熟料煅烧中的有关问题的解析(配套)
水泥窑煅烧工艺异常情况原因分析及处理措施
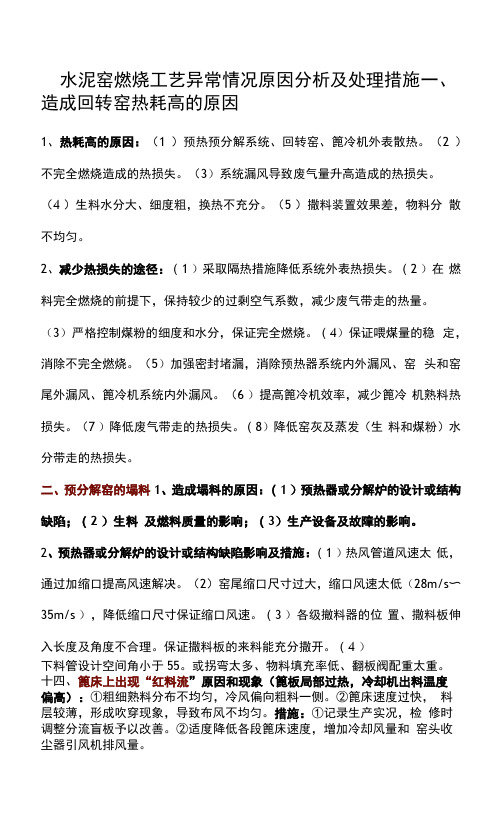
水泥窑燃烧工艺异常情况原因分析及处理措施一、造成回转窑热耗高的原因1、热耗高的原因:(1 )预热预分解系统、回转窑、篦冷机外表散热。
(2 )不完全燃烧造成的热损失。
(3)系统漏风导致废气量升高造成的热损失。
(4 )生料水分大、细度粗,换热不充分。
(5 )撒料装置效果差,物料分散不均匀。
2、减少热损失的途径:(1 )采取隔热措施降低系统外表热损失。
(2 )在燃料完全燃烧的前提下,保持较少的过剩空气系数,减少废气带走的热量。
(3)严格控制煤粉的细度和水分,保证完全燃烧。
(4)保证喂煤量的稳定,消除不完全燃烧。
(5)加强密封堵漏,消除预热器系统内外漏风、窑头和窑尾外漏风、篦冷机系统内外漏风。
(6 )提高篦冷机效率,减少篦冷机熟料热损失。
(7 )降低废气带走的热损失。
(8)降低窑灰及蒸发(生料和煤粉)水分带走的热损失。
二、预分解窑的塌料1、造成塌料的原因:(1 )预热器或分解炉的设计或结构缺陷;(2 )生料及燃料质量的影响;(3)生产设备及故障的影响。
2、预热器或分解炉的设计或结构缺陷影响及措施:(1 )热风管道风速太低,通过加缩口提高风速解决。
(2)窑尾缩口尺寸过大,缩口风速太低(28m/s〜35m/s ),降低缩口尺寸保证缩口风速。
(3 )各级撤料器的位置、撒料板伸入长度及角度不合理。
保证撒料板的来料能充分撒开。
(4 )下料管设计空间角小于55。
或拐弯太多、物料填充率低、翻板阀配重太重。
十四、篦床上出现“红料流”原因和现象(篦板局部过热,冷却机出料温度偏高):①粗细熟料分布不均匀,冷风偏向粗料一侧。
②篦床速度过快,料层较薄,形成吹穿现象,导致布风不均匀。
措施:①记录生产实况,检修时调整分流盲板予以改善。
②适度降低各段篦床速度,增加冷却风量和窑头收尘器引风机排风量。
十五、篦板温度偏高原因:①熟料粒度过细;②篦床上出现〃红料流〃;③ 风室冷却风量过大,或料层较薄,熟料层被吹穿;④风室冷却风量过小,缺乏以充分冷却熟料;⑤窑皮跨落,篦床上有大量熟料堆积,无法及时冷却所致;⑥篦床速度过快,料层过薄;⑦篦板脱落或篦绛较宽,漏料比拟严重。
如何提高熟料煅烧质量

二 日常操作中的调整
烧成ቤተ መጻሕፍቲ ባይዱ温度:
窑前火焰发浑 熟料呈滑落状态 窑主电机持续降低 细粉料结粒较少 熟料外观发白,并疏 松多孔 立升重偏低 可以判断熟料温度偏 低,应立即调整
二 日常操作中的调整
熟料煅烧时间:
在三率值不变,喂料料不变的情况下 1、C3S形成不仅需要温度,还需要一定时间,提高熟料煅
2、熟料急冷效果较差,会造成C3S分解成C2S+f-CaO,造 成熟料游离钙升高,造成出篦冷机熟料温度过高
二 日常操作中的调整
熟料急冷效果:
熟料快速冷却,有助 于提高二次风温、三次 风温 在保持篦冷机料层 500mm-700mm的情 况下,加大一二室风量、 适度使用三四室风量、 尽量减少五六室的风量 尽量保证熟料既可以 吹透,但不可吹穿
吸收形成C3S的能力,提高熟料强度 2、窑内温度低,物料黏散,结粒困难,熟料不密实,烧成
不充分,造成熟料强度下降 操作中应多关注窑头摄像头,根据情况调整,可增加窑头
看火次数,确认熟料结粒情况
二 日常操作中的调整
烧成带温度:
窑前火焰白亮 熟料带起高度较高 窑主电机电流高 熟料结粒均齐,细粉 料结粒较少 熟料外观发黑并有光 泽,结构致密 立升重较高 可以判断熟料煅烧较 好
质量总结会 ——窑操作经验交流
主要内容
一 熟料煅烧中影响强度的因素 二 日常操作中的调整
一 熟料煅烧中影响强度的因素
因素:
1、分解炉温度 2、烧成带温度 3、熟料煅烧时间 4、熟料急冷效果 5、煤粉质量和
窑内通风的影响
影响熟料强度
二 日常操作中的调整
分解炉温度:
1、适当提高分解炉温度可提高窑尾温度,提高入窑分解率, 减少窑内温度的损耗
影响高镁熟料煅烧质量的原因分析及对策

度大 。 Mg O含 量 大 于 42 .%时 ,熟 料 出现 结 球 严 重 , 窑 电流 平 均 达 4 0 以 上 , 繁 出 现 结 大 球 , 却 5A 频 冷 破 碎 之后 的 熟 料 大 多数 为 黄 块 . 头 飞砂 严 重 生 窑
产 中 我 们 采 取 常 规 的 降 铁 措 施 . 现 象 不 但 没 有 扭
.
我 们综 合考 虑 了过渡 液相 过早 出现 易形 成 黏性
.
仅仅是 表面张力 降低 、 相黏度 降低 的问题 。 液 与此
相 反 , Mg 即 O含 量 大 于 42 时 , 料 液 相 黏 度 增 .% 熟 加 , 阿利 特 结 晶 困难 。 时 , 然 液 相 量 增 加 , 使 此 虽 表
量 降低 铝 率 , 以降 低 液相黏 度 , 解 熟 料结 粒 , 缓 避免
善 生料 的易 烧性 。 之 与煅 烧 能力 相适 应 . 免 造 成 使 避 窑 内结 圈 , 形成 还原 气 氛 . 且 针对 Mg 并 O含 量 于 32 . %而小 于 42 .%时 . 由于 Mg O 能 降低 液 相 黏度 , 一 定 程 度上 改 善 了易烧 性 . 在 则选 用 三 高配 料 方 案 .将 熟 料 K 提 高 到 09 _ .2 S H .2 00 .M + 提高 到 26 O1 I 提 高 到 1 ± ., 高 铝率 等 率值 。 .± ., M . O1 提 5 在此种情况下 随 着 Mg 的提 高 ,适 当 降 低 生 料 O F e0 指 标 , 2, 以增 加 液相 黏 度 , 解 烧 结 范 围变 窄 , 缓 改 善熟 料质 量 和操 作 的适 应性
3 采 取 的对 策
31 加 强石灰 石矿 点和 均化 质量 控 制 . 为 了 使 熟 料 中 Mg 含 量 达 到 公 司 内 控 指 标 O ( O= .- .% ) 必 须 控 制 石 灰 石 中 Mg 28 Mg 40 02 , O= .±
低碱熟料煅烧中黏散料产生原因及措施

低碱熟料煅烧中黏散料产生原因及措施标题:低碱熟料煅烧中黏散料产生原因及措施引言:在熟料煅烧的过程中,出现黏散料会导致生产过程不稳定、工艺效果下降,并且可能对矿窑设备造成损坏。
因此,了解黏散料的产生原因以及相应的措施,对于提高生产效率和保护设备的安全至关重要。
本文将深入探讨低碱熟料煅烧中黏散料产生的原因,并提出可行的解决方案。
一、低碱熟料煅烧中黏散料的原因1. 煅烧温度过低低碱熟料煅烧过程中,如果温度不足以达到矿石中黏性物质的软化点,就容易出现黏散料。
这是因为低温无法将黏性物质完全熔化,导致其成为粘结材料。
2. 石炭燃烧不充分低碱熟料生产过程中,使用石炭进行燃烧,但燃烧不充分会造成煅烧系统内含有高碳残留物。
这些残留物会在煅烧过程中生成焦炭,并且附着在颗粒表面,形成黏散料。
3. 石炭含硫量高石炭中含有一定的硫分,若石炭含硫量过高,会导致煅烧过程中生成硫酸钠,进而与其他矿石中的氧化钠反应,形成黏性物质。
4. 过高的氧气浓度在低碱熟料煅烧过程中,如果氧气浓度过高,会导致煅烧过程中氧化反应速度过快,矿石中的黏性物质没有充分软化,从而形成黏散料。
二、解决低碱熟料煅烧中黏散料问题的措施1. 控制煅烧温度通过提高煅烧温度,确保矿石中的黏性物质能够被完全软化熔融,从而避免黏散料的产生。
此外,还应保持煅烧温度的稳定,以确保矿石中的黏性物质能够充分软化,避免出现过低温度的情况。
2. 提高石炭燃烧效率加强煅烧系统内石炭燃烧的过程控制,确保石炭燃烧充分,减少煅烧过程中的焦炭生成。
采取一些措施,如增加燃烧区域的供氧量和加强燃烧区域与石炭之间的接触,能够有效提高燃烧效率。
3. 降低石炭硫含量通过降低石炭的硫含量,减少煅烧过程中产生的硫酸钠,从而减少黏性物质的生成。
可以采取煅烧前对石炭进行预处理、使用低硫石炭等措施来达到降低石炭硫含量的目的。
4. 控制氧气浓度通过合理调控煅烧系统内的氧气浓度,避免过高的氧气浓度导致反应速度过快,矿石中的黏性物质没有充分软化的问题。
关于熟料煅烧结粒较差及配料打算分析报告

关于熟料煅烧结粒较差分析及
下阶段配料打算分析报告
针对近期出窑熟料结粒较差、飞砂大、细粉料多的现状,结合目前配料方案及原材料使用情况,制定下阶段配料方案,形成分析报告如下。
一、原燃材料状况:
1、矿山资源使用现状
2、粘土资源使用现状
粘土矿自试生产以来,使用黄洼水库南(水库边至蒋庄北东向)粘土,水分18.0%,化学成分见下表:
3、铁质原材料
质量分析;
4、原煤
二、原因分析:
1、八月份熟料成分分析
2、硫碱比
(从液相量、Al2O3、Fe2O3含量及三率值等方面进行分析)
结论:
三:下阶段配料思路:
1、矿山开采方面
根据石灰石矿山现阶段开采方案,在9月份将中采160米以上部分削顶后,开始向东山开拓发展。
采准矿量将受到限制,为有效降低下盘围岩低品位石灰石出矿带来的有害成分高的问题,后期将采取以下几点措施来改善入堆场石灰石成分;
1)要求矿山分厂加大西采148-135米的开采力度,确保高品位石灰石的采准矿量。
2)加快中采148米以上部分的开采进度,确保备矿量有充足的搭配空间。
3)减少下盘围岩低品位石灰石的使用量,降低出矿石灰石中有害成分(K2O+Na2O、MgO、SiO2、SO3)的含量。
2、原燃材料使用方面
通过前期使用的原煤情况来看,由于渤港煤用量大,受内水高、易磨性较差的影响,对原煤粉磨及回转窑煅烧十分不利,为改善原煤使用现状,后期采取措施有;
1)增加淮南煤采购量,以降低入磨煤粉的内水、易磨性等特点,同时使用淮南煤的高Al2O3特性,改善硅率
3、配料控制思路
①原燃材料成分数据
②原煤工业分析:
(2)生料配比如下
(3)生、熟料理论成份。
水泥窑煅烧异常情况分析及操作
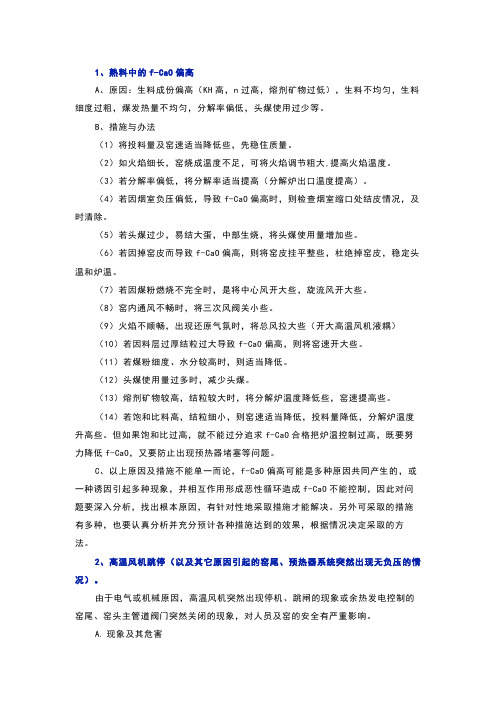
1、熟料中的f-CaO偏高A、原因:生料成份偏高(KH高,n过高,熔剂矿物过低),生料不均匀,生料细度过粗,煤发热量不均匀,分解率偏低,头煤使用过少等。
B、措施与办法(1)将投料量及窑速适当降低些,先稳住质量。
(2)如火焰细长,窑烧成温度不足,可将火焰调节粗大,提高火焰温度。
(3)若分解率偏低,将分解率适当提高(分解炉出口温度提高)。
(4)若因烟室负压偏低,导致f-CaO偏高时,则检查烟室缩口处结皮情况,及时清除。
(5)若头煤过少,易结大蛋,中部生烧,将头煤使用量增加些。
(6)若因掉窑皮而导致f-CaO偏高,则将窑皮挂平整些,杜绝掉窑皮,稳定头温和炉温。
(7)若因煤粉燃烧不完全时,是将中心风开大些,旋流风开大些。
(8)窑内通风不畅时,将三次风阀关小些。
(9)火焰不顺畅,出现还原气氛时,将总风拉大些(开大高温风机液耦)(10)若因料层过厚结粒过大导致f-CaO偏高,则将窑速开大些。
(11)若煤粉细度、水分较高时,则适当降低。
(12)头煤使用量过多时,减少头煤。
(13)熔剂矿物较高,结粒较大时,将分解炉温度降低些,窑速提高些。
(14)若饱和比料高,结粒细小,则窑速适当降低,投料量降低,分解炉温度升高些。
但如果饱和比过高,就不能过分追求f-CaO合格把炉温控制过高,既要努力降低f-CaO,又要防止出现预热器堵塞等问题。
C、以上原因及措施不能单一而论,f-CaO偏高可能是多种原因共同产生的,或一种诱因引起多种现象,并相互作用形成恶性循环造成f-CaO不能控制,因此对问题要深入分析,找出根本原因,有针对性地采取措施才能解决。
另外可采取的措施有多种,也要认真分析并充分预计各种措施达到的效果,根据情况决定采取的方法。
2、高温风机跳停(以及其它原因引起的窑尾、预热器系统突然出现无负压的情况)。
由于电气或机械原因,高温风机突然出现停机、跳闸的现象或余热发电控制的窑尾、窑头主管道阀门突然关闭的现象,对人员及窑的安全有严重影响。
熟料质量控制及煅烧方面的影响因素

培训材料熟之三料质量控制及煅烧方面的影响因素一、熟料质量控制的重要性1、熟料质量是确保水泥质量的核心,熟料质量达不到要求,难以磨制优质的水泥产品。
其中配料和煅烧是决定熟料质量的关键。
2、从生料到熟料,是一个化学反应过程。
化学反应,最基本的核心就是要求参预化学反应的物质间的比例要满足理论要求。
参预化学反应的某一物质的量,不得过剩或者不足,否则,化学反应形成的结果,不是当初设计的结果。
因此,熟料生产过程实际上要求是很精细的,不是表面上的那种粗糙现象。
3、设计合理的熟料率值,通过良好的煅烧,才干生产出优质的水泥熟料。
1、原料磨工艺变化现代水泥企业,以节能高效为主要导向,装备和工艺流程日益简化和高效。
2、原料磨由过去的球磨机改为现代立磨,原料磨工艺装备的改变,对产品质量的影响。
3、球磨机的工艺特点,决定了生料细度更加均匀,900 孔细度小,只在 3.0%以内, 1800 孔细度在 12%以内。
立磨的生料细度粗, 900 孔细度在 6.0-8.0%, 1800 孔细度在 22%摆布。
由上看出,现代水泥工业改成立磨后,生料的颗粒级配产生了较大的变化,立磨的生料粗大颗粒占比例明显上升,中等颗粒的比例,也较球磨机增加了一倍。
4、现代水泥工业、细度标准的变化。
80 年代,国家旋窑管理规程对细度有控制要求,最开始的标准规定生料细度小于等于 10%,作为一次水泥工艺管理的标准来执行,其后更改为 12%。
后来随着先进水泥工艺发展,生料细度作为一次过程控制指标,再也不强制执行,由企业根据自身生产需要自行控制。
质量体系认证,也将细度标准作为企业自行制定来审核,细度标准被企业自身不断放松标准。
按照现行立磨的生产工艺,生料细度按 10%、12%、16% 等等标准,已经无法满足当前立磨工艺的要求,根据立磨的特点及与窑的产能关系,细度只能控制在 20-22%之间,即使控制较好的工厂细度也在 8 摆布。
但是 , 目前的细度控制指标,不表示细度粗对煅烧没有影响。
低碱熟料煅烧中产生黏散料的原因及措施

低碱熟料煅烧中产生黏散料的原因及措施
低碱熟料煅烧过程中,黏散料的产生是一个常见的问题。
黏散料的产
生会影响熟料的品质和生产效率,因此需要采取措施来解决这个问题。
产生黏散料的原因主要有以下几点:
1. 原料成分不均匀:熟料煅烧过程中,原料成分不均匀会导致烧结不良,从而产生黏散料。
2. 煅烧温度过高:煅烧温度过高会导致熟料烧结不良,从而产生黏散料。
3. 煅烧时间过长:煅烧时间过长会导致熟料烧结不良,从而产生黏散料。
4. 煅烧过程中的气氛不稳定:煅烧过程中的气氛不稳定会导致熟料烧
结不良,从而产生黏散料。
为了解决黏散料的产生问题,可以采取以下措施:
1. 原料配比均匀:在生产过程中,要确保原料配比均匀,避免原料成
分不均匀导致烧结不良。
2. 控制煅烧温度:在煅烧过程中,要控制煅烧温度,避免温度过高导
致熟料烧结不良。
3. 控制煅烧时间:在煅烧过程中,要控制煅烧时间,避免时间过长导
致熟料烧结不良。
4. 稳定煅烧气氛:在煅烧过程中,要稳定煅烧气氛,避免气氛不稳定
导致熟料烧结不良。
5. 采用合适的煅烧工艺:在生产过程中,要采用合适的煅烧工艺,避
免产生黏散料。
综上所述,低碱熟料煅烧中产生黏散料的原因主要是原料成分不均匀、煅烧温度过高、煅烧时间过长和煅烧过程中的气氛不稳定等因素。
为
了解决这个问题,可以采取措施如原料配比均匀、控制煅烧温度和时间、稳定煅烧气氛和采用合适的煅烧工艺等。
这些措施可以有效地解
决黏散料的产生问题,提高熟料的品质和生产效率。
- 1、下载文档前请自行甄别文档内容的完整性,平台不提供额外的编辑、内容补充、找答案等附加服务。
- 2、"仅部分预览"的文档,不可在线预览部分如存在完整性等问题,可反馈申请退款(可完整预览的文档不适用该条件!)。
- 3、如文档侵犯您的权益,请联系客服反馈,我们会尽快为您处理(人工客服工作时间:9:00-18:30)。
二、结圈的预防和处理
(一)结圈的预防: (1)选择适宜的配料方案,稳定生料成分,提高 煅烧操作水平。一般讲:烧高饱和比、高硅酸率的 料子不易结圈,但煅烧很困难,对保护窑皮和熟料 质量不利。而烧低饱和比、低硅酸率的料子,烧结 范围窄,液相量多,结粒粗,煅烧不易控制,易结圈。 烧高饱和比、低硅酸率或低饱和比、高硅酸率的 料子都可易烧不结圈。因此配料方案应采用较高 饱和比和较高硅酸率适当减少熔媒矿物的配料方 案,对防止结圈有利。另外高铝氧率的料子C3A含 量高,液相粘度大,易结圈。在配料方案中应在适 当减少物料中液相量的条件下,降低铝氧率值。
(2)圈位距下料口较近,大都是由于窑皮情况不好, 火焰过长,喷煤管长时间在外边时结的圈。处理有两种 操作法:一是不减喂料的操作。当来料偏少时将喷煤 管拉出,同时提高一、二次风温和增加二次风量,尾温 偏下限控制,提高烧成温度,使烧成带前移,火点落在圈 位上,逐步烧掉。操作中要及时加减煤量,掌握来料多 少和火焰变化情况,发现火焰伸长或压缩要及时调整, 防止损伤窑皮及轻烧品出窑;二是减喂料的操作。适 当减少喂料量,减少二次风量,当尾温偏低时,将喷煤管 拉到最外,待预烧较差的物料进入烧成带后,即可缩短 火焰强制煅烧,使前结圈强火烧掉。此种方法是在拉出 喷煤管无法烧到时被迫进行的。由于喷煤管拉出过多, 加上生料很近,黑火焰很短,不可能维持正常火焰形状, 操作中更要注意来料变化,加强勤看。
Байду номын сангаас
熟料圈的处理
在处理熟料圈时 , 要根据圈体的特点和远 近 , 分别采取不同的处理方法 , 才能达到较好 的效果。一般采用冷热交替法处理,烧远圈时 以冷为主,烧近圈时以烧为主。 (1)当窑内窑皮长得长而厚或有轻度圈 根时,将喷煤管偏外拉出,移动燃烧带位置,降低 结圈部位温度,改变煤灰沉落位置,使厚长的窑 皮逐渐垮落。调整风煤配合,加速煤粉燃烧,使 高温带两端低温部分不拖长,防止圈根继续成 长。
(3)在生产中要确定一个经济合理的产量指标,适当 快速转窑操作,对防止回转窑结圈是一个有利措施。 结圈大都在窑产量较高时形成的,往往都是由于增加 窑产量的条件超过所规定的最高抽风能力,而造成燃 料不完全燃烧的缘故。当窑产量增加到一定限度之后, 用煤量增加,煤灰大量沉落,窑内还原气氛浓厚,操作上 必然拉大排风,窑内气流速度增加,火焰拉长,液相提前 出现,就容易形成熟料圈。为此在生产管理上要加强 原、燃料质量控制,稳定入窑生料成分,保持喂料均匀, 在加强预烧的基础上,采取薄料快转、长焰顺烧,稳定 热工制度,提高快转率等措施,对预防结圈十分有效。
(2) 当窑内厚长窑皮处理不当或不及时而导致周 期性快、慢车加重,使厚窑皮发展形成熟料圈时。首 先要确定圈的位置和厚度及圈后积料情况。然后减 少喂料量,一般减少到正常喂料量的 70%~80%。提高 火焰温度 , 加强预烧 , 逐渐加快窑速 , 保持窑的快转 , 卸出圈后部分积料。待圈后积料减少时,可将喷煤管 伸入窑内 , 适当抬高喷煤嘴 , 使火焰的高温区移向圈 体处。此时排风不宜加得过大,防止火焰温度降低。 烧 4 ~ 5h 后 , 再将喷煤管拉出烧 , 这样反复处理 , 使圈 体受温度变化而垮落。在处理熟料圈时,要适当改变 原料成分,减少物料中的液相量,适当改变煤的配合, 采用高挥发物,低灰分的煤,保证煤粉完全燃烧,以防 圈的发展。 处理熟料圈时,一定要在保护窑皮的基础上进行,勿 使火焰过分集中。经处理后圈根仍很牢固,而且严重 损伤窑皮及衬料时,应停窑除圈。
7、熟料粒度与黄心熟料
熟料结粒越大,黄心料生成越多。 分析大粒熟料生成原因:一是熟料 煅烧中液相主要成分AI2O3、 Fe2O3 、 尤其 Fe2O3含量高时易产生;二是成 分正常煅烧温度高,或二者都发生; 三是熟料层厚,翻滚慢容易产生大 粒。
8、喷煤嘴端面位置与黄心熟料
喷煤嘴愈接近料层,黄心料生成 愈多。以水平方向靠近料层尤甚。 喷煤嘴靠近料层,火焰层铺到物料 表面上,火焰中的碳粒紧贴物料向 前运行,未燃或正在燃烧的碳粒容 易进入熟料中,物料被严重的还原 气氛覆盖,故黄心料多。
1、煤耗越高,熟料黄心率越高。
因为煤耗越大,尤其在用风不能合 理调配情况下,风煤量失衡,或一、二 次风比例不当,煤粉在火焰中分布的浓 度加大,容易产生还原火焰,易使熟料 形成黄心。
2、煤粉细度与黄心熟料
煤粉细度越细,黄心熟料的生成量越低。 煤粉在火焰中的分布是不均匀的,从而引起 火焰中不同部位的气氛不同,且其程度不一。 煤粉粗,一方面燃烧速度慢,未燃尽便可能 落在物料之上(指出现液相后的物料,下 同);另一方面,加大了煤粉分布的不均匀 性,使火焰局部由于煤粉浓度高产生还原气 氛,甚沉落于物料之上,明显地增大了黄心 熟料的生成,严重时还会产生过多低熔FeO 而引起回转窑结圈。
3、料层厚度与黄心熟料
料层加厚,熟料黄心率增大。一 般料层厚度大,窑转速减慢,物料的 翻滚次数少,部分正在燃烧或还未燃 烧的碳粒,在落下后被埋入物料之后, 由于暴露于含有少量氧的火焰的机会 少,而在物料内部产生还原气氛,从 而使黄心熟料增加。
4、容重与黄心熟料
正常成分的熟料,煅烧容重越高, 黄心熟料生成越多。因为在正常煅烧情 况下,容重一般反映了煅烧物料达到温 度的高低,也反映了火焰所达到的最高 温度,容重高,煅烧火焰温度要高,用 煤量相对有增大。如同煤耗增大那样, 容易产生还原气氛而使黄心熟料增加。
六、水泥回转窑结圈的预防和处理
回转窑结圈一般分为两种: 1、前结圈(又称窑口圈),是结在在烧 成带和冷却带的交界处部位的圈。 2、后结圈(又称熟料圈、二道圈),是 结在窑内烧成带与放热反应带之间的圈。
一、结圈的形成
在熟料煅烧过程中,生料在1200℃左 右出现液相,在1250℃左右液相粘度开始 变小,液相量增加,由于料层覆盖温度突降, 加之筒体表面散热,液相在窑壁上凝固下 来,形成窑皮。 该温度条件及区域内若熔化和固化 的过程达到平衡 , 窑皮就不会增厚。当熔 化的少固化的多,其厚度增长到一定程度 , 即形成圈。当衬料与物料的温差大时 , 在 足够液相的条件下,圈体越结越厚。
(2)降低煤粉细度,加强风煤混合,消除不完全燃烧。 煤粉细度粗,着火速度慢,燃烧时间长,火焰的热力分散。 在二次风量不足通风不良的情况下,物料预烧不好。 一次风量不足,风速、风压减小,风煤混合不好,容易产 生不完全燃烧形成还原焰。尤其使用单通道喷煤管 的回转窑,一次风中的氧很难达到火焰中心区严重缺 氧,大量碳粒和CO不能在烧成带燃烧,而在分解带甚 至窑尾才燃烧。同时在烧成带产生大量CO,使物料中 部分氧化铁被还原成氧化亚铁,形成FeO· SiO2低熔点 的化合物。而FeO· SiO2液相在1100℃左右能促使硅 方解石〔2(CaO· SiO2)· CaCO3〕的形成,而硅方解石在 1180~1220℃的液相形成,最容易使烧成带液相提前 出现,将未熔的物料粘结在一起,造成结圈。
(一)前结圈的形成
前结圈(又称窑口圈),是结在在烧成带和冷却 带的交界处部位的圈。在正常煅烧条件下,物料温度 为1350~1450℃,液相量约为24%,其粘度较大。当 熟料离开烧成带时,液相开始冷却,进入冷却带的液 相已基本固化。在烧成带和冷却带的交界处存在着 较大的温差,窑口物料温度高于窑皮温度。当熟料 进入冷却带时,带有液相的高温熟料覆盖在温度较 低的末端窑皮上,就会很快粘结、越粘越厚,最后形 成前结圈。
影响立升重的因素
熟料中所含液相量及各种矿物的组成比 例和率值。 熟料的烧结过程及冷却过程。 熟料结构的孔隙率和结粒情况。 燃料的加入方式(煅烧工艺的选择)及 窑内 气氛和操作水平等。
5、Fe2O3与黄心熟料
随着Fe2O3含量的上升,黄心熟
量明显增加。尤其熟料中的Fe2O3含 量超过4.10%,Fe2O3含量大的熟料, 煅烧过程中对还原气氛更加敏感, 因此黄心率大大增加。
6、CaO含量与熟料黄心料
在熟料Fe2O3含量正常的情况下, 随CaO含量的增加,黄心熟料量增加。 实际上,熟料CaO含量的增大,也就 是KH值增大,熟料的易烧性下降, 煅烧煤耗增加,如同煤耗增大黄心 熟料量增加一样,加大了黄心熟料 的生成。
二、结圈的处理
(一)前结圈的处理 前结圈不高时,对煅烧操作影响不大,尚可增加 烧成带料层厚度,延长物料在烧成带停留时间,减少 烧成带向窑前辐射散热。但当前结圈结高时,既影响 看火操作,又影响窑内通风及火焰形状,大块熟料滚 不出来,易损烧成带窑皮及衬料。此时应调整风煤或 移动喷煤管及时处理。 (1)圈位距下料口较远,大都是在窑皮情况较好、 煅烧正常、高温带位置合适、喷煤管长时间在里边 时结的圈。处理时可不关排风、不减少喂料量,只要 拉出喷煤管就可以烧掉。
(二)熟料圈的形成
熟料圈(又称二道圈),是结在窑内烧成带与放热反 应带之间的圈,也是回转窑内危害最大的结圈。在熟 料煅烧过程中,当物料温度达到1280℃时,其液相粘度 较大,熟料圈最易形成,冷却后比较坚固,不易除掉,在 正常煅烧情况下,熟料圈体的内径部分,往往被烧熔而 掉落,保持正常的圈体内径。如果在1250~1280℃温 度范围内出现的液相量偏多,往往形成妨碍生产的熟 料圈。熟料圈一般结在烧成带的边界或更远,开始是 烧成带后边的窑皮逐渐增长,逐渐长厚,发展到一定程 度即形成熟料圈。严重熟料圈的窑皮长度有的甚至 长出正常窑皮长度的几倍。