温度曲线设定
如何正确设定回流炉温度曲线

如何正确设定回流炉温度曲线前言红外回流焊是SMT大生产中重要的工艺环节,它是一种自动群焊过程,成千上万个焊点在短短几分钟内一次完成,其焊接质量的优劣直接影响到产品的质量和可靠性,对于数字化的电子产品,产品的质量几乎就是焊接的质量。
做好回流焊,人们都知道关键是设定回流炉的炉温曲线,有关回流炉的炉温曲线,许多专业文章中均有报导,但面对一台新的红外回流炉,如何尽快设定回流炉温度曲线呢?这就需要我们首先对所使用的锡膏中金属成分与熔点、活性温度等特性有一个全面了解,对回流炉的结构,包括加热温区的数量、热风系统、加热器的尺寸及其控温精度、加热区的有效长度、冷却区特点、传送系统等应有一个全面认识,以及对焊接对象--表面贴装组件(SMA)尺寸、组件大小及其分布做到心中有数,不难看出,回流焊是SMT工艺中复杂而又关键的一环,它涉及到材料、设备、热传导、焊接等方面的知识。
本文将从分析典型的焊接温度曲线入手,较为详细地介绍如何正确设定回流炉温度曲线,并实际介绍BGA以及双面回流焊的温度曲线的设定。
理想的温度曲线图1 理想的温度曲线图1是中温锡膏(Sn63/Sn62)理想的红外回流温度曲线,它反映了SMA通过回流炉时,PCB上某一点的温度随时间变化的曲线,它能直观反映出该点在整个焊接过程中的温度变化,为获得最佳焊接效果提供了科学的依据,从事SMT焊接的工程技术人员,应对理想的温度曲线有一个基本的认识,该曲线由四个区间组成,即预热区、保温区/活性区、回流区、冷却区,前三个阶段为加热区,最后一阶段为冷却区,大部分焊锡膏都能用这四个温区成功实现回流焊。
故红外回流炉均设有4-5个温度,以适应焊接的需要。
为了加深对理想的温度曲线的认识,现将各区的温度、停留时间以及焊锡膏在各区的变化情况,介绍如下:(1)预热区预热区通常指由室温升至150℃左右的区域。
在这个区域,SMA平稳升温,在预热区,焊膏中的部分溶剂能够及时挥发,元器件特别是IC器件缓缓升温,以适应以后的高温。
回流焊温度曲线测试操作指示
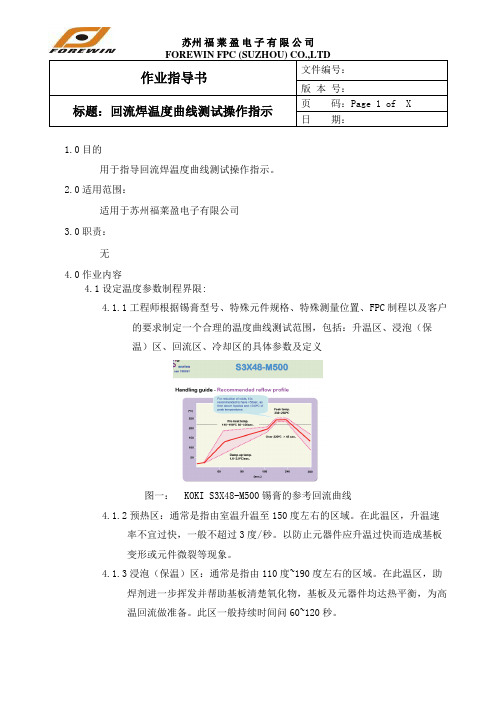
1.0目的用于指导回流焊温度曲线测试操作指示。
2.0适用范围:适用于苏州福莱盈电子有限公司3.0职责:无4.0作业内容4.1设定温度参数制程界限:4.1.1工程师根据锡膏型号、特殊元件规格、特殊测量位置、FPC制程以及客户的要求制定一个合理的温度曲线测试范围,包括:升温区、浸泡(保温)区、回流区、冷却区的具体参数及定义图一: KOKI S3X48-M500锡膏的参考回流曲线4.1.2预热区:通常是指由室温升温至150度左右的区域。
在此温区,升温速率不宜过快,一般不超过3度/秒。
以防止元器件应升温过快而造成基板变形或元件微裂等现象。
4.1.3浸泡(保温)区:通常是指由110度~190度左右的区域。
在此温区,助焊剂进一步挥发并帮助基板清楚氧化物,基板及元器件均达热平衡,为高温回流做准备。
此区一般持续时间问60~120秒。
4.1.4回流区:通常是指超过217度以上温度区域。
在此温区,焊膏很快熔化,迅速浸润焊接面,并与基板PAD形成新的合金焊接层,达到元件与PAD之间的良好焊接。
此区持续时间一般设定为:45~90秒。
最高温度一般不超过250度(除有特定要求外)。
4.1.5冷却区:该区为焊点迅速降温,将焊料凝固,使焊料晶格细化,提高焊接强度。
本区降温速率一般设置为-3~-1度/秒左右。
4.2测温板的制作4.2.1采用与生产料号一致的样品板作为测温板,制作测温板时,原则上应保留必要的具有代表性的测温元器件,以保证测试测量温度与实际生产温度保持一致。
4.2.2测温板与生产料号在无法保持一致情况下,经工程师验证认可,可使用与之同类型的测温板进行测量。
4.2.3测温点应该选择最具有代表性的区域及元件,比如最大及最小吸热量的元件,零件选取优先级(如Socket->Motor->大型BGA ->小型BGA->QFP或SOP->标准Chip)除此之外,还应选择介于两者之间的一个测温区。
如图:4.2.4一般测温点在每板上不得少于3个,有BGA或大型IC至少选取4个,基于特殊代表型元件为首选原则选取元件。
如何设定回流焊温度曲线

如何设定回流焊温度曲线如何设定回流焊温度曲线首先我们要了解回流焊的几个关键的地方及温度的分区情况及回流焊的种类.影响炉温的关键地方是:1:各温区的温度设定数值2:各加热马达的温差3:链条及网带的速度4:锡膏的成份5:PCB板的厚度及元件的大小和密度6:加热区的数量及回流焊的长度7:加热区的有效长度及泠却的特点等回流焊的分区情况:1:预热区(又名:升温区)2:恒温区(保温区/活性区)3:回流区4 :泠却区那么,如何正确的设定回流焊的温度曲线下面我们以有铅锡膏来做一个简单的分析(Sn/pb)一:预热区预热区通常指由室温升至150度左右的区域,在这个区域,SMA平稳升温,在预热区锡膏的部分溶剂能够及时的发挥。
元件特别是集成电路缓慢升温。
以适应以后的高温,但是由于SMA表面元件大小不一。
其温度有不均匀的现象。
在些温区升温的速度应控制在1-3度/S 如果升温太快的话,由于热应力的影响会导致陶瓷电容破裂/PCB变形/IC芯片损坏同时锡膏中的溶剂挥发太快,导致锡珠的产生,回流焊的预热区一般占加热信道长度的1/4—1/3 时间一般为60—120S二:恒温区所谓恒温意思就是要相对保持平衡。
在恒温区温度通常控制在150-170度的区域,此时锡膏处于融化前夕,锡膏中的挥发进一步被去除,活化剂开始激活,并有效的去除表面的氧化物,SMA表面温度受到热风对流的影响。
不同大小/不同元件的温度能够保持平衡。
板面的温差也接近最小数值,曲线状态接近水平,它也是评估回流焊工艺的一个窗口。
选择能够维持平坦活性温度曲线的炉子将提高SMA的焊接效果。
特别是防止立碑缺陷的产生。
通常恒温区的在炉子的加热信道占60—120/S的时间,若时间太长也会导致锡膏氧化问题。
导致锡珠增多,恒温渠温度过低时此时容易引起锡膏中溶剂得不到充分的挥发,当到回流区时锡膏中的溶剂受到高温容易引起激烈的挥发,其结果会导致飞珠的形成。
恒温区的梯度过大。
这意味着PCB的板面温度差过大,特别是靠近大元件四周的电阻/电容及电感两端受热不平衡,锡膏融化时有一个延迟故引起立碑缺陷。
回流焊炉温曲线的设定

图 5-5 锡银铜焊焊料;免洗工艺
32
图 5-6 锡铅焊料;水溶性助焊剂
图 5-7 锡银铜焊料;水溶性助焊剂
33
图 5-8 锡铅焊料;水溶性助焊剂
图 5-9 锡银铜焊料;水溶性助焊剂
34
图 5-10 锡银铜焊焊料;免洗工艺;氮气回流
图 5-11 锡银铜焊焊料;免洗工艺;空气回流
35
图 5-16 锡铅焊料(SnPb)
16
• 回流段: 在这一区域里加热器的温度设置得最高,使组件的温度快速上升至峰 值温度。在回流段其焊接峰值温度视所用焊膏的不同而不同,一般推 荐为焊膏为焊膏的溶点温度加20-40º C.对于熔点为183º C的63Sn/37Pb 焊膏和熔点为179º C的Sn62/Pb36/Ag2膏焊,峰值温度一般为210230º C/S,再流时间不要过长,以防对SMA造成不良影响。理想的温度 曲线是超过焊锡熔点的“尖端区”覆盖的体积最小。 • 冷却段 这段中焊膏中的铅锡粉末已经熔化并充分润湿被连接表面,应该用尽 可能快的速度来进行冷却,这样将有助于得到明亮的焊点并有好的外 形和低的接触角度。缓慢冷却会导致电路板的更多分解而进入锡中, 从而产生灰暗毛糙的焊点。在极端的情形下,它能引起沾锡不良和弱 焊点结合力。冷却段降温速率一般为3~4º C/S冷却至75º C即可。
240 220 200 180 160 140 120 100 80 60 40 20 0 0 30 60 90 120 150 180 210 240 270 300 <3° C/ Sec 1.3 - 1.6°C/Sec
Peak Temp.
210 - 225°C
0.5 - 0.6 °C/ Sec
Soaking Zone
讲师:王勇
炉温工艺曲线的设置方法

炉温工艺曲线的设置方法 High quality manuscripts are welcome to download如何设定出合格的炉温工艺曲线什么是回流焊:回流焊是英文Reflow是通过重新熔化预先分配到印制板焊盘上的膏装软钎焊料,实现表面组装元器件焊端或引脚与印制板焊盘之间机械与电气连接的软钎焊。
回流焊是将元器件焊接到PCB板材上,回流焊是专门针对SMD表面贴装器件的。
回流焊是靠热气流对焊点的作用,胶状的焊剂在一定的高温气流下进行物理反应达到SMD的焊接;之所以叫"回流焊"是因为气体在焊机内循环来回流动产生高温达到焊接目的。
(回流焊温度曲线图)“产品质量是生产出来的,不是检验出来,只有在生产过程中的每个环节,严格按照生产工艺和作业指导书要求进行,才能保证产品的质量。
电子厂SmT贴片焊接车间在SmT生产流程中,回流炉参数设置的好坏是影响焊接质量的关键,通过温度曲线,可以为回流炉参数的设置提供准确的理论依据,在大多数情况下,温度的分布受组装电路板的特性、焊膏特性和所用回流炉能力的影响。
如何正确的设定回流焊温度曲线:首先我们要了解回流焊的几个关键的地方及温度的分区情况及回流焊的种类.影响炉温的关键地方是:1:各温区的温度设定数值2:各加热马达的温差3:链条及网带的速度4:锡膏的成份5:PCB板的厚度及元件的大小和密度6:加热区的数量及回流焊的长度7:加热区的有效长度及泠却的特点等回流焊的分区情况:1:预热区(又名:升温区)2:恒温区(保温区/活性区)3:回流区4 :泠却区回流焊焊接影响工艺的因素:1.通常PLCC、QFP与一个分立片状元件相比热容量要大,焊接大面积元件就比小元件更困难些。
2.在回流焊炉中传送带在周而复使传送产品进行回流焊的同时,也成为一个散热系统,此外在加热部分的边缘与中心散热条件不同,边缘一般温度偏低,炉内除各温区温度要求不同外,同一载面的温度也差异。
3.产品装载量不同的影响。
流焊温度曲线设定)
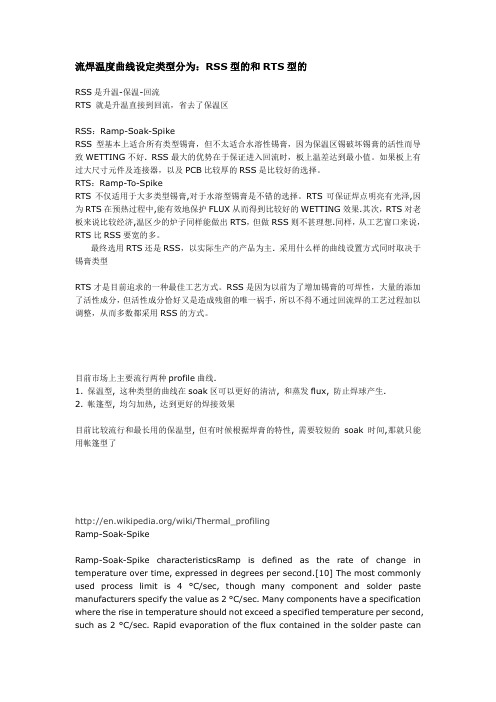
流焊温度曲线设定类型分为:RSS型的和RTS型的RSS是升温-保温-回流RTS 就是升温直接到回流,省去了保温区RSS:Ramp-Soak-SpikeRSS型基本上适合所有类型锡膏,但不太适合水溶性锡膏,因为保温区锡破坏锡膏的活性而导致WETTING不好. RSS最大的优势在于保证进入回流时,板上温差达到最小值。
如果板上有过大尺寸元件及连接器,以及PCB比较厚的RSS是比较好的选择。
RTS:Ramp-To-SpikeRTS不仅适用于大多类型锡膏,对于水溶型锡膏是不错的选择。
RTS可保证焊点明亮有光泽,因为RTS在预热过程中,能有效地保护FLUX从而得到比较好的WETTING效果.其次,RTS对老板来说比较经济,温区少的炉子同样能做出RTS,但做RSS则不甚理想.同样,从工艺窗口来说,RTS比RSS要宽的多。
最终选用RTS还是RSS,以实际生产的产品为主. 采用什么样的曲线设置方式同时取决于锡膏类型RTS才是目前追求的一种最佳工艺方式。
RSS是因为以前为了增加锡膏的可焊性,大量的添加了活性成分,但活性成分恰好又是造成残留的唯一祸手,所以不得不通过回流焊的工艺过程加以调整,从而多数都采用RSS的方式。
目前市场上主要流行两种profile曲线.1. 保温型, 这种类型的曲线在soak区可以更好的清洁, 和蒸发flux, 防止焊球产生.2. 帐篷型, 均匀加热, 达到更好的焊接效果目前比较流行和最长用的保温型, 但有时候根据焊膏的特性, 需要较短的soak时间,那就只能用帐篷型了/wiki/Thermal_profilingRamp-Soak-SpikeRamp-Soak-Spike characteristicsRamp is defined as the rate of change in temperature over time, expressed in degrees per second.[10] The most commonly used process limit is 4 °C/sec, though many component and solder paste manufacturers specify the value as 2 °C/sec. Many components have a specification where the rise in temperature should not exceed a specified temperature per second, such as 2 °C/sec. Rapid evaporation of the flux contained in the solder paste canlead to defects, such as lead lift, tombstoning, and solder balls. Additionally, rapid heat can lead to steam generation within the component if the moisture content is high, resulting in the formation of microcracks.[11]In the soak segment of the profile, the solder paste approaches a phase change. The amount of energy introduced to both the component and the PCB approaches equilibrium. In this stage, most of the flux evaporates out of the solder paste. The duration of the soak varies for different pastes. The mass of the PCB is another factor that must be considered for the soak duration. An over-rapid heat transfer can cause solder splattering and the production of solder balls, bridging and other defects. If the heat transfer is too slow, the flux concentration may remain high and result in cold solder joints, voids and incomplete reflow.[12]After the soak segment, the profile enters the ramp-to-peak segment of the profile, which is a given temperature range and time exceeding the melting temperature of the alloy. Successful profiles range in temperature up to 30 °C higher than liquidus, which is approximately 183 °C for eutectic and approximately 217 °C for lead-free.[13]The final area of this profile is the cooling section. A typical specification for the cool down is usually less than −6 °C/sec (falling slope).[14][edit] Ramp-to-SpikeRamp-To-Spike characteristicsThe Ramp to Spike (RTS) profile is almost a linear graph, starting at the entrance of the process and ending at the peak segment, with a greater Δt (change in temperatu re) in the cooling segment. While the Ramp-Soak-Spike (RSS) allows for about 4 °C/sec, the requirements of the RTS is about 1–2 °C/sec. These values depend on the solder paste specifications. The RTS soak period is part of the ramp and is not as easily distinguishable as in RSS. The soak is controlled primarily by the conveyor speed. The peak of the RTS profile is the endpoint of the linear ramp to the peak segment of the profile. The same considerations about defects in an RSS profile also apply to an RTS profile.[15]When the PCB enters the cooling segment, the negative slope generally is steeper than the rising slope.[16][edit] Thermocouple attachmentsThermocouples are two dissimilar metals joined by a welded bead. For a thermocouple to read the temperature at any given point, the welded bead must come in direct contact with the object whose temperatures need to be measured. The two dissimilar wires must remain separate, joined only at the bead; otherwise, the reading is no longer at the welded bead but at the position where the metals first make contact, rendering the reading invalid.[17]A zigzagging thermocouple reading on a profile graph indicates loosely attached thermocouples. For accurate readings, thermocouples are attached to areas that are dissimilar in terms of mass, location and known trouble spots. Additionally, they should be isolated from air currents. Finally, the placement of several thermocouples should range from populated to less populated areas of the PCB for the best sampling conditions.[18]Several methods of attachment are used, including epoxy, high-temperature solder, Kapton and aluminum tape, each with various levels of success for each method.[19]Epoxies are good at securing TC conductors to the profile board to keep them from becoming entangled in the oven during profiling. Epoxies come in both insulator and conductor formulations The specs need to be checked otherwise an insulator can play a negative role in the collection of profile data. The ability to apply this adhesive in similar quantities and thicknesses is difficult to measure in quantitative terms. This decreases reproducibility. If epoxy is used, properties and specifications of that epoxy must be checked. Epoxy functions within a wide range of temperature tolerances.[19]The properties of solder used for TC attachment differ from that of electrically connective solder. High temperature solder is not the best choice to use for TC attachment for several reasons. First, it has the same drawbacks as epoxy – the quantity of solder needed to adhere the TC to a substrate varies from location to location. Second, solder is conductive and may short-circuit TCs. Generally, there is a short length of conductor that is exposed to the temperature gradient. Together, this exposed area, along with the physical weld produce an Electromotive Force (EMF). Conductors and the weld are placed in a homogeneous environment within the temperature gradient to minimize the effects of EMF.[19]Kapton tape is one of the most widely used tapes and methods for TC and TC conductor attachment. When several layers are applied, each layer has an additive effect on the insulation and may negatively impact a profile. A disadvantage of this tape is that the PCB has to be very clean and smooth to achieve an airtight cover over the thermocouple weld and conductors.[19] Another disadvantage to Kapton tape is that at temperatures above 200 °C the tape becomes elastic and, hence, the TCs have a tendency to lift off the substrate surface. The result is erroneous readings characterized by jagged lines in the profile.Aluminum tape comes in various thicknesses and density. Heavier aluminum tape can defuse the heat transfer through the tape and act as an insulator. Low density aluminum tape allows for heat transfer to the EMF-producing area of the TC. The thermal conductivity of the aluminum tape allows for even conduction when the thickness of the tape is fairly consistent in the EMF-producing area of thethermocouple。
波峰焊炉温曲线设定规范

工程管理波峰焊炉温曲线设定规范PAGE4 OF5 REV A6.5.4.1使用有铅系列焊锡(Sn63/Pb37)炉温Profile 的如下:Solder peak temperature : 220- 245℃Preheat completed temperature: 80-120℃ Preheat Time (Temperature from80℃ to 120℃): 50-100 sec Soak Time (Temperature above 183℃): 2-9 sec6.5.5 炉温稳定性曲线测试:对各线波峰焊用标准测试样板及标准Profile 测量波峰焊炉的炉温, 测出的Profile 与 标准Profile (如附件二所示)进行比较, Solder peak temperature deviation < 5℃ Preheat completed temperature deviation < 5℃Solder Time (Temperature abov e 183℃) deviation < 2 sec如果偏差值在以上范围内﹐证明此炉稳定, 可量产用﹔若不符合标准, 及时通知设备工程师确认6.5.6 若对波峰焊炉有重大的维修, 维修后则重复6.5.5 6.6标准测试样板炉温曲线Profile 量测规定:6.6.1 每周一次用标准测试样板对各波峰焊炉以标准炉温参数测量.6.6.2 测定完成后将炉温曲线打印出来, 经由主管确认符合规格后置于对应的波峰焊炉上即可正常生产6.6.3所有的炉温曲线图应保存在规定的文件夹和计算机指定的地方存盘以利备查, 炉温曲线 6.7备注:Preheat Solder soakSolder peak TempPreheat completed Temp。
温度曲线的设定

温度曲线的设定温度曲线是由回流焊炉的多个参数共同作用的结果,其中起决定性作用的两个参数是传送带速度和温区的温度设定。
传送带速度决定了印刷线路板暴露在每个温区的持续时间,增加持续时间可以使印刷线路板上元器件的温度更加接近该温区的设定温度。
每个温区所用的持续时间的总和又决定了整个回流过程的处理时间。
每个温区的温度设定影响印刷线路板通该温区时温度的高低。
印刷线路板在整个回流焊接过程中的升温速度则是传送带速和各温区的温度设定两个参数共同作用的结果。
因此只有合理的设定炉温参数才能得到理想的炉温曲线。
现以最为常用的RSS曲线为例介绍一下炉温曲线的设定方法。
链速的设定:设定温度曲线时第一个要考虑参数是传输带的速度设定,该设定将决定印刷线路板通过加热通道所花的时间。
传送带速度的设定可以通过计算的方法获得。
这里要引入一个指标,负载因子。
负载因子:F=L/(L+s) L=基板的长,S=基板与基板间的间隔。
负载因子的大小决定了生产过程中炉内的印刷线路板对炉内温度的影响程度。
负载因子的数值越大炉内的温度越不稳定,一般取值在0.5~0.9之间。
在权衡了效率和炉温的稳定程度后建议取值为0.7-0.8。
在知道生产的板长和生产节拍后就可以计算出传送带的传送速度(最慢值)。
传送速度(最慢值)=印刷线路板长/0.8/生产节拍。
传送速度(最快值)由锡膏的特性决定,绝大多数锡膏要求从升温开始到炉内峰值温度的时间应不少于180秒。
这样就可以得出传送速度(最大值)=炉内加热区的长度/180S。
在得出两个极限速度后就可以根据实际生产产品的难易程度选取适当的传送速度一般可取中间值。
温区温度的设定:一个完整的RSS炉温曲线包括四个温区。
分别为:预热区:其目的是将印刷线路板的温度从室温提升到锡膏内助焊剂发挥作用所需的活性温度135℃,温区的加热速率应控制在每秒1~3℃,温度升得太快会引起某些缺陷,如陶瓷电容的细微裂纹。
保温区:其目的是将印刷线路板维持在某个特定温度范围并持续一段时间,使印刷线路板上各个区域的元器件温度相同,减少他们的相对温差,并使锡膏内部的助焊剂充分的发挥作用,去除元器件电极和焊盘表面的氧化物,从而提高焊接质量。
- 1、下载文档前请自行甄别文档内容的完整性,平台不提供额外的编辑、内容补充、找答案等附加服务。
- 2、"仅部分预览"的文档,不可在线预览部分如存在完整性等问题,可反馈申请退款(可完整预览的文档不适用该条件!)。
- 3、如文档侵犯您的权益,请联系客服反馈,我们会尽快为您处理(人工客服工作时间:9:00-18:30)。
如何正确设定回流炉温度曲线正确设定回流炉温度曲线是获得优良焊接质关键前言红外回流焊是SMT大生产中重要的工艺环节,它是一种自动群焊过程,成千上万个焊点在短短几分钟内一次完成,其焊接质量的优劣直接影响到产品的质量和可靠性,对于数字化的电子产品,产品的质量几乎就是焊接的质量。
做好回流焊,人们都知道关键是设定回流炉的炉温曲线,有关回流炉的炉温曲线,许多专业文章中均有报导,但面对一台新的红外回流炉,如何尽快设定回流炉温度曲线呢?这就需要我们首先对所使用的锡膏中金属成分与熔点、活性温度等特性有一个全面了解,对回流炉的结构,包括加热温区的数量、热风系统、加热器的尺寸及其控温精度、加热区的有效长度、冷却区特点、传送系统等应有一个全面认识,以及对焊接对象--表面贴装组件(SMA)尺寸、组件大小及其分布做到心中有数,不难看出,回流焊是SMT工艺中复杂而又关键的一环,它涉及到材料、设备、热传导、焊接等方面的知识。
本文将从分析典型的焊接温度曲线入手,较为详细地介绍如何正确设定回流炉温度曲线,并实际介绍BGA以及双面回流焊的温度曲线的设定。
理想的温度曲线图1是中温锡膏(Sn63/Sn62)理想的红外回流温度曲线,它反映了SMA通过回流炉时,PCB上某一点的温度随时间变化的曲线,它能直观反映出该点在整个焊接过程中的温度变化,为获得最佳焊接效果提供了科学的依据,从事SMT焊接的工程技术人员,应对理想的温度曲线有一个基本的认识,该曲线由四个区间组成,即预热区、保温区/活性区、回流区、冷却区,前三个阶段为加热区,最后一阶段为冷却区,大部分焊锡膏都能用这四个温区成功实现回流焊。
故红外回流炉均设有4-5个温度,以适应焊接的需要。
图1 理想的温度曲线为了加深对理想的温度曲线的认识,现将各区的温度、停留时间以及焊锡膏在各区的变化情况,介绍如下:(1)预热区预热区通常指由室温升至150℃左右的区域。
在这个区域,SMA平稳升温,在预热区,焊膏中的部分溶剂能够及时挥发,元器件特别是IC器件缓缓升温,以适应以后的高温。
但SMA 表面由于元器件大小不一,其温度有不均匀现象,在预热区升温的速率通常控制在1.5℃-3℃/sec。
若升温太快,由于热应力的作用,导致陶瓷电容的细微裂纹、PCB变形、IC芯片损坏,同时锡膏中溶剂挥发太快,导致飞珠的发生。
炉子的预热区一般占加热信道长度的1/4-1/3,其停留时间计算如下:设环境温度为25℃,若升温速率按3℃/sec计算则(150-25)/3即为42sec,若升温速率按1.5℃/sec计算则(150-25)/ 1.5即为85sec。
通常根据组件大小差异程度调整时间以调控升温速率在2℃/sec以下为最佳。
(2)保温区/活性区保温区又称活性区,在保温区温度通常维持在150℃±10℃的区域,此时锡膏处于熔化前夕,焊膏中的挥发物进一步被去除,活化剂开始激活,并有效地去除焊接表面的氧化物,SMA 表面温度受热风对流的影响,不同大小、不同质地的元器件温度能保持均匀,板面温度差△T接近最小值,曲线形态接近水平状,它也是评估回流炉工艺性的一个窗口,选择能维持平坦活性温度曲线的炉子将提高SMA的焊接效果,特别是防止立碑缺陷的产生。
通常保温区在炉子的二、三区之间,维持时间约60-120s,若时间过长也会导致锡膏氧化问题,以致焊接后飞珠增多。
(3)回流区回流区的温度最高,SMA进入该区后迅速升温,并超出锡膏熔点约30℃-40℃,即板面温度瞬时达到215℃-225℃(此温度又称之为峰值温度),时间约为5-10sec,在回流区焊膏很快熔化,并迅速润湿焊盘,随着温度的进一步提高,焊料表面张力降低,焊料爬至组件引脚的一定高度,形成一个"弯月面"。
从微观上看,此时焊料中的锡与焊盘中的铜或金由于扩散作用而形成金属间化合物,以锡铜合金为例,当锡膏熔化后,并迅速润湿铜层,锡原子与铜原子在其界面上互相渗透初期Sn-Cu合金的结构为Cu6Sn5,其厚度为1-3μ,若时间过长、温度过高时,Cu原子进一步渗透到Cu6Sn5中,其局部组织将由Cu6Sn5转变为Cu3Sn合金,前者合金焊接强度高,导电性能好,而后者则呈脆性,焊接强度低、导电性能差,SMA 在回流区停留时间过长或温度超高会造成PCB板面发黄、起泡、以致元器件损坏。
SMA在理想的温度下回流,PCB色质保持原貌,焊点光亮。
在回流区,锡膏熔化后产生的表面张力能适度校准由贴片过程中引起的元器件引脚偏移,但也会由于焊盘设计不正确引起多种焊接缺陷,如"立碑"、"桥联"等。
回流区的升温速率控制在2.5-3℃/sec,一般应在25sec-30sec 内达到峰值温度。
(4)冷却区SMA运行到冷却区后,焊点迅速降温,焊料凝固。
焊点迅速冷却可使焊料晶格细化,结合强度提高,焊点光亮,表面连续呈弯月面状。
通常冷却的方法是在回流炉出口处安装风扇,强行冷却。
新型的回流炉则设有冷却区,并采用水冷或风冷。
理想的冷却曲线同回流区升温曲线呈镜面对称分布。
在大生产中,每个产品的实际工作曲线,应根据SMA大小、组件的多少及品种反复调节才能获得,从时间上看,整个回流时间为175sec-295sec即3分钟-5分钟左右,(不包括进入第一温区前的时间)。
温度曲线的设定1、测试工具:在开始测定温度曲线之前,需要有温度测试仪,以及与之相配合的热电偶,高温焊锡丝、高温胶带以及待测的SMA,当然有的回流炉自身带有温度测试仪,(设在炉体内),但因附带的热电偶较长,使用不方便,不如专用温度测试记录仪方便。
特别这类测试仪所用的小直径热电偶,热量小、响应快、得到的结果精确。
2、热电偶的位置与固定热电偶的焊接位置也是一个应认真考虑的问题,其原则是对热容量大的组件焊盘处别忘了放置热电偶,见图2,此外对热敏感组件的外壳,PCB上空档处也应放置热电偶,以观察板面温度分布状况。
图2 热电偶的位置将热电偶固定在PCB上最好的方法是采用高温焊料(Sn96Ag4)焊接在所需测量温度的地方,此外还可用高温胶带固定,但效果没有直接焊接的效果好。
总之根据SMA大小以及复杂减度设有3个或更多的电偶。
电偶数量越多,其对了解SMA板面的受热情况越全面。
3、锡膏性能对于所使用锡膏的性能参数也是必须考虑的因素之一,首先是考虑到其合金的熔点,即回流区温度应高于合金熔点的30-40℃。
其次应考虑锡膏的活性温度以及持续的时间,有条件时应与锡膏供应商了解,也可以参考供应商提供的温度曲线。
4.炉子的结构:对于首次使用的回流炉,应首先考察一下炉子的结构。
看一看有几个温区,有几块发热体,是否独立控温。
热电偶放置在何处。
热风的形成与特点,是否构成温区内循环,风速是否可调节。
每个加热区的长度以及加热温区的总长度。
目前使用的红外回流炉,一般有四个温区,每个加热区有上下独立发热体。
热风循环系统各不相同,但基本上能保持各温区独立循环。
通常第一温区为预热区,第二、三温区为保温区,第四温区为回流区,冷却温区为炉外强制冷风,近几年来也出现将冷却区设在炉内,并采用水冷却系统。
当然这类炉子其温区相应增多,以至出现八温区以上的回流炉。
随着温区的增多,其温度曲线的轮廓与炉子的温度设置将更加接近,这将会方便于炉温的调节。
但随着炉子温区增多,在生产能力增加的同时其能耗增大、费用增多。
5、炉子的带速:设定温度曲线的第一个考虑的参数是传输带的速度设定,故应首先测量炉子的加热区总长度,再根据所加工的SMA尺寸大小、元器件多少以及元器件大小或热容量的大小决定SMA 在加热区所运行的时间。
正如前节所说,理想炉温曲线所需的焊接时间约为3-5分钟,因此不难看出有了加热区的长度,以及所需时间,就可以方便地计算出回流炉运行速度。
各区温度设定:接下来必须设定各个区的温度,通常回流炉仪表显示的温度仅代表各加热器内热电偶所处位置的温度,并不等于SMA经过该温区时其板面上的温度。
如果热电偶越靠近加热源,显示温度会明显高于相应的区间温度,热电偶越靠近PCB的运行信道,显示温度将越能反应区间温度,因此可打开回流炉上盖了解热电偶所设定的位置。
当然也可以用一块试验板进行模拟测验,找出PCB上温度与表温设定的关系,通过几次反复试验,最终可以找出规律。
当速度与温度确定后,再适当调节其它参数如冷却风扇速度,强制空气或N2流量,并可以正式使用所加工的SMA进行测试,并根据实测的结果与理论温度曲线相比较或与锡膏供应商提供的曲线相比较。
并结合环境温度、回流峰值温度、焊接效果、以及生产能力适当的协调。
最后将炉子的参数记录或储存以备后用。
虽然这个过程开始较慢和费力,但最终可以以此为依据取得熟练设定炉温曲线的能力。
两种典型的温度曲线设定1、BGA焊接温度的设定BGA是近几年使用较多的封装器件,由于它的引脚均处于封装体的下方,因为焊点间距较大(1.27mm)焊接后不易出现桥连缺陷,但也带来一些新问题,即焊点易出现空洞或气泡,而在QFP或PLCC器件的焊接中,这类缺陷相对的要少得多。
就其原因来说这与BGA焊点在其下方阴影效应大有关。
故会出现实际焊接温度比其它元器件焊接温度要低的现状,此时锡膏中溶剂得不到有效的挥发,包裹在焊料中。
图3为实际测量到的BGA器件焊接温度。
图中,第一根温度曲线为BGA外侧,第二根温度曲线为BGA焊盘上,它是通过在PCB上开一小槽,并将热电偶伸入其中,两温度上升为同步上升,但第二根温度曲线显示出的温度要低8℃左右,这是BGA体积较大,其热容量也较大的缘故,故反映出组件体内的温度要低,这就告诉我们,尽管热电偶放在BGA体的外侧仍不能如实地反映出BGA焊点处的温度。
因此实际工作中应尽可能地将热电偶伸入到BGA体下方,并调节BGA的焊接温度使它与其它组件温度相兼容。
图3 BGA温度测试点的选择2、双面板焊接温度的设定早期对双面板回流焊接时,通常要求设计人员将器件放在PCB的一侧,而将阻容组件放在另一侧,其目的是防止第二面焊接时组件在二次高温时会脱落。
但随着布线密度的增大或SMA功能的增多,PCB双面布有器件的产品越来越多,这就要求我们在调节炉温曲线时,不仅在焊接面设定热电偶而且在反面也应设定热电偶,并做到在焊接面的温度曲线符合要求的同时,SMA反面的温度最高值不应超过锡膏熔化温度(179℃),见图4图4 双面板焊接温度曲线从图中看出当焊接面的温度达到215℃时反面最高温度仅为165℃,未达到焊膏熔化温度。
此时SMA反面即使有大的元器件,也不会出现脱落现象。
常见有缺陷的温度曲线下列温度曲线是设定时常见的缺陷:1、活性区温度梯度过大立碑是片式组件常见的焊接缺陷,引起的原因是由于组件焊盘上的锡膏熔化时润湿力不平衡,导致组件两端的力距不平衡故易引起组件立碑。