钢管应力计算
管道应力计算
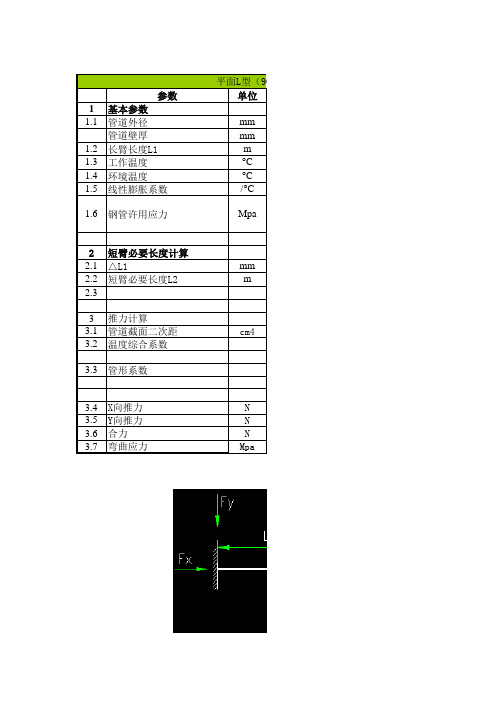
3 推力计算
3.1 管道截面二次距
cm4
3.2 温度综合系数
3.3 管形系数
3.4 X向推力
N
3.5 Y向推力
N
3.6 合力
N
3.7 弯曲应力
Mpa
平面L型(90度)自然补偿推力和应力计算 符号或公式
数据
Do S L1; T1 T2
σ;取决于管道的材料和使用温度,见工业金属 管道设计规范
159.00 4.50 30.00
参数 1 基本参数 1.1 管道外径
管道壁厚 1.2 长臂长度L1 1.3 工作温度 1.4 环境温度 1.5 线性膨胀系数
1.6 钢管许用应力
平面L型(90度)自然补偿推力和应力计算 单位源自mm mm m °C °C /°C
Mpa
2 短臂必要长度计算
2.1 △L1
mm
2.2 短臂必要长度L2
m
2.3
120.00 0.00
0.00001266
105.00000000
△L1=L1*a*(T1-T2) L2min=1.1SQRT(△L1*Do/300) L2取值
I;动力管道设计手册,表9-4 C; L1/L2;用以在表9-5查Kx,Ky等 Kx Ky Kb Fx=9.8Kx*C*I/L1/L1 Fy=9.8Ky*C*I/L1/L1 F=SQRT(Fx*Fx+Fy*Fy) σb=0.098*Kb*C*Do/L1
45.576 5.41 5.00
652 0.288
6 52 16 825 106 33 111 12.34
钢管的应力分析和变形计算
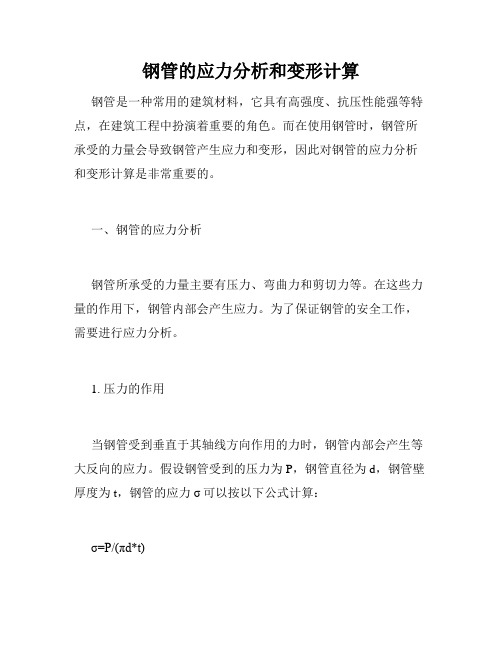
钢管的应力分析和变形计算钢管是一种常用的建筑材料,它具有高强度、抗压性能强等特点,在建筑工程中扮演着重要的角色。
而在使用钢管时,钢管所承受的力量会导致钢管产生应力和变形,因此对钢管的应力分析和变形计算是非常重要的。
一、钢管的应力分析钢管所承受的力量主要有压力、弯曲力和剪切力等。
在这些力量的作用下,钢管内部会产生应力。
为了保证钢管的安全工作,需要进行应力分析。
1. 压力的作用当钢管受到垂直于其轴线方向作用的力时,钢管内部会产生等大反向的应力。
假设钢管受到的压力为P,钢管直径为d,钢管壁厚度为t,钢管的应力σ可以按以下公式计算:σ=P/(πd*t)2. 弯曲力的作用当钢管受到弯曲力作用时,钢管的弯曲应力最大。
在这种情况下,可采用莫尔-库伦公式来计算钢管的应力,公式如下:σ=M*y/I其中,M为弯曲力矩,y为点到钢管中心轴线的距离,I为钢管截面惯性矩。
3. 剪切力的作用当钢管受到剪切力作用时,钢管产生剪切变形并产生剪切应力,采用最大剪切应力理论进行计算可得:τ=F/(2A)其中,F为作用于钢管上的剪切力,A为钢管的横截面积。
二、钢管的变形计算钢管受到力量作用时,其会产生变形。
变形计算是为保证钢管在受力的过程中不超过允许变形量所必需的计算。
1. 弹性变形计算钢管在受到作用力时会产生弹性变形。
当钢管的受力时限制在弹性范围内,可采用胡克定律进行弹性变形的计算。
假设当钢管受力后变形量为ΔL,弹性模量为E,作用力为P,则弹性变形量可按照以下公式进行计算:ΔL=PL/(AE)2. 塑性变形计算当钢管受到的力量超出了材料所能承受的弹性极限后,钢管会产生塑性变形。
而塑性变形后的钢管形状难以计算,因此在进行变形计算时通常采用杆件理论进行处理。
杆件理论根据杆件的几何形状、材料和作用力进行杆件弯曲变形和剪切变形的计算,由于钢管直径较小,通常将钢管视为杆件。
在杆件弯曲变形计算中,采用冯·米塞斯的应变能理论和极大应力原理进行计算;在杆件剪切变形计算中,采用科西桥公式进行计算,同时应注意剪应力不应超出材料的剪切强度。
应力计算书
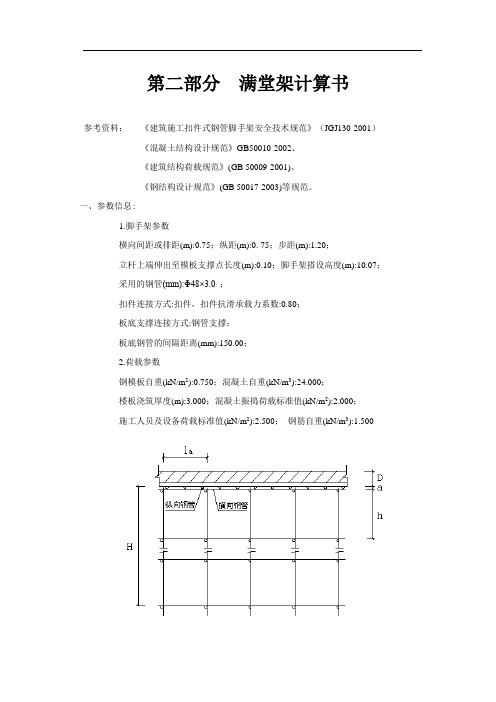
第二部分满堂架计算书参考资料:《建筑施工扣件式钢管脚手架安全技术规范》(JGJ130-2001)《混凝土结构设计规范》GB50010-2002、《建筑结构荷载规范》(GB 50009-2001)、《钢结构设计规范》(GB 50017-2003)等规范。
一、参数信息:1.脚手架参数横向间距或排距(m):0.75;纵距(m):0. 75;步距(m):1.20;立杆上端伸出至模板支撑点长度(m):0.10;脚手架搭设高度(m):10.07;采用的钢管(mm):Φ48×3.0 ;扣件连接方式:扣件,扣件抗滑承载力系数:0.80;板底支撑连接方式:钢管支撑;板底钢管的间隔距离(mm):150.00;2.荷载参数钢模板自重(kN/m2):0.750;混凝土自重(kN/m3):24.000;楼板浇筑厚度(m):3.000;混凝土振捣荷载标准值(kN/m2):2.000;施工人员及设备荷载标准值(kN/m2):2.500;钢筋自重(kN/m3):1.500图1 底板支撑架立面简图图2 底板支撑架荷载计算单元二、纵向支撑钢管的计算:纵向钢管按照均布荷载下简支梁计算,截面力学参数为截面抵抗矩 w=4.49cm3截面惯性矩 I=10.78cm4弹性模量 E=2.06×106N/mm1.荷载的计算:(1)钢筋混凝土自重(kN/m):q11= (24.000+1.500)×0.15×3.000 = 11.475 kN/m;(2)模板的自重线荷载(kN/m):q12= 0.750×0.15 = 0.1125 kN/m ;(3)活荷载为施工人员及设备、混凝土振捣时产生的荷载(kN):q2 = (2.500 +2.000)×0.15 = 0.675kN/m;2.强度计算:最大弯矩考虑为简支梁均布荷载作用下的跨中弯矩。
M=ql2/8q=q11+ q12+ q2=12.2625 kN/m最大弯距 M max = 12.2625×0. 752 /8= 0.862 kN.M;最大支座力计算公式如下:N=ql/2最大支座力 N = 12.2625×0.75/2=4.598 kN ;截面应力σ= M/W= 0.862×106/4490.0 =192.028 N/mm2;纵向钢管的计算强度为 192.028小于205.0 N/mm2,满足要求!3.挠度计算:最大挠度考虑为简支梁均布荷载作用下的挠度计算公式如下:W=5ql4/384EIq=q11+ q12+ q2=12.2625 kN/m均布荷载作用下的最大挠度W= 5×12.2625×75.04/( 100×2.060×105×107800.0 ) =0.227 mm;支撑钢管的最大挠度小于750.0/150与10 mm,满足要求!三、横向支撑10#槽钢计算:横向10#槽钢按照均布荷载下简支梁计算,截面力学参数为截面抵抗矩 w=39.7cm3截面惯性矩 I=198.3cm4弹性模量 E=2.06×106N/mm1.荷载的计算:(1)钢筋混凝土自重(kN/m):q11= (24.000+1.500)×0.75×3.000 = 57.375 kN/m;(2)模板的自重线荷载(kN/m):q12= 0.750×0.75 = 0.5625 kN/m ;(3)活荷载为施工人员及设备、混凝土振捣时产生的荷载(kN):q2 = (2.500 +2.000)×0.75 = 3.375kN/m;2.强度计算:最大弯矩考虑为简支梁均布荷载作用下的跨中弯矩。
钢管应力分析综合计算表V1.0
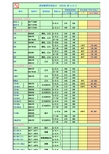
在下列温度下的许用应力 / MPa ≤20℃ 9 100℃ 10 150℃ 11 200℃ 12 250℃ 13 300℃ 14 350℃ 15 400℃ 16 425℃ 17 450℃ 18 475℃ 19 500℃ 20
113 130 110 112 112 111 130 130 131 131 137 137 137 163 163 170 170 133 128 122 128 147 147 141 147 150 150 122 116 157 157 137 137 137 137 137 137 137 137
bh
钢பைடு நூலகம் 标准号
常用钢管许用应力 (GB150 表 A.0.1)
使用状态 厚度/mm 常温强度指标 σ b / MPa σ s / MPa 待定温度下的许用应力 t/℃ σ t / MPa
炭素钢钢管(焊接管) Q235-A Q235-B 20# 10# 10# 10# 20# 20# 20# 20G GB/T14980 GB/T13793 GB/T13793 GB9948 GB6479 GB/T8163 GB3087 GB/T8163 GB3087 GB9948 GB6479 GB5310 GB6479 GB/T8163 GB6479 热轧、正火 热轧、正火 热轧、正火 热轧、正火 热轧、正火 热轧、正火 正火 δ ≤12 δ ≤12.7 δ ≤16 δ ≤15 16~40 δ ≤26 δ ≤15 16~40 δ ≤15 16~26 δ ≤16 δ ≤16 17~40 δ ≤15 16~40 δ ≤16 17~40 δ ≤16 δ ≤16 17~40 δ ≤16 δ ≤16 δ ≤16 17~40 δ ≤16 δ ≤16 17~40 δ ≤16 17~40 正火加回火 δ ≤16 17~40 δ ≤18 δ ≤14 δ ≤18 δ ≤14 δ ≤18 δ ≤14 δ ≤18 δ ≤18 375 390 330 335 335 333 390 390 392 392 410 410 410 490 490 510 510 400 410 410 410 440 440 440 470 450 450 390 390 470 470 235 235 205 205 195 196 245 235 245 226 245 245 235 320 310 350 340 240 205 195 205 235 235 225 255 280 270 195 185 295 285 385℃ 89.900 20℃ 220℃ 220℃ 133.000 98.600 95.600 150℃ 85℃ 85℃ 85℃ 85℃ 130.000 130.000 130.188 130.188 137.000
无缝钢管受力计算

无缝钢管受力计算无缝钢管是一种经过热轧或冷拔制成的钢质管道,具有优良的机械性能和高耐压能力,广泛应用于石油、化工、水利、天然气等领域。
在设计和使用过程中,对无缝钢管的受力计算是非常重要的,可以确保其安全可靠地运行。
无缝钢管的受力计算主要包括轴向力、弯曲力和剪切力的计算。
下面将详细介绍这些计算方法。
1.轴向力计算轴向力是指垂直于截面的力,可以通过应力计算公式来求得。
设无缝钢管的外径为D,壁厚为t,应力为σ,轴向力为N,则有以下公式:N=σ*A其中A为截面面积,可以根据无缝钢管的外径和壁厚计算得到:A=π*(D/2)^2-π*((D/2)-t)^22.弯曲力计算弯曲力是指沿管轴线方向施加的力,可以通过弯矩计算公式来求得。
设无缝钢管的长度为L,弯矩为M,则有以下公式:M=σ*I/y其中I为截面惯性矩,y为截面离中性轴的距离,可以根据无缝钢管的外径和壁厚计算得到:I=π*(D/2)^4/64y=(D/2)–t/23.剪切力计算剪切力是指垂直于截面平面的力,可以通过剪应力计算公式来求得。
设无缝钢管的外径为D,剪应力为τ,剪切力为Q,则有以下公式:Q=τ*A其中A为截面面积,可以根据无缝钢管的外径和壁厚计算得到:A=π*(D/2)^2-π*((D/2)-t)^2受力计算除了要考虑产生力的原因外,还需要考虑材料本身的性能和使用条件。
在实际应用中,需要考虑到的因素有以下几点:1.强度:无缝钢管的受力计算前提是钢管具有足够的强度,能够承受所施加的力。
因此,在进行受力计算前,需要明确钢管的材料强度和弹性模量等性能指标。
2.用途和工况:不同的使用场景和工况对无缝钢管的受力要求是不同的,需要根据具体的使用场景和工况来确定受力计算的参数和需求。
3.温度影响:由于温度的变化会对钢管的材料性能产生影响,因此在受力计算时需要考虑到温度的影响。
一般来说,随着温度的升高,材料的强度和刚度会下降,因此需要对温度进行适当的修正。
4.安全系数:在受力计算中,还需要考虑钢管的安全系数,以保证钢管在使用过程中不会超过其承受能力,确保其安全可靠地运行。
钢管应力计算
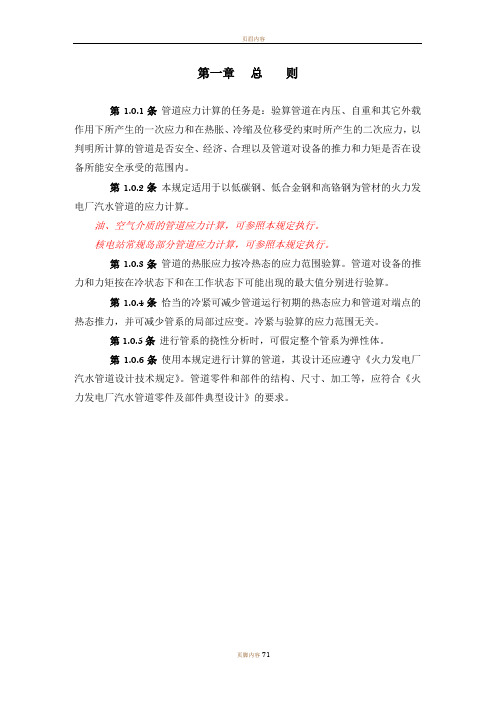
第一章总则第1.0.1条管道应力计算的任务是:验算管道在内压、自重和其它外载作用下所产生的一次应力和在热胀、冷缩及位移受约束时所产生的二次应力,以判明所计算的管道是否安全、经济、合理以及管道对设备的推力和力矩是否在设备所能安全承受的范围内。
第1.0.2条本规定适用于以低碳钢、低合金钢和高铬钢为管材的火力发电厂汽水管道的应力计算。
油、空气介质的管道应力计算,可参照本规定执行。
核电站常规岛部分管道应力计算,可参照本规定执行。
第1.0.3条管道的热胀应力按冷热态的应力范围验算。
管道对设备的推力和力矩按在冷状态下和在工作状态下可能出现的最大值分别进行验算。
第1.0.4条恰当的冷紧可减少管道运行初期的热态应力和管道对端点的热态推力,并可减少管系的局部过应变。
冷紧与验算的应力范围无关。
第1.0.5条进行管系的挠性分析时,可假定整个管系为弹性体。
第1.0.6条使用本规定进行计算的管道,其设计还应遵守《火力发电厂汽水管道设计技术规定》。
管道零件和部件的结构、尺寸、加工等,应符合《火力发电厂汽水管道零件及部件典型设计》的要求。
第二章钢材的许用应力第2.0.1条钢材的许用应力,应根据钢材的有关强度特性取下列三项中的最小值:σb20/3,σs t/1.5或σs t(0.2%)/1.5,σD t/1.5其中σb20——钢材在20℃时的抗拉强度最小值(MPa);σs t——钢材在设计温度下的屈服极限最小值(MPa);σs t(0.2%)——钢材在设计温度下残余变形为0.2%时的屈服极限最小值(MPa);σD t——钢材在设计温度下105h持久强度平均值。
常用钢材的许用应力数据列于附录A。
国产常用钢材和附表中所列的德国钢材的许用应力按本规定的安全系数确定。
美国钢材的许用应力摘自美国标准ASME B31.1。
对于未列入附录A的钢材,如符合有关技术条件可作为汽水管道的管材时,它的许用应力仍按本规定计算。
第三章管道的设计参数第3.0.1条设计压力的取用管道设计压力(表压)系指管道运行中内部介质最大工作压力。
钢管应力计算
第一章总则第1.0.1条管道应力计算的任务是:验算管道在内压、自重和其它外载作用下所产生的一次应力和在热胀、冷缩及位移受约束时所产生的二次应力,以判明所计算的管道是否安全、经济、合理以及管道对设备的推力和力矩是否在设备所能安全承受的范围内。
第1.0.2条本规定适用于以低碳钢、低合金钢和高铬钢为管材的火力发电厂汽水管道的应力计算。
油、空气介质的管道应力计算,可参照本规定执行。
核电站常规岛部分管道应力计算,可参照本规定执行。
第1.0.3条管道的热胀应力按冷热态的应力范围验算。
管道对设备的推力和力矩按在冷状态下和在工作状态下可能出现的最大值分别进行验算。
第1.0.4条恰当的冷紧可减少管道运行初期的热态应力和管道对端点的热态推力,并可减少管系的局部过应变。
冷紧与验算的应力范围无关。
第1.0.5条进行管系的挠性分析时,可假定整个管系为弹性体。
第1.0.6条使用本规定进行计算的管道,其设计还应遵守《火力发电厂汽水管道设计技术规定》。
管道零件和部件的结构、尺寸、加工等,应符合《火力发电厂汽水管道零件及部件典型设计》的要求。
第二章钢材的许用应力第2.0.1条钢材的许用应力,应根据钢材的有关强度特性取下列三项中的最小值:σb20/3,σs t/1.5或σs t(0.2%)/1.5,σD t/1.5其中σb20——钢材在20℃时的抗拉强度最小值(MPa);σs t——钢材在设计温度下的屈服极限最小值(MPa);σs t(0.2%)——钢材在设计温度下残余变形为0.2%时的屈服极限最小值(MPa);σD t——钢材在设计温度下105h持久强度平均值。
常用钢材的许用应力数据列于附录A。
国产常用钢材和附表中所列的德国钢材的许用应力按本规定的安全系数确定。
美国钢材的许用应力摘自美国标准ASME B31.1。
对于未列入附录A的钢材,如符合有关技术条件可作为汽水管道的管材时,它的许用应力仍按本规定计算。
第三章管道的设计参数第3.0.1条设计压力的取用管道设计压力(表压)系指管道运行中内部介质最大工作压力。
钢管应力计算
第一章总则第1.0.1条管道应力计算的任务是:验算管道在内压、自重和其它外载作用下所产生的一次应力和在热胀、冷缩及位移受约束时所产生的二次应力,以判明所计算的管道是否安全、经济、合理以及管道对设备的推力和力矩是否在设备所能安全承受的范围内。
第1.0.2条本规定适用于以低碳钢、低合金钢和高铬钢为管材的火力发电厂汽水管道的应力计算。
油、空气介质的管道应力计算,可参照本规定执行。
核电站常规岛部分管道应力计算,可参照本规定执行。
第1.0.3条管道的热胀应力按冷热态的应力范围验算。
管道对设备的推力和力矩按在冷状态下和在工作状态下可能出现的最大值分别进行验算。
第1.0.4条恰当的冷紧可减少管道运行初期的热态应力和管道对端点的热态推力,并可减少管系的局部过应变。
冷紧与验算的应力范围无关。
第1.0.5条进行管系的挠性分析时,可假定整个管系为弹性体。
第1.0.6条使用本规定进行计算的管道,其设计还应遵守《火力发电厂汽水管道设计技术规定》。
管道零件和部件的结构、尺寸、加工等,应符合《火力发电厂汽水管道零件及部件典型设计》的要求。
第二章钢材的许用应力第2.0.1条钢材的许用应力,应根据钢材的有关强度特性取下列三项中的最小值:σb20/3,σs t/1.5或σs t(0.2%)/1.5,σD t/1.5其中σb20——钢材在20℃时的抗拉强度最小值(MPa);σs t——钢材在设计温度下的屈服极限最小值(MPa);σs t(0.2%)——钢材在设计温度下残余变形为0.2%时的屈服极限最小值(MPa);σD t——钢材在设计温度下105h持久强度平均值。
常用钢材的许用应力数据列于附录A。
国产常用钢材和附表中所列的德国钢材的许用应力按本规定的安全系数确定。
美国钢材的许用应力摘自美国标准ASME B31.1。
对于未列入附录A的钢材,如符合有关技术条件可作为汽水管道的管材时,它的许用应力仍按本规定计算。
第三章管道的设计参数第3.0.1条设计压力的取用管道设计压力(表压)系指管道运行中内部介质最大工作压力。
钢管应力计算【可编辑范本】
第一章总则第1。
0.1条管道应力计算的任务是:验算管道在内压、自重和其它外载作用下所产生的一次应力和在热胀、冷缩及位移受约束时所产生的二次应力,以判明所计算的管道是否安全、经济、合理以及管道对设备的推力和力矩是否在设备所能安全承受的范围内。
第1.0.2条本规定适用于以低碳钢、低合金钢和高铬钢为管材的火力发电厂汽水管道的应力计算。
油、空气介质的管道应力计算,可参照本规定执行。
核电站常规岛部分管道应力计算,可参照本规定执行。
第1.0.3条管道的热胀应力按冷热态的应力范围验算。
管道对设备的推力和力矩按在冷状态下和在工作状态下可能出现的最大值分别进行验算。
第1.0.4条恰当的冷紧可减少管道运行初期的热态应力和管道对端点的热态推力,并可减少管系的局部过应变。
冷紧与验算的应力范围无关.第1。
0。
5条进行管系的挠性分析时,可假定整个管系为弹性体。
第1.0。
6条使用本规定进行计算的管道,其设计还应遵守《火力发电厂汽水管道设计技术规定》。
管道零件和部件的结构、尺寸、加工等,应符合《火力发电厂汽水管道零件及部件典型设计》的要求。
第二章钢材的许用应力第2。
0.1条钢材的许用应力,应根据钢材的有关强度特性取下列三项中的最小值:σb20/3,σst/1。
5或σst(0。
2%)/1.5,σD t/1.5其中σb20—-钢材在20℃时的抗拉强度最小值(MPa);σs t-—钢材在设计温度下的屈服极限最小值(MPa);σs t(0。
2%)—-钢材在设计温度下残余变形为0。
2%时的屈服极限最小值(MPa);σDt——钢材在设计温度下105h持久强度平均值。
常用钢材的许用应力数据列于附录A.国产常用钢材和附表中所列的德国钢材的许用应力按本规定的安全系数确定.美国钢材的许用应力摘自美国标准ASMEB31.1。
ﻩ对于未列入附录A的钢材,如符合有关技术条件可作为汽水管道的管材时,它的许用应力仍按本规定计算.第三章管道的设计参数第3.0。
钢管应力计算之欧阳法创编
第一章总则第1.0.1条管道应力计算的任务是:验算管道在内压、自重和其它外载作用下所产生的一次应力和在热胀、冷缩及位移受约束时所产生的二次应力,以判明所计算的管道是否安全、经济、合理以及管道对设备的推力和力矩是否在设备所能安全承受的范围内。
第1.0.2条本规定适用于以低碳钢、低合金钢和高铬钢为管材的火力发电厂汽水管道的应力计算。
油、空气介质的管道应力计算,可参照本规定执行。
核电站常规岛部分管道应力计算,可参照本规定执行。
第1.0.3条管道的热胀应力按冷热态的应力范围验算。
管道对设备的推力和力矩按在冷状态下和在工作状态下可能出现的最大值分别进行验算。
第1.0.4条恰当的冷紧可减少管道运行初期的热态应力和管道对端点的热态推力,并可减少管系的局部过应变。
冷紧与验算的应力范围无关。
第1.0.5条进行管系的挠性分析时,可假定整个管系为弹性体。
第1.0.6条使用本规定进行计算的管道,其设计还应遵守《火力发电厂汽水管道设计技术规定》。
管道零件和部件的结构、尺寸、加工等,应符合《火力发电厂汽水管道零件及部件典型设计》的要求。
第二章钢材的许用应力第2.0.1条钢材的许用应力,应根据钢材的有关强度特性取下列三项中的最小值:σb20/3,σs t/1.5或σs t(0.2%)/1.5,σD t/1.5其中σb20——钢材在20℃时的抗拉强度最小值(MPa);σs t——钢材在设计温度下的屈服极限最小值(MPa);σs t(0.2%)——钢材在设计温度下残余变形为0.2%时的屈服极限最小值(MPa);σD t——钢材在设计温度下105h持久强度平均值。
常用钢材的许用应力数据列于附录A。
国产常用钢材和附表中所列的德国钢材的许用应力按本规定的安全系数确定。
美国钢材的许用应力摘自美国标准ASME B31.1。
对于未列入附录A的钢材,如符合有关技术条件可作为汽水管道的管材时,它的许用应力仍按本规定计算。
第三章管道的设计参数第3.0.1条设计压力的取用管道设计压力(表压)系指管道运行中内部介质最大工作压力。
- 1、下载文档前请自行甄别文档内容的完整性,平台不提供额外的编辑、内容补充、找答案等附加服务。
- 2、"仅部分预览"的文档,不可在线预览部分如存在完整性等问题,可反馈申请退款(可完整预览的文档不适用该条件!)。
- 3、如文档侵犯您的权益,请联系客服反馈,我们会尽快为您处理(人工客服工作时间:9:00-18:30)。
第一章总则第1.0.1条管道应力计算的任务是:验算管道在内压、自重和其它外载作用下所产生的一次应力和在热胀、冷缩及位移受约束时所产生的二次应力,以判明所计算的管道是否安全、经济、合理以及管道对设备的推力和力矩是否在设备所能安全承受的范围内。
第1.0.2条本规定适用于以低碳钢、低合金钢和高铬钢为管材的火力发电厂汽水管道的应力计算。
油、空气介质的管道应力计算,可参照本规定执行。
核电站常规岛部分管道应力计算,可参照本规定执行。
第1.0.3条管道的热胀应力按冷热态的应力范围验算。
管道对设备的推力和力矩按在冷状态下和在工作状态下可能出现的最大值分别进行验算。
第1.0.4条恰当的冷紧可减少管道运行初期的热态应力和管道对端点的热态推力,并可减少管系的局部过应变。
冷紧与验算的应力范围无关。
第1.0.5条进行管系的挠性分析时,可假定整个管系为弹性体。
第1.0.6条使用本规定进行计算的管道,其设计还应遵守《火力发电厂汽水管道设计技术规定》。
管道零件和部件的结构、尺寸、加工等,应符合《火力发电厂汽水管道零件及部件典型设计》的要求。
第二章 钢材的许用应力第2.0.1条 钢材的许用应力,应根据钢材的有关强度特性取下列三项中的最小值:σb 20/3,σs t /1.5或σs t (0.2%)/1.5,σD t /1.5 其中 σb 20——钢材在20℃时的抗拉强度最小值(MPa );σs t ——钢材在设计温度下的屈服极限最小值(MPa ); σs t (0.2%)——钢材在设计温度下残余变形为0.2%时的屈服极限最小值(MPa );σD t ——钢材在设计温度下105h 持久强度平均值。
常用钢材的许用应力数据列于附录A 。
国产常用钢材和附表中所列的德国钢材的许用应力按本规定的安全系数确定。
美国钢材的许用应力摘自美国标准ASME B31.1。
对于未列入附录A 的钢材,如符合有关技术条件可作为汽水管道的管材时,它的许用应力仍按本规定计算。
第三章管道的设计参数第3.0.1条设计压力的取用管道设计压力(表压)系指管道运行中内部介质最大工作压力。
对于水管道,设计压力的取用,应包括水柱静压的影响,当其低于额定压力的3%时,可不考虑。
主要管道的设计压力,应按下列规定选用:一.主蒸汽管道当为亚临界参数时,取用锅炉过热器出口的额定工作压力或锅炉最大连续蒸发量下的工作压力。
当为超临界参数时,取用锅炉最大连续蒸发量下过热器出口工作压力的1.05倍。
当锅炉和汽轮机允许超压5%(简称5%OP)运行时,应加上5%的超压值。
二.再热蒸汽管道取用汽轮机最大计算出力工况(调节汽门全开,简称VWO或VWO+5%OP)热平衡中高压缸排汽压力的1.15倍。
对于再热器出口联箱到汽轮机的部分,可减至再热器出口安全阀动作的最低整定压力。
三.汽轮机抽汽管道非调整抽汽管道,取用汽轮机最大计算出力工况下该抽汽压力的1.1倍,且不小于0.1MPa。
调整抽汽管道,取其最高工作压力。
四.背压式汽轮机排汽管道取其最高工作压力。
五.减压装置后的蒸汽管道取其最高工作压力。
六.与直流锅炉启动分离器连接的汽水管道取用分离器各种运行工况中可能出现的最高工作压力。
七.高压给水管道非调速给水泵出口管道,从前置泵到主给水泵或从主给水泵至锅炉省煤器进口区段,分别取用前置泵或主给水泵特性曲线最高点对应的压力与该泵进水侧压力之和;调速给水泵出口管道,从给水泵出口至关断阀的管道,设计压力取用泵在额定转速特性曲线最高点对应的压力与进水侧压力之和;从泵出口关断阀至锅炉省煤器进口区段,取用泵在额定转速及设计流量下泵提升压力的1.1倍与泵进水侧压力之和。
以上高压给水管道压力,应考虑水泵进水温度对压力的修正。
八.低压给水管道对于定压除氧系统,取用除氧器额定压力与最高水位时水柱静压之和;对于滑压除氧系统,取用汽轮机最大计算出力工况下除氧器加热抽汽压力的1.1倍与除氧器最高水位时水柱静压之和。
九.凝结水管道凝结水泵进口侧管道,取用泵吸入口中心线至汽轮机排汽缸接口平面处的水柱静压(此时凝汽器内按大气压力),且不小于0.35MPa;单级泵系统泵出口侧管道,取用泵出口阀关断情况下泵的扬程与进水侧压力(上述水柱静压)之和;两级泵系统的凝结水泵出口侧管道,取用原则同单级泵系统泵出口侧管道;两级泵系统的凝结水升压泵出口侧管道,取用两台泵(凝结水泵和凝结水升压泵)出口阀关闭情况下泵的扬程之和。
十.加热器疏水管道取用汽轮机最大计算出力工况下抽汽压力的1.1倍,且不小于0.1MPa。
当管道中疏水静压引起压力升高值大于抽汽压力的3%时,尚应计及静压的影响。
十一.锅炉排污管道锅炉排污阀前或者当排污阀后管道装有阀门或堵板等可能引起管内压力升高时,对于定期排污管道,设计压力应不小于汽包上所有安全阀中的最低整定压力与汽包最高水位至管道最低点水柱静压之和;对于连续排污管道,设计压力应不小于汽包上所有安全阀的最低整定压力。
当锅炉排污阀后不会引起管内压力升高时,排污管道(定期排污或连续排污)的设计压力按表3.0.1选取。
10.301十二.给水再循环管道当采用单元制系统时,进除氧器的最后一道关断阀及其以前的管道,取用相应的高压给水管道的设计压力,其后的管道,对于定压除氧系统,取用除氧器额定压力;对于滑压除氧系统,取用汽轮机最大计算出力工况下除氧器加热抽汽压力的1.1倍。
当采用母管制系统时,节流孔板及其以前的管道,取用相应的高压给水管道的设计压力;节流孔板后的管道,当未装设阀门或介质出路上的阀门不可能关断时,取用除氧器的额定压力。
十三.安全阀后排汽管道应根据排汽管道的水力计算结果确定。
第3.0.2条设计温度的取用设计温度系指管道运行中内部介质的最高工作温度。
主要管道的设计温度,应按下列规定选用:一.主蒸汽管道取用锅炉过热器出口蒸汽额定工作温度加上锅炉正常运行时允许的温度偏差值。
温度偏差值,可取用5℃。
二.再热蒸汽管道高温再热蒸汽管道,取用锅炉再热器出口蒸汽额定工作温度加上锅炉正常运行时允许的温度偏差,温度偏差值,可取用5℃;低温再热蒸汽管道,取用汽轮机最大计算出力工况下高压缸排汽参数,等熵求取在管道设计压力下的相应温度。
如制造厂有特殊要求时,该设计温度应取用可能出现的最高工作温度。
三.汽轮机抽汽管道非调整抽汽管道,取用汽轮机最大计算出力工况下抽汽参数,等熵求取管道设计压力下的相应温度;调整抽汽管道,取用抽汽的最高工作温度。
四.背式压汽轮机排汽管道取用排汽的最高工作温度。
五.减温装置后的蒸汽管道取用减温装置出口蒸汽的最高工作温度。
六.与直流锅炉启动分离器连接的汽水管道取用分离器各种运行工况中管道可能出现的汽水最高工作温度。
七.高压给水管道取用高压加热器后高压给水的最高工作温度。
八.低压给水管道对于定压除氧器系统,取用除氧器额定压力对应的饱和温度;对于滑压除氧器系统,取用汽轮机最大计算出力工况下1.1倍除氧器加热抽汽压力对应的饱和温度。
九.凝结水管道取用低压加热器后凝结水的最高工作温度。
十.加热器疏水管道取用该加热器抽汽管道设计压力对应的饱和温度。
十一.锅炉排污管道锅炉排污阀前或者当排污阀后管道装有阀门或堵板等可能引起管内压力升高时,排污管道(定期排污或连续排污)的设计温度,取用汽包上所有安全阀中的最低整定压力对应的饱和温度。
锅炉排污阀后不会引起管内压力升高时,排污管道(定期排污或连续排污)的设计温度按表3.0.2选取。
10.301十二.给水再循环管道对于定压除氧系统,取用除氧器额定压力对应的饱和温度;对于滑压除氧系统,取用汽轮机最大计算出力工况下1.1倍除氧器加热抽汽压力对应的饱和温度。
十三.安全阀后排汽管道排汽管道的设计温度,应根据排汽管道水力计算中相应数据选取。
第四章 承受内压的管子壁厚计算一.第4.0.1条 直管最小壁厚S m 应按下列规定计算:按直管外径确定时:)11.0.4(-++=α2Ypη2[σ]pD S t o m 二.按直管内径确定时:)21.0.4(---++=Y)2p(1η2[σ]2Ypαηα2[σ]pD S t t i m以上两式中 S m —直管的最小壁厚(mm )p —设计压力(MPa );D 0—管子外径(mm )。
设计计算时,管道外径选用标准和材料技术条件表内所列的外径来计算Sm 值。
当计算现有的或库存的管道的许用工作压力时,实测管道外径和管端较薄处的最小壁厚,用来计算许用工作压力。
D i —管子内径(mm )。
设计计算时,管道内径可取采购技术条件内允许的最大可能值。
当计算现有的或库存的管道许用工作压力时,实测内径和管端最簿处的最小壁厚可用来计算许用工作压力。
[σ]t —钢材在设计温度下的许用应力(MPa ); Y — 温度对计算管子壁厚公式的修正系数,对于铁素体钢,482℃及以下时Y = 0.4,510℃时Y = 0.5,538℃及以上时Y = 0.7;对于奥氏体钢,566℃及以下时Y = 0.4,593℃时Y = 0.5,621℃及以上时Y = 0.7;中间温度的Y 值,可按内插法计算;当管子的D 0 / S m < 6时,对于设计温度小于等于482℃的铁素体和奥氏体钢,其Y 值应按下式计算:Y= D i / (D i + D 0)。
α —考虑腐蚀﹑磨损和机械强度要求的附加厚度(mm ) η—许用应力的修正系数,无缝钢管的η=1.0,纵缝焊接钢管按有关制造技术条件检验合格者,其η值按表4.0.1取用,螺旋焊缝钢管按SY/T5037-2000标准生产制作和无损检验合格者,η=0.9。
第4.0.2条 直管计算壁厚S c 应按下列方法确定:S c = S m +c(4.0.2-1) 式中 c ─直管壁厚负偏差值(mm )。
一.对于热轧生产的无缝钢管,壁厚负偏差系数值可按下式确定:c = AS m(4.0.2-2) 式中 A ─直管壁厚负偏差系数,根据管子产品技术条件中规定的壁厚允许负偏差(m%)按公式m m A -=100计算,或按表4.0.2取用。
二.对于按内径确定壁厚及采用热挤压生产的无缝钢管,壁厚负偏差值应根据管子产品技术条件中的规定选用。
三. 对于焊接钢管,采用钢板厚度的负偏差值,但C 值不得小于0.5 mm 。
第4.0.3条 直管公称壁厚S n ,对于按外径确定壁厚的钢管,根据直管计算壁厚S c 按管子产品规格选用;对于按内径确定壁厚的无缝钢管,根据直管计算壁厚S c 和制造厂产品技术条件中的有关规定选用。
在任何情况下,S n 均应等于或大于S c 。
第4.0.4条 弯管的壁厚应按下列方法确定:一.用作弯管的直管,其最小壁厚根据弯曲半径而定,按表4.0.4取用。
6倍管子外径二.弯管后任何一点的实测最小壁厚不得小于直管最小壁厚S m。
第五章补偿值的计算第5.0.1条管道一般以设备连接点或固定点分为若干管段,设备连接点或固定点之间互相连接的各管段,构成一个独立的计算管系,统一进行挠性分析和计算。