量的通⽤设备在继电器控制基础上,采⽤单⽚机控制、PLC 控制等新的控制技术来提⾼⾃动化程度。
对于PLC 控制⽽⾔,具有编程灵活,安装维修⽅便,抗⼲扰能⼒强等优点。
基于PLC实现对剪板机自动控制的设计
基于PLC实现对剪板机自动控制的设计一、引言剪板机是一种常见的金属加工设备,用于对金属板材进行裁剪和切割,广泛应用于制造业中。
传统的剪板机控制方式主要依赖于人工操作,存在效率低、精度不高等问题。
为了提高剪板机的自动化程度和生产效率,需要引入现代控制技术,即基于PLC实现对剪板机的自动控制。
二、剪板机的工作原理剪板机主要由机架、传动系统、工作台、夹紧装置和切割装置等部分组成。
其工作原理是利用刀座的上下运动来对金属板材进行裁剪和切割。
传统的控制方式是通过按钮和手柄来控制刀座的上下运动。
这种方式存在操作不便、效率低、安全性差等问题。
三、基于PLC的剪板机控制系统设计1. 系统结构基于PLC的剪板机控制系统主要由PLC控制器、传感器、执行机构和人机界面组成。
PLC控制器负责逻辑控制和运动控制,传感器用于检测工件的位置和状态,执行机构实现工件的夹紧和切割,人机界面用于操作和监控整个系统的运行情况。
2. 系统功能(1)自动定位功能:通过传感器检测工件的位置和长度,PLC控制器根据预设的切割长度自动调整刀座的位置,实现自动定位功能。
(2)自动夹紧功能:当工件到位后,PLC控制器通过执行机构自动夹紧工件,确保工件在切割过程中的稳定性。
(4)故障诊断功能:系统可以实时监测各传感器和执行机构的状态,一旦出现故障,即可通过人机界面进行故障诊断和排除。
3. 系统控制PLC控制器采用编程控制方式,利用PLC编程软件对系统的控制逻辑进行编程。
编程的主要内容包括工件位置的检测、刀座运动控制、气缸的控制、故障诊断等。
四、系统实现步骤1. 传感器安装和接线:根据实际情况选择合适的位置安装传感器,并将传感器与PLC 控制器进行接线连接。
2. 执行机构调试:安装好执行机构后,进行执行机构的调试和参数设置,确保夹紧和切割的动作正常有效。
3. PLC编程:根据设计要求,对PLC进行编程,实现自动定位、夹紧、切割和故障诊断等功能。
4. 人机界面设计:设计合理的人机界面,显示系统的运行状态和工艺参数,提供操作和监控功能。
PLC剪板机控制文档
一、控制要求下图是剪板机的结构示意图,据剪板机的工作特点,对控制系统提出控制要求如下:1、通电后,检测各工作机构的状态,控制各工作机构处于初始位置;2、开始时压钳和剪刀在上限位置,限位开关I0.0和I0.1为ON,按下启动按钮I1.0;3、首先板料右行(Q0.0为ON)至限位开关I0.3动作;4、压钳下行(Q0.1为ON并保持),压紧板料后,压力开关I0.4为ON,压钳保持压紧,剪刀开始下行(Q0.2为ON).剪断板料;5、剪断板料后,I0.2变为ON,压钳和剪刀同时上行(Q0.3和Q0.4为ON),他们分别碰到限位开关I0.0和I0.1后,分别停止上行;6、都停止后,又开始下一周期的工作,剪完10块料后,停止工作并停在初始状态。
图1.剪板机结构示意图二、控制方案设计根据题目的设计要求,PLC因其具有极高的稳定性以及很好的抗干扰的能力可以保证控制工作机构进行运动时有很好的保障。
并结合本题目的要求,故决定使用PLC来控制工作机构的运动。
德国西门子公司生产的可编程序控制器在我国的应用也相当广泛,在冶金、化工、印刷生产线等领域都有应用。
S7系列PLC产品可分为微型PLC(如S7-200),小规模性能要求的PLC(如S7-300)和中、高性能要求的PLC(如S7-400)等。
采用可编程硬件控制器较好地解决了这一问题。
它是一种将计算机技术,自动控制技术和通信技术结合在一起的新型工业自动控制设备,不仅能实现对开关量信号的逻辑控制,还能实现与上位计算机等智能设备之间的通信。
因此,将PLC应用于该控制,完全能满足技术要求,且具有操作简单、运行可靠、工艺参数修改方便、自动化程度高等优点。
三、所用器件造型3.1 PLC的构成:从结构上分,PLC分为固定式和组合式(模块式)两种。
固定式PLC包括CPU板、I/O板、显示面板、内存块、电源等,这些元素组合成一个不可拆卸的整体。
模块式PLC包括CPU模块、I/O模块、内存、电源模块、底板或机架,这些模块可以按照一定规则组合配置。
- 1、下载文档前请自行甄别文档内容的完整性,平台不提供额外的编辑、内容补充、找答案等附加服务。
- 2、"仅部分预览"的文档,不可在线预览部分如存在完整性等问题,可反馈申请退款(可完整预览的文档不适用该条件!)。
- 3、如文档侵犯您的权益,请联系客服反馈,我们会尽快为您处理(人工客服工作时间:9:00-18:30)。
石家庄铁道大学四方学院
集中实践报告书
课题名称 剪板机控制的PLC 控制
姓 名 *** 学 号 2012**** 系、 部 电气工程系 专业班级 方**** 指导教师
李**
2014年12月31 日
※※
※
※
※
※
※
※
※ ※※ ※
※ ※
※ ※
※
※
※
※※※
※
※
2012级 PLC 课程设计
目录
第1章设计目的 (1)
第2章设计要求 (1)
第3章I/O分配表和接线图 (2)
3.1PLC选型 (2)
3.2I/O分配 (2)
3.3 I/O接线图 (2)
第4章PLC程序设计 (3)
4.1梯形图设计 (3)
4.2指令语句表 (4)
第5章设计总结 (4)
参考文献 (5)
第1章 设计目的
熟悉常用控制电器的结构原理、用途,达到正确使用和选用的目的。
掌握电气控制电路的基本环节,具备阅读和分析电气控制电路图的能力。
具备独立设计简单电气控制电路的能力。
熟悉掌握PLC 的工作原理与系统构成、指令系统、编程方法及PLC 控制系统的设计。
具备应用PLC 实现电气控制自动化要求的设计、安装、调试、故障处理能力。
第2章 设计要求
要求剪板机剪满10块板后停止动作(X 为输入,Y 为输出) 1、初始状态时,压钳见到在原位 10,0=X ,11,0=X ;
2、开始剪板启动,01X ,首先板料右行0,0Y ,当板料到达预定要剪得长度时,13,0=Y ;
3、此时压钳1,0Y 开始下行知道压住板料,当压钳压力达到所需压力时,压力继电器14,0=X ;
4、剪刀开始下行剪板2,0Y ,此时压钳1,0Y 仍维持不变,当剪刀剪完板料下行至2,0X 时,仍有12,0=X ;
5、压钳上行至3,0Y ,剪刀上行4,0Y 。
第3章 I/O 分配表和接线图
3.1 PLC 选型
三菱公司近年来推出的FX 系列PLC 有FX 0、FX 2、FX 0S 、FX 0N 、FX 2C 、FX 1S 、FX 1N 、FX 2N 、FX 2NC 等系列型号。
FX 0S 的功能简单实用,价格便宜,可用于小型开关量控制系统;FX 0N 可用于要求较高的中小型控制系统;FX 2N 的功能最强,可用于要求很高的系统。
综上所述,选用FX2N -16MR 的PLC 。
3.2 I/O 分配
X1 ,01X Y1 0,0Y X2 13,0=X Y2 1,0Y X3 14,0=X Y3 2,0Y X4 2,0X Y4 3,0Y X5 10,0=X Y5 4,0Y X6 11,0=X X7 停止
3.3 I/O 接线图
第4章PLC程序设计4.1梯形图设计
4.2指令语句表
第5章设计总结
设计过程中,由于程序不是很长,没有遇到太多的问题,但是仍然会有小的问题,比如PLC的选型,I/O接线图的绘制。
由于本人对真正意义上的生产还缺乏经验,因此要想达到实际生产要求还需要许多改进的地方。
PLC作为一种通用的工业自动控制装置,综合了计算机技术、自动控制技术和通信技术。
由于它具有可靠性高、体积小、功能强、程序设计简单、灵活通用、维护方便等一系列的优点,因而在冶金、能源、化工、交通、电力等领域中有着广泛的应用,因此有着良好的发展前景。
近些年,为了适应市场的各方面的需求,各生产厂家对其不断进行改进,推出了功能更强、结构更完善的新产品。
总体来说,朝两个方向发展:一是向超小型、专用化和低价格的方向发展,以进行单机控制;另一个是向大型、高速、多功能和分布式全自动网络化方向发展,以适应现代化大型工厂、企业自动化的需要。
因此,在未来的全自动化工厂里,PLC将发挥很大的作用。
参考文献
[1] 郁汉祺. 电气控制与可编程序控制器应用技术. 东南大学出版社. 2010
[2] 邓则名. 程良伦. 谢光汉. 电器与可编程控制器应用技术. 1997
[3] 王兆义. 小型可编程序控制器实用技术. 机械工业出版社. 1997
[4] 张万忠. 可编程序控制器应用技术. 化学工业出版社. 2002。