阀体零件的工艺工装设计
阀体的加工工艺设计和工艺装备设计

毕业设计题目阀体的加工工艺设计和工艺装备设计系机电工程系专业机械制造及自动化完成日期2009 年10 月30 日毕业设计评分标准湖南铁道职业技术学院毕业设计评阅书学生姓名班级JZ073题目阀体的加工工艺设计和工艺装备设计指导教师职称(务)教授1、指导教师评语:签名:年月日2、答辩委员会综合评语:经毕业设计(论文)答辩委员会综合评定成绩为:答辩委员会主任(签字):年月日毕业设计任务书机电工程系一、设计课题名称: 阀体零件加工工艺与工艺装备设计二、指导教师: 朱鹏超三、设计要求1、设计零件加工工艺。
2、根据图纸加工要求设计指定工序的工艺装备。
3、结构紧凑,动作平稳,定位准确,夹紧可靠,使用安全。
4、保证零件加工精度。
5、全部设计资料均由计算机完成。
四、设计依据1、零件图2、企业现场加工条件。
五、参考资料1、《机床夹具设计》李庆寿主编机械工业出版社2、《机械工程及自动化简明设计手册》机械工业出版社3、《夹具设计手册》机械工业出版社4、《夹具设计图册》机械工业出版社5、《机械制造工艺学》郑修本机械工业出版社六、设计内容及工作量(一)设计内容1.设计零件加工工艺规程①根据零件的生产纲领,确定生产类型;②分析被加工零件图的原始资料,审查、改善零件的结构工艺性,绘制零件图;③确定毛坯类型、结构及尺寸,绘制毛坯图;④拟定工艺路线,选择定位基准、夹紧部位和各表面的加工方法;⑤选择加工设备及工艺装备;⑥确定工序尺寸及其公差;⑦确定切削用量及工时定额;⑧填写工艺卡片、绘制工序图。
2.设计工艺装备,并并完成非标准零件的设计3.撰写毕业设计说明书(二)完成工作量1.零件图一套2.毛坯图一张3.零件加工工艺文件(含工序图等工艺文件)一套4.毕业设计说明书(主要包括零件分析,毛坯选择,加工顺序安排,加工路线的拟定,设备选用、工艺装备设计过程、加工质量分析及解决方法等)一份(三)设计进度七、说明书的格式和装订要求(一)毕业设计封面(全系统一格式)(二)评分标准(全系统一格式)(三)毕业设计评阅书(全系统一格式)(四)毕业设计任务书(指导教师下发)(五)目录(六)毕业设计正文(七)结束语(八)参考文献(九)工艺过程卡片、工序卡片(十)设计图纸注:说明书用A4纸打印或书写,毕业设计正文字数不少于1.5万字(含空格)毕业设计内容计:封面张说明书(论文) 页表格张插图幅附设计图张完成日期2009 年10 月30 日目录前言 (1)第1章毕业设计任务概述 (2)第2章零件图样分析 (3)2.1 零件的功用、材料和性能 (3)2.2 形体分析 (3)2.3 技术要求分析 (4)2.4 零件的工艺性分析 (5)第3章毛坯设计 (7)3.1 生产纲领 (7)3.2 毛坯制造方法 (7)3.3 毛坯尺寸确定 (8)3.4 毛坯简图 (8)第4章零件加工工艺方案的拟定 (9)4.1 加工顺序的安排 (9)4.2 各加工表面加工阶段的划分 (11)4.3 安排加工工艺路线 (12)4.4 工艺方案的比较与优先 (13)第5章工序设计 (14)5.1 定位基准的选择 (14)5.2 加工设备的选择 (16)5.3 刀具的选择 (20)5.4 切削用量的选择 (20)5.5 量具的选择 (22)5.6 夹具的选择 (22)5.7 时间定额计算 (22)第6章机床夹具概述 (24)第7章工件的定位及定位元件 (26)7.1 工件在夹具中的定位 (26)7.2 定位误差分析 (27)第8章工件的夹紧和夹紧装置 (28)8.1 夹紧装置的组成 (28)8.2 夹紧力的确定 (28)第9章夹具体及分度装置 (30)9.1 夹具体 (30)9.2 分度装置 (30)第10章阀体零件的车床夹具设计 (32)10.1 车床夹具的主要类型 (32)10.2车床夹具的设计要点 (33)10.3阀体零件的车床专用夹具的加工误差分析 (34)10.4阀体零件的车床夹具的加工误差分析 (35)参考文献 (37)结束语 (38)前言这次毕业设计是机械制造与自动化的一个十分重要的学习环节,是对入学以来所学的机械方面的知识进行了一次全面的检查、巩固和提高。
{生产工艺技术}阀体工艺工装设计及部分零件的制作
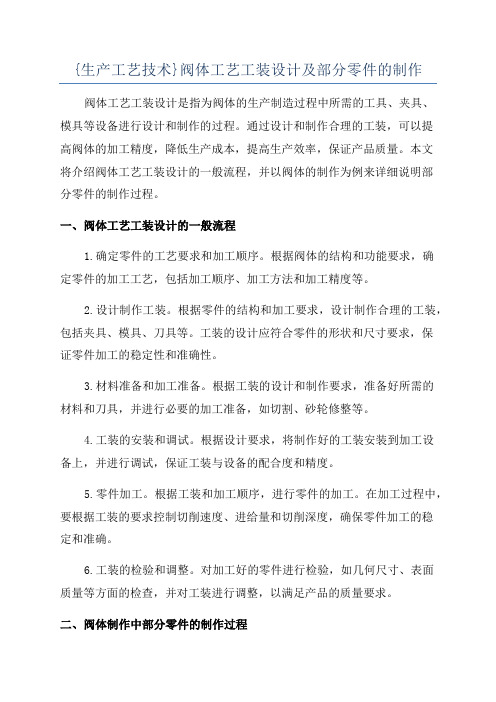
{生产工艺技术}阀体工艺工装设计及部分零件的制作阀体工艺工装设计是指为阀体的生产制造过程中所需的工具、夹具、模具等设备进行设计和制作的过程。
通过设计和制作合理的工装,可以提高阀体的加工精度,降低生产成本,提高生产效率,保证产品质量。
本文将介绍阀体工艺工装设计的一般流程,并以阀体的制作为例来详细说明部分零件的制作过程。
一、阀体工艺工装设计的一般流程1.确定零件的工艺要求和加工顺序。
根据阀体的结构和功能要求,确定零件的加工工艺,包括加工顺序、加工方法和加工精度等。
2.设计制作工装。
根据零件的结构和加工要求,设计制作合理的工装,包括夹具、模具、刀具等。
工装的设计应符合零件的形状和尺寸要求,保证零件加工的稳定性和准确性。
3.材料准备和加工准备。
根据工装的设计和制作要求,准备好所需的材料和刀具,并进行必要的加工准备,如切割、砂轮修整等。
4.工装的安装和调试。
根据设计要求,将制作好的工装安装到加工设备上,并进行调试,保证工装与设备的配合度和精度。
5.零件加工。
根据工装和加工顺序,进行零件的加工。
在加工过程中,要根据工装的要求控制切削速度、进给量和切削深度,确保零件加工的稳定和准确。
6.工装的检验和调整。
对加工好的零件进行检验,如几何尺寸、表面质量等方面的检查,并对工装进行调整,以满足产品的质量要求。
二、阀体制作中部分零件的制作过程以阀体的主体零件为例,介绍部分零件的制作过程。
1.阀体材料准备。
根据零件的材料要求,准备好相应的材料。
阀体主体零件采用碳钢材料,需先进行锻造和模锻处理。
2.零件热处理和表面处理。
将零件进行热处理,以提高材料的强度和硬度,并进行表面处理,如喷砂、喷涂等,以增加零件的表面质量和耐腐蚀性。
3.零件的精整加工。
根据工装的要求,对零件进行精细加工,包括铣削、车削、钻孔、刨削等,以达到零件的设计要求。
4.零件的装配和调试。
将各个零件进行装配,并进行必要的调试,以确保零件的功能和一致性。
5.零件的检验和质量控制。
阀的工艺设计方案

工艺设计方案一.阀体的加工工艺设计1.阀体工艺方案设计阀体设计图阀体表面由圆柱面﹑槽﹑圆弧等构成,是回转体结构,形状较为复杂,可以用普通车床或者数控车床进行加工;内部主要由孔构成,深孔可以用车床加工,异型孔形状较为复杂,配合面尺寸精度要求较高,可以选用数控铣床进行加工。
2.阀体工艺路线设计阀体总的加工路线是先进行车削加工,再进行铣削加工。
车削加工工艺路线如下:车削加工工艺路线表工序号夹具名称使用设备车间001 三爪卡盘普通车床加工车间工步工步内容刀具号刀具主轴转速/(r/min)进给速度/(mm/r)背吃刀量/(mm)备注1 粗车端面T01 端面车刀360 0.19 12 精车端面T01 端面车刀530 0.1 0.53 钻中心孔T02 中心钻2484 钻φ20*4孔T03 φ20麻花钻2485 钻φ5*4孔T04 φ5麻花钻360 0.19 56 钻φ30孔T05 φ30麻花钻2487 倒角T01 端面车刀5308 粗车端面T01 端面车刀360 0.19 1 工件调头装夹9 精车端面T01 端面车刀530 0.1 0.510 粗镗孔T05 镗刀360 0.19 511 半精镗孔T05 镗刀360 0.19 112 精镗孔T05 镗刀530 0.1 0.513 粗车外圆T06 外圆车刀360 0.19 0.414 精车外圆T06 外圆车刀530 0.1 0.115 倒角T01 端面车刀530铣削加工工艺路线如下:铣削加工工艺路线表工序号夹具名称使用设备车间002 三爪卡盘FANUC数控铣床加工车间工步工步内容刀具号刀具主轴转速/(r/min)进给速度/(mm/min)背吃刀量/(mm)备注1 粗铣轮廓T01 φ12立铣刀800 30 62 精铣轮廓T01 φ12立铣刀1200 30 0.23.阀体加工程序设计用Master CAM软件进行阀体的造型,构造出阀体的几何形状,利用软件的功能定义刀路并生成NC程序。
阀体零件机械加工工艺及装备设计概述
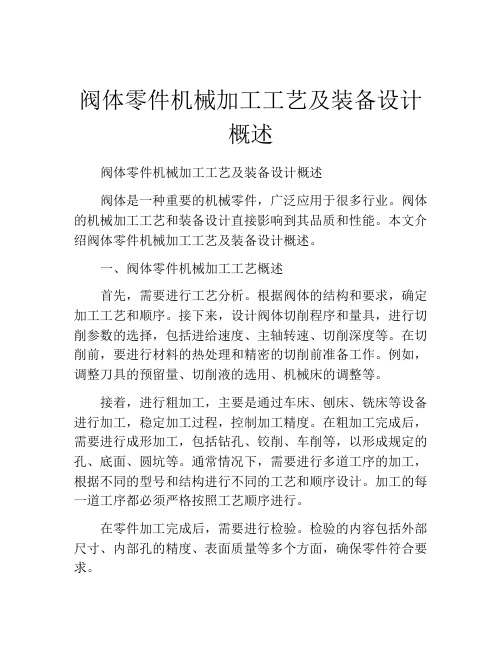
阀体零件机械加工工艺及装备设计概述阀体零件机械加工工艺及装备设计概述阀体是一种重要的机械零件,广泛应用于很多行业。
阀体的机械加工工艺和装备设计直接影响到其品质和性能。
本文介绍阀体零件机械加工工艺及装备设计概述。
一、阀体零件机械加工工艺概述首先,需要进行工艺分析。
根据阀体的结构和要求,确定加工工艺和顺序。
接下来,设计阀体切削程序和量具,进行切削参数的选择,包括进给速度、主轴转速、切削深度等。
在切削前,要进行材料的热处理和精密的切削前准备工作。
例如,调整刀具的预留量、切削液的选用、机械床的调整等。
接着,进行粗加工,主要是通过车床、刨床、铣床等设备进行加工,稳定加工过程,控制加工精度。
在粗加工完成后,需要进行成形加工,包括钻孔、铰削、车削等,以形成规定的孔、底面、圆坑等。
通常情况下,需要进行多道工序的加工,根据不同的型号和结构进行不同的工艺和顺序设计。
加工的每一道工序都必须严格按照工艺顺序进行。
在零件加工完成后,需要进行检验。
检验的内容包括外部尺寸、内部孔的精度、表面质量等多个方面,确保零件符合要求。
二、阀体零件机械加工装备设计概述阀体零件机械加工需要的装备有很多,不同的零件需要不同的设备进行加工。
下面简单介绍几种常用的设备:1. 数控车床数控车床是加工阀体零件的重要机器,具有高精度、高效率等特点。
在进行钻孔、车削等成形加工时,能够精确控制刀具的运动轨迹和加工参数,保证加工精度。
此外,数控车床还可以进行自动化加工,大大提高了生产效率和质量。
2. 铣床铣床是加工中心性零件的重要设备。
通过旋转刀具的转轴,将刀具与工件进行交换加工,形成规定的几何形状。
铣床广泛应用于加工立式滑动翻板阀体等零件。
3. 磨床磨床是进行精密加工和高表面质量加工的设备,在零件加工的后期,进行磨削和抛光,改善表面的光洁度、平度和精度。
磨床的加工精度可以达到0.1微米。
4. 激光切割机激光切割机通过高能激光束瞬间熔化并气化金属,依靠机器控制切割头的走向,完成对零件的切割。
空压机减荷阀体加工工艺及工装设计
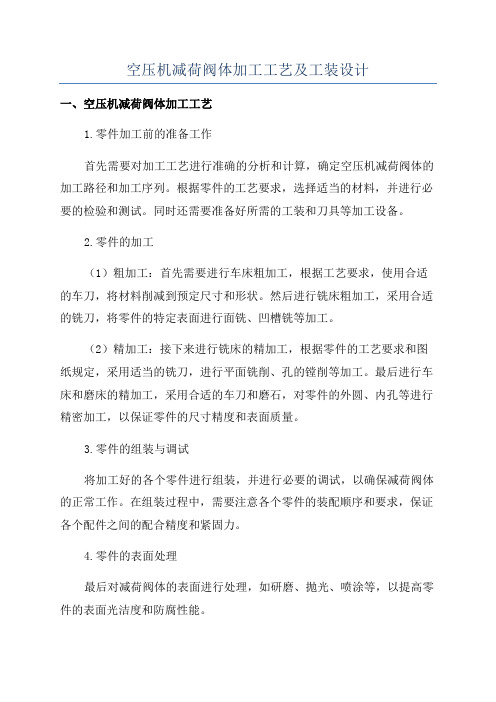
空压机减荷阀体加工工艺及工装设计一、空压机减荷阀体加工工艺1.零件加工前的准备工作首先需要对加工工艺进行准确的分析和计算,确定空压机减荷阀体的加工路径和加工序列。
根据零件的工艺要求,选择适当的材料,并进行必要的检验和测试。
同时还需要准备好所需的工装和刀具等加工设备。
2.零件的加工(1)粗加工:首先需要进行车床粗加工,根据工艺要求,使用合适的车刀,将材料削减到预定尺寸和形状。
然后进行铣床粗加工,采用合适的铣刀,将零件的特定表面进行面铣、凹槽铣等加工。
(2)精加工:接下来进行铣床的精加工,根据零件的工艺要求和图纸规定,采用适当的铣刀,进行平面铣削、孔的镗削等加工。
最后进行车床和磨床的精加工,采用合适的车刀和磨石,对零件的外圆、内孔等进行精密加工,以保证零件的尺寸精度和表面质量。
3.零件的组装与调试将加工好的各个零件进行组装,并进行必要的调试,以确保减荷阀体的正常工作。
在组装过程中,需要注意各个零件的装配顺序和要求,保证各个配件之间的配合精度和紧固力。
4.零件的表面处理最后对减荷阀体的表面进行处理,如研磨、抛光、喷涂等,以提高零件的表面光洁度和防腐性能。
二、空压机减荷阀体工装设计1.工装的选用根据空压机减荷阀体的加工要求和零件的形状特点,选择合适的工装进行加工。
通常可以采用车床夹具、铣床夹具、磨床夹具等进行零件的固定和定位。
2.工装的设计根据空压机减荷阀体的加工路径和加工序列,设计合适的工装夹具。
在设计过程中,需要考虑到零件的固定和定位要求,尺寸精度的控制,生产效率的提高等因素。
3.工装的制造和调试根据工装的设计图纸,制造相应的工装夹具,并进行必要的调试和测试。
在调试过程中,需要确保工装夹具与零件的配合精度和固定可靠性。
总结:空压机减荷阀体加工工艺及工装设计是一个复杂而重要的工作,需要综合考虑加工工艺要求、零件特点、工装选用等多方面因素。
只有在加工工艺和工装设计合理的前提下,才能保证空压机减荷阀体的质量和性能。
机械工艺夹具毕业设计3阀体的加工工艺设计和工艺装备设计
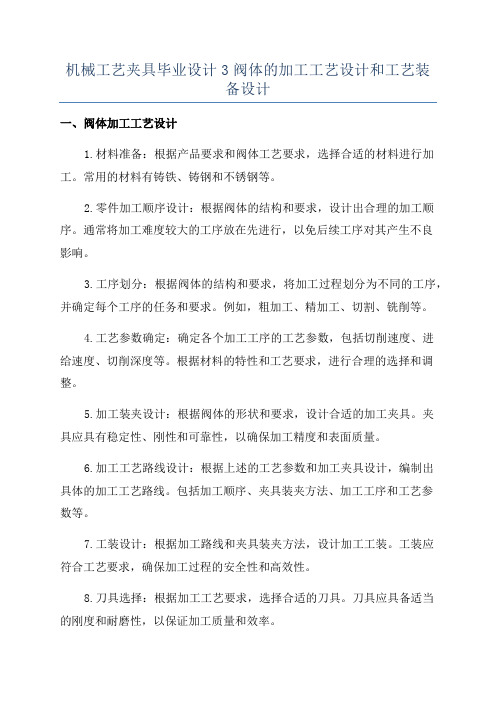
机械工艺夹具毕业设计3阀体的加工工艺设计和工艺装备设计一、阀体加工工艺设计1.材料准备:根据产品要求和阀体工艺要求,选择合适的材料进行加工。
常用的材料有铸铁、铸钢和不锈钢等。
2.零件加工顺序设计:根据阀体的结构和要求,设计出合理的加工顺序。
通常将加工难度较大的工序放在先进行,以免后续工序对其产生不良影响。
3.工序划分:根据阀体的结构和要求,将加工过程划分为不同的工序,并确定每个工序的任务和要求。
例如,粗加工、精加工、切割、铣削等。
4.工艺参数确定:确定各个加工工序的工艺参数,包括切削速度、进给速度、切削深度等。
根据材料的特性和工艺要求,进行合理的选择和调整。
5.加工装夹设计:根据阀体的形状和要求,设计合适的加工夹具。
夹具应具有稳定性、刚性和可靠性,以确保加工精度和表面质量。
6.加工工艺路线设计:根据上述的工艺参数和加工夹具设计,编制出具体的加工工艺路线。
包括加工顺序、夹具装夹方法、加工工序和工艺参数等。
7.工装设计:根据加工路线和夹具装夹方法,设计加工工装。
工装应符合工艺要求,确保加工过程的安全性和高效性。
8.刀具选择:根据加工工艺要求,选择合适的刀具。
刀具应具备适当的刚度和耐磨性,以保证加工质量和效率。
1.加工中心:对于复杂的阀体结构,可以选择使用加工中心进行加工。
加工中心具有高精度、高速度和高质量的加工能力,为阀体加工提供支持。
2.数控车床:对于要求不高的阀体加工,可以选择使用数控车床进行加工。
数控车床具备自动化加工功能,能够提高加工效率和质量。
3.切割机床:对于阀体的切割加工,可以选择使用切割机床。
切割机床能够实现高效、精确的切割,满足阀体加工的需求。
4.加工夹具:根据阀体的形状和要求,设计合适的加工夹具。
夹具应具有稳定性、刚性和可靠性,以确保加工精度和表面质量。
5.质量检测设备:在加工过程中,需要对阀体进行质量检测,以确保加工质量符合要求。
常用的质量检测设备有三坐标测量机、硬度计等。
总结:毕业设计中的机械工艺夹具设计对于阀体的加工工艺和工艺装备设计起到重要的作用。
球阀阀体的加工工艺设计和工艺装备设计【车夹具】

球阀阀体的加工工艺设计和工艺装备设计【车夹具】
湖南铁道职业技术学院
课程设计
题目球阀阀体零件机械加工工艺课程设计
系机电工程系
专业机械制造及自动化
学生姓名班级
指导教师职称(务)教授
完成日期2014 年10 月9 日
课程设计评阅书
机械加工工艺课程设计任务书
机电工程系
一、设计课题名称阀体零件加工工艺设计
二、指导教师
朱鹏超
三、设计要求
1、保证零件加工质量。
2、适合一般现场条件,能显著提高生产效率。
3、降低生产成本,适应性强。
4、工艺合理,工艺资料齐全,说服力强。
四、设计依据
详见零件图
五、参考资料
1、机械制造工艺学
2、机械制造工艺设计手册
3、切削用量手册
4、公差配合与技术测量
六、设计内容及工作量
(一)设计内容
1、根据零件图确定加工余量。
2、进行加工方案设计与比较。
3、机械制造工艺设计。
4、编写设计说明书。
(二)工作量
1、零件图1张;
2、工艺卡片一套;
3、设计说明书1份
(设计内容与要求说明、设计指导思想、零件图样分析、毛坯设计、加工方案分析比较确定、机械制造工艺设计、设计说明、结束语等)
(三)设计进度。
阀体零件的工艺研究与工装设计设计
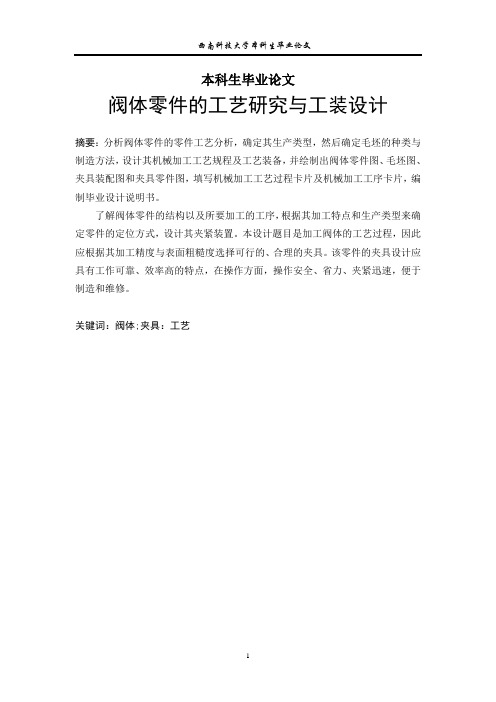
本科生毕业论文阀体零件的工艺研究与工装设计摘要:分析阀体零件的零件工艺分析,确定其生产类型,然后确定毛坯的种类与制造方法,设计其机械加工工艺规程及工艺装备,并绘制出阀体零件图、毛坯图、夹具装配图和夹具零件图,填写机械加工工艺过程卡片及机械加工工序卡片,编制毕业设计说明书。
了解阀体零件的结构以及所要加工的工序,根据其加工特点和生产类型来确定零件的定位方式,设计其夹紧装置。
本设计题目是加工阀体的工艺过程,因此应根据其加工精度与表面粗糙度选择可行的、合理的夹具。
该零件的夹具设计应具有工作可靠、效率高的特点,在操作方面,操作安全、省力、夹紧迅速,便于制造和维修。
关键词:阀体;夹具:工艺Technology research and equipment design of body partsAbstract:the analysis valve chest components craft analysis, determined its product ion type, then the determination materials type and the manufacture method, design its machine-finishing technological process and the craft equipment, and draws up t he valve chest detail drawing, the materials chart, the jig assembly drawing and the jig detail drawing, the filling in machine-finishing technological process card and th e machine-finishing working procedure card, the establishment curriculum designs t he instruction booklet.Understood the valve chest components the structure as well as must process the wo rking procedure, according to its processing characteristic and the production type d etermined the components the locate mode, designs design topic processes four aper ture same threaded holes, therefore should act according to its processing precision and the surface roughness choice feasible, the reasonable components jig design sho uld have the work reliably, the efficiency high characteristic, in the operation aspect , the operational safety, reduces effort, the clamp is rapid, and advantageous for the manufacture and the service.Key words:valve body , fixture ,craft目录第一章绪论 (5)1.1 概述 (5)1.2 国内外现状研究 (5)1.3 主要研究内容、设计思想及工作方法或工作流程 (7)1.4 选题的意义 (8)第二章阀体的工艺分析及生产类型的确定 (9)2.1 阀体的作用 (9)2.2 阀体的技术要求 (9)2.3 阀体的工艺分析 (10)2.3.1 小批量工艺分析 (10)2.3.2 大批量工艺分析 (11)第三章确定毛坯和绘制毛坯图 (13)3.1 选择毛坯种类 (13)3.2 毛坯形状的确定 (13)3.3 毛坯尺寸的确定 (14)第四章拟定阀体工艺路线 (15)4.1 定位基准选择 (15)4.2 表面加工方法确定 (15)4.3 加工阶段划分 (16)4.4工序的集中和分散 (17)4.5 工序顺序安排 (17)4.6 确定阀体工艺路线 (18)第五章工艺装备的选择 (21)5.1 机床的选择 (21)5.2 刀具的选择 (22)5.3 量具的选用 (22)第六章加工余量和工序尺寸的确定 (23)6.1 确定加工余量的目的 (23)6.2 工序余量的选用原则 (23)6.3阀体零件的加工余量 (23)第七章 切削用量和切削时间的计算 (25)7.1 铣上下端面 (25)7.1.1粗铣下端面 (25)7.1.2精铣下端面 (26)7.2 铣前后端面 (27)7.2.1选择机床 (27)7.3 辅助时间a t 的计算 (28)7.4 镗孔35H728φφ、 (28)7.5 镗孔φ22H8,φ32H8 (29)7.6 钻4×M6螺纹孔 (30)7.6.1 钻孔 (30)7.6.2 攻螺纹 (31)7.7 钻2×M8螺纹孔 (32)第八章 阀体零件的专用夹具设计 (34)8.1 基本技术要求 (34)8.2 设计主旨 (34)8.3 专用夹具 (34)8.3.1 车床夹具的主要类型 (35)8.3.2 车床夹具的设计特点 (35)8.3.3 阀体零件的车床夹具专用设计 (37)8.4 夹具的设计步骤 (37)8.4.1 夹具类型的选择 (38)8.4.2 定位方案的确定 (38)8.5车床夹具的误差分析 (40)总结 (41)致谢 (42)参考文献 (43)第一章绪论1.1 概述阀体属于箱体类零件,就制造而言,这类零件的特点是:结构较复杂,所需加工机床种类较多,随着生产纲领和生产条件的不同,其制造工艺和相应的工装也差别较大。
- 1、下载文档前请自行甄别文档内容的完整性,平台不提供额外的编辑、内容补充、找答案等附加服务。
- 2、"仅部分预览"的文档,不可在线预览部分如存在完整性等问题,可反馈申请退款(可完整预览的文档不适用该条件!)。
- 3、如文档侵犯您的权益,请联系客服反馈,我们会尽快为您处理(人工客服工作时间:9:00-18:30)。
阀体零件的工艺工装设计任务书1.课题意义及目标本设计要求在给定工艺条件及生产批量的前提下,编制零件的机械加工工艺规程,设计专用夹具(要求用Pro/E或Solidworks进行3D设计)。
2.主要任务(1)绘制被加工零件的零件图1张(2)绘制被加工零件的毛坯图1张(3)编制机械加工工艺规程卡片1套(4)设计并绘制夹具装配图1套(5)设计并绘制夹具主要零件图1张(6)编写设计说明书1份3.主要参考资料[1] 王先奎. 机械制造工艺学 [M]. 北京:机械工业出版社[2] 肖继德. 机床夹具设计 [M]. 北京:机械工业出版社[3] 李益明. 机械制造工艺设计简明手册 [M]. 北京:机械工业出版社[4] 孟宪栋. 机床夹具图册 [M]. 北京:机械工业出版社[5] 艾兴. 切削用量手册 [M]. 北京:机械工业出版社4. 进度安排审核人:年月日阀体零件的工艺工装设计摘要:在制造业中,机械制造尤为重要,大批生产的产品越来越多,工艺工装的设计对生产而言越来越重要。
它与产品的质量、生产效率及成本息息相关。
随着不规则零件的广泛应用,工艺设计显得尤为重要。
本设计通过对阀体零件的结构特点和加工要求,制定了一套较合理的工艺工装设计。
本设计的被加工零件材料为灰铸铁,生产纲领为大批生产。
由设计题目可知,设计分两大部分一是工艺设计,二是工装设计。
在工艺设计中,主要对毛坯尺寸、各表面加工方法、工艺安排、刀具及刀具材料、工序内容和工序安排进行设计。
在工装设计中,通过对被加工零件的分析,主要对定位位原件、加紧机构、夹具体及连接原件的选择进行分析设计。
最后对零件与夹具进行了三维实体建模,更直观的展示出零件加工中的定位与夹紧。
关键词:阀体零件灰铸铁工艺设计工装设计Technical Design for Valve Body PartsAbstract:Machinery manufacturing is particularly important in the manufacturing, a large number of production become more and more and technology design for the production become more and more important. It is closely related to the quality, production efficiency and the cost of product. With the wide application of irregular parts, process design is particularly important.This design through the structural characteristics and processing requirements set a set of more reasonable process design. The material of this design is gray cast iron, and the production program is mass production. According to the title ,it includes two parts . One is the design of the technology, the other is the design of tooling. In the process design, the main task is to design the blank size, the surface processing method, process arrangement, cutting tools and cutting tool material,working procedure and working procedure arrangement. In the design of tooling, via the analysis of the parts to design and analysis the positioning bits, the selection of the mechanism, the concrete and the connection of the original.At last, the 3D solid modeling of the parts and fixtures is carried out, and the positioning and clamping of the parts are displayed more intuitively. Keywords: Body parts Gray iron Process design Design of tooling目录1 绪论 (1)2.零件的工艺性分析 (1)3. 确定毛坯尺寸、设计毛坯图 (3)3.1选择毛坯 (3)3.2确定机械加工余量、毛坯尺寸和公差 (3)3.3设计毛坯图 (4)4. 选择加工方法拟定工艺路线 (5)4.1.1工序基准 (5)4.1.2定位基准 (5)4.2确定各表面加工方法 (5)4.3拟定工艺路线 (6)4.3.1方案一 (6)4.3.2方案二 (7)5. 工序设计 (9)5.1工序的选择 (9)5.2工序内容的确定 (9)6. 钻4xΦ14孔工序专用夹具设计 (33)6.1明确任务要求 (33)6.2确定夹具结构方案 (33)6.2.1定位方案的确定 (33)6.2.2设计定位原件 (34)6.2.3设计夹具体 (35)6.2.4绘制夹具总图 (35)总结 (36)参考文献 (37)致谢 (38)1 绪论经济的支柱产业,是国家创造力、竞争力和综合国力的重要体现。
机械制造工艺是应先进的工业和科学技术发展的需求发展起来的。
现代工业科学技术的发展又为机械制造业很好的提供了近一步发展的技术支持,形成良性循环,如新材料的使用、计算机技术、微电子技术、控制理论技术、信息处理技术、测试技术、人工智能理论与技术的发展与应用都促进了制作工艺技术的发展。
现代机械制造中较多的采用了数控机床、机器人、柔性制造的单元和系统等高技术的集成,来满足产品个性化和多样化的要求。
现在国内将众多学者将目光放在特种加工,但是由于特种加工的物理微观过程极其复杂,很难用简单的解析式表达出来,虽然学者采用很多理论对不同的特种加工技术进行了深入研究,也取得了卓越的理论成就,却离实际应用有一定的差距。
因此目前的研究手段,依然采用传统的加工机理通过实验统计的方式来了解特种加工的工艺规律。
工件在工艺规程确定之后,按工艺规程所定的顺序进行加工。
加工除了需机床、刀具、量具外,大批生产时还需专用的机床夹具。
夹具是机床与被加工工件间的连接装置,是工件对于机床或刀具获得正确位置的保障。
夹具的好坏会直接影响到工件加工表面位置精度与生产率;近几年,数控机床、加工中心、成组技术、柔性制造系统等新型加工技术的广泛应用,对机床夹具也提了新的要求:要能装夹一组具有相似特征的工件、能适用于精密加工的高精度机床和各种现代化的制造技术的新型机床以及采用以液压站等为动力的高效夹紧装置。
综合运用机械设计制造及其自动化专业的专业知识,分析和解决实际工程问题,以及设计机床夹具的能力。
通过设计过程,熟悉有关标准和设计资料,学会使用有关手册和数据库。
也作为我们未来从事机械制造技术工作的一次重要的基本训练。
本课题的的设计重点是明白机械加工工艺规程和工艺装备设计,其中机械加工工艺过程就是用切削的方法改变毛坯的形状、尺寸和材料的物理机械性,成为具有所需要的一定精度、粗糙度等的零件。
学习研究机械加工工艺规程的意义与作用及相关工装夹具的设计。
2.零件的工艺性分析通过对零件图的重新绘制,该零件为类回转体零件,其主体部分以中心轴为回转中心,一端直径为160mm宽度的16mm的底座,在外圆上有两个尺寸不同的圆柱凸台,两者轴线之间的角度为90度,回转中心处在同一径向平面上。
大凸台中心处是一个直径为48mm的螺纹孔,小凸台中心上是直径为18mm的螺纹孔。
该零件两端的沉孔精度要求不高可由粗加工完成,内腔的壁经度要求较高,内腔壁的精度为7级表面粗糙度为Ra3.2,此外大端面一端的直径为60mm的内孔,表面粗糙度为Ra6.3,两端的沉孔精度为11级,表面粗糙度为Ra6.3。
属于类回转体的两端面及内腔,其各表面的加工精度,及表面粗糙度可通过机械加工获得。
首先加工两个端面,其中大端面为设计基准。
内腔各尺寸以大端面及轴线为设计基准。
其精度要求较高,尺寸较大的内腔可采用镗削加工。
大端面的各个孔,位置分布均匀,且厚度不大,便于对空的加工。
两个凸台的端面及尺寸大的凸台的内螺纹,可通过车床加工获得,尺寸较小的凸台的螺纹可在打孔时值直接获得。
总体来说此零件的工艺性较好。
3. 确定毛坯尺寸、设计毛坯图3.1选择毛坯所选的毛坯应满足力学的性能要求,相同的材料在不同的加工方法下,其力学性能也不相同。
还应考虑零件的结构和形状尺寸,除此之外还应考虑生产的纲领和批量及现场条件和发展。
根据零件图的要求,此零件采用的材料为灰铸铁,形状简单,故采用铸件毛坯。
由于零件的生产类型为大批生产根据参考文献[3]表2.2-6可知采用砂型铸件,不但生产效率高,同时保证了毛坯的尺寸,便于加工。
3.2确定机械加工余量、毛坯尺寸和公差根据[3]表2.2-2确定所选公差等级为CT13。
根据参考文献[3]表2.2-6得机械加工余量等级为G。
根据表2.2-5查出要求的机械加工余量,再根据表2.2-1查出铸件尺寸公差。
从而确定出铸件的单边余量及双边余量。
根据各加工表面精度及零件尺寸确定毛坯的尺寸,在毛坯中,大端面上的各孔孔及小凸台的螺纹孔为实心。
由公式R= F+RMA+CT/2(单边余量)R= F+2RMA+CT/2(双边外尺寸余量)R= F-2RMA-CT/2(双边内尺寸余量)式中R为毛坯基本尺寸 F为加工零件尺寸 RMA为要求的机械加工余量可计算出毛坯尺寸其中M48的螺纹孔计算结果为36.24mm考虑到零件图的具体形状,取尺寸值为36mm。
毛坯各尺寸见下表:3.3设计毛坯图根据零件尺寸确定外圆角半径为3mm,内圆角半径为3mm,是圆角尺寸能够保证个表面的加工余量。
确定分模位置零件为类回转体零件,结构简单。
为方便起模,分模位置应选在零件中心轴线上,分型面为过零件轴心和大凸台轴线的面。
热处理方式采用时效处理,消除毛坯内部应力,以保证加工精度。