数控加工程序编制G74
G代码的详细解释(主要是车床)
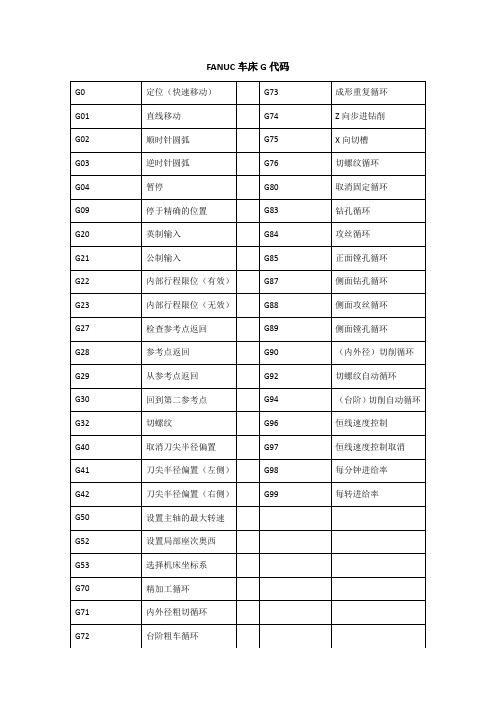
FANUC车床G代码切螺纹(G32)1、格式G32 X(U)_Z(W)_F_;G32 X(U) _Z(W)_E_;F--螺纹导程设置E--螺距(毫米)X(U)__ Z(W)__螺纹切削的终点坐标值在编制切螺纹程序时应当带主轴转速RPM均匀控制的功能(G97),并且要考虑螺距部分的某些特性。
在螺纹切削方式下移动速率控制和主轴速率控制功能将被忽略。
而且在送进保持按钮起作用时,其移动进程在完成一个切削循环后就停止了。
X省略时为圆柱螺纹切削,Z 省略时为端面螺纹切削;X、Z均布省略时为锥螺纹切削;F为导程。
螺纹切削应注意在两端设置足够的升速进刀段和降速退刀段。
2、举例G00 X29.4;(1循环切削)G32 Z-23. F0.2;G00 X32;Z4;X29;(2切削循环)G32 Z-23. F0.2;G00 X32;Z4刀具直径偏置功能(G40/G41/G42)精加工循环(G70)G7l U(△d) R(e);G71 P(ns) Q(nƒ) u(△u) W(△ω) F(ƒ) S(s) T(t);G70 P(ns) Q(nƒ);格式中,△d为切削深度(半径值指定,不带正负符号,且为模态指令);e为退刀量(模态指令);ns为精车程序段的开始段落号;nƒ为精车程序段的结束段落号;△u为x轴方向的精车余量(有正负符号,直径指令);△ω为z轴方向的精车余量(有正负符号);ƒ、s、t为粗加工循环中的进给速度、主轴转速及刀具功能;G70为精车循环,该命令不能单独使用,需在粗车复合循环指令之后。
精加工时,G71等中的F、S、T指令无效,只有在ns~nf中的才有效。
该指令执行如图所示的粗加工和精加工,其中其精加工路径为A→A′→B′→B的轨迹。
1.采用复合固定循环需设置一个循环起点,刀具按照数控系统安排的路径一层一层按照直线插补形式分刀车削成阶梯形状,最后沿着粗车轮廓车削一刀,然后返回到循环起点完成粗车循环。
数控加工G代码及介绍(FANUC系统)

FANUC 0-TD系统FANUC 0-TD系统G 代码命令代码组及其含义“模态代码” 和“一般” 代码“形式代码” 的功能在它被执行后会继续维持,而“一般代码” 仅仅在收到该命令时起作用。
定义移动的代码通常是“模态代码”,像直线、圆弧和循环代码。
反之,像原点返回代码就叫“一般代码”。
每一个代码都归属其各自的代码组。
在“模态代码”里,当前的代码会被加载的同组代码替换。
G代码组别解释G00 01 定位 (快速移动)G01 直线切削G02 顺时针切圆弧(CW,顺时钟)G03 逆时针切圆弧(CCW,逆时钟)G04 00 暂停 (Dwell)G09 停于精确的位置G20 06 英制输入G21 公制输入G22 04 内部行程限位有效G23 内部行程限位无效G27 00 检查参考点返回G28 参考点返回G29 从参考点返回G30 回到第二参考点G32 01 切螺纹G40 07 取消刀尖半径偏置G41 刀尖半径偏置(左侧)G42 刀尖半径偏置(右侧)G50 00 修改工件坐标;设置主轴最大的 RPMG52 设置局部坐标系G53 选择机床坐标系G70 00 精加工循环G71 内外径粗切循环G72 台阶粗切循环G73 成形重复循环G74 Z 向步进钻削G75 X 向切槽G76 切螺纹循环G80 10 取消固定循环G83 钻孔循环G84 攻丝循环G85 正面镗孔循环G87 侧面钻孔循环G88 侧面攻丝循环G89 侧面镗孔循环G90 01 (内外直径)切削循环G92 切螺纹循环G94 (台阶) 切削循环G96 12 恒线速度控制G97 恒线速度控制取消G98 05 每分钟进给率G99 每转进给率代码解释G00 定位1. 格式 G00 X_ Z_ 这个命令把刀具从当前位置移动到命令指定的位置(在绝对坐标方式下),或者移动到某个距离处 (在增量坐标方式下)。
2. 非直线切削形式的定位我们的定义是:采用独立的快速移动速率来决定每一个轴的位置。
数控铣床的程序编制基本指令

基本指令编程及应用
1 加工坐标系的设定指令
(1)G92——预置寄存指令,即建立坐标系,机床(刀 具、工作台)不产生运动,通过该指令设定起刀点即 程序开始运动的起点。 格式:G92 X Y Z ;
式中X、Y、Z尺寸字是指起刀点相对于加工原点的位 置。 应用: 应用:G92 X20 Y10 Z10 示意图如右图
超链文件\用户宏程序应用举例.doc
6 编程时应注意的问题
§4.3 图形的数学处理
1 直线轮廓的图形处理
两平行铣削平面的数学处理 两相交铣削平面的数学处理 定斜角直线轮廓的处理
2 空间曲面的数学处理
铣削空间曲面的方法 确定行距与步长(插补段的长度)
行距S的计算方法 确定步长L
§4.4 典型零件的程序处理
平面凸轮的工艺分析及编程 应用宏功能指令加工空间曲线 铣削软件模拟(1):熟悉铣削加工仿真软件的 1 : 使用 铣削软件模拟(2):能进行一般零件的铣削加 工仿真
平面凸轮的工艺分析及编程
平面凸轮的工艺分析及编程
1 工艺分析 2 加工调整(超链文件\数控加工工序卡.doc) 3 数学处理(超链文件\平面凸轮数学处理方法.doc)
式中:X、Y、Z--比例中心坐标(绝对方式),P-比例系数。
(2)各轴以不同比例编程 编程格式:G51 X~ Y~Z~ I~J~K~ G50
式中:X、Y、Z --比例中心坐标;I、J、K -- 对 应X、Y、Z轴的比例系数 (3)镜像功能(比例及镜像功能)
§4.2.2 基本指令编程及应用
9.坐标系旋转功能 G68、G69
1 加工坐标系的设定指令
(3)G54、G55、G56、G57、G58、G59 这些指令可
实训任务九 固定循环G70-G71-G72-G73-G74-G75
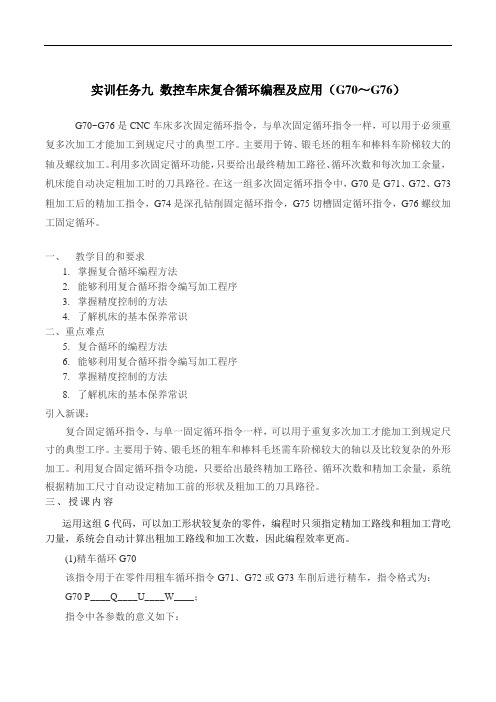
实训任务九数控车床复合循环编程及应用(G70~G76)G70~G76是CNC车床多次固定循环指令,与单次固定循环指令一样,可以用于必须重复多次加工才能加工到规定尺寸的典型工序。
主要用于铸、锻毛坯的粗车和棒料车阶梯较大的轴及螺纹加工。
利用多次固定循环功能,只要给出最终精加工路径、循环次数和每次加工余量,机床能自动决定粗加工时的刀具路径。
在这一组多次固定循环指令中,G70是G71、G72、G73粗加工后的精加工指令,G74是深孔钻削固定循环指令,G75切槽固定循环指令,G76螺纹加工固定循环。
一、教学目的和要求1.掌握复合循环编程方法2.能够利用复合循环指令编写加工程序3.掌握精度控制的方法4.了解机床的基本保养常识二、重点难点5.复合循环的编程方法6.能够利用复合循环指令编写加工程序7.掌握精度控制的方法8.了解机床的基本保养常识引入新课:复合固定循环指令,与单一固定循环指令一样,可以用于重复多次加工才能加工到规定尺寸的典型工序。
主要用于铸、锻毛坯的粗车和棒料毛坯需车阶梯较大的轴以及比较复杂的外形加工。
利用复合固定循环指令功能,只要给出最终精加工路径、循环次数和精加工余量,系统根据精加工尺寸自动设定精加工前的形状及粗加工的刀具路径。
三、授课内容运用这组G代码,可以加工形状较复杂的零件,编程时只须指定精加工路线和粗加工背吃刀量,系统会自动计算出粗加工路线和加工次数,因此编程效率更高。
(1)精车循环G70该指令用于在零件用粗车循环指令G71、G72或G73车削后进行精车,指令格式为:G70 P____Q____U____W____;指令中各参数的意义如下:P:精车程序第一段程序号;Q:精车程序最后一段程序号;U:沿X方向的精车余量;W:沿Z方向的精车余量。
编程注意事项:(1)精车过程中的F、S、T在程序段号P到Q之间指定。
(2)在车削循环期间,刀尖半径补偿功能有效。
(3)在P和Q之间的程序段不能调用子程序。
加工中心的程序编制
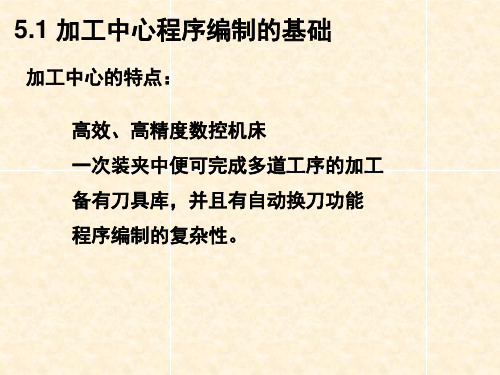
//返回Z向起始点
N90 M05
//主轴停
N100 M30
//程序结束并返回起点
加工坐标系设置:G56 X= - 400,Y = -150,Z = - 50。
5.2.2螺纹加工循环指令(攻螺纹加工) 1、G84(右旋螺纹加工循环指令)
a )G84(G98)
螺纹加工循环
b )G84(G99)
2、G74(左旋螺纹加工循环指令)
N10 G54 G90 G00 X0 Y0 Z30
//进入加工坐标系
N20 T01 M98 P9000
//换用T01号刀具
N30 G43 G00 Z5 H01
//T01号刀具长度补偿
N40 S600 M03
//主轴起动
N50 G99 G81 X40 Y-35 Z-63 R-27 F120 //加工#1孔(回R平面)
5.1.2 加工中心的工艺及工艺装备
工艺范围: 铣削
钻削
螺纹加工
镗削加工
1、工艺性分析
(1)选择加工内容 加工中心适合加工: 形状复杂 工序较多 精度要求较高的零件
(2)检查零件图样 基准要统一
零件加工的基准统一
(3)分析零件的技术要求
(4)审查零件的结构工艺性 2、工艺过程设计
主要考虑的问题: 精度 效率
//换刀子程序结束,返回主程序。
5.2 FANUC系统固定循环功能
固定循环功能:它规定对于一些典型孔加工中的固 定、连续的动作,用一个G指令表达,即用固定循 环指令来选择孔加工方式。
主要用于:钻孔、攻螺纹和镗孔等
六个基本动作:
1、在XY平面定位
2、快速移动到R平面
4、孔底动作
3、孔的切削加工
数控技术期末复习题
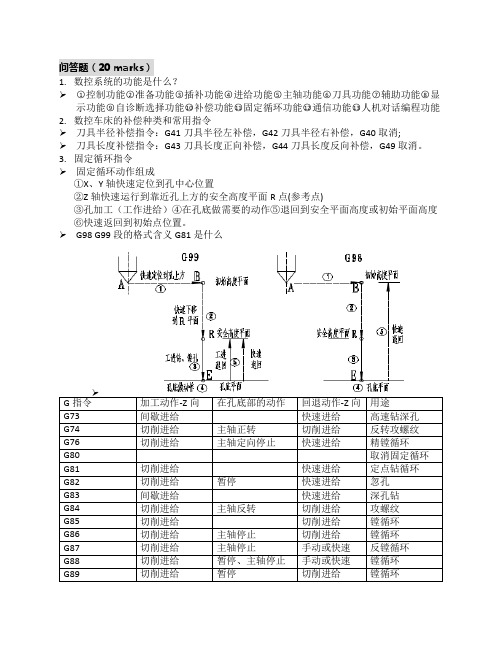
问答题(20 marks)1.数控系统的功能是什么?➢○1控制功能○2准备功能○3插补功能○4进给功能○5主轴功能○6刀具功能○7辅助功能○8显示功能○9自诊断选择功能○10补偿功能○11固定循环功能○12通信功能○13人机对话编程功能2.数控车床的补偿种类和常用指令➢刀具半径补偿指令:G41刀具半径左补偿,G42刀具半径右补偿,G40取消;➢刀具长度补偿指令:G43刀具长度正向补偿,G44刀具长度反向补偿,G49取消。
3.固定循环指令➢固定循环动作组成①X、Y轴快速定位到孔中心位置②Z轴快速运行到靠近孔上方的安全高度平面R点(参考点)③孔加工(工作进给)④在孔底做需要的动作⑤退回到安全平面高度或初始平面高度⑥快速返回到初始点位置。
➢G98 G99段的格式含义G81是什么计算题(25 marks)1.已知编程要求的进给速度F=1000mm/min,试求:➢在开环数控系统采用脉冲增量插补时,执行元件步进电机的脉冲频率f?(已知脉冲当量δ=0.01mm.)➢采用数据采样插补方式时,轮廓步长应为多少可满足要求的进给速度?(已知插补周期T=8ms.)F=60δf ; f=100060∗0.01=1666.67(Hz) ; L=FT=1000∗860∗1000=0.1333(mm)2.数字积分法➢直线插补举例设有一直线OA,起点在坐标原点,终点的坐标为(4,6)。
试用DDA法直线插补此直线。
➢圆弧插补举例有第一象限逆圆弧DDA,起点A(5,0),终点(0,5),设寄存器位数为3。
试用 DDA法插补此圆弧。
3.逐点比较法➢直线插补举例欲加工第一象限直线OE,终点坐标为xe=3 , ye =5,试用逐点比较法进行插补计算,并画➢圆弧插补举例加工第一象限逆圆弧,起点为A(5,0),终点为B(0,5),试用逐点比较法进行插补计算,并画第四章数控插补原理插补算法分类:目前使用的插补算法有两类:脉冲增量插补(基准脉冲插补法)和数字增量插补(数据采样插补)。
数控车床使用G74指令加工端面槽方法初探

数控车床使用G74指令加工端面槽方法初探作者:林良颖来源:《CAD/CAM与制造业信息化》2013年第06期本文介绍了在GSK980T数控系统的车床上,普通轴类零件的端面槽加工方法,阐述了端面槽的加工工艺。
从加工效率和加工表面质量2个方面,对刀具形状、刀具路径以及代码选择进行了分析,合理地选用了相应的G代码进行编程加工。
在广州数控GSK980T的系统中,G74是端面深孔加工循环指令。
无论在系统使用说明书还是市面上的一些教学书籍里,都只介绍了使用G74进行钻孔和镗孔加工的车削方法。
笔者在指导学生实训的过程中,对使用G74进行端面槽加工进行了一些尝试。
本文将对使用G74加工端面槽过程中的编程方法、切削用量以及刀具角度等方面进行初步探讨,希望在工作和学习中对读者有所助益。
一、G74的指令格式及使用说明1.格式G74的指令格式如下:◎G74 R(e);◎G74 X(U)Z(W)P(Δi)Q(Δk)R(Δd)F(f)。
2.各参数的含义各参数的含义如下:◎R(e)——每次Z方向切削Q值后的退刀量;◎X,Z——绝对值终点坐标尺寸;◎P(Δi)——X方向的每次循环移动量(直径),即X方向的每次吃刀深度;◎Q(Δk)——Z方向的每次循环移动量;◎R(Δd)——切削终点时X方向的退刀量;◎F(f)——切削进给速度。
3.走刀方向、路线走刀方向、路线示意图,如图1所示。
二、编程举例现要加工图2所示的零件的端面槽。
端面槽宽7mm,槽深6mm。
此槽的特点是槽较宽,但不是深槽。
从加工工艺上考虑,不能一次切削,径向进刀只能是采用分级进刀,同样轴向进给也要分刀进给。
现采用手工编程的方式在数控车床上加工该槽,在编程前先设置好加工路线和刀具。
◎加工路线分2种:①从槽的内边到槽的外边切削;②从槽外边到槽内边的切削。
◎刀具选用4mm的切槽刀。
◎根据该系统的特点,可选用的G代码有2种:单一指令G01和循环指令G74。
但因为G01的编程较为复杂,容易出错,因此选择循环指令G74最为合适。
数控加工程序编制-加工中心-孔类零件程序编制全解

G88循环
二、相关知识
(二)固定循环功能
(5)精镗循环(G76) 指令格式: G76 X_ Y_ Z_ R_ Q_ F_
精镗时,主轴在孔底定向停止后,向刀尖反方向移 动,然后快速退刀。
这种带有让刀的退刀不会划伤已加工平面,保证了 镗孔精度。
程序格式中,Q 表示刀尖的偏移量,一般为正数, 移动方向由机床参数设定。
1
钻中心孔
2
钻φ5mm通孔
3
攻丝
螺纹孔加工工序卡
刀具规格
类型
材料
A4中心钻
高速钢
Φ4.2mm麻花钻 高速钢
M5mm细牙丝锥 高速钢
主轴转速 (r/min)
1200 600 80
进给速度 (mm/min)
20 30 64
(6)编制零件螺纹孔钻中心孔加工程序
四、拓展知识
用西门子802D孔及螺纹加工循环指令加工图零件。
(二)固定循环功能
(2)带停顿的钻孔循环(G82) 指令格式:
G82 X_Y_Z_P_R_F_
G82循环
该指令除了要在孔底暂停外,其它动作与G81相同。暂 停时间由地址P给出。此指令主要用于加工盲孔,以提 高孔深精度。
二、相关知识
(二)固定循环功能
(3)断屑式深孔加工循环(G73)
指令格式: G73 X_Y_Z_Q_R_F_
三、工作任务的完成
(一)数控加工工艺的制订
4.刀具准备,填写刀具卡
序号
1 2 3
4
5 6 7
刀具号
T05 T06 T07
名称 麻花钻 麻花钻 镗刀
T08 镗刀
T09 中心钻 T10 机用铰刀 T11 麻花钻
刀具规格 直径
- 1、下载文档前请自行甄别文档内容的完整性,平台不提供额外的编辑、内容补充、找答案等附加服务。
- 2、"仅部分预览"的文档,不可在线预览部分如存在完整性等问题,可反馈申请退款(可完整预览的文档不适用该条件!)。
- 3、如文档侵犯您的权益,请联系客服反馈,我们会尽快为您处理(人工客服工作时间:9:00-18:30)。
•
•
◆ Δd为刀具在切削底部的Z向退刀量,无要求时可省略;
注:程序段中的Δi、Δk值,在FANUC系统中,不能输入小数点,而直接输入 最小
G74 R(e); G74 Z(W) Q(△k) F ~ ;
式中:e —退刀量; Z(W) — 钻削深度; ∆ k — 每次钻削长度(不加符号)。
例:编写进行图示零件切断加工的程序其中:e=5,∆ k=20,F=0.1。 O0001; N10 G54 T0101; N20 M03 S600; N30 G00 X0 Z1.; N40 G74 R5.; N50 G74 Z-80. Q20. F0.1; N60 G00 X100. Z50.; N70 M30;
二、扩孔
2. 扩孔钻的结构
1) 齿数多(3、4齿); 2)不存在横刃; 3)切削余量小,排屑容易。
图6-10扩孔钻三 Nhomakorabea铰孔1. 铰刀的类型
直柄机用铰刀 套式机用铰刀 锥柄机用铰刀 硬质合金锥柄机用铰刀
手用铰刀
直柄莫氏圆锥铰刀
手用1:50 锥度铰刀 可调节手用铰刀 图6-14 铰刀的类型
四、镗孔
螺纹切削G32与G01
指令格式:G32 X(U)__Z(W)__F__; X、Z:为螺纹切削的终点坐标值。 U 、 W :为增量编程时,有效螺纹终点相对于螺纹切削起点的 增量。 Z F为螺纹导程。
X
G92与G90
G92 X(U) Z(W) F ; 各参数的含义: X(U) Z(W) :螺纹切削终点处的坐标;
金 刚 镗 IT5~7 Ra0.16~1.25
珩 磨 IT5~6 Ra0.04~1.25 研 磨 IT5~6 Ra0.008~0.63
粗 镗 IT12~13 Ra 5~20
粗 拉 IT9~10 Ra 1.25~5
孔的典型加工工艺路线
孔加工刀具
螺纹车刀 内孔车刀
钻头
内切槽车刀 内螺纹车刀
铰刀 丝锥
F: 螺纹导程的大小,如果是单线螺纹, 则为螺距的大小。
螺纹复杂循环指令G76与G71
G76 P(m)(r)(a) Q(∆dmin )R(d) G76 X(U) Z(W) R(i) P(k) Q(Δd ) F(L)
径向切槽循环G75 • • 1)指令格式 G75 R(e)
•
• • • •
G75 X()Z()P(Δi)Q(Δk)R(Δd)F()
一、钻孔
二、扩孔
1. 工艺特点 1)扩孔是孔的半精加工方法; 2)一般加工精度为IT10~IT9; 3)孔的表面粗糙度可控制在Ra6.3 ~ 3.2μm。
当钻削 dw > 30mm 直径的孔时,为了减小钻削力 及扭矩,提高孔的质量,一般先用(0.5~0.7)dw 大小的钻头钻出底孔,再用扩孔钻进行扩孔,则可 较好地保证孔的精度和控制表面粗糙度,且生产率 比直接用大钻头一次钻出时还要高。
•
编程单位.如:P1500表示径向每次切深量为1.5mm
• • • • • • •
1、径向切槽循环G75 1)指令格式 G75 R(e) G75 X()Z()P(Δi)Q(Δk)R(Δd)F() ◆ e 为退刀量,其值为模态值; ◆ X() Z()为切模终点处的坐标; ◆ Δi为X方向的每次切深量,用不带符号的半径量表示;
六、内圆磨削
内圆磨削与外圆磨削相比,存在如下一些主要问题: 1) 内圆磨削的表面较外圆磨削的粗糙。 2) 生产率较低。 3) 磨削接触区面积较大,砂轮易堵塞,散热和切削液 冲刷困难。
因此内孔磨削一般仅适用于淬硬工件的精加工, 在单件、小批生产中和在大批大量生产中都有应用。
1.G74指令格式(2)
•
• • •
◆ Δk为刀具完成一次径向切削后,在Z方向的偏移量,用不带符号的值表;
◆ Δd为刀具在切削底部的Z向退刀量,无要求时可省略; 注:程序段中的Δi、Δk值,在FANUC系统中,不能输入小数点,而直接输入最 小 编程单位.如:P1500表示径向每次切深量为1.5mm
数控加工程序编制
轴套的数控加工程序编制
3.编程举例(1)
【示例2-25】 加 工如图所示的端面 环形槽及中心孔零 件,编写加工程序。
3.编程举例(2)
以工件右端面中心 为工件坐标系原点, 切槽刀刀宽为 3㎜ , 以左刀尖为刀位点; 选择φ10钻头进行 中心孔加工。
O2024 3.编程举例( 3) T0101; G99 M03 S600; G00 X24.0 Z2.0; G74 R0.3; G74 X20.0 Z-5.0 P2000 Q2000 F0.1; G00 X100.0 Z50.0; T0202; G00 X0.0 Z2.0; G74 R0.3; G74 Z-28.0 Q2000 F0.08; G00 X100.0 Z50.0; M05; M30;
一、钻孔
钻头 钻套 钻模板
工件
一、钻孔
1. 工艺特点
1)钻孔是孔的粗加工方法; 2)可加工直径0.05~125mm的孔; 3)孔的尺寸精度在IT10以下; 4)孔的表面粗糙度一般只能控制在Ra12.5μm。
对于精度要求不高的孔,如螺栓的贯穿孔、 油孔以及螺纹底孔,可直接采用钻孔。
2. 高速钢麻花钻的结构
图6-22 常见的拉削截形(A~G为内拉拉削,H~L为外拉削)
六、内圆磨削
六、内圆磨削
1. 工艺特点 1)磨削是零件精加工的主要方法之一; 2)对长径比小的,内孔磨削的经济精度可达IT5~ IT6,表面粗糙度可控制到Ra0.8mm~Ra0.2mm; 3)可加工较硬的金属材料和非金属材料,如淬火钢、 硬质合金和陶瓷等。
孔加工方法选择
扩 IT9~13 Ra 1.25~40 钻 IT10~13 Ra 5~80 半 精 镗 IT10~11 Ra 2.5~10 饺 IT6~9 Ra 0.32~10 手 饺 IT5 Ra0.08~1.25 滚 压 IT6~8 Ra0.01~1.25
精 镗 IT7~9 Ra 0.63~5
粗 磨 IT9~11 Ra1.25~10 精 拉 IT7~9 Ra0.16~0.63 推 IT6~8 Ra0.08~1.25 精 磨 IT7~8 Ra0.08~0.63
2.走刀路线分析
●刀具端面切槽时,以Δk的切深量进行轴向 切削,然后回退 e 的距离,方便断屑,再以 Δk的切深量进行轴向切削,再回退 e距离, 如此往复,直至到达指定的槽深度; ●刀具逆槽宽加工方向移动一个退刀距离Δd, 并沿轴向回到初始加工的Z向坐标位置,然后 沿槽宽加工方向刀具移动一个距离Δi,进行 第二次槽深方向加工,如此往复,直至达到 槽终点坐标。
G74 R(e); G74 X(U) Z(W) P(Δi)Q(Δk)R(Δd)F ; e—退刀量,该值是模态值; X(U)、Z(W)—切槽终点处坐标值; Δi—刀具完成一次轴向切削后,在X方向的移动量(该值 用不带符号的半径值表示); Δk—Z方向每次切削深度(该值用不带符号的值表示); Δd—刀具在切削底部的退刀量,d的符号总是“+”值; F—切槽进给速度。 该循环可实现断屑加工,如果X(U)和P(Δi)都被忽略, 则是进行中心孔加工。
1. 工艺特点
1)镗孔可不同孔径的孔进行粗、半精和精加工; 2)加工精度可达为IT7~IT6; 3)孔的表面粗糙度可控制在Ra6.3 ~ 0.8μm。 4)能修正前工序造成的孔轴线的弯曲、偏斜等形 状位置误差;
四、镗孔
2. 镗刀结构
五、拉孔
五、拉孔
1. 拉削过程
图6-26 拉削键槽
2. 拉削工艺范围