密封圈过程流程图
密封圈的设计步骤
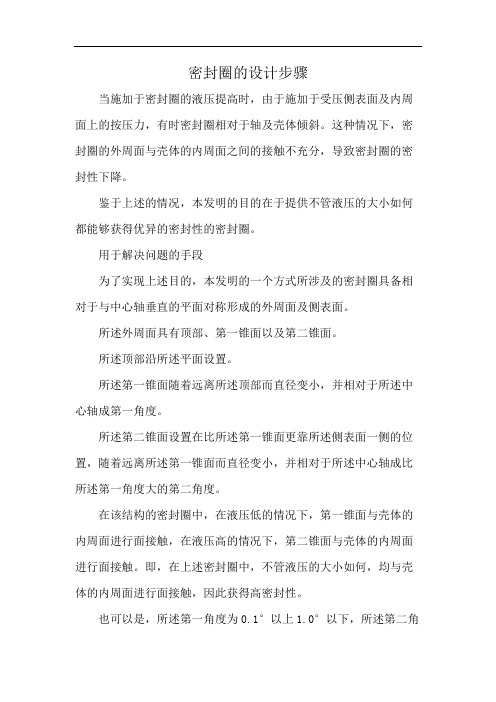
密封圈的设计步骤当施加于密封圈的液压提高时,由于施加于受压侧表面及内周面上的按压力,有时密封圈相对于轴及壳体倾斜。
这种情况下,密封圈的外周面与壳体的内周面之间的接触不充分,导致密封圈的密封性下降。
鉴于上述的情况,本发明的目的在于提供不管液压的大小如何都能够获得优异的密封性的密封圈。
用于解决问题的手段为了实现上述目的,本发明的一个方式所涉及的密封圈具备相对于与中心轴垂直的平面对称形成的外周面及侧表面。
所述外周面具有顶部、第一锥面以及第二锥面。
所述顶部沿所述平面设置。
所述第一锥面随着远离所述顶部而直径变小,并相对于所述中心轴成第一角度。
所述第二锥面设置在比所述第一锥面更靠所述侧表面一侧的位置,随着远离所述第一锥面而直径变小,并相对于所述中心轴成比所述第一角度大的第二角度。
在该结构的密封圈中,在液压低的情况下,第一锥面与壳体的内周面进行面接触,在液压高的情况下,第二锥面与壳体的内周面进行面接触。
即,在上述密封圈中,不管液压的大小如何,均与壳体的内周面进行面接触,因此获得高密封性。
也可以是,所述第一角度为0.1°以上1.0°以下,所述第二角度为1.0°以上5.0°以下。
在该结构的密封圈中,第一锥面和第二锥面将更确切地与壳体的内周面进行面接触,因此获得特别高的密封性。
也可以是,所述第二锥面的所述中心轴的方向上的尺寸比所述第一锥面的所述中心轴的方向上的尺寸大。
在该结构的密封圈中,第二锥面的面积大、即第二锥面与壳体的内周面之间的接触面的面积增大,因此,在液压高的情况下,获得更稳定的密封性。
也可以是,所述密封圈还具备连接所述外周面和所述侧表面的倒圆角面。
通过该结构,所述密封圈能够相对于轴和壳体顺畅地滑动。
也可以是,所述侧表面随着远离所述外周面而接近所述平面。
也可以是,所述侧表面相对于所述平面成比所述第二角度大的第三角度。
通过该结构,所述密封圈的侧表面难以与槽部的侧表面进行面接触。
油封密封及工作原理PPT课件

安装速度不能太快,否则会 使油封外径变形。 建议:安装速度 v<1200mm/min
油封安装到位后,应对油封 保持一段时间的压力,以减 少或避免油封的回弹。
5.2主要的油封检测工具
投影仪:油封全尺寸检测,主要用于模腔认证 塞规:用于检测主唇口尺寸(如图) 比较仪:用于检测油封外径 卡尺:用于检测油封高度 弹簧拉力试验机:检测弹簧拉伸
应力 气密性检测:检测油封气密性,
主要用于发动机油封 5.3 油封外观检测标准简介
6.油封漏油的原因及预防
FPM:在温度-30 ℃ ~ 200℃,转速 6000rpm,绝大多数的车用润滑油情况 下;
3.油封的制造及注意事项
橡胶油封加工是按如下工艺流程进行的: 产品制造过程中的每个工序由多功能小组进行PFMEA分
析,并中制定控制计划对影响产品功能的过程特性加以 控制,使产品特性得以满足. 油封制造过程应注意事项:
4.1.3对偏心的要求 轴—座偏心是影响油封漏油的重要因素 轴—座偏心示意图 对偏心量的要求:
建议e≦0.15mm 任何程度的轴的偏心度 都影响密封性能并逐渐地 增加由于磨损和弹性体的 递增的硬化所引起的疲劳 破坏的机会.
对轴跳动的要求
轴跳动量是影响 油封漏油的重要 因素
轴跳动示意图 对轴跳动的要求:
建议:保压时间t=5秒
油封安装常用方法
油封装配现场情况:
1、与油封唇口相接触的凸缘生锈 倒角为尖角
2、现场环境差 工位器具清洁度差 各种零件混装
3、油封涂油不均匀 4、压配工装有残渣
倒角为尖角并有毛刺
密封圈半自动组装

密封圈半自动组装
密封圈的半自动组装通常包括以下步骤:
1. 准备工作:收集密封圈的组装所需的材料和工具,确保工作台面和设备清洁整齐。
2. 预处理密封圈:检查密封圈的质量,确保没有损坏或缺陷。
如果有问题,将其从组装过程中排除。
3. 将密封圈放置在合适的工装上:使用工装或夹具将密封圈固定在合适位置,以便进行下一步操作。
4. 涂抹润滑剂:如果需要,在密封圈和安装部件之间涂抹一层适当的润滑剂,以减少摩擦并确保更好的密封效果。
5. 安装密封圈:将已涂抹润滑剂的密封圈放置于要密封的部件上。
根据需要,可以使用手动工具或半自动设备来完成此步骤。
确保密封圈正确地安装在其预定的位置上。
6. 检查安装质量:确认密封圈已正确安装并且没有任何缺陷。
必要时,可以进行目视检查或使用测试设备来验证安装质量。
7. 清理和整理工作区:在组装完成后,清理并整理工作区,保持材料和工具的有序。
需要注意的是,半自动组装过程中是否还涉及其他步骤,以及具体的组装方法和工装设备,可能会因密封圈的类型和规格而
有所不同。
因此,在实际操作中,需要根据具体的情况进行调整和操作。
胶辊胶圈工艺流程图

胶辊、胶圈工艺示意图
一、胶辊
1、处理辊(84,80-1等)
塑炼(15分钟/车,90度投料)→过滤→明胶→混炼(两包一折,停放8小时以上;1mm 以下四小时一卷)→回练(停放6小时以上;1mm以上四包一卷)→过滤→加硫(静电;两包一折;1mm以下四包一卷)→停放8小时以上,待用
2、不处理辊(60-80B等)
塑炼(第一天;硫磺母胶;15分钟/车;6小时后第二次塑炼)→过滤(第二天;称重及混炼)→混炼(四包一卷;停放6小时后再回练)→吃锌(第三天;过滤后;四包一卷;停放6小时后再回练)→压出(第四天;只限两层堆放;停放2-4小时后)→成型→待用
二、胶圈
101-107圈
塑炼(15分钟/车,90度投料)→热练(165℃±5℃;透明,无白花,不发黄;0.5mm以下出片)→混炼(两包一折;1mm以下四包一卷)→回练(停放8小时后再回练;1mm以下六包一卷)→待用
三、要求
1、所有堆放在生产现场的塑炼胶、皮辊胶、皮圈胶及机头胶都必须标明胶种、型号、日期
及班次。
2、在接到“计划任务书”后,一定要在弄懂工艺的前提下再实施作业。
做到“不懂不开车”,
以防损失。
3、以上内容希各操作工自行对照,整改。
严格自觉遵守工艺,严防“自由操作”倾向。
密封件定位套工艺过程卡

机械加工工艺过程卡片产品型号零件图号产品名称密封件定位套零件名称共 2 页第 1 页材料牌号HT200毛坯种类铸造毛坯外形尺寸227mmX265mm每毛坯件数 1 每台件数 1 备注工序号工名序称工序内容车间工段设备工艺装备工时准终单件1 备料2 铸造铸件各部留加工余量7mm3 清砂清砂4 热处理人工时效处理5 粗车夹工件右端外圆,照顾铸件壁厚均匀,车内径各部尺寸以及左端面和φ260外圆,留加工余量2mm,法兰盘壁厚23mm,其余各部留余量3mmCA61406 粗车倒头,以内径定位装夹工件,法兰盘外圆找正,车外圆各部,及右端面和右端总长199mm,留加工余量2mmCA61407 精车夹工件右端外圆,车内径至尺寸φ1308.06.0++mm,深195mm处车内槽φ136mm×4mm,车外端面,保证工件总长221mm,车φ260mm法兰盘厚度20mmCA61408 精车倒头,以内径定位装夹工件,精车右端外圆各部尺寸,留磨量0.8mm(注φ160mm不留加工余量),车内径φ905.02.0++mm至尺寸φ90mm,切各环槽至图样尺寸CA61409 磨夹工件右端外圆,内径找正,磨削内径至图样尺寸φ130045.0015.0++mm,靠磨φ136mm端面M1432A10 磨以内径定位装夹工件,磨φ16510.015.0--mm外圆,磨φ18010.015.0--mm外圆至图样尺寸M1432A11 钳划φ175mm中心圆上3×M8孔线,划φ222mm中心圆上3×φ13mm孔线Z52512 钳钻3×φ13mm孔,钻3×M8底孔φ6.7mm、攻螺纹M8、深15mmZ52513 检验桉图样检查各部尺寸和精度摇臂钻床14 入库入库高频感应加热淬火设备设计(日期)校对(日期)审核(日期)标准化(日期)会签(日期)标记处数更改文件号签字日期标记处数更改文件号签字日期。
密封制品工艺流程和密封材料

橡胶密封制品的主要生产工艺流程橡胶密封制品是以橡胶及其他各种配合剂原料.混练.半制品制造,硫化和修整等工序生产的,在橡胶工业制品中,上述主要工艺过程具有通用性.由于橡胶密封制品的品种.规格.结构复杂.除上述主要工艺过程外,还有很多辅助工艺过程,例如骨架油封,该制品的生产除橡胶外,还要有骨架材料,黏合剂,弹簧等配件的配套工艺,为了便于设计和指导生产,一般把橡胶密封制品的主要工艺过程和辅助工艺过程,用图示法按先后顺序连接起来,这就是工艺流程示意图,橡胶密封制品生产工艺过程的主要工序有以下五项:一是配料,涉及的原材料品种多,。
不同胶种所用的原材料差别很大,因此。
,必须分门别类仔细称量复核,不可配错料,二是混炼胶制造,要求分散均匀,性能稳定,工艺性能好。
尤其是硬度达90度。
,(邵尔A)的胶料的流动性要好。
焦烧性能好。
而且要求采用开炼机和密炼机都能制造,某些高精度的橡胶密封胶料还要进行滤胶或研磨,三是半成品制造,对于通用的模压硫化机方法,要求制造的半成品单耗(形状和质量)准确,使其装模速度快。
硫化后的制品胶边薄。
应尽可能采用精密预成型设备制造。
对于采用注射模压硫化方法,,虽不需专门制造半成品,但也应使胶料具有很好的流动性,而对于一些嵌骨架的复合橡胶密封件。
还要对各种骨架材料进行表面处理,包括选择适宜的粘合剂进行涂敷,。
四是硫化,采用高温短时,多模腔,大板模,撕边模。
不断提高生产效率,才有经济效益。
五是修整,采用机械化和半自动化去边和装配,确保产品的精度和尺寸公差通用的橡胶密封制品材料通用的橡胶密封制品在国防,化工,煤炭,石油,冶金,交通运输和机械制造工业等方面的应用越来越广泛,已成为各种行业中的基础件和配件。
橡胶密封制品常用材料如下。
1 丁腈橡胶丁腈橡胶具有优良的耐燃料油及芳香溶剂等性能,但不耐酮,酯和氯化氢等介质,因此耐油密封制品以及采用丁腈橡胶为主。
2 氯丁橡胶氯丁橡胶具有良好的耐油和耐溶剂性能。
它有较好的耐齿轮油和变压器油性能,但不耐芳香族油。
O型密封圈的装配ppt课件
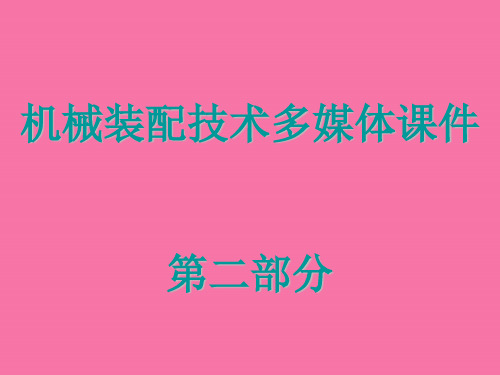
密封件可分为静密封件和动密封件 两大类。
O型密封圈〔如右图示〕是截面外 形为圆形的圆环形密封元件。其资料普 通为弹性橡胶,它具有良好的密封性能 ,且具有自封才干。密封压力可为 1.33×10 -5Pa~400MPa〔动密封可为 35MPa〕。
温度范围可为-60~~+120 oC
3 态度目的: 培育科学探求密封原理、正确运用装 拆工具的良好质量。
O型密封圈的装配
二、教学重点: 明确密封、密封件的概念、种类、密封的 意义、密封件装配的总要求。
三、教学难点: 0型密封圈的装配与装配工具及其运用。
四、作业: P86-1
O型密封圈的装配
五、导入:前面我们学习了滚动轴承的装配 …… ~ ~
安装油封时引荐运用的方法如下:
在安装油封时,应防止采用如以下图示的方法,防止产生油封 的变形。
第二节 油封的装配
第15讲 完
16
压盖填料的装填、密封垫的装配
一、教学目的
〔一〕知识目的: 1掌握压盖填料的功用、密封机理; 2明确压盖填料的资料及预压意义〔作用〕; 3明确密封垫的类型、要求、及运用。
当采用带防尘唇的油封时,可在密封唇和防尘唇间填满光滑脂 ,如下右图示。
七、油封的安装
油封安装时,首先应对油封、 轴及孔进展严厉的清理与清洗,在 轴和油封上涂抹光滑油或脂;轴端 应有导入倒角,锐边倒圆,其角度 为30℃~50℃,如右图示;腔体孔 口至少有2mm长度的倒角,其角度 为15℃~30℃,不允许有毛刺,如 以下图示。
作为动密封件,其预紧缩量约为8~20%
O型密封圈用在液压油缸中,遭到油压作用而发生变形,并被 挤压到堵塞液体走漏通道的一侧,紧贴槽侧和缸的内壁,从而使密 封作用加强。并随着油压的添加,密封性能越好,这种性能称为自 密封性。
O型密封圈设计流程
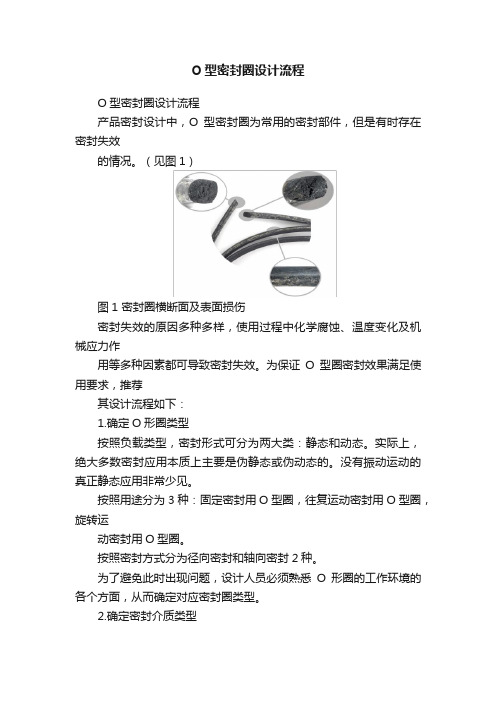
O型密封圈设计流程O型密封圈设计流程产品密封设计中,O型密封圈为常用的密封部件,但是有时存在密封失效的情况。
(见图1)图1 密封圈横断面及表面损伤密封失效的原因多种多样,使用过程中化学腐蚀、温度变化及机械应力作用等多种因素都可导致密封失效。
为保证O型圈密封效果满足使用要求,推荐其设计流程如下:1.确定O形圈类型按照负载类型,密封形式可分为两大类:静态和动态。
实际上,绝大多数密封应用本质上主要是伪静态或伪动态的。
没有振动运动的真正静态应用非常少见。
按照用途分为3种:固定密封用O型圈,往复运动密封用O型圈,旋转运动密封用O型圈。
按照密封方式分为径向密封和轴向密封2种。
为了避免此时出现问题,设计人员必须熟悉O形圈的工作环境的各个方面,从而确定对应密封圈类型。
2.确定密封介质类型在确定O形圈类型之后,下一步是根据密封的流体类型的合适材料类型。
通常,设计人员需要使用单个O形圈密封来平衡各种介质的相容性,考虑是否存在化学腐蚀或溶胀现象等。
具体适用情况见图2。
图2不同密封弹性体材料使用特性所选定弹性体材料在与工作介质接触后,必须只存在微小的性能参数变化(主要性能指标为抗张强度,体积,伸长率和弹性模量)。
为了成功选择O形圈,必须选择与其接触的所有介质均兼容的弹性体材料。
3.定义应用时间,温度和压力范围选择过程的下一步涉及应用程序的其他环境参数:温度,压力和时间。
密封设计需要综合考虑密封处的压力、温度、连续工作时间、运行周期等工作条件。
不论选择用于何种密封应用的弹性体材料,要考虑的最重要因素之一是使用温度范围。
图3罗列了主要弹性体在正常和极限(短期使用)温度范围内的性能。
图3 常用密封弹性体材料使用温度范围图3列出了常用密封弹性体材料及其工作温度性能。
根据设计所需的温度范围,可能需要在步骤2和3之间进行迭代过程以选择正确的密封弹性体材料。
另外由于压力差导致密封圈挤出(见图4)的情况时有发生。
图4 密封圈挤出示意图不同硬度的O形圈材料的挤出特性存在较大的差异(见图5)。