镍基高温合金溅射NiCrALY涂层盐腐蚀行为
Incoloy-800H合金表面镀镍层在氯化物熔盐中的腐蚀行为
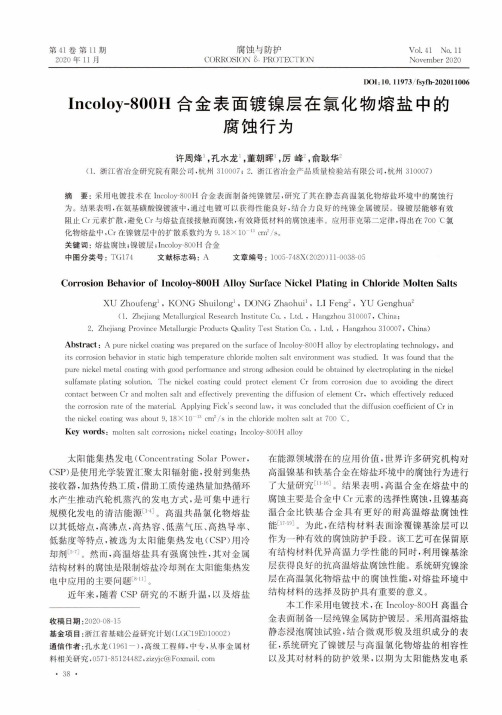
第41卷第11期 2020年11月腐蚀与防护CORROSION PROTECTIONVol. 41 No. 11November 2020IX)I : 10. 11973 fsyfh-202011006Incoloy-800H合金表面镀镍层在氯化物熔盐中的腐蚀行为许周烽1,孔水龙1,董朝晖1,厉峰,俞耿华(1.浙江省冶金研究院有限公司,杭州310007; 2.浙江省冶金产品质量检验站有限公司•杭州310007)摘要:采用电镀技术在Inc〇l〇y-800H合金表面制备纯镍镀层,研究了其在静态高温氯化物熔盐环境中的腐蚀行 为。
结果表明,在氨基磺酸镍镀液中•通过电镀可以获得性能良好,结合力良好的纯镍金属镀层。
镍镀层能够有效 阻止〇元素扩散.避免C r与熔盐直接接触而腐蚀,有效降低材料的腐蚀速率。
应用菲克第二定律,得出在70C T C’氯 化物熔盐中,C r在镍镀层中的扩散系数约为9. 18X1CT13cm2/s。
关键词:熔盐腐蚀;镍镀层;Incoloy-800H合金中图分类号:TG174 文献标志码:A文章编号:1005-748X(2020) 11-0038-05Corrosion Behavior of Incoloy-800H Alloy Surface Nickel Plating in Chloride Molten SaltsXU Zhoufeng1,KONG Shuilong1,DONG Zhaohui1,LI Feng2,YU Genghua2(1. Zhejiang Metallurgical Research Institute C o.,L td.,Hangzhou 310007,China;2. Zhejiang Province Metallurgic Products Quality Test Station Co. , L td.,Hangzhou 310007,China)Abstract:A pure nickel coating was prepared on the surface of Incoloy-800H alloy by electroplating technology, and its corrosion behavior in static high temperature chloride molten salt environment was studied. It was found that the pure nickel metal coating with good performance and strong adhesion could be obtained by electroplating in the nickel sulfamate plating solution* The nickel coating could protect element Cr from corrosion due to avoiding the direct contact between Cr and molten salt and effectively preventing the diffusion of element Cr, which effectively reduced the corrosion rate of the material. Applying Fick^ second law, it was concluded that the diffusion coefficient of Cr in the nickel coating was about 9. 18X10-13 cm2/s in the chloride molten salt at 700 C.Key words:molten salt corrosion;nickel coating;Incoloy-800H alloy太阳能集热发电(Concentrating Solar Power, CSP)是使用光学装置汇聚太阳辐射能,投射到集热 接收器,加热传热工质,借助工质传递热量加热循环 水产生推动汽轮机蒸汽的发电方式,是可集中进行 规模化发电的清洁能源[1_4]。
镍基耐蚀合金的高温高压氧化行为研究
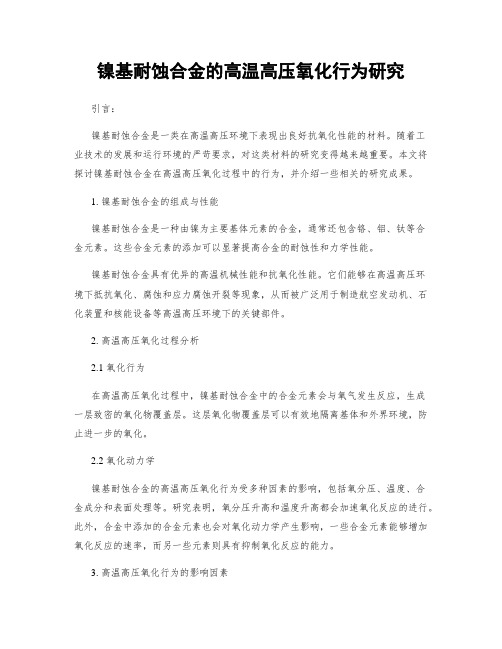
镍基耐蚀合金的高温高压氧化行为研究引言:镍基耐蚀合金是一类在高温高压环境下表现出良好抗氧化性能的材料。
随着工业技术的发展和运行环境的严苛要求,对这类材料的研究变得越来越重要。
本文将探讨镍基耐蚀合金在高温高压氧化过程中的行为,并介绍一些相关的研究成果。
1. 镍基耐蚀合金的组成与性能镍基耐蚀合金是一种由镍为主要基体元素的合金,通常还包含铬、铝、钛等合金元素。
这些合金元素的添加可以显著提高合金的耐蚀性和力学性能。
镍基耐蚀合金具有优异的高温机械性能和抗氧化性能。
它们能够在高温高压环境下抵抗氧化、腐蚀和应力腐蚀开裂等现象,从而被广泛用于制造航空发动机、石化装置和核能设备等高温高压环境下的关键部件。
2. 高温高压氧化过程分析2.1 氧化行为在高温高压氧化过程中,镍基耐蚀合金中的合金元素会与氧气发生反应,生成一层致密的氧化物覆盖层。
这层氧化物覆盖层可以有效地隔离基体和外界环境,防止进一步的氧化。
2.2 氧化动力学镍基耐蚀合金的高温高压氧化行为受多种因素的影响,包括氧分压、温度、合金成分和表面处理等。
研究表明,氧分压升高和温度升高都会加速氧化反应的进行。
此外,合金中添加的合金元素也会对氧化动力学产生影响,一些合金元素能够增加氧化反应的速率,而另一些元素则具有抑制氧化反应的能力。
3. 高温高压氧化行为的影响因素3.1 合金成分合金成分对镍基耐蚀合金的高温高压氧化行为有着重要影响。
合金中添加的合金元素可以通过形成稳定的氧化物相来提高耐蚀性能,并抑制氧化反应的进行。
例如,铬元素可以形成致密的Cr2O3氧化物覆盖层,有效地阻止氧气的进一步渗透。
而铝元素可以与氧气反应生成Al2O3氧化物层,具有良好的氧化保护性能。
3.2 表面处理表面处理是改善镍基耐蚀合金高温高压氧化性能的重要手段之一。
常用的表面处理方法包括化学镀铝、溅射陶瓷涂层和表面氮化等。
这些表面处理方法能够在合金基体表面形成一层致密的氧化物或涂层,从而提高合金的氧化抗性和耐蚀性能。
ni基高温合金γ'相化学腐
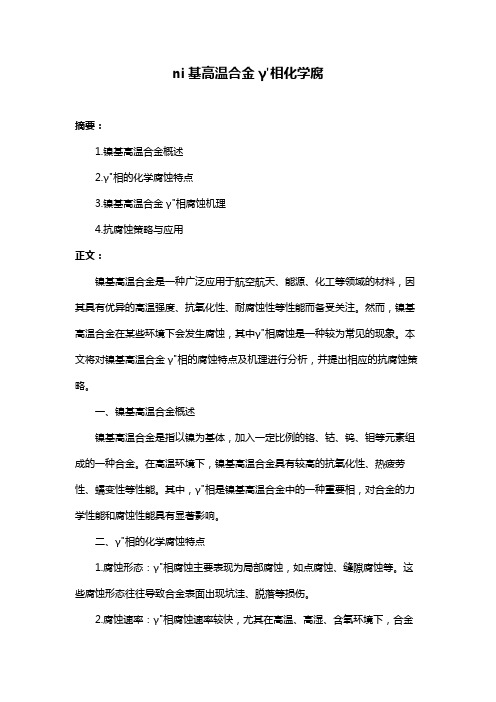
ni基高温合金γ'相化学腐摘要:1.镍基高温合金概述2.γ"相的化学腐蚀特点3.镍基高温合金γ"相腐蚀机理4.抗腐蚀策略与应用正文:镍基高温合金是一种广泛应用于航空航天、能源、化工等领域的材料,因其具有优异的高温强度、抗氧化性、耐腐蚀性等性能而备受关注。
然而,镍基高温合金在某些环境下会发生腐蚀,其中γ"相腐蚀是一种较为常见的现象。
本文将对镍基高温合金γ"相的腐蚀特点及机理进行分析,并提出相应的抗腐蚀策略。
一、镍基高温合金概述镍基高温合金是指以镍为基体,加入一定比例的铬、钴、钨、钼等元素组成的一种合金。
在高温环境下,镍基高温合金具有较高的抗氧化性、热疲劳性、蠕变性等性能。
其中,γ"相是镍基高温合金中的一种重要相,对合金的力学性能和腐蚀性能具有显著影响。
二、γ"相的化学腐蚀特点1.腐蚀形态:γ"相腐蚀主要表现为局部腐蚀,如点腐蚀、缝隙腐蚀等。
这些腐蚀形态往往导致合金表面出现坑洼、脱落等损伤。
2.腐蚀速率:γ"相腐蚀速率较快,尤其在高温、高湿、含氧环境下,合金的腐蚀速率更为明显。
3.腐蚀产物:γ"相腐蚀产物主要为氧化物、硫化物等,这些腐蚀产物会进一步加剧合金的腐蚀。
三、镍基高温合金γ"相腐蚀机理1.电化学腐蚀:镍基高温合金在含有氯离子、硫离子等活性离子环境下,易发生电化学腐蚀。
活性离子在合金表面与合金元素发生反应,产生局部腐蚀。
2.氧化膜破裂:镍基高温合金在高温环境下,表面会形成一层氧化膜保护层。
然而,在某些条件下,氧化膜会发生破裂,导致合金表面暴露,进而发生腐蚀。
3.合金元素扩散:在腐蚀过程中,合金中的铬、钨等元素会向腐蚀前沿扩散,使得腐蚀产物不断生成并堆积,从而加速腐蚀进程。
四、抗腐蚀策略与应用1.合金成分优化:通过调整合金成分,提高镍基高温合金的抗氧化性、耐腐蚀性。
例如,增加铬、钨等元素的含量,以提高合金的耐腐蚀性能。
两种MCrAlY复合涂层在熔融Na2SO4+NaCl中的热腐蚀行为

2 3 — 2 5 2 2 0 — 2 3 0 1 9 — 2 l 2 2 0 — 2 3 0 0 . 2 5 加 . 2 7 O . 2 8 - o . 3 O 1 0 3 Ni C o C r AI Y S i B 8 5 - 8 7
叶片上最常用的涂层之一 , 具有优 良的抗氧化及抗热 3 0× 5 0 X 5 m m3 的N i C r 板, 挂 钩材 料 为 纯铜 丝 , 电 腐蚀性能 ,能够显著提高发动机叶片的使用寿命 1 。 镀工艺如表 4 所示 。在电镀后 , 采取如 同 C 2 涂层同 为提高涂层 中的 A l 、 C r 含量并抑制涂层与基体互扩 样工艺沉积 N i C o C r A 1 Y S i B+ A 1 S i Y涂层。 ( 3 ) 将涂 层试样进行 ( 9 5 0 o C , 保温 6 h ) 真空退 散, 本 文采 用电弧离 子镀 ( A I P ) 及电镀 技术 , 制备 了 含c r 基扩散阻挡层的 M C r A I Y复合涂层 ,分析了普 火扩 散处 理 。 表 1 合金靶材的成分( v v t . %) 通 MC r A 1 Y涂 层 ( 后 面用 C l 表示 ) 、不 含 阻挡 层 的 l C 。 1 c r I A l I S i Y 1 B 1 N i MC r A 1 Y复 合 涂 层 ( 后面用 C 2表 示 ) 和含 C r 基 扩 散 N i C 。 C r A I Y S i B f 3 0 _ 3 4 I 1 8 - 2 2 i 9 一 I 1 l 0 . 5 — 2 0 . 3 - o . 8 1 0 . 0 1 - 0 . 0 3 I 其 阻挡层的 M C r A I Y复合涂层( 后面用 C 3 表示 ) 的微观 A I S i Y l一 1~ l 9 3 . 7 I 4 . 8 1 . 5 l — I 余 组 织 结 构 ,并 研 究 了 三种 涂 层 在 9 0 0℃下 , 在 表2 电弧离子镀 的沉积工艺参数 N a 2 S O 4 + N a C 1 中 的涂 盐 热腐蚀 行 为 。
NiCrBSi超音速火焰喷涂层在水溶液中的腐蚀行为

收稿日期:2002212201;修订日期:2003201219作者简介:赵卫民,女,1970年生,汉族,河北乐亭人,在读博士,讲师,主要从事材料成型及腐蚀防护方面的研究工作NiCrBSi 超音速火焰喷涂层在水溶液中的腐蚀行为赵卫民 王 勇 韩 涛 董立先(石油大学机电工程学院东营257061)摘要:采用高速氧燃料火焰喷涂(H VOF )方法在普通碳钢表面制备了镍基合金涂层,对其组织结构进行了观察,并利用电化学方法对其在水溶液中的腐蚀行为进行研究,探讨H VOF 涂层应用于水介质环境中的可能性.试验结果表明:NiCrBS i 喷涂层在1m ol/L NaOH 溶液中表面能够形成致密钝化膜,耐碱腐蚀的性能最好.涂层在酸性溶液中的腐蚀速度大于在中性315%NaCl 溶液中的腐蚀速度.利用冰醋酸将315%NaCl 溶液的pH 值调整到3,可以提高实验结果的重现性.酸性溶液中,只要被测试表面处于活性溶解状态,腐蚀试验重现性都能满足要求.另外,缺陷越少涂层的耐蚀性越好,减少涂层中的孔隙等缺陷是提高涂层耐蚀性的关键.关键词:H VOF 镍基合金 耐蚀性 显微组织中图分类号:TG 1741442 文献标识码:A 文章编号:100524537(2004)01200372041前言镍基耐蚀合金在酸、碱、盐等各种腐蚀环境中一般都具有良好的耐蚀性能,但由于价格昂贵使其应用受到一定限制.通过表面处理的方法在钢铁等廉价基体上沉积一层镍基合金就能解决经济性与实用性的矛盾,是目前人们所希望采用的一种方法.利用镍基自熔合金进行喷熔是一种合适的制备耐蚀覆盖层的方法,但会使母材过热从而对材料的性能产生不利影响.H VOF 涂层结合强度高、孔隙率低、含氧化物少,在发展耐蚀涂层方面很有前景.有人研究了Ni 和其他金属合金超音速火焰喷涂涂层的耐蚀性,发现涂层致密、组织均匀是必要条件[1].Harvey 等人发现减少喷态Inconel 合金中的总体氧含量在获得耐蚀性接近锻造金属的涂层方面意义重大.近几年,对H VOF 涂层性能的研究很多,但主要集中于耐磨性、抗疲劳和耐高温抗氧化性能,而且研究对象多为WC 2C o 或Cr 3C 22NiCr 等金属陶瓷.也有一些针对涂层在腐蚀介质中的性能报导[2~16],但没有发现关于Ni 2Cr 2B 2Si 系喷涂层腐蚀行为的报导.本文对H VOF 制备的Ni 2Cr 2B 2Si 系喷涂层的组织进行了观察分析,并采用电化学方法研究其在水溶液中的腐蚀行为,探讨H VOF 涂层应用于水介质环境中的可能性.2试验方法基体材料为常用的低碳钢材Q235,试样尺寸为45mm ×30mm ×5mm.喷涂材料为目数150~400的市售镍基自熔合金粉末,其化学成分(%)为:C <011,Cr 510~1010,B 113~116,Si 215~315,Fe <510,Ni 为余量.碳钢试样首先经丙酮清洗去油和喷砂处理,然后采用西安交通大学焊接研究所研制的CH 22000型H VOF 系统制备015mm 左右的涂层.以丙烷作燃料气体,氧气作助燃气体,氮气为送粉气体.在现有设备下采用某一固定工艺规范参数获得的涂层:C 3H 8、O 2和N 2的工作压力分别为0135MPa 、0155MPa 和014MPa ,流量分别为3617L/min 、44213L/min 和22L/min ,送粉速度25g/min ,喷涂距离固定在200mm.为研究孔隙率对涂层耐蚀性能的影响,用同样的镍基粉末在同样的基材上制备氧乙炔火焰喷涂层试样.喷枪为SPH 22型,氧气压力013MPa ,乙炔压力01075MPa ,选用中性偏还原性焰.腐蚀试验用电化学测试方法,用美国Perkin 2Elmer 公司生产的K 0235平板电池.研究电极为镍基涂层试样,非测试面无需封装.测试表面用水砂纸由粗到细打磨到800目,去离子水冲洗干净后丙酮脱脂,干燥后备用.辅助电极为铂铑合金.腐蚀介质采用015m ol/L H 2S O 4和110m ol/L HCl 、315%NaCl 、315%NaCl (冰醋酸酸化到pH 值为3)、110m ol/L NaOH 水溶液.中性溶液中参比电极采用饱和甘汞电极,酸性溶液中采用饱和硫酸亚汞电极,碱性溶液中采用1m ol/L 氧化汞电极.工作电极暴露面积1cm 2.设备为Perkin 2Elmer 公司生产的M283恒电位仪,配合M352腐蚀测试软件.测量开路电位OCP 随时间的变化情况、T afel 极化曲线、动电位极化曲线.E corr ~t 测定时间段为3600s.T afel 极化扫描范围为-250mV ~250mV (相对开路电位OCP ),动电位极化扫描范围为-250mV ~116V (相对开路电位OCP ),扫描速度均为01166mV/s.第24卷第1期2004年2月 中国腐蚀与防护学报Journal of Chinese Society for Corrosion and Protection V ol 124N o 11Feb 12004将锯切试样用树脂进行镶嵌.采用标准金相试样制备程序,对试样横截面进行打磨、抛光、干燥脱脂后腐蚀.用光学显微镜和JS M 25410LV 扫描电镜(SE M )观察喷涂层组织.3结果与分析311组织观察喷涂过程中,每个喷涂粒子经过与基体碰撞后都将发生扁平化而形成一定形态的扁平粒子,涂层呈现由这些扁平粒子互相交错堆叠而形成的组织结构.由于粒子表面存在一定的粗糙度,后续粒子对已沉积的粗糙表面的不完全填充会形成一定量的孔隙.图1是H VOF 涂层和氧乙炔喷涂层抛光后用王水腐蚀后的形貌.可知,两种涂层均呈现典型的喷涂态结构,但H VOF 涂层的粒子扁平化程度高,孔隙较为细小.312HV OF 涂层在酸、碱、盐溶液中的腐蚀行为分别测试H VOF 涂层在015m ol/L H 2S O 4、110m ol/L HCl 、315%NaCl 、315%NaCl (冰醋酸酸化到pH 值为3)、110m ol/L NaOH 水溶液中稳定1h 后的T afel 曲线,测试分析结果见表1.表中ε为标准误差,计算公式为:ε=6Ni =1(x i - x )N2,其中N 为试验重复次数.可知,涂层在碱性溶液中的腐蚀速度最小,酸性溶液的侵蚀性大,而且Cl -比S O 2-4对涂层的侵蚀能力更强.利用冰醋酸将315%NaCl 溶液的pH 值调整到3,可以提高实验结果的重现性,降低实验误差.实验分析表明,涂层在碱性介质中的腐蚀速度之所以最小,是因为其表面能够形成致密的钝化膜所致.图2为H VOF涂层在015m ol/L H 2S O 4、315%NaCl 和110m ol/L NaOH 水溶液中的E corr ~t 曲线.W Stephen T ait 博士指出[17],电位变化的方向显示E D L 适应电解质化学性能的情况,电位上升一般表明金属表面在电解质中能够形成钝化膜保护金属不受进一步腐蚀,电位下降表明金属表面只能形成多孔的腐蚀产物层,能减缓腐蚀,但不能对金属形成有效保护.图3为涂层在015m ol/L H 2S O 4、315%NaCl 和110m ol/L NaOH 水溶液中的动电位极化曲线.与碳钢的极化曲线(图4)做对比可知,涂层在315%NaCl 和110m ol/L NaOH 水溶液中进行极化过程中都存在碳钢所不具备的电流突然增大的拐点,说明两者在自然腐蚀状态下表面都存在钝化Fig.1Microstructure of as -deposited coatings (corroded with aqua regia )(a )H VOF ,(b )oxyacetylene sprayingT able 1Summary of the corrosion parameters obtained from theT afel polarization curvess olution I corr./μA ・cm -2εI corr015m ol/L H 2S O 4811458710684119841231157%110m ol/L HCl 174161591816219165182123%315%NaCl 7135681513419926195412116%315%NaCl(acidified with acetic acid )531744919856123531322178%110m ol/L NaOH1110001473018100179418164%Fig.2E corr 2t behavior of H VOF coatings in various s olutions83中国腐蚀与防护学报第24卷Fig.3P otentiodynamic polarization curves of H VOF coatings in vari2 ous s olutions Fig.4P otentiodynamic polarizaion curves of carbon steel in315% NaCl膜,为自钝化.不过,处于NaOH水溶液中的涂层维钝电流小而且比较稳定,说明表面钝化膜非常致密.处于315%NaCl水溶液中的涂层表面虽然有钝化膜,但比较薄弱,维钝电流随极化电位的升高而增大,钝化区范围也比碱性溶液中的涂层窄的多.镍基涂层在015m ol/L H2S O4溶液中极化时具有典型的活化-钝化转变特征,说明自然腐蚀状态下表面处于活性溶解状态,因此材料的腐蚀电流密度应比处于自钝化状态的大.在酸性环境下,S O2-4、Cl-对涂层的腐蚀速度影响非常大,与各种阴离子对涂层表面状态的影响有关.Cl-穿透性强,较S O2-4破坏形成钝化膜的能力更强,因此涂层在HCl中的腐蚀速度大于在015m ol/L H2S O4中的腐蚀速度.至于加入冰醋酸后可提高涂层在NaCl溶液中实验结果的重现性,主要是由于冰醋酸在其中起了缓冲液的作用.涂层在NaCl溶液中发生腐蚀时,阴极反应为O2+2H2O+4e→4OH-,结果溶液的pH值增大,涂层的表面状态可能会随试验时间的延长发生变化.冰醋酸是弱电离物质,电离能力随溶液pH 值增大而增大,电离出的H+与OH-发生中和反应,从而起到调节和维持溶液原有pH值的目的.另外由表1可知,涂层在1m ol/L NaOH和315%NaCl溶液中T afel区拟合结果重现性不好,这可能是由于此时涂层表面存在钝化膜所致,因为T afel方程适合于活化极化控制的腐蚀过程.可以说,要想提高电化学测试拟合结果的重现性,应该选择能使被测表面处于活性溶解状态的腐蚀介质.313喷涂质量对涂层耐蚀性能的影响将H VOF涂层、氧乙炔喷涂层放在用冰醋酸调整pH值到3的315%NaCl水溶液中,1h后测量试样的T afel极化曲线,拟合结果为H VOF涂层的I corr.值为51186μA/cm2,氧乙炔喷涂层的为74196μA/cm2.由于H VOF喷涂层扁平化程度高,层状组织不明显,孔隙率小于氧乙炔喷涂层,因此喷涂层质量越高耐蚀性越好.涂层中孔隙的存在对涂层耐蚀性有很大的影响,腐蚀性介质在涂层中的扩散速度受涂层孔隙率的影响.涂层中大量孔隙的存在,会缩短扩散通道,加大吸水量,降低涂层耐蚀性.相反,当涂层中孔隙较少时,涂层具有较好的耐蚀性能.控制涂层质量,减少涂层中的孔隙和夹杂等,是提高涂层耐蚀性能的途径.图5是将H VOF涂层、氧乙炔喷涂层放在315% NaCl水溶液中进行动电位强极化,极化后在SE M下观察涂层腐蚀形貌.H VOF涂层的腐蚀沿粉末颗粒间的界面进行,腐蚀后仍然保持了喷涂态的形貌.氧乙炔喷涂层腐蚀后则成片剥落,表面有大量的腐蚀产物.分析认为,这是由于喷涂层颗粒间非冶金结合,其内聚结合力远小于冶金结合力,孔隙和夹杂的存在都也会消弱这种结合力.另外,当涂层中存在贯穿性孔隙,或者在腐蚀介质的作用下形成贯穿性孔隙后,腐蚀介质会渗入涂层内部,在涂层与基体间的界面处发生腐蚀,造成耐蚀性好的涂层失去依托,成片脱落.控制涂层中孔隙的大小和数目,也是防止发生涂层整体失效的重要举措.4结论(1)H VOF涂层与普通氧乙炔火焰喷涂层相比,涂层质量获很大提高.粒子扁平化程度高,孔隙少而小.(2)喷涂层在1m ol/L NaOH溶液中表面能够形成致密钝化膜,耐碱腐蚀的性能最好.涂层在酸性溶液中的腐蚀速度大于在中性315%NaCl溶液中的腐蚀速度.(3)利用冰醋酸将315%NaCl溶液的pH值调整到3,可以提高实验结果的重现性.酸性溶液中,931期赵卫民等:NiCrBS i超音速火焰喷涂层在水溶液中的腐蚀行为 Fig.5SE M image of coatings after potentiodynamic polarization in 315%NaCl (a )H VOF ,(b )oxyacetylene flame spraying只要被测试表面处于活性溶解状态,腐蚀试验重现性都能满足要求.(4)涂层的质量越高,孔隙越少,耐蚀性越好.提高涂层质量,减少涂层中的孔隙等缺陷,是提高涂层耐蚀性的关键.参考文献:[1]Edris H ,M cCartney D G,S turgeon A J.M icrostructural characterizationof high velocity oxy -fuel sprayed coatings of Inconel 625[J ].J.M ater.Sci.,1997:863-872[2]Perry J M ,Neville A ,W ils on V A ,et al.Assessment of the corrosionrates and mechanisms of a WC 2C o 2Cr H VOF coating in static and liquid 2s olid im pingement saline environments [J ].Surf.C oat.T echnol.,2001,137(1):43-51[3]Otsubo F ,Era H ,K ishitake K.Resistance to hydrochloric acid s olution ofFe -Cr 2M o 28P 22C am orphous coatings sprayed by H VOF process [J ].Quarterly J.Jap.W eld.S oc.,2001,19(1):54-59[4]Tuominen J ,Vuoristo P ,M antyl T ,et al.Im proving corrosion propertiesof high 2velocity oxy 2fuel sprayed Inconel 625by using a high 2power con 2tinuous wave neodymium 2doped yttrium aluminum garnet laser [J ].J.Thermal S pray T echnol.,2000:513-519[5]Lee C H ,M in K O.E ffects of heat treatment on the microstructure andproperties of H VOF 2sprayed Ni 2Cr 2W 2M o 2B alloy coatings [J ].Surf.C oat.T echnol.,2000,10:49-57[6]R odriguez M ,S taia M ,G il L ,et al.E ffect of heat treatment on propertiesof nickel hard surface alloy deposited by H VOF[J ].Surf.Eng.,2000:415-420[7]Ji G angchang ,W ang Y uyue ,Li Changjiu ,et al.Erosion of high velocityoxy 2fuel sprayed Cr 3C 22NiCr coatings[J ].J.X i ’an Jiaotong University ,2000,34(5):59-63[8]Natishan P M ,Lawrence S H ,F oster R L ,et al.Salt fog corrosion behav 2ior of high 2velocity oxygen 2fuel thermal spray coatings com pared to elec 2trodeposited hard chromium[J ].Surf.C oat.T echnol.,2000:218-223[9]G il Linda ,M ariana H S taia.M icrostructure and properties of H VOF ther 2mal sprayed NiWCrBS i coatings[J ].Surf.C oat.T echnol.,1999:423-429[10]Dent A H ,H orlock A J ,M cCartney D G,et al.C orrosion behavior andmicrostructure of high 2velocity oxy 2fuel sprayed nickel 2base am orphous/nanocrystalline coatings [J ].J.Thermal S pray T echnol.,1999,8(3):399-404[11]Hazan J ,C oddet Ch.C orrosion behaviour in low concentrated sulfate s o 2lution of thermal spray (H VOF )zinc coatings on steel[J ].M ater.Sci.F orum ,1998:719-728[12]H ofman R ,Vreijling M P W ,Ferrari G M ,et al.E lectrochemical meth 2ods for characterization of thermal spray corrosion resistant stainless steel coatings[J ].M ater.Sci.F orum ,1998:641-654[13]W ang B Q.Dependence of erosion 2corrosion on carbide/metal matrixproportion for H VOF Cr 3C 22NiCr coatings [J ].Surf.Eng.,1998,14(2):165-169[14]Neville A ,H odgkiess T.C orrosion behavior and microstructure of tw othermal spray coatings[J ].Surf.Eng.,1996,12(4):303-312[15]K ishitake K,Era H ,Otsubo F.Thermal 2sprayed Fe 210Cr 213P 27C am or 2phous coatings possessing excellent corrosion resistance [J ].J.Thermal S pray T echnol.,1996,5(4):476-482[16]Zhao L ,Lugscheider E ,Fischer A ,et al.Thermal spraying of a high ni 2trogen duplex austenitic 2ferritic steel [J ].Surf.C oat.T echnol.,2001:208-215[17]W illiam S tephen T ait.An Introduction to E lectrochemical C orrosionT esting for Practicing Engineers and Scientists[M].Racine ,W isconsin :Pairodacs Publications ,1994:39STU DY ON THE CORR OSION BEHAVIOR OF HV OF SPRAYE D NiCrBSi COATING SZH AO Weimin ,W ANG Y ong ,H AN T ao ,DONGLixian(Mechanical Department ,Univer sity o f Petroleum ,Dongying 257061)Abstract :The nickel 2base alloy powder was sprayed to a steel substrate using H VOF ,and the corrosion resistance of thecoatings was evaluated using electrochemical tests ,s o as to offer an experimental basis to expand a promising applied field of H VOF in aqueous medium.The results show that NiCrBSi coating has excellent corrosion resistance in alkali s olution ,because the surface can keep in a self 2passivation condition.The corrosion current of the coating in s our s olutions is biggerthan that in 3.5%NaCl ,and the corrosion caused by Cl -is serious than that caused by S O 2-4.The reproducibility of the test results can be im proved when the 3.5%NaCl aqueous s olution is acidified with acetic acid ,and using a corrosive medium that keeps the tested surface in an active 2diss olved condition ,which can get the same purpose.The less the de 2fects in the coating ,the better the corrosion resistance.Im proving the quality and reducing the porosity of coatings are the key to get the coatings with high corrosion resistance.K ey w ords :H VOF ,nickel 2base alloy ,corrosion resistance ,microstructure04中国腐蚀与防护学报第24卷。
三种镍基单晶高温合金的热腐蚀行为研究
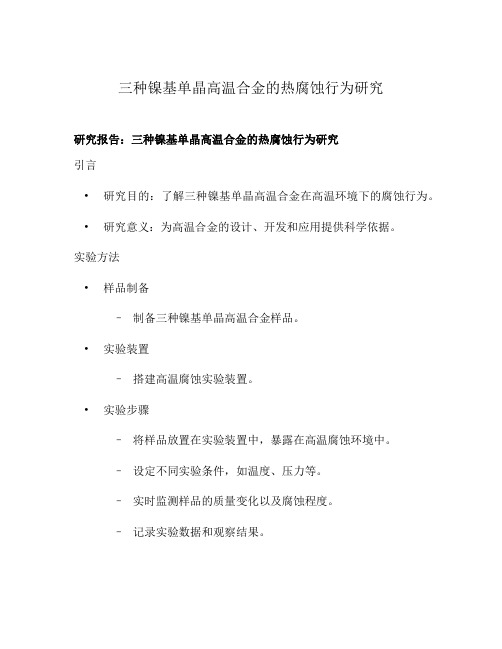
三种镍基单晶高温合金的热腐蚀行为研究研究报告:三种镍基单晶高温合金的热腐蚀行为研究引言•研究目的:了解三种镍基单晶高温合金在高温环境下的腐蚀行为。
•研究意义:为高温合金的设计、开发和应用提供科学依据。
实验方法•样品制备–制备三种镍基单晶高温合金样品。
•实验装置–搭建高温腐蚀实验装置。
•实验步骤–将样品放置在实验装置中,暴露在高温腐蚀环境中。
–设定不同实验条件,如温度、压力等。
–实时监测样品的质量变化以及腐蚀程度。
–记录实验数据和观察结果。
实验结果•腐蚀行为分析–对三种镍基单晶高温合金的腐蚀速率进行比较。
–观察腐蚀表面的变化,如形成的氧化物层厚度、裂纹等。
–分析不同实验条件对腐蚀行为的影响。
结论•三种镍基单晶高温合金的热腐蚀行为研究得出以下结论:1.实验条件不同对腐蚀速率有显著影响。
2.氧化物层厚度与腐蚀程度呈正相关关系。
3.样品表面出现裂纹是腐蚀的严重程度指标之一。
•结果分析可以为镍基单晶高温合金的设计和应用提供指导。
展望•对于未来的研究方向和可能的改进进行探讨。
•基于本研究结果的应用前景展望。
注:本报告使用Markdown格式撰写,不包含HTML字符、网址、图片和电话号码等内容。
引言•研究目的:了解三种镍基单晶高温合金在高温环境下的热腐蚀行为,为提高材料的腐蚀抗性提供基础数据。
•研究意义:高温合金广泛用于航空、航天、能源等领域,而高温腐蚀是制约其应用的重要问题,因此对其热腐蚀行为的研究具有重要的应用价值和科学意义。
实验方法•样品制备–选择三种镍基单晶高温合金作为研究对象。
–使用先进的制备技术,制备具有一致晶粒结构和成分的样品。
•实验装置–设计和搭建高温腐蚀实验装置,确保温度、压力和气氛等参数的准确控制。
•实验步骤–将样品放置在实验装置中,暴露在高温腐蚀环境中。
–采用周期性腐蚀测试方法,实时监测样品的质量损失情况。
–使用扫描电子显微镜(SEM)观察腐蚀表面的形貌,分析氧化物层的厚度和结构。
–利用X射线衍射(XRD)技术分析样品的相变和晶格结构的变化。
镍基高温合金溅射NiCrALY涂层盐腐蚀行为
第一章绪论1.1. 铸造高温合金的发展自从20世纪40年代初期第一台航空喷气发动机采用第一个铸造涡轮工作叶片以来,铸造高温合金的发展经历了一段曲折而又辉煌的历程。
半个世纪以来,航空发动机涡轮前温度从40年代的730℃提高到90年代的1677℃,推重比从大约3提高到10,这一巨大进展固然离不开先进的设计思想、精湛的制造工艺以及有效的防护涂层,但是高性能的铸造高压涡轮叶片合金的应用更是功不可没。
在这世纪之初回顾铸造高温合金发展的历程,不能不提到如下几件使人难忘的重大事件[1]。
美国GE公司为其J33航空发动机选用了钴基合金HS 21制作涡轮工作叶片,代替原先用的锻造高温合金Hasteelloy B。
,从此开创了使用铸造高温合金工作叶片的历史。
到60年代初,由于发动机工作温度提高,要求叶片合金的热强性能进一步提高,使高温合金合金化程度不断提高,于是出现了复杂合金化与压力加工困难的矛盾,并且越来越尖锐,加之这一时期铸造技术进步,使合金性能和叶片质量提高,出现了大批复杂合金化的高性能合金,使铸造高温合金叶片的应用越来越广泛。
我国第一个铸造高温合金是北京航空材料研究院于1958年研制的K401合金,用作WP6发动机的导向叶片。
我国第一个铸造涡轮工作叶片是60年代初在黎明发动机厂研制的WP6S发动机一级涡轮叶片(K406合金)。
70年代中期,由中科院金属研究所研制成功的K417镍基铸造高温合金制作涡轮叶片用于WP-7型发动机,投入生产,成为我国最先服役于航线的铸造涡轮叶片合金。
70年代之后,由于定向凝固和单晶合金的出现,使得所有国家的先进新型发动机几乎无一例外地选用铸造高温合金制作最高温区工作的叶片,从此确立了铸造高温合金叶片的稳固地位[2]。
1.2镍基高温合金的发展早在60年代,国内外就开始对从高温合金诞生的金属间化合物(Ni3Al、NiAl、Ti3Al、TiAl)为基的合金进行了广泛的研究,因为这些化合物具有诱人的低密度、高模量和良好的抗氧化性,认为是有发展前景的替换材料。
NiCrAlY涂层在1050℃下的微观结构演变及抗氧化性能研究
NiCrAlY涂层在1050℃下的微观结构演变及抗氧化性能研究吴瑞祥;杨尚琴;杨洪志【期刊名称】《湘潭大学学报(自然科学版)》【年(卷),期】2024(46)2【摘要】为了进一步研究NiCrAlY涂层高温氧化过程中的微观结构演变,分析涂层结构与抗氧化性能之间的内在作用机理,为新型耐高温长寿命涂层的研制提供理论与数据参考.采用电弧离子镀技术,在镍基高温合金基体表面沉积NiCrAlY涂层,并将真空热处理后的涂层在1050℃进行恒温氧化200 h后,通过扫描电子显微镜、X射线衍射和X射线能谱仪等检测手段,对NiCrAlY涂层在氧化过程中的微观结构演变和抗高温氧化机理进行研究.研究结果表明,真空热处理能够有效改善涂层的组织结构和均匀化涂层成分.涂层氧化过程中形成的α-Al_(2)O_(3)和Cr_(2)O_(3)对涂层具有良好的防护作用,能够降低涂层的氧化速度,抑制NiCr_(2)O_(4)尖晶石有害相的形成.氧化过程的持续进行,使得涂层中近氧化层侧的Al浓度降低,导致非保护性氧化物的形成,使得氧化层发生剥落,涂层的抗氧化性能降低,氧化物层出现分层现象,由疏松较厚的外氧化层和致密较薄的内氧化物层组成.涂层增重随氧化时间的变化曲线遵循抛物线规律,恒温氧化过程中涂层的平均氧化速率为0.0856 g·m^(-2)·h^(-1).该文对深入理解涂层的抗高温氧化机理及新型涂层的研制提供了理论与实验数据参考.【总页数】8页(P102-109)【作者】吴瑞祥;杨尚琴;杨洪志【作者单位】国家建筑城建机械质量监督检验中心;湘潭大学材料科学与工程学院【正文语种】中文【中图分类】TG15【相关文献】1.NiCrAlY涂层抗氧化性及氧化过程中的微观结构演变2.不同冷热循环条件下NiCrAlY涂层体系的微观组织演变规律及失效机理3.两种NiCrAlY涂层1050℃恒温抗氧化性能4.微观组织结构对NiCrAlY涂层抗高温氧化性能的影响因版权原因,仅展示原文概要,查看原文内容请购买。
镍基耐蚀合金的高温环境腐蚀行为研究
镍基耐蚀合金的高温环境腐蚀行为研究镍基耐蚀合金是一类具有优良耐蚀性能的材料,广泛应用于高温环境中,例如航空发动机、石化装置、核电站等领域。
这些合金在高温、高压和腐蚀性介质的作用下,能够保持其力学性能和抗腐蚀性能,发挥重要作用。
高温环境下腐蚀是一种复杂的化学过程,涉及物质的相互作用、传质和电化学反应等多个方面。
了解镍基耐蚀合金在高温环境中的腐蚀行为对于材料的选择、设计和改进具有重要意义。
本文将对镍基耐蚀合金在高温环境中的腐蚀行为进行研究,并探讨其机理和影响因素。
首先,镍基耐蚀合金在高温环境中的腐蚀行为主要包括氧化腐蚀和热腐蚀两个方面。
氧化腐蚀是指合金表面与氧气反应产生金属氧化物的过程,如表面形成的钝化层。
热腐蚀是指合金在高温条件下与腐蚀性介质接触而引起的化学反应,如金属溶解、金属与气体或液体产生反应等。
其次,镍基耐蚀合金在高温环境中的腐蚀行为受到多种因素的影响。
首先是介质的性质,包括温度、氧气分压、酸碱度等。
高温环境中的腐蚀介质通常包括氧气、水蒸气、硫化物、氟化物等,它们对合金的腐蚀有着不同的作用机制。
其次是合金的化学成分和微观结构。
镍基耐蚀合金通常含有大量的合金元素,如铬、钼、钛等,这些元素能够增强合金的耐蚀性能,但过量的合金元素也可能导致合金的不稳定性。
此外,合金的晶体结构、相变、晶界和缺陷等微观结构也对腐蚀行为有一定影响。
针对以上影响因素,研究者们采用了多种方法来研究镍基耐蚀合金在高温环境中的腐蚀行为。
一种常用的方法是电化学测试,如腐蚀电位和极化曲线测量,可以评估合金的腐蚀倾向和速率。
此外,还可以采用材料表面和截面的观察方法,如扫描电子显微镜(SEM)、能量散射X射线光谱(EDX)等,来研究合金的表面形貌、元素分布和相变等。
另外,还可以利用材料力学性能测试、质量损失测量等方法综合评估合金在高温环境中的腐蚀行为。
在研究中,发现了一些常见的镍基耐蚀合金的高温环境腐蚀行为。
例如,针对镍基耐蚀合金在含氯环境中的腐蚀行为研究表明,合金中的铬元素能够与氯离子结合形成稳定的氯化物,从而有效抑制了氯离子对合金的腐蚀作用。
NiCrAlY涂层与镍基单晶高温合金基体的互扩散行为
第51卷第11期2020年11月中南大学学报(自然科学版)Journal of Central South University (Science and Technology)V ol.51No.11Nov.2020NiCrAlY 涂层与镍基单晶高温合金基体的互扩散行为邓鹏1,2,荔琴3,刘英坤1,2,尹斌2,石倩2,张利军3,杨焜2,邓春明2,李风1(1.广东工业大学材料与能源学院,广东广州,510006;2.广东省科学院新材料研究所,现代材料表面工程技术国家工程实验室,广东省现代表面工程技术重点实验室,广东广州,510651;3.中南大学粉末冶金国家重点实验室,湖南长沙,410083)摘要:采用多弧离子镀技术在镍基单晶高温合金基体表面制备NiCrAlY 涂层,并利用XRD 、SEM/EDS 、EPMA 等表征方法研究试样在1100℃热暴露100h 过程中涂层/基体之间互扩散引发的微观结构演变与各组元的成分分布。
基于所测定的各组元成分−距离曲线,采用基于数值回归方法框架的HitDIC 软件获得各组元沿整个扩散通道的主互扩散系数。
研究结果表明:在1100℃热暴露初期,NiCrAlY 涂层和基体界面处形成了互扩散区(IDZ)和二次反应区(SRZ),而且IDZ 和SRZ 的厚度随热暴露时间不断增大;在SRZ 中析出的颗粒状和针状拓扑密堆相(TCP)主要由Re ,Cr ,W 等元素组成,且与合金基体界面成特定角度;在热暴露过程中NiCrAlY 涂层与基体间主要发生Cr 元素向基体的内扩散和Ni ,Al ,Ta ,Re ,W 等元素由基体向涂层的外扩散,且随着热暴露时间的延长,涂层与基体界面处元素的浓度梯度逐步减小;采用数值回归法获得的模拟结果与实测成分−距离曲线吻合较好,且Al ,Co 和Cr 成分变化对所得各组元主互扩散系数的影响较大。
关键词:NiCrAlY 涂层;镍基单晶高温合金;互扩散;热暴露;数值回归法中图分类号:TG174.44文献标志码:A开放科学(资源服务)标识码(OSID)文章编号:1672-7207(2020)11-3187-12Interdiffusion behavior between NiCrAlY coating and Ni-basedsingle-crystal superalloyDENG Peng 1,2,LI Qin 3,LIU Yingkun 1,2,YIN Bin 2,SHI Qian 2,ZHANG Lijun 3,YANG Kun 2,DENG Chunming 2,LI Feng 1(1.School of Materials and Energy,Guangdong University of Technology,Guangzhou 510006,China;2.Institute of New Materials,Guangdong Academy of Sciences,National Engineering Laboratory for Modern Materials Surface Engineering Technology,The key Lab of Guangdong for Modern Surface EngineeringDOI:10.11817/j.issn.1672-7207.2020.11.022收稿日期:2020−08−25;修回日期:2020−09−22基金项目(Foundation item):广东省重点领域研发计划项目(2019B010936001);广州市重点领域研发计划项目(202007020008);广东省科学院项目(2020GDASYL-20200104028,2020GDASYL-20200402005);广东省基础与应用基础研究基金资助项目(2020A1515010948)(Project(2019B010936001)supported by Research and Development Plan of Key Areas in Guangdong Province;Project(202007020008)supported by the Research and Development Project in Key Areas of Guangzhou;Projects (2020GDASYL-20200104028,2020GDASYL-20200402005)supported by Guangdong Academy of Sciences;Project (2020A1515010948)supported by the Guang dong Basic and Applied Basic Research Foundation)通信作者:邓春明,博士,教授级高级工程师,从事热喷涂研究;E-mail :**********************第51卷中南大学学报(自然科学版)Technology,Guangzhou510651,China;3.State Key Laboratory of Powder Metallurgy,Central South University,Changsha410083,China) Abstract:A NiCrAlY coating was deposited on Ni-based single crystal superalloy by arc ion plating technology. The microstructure evolution and element interdiffusion behavior caused by the interdiffusion between the coating and substrate during thermal exposure at1100℃for up to100h were characterized by X-ray diffraction(XRD), scanning electron microscopy(SEM)equipped with energy dispersive spectroscopy(EDS),electron probe micro-analyze(EPMA),and so on.Based on the experimental composition profiles,the main interdiffusion coefficients of each composition along the entire diffusion channel were obtained by HitDIC(high-throughput determination of interdiffusion coefficients)software,which has been developed in the framework of numerical inverse method. The results show that the interdiffusion zone(IDZ)and second reaction zone(SRZ)are formed at the interface between coating and substrate at the initial stage of thermal exposure at1100℃,and both widths increase withthe extension of thermal exposure time.The precipitated granular and needle-like topologically close-packed(TCP) phases in the SRZ are inclined by a certain angle to the coating/substrate interface and are mainly composed of Re,Cr and W etc.During the thermal exposure process,the inward diffusion of Cr from the coating to the substrate are accompanied with the outward diffusion of Ni,Al,Ta,Re and W caused the decrease of concentration gradient of components at the interface of coating/substrate.Besides,the numerical inverse method is conducted,and the simulation results are in good agreement with the experiment composition profiles.The main interdiffusion coefficients of each composition are mainly affected by Al,Co and Cr components.Key words:NiCrAlY coating;Ni-based single-crystal superalloy;interdiffusion;thermal exposure;numerical inverse method单晶高温合金具备优异的抗蠕变、抗疲劳和抗热腐蚀性能,因而广泛用于制造航空发动机和燃气轮机叶片[1−2]。
- 1、下载文档前请自行甄别文档内容的完整性,平台不提供额外的编辑、内容补充、找答案等附加服务。
- 2、"仅部分预览"的文档,不可在线预览部分如存在完整性等问题,可反馈申请退款(可完整预览的文档不适用该条件!)。
- 3、如文档侵犯您的权益,请联系客服反馈,我们会尽快为您处理(人工客服工作时间:9:00-18:30)。
第一章绪论
1.1. 铸造高温合金的发展
自从20世纪40年代初期第一台航空喷气发动机采用第一个铸造涡轮工作叶片以来,铸造高温合金的发展经历了一段曲折而又辉煌的历程。
半个世纪以来,航空发动机涡轮前温度从40年代的730℃提高到90年代的1677℃,推重比从大约3提高到10,这一巨大进展固然离不开先进的设计思想、精湛的制造工艺以及有效的防护涂层,但是高性能的铸造高压涡轮叶片合金的应用更是功不可没。
在这世纪之初回顾铸造高温合金发展的历程,不能不提到如下几件使人难忘的重大事件[1]。
美国GE公司为其J33航空发动机选用了钴基合金HS 21制作涡轮工作叶片,代替原先用的锻造高温合金Hasteelloy B。
,从此开创了使用铸造高温合金工作叶片的历史。
到60年代初,由于发动机工作温度提高,要求叶片合金的热强性能进一步提高,使高温合金合金化程度不断提高,于是出现了复杂合金化与压力加工困难的矛盾,并且越来越尖锐,加之这一时期铸造技术进步,使合金性能和叶片质量提高,出现了大批复杂合金化的高性能合金,使铸造高温合金叶片的应用越来越广泛。
我国第一个铸造高温合金是北京航空材料研究院于1958年研制的K401合金,用作WP6发动机的导向叶片。
我国第一个铸造涡轮工作叶片是60年代初在黎明发动机厂研制的WP6S发动机一级涡轮叶片(K406合金)。
70年代中期,由中科院金属研究所研制成功的K417镍基铸造高温合金制作涡轮叶片用于WP-7型发动机,投入生产,成为我国最先服役于航线的铸造涡轮叶片合金。
70年代之后,由于定向凝固和单晶合金的出现,使得所有国家的先进新型发动机几乎无一例外地选用铸造高温合金制作最高温区工作的叶片,从此确立了铸造高温合金叶片的稳固地位[2]。
1.2镍基高温合金的发展
早在60年代,国内外就开始对从高温合金诞生的金属间化合物(Ni3Al、NiAl、Ti3Al、TiAl)为基的合金进行了广泛的研究,因为这些化合物具有诱人的低密度、高模量和良好的抗氧化性,认为是有发展前景的替换材料。
70年代中期,美国Howmet公司发展了高温合金细晶铸造法,从而在合金凝固过程的晶粒控制方面
又走出了新路子。
最先发展的是控制热参数的Grain X法,然后又发展出机械搅拌的Microcast X法,所得到的铸件晶粒尺寸可达ASTMNo.35(0.125~0.0625mm)。
加上热等静压(HIP)处理和其后热处理,使合金的中、低温拉伸、持久、疲劳性能大为改善,尤其是低周疲劳明显提高。
在航天工业中,发动机工作效率的不断改进与增加发动机的温度热容同步进行,航空发动机的发展历史,可以简单的描述为不断提高航空发动机推力和涡轮前进口温度的历史。
发动机每升高5℃,可增加发动机功率1.3%和热效率0.4%。
50年代典型的发动机为JT3D推力为7450kg,涡轮前进口温度为889℃,70年代F100发动机的推力为11340kg,涡轮前进口温度为1310℃,而80年代的一些有特色发动机涡轮前进口温度已高达1430℃[3]。
发动机工作效率的不断提高是伴随着发动机温度容量的不断提高而提高,因而要求发动机叶片材料有更高的承温能力。
镍基高温合金经历了近60年的发展历程,已经研制出一系列具有优良性能的高温合金,例如:耐腐蚀、抗高温蠕变、高屈服强度和断裂韧性等高温合金,几乎所有合金都是在Ni-Al-Cr-Ti系沉淀强化型合金的基础上发展进化而来的[4]。
设法消除与应力轴垂直的横向晶界,可较大幅度提高合金的高温力学性能。
基于这种想法发展了定向凝固技术,它的出现,不仅提高了高温合金的蠕变性能,而且也极大的提高了热疲劳性能[5]。
人们在研究定向凝固技术的同时,也在研究另一种新型的技术,制单晶技术。
单晶的特点是无晶界,不存在高温晶界弱化、纵箱境界裂纹等问题[6,7]。
而且单晶的合金化特点是不需要加入境界强化元素,合金成分简单,还能大大提高了合金的初熔温度,可采用更高的固溶处理温度,有效的调整了γ′强化相的形貌、体积分数和尺寸分布,与铸造和定向凝固合金比较,单晶合金具有更高的抗热疲劳、机械疲劳、抗氧化及抗蠕变性能,显著提高了高温合金的工作温度,提高了工件的承温能力,可以使工件在高的温度下正常工作。
因而,随着航空航天工业的迅猛发展,单晶合金必将取代现有的合金,成为航天发动机的叶片的最佳使用材料[8]。
1.3高温腐蚀
金属材料如果暴露在高温空气气氛中,几乎都会发生氧化,在某些情况下甚至发生氮化,引起不良后果。
所以形成的氧化膜的性质决定了合金抗氧化/氮化好坏的程度。
如果在金属表面能够形成一层稳定、连续、致密、生长速度慢,不
易开裂、粘附性好的氧化膜可以起到很好的保护作用。
一般情况下,形成Cr 2 O3、Al 2 O3 、SiO2则能够满足金属抗高温氧化腐蚀的要求。
在高温下使用最广泛的是能形成Cr 2 O3膜的高温合金,主要是镍、钴、铁基的高温合金和高温钛合金。
Ni基高温合金根据高温氧化环境中生成的保护膜的类型不同,可分为Cr 2 O3型和Al2O3型两类。
镍基合金属于前一类。
在实际应用条件下,金属高温结构材料既要具备足够的力学性能,又要具有优良的抗高温腐蚀性能。
但对于同一合金,这两方面的性能相互矛盾,不可能同时得到解决。
一个非常有效的途径就是在合金表面施加防护涂层,这既可以提高合金抗高温腐蚀性能,又可以保持合金的力学性能在许可的范围内[9]。
因此,高温防护涂层从上个世纪五十年代初开始一直是航空航天等高温领域研究的热点。
1.4高温防护涂层
高温防护涂层按组成涂层的材料可分为金属高温防护涂层和非金属高温防护涂层两大类。
这里主要介绍Ni基高温合金的防护涂层。
金属防护涂层通过金属在服役中涂层表面形成稳定的保护性氧化膜,起着保护基体合金免受高温氧化和腐蚀的作用。
防护涂层分为热扩散涂层(Diffusion Coating)、包覆涂层(Overlay Coating)、热障涂层(Thermal Barrier Coating)。
1.4.1 NiCrAlY涂层
1.4.1热扩散涂层
热扩散涂层(或称渗铝涂层),是通过基体接触并与其内确定元素反应从而改变了基体外层形成的涂层。
这类涂层是基于镍、钴、铁基合金经扩散渗铝过程而在基体表面形成金属间化合物来提高合金的抗氧化性。
最常见的扩散元素铝、铬、硅等。
其中以铝化物涂层应用最广,占整个高温防护涂层的90%。
最早在高温合金上采用的铝化物涂层是由Van Aller提出并利用粉末包装技术制备的[10]。
之后在20世纪50年代发展起来的主要渗铝方法有:热浸渗铝、料浆渗铝、气体渗铝、喷镀渗铝、电泳渗铝、电解渗铝、化学气相沉积(简称CVD)等。
其中以固体粉末渗铝工艺最为成熟。
渗铝涂层具有优良的抗氧化性能,但它仍存在很多缺点。
例如,涂层脆性大,易开裂剥落,退化速度快,耐热腐蚀能力差等。
为改善单渗铝涂层的性能,在渗铝层中加入Cr、Si、Pt、Pd等元素形成改性的铝化物涂层,达到改善其性能的。