4.2盘套类零件的加工分解
盘套类零件加工工艺 PPT

案例教学
一单元 盘套类零件的功用、结构特点、技术要求、材料与毛坯
(一)盘类零件 1、盘类零件的功用及结构特点
盘类零件在机器中主要起支承、连接作用。 主要由端面、外圆、内孔等组成,一般零件直 径大于零件的轴向尺寸,如齿轮、带轮、法兰盘、 端盖、模具、联轴节、套环、轴承环、螺母、垫圈 等。 一般用于传递动力、改变速度、转换方向或起 支承、轴向定位或密封等作用。 零件上常有轴孔;常设计有凸缘、凸台或凹坑 等结构;还常有较多的螺孔、光孔、沉孔、销孔或 键槽等结构;有些还具有轮辐、辐板、肋板以及用 于防漏的油沟和毡圈槽等密封结构。 各类盘类零件见图2-3(1)(2)所示。
盘套类零件加工工艺的设计与实施
重点:
1. 盘套类零件的加工工艺分析; 2. 盘套类零件的定位基准确定; 3. 盘套类零件的加工路线的确定; 4. 加工经济性分析。
难点:
盘套类零件的加工路线的确定及加工经济性分析。
盘套类零件加工工艺的设计与实施
第二部分 过程设计描述
该情境的学习与工作流程如下图:
资讯
分组点评 每小组选派4人(含组长),对前期所进行的资讯内容中的1、2、
3项进行畅谈。最后由老师进行归类评述,并对资讯方法进行点评 和指导。
学习情景2 常规特征零件的数控车削加工
大家有疑问的,可以询问和交流
精品课程
可以互相讨论下,但要小声点
9
盘套类零件加工工艺的设计与实施
第三部分 学习情境
步骤一:资讯
图2-4 套筒类零件案例
a)滑动轴承 b)滑动轴承 c)钻套 d)衬套 e)气缸 套 f)油缸
盘套类零件加工工艺的设计与实施
第三部分 学习情境
步骤一:资讯
案例教学 一单元 盘套类零件的功用、结构特点、技术要求、材料与毛坯
盘类零件加工工艺设计、编程与加工
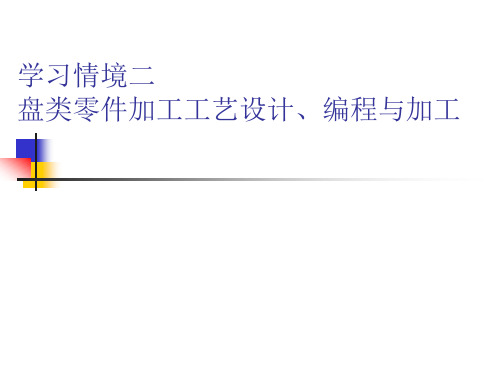
给轨迹。 程序段格式为: G81 X_ Z_ F_ 其中,X、Z值在绝对值编程时为切削终点(C点)在
工件坐标系中的坐标值。在增量值编程时为切削终 点(C点)相对于循环起点(A点)的坐标值,有正 负之分,即图5.13(a)中的U、W值。
图2.1 常用盘套类零件
2.盘套零件的工艺 盘套类零件的基本工艺路线如下图2.2所示。
图2.2 基本工艺路线
二、孔加工方法及刀具 1.孔加工的常用方法及刀具 孔的加工方法通常有钻孔、扩孔、车孔和铰孔。
钻孔的常用刀具是麻花钻。钻孔属于粗加工,其尺寸精度一 般可达IT11~IT12,表面粗糙度Ra12.5~25µm。
图1.20 外径切槽循环G75-逐次进给
2.直接切到槽底,然后回退,其动作顺序如图1.22 所示:A->B->A->C->D->C->……。
(2)盘类零件常用的装夹方法 ①一次装夹。由于数控车床具备自动换刀功能,在
单件、小批量生产中采用一次装夹方式优势明显。 ②以内孔为基准的装夹。当盘套类零件的外圆形状
复杂而内孔相对比较简单时,可以先将孔加工至图 纸要求,再按孔的尺寸配置心轴,以内孔为定位基 准套在心轴上加工.,从而保证工件的同轴度和垂 直度等位置精度。 ③以外圆为基准的装夹。当盘套类零件的内孔形状 复杂而外圆相对比较简单时,在车床上可以先加工 外圆至尺寸要求,再以外圆为装夹基准加工其他部 位,从而保证零件的位置精度。
图2.3 内孔车刀 (a)通孔车刀 (b)盲孔车刀 (c)双后角
(2)内孔车刀的选用。常用的内孔车刀有3种不同 截面形状的刀柄,即圆柄、矩形柄和正方形柄。普 通型和模块式的圆柄车刀多用于车削中心和数控车 床上,如图2.6(a)所示。矩形和方形柄多用于普 通车床,如图2.6(b)所示。
盘 套类加工工艺

第二节 盘、套类零件工艺设计一、盘、套类零件特点(一)盘类零件1、功用盘类零件在机器中主要起支承、连接作用。
2、结构特点盘类零件主要由端面、外圆、内孔等组成,一般零件直径大于零件的轴向尺寸。
3、技术要求盘类零件往往对支承用端面有较高平面度及轴向尺寸精度及两端面平行度要求;对转接作用中的内孔等有与平面的垂直度要求,外圆、内孔间的同轴度要求等。
(二)套类零件1、功用套类零件在机器中主要起支承和导向作用。
2、结构特点零件主要由有较高同轴要求的内外圆表面组成,零件的壁厚较小,易产生变形,轴向尺寸一般大于外圆直径。
3、主要技术要求孔与外圆一般具有较高的同轴度要求;端面与孔轴线(亦有外圆的情况)的垂直度要求;内孔表面本身的尺寸精度、形状精度及表面粗糙度要求;外圆表面本身的尺寸、形状精度及表面粗糙度要求等。
二、盘、套类零件制造工艺(教学)案例案例3:支承块加工。
零件图三维图1、零件工艺性分析(1)零件材料:45钢。
切削加工性良好。
刀具材料及几何参数选择同案例1。
(2)零件组成表面:两端面,外圆面,中间孔及沉孔,安装孔,侧面,十字槽,倒角等。
(3)零件结构分析:两端面起支承作用,光度要求高,轴向尺寸在安装后通过配磨保证两件等高。
轴向尺寸小,为典型的盘类零件。
(4)主要技术条件:端面粗糙度要求Ra0.4µm两端面保证平行。
2、零件工艺设计(1)毛坯选择按零件形状及要求,可选棒料。
(2)基准及安装方案分析该零件的主要基准无疑为两端面,安装孔及十字槽等表面加工均为端面作定位基准,侧表面位置,孔的中心考虑精度要求不高,且该零件为单件生产,采用划线确定;两平面的平行度则采用互为基准的方法保证。
(3)零件表面加工方法按端面Ra0.4µm的要求,其终加工方法选择精磨。
为确保零件安装平整,安装孔应与端面垂直,在加工安装孔,铣十字槽前先粗磨好平面,孔及槽等表面加工后再精磨平面。
侧面采用铣削,安装孔采用钻削,中间孔及沉孔可采用车削。
盘类零件的加工工艺分析

2)+35外 圆 面选 用 公 差 等 级 为 1T6, 上偏 差 为 0,下 用通用的机床设备。
偏 差 为一0.016 ml/1,对 +20H7的 同轴 度要 求 为 0.02 mm,
机床 夹 具 是工 件在 机 床 上进 行切 削 过程 中 ,保 证 f:
表 粗 糙度 为 RaO.8 、
表 面粗 糙度 为 尺00.8。
定心 卡盘 安装 。采 用三 爪 白定心 卡 盘装夹 外 圆时 ,为 保证
4)+20内孔选用公差 等级为 IT7,上 偏差为 0.021 mm, 定位 的可靠 性 ,通 常采 用 反 爪装 夹 方 法 (限制 了工 件 的 5
下偏 差 为 0,表 面粗 糙 度为 Ra1.6。
法兰盘及轴承环等。盘类零件用于传递动力 、转换方向或 为 后续 加T 的精 准 。根 据粗 基 准 的选 择 原则 ,选 取 毛坯
起 轴 向定 位 及密 封等 作用 。为 加强 支 承 ,盘类 零 件上 常设 西35外 网端 面作 为粗基 准 ,在 车床 卜选用 三爪 卡盘 装 夹工
有凸台 、凹坑等,此外 ,为与其它零件连接 ,盘类零件上还 件 ,以消 除法 兰盘 毛坯件 的 自由度 ,达到完 全定位 的 目的 。
个 自由度 );在对 内孔 进 行 装 夹 时 ,利 用 三 爪 卡 盘 离心 力
5)宽 度 为 34 Illnl的 左 右 两 端 面 的 表 面 粗 糙 度 为 的作 用 完成 对法 兰 盘零 件 的定 位 和夹 紧 。2)专 用 夹 具安
尺 a6.3。
装 。利用 外 圆作 径 向定 位 基准 时 ,选 用定 位环 作 为定 位
工 ,毛坯铸造完毕后 ,进行人工时效处理 ,以
消除 毛 坯 内部 的残余 应 力 ,避 免 在机 械 加 工
4.2精基准及加工方法的选择(2)
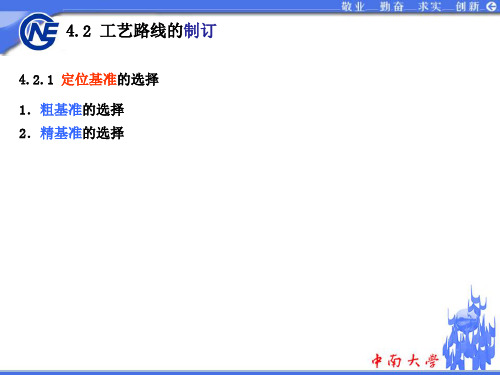
4.2.3 典型表面的加工路线 1. 外圆表面的加工路线
①粗车—半精车—精车
加工精度等于或低于IT7, 表面粗糙度≥Ra5μ m的外 圆表面; ②粗车—半精车—粗磨—精磨 加工精度等于或低于IT6, 表面粗糙度≥Ra0.16μ m的 外圆表面,特别是要求淬 火的工件;
图7 外圆表面的加工路线
③粗车—半精车—精车一金刚石车 主要适用于加工不宜采用磨削加工的有色金 属(如铜、铝); ④粗车—半精车—粗磨—精磨—研磨(超精加工、砂带磨、镜面磨或抛光 ) 以 减小表面粗糙度、提高精度为主要目的。
谢谢大家!
(4)自为基准原则 旨在减小表面粗糙度,减小加工余量或保证加工余量均 匀的工序,常以加工面本身为基准进行加工。 如精铰孔时,铰刀与主轴采用浮动连接,加工时是以孔本身为定位基 准;磨削车床床身导轨面(M4-2)时,常在磨头上装百分表以导轨面本身 为基准来找正工件。 自为基准加工只能提高加工表面的尺寸精度,不能提高表面间的相互 位置精度,后者应由先行工序保证。 (5)便于装夹原则 所选精基准,应能保证定位准确、可靠,夹紧机构简单, 操作方便。该原则始终不能违反。
如图是在钻床上成批加工工件孔的工序简图。若选N面为尺寸B的定位基准 [见b] ,钻头相对1面位置已调整好且固定不动,则加工这一批工件时尺寸B 不受尺寸A变化的影响;若选M面为定位基准 [见c] ,钻头相对2面已调整好 且固定不动,则加工的尺寸B要受到尺寸A变化的影响,使尺寸B精度下降。
(2) 统一基准原则 选择多个表面加工时都能使用的定位基准作为 精基准, 并应尽早地将该基准面加工出来, 以便后续较多工序可以 以它为精基准。 如轴类多以两个顶尖孔为定位基准;齿轮加 工以内孔和端面为定位基准;箱体加工以平面和两 个销孔为定位基准;活塞类工件以内止口和中心孔 为定位基准(见图6)。
套类零件加工工艺
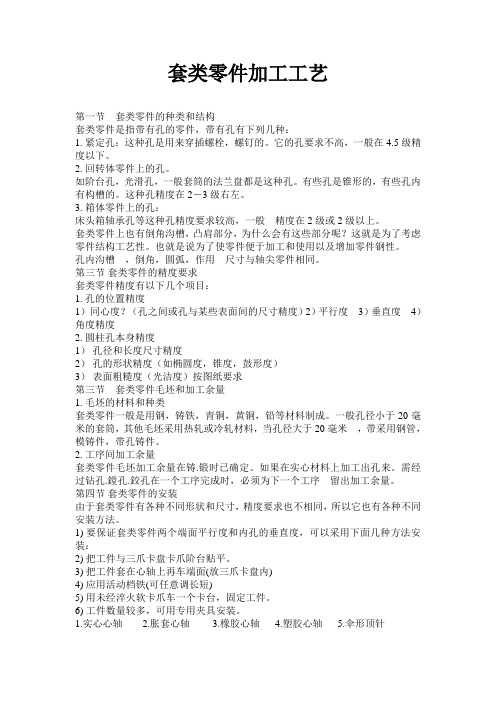
套类零件加工工艺第一节套类零件的种类和结构套类零件是指带有孔的零件,带有孔有下列几种:1. 紧定孔:这种孔是用来穿插螺栓,螺钉的。
它的孔要求不高,一般在4.5级精度以下。
2. 回转体零件上的孔。
如阶台孔,光滑孔,一般套筒的法兰盘都是这种孔。
有些孔是锥形的,有些孔内有构槽的。
这种孔精度在2-3级右左。
3. 箱体零件上的孔:床头箱轴承孔等这种孔精度要求较高,一般精度在2级或2级以上。
套类零件上也有倒角沟槽,凸肩部分,为什么会有这些部分呢?这就是为了考虑零件结构工艺性。
也就是说为了使零件便于加工和使用以及增加零件钢性。
孔内沟槽,倒角,圆弧,作用尺寸与轴尖零件相同。
第三节套类零件的精度要求套类零件精度有以下几个项目:1. 孔的位置精度1)同心度?(孔之间或孔与某些表面间的尺寸精度)2)平行度3)垂直度4)角度精度2. 圆柱孔本身精度1)孔径和长度尺寸精度2)孔的形状精度(如椭圆度,锥度,鼓形度)3)表面粗糙度(光洁度)按图纸要求第三节套类零件毛坯和加工余量1. 毛坯的材料和种类套类零件一般是用钢,铸铁,青铜,黄铜,铅等材料制成。
一般孔径小于20毫米的套筒,其他毛坯采用热轧或冷轧材料,当孔径大于20毫米,带采用钢管,模铸件,带孔铸件。
2. 工序间加工余量套类零件毛坯加工余量在铸.锻时已确定。
如果在实心材料上加工出孔来。
需经过钻孔.鏜孔.鉸孔在一个工序完成时,必须为下一个工序留出加工余量。
第四节套类零件的安装由于套类零件有各种不同形状和尺寸,精度要求也不相同,所以它也有各种不同安装方法。
1) 要保证套类零件两个端面平行度和内孔的垂直度,可以采用下面几种方法安装:2) 把工件与三爪卡盘卡爪阶台贴平。
3) 把工件套在心轴上再车端面(放三爪卡盘内)4) 应用活动档铁(可任意调长短)5) 用未经淬火软卡爪车一个卡台,固定工件。
6) 工件数量较多,可用专用夹具安装。
1.实心心轴2.胀套心轴3.橡胶心轴4.塑胶心轴5.伞形顶针6.闷头中心孔顶工釿第五节内孔表面的加工方法一. 钻孔注意以下几点:1)钻头引向端面,不可用力太大,防止断钻头和偏孔。
《套类零件的加工》课件

磨削加工具有极高的加工精度和表面质量,适 用于对精度要求极高和对表面质量要求严格的 零件加工。
套类零件的其他加工方法
01
套类零件除了车削、铣削和磨削 等常见加工方法外,还包括钻削 、铰削、镗削、攻丝等加工方法 。
05
套类零件的加工质 量控制与检测
套类零件的加工精度控制
加工工艺流程
详细介绍套类零件的加工 工艺流程,包括毛坯准备 、粗加工、半精加工和精 加工等阶段。
加工设备选择
根据零件特点和加工精度 要求,选择合适的机床和 工具,确保加工过程的稳 定性和精度。
热处理和表面处理
介绍套类零件在加工过程 中可能涉及的热处理和表 面处理方法,以及它们对 零件精度的影响。
套类零件的尺寸检测与测量方法
尺寸检测原则
明确套类零件的尺寸检测原则,确定检测项目和检测方法。
测量工具选择
根据套类零件的尺寸和精度要求,选择合适的测量工具,如卡尺 、千分尺、量规等。
测量方法与操作技巧
详细介绍套类零件的测量方法与操作技巧,确保测量结果的准确 性和可靠性。
THANKS
感谢您的观看
套类零件的表面质量检测
表面粗糙度检测
表面涂层质量检测
使用表面粗糙度测量仪对套类零件的 表面粗糙度进行检测,确保符合设计 要求。
对套类零件表面的涂层进行质量检测 ,包括涂层厚度、硬度、附着力等方 面的检测。
表面缺陷检测
通过目视检查、无损检测等方法,检 查套类零件表面是否存在裂纹、气孔 、夹渣等缺陷。
套类零件的加工实 例
实例一:轴承套的加工
总结词
工艺流程复杂,需要高精度加工
盘套类零件加工工艺的设计与编制
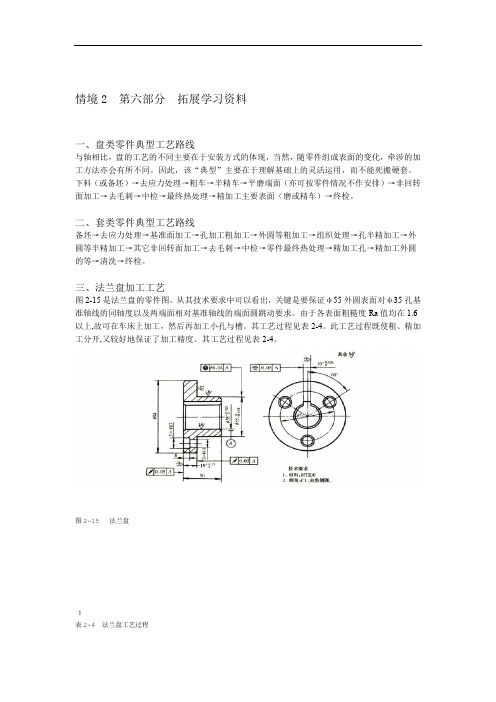
情境2 第六部分拓展学习资料一、盘类零件典型工艺路线与轴相比,盘的工艺的不同主要在于安装方式的体现,当然,随零件组成表面的变化,牵涉的加工方法亦会有所不同。
因此,该“典型”主要在于理解基础上的灵活运用,而不能死搬硬套。
下料(或备坯)→去应力处理→粗车→半精车→平磨端面(亦可按零件情况不作安排)→非回转面加工→去毛刺→中检→最终热处理→精加工主要表面(磨或精车)→终检。
二、套类零件典型工艺路线备坯→去应力处理→基准面加工→孔加工粗加工→外圆等粗加工→组织处理→孔半精加工→外圆等半精加工→其它非回转面加工→去毛刺→中检→零件最终热处理→精加工孔→精加工外圆的等→清洗→终检。
三、法兰盘加工工艺图2-15是法兰盘的零件图。
从其技术要求中可以看出,关键是要保证φ55外圆表面对φ35孔基准轴线的同轴度以及两端面相对基准轴线的端面圆跳动要求。
由于各表面粗糙度Ra值均在1.6以上,故可在车床上加工,然后再加工小孔与槽。
其工艺过程见表2-4。
此工艺过程既使粗、精加工分开,又较好地保证了加工精度。
其工艺过程见表2-4。
图2-15 法兰盘1表2-4 法兰盘工艺过程四、中心架和跟刀架中心架和跟刀架图2-162在加工细长轴或长套筒零件时,为了防止其弯曲变形,必须使用中心架或跟刀架作为辅助支承。
中心架上有三个等分布置并能单独调节伸缩的支承爪。
使用时,用压板、螺钉将中心架固定在床身导轨上,调节支承爪,使工件轴线与主轴轴线重合,且支承爪与工件表面的接触应松紧适当,如图2-16所示。
跟刀架上一般有两个能单独调节伸缩的支承爪,它们分别安在工件的上面和车刀的对面,如图2-16所示。
五、互为基准原则两个被加工表面之间位置精度较高,要求加工余量小而均匀时。
互为基准图2-17六、找正法装夹工件(1)直接找正法用百分表、划针或目测在机床上直接找正工件的有关基准,使工件占有正确的位置称为 2-18所示。
直接找正法。
单件和小批生产。
直接找正法如图)划线找正法(2使工件获得正确的位置称划在机床上用划线盘按毛坯或半成品上预先划好的线找正工件,所示。
- 1、下载文档前请自行甄别文档内容的完整性,平台不提供额外的编辑、内容补充、找答案等附加服务。
- 2、"仅部分预览"的文档,不可在线预览部分如存在完整性等问题,可反馈申请退款(可完整预览的文档不适用该条件!)。
- 3、如文档侵犯您的权益,请联系客服反馈,我们会尽快为您处理(人工客服工作时间:9:00-18:30)。
(3)内外圆回转表面的同轴度公差很小。
(4)结构比较简单。
4.2.1 套筒类零件的结构特点和技术要求
2.套筒类零件的毛坯制造方式
毛坯制造方式主要取决于其结构尺寸、材料和生产批
量的大小。孔径较大 ( 如 d > 20mm) 时 , 常采用无缝钢管或带 孔的铸件和锻件。孔径较小时 , 多选用热轧或冷拉棒料 , 也 可采用实心铸件。大批量生产时,可采用冷挤压棒料、粉末 冶金棒料等。套筒类零件的材料以钢、铸铁、青铜或黄铜 为主 , 也有采用双金属结构 ( 即在钢或铸铁套的内壁上浇注 一层轴承合金材料)的。套筒类零件常用的热处理方法有渗 碳、淬火、表面淬火、调质、高温时效及渗氮等。
4.2.3
2.减小变形
套筒类零件加工特点
套类零件的结构特点是孔的壁厚较薄,薄壁套类零件在
加工过程中,常因夹紧力.切削力和热变形的影响而引起变 形。为防止变形常采取—些工艺措施: 1) 将粗、精加工分开进行 为减少切削力和切削热的影响, 使粗加工产生的变形在精加工中得以纠正。
2) 减少夹紧力的影响 在工艺上采取以下措施减少夹紧力
图4-17液压缸简图
4.2.2 典型套筒类零件的加工工艺分析
该零件孔长而壁薄,为保证内外圆的同轴度,加工外圆时 参照空心主轴的装夹方法,即采用双顶尖顶孔口1°30′的锥 面或一头夹紧一头用中心架支承。加工内孔与一般深孔加工 时的装夹相同,多采用夹一头,另一端用中心架托住外圆。孔 的粗加工采用镗削,半精加工多采用浮动铰刀铰削。铰削后, 孔径尺寸精度一般为IT9~IT7,表面粗糙度达Ra2.3~0.32μ m。
4.2.3
套筒类零件加工特点
1深孔加工的工艺特点
通常把孔的深度与直径之比(L/D>5)的孔称为深孔。深径比 不大的孔,可用麻花钻在普通钻床,车床上加工;深径比 大的孔,必须采用特殊的刀具,设备及加工方法。深孔加 工比一般的孔加工要复杂和困难得多。深孔加工的工艺主 要有以下特点: 深孔加工的刀杆细长,强度和刚性比较差,在加工时容易 引偏和振动,因此,在刀头上设置支承导向极为重要。 切屑排除困难。如果切屑堵塞,则会引起刀具崩刃,甚至 折断,因此需采用强制排屑措施。 刀具冷却散热条件差。切屑液不易注入切屑区,使刀具温 度升高,刀具寿命降低,因此,必须采用有效的降温方法。
4.2.3
套筒类零件加工特点
4.2.3
套筒类零件加工特点
4.2.3
4 刀具结构特点
套筒类零件加工特点
刀具的导向性能好,防止加工中引偏。 为了有利于排屑,必须能使切屑成碎裂状或粉状屑,
而不是呈带状。
刀具上必须有进出油孔或通道,供流通切削液并排
除切屑。
刀具必须有良好的切屑性能,并且在连续切削的条 件下,具有较高的耐磨性和红硬性。
(如连杆小端衬套)时,内、外圆表面的同轴度公差可以较大;
若内孔的最终加工是在装配之前完成,则同轴度公差较小,通 常为0.06~0.01mm。套的端面(包括凸缘端面)如在工作中承
受载荷或加工中作为定位面时 ,端面与外圆或内孔轴线的垂
直度要求较高,一般为0.05~0.02mm。
4.2.1 套筒类零件的结构特点和技术要求
② 夹紧力的位置宜选在零件刚性较强的部位,以改
善在夹紧力作用下薄壁零件的变形。
4.2.3
套筒类零件加工特点
③ 改变夹紧力的方向,将径向夹紧改为轴向夹紧。
④ 在工件上制出加强刚性的工艺凸台或工艺螺纹以
减少夹紧变形,加工时用特殊结构的卡爪夹紧,
加工终了时将凸边切去。如表 5.3 工序 2 先车出 M88mm × 1.5mm 螺纹供后续工序装夹时使用。 在工序 3 中利用该工艺螺纹将工件固定在夹具中, 加工完成后,在工序 5 车去该工艺螺纹。
4.2.1 套筒类零件的结构特点和技术要求
3.套筒类零件的技术要求
套筒类零件的外圆表面多以过盈或过渡配合与机架或 箱体孔配合,起支承作用。内孔主要起导向作用或支承作用, 常与传动轴、主轴、活塞、滑阀相配合。有些套的端面或 凸缘端面有定位或承受载荷作用。
套筒类零件的主要技术要求为
(1)内孔与外圆的尺寸精度一般为 IT7~IT6。为保证内
要求,其公差值为Ø 0.03mm; ③ 材料45钢,调质220~240HBS。
4.2.2 典型套筒类零件的加工工艺分析
4.2.2 典型套筒类零件的加工工艺分析
2.工艺分析 ① 该零件的主要表面均为回转表面,应选用车削方法,主 要工艺路线为:粗车—调质—精车。在精车过程中, 应使孔(Ø ),小外圆(Ø )和台阶端面在一次 0.025 350 550 装夹加工出来,即“一刀活”;再以孔定位,心轴装夹 0.019 精 车大端面,即可保证该零件的位置精度要求。 ② 在精车之后钻Ø16孔,铣削宽16的圆弧槽。 ③ 毛坯选用锻件。 3.工艺过程 锻造毛坯—粗车—调质—精车—划线—钻孔 —铣槽—检验
4.2.2 典型套筒类零件的加工工艺分析
液压缸内孔的表面质量要求很高 ,精加工铰孔后, 还需采用钢珠滚压,以改善内圆表面,使其熨平并形成 残余压应力,提高使用寿命。为此,较多的专业生产厂 采用专用组合刀具来完成液压缸内孔的粗加工、半精 加工、精加工和滚压加工 , 专业组合刀具是将镗刀、 浮动铰刀和钢珠滚压头等集成在一起。内孔经滚压后, 尺寸误差在 0.01mm 以内 , 表面粗糙度为 Ra0.16μm 或 更小, 且表面经硬化后更为耐磨。但是目前对铸造液 压缸体尚未采用滚压工艺 , 原因是铸件表面缺陷对滚 压有很大影响,因此,常以精细镗、珩磨、研磨等精密 加工作为缸体内孔加工的最终工序。
的影响。
4.2.3
套筒类零件加工特点
4.2.3
套筒类零件加工特点
① 采用径向夹紧时,夹紧力不应集中在工件的某一
径向截面上,而应使其分布在较大的面积上,以减 小工件单位面积上所承受的夹紧力。如可将工件安 装在一个适当厚度的开口圆环中,在连同此环一起 夹紧。也可采用增大接触面积的特殊卡爪。以孔定
位时,宜采用张开式心轴装夹。
4.2.2 典型套筒类零件的加工工艺分析
4.工艺卡片
4.2.2 典型套筒类零件的加工工艺分析
三、液压缸体零件工艺过程
液压缸体(如图4-17所示)属于长孔薄壁类零件,且精度和表面粗糙
度都控制较严。液压缸的毛坯多为无缝钢管,如果为铸件,由于其 组织可能不够紧密,会出现砂眼、针孔或疏松等缺陷,加工过程中 应该增加用泵定压定时的验漏工序。
孔的耐磨性和功能要求 , 其表面粗糙度要求 Ra2.5 ~ 0.16μm,
外圆的表面粗糙度为Ra5~0.63μm。
4.2.1 套筒类零件的结构特点和技术要求
(2) 通常将外圆与内孔的几何形状精度控制在直径公差 以内即可,较精密的可控制在直径公差的1/2~1/3,甚至更 小。较长的套筒零件除有外圆的圆柱度要求外 ,还有孔的圆 柱度要求。 (3) 内、外圆表面之间的同轴度公差按零件的装配要求 而定。当内孔的最终加工是将套装入机座或箱体之后进行
4.2.2 典型套筒类零件的加工工艺分析
表4-3 液压缸加工工艺路线
4.2.3
套筒类零件加工特点
1.工艺措施
套筒类零件内外表面的同轴度以及端面与孔轴线的垂 直度要求较高,一般可采用以下工艺措施: (1)在一次安装中完成内外表面及端面的全部加工 ,这 样可消除工件的安装误差并获得很高的相互位置精度。但
4.2.3
套筒类零件加工特点
4.2.3
3 冷却和排屑方式
套筒类零件加工特点
(1)内排屑方式 高压切削油由钻杆与工件孔壁间的空隙处 压入切削区,然后带着切屑从钻杆中的内孔排出。这样不 会划伤已加工的孔壁,而且钻杆直径可增大,也同时增强 了钻杆的扭转刚性和弯曲刚性。因此可提高进给量,且孔 轴线偏移量也小,一般为0.1-0.3mm/m。 采用深孔钻头需配备油压头,深孔钻头装在油压头机构 内。油压头的前端与工件贴合,工件由主轴带动旋转。足 够流量的高压油从油压头中的油管注入,通过钻杆和工件 壁间的空隙处压入切削区,起冷却作用,再从钻杆内孔中 带着大量切屑排出。压力和流量过小时,不易使切屑排出, 使温度升高,刀具容易磨损。 (2)外排屑方式 切削液的流向正好与内排屑方式相反。
4.2.2 典型套筒类零件的加工工艺分析
4.பைடு நூலகம்.2 典型套筒类零件的加工工艺分析
4.2.2 典型套筒类零件的加工工艺分析
二、接盘零件工艺过程
1. 接盘零件的主要表面及其技术要求 ① 孔A(Ø 350
0.025
):IT7, Ra1.6 m ;
② 小外圆(Ø550 ):IT6, Ra1.6 m对孔A的轴线有同轴度 0.019
套筒类零件由于功用、结构形状及尺寸、材料、热处理
方法的不同,其工艺过程差别较大。其中,保证内孔与外圆的
同轴度公差,以及端面与内圆(外圆)轴线的垂直度公差,是拟 定工艺规程时需要关注的主要问题。
4.2.2 典型套筒类零件的加工工艺分析
一、法兰盘零件工艺过程
4.2.2 典型套筒类零件的加工工艺分析
4.2.2 典型套筒类零件的加工工艺分析
4.2.3
2、深孔的钻削方式
套筒类零件加工特点
在单件小批生产中,深孔钻削常在卧式车床或转塔车床上用 接长的麻花钻加工。有时工件作两次安装,从两端钻成。钻 削时钻头须多次退出,以排屑和冷却刀具。采用这用切屑方 式,劳动强度大且生产率低。在大批量生产中,普遍用深孔 钻床和使用深孔钻头进行加工。
深孔加工一般采用工件旋转,钻头轴向进送,或钻头与工件 同时反向旋转,钻头轴向进送方式进行,这两种方式都不易 使深孔的轴线偏斜,尤其后者更为有利,但设备比较复杂。 若工件很大,旋转有困难,则可将工件固定,使钻头旋转并 轴向进送。当旋转轴线与工件轴线有偏斜,则加工后的轴线 也将有偏斜。
4.2.1 套筒类零件的结构特点和技术要求
图4-16套筒类零件的结构形式