高速金属切削的摩擦分析及有限元模拟
铝合金高速切削有限元仿真及实验研究

铝合金高速切削有限元仿真及实验研究作者:汪健明刘康来源:《软件工程》2021年第12期摘要:为了研究不同切削参数对铝合金切削过程中切削力和切削温度的影响,以铝合金7075-T651为对象,采用仿真与实验验证结合的方法,利用金属有限元切削专用软件AdvantEdge建立了铝合金7075-T651的二维正交切削仿真模型,并进行合理的工件和刀具材料参数以及本构模型设置。
通过仿真分析,研究了切削力和切削温度与进给速度以及切削深度的关系,并通过实验进行验证。
仿真和实验结果表明:在一定范围内,随着进给速度和切削深度的增大,切削力和切削温度增大。
切削铝合金7075-T651时,应采用较小的切削深度和进给速度。
关键词:AdvantEdge;铝合金7075-T651;切削力;切削温度中图分类号:TP319 文献标识码:AAbstract: In order to study the influence of different cutting parameters on cutting force and cutting temperature in cutting process of aluminum alloy, this research uses aluminum alloy 7075-T651 as the object, and takes the method of combining simulation and experimental verification as the research method. This paper proposes to use special software AdvantEdge of metal finite element cutting to establish two-dimensional orthogonal cutting simulation model of aluminum alloy 7075-T651. Reasonable workpieces, tool material parameters and constitutive model are set. Through simulation analysis, the relationship between cutting force and cutting temperature, feed speed and depth of cut are studied and verified by experiments. Simulation and experimental results show that within a certain range, with the increase of feed speed and cutting depth, cutting force and cutting temperature increase. When cutting aluminum alloy 7075-T651, smaller depth of cutting and feed rate should be used.Keywords: AdvantEdge; aluminum alloy 7075-T651; cutting force; cutting temperature1 引言(Introduction)由于鋁合金7075-T651具有高比强度和良好的热加工性能,以及高韧性和良好的耐腐蚀性,近年来在航空航天、模具加工、机械设备以及夹具中得到了越来越多的应用[1-2]。
高速金属切削的摩擦分析及有限元模拟

-T r - Tr
式中: A、B、 n、 C、D、E 和 m 是由材料自身决定的
子表示:
常数; Tm 为 材料 的熔 点; T r 为室 温; T 为工 件 的瞬
f ( x ) = p 当 n ( x ) p, 0< x lp
( 2 a) 时温度; 为应变; 为应变速率。
f ( x ) = n ( x ) 当 n (x ) < p, lp < x lc ( 2b) 式中: f 为摩 擦 剪切 应力; p 是 工件 材 料的 剪切 强
刀刃倒角半径0012mm切削宽度1mm摩擦模型41库仑摩擦模型根据库仑摩擦定律r为了确定合适的摩擦因数作者应用平均摩擦因数法即通过试验得出多组切削力f和吃刀抗力f代入式46可得出相应的摩擦因数最后将所得的摩擦因数取平均值作为最终的摩擦因数
2007年 1月 第 32卷 第 1期
润滑与密封
LUBR ICAT ION ENG INEER ING
结摩擦区内, 摩擦 剪切应 力恒定; 在滑移 摩擦 区内, 摩擦因数恒定。前刀面上的摩擦剪切应力可由以下式
变、应变率和温度的函数。本研究使用的材料本构方
程为修改的 Johnson-Cook经验模型 [5] :
= (A + B n ) 1+ C ln (D - ET* m )
(3)
其中 T*
=
T Tm
表 2 切削工艺参数
进给量
0 075 mm
刀具后角
15 3
切削速度
300 m /m in 刀具前角
-7
刀刃倒角半径 0 012 mm
切削宽度
1 mm
根据库仑摩擦定律 f (x ) = n ( x ), 为 了确定合 适的摩擦因数 , 作者应用平 均摩擦因数 法, 即通过
金属切削过程模拟的有限元仿真

金属切削过程模拟的有限元仿真摘要: 本文在建立车削三维有限元模拟基础上,运用有限元对车削过程中车削的变形系数,工件与刀具的温度分布,切削力进行了模拟,并对结果进行了分析讨论。
该模拟的结果对实际工作有重要的现实作用。
关键词:切削 有限元 模拟1 绪 论1.1本课题的研究背景1.1.1微电子等领域突出的散热问题在现代工业领域,有很多专门用途的设备,它们的工作性能和工作效率取决于关键零件的结构和性能,如空气冷却器,热交换器的散热管,激光器热辐射表面,环保设备的过滤表面,螺纹表面等等。
我们把这类起特定作用的表面统称为“功能表面”。
这些表面大多数采用组装式结构(套装、镶嵌、钎焊、高频焊)、切削、滚压等方法加工。
早在19世纪中期,Jone 就提出在管内插入螺旋线以强化蒸汽的冷凝过程,从此人们就开始了在传热管等传热材料上进行翅加工技术的研究。
70年代出现能源危机,研究翅化管的加工技术及其强化传热机理有了进一步的发展,随着加工制造技术的不断进步,近20年来对强化换热元件的研究在化工、能源、制冷、航空、电子等工业部门有了很大的进展,各式各样的强化换热元件层出不穷,为提高传热效率作出了重要的贡献。
但是随着微电子及化工等领域,尤其是微电子领域对产品性能的无限追求,芯片集成度不断提高,带来致命的高热流密度,电子器件的冷却问题越来越突出。
英特尔公司负责芯片设计的首席执行官帕特-盖尔欣格指出,如果芯片耗能和散热的问题得不到解决,到2005年芯片上集成了2亿个晶体管时,就会热得象“核反应堆”,2010年时会达到火箭发射时高温气体喷射的水平,而到2015年就会与太阳的表面一样热。
目前芯片发热区域(cm cm 5.15.1 )上的功耗已超过105W ,且未来有快速增加的趋势。
芯片产生的这些热量如果不能及时散出,将使芯片温度升高而影响到电子器件的寿命及工作的可靠性,因而电子器件的有效散热方式已成为获得新一代电子产品的关键科学问题之一。
两种典型金属高速切削过程有限元模拟与分析的开题报告
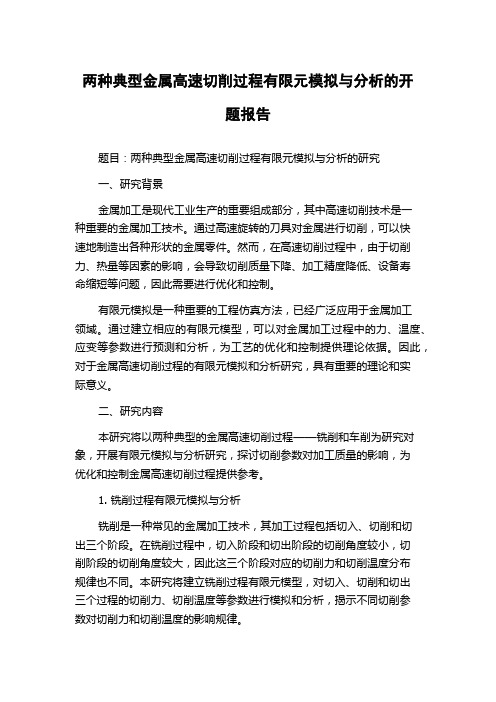
两种典型金属高速切削过程有限元模拟与分析的开题报告题目:两种典型金属高速切削过程有限元模拟与分析的研究一、研究背景金属加工是现代工业生产的重要组成部分,其中高速切削技术是一种重要的金属加工技术。
通过高速旋转的刀具对金属进行切削,可以快速地制造出各种形状的金属零件。
然而,在高速切削过程中,由于切削力、热量等因素的影响,会导致切削质量下降、加工精度降低、设备寿命缩短等问题,因此需要进行优化和控制。
有限元模拟是一种重要的工程仿真方法,已经广泛应用于金属加工领域。
通过建立相应的有限元模型,可以对金属加工过程中的力、温度、应变等参数进行预测和分析,为工艺的优化和控制提供理论依据。
因此,对于金属高速切削过程的有限元模拟和分析研究,具有重要的理论和实际意义。
二、研究内容本研究将以两种典型的金属高速切削过程——铣削和车削为研究对象,开展有限元模拟与分析研究,探讨切削参数对加工质量的影响,为优化和控制金属高速切削过程提供参考。
1. 铣削过程有限元模拟与分析铣削是一种常见的金属加工技术,其加工过程包括切入、切削和切出三个阶段。
在铣削过程中,切入阶段和切出阶段的切削角度较小,切削阶段的切削角度较大,因此这三个阶段对应的切削力和切削温度分布规律也不同。
本研究将建立铣削过程有限元模型,对切入、切削和切出三个过程的切削力、切削温度等参数进行模拟和分析,揭示不同切削参数对切削力和切削温度的影响规律。
2. 车削过程有限元模拟与分析车削是一种高效的金属加工技术,可以用于加工圆形、柱形等各种形状的零件。
在车削过程中,刀具切入工件后,与之接触的区域产生高温,导致金属发生塑性变形。
本研究将建立车削过程有限元模型,对切削力、切削温度等参数进行模拟和分析,揭示不同切削参数对加工质量的影响规律。
三、研究意义通过本研究,可以深入了解金属高速切削过程中的力学、热学和材料学等基本规律,为优化和控制切削过程提供理论依据。
此外,通过对不同切削参数对切削力、切削温度等参数的影响规律的分析,可以为金属加工工艺的优化和改进提供实用的建议和方法。
金属切削原理中切削力效果的仿真模拟研究

金属切削原理中切削力效果的仿真模拟研究随着工业技术的快速发展,金属切削加工在各个领域中都扮演着重要的角色。
而在金属切削加工过程中,切削力效果的研究对于提高切削加工的效率和质量具有重要的影响。
本文将以金属切削原理中切削力效果的仿真模拟研究为题,探讨金属切削过程中切削力的影响因素以及仿真模拟的方法。
首先,我们需要了解金属切削加工中切削力的概念和作用。
切削力是指在金属切削过程中刀具对工件产生的力。
它是通过与工件表面接触形成的摩擦力和切削力的合力,用于克服金属材料的强度和硬度,从而将金属材料切削成预定形状和尺寸的零件。
切削力直接影响着切削加工的效率、切削工具的寿命以及加工表面质量等方面。
在金属切削过程中,切削力的大小和方向受到多种因素的影响。
首先是刀具的几何形状和刀具材料的选择。
刀具的刃角、刃宽以及刀具材料的硬度和耐磨性等因素都会直接影响切削力的大小。
其次是被切削材料的性质。
材料的硬度、塑性和热导率等特性都会对切削力产生影响。
此外,切削速度、进给量和切削深度等工艺参数也会对切削力产生影响。
因此,研究这些影响因素对切削力的影响是非常必要的。
为了研究金属切削过程中切削力效果,研究人员常常采用仿真模拟的方法。
仿真模拟可以通过建立切削力的数学模型和计算机模拟技术,准确预测切削过程中的切削力大小和方向,并分析各种影响因素对切削力的影响。
其中,有限元法是一种常用的仿真模拟方法。
有限元法是一种数值计算方法,广泛应用于工程领域中的结构力学和材料力学问题。
在金属切削过程中,有限元法可以通过将切削区域划分成许多小块,建立小块上的切削力模型,并通过求解数学方程组来计算切削力的大小和方向。
通过调整模型中的参数,如刀具几何形状、工件材料特性、切削速度等,可以得到不同情况下的切削力效果。
此外,还可以使用商业仿真软件来进行金属切削过程中切削力效果的仿真模拟研究。
这些软件通过提供各种切削过程的模型和计算工具,能够更加方便地进行切削力的预测和分析。
金属材料超高速磨削温度场的实验研究与有限元仿真

S m u a i n a d Ex e i e t lRe e r h o m pe a u e Fi l n Ulr - i h Sp e i l to n p r m n a s a c fTe r t r ed i t a h g e d
21 0 2年 3月 第4 0卷 第 5期
机床与液压
MACHI NE O0L & HYDRAUL CS T I
M a .2 2 r 01
Vo . 0 No 5 14 .
DOI 1 . 9 9 jis. 0 1— 8 1 2 1 . 5 0 9 : 0 3 6 /.sn 1 0 3 8 . 0 2 0 . 0
Gr n ng o e a l a e i l i nie El m e tM e h d i di fM t li M t r a s Usng Fi t e n c to
YAN ng Yo . GU0 ,ZHANG o ua Li Gu h
( . h n saA rn ui l oai a a dT c ncl o ee 1 C a gh eo a t a V ct n l n eh i l g , c o aC l
h a o r e mo e sw r n lz d e t u c d l e e a ay e .T e a a y i r s l h w t a t e P ce u e a u ce s s g id n e t o n gi d s h n l ss e u t s o h t h t e lt mb r v e i r a e , rn ig h a w i rn - s wi h n L l n l f i g z n h n e r m h ra ge h a no a u i r h a .T e m ̄ i m rn ig tmp r t r s w t h w e ts u c d l a e n o e c a g sf o t e t n l e ti t n f m e t h i o mu g id n e e au e i te t o h a o r e mo es r h s l r u p e ri i e e t o i o s i h rn ig z n . i a ,b ta p a n d f r n st n n t e g d n o e mi f p i i Ke wo d :U t ih s e d g d n y rs l a h g p e n ig; G n i g t mp r t r ; T e mo o p e F n t l me tmeh d r i r d n e e a u e h r c u l ; i i e e n真
《0Cr18Ni9Ti-U71Mn摩擦副高速重载磨损行为的有限元模拟》范文
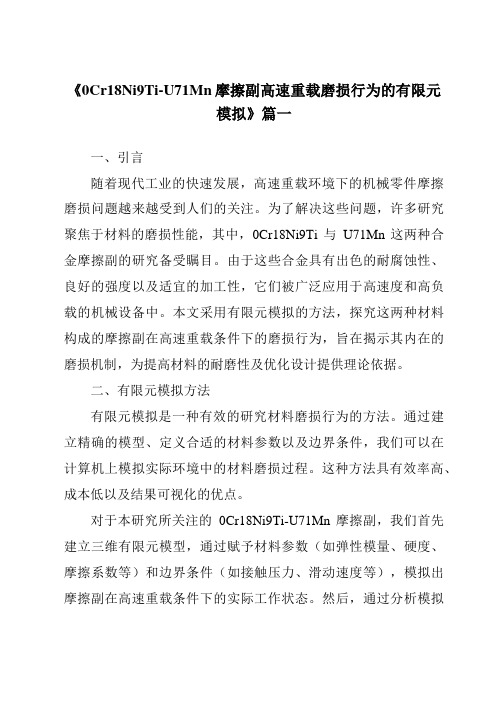
《0Cr18Ni9Ti-U71Mn摩擦副高速重载磨损行为的有限元模拟》篇一一、引言随着现代工业的快速发展,高速重载环境下的机械零件摩擦磨损问题越来越受到人们的关注。
为了解决这些问题,许多研究聚焦于材料的磨损性能,其中,0Cr18Ni9Ti与U71Mn这两种合金摩擦副的研究备受瞩目。
由于这些合金具有出色的耐腐蚀性、良好的强度以及适宜的加工性,它们被广泛应用于高速度和高负载的机械设备中。
本文采用有限元模拟的方法,探究这两种材料构成的摩擦副在高速重载条件下的磨损行为,旨在揭示其内在的磨损机制,为提高材料的耐磨性及优化设计提供理论依据。
二、有限元模拟方法有限元模拟是一种有效的研究材料磨损行为的方法。
通过建立精确的模型、定义合适的材料参数以及边界条件,我们可以在计算机上模拟实际环境中的材料磨损过程。
这种方法具有效率高、成本低以及结果可视化的优点。
对于本研究所关注的0Cr18Ni9Ti-U71Mn摩擦副,我们首先建立三维有限元模型,通过赋予材料参数(如弹性模量、硬度、摩擦系数等)和边界条件(如接触压力、滑动速度等),模拟出摩擦副在高速重载条件下的实际工作状态。
然后,通过分析模拟结果,我们可以了解材料的应力分布、温度变化以及磨损情况等关键信息。
三、高速重载磨损行为分析根据有限元模拟结果,我们分析了0Cr18Ni9Ti-U71Mn摩擦副在高速重载条件下的磨损行为。
首先,我们发现由于接触压力和滑动速度的增加,摩擦副的应力分布发生了显著变化。
在接触区域,应力集中现象明显,导致材料局部发生塑性变形和磨损。
此外,由于摩擦热的产生,接触区域的温度也显著升高,进一步加剧了材料的磨损。
在分析过程中,我们还发现0Cr18Ni9Ti和U71Mn两种材料在磨损过程中的表现有所不同。
0Cr18Ni9Ti由于具有较高的硬度和耐腐蚀性,在磨损过程中表现出较好的耐磨性。
而U71Mn虽然具有较高的强度和韧性,但在高温和高应力条件下容易发生软化,导致磨损加剧。
金属切削加工有限元模拟技术发展现状分析大学论文

金属切削加工有限元模拟技术发展现状分析摘要:随着科学技术的突飞猛进,人们对金属切削的掌握能力越来越高,同时也有了更高的要求,要求更高的效率,更高的精度,在这种情况下金属切削的有限元模拟技术应运而生,它的成本更低,操作更方便,对金属切削有很大的价值。
本文初步介绍了有限元法以及有限元法的当前发展,讨论了金属切削过程中有限元模型的类型,对所涉及的网格划分,刀-屑接触,以及分离准则等关键技术进行了研究。
关键词:金属切削:有限元法:刀-屑接触:有限元模拟Analysis of development status of finite element simulationtechnology for metal cutting processAbstract: With the rapid development of science and technology, people grasp of metal-cutting more and more, but also have higher requirements, requiring higher efficiency, higher accuracy, in this case the finite element simulation of metal cutting technology came into being, its lower cost, more convenient operation, the metal cutting is of great value.This paper introduces the current preliminary finite element method and finite element method, discussed the type of metal cutting process finite element model of the mesh covered knife - key technologies chip contact and separation criteria were studied.Keywords: Metal Cutting;Finite Element Method;tool-chip contact;Finite Element Simulation目录摘要................................................ 错误!未定义书签。
- 1、下载文档前请自行甄别文档内容的完整性,平台不提供额外的编辑、内容补充、找答案等附加服务。
- 2、"仅部分预览"的文档,不可在线预览部分如存在完整性等问题,可反馈申请退款(可完整预览的文档不适用该条件!)。
- 3、如文档侵犯您的权益,请联系客服反馈,我们会尽快为您处理(人工客服工作时间:9:00-18:30)。
Fr iction Ana lysis and F in ite Elem en t S i m ula tion s of H igh2speed M eta l Cuttin g
W a ng X iao Lu S hub in Gao C hua nyu
( J iangsu U niversity, Zhenjiang J iangsu 212013, China)
表 1 工件与刀具的材料特性
泊松比
013 0122
- 1 - 1 比热 / (J ・ kg ・ ℃ )
热传导率 / (W ・ m
5115 120
- 1
- 1 ・ ℃ )
热膨胀系数 / ( × 10
- 6
- 1 ℃ )
470 34313
113 ( 425 ℃) 114 ( 650 ℃) 512
3 切削模型
收稿日期 : 2006 - 06 - 19 作者简介 : 王霄 ( 1964 —) , 男 , 博士研究生 , 副教授 , 主要研 究方向 : 微造型及性能数值模拟 , CAD /CAE /CAM , 虚拟样机 技术等 1 E 2 mail: wx@ ujs1 edu1 cn1
在早期的切削加工分析中 , 普遍采用传统的库仑 摩擦理论 , 其认为前刀面上摩擦剪切应力与正应力成 正比 , 数学公式如下 : τ σn ( 1) f =μ σ μ 式中 : τ 为摩擦剪切应力 ; 是正应力 ; 是摩擦 f n 因数 。
和刀 2 屑接触长度的预测值更接近参考文献中的值 。 定性上说明了粘结 2 滑 移摩擦模型更符合金属切削的 实际摩擦模型 , 也证明了刀 2 屑接触表面上滑移摩擦 和粘结摩擦是同时存在的 。 6 结论 ( 1 ) 在金属正交切削过程中 , 刀 2 屑接触表面不 仅存在滑移摩擦 , 同时还存在粘结摩擦 。 ( 2 ) 所建立的滑移 2 粘结摩擦模型能较好地反映 了金属切削的真实摩擦状况 , 同时也说明了利用有限 元方法分析金属切削加工的过程是有效的手段 , 这为 切削的有限元分析提供了良好的理论基础 。
材料 工件材料 刀具材料 杨氏模量 / GPa
260 522 ( 20 ℃) 620 ( 100 ℃)
2 工件材料模型
切削过程中 , 由于温度 、应变和应变率的增加 , 工件材料在切削区域发生变形 。为了考虑这些因素对 材料特性的影响 , 可以将工件的流动应力看作是应 变 、应变率和温度的函数 。本研究使用的材料本构方 [5 ] 程为修改的 Johnson 2 Cook 经验模型 : n σ = ( A + Bε ) 1 + C ln ε ( D - ET3 m ) ( 3) 其中 T =
第 32 卷
Zorev 的研究 , 切屑与前刀面的接触表面上可划分为 滑移摩擦区域和粘结摩擦区域 , 如图 1 所示 。在靠近 切削刃的长度 lp 内 , 由于切削时产生的高温和高压 使得切屑底层材料软化 , 切屑底层的金属材料粘嵌在 前刀面上的 , 从而形成了粘结摩擦区域 。在此区域 内 , 摩擦剪切应力等于工件材料的剪切强度 τ p 。在 刀2 屑接触表面的剩余区域 lc 内 , 是滑移摩擦区 , 摩 擦剪切应力可用库仑摩擦定律计算 。也就是说 , 在粘 结摩擦区内 , 摩擦剪切应力恒定 ; 在滑移摩擦区内 , 摩擦因数恒定 。前刀面上的摩擦剪切应力可由以下式 子表示 : τ σn ( x ) ≥ τ ( 2a ) 当μ f ( x ) =τ p p , 0 < x ≤ lp τ σn ( x ) σn ( x ) <τ ( 2b ) 当μ f ( x ) =μ p , lp < x ≤ lc τ τ 式中 : f 为摩擦剪切应力 ; p 是工件材料的剪切强 度 ; σn 是正应力 ; μ是摩擦因数 。
Keywords: high 2speed cutting; finite element simulation; sticking2sliding; friction model
在机械制造的研究领域中 , 对金属切削过程的研 究一直是国内外研究的热点和难点 。有限元法在求解 非线性和多场耦合方面的强大功能日益明显 , 从而在 [1 - 2 ] 切削加工过程的研究中得到了广泛的应用 。用有 限元方法模拟金属切削加工过程 , 其预测结果主要受 到 2 个因素的影响 : ( 1 ) 切削区材料的流动应力特 性 ; (2) 刀 2 屑接触表面的摩擦特性 。当通过大应变 速率和温度变形试验获得了工件材料的本构模型 , 那 么材料流动应力的不确定性对有限元模拟的影响就会 大大降低 。在此前提下 , 正确地模拟刀 2 屑 接触表面 的摩擦状况是对金属切削过程进行数值模拟的关键 。 本文作者利用有限元通用软件 DEFORM 2 2D 在高速条 件下 , 模拟 P20 模具钢的切削过程 , 对刀 2 屑接触表 面的摩擦建立不同的摩擦模型 。本文的一个特点是通 过定义摩擦窗口 , 实现在一个摩擦模型中应用 2 种不 同的摩擦条件 , 模拟出更符合实际的摩擦模型 。 1 刀2 屑接触表面的摩擦分析
3
T - Tr Tm - T r
式中 : A、B 、 n、 C、D、 E 和 m 是由材料自身决定的 常数 ; Tm 为材料的熔点 ; T r 为室温 ; T 为工件的瞬 时温度 ; ε为应变 ; ε为应变速率 。 本文所选用工件材料为 P20 模具钢 , 刀具为未涂 层的 WC 材料 , 材料特性如表 1 所示 。
参考文献
【1 】谢峰 , 刘正士 , 杨海东 . 金属切削刀具前 、后刀面摩擦状 况的数值模拟 [ J ]. 应用科学学报 , 2004, 22 ( 2 ) : 223
- 227. Xie Feng, L iu Zhengshi, Yang Haidong. The Numerical Simu2 lation of Friction Status on the Rake Face and Flank Face of Cutting Tool [ J ]. Journal of App lied Sciences, 2004, 22 (2) : 223 - 227.
Abstract: Based on the updated Lagrangian finite element formulation, the si m ulations of orthogonal metal cutting were
conducted under high speed condition. The Coulomb friction model and sticking2sliding friction model were built up respec2 tively on the tool2chip interface. The p redictions of cutting force, thrusting force, chip thickness, tool2chip contact length were given in the simulations . According to the comparisons with experim ental data, the sticking2sliding friction model is found to be closer to the true model . It is shown that the sliding and the sticking friction exist simultaneously on the tool2 chip interface during the metal cutting .
表 2 切削工艺参数
进给量 切削速度 刀刃倒角半径
01075 mm 300 m /m in 01012 mm
σn ( x ) , 为了确定合 根据库仑摩擦定律 τ f ( x ) =μ 适的摩擦因数 μ , 作者应用平均摩擦因数法 , 即通过 试验得出多组切削力 Fc 和吃刀抗力 F t , 代入式 ( 4 ) 和 ( 5 ) 中 , 求 得 切 向 力 Ff 和 法 向 力 F n , 通 过 式 ( 6 ) 可得出相应的摩擦因数 , 最后将所得的摩擦因 数取 平 均 值 , 作 为 最 终 的 摩 擦 因 数 。根 据 试 验 数 [4 ] 据 , 算得平均摩擦因数 μ = 015。 α - F t sin α ( 4) Fn = Fc cos α + F t cos α ( 5) Ff = Fc sin μ=
Ff Fn ( 6)
刀具后角 刀具前角 切削宽度
1513 ° - 7° 1 mm来自412 粘结 2 滑移摩擦模型
图 2 切削模型与网格划分
4 摩擦模型 411 库仑摩擦模型
图 3 摩擦区的定义
本模型中 , 在刀 2 屑 表面上同时应用不同的摩擦
2007 年第 1 期
王 霄等 : 高速金属切削的摩擦分析及有限元模拟
图 1 前刀面的摩擦模型
在高速切削中 , 前刀面上的正应力和温度会迅速 增加 。当前刀面上的正应力超过一定的极限值后 , 用 传统的库仑摩擦理论所得出的摩擦剪切应力已经远远 大于实际的值 , 这时方程 ( 1 ) 就不能很好地反映工 件与刀具之间的摩擦剪切应力与正应力的关系 。根据
130
润滑与密封
图 4 切屑的形状
切削模拟的过 程 和切 屑的形状如图 4 所示 。采 用传统的库仑摩擦模型模 拟的切屑卷曲相对采用粘 结2 滑移 摩 擦 模 型 的 较 大 , 这是因为后者的切屑与刀 具之间具有粘附作用 , 不 易发生弯曲变形 。采用库 图 5 切削力 Fc 、背向 仑摩擦模型计算所得的单 力 F t 的预测值 位切削宽度上的切削力 Fc1 与试验值比较 和吃刀抗力 F t1 分别为 210 N /mm 和 104 N /mm; 采用粘结 2 滑移摩擦模型时 , 切 削力 Fc2和吃刀抗力 F t2 分别为 225 N /mm 和 140 N /