不锈钢堆焊
《2024年无铋不锈钢FCAW堆焊工艺优化》范文

《无铋不锈钢FCAW堆焊工艺优化》篇一一、引言随着现代工业的快速发展,堆焊技术作为一项重要的金属加工技术,其应用领域越来越广泛。
无铋不锈钢FCAW(Flux Cored Arc Welding)堆焊工艺作为一种新兴的堆焊方法,具有较高的堆焊质量和生产效率。
然而,由于堆焊过程中的复杂性和多变性,仍存在一些问题需要进一步研究和优化。
本文旨在探讨无铋不锈钢FCAW堆焊工艺的优化方法,以提高堆焊质量和生产效率。
二、无铋不锈钢FCAW堆焊工艺概述无铋不锈钢FCAW堆焊工艺是一种以熔化极气体保护焊为基础的堆焊方法。
该工艺采用无铋填充材料,通过电弧熔化并喷涂在基材表面,形成一层新的金属层。
该工艺具有焊接速度快、热影响区小、焊接变形小等优点,广泛应用于机械制造、石油化工、航空航天等领域。
三、无铋不锈钢FCAW堆焊工艺存在的问题尽管无铋不锈钢FCAW堆焊工艺具有诸多优点,但在实际应用中仍存在一些问题。
主要包括:1. 堆焊质量不稳定:受焊接参数、填充材料、基材表面状态等因素影响,堆焊质量存在波动。
2. 生产效率有待提高:焊接过程中产生的飞溅、烟尘等问题会影响生产效率。
3. 环境保护问题:焊接过程中产生的烟尘和气体对环境造成一定污染。
四、无铋不锈钢FCAW堆焊工艺优化方法针对无铋不锈钢FCAW堆焊工艺存在的问题,我们提出以下优化方法:1. 优化焊接参数:通过调整电流、电压、焊接速度等参数,使焊接过程更加稳定,从而提高堆焊质量。
2. 改进填充材料:研发新型无铋填充材料,提高其与基材的匹配性,降低焊接过程中的飞溅和烟尘。
3. 引入自动化技术:采用自动化设备进行堆焊,减少人为因素对焊接质量的影响,提高生产效率。
4. 优化烟尘处理系统:改进烟尘处理系统,减少对环境的污染。
五、实施与效果通过上述优化方法,我们对无铋不锈钢FCAW堆焊工艺进行了实践。
实践结果表明,优化后的工艺显著提高了堆焊质量和生产效率,降低了烟尘排放,取得了良好的效果。
奥氏体不锈钢堆焊的层间温度

奥氏体不锈钢堆焊的层间温度奥氏体不锈钢是一种常用的材料,具有优良的耐腐蚀性和机械性能。
在工业生产中,有时需要进行堆焊修复或涂覆保护层等工艺,这就涉及到奥氏体不锈钢的层间温度问题。
本文将围绕这一问题展开讨论。
我们需要了解奥氏体不锈钢的特性。
奥氏体不锈钢是由铁、铬、镍等元素组成的合金材料,其中铬的含量通常在10.5%以上。
这使得奥氏体不锈钢具有良好的耐腐蚀性能,能够在潮湿、酸性或碱性环境中长期使用而不生锈。
同时,奥氏体不锈钢还具有良好的机械性能,强度高、韧性好,适用于各种工程和制造领域。
在堆焊过程中,层间温度是一个重要的考虑因素。
层间温度过高会导致奥氏体不锈钢的组织发生变化,甚至出现晶间腐蚀和脆化现象,降低了材料的性能。
因此,在进行奥氏体不锈钢堆焊时,需要控制好层间温度,避免出现过高的情况。
那么,如何控制奥氏体不锈钢的层间温度呢?首先,我们可以通过合理的焊接参数来控制层间温度。
焊接参数包括焊接电流、焊接电压、焊接速度等。
通过调整这些参数,可以控制焊接过程中的热输入量,从而控制层间温度。
此外,还可以采用预热和后热处理等措施,来提高焊接接头的温度均匀性,减少层间温度的差异。
选择合适的焊接材料也是控制层间温度的关键。
一些特殊的堆焊材料,如钎焊材料、焊条等,具有较低的熔点和热导率,可以有效降低层间温度。
此外,还可以选择一些具有良好热导性能的辅助材料,如铜垫片、铝垫片等,来加速热量的传导,降低焊接过程中的温度梯度,减少层间温度的差异。
焊接过程中的气氛环境也会对层间温度产生影响。
一些气氛中含有氧气、氢气等活泼元素的环境,会加剧奥氏体不锈钢的氧化和脱氢反应,导致层间温度升高。
因此,在焊接过程中,需要采取相应的保护措施,如使用惰性气体保护、减少气氛中的杂质含量等,来降低层间温度的升高。
奥氏体不锈钢的层间温度对于堆焊修复等工艺是一个重要的问题。
通过合理控制焊接参数、选择合适的焊接材料、调整焊接气氛等措施,可以有效降低层间温度,保证奥氏体不锈钢在堆焊过程中的性能和质量。
20MnMo超厚锻件不锈钢堆焊工艺4页word文档

20MnMo超厚锻件不锈钢堆焊工艺1 前言粗甲醇水冷器设备管板为20MnMo锻件堆焊不锈钢耐蚀层,尺寸为φ2700×400mm堆焊耐蚀层厚度为6mm。
由于堆焊工作量大、工期紧我们决定采用埋弧自动带极堆焊,对锻件边缘无法进行带极堆焊的部位采用焊条电弧焊。
2 焊接性分析及对策20MnMo锻件的供货热处理状态为淬火+回火(Q+T),经过淬火+回火后的显微组织是回火低碳马氏体、下贝氏体或回火索氏体,这类组织虽然可以保证较高的力学性能但在焊接?嵊跋烨?容易产生冷裂纹和韧性下降[1]。
焊接热影响区韧性下降的问题可以通过控制焊接热输入的大小的方法来解决,焊接热输入的大小已通过事先的焊接工艺评定验证进行了验证。
本文着重介绍施焊过程中为预防焊接冷裂纹的产生所采取的措施。
众所周知,焊接冷裂纹产生的三要素是拘束应力、扩散氢以及淬硬倾向。
超厚20MnMo锻件调质状态下的淬硬倾向以及拘束应力敏感性都很大。
待施焊的管板是厚度达到400mm的超厚锻件,厚度的增加直接导致了焊接过程中产生较大的拘束应力,同时厚度较大如果预热不均匀也会产生较大的内应力。
为了防止冷裂纹的产生施工过程中我们从拘束应力、扩散氢以及淬硬倾向三个方面采取了如下措施:(1)严格清理待焊表面铁锈、氧化皮、油污等;(2)严格按要求烘干焊条、焊剂;(3)预热采用大型加热炉进行炉内预热保证预热均匀;(4)预热好后出炉将除了待堆焊面外的各个面用保温石棉包裹防止热量散失过快;(5)焊接过程中停止施焊或焊接完成后应进行焊后消氢处理;(6)焊后进行消除应力热处理。
3 减小焊接变形埋弧自动带极堆焊的热输入较大,为防止管板产生超差变形我们在生产过程中采用中心对称交叉的焊接顺序。
沿着中心线将圆周按逆时针标注为0°、90°、180°、360°,第1层的第1道沿直径从0°方向起弧焊到180°熄弧;第2道从直径的右侧从180°方向启弧焊到0°熄弧;第3道从直径的左侧从0°方向启弧焊到180°熄弧,按如此规律上下两半圆周对称施焊且相邻两焊道(即2和4道,3和5道)的施焊方向相反。
不锈钢带极堆焊质量问题及控制措施【建筑工程类独家文档首发】
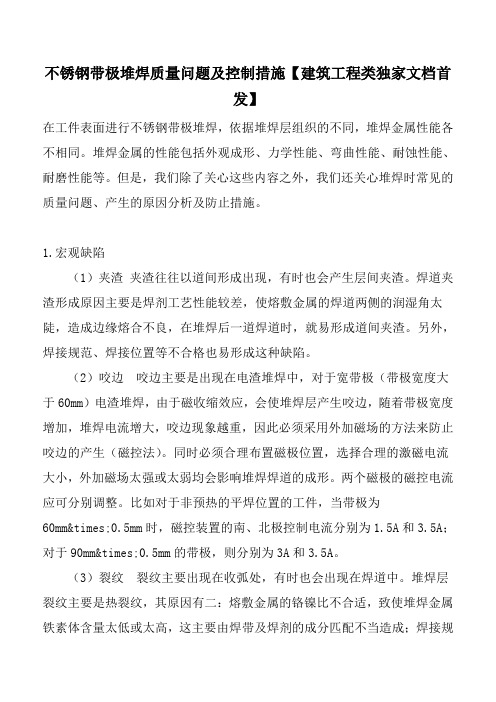
不锈钢带极堆焊质量问题及控制措施【建筑工程类独家文档首发】在工件表面进行不锈钢带极堆焊,依据堆焊层组织的不同,堆焊金属性能各不相同。
堆焊金属的性能包括外观成形、力学性能、弯曲性能、耐蚀性能、耐磨性能等。
但是,我们除了关心这些内容之外,我们还关心堆焊时常见的质量问题、产生的原因分析及防止措施。
1.宏观缺陷(1)夹渣夹渣往往以道间形成出现,有时也会产生层间夹渣。
焊道夹渣形成原因主要是焊剂工艺性能较差,使熔敷金属的焊道两侧的润湿角太陡,造成边缘熔合不良,在堆焊后一道焊道时,就易形成道间夹渣。
另外,焊接规范、焊接位置等不合格也易形成这种缺陷。
(2)咬边咬边主要是出现在电渣堆焊中,对于宽带极(带极宽度大于60mm)电渣堆焊,由于磁收缩效应,会使堆焊层产生咬边,随着带极宽度增加,堆焊电流增大,咬边现象越重,因此必须采用外加磁场的方法来防止咬边的产生(磁控法)。
同时必须合理布置磁极位置,选择合理的激磁电流大小,外加磁场太强或太弱均会影响堆焊焊道的成形。
两个磁极的磁控电流应可分别调整。
比如对于非预热的平焊位置的工件,当带极为60mm×0.5mm时,磁控装置的南、北极控制电流分别为1.5A和3.5A;对于90mm×0.5mm的带极,则分别为3A和3.5A。
(3)裂纹裂纹主要出现在收弧处,有时也会出现在焊道中。
堆焊层裂纹主要是热裂纹,其原因有二:熔敷金属的铬镍比不合适,致使堆焊金属铁素体含量太低或太高,这主要由焊带及焊剂的成分匹配不当造成;焊接规范不当,电流过大也易造成热裂纹。
(4)未熔合堆焊层与母材间结合面或层间易出现未熔合现象,由于烧结型焊剂比熔炼型焊剂堆焊重量轻,故熔深比较小。
一旦操作不当或焊接规范参数掌握不适,易出现结合面未熔合或层间未熔合缺陷。
上面介绍了常见宏观缺陷及防止措施,除此之外,在实际产品堆焊时,还应注意以下几点。
一是焊前严格对母材打磨,去除铁锈、油污等影响焊接的因素且必须预热。
防爆起重机车轮不锈钢堆焊工艺

防爆起重机车轮不锈钢堆焊工艺
防爆起重机车轮通常采用不锈钢堆焊工艺来增强其耐腐蚀性和耐磨性。
不锈钢堆焊工艺主要包括以下几个步骤:
1. 准备工作:将车轮表面清洁干净,去除任何污垢和油脂。
2. 选择合适的不锈钢焊丝:根据车轮的材质和使用环境,选择适合的不锈钢焊丝。
常用的不锈钢焊丝有304、316等。
3. 进行堆积焊接:将不锈钢焊丝加热至熔化温度后,将其堆焊在车轮表面。
焊接过程要保持适当的焊接速度和焊接温度,以确保焊缝的质量。
4. 进行后处理:焊接完成后,对焊缝进行打磨和抛光,以使其与车轮表面平整光滑。
5. 进行质量检验:对堆焊部位进行质量检验,包括焊缝的密实性、无裂纹和气孔等缺陷。
需要注意的是,防爆起重机车轮的不锈钢堆焊工艺必须符合相关的标准和要求,以确保其安全可靠性。
在进行堆焊时,操作人员必须佩戴防护设备,并进行必要的防爆安全措施,以避免火花引发爆炸等危险。
不锈钢板堆焊
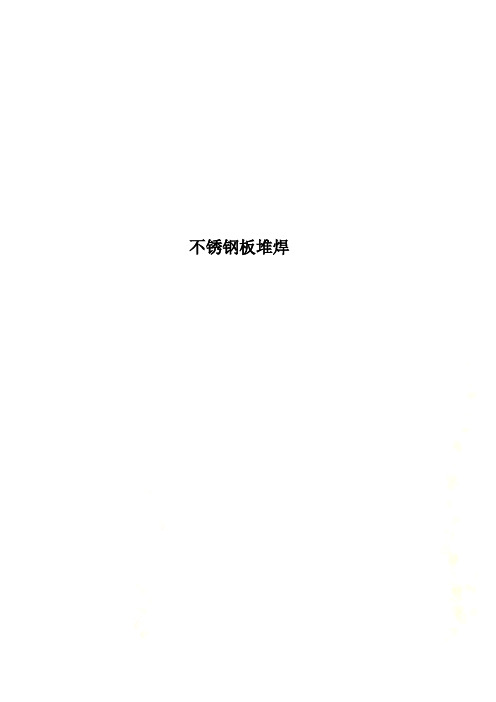
不锈钢板堆焊焊接工艺指导书单位名称四川良川机械设备有限公司焊接工艺规程编号LCJX-26-04 日期2010.09.20 所依据焊接工艺评定报告编号LCJX-26-P04焊接方法GTAW 机械化程度(手工、机械、自动)手工焊接接头:(LC04)不锈钢板堆焊坡口形式无衬垫(材料及规格)无其他简图:(接头形式、坡口形式与尺寸、焊层、焊道布置及顺序)母材:ZG0Cr18Ni9类别号Ⅶ组别号Ⅶ— 1 与类别组别号相焊及标准号GB12230 材料代号302 与标准号GB/T984-2001 材料代号HS111 相焊厚度范围:10母材:对接焊缝角焊缝管子直径、壁厚范围:对接焊缝角焊缝其他堆焊焊接材料:焊接类别不锈钢板堆焊焊材标准GB/T984-2001填充金属尺寸φ3焊材型号钴基焊丝焊材牌号(金属材料代号)HS111焊缝金属厚度范围:对接焊缝角焊缝其他堆焊层≥3mm耐蚀堆焊金属化学成分(%)C SiWFeS Cr Ni Mn Co Ti Nb1.0~1.7≤27.0~10≤326~32≤2 余量其他:焊接位置:对接焊缝的位置向上立焊的焊接方向:(向上、向下)角焊缝的位置立焊的焊接方向:(向上、向下)焊后热处理:保温温度范围(℃)650±10 保温时间(h)120min,炉冷预热:最小预热温度(℃)无最大层间温度(℃)300保持预热时间无加热方式气体:气体种类混合比流量(L/min)保护气氩气无15~30尾部保护气无背面保护气无电特性:电流种类直流极性直流反接焊接电流范围(A)100~120 电弧电压(V)23~27焊接速度(范围)10~15Cm/min钨极类型及直径φ 3 喷嘴直径(mm)12熔滴过渡形式无焊丝送进速度(cm/min)无(按所焊位置和厚度,分别列出电流和电压范围,记入下表)焊道/ 焊层焊接方法填充材料焊接电流电弧电压(V)焊接速度(cm/min)线能量(kJ/cm)牌号直径极性电流(A)1 GTAWHS111 φ3 反接100~115 22~24 12~132 GTAWHS111 φ3 反接150~170 23~27 14~153 GTAWHS111 φ3 反接170~200 25~29 15~17技术措施:摆动焊或不摆动焊无摆动参数焊前清理和层间清理打磨背面清根方法无单道焊或多道焊(每面)五单丝焊或多丝焊单导电嘴至工件距离(mm)锤击无其他:注:对每一种母材与焊接材料的组合均需分别填表。
不锈钢堆焊工艺

不锈钢堆焊工艺1. 引言不锈钢是一种具有耐腐蚀性和高温强度的金属材料,广泛应用于化工、石油、食品加工等领域。
在某些情况下,不锈钢的制造过程中需要进行堆焊,以修复或增强材料的性能。
不锈钢堆焊工艺是一种将不锈钢材料焊接到基材上的技术,本文将详细介绍不锈钢堆焊工艺的过程、方法和注意事项。
2. 不锈钢堆焊工艺的过程不锈钢堆焊工艺的过程主要包括以下几个步骤:2.1 表面准备在进行不锈钢堆焊之前,首先需要对基材进行表面准备。
表面准备的目的是清除基材表面的污垢、氧化物和油脂等杂质,以确保焊接的质量。
常用的表面准备方法包括机械清理、化学清洗和溶剂清洗等。
2.2 堆焊材料选择不锈钢堆焊的材料选择非常重要。
通常情况下,堆焊材料应与基材具有相似的化学成分和机械性能,以确保焊接接头的强度和耐腐蚀性。
此外,还需要考虑不锈钢的耐腐蚀性和热膨胀系数等特性。
2.3 堆焊工艺参数设定堆焊工艺参数的设定对焊接接头的质量和性能有重要影响。
常用的堆焊工艺参数包括焊接电流、焊接电压、焊接速度和填充材料的厚度等。
这些参数应根据具体的堆焊材料和焊接要求进行合理设定。
2.4 堆焊过程控制在堆焊过程中,需要控制焊接参数、焊接速度和填充材料的均匀性等。
同时,还需要注意焊接过程中的温度控制,以避免产生过高的温度导致不锈钢发生晶间腐蚀等问题。
此外,还需要注意堆焊过程中的保护气体的选择和流量控制,以防止氧化和污染。
2.5 堆焊接头质量检验堆焊接头质量检验是确保堆焊工艺的关键步骤之一。
常用的堆焊接头质量检验方法包括可视检查、超声波检测和X射线检测等。
这些方法可以检测焊接接头的缺陷、裂纹和气孔等问题,以确保接头的质量合格。
3. 不锈钢堆焊工艺的方法不锈钢堆焊工艺的方法主要包括以下几种:3.1 熔化堆焊熔化堆焊是将填充材料加热至熔化状态,并与基材融合形成焊接接头的方法。
熔化堆焊可以使用电弧焊、气焊或激光焊等方法进行。
这种方法适用于不锈钢的大面积堆焊和高强度要求的场合。
核电设备稳压器筒体内表面不锈钢堆焊技术
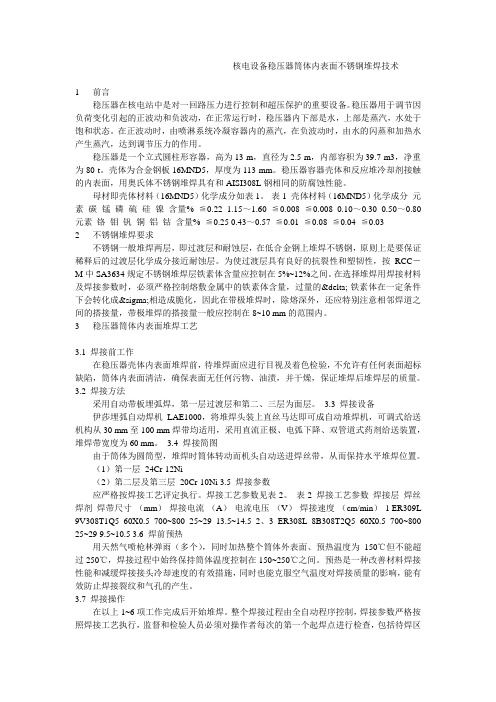
核电设备稳压器筒体内表面不锈钢堆焊技术1 前言稳压器在核电站中是对一回路压力进行控制和超压保护的重要设备。
稳压器用于调节因负荷变化引起的正波动和负波动,在正常运行时,稳压器内下部是水,上部是蒸汽,水处于饱和状态。
在正波动时,由喷淋系统冷凝容器内的蒸汽,在负波动时,由水的闪蒸和加热水产生蒸汽,达到调节压力的作用。
稳压器是一个立式圆柱形容器,高为13 m,直径为2.5 m,内部容积为39.7 m3,净重为80 t。
壳体为合金钢板16MND5,厚度为113 mm。
稳压器容器壳体和反应堆冷却剂接触的内表面,用奥氏体不锈钢堆焊具有和AISI308L钢相同的防腐蚀性能。
母材即壳体材料(16MND5)化学成分如表1。
表1 壳体材料(16MND5)化学成分元素碳锰磷硫硅镍含量% ≦0.22 1.15~1.60 ≦0.008 ≦0.008 0.10~0.30 0.50~0.80 元素铬钼钒铜铝钴含量% ≦0.25 0.43~0.57 ≦0.01 ≦0.08 ≦0.04 ≦0.032 不锈钢堆焊要求不锈钢一般堆焊两层,即过渡层和耐蚀层,在低合金钢上堆焊不锈钢,原则上是要保证稀释后的过渡层化学成分接近耐蚀层。
为使过渡层具有良好的抗裂性和塑韧性,按RCC-M中SA3634规定不锈钢堆焊层铁素体含量应控制在5%~12%之间。
在选择堆焊用焊接材料及焊接参数时,必须严格控制熔敷金属中的铁素体含量,过量的δ-铁素体在一定条件下会转化成σ相造成脆化,因此在带极堆焊时,除熔深外,还应特别注意相邻焊道之间的搭接量,带极堆焊的搭接量一般应控制在8~10 mm的范围内。
3 稳压器筒体内表面堆焊工艺3.1 焊接前工作在稳压器壳体内表面堆焊前,待堆焊面应进行目视及着色检验,不允许有任何表面超标缺陷,筒体内表面清洁,确保表面无任何污物、油渍,并干燥,保证堆焊后堆焊层的质量。
3.2 焊接方法采用自动带板埋弧焊,第一层过渡层和第二、三层为面层。
- 1、下载文档前请自行甄别文档内容的完整性,平台不提供额外的编辑、内容补充、找答案等附加服务。
- 2、"仅部分预览"的文档,不可在线预览部分如存在完整性等问题,可反馈申请退款(可完整预览的文档不适用该条件!)。
- 3、如文档侵犯您的权益,请联系客服反馈,我们会尽快为您处理(人工客服工作时间:9:00-18:30)。
焊条选用的原则焊条的选用须在确保焊接结构安全、可靠使用的前提下,根据被焊材料的化学成分、力学性能、板厚及接头形式、焊接结构特点、受力状态、结构使用条件对焊缝性能的要求、焊接施工条件和技术经济效益等综合考查后,有针对性地选用焊条、必要时还需进行焊接性试验。
(1)同种钢材焊接时焊条选用要点1)考虑焊缝金属力学性能和化学成分对于普通结构钢,通常要求焊缝金属与母材等强度,应选用熔敷金属抗拉强度等于或稍高于母材的焊条。
对于合金结构钢,有时还要求合金成分与母材相同或接近。
在焊接结构刚性大、接头应力高、焊缝易产生裂纹的不利情况下,应考虑选用比母材强度低的焊条。
当母材中碳、硫、磷等元素的含量偏高时,焊缝容易产生裂纹,应选用抗裂性能好的碱性低氢型焊条。
2)考虑焊接构件使用性能和工作条件对承受动载荷和冲击载荷的焊件,除满足强度要求外,主要应保证焊缝金属具有较高的冲击韧性和塑性,可选用塑、韧性指标较高的低氢型焊条。
在高温、低温、耐磨或其他特殊条件下工作的焊接件,应选用相应的耐热钢、低温钢、堆焊或其他特殊用途焊条。
3)考虑焊接结构特点及受力条件对结构形状复杂、刚性大的厚大焊接件,由于焊接过程中产生很大的内应力、易使焊缝产生裂纹,应选用抗裂性能好的碱性低氢焊条。
对受力不大、焊接部位难以清理干净的焊件,应选用对铁锈、氧化皮、油污不敏感的酸性焊条。
对受条件限制不能翻转的焊件,应选用适于全位置焊接的焊条。
4)考虑施工条件和经济效益在满足产品使用性能要求的情况下,应选用工艺性好的酸性焊条。
在狭小或通风条件差的场合,应选用酸性焊条或低尘焊条。
对焊接工作量大的结构,有条件时应采用高效率焊条,如铁粉焊条、高效率重力焊条等,或选用底层焊条、立向下焊条之类专用焊条,以提高焊接生产率。