5大工具《FMEA失效分析(最新教材)》
某公司质量管理体系五种核心工具FMEA
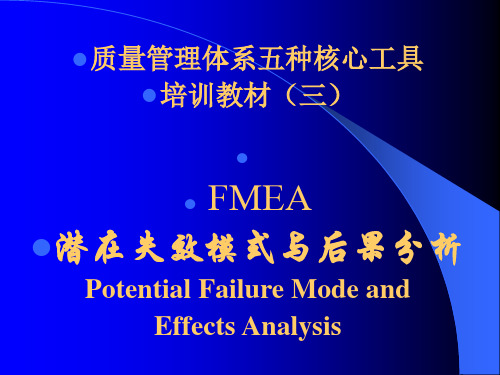
当设计为一复杂系统时,DFMEA可使用两者综合的分 析方法。
DFMEA的分析架构可由上至下或由下至上。
— 如果蓝图、工程或设计资料中很能明确的定义出硬件, 则DFMEA通常使用硬件分析法且多使用由下至上的架构。
尽早做好FMEA文件,尽早提出“建议措施”并能得到
设计FMEA标准表格
潜在失效模式及后果分析
(设计FMEA)
_____系统
FMEA编号_________
______子系统
页码:第 页 共 页
零件组:__________________ 设计责任:____________ 编制者:____________ _
—— 在一个新的环境、地点或应用上,利用了现 有的设计或过程(假设现有的设计或过程已有 FMEA)。该FMEA的领域是对现有的设计或过程在 新环境、地点或应用上的影响分析。
依靠团队的智慧 ——FMEA的输入应依靠小组的努力 ——由知识和经验丰富的人员组成小组(如:对
设计、分析/测试、制造、装配、服务、回收再利用、 质量及可靠度方面的工程人员)
也应考虑产品维护(服务)和回收利用技术的/物 质的限制。例如:工具的可获得性、诊断能力、材料 分类符号(回收利用)。
㈦、设计FMEA初始阶段的工作
在进行设计FMEA开始时,负责设计的工程师应 列出设计希望做什么?不希望做什么?
— 充分理解、明了设计意图
— 顾客要求和需求,其来源如:通过质量功能展开、 车辆要求文件、已知的产品要求和/或制造、装配、服 务、回收利用等要求。
变速器部件
潜在失效模式:
……
5大工具《FMEA失效分析(最新教材)》
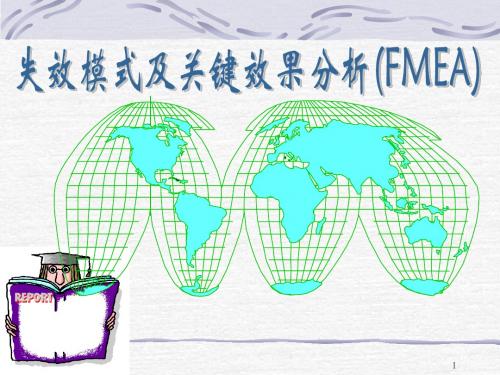
一、基本概念 (续)
8.失效的判定
不同的产品,不同的使用状况,不同的 失效模式,失效的判定很难统一规定。例如: 齿轮出现蚀点,对精密仪器而言即为失效, 但对重型机械,则不算失效,除非腐蚀到一 定的程度。
9.失效的原因
研究失效,首先要得到失效的真实状况, 比如失效出现的部位,发生的时间、失效模式、 失效原因、失效产生的影响、失效改正方法、 修复方式及修复成本等。
失效探測度(D)評價準則
探查性 評價準則:在下一個或後續工藝前,或另部件 離開製造或裝配工位之前,利用過程控制方法 找出缺陷存在的可能性 沒有已知的控制方法能找出失效模式 現行控制方法找出失效模式的可能性很微小 現行控制方法找出失效模式的可能性微小 現行控制方法找出失效模式的可能性很小 現行控制方法找出失效模式的可能性小 現行控制方法找出失效模式的可能性中等 現行控制方法找出失效模式的可能性中等偏上 現行控制方法找出失效模式的可能性高 現行控制方法找出失效模式的可能性很高 現行控制方法幾乎肯定能找出失效模式,已知 相似工藝的可靠的探測控制方法 排度 幾乎不可能 很微小 微小 很小 小 中等 中上 高 很高 幾乎肯定 10 9 8 7 6 5 4 3 2 1
5
FMEA潛在失效模式及後果分析
兩種FMEAs
過程FMEA:
由製造工程師/小組採用的一種分析技術,以加 工工藝過程的每道工序為分析對象 用來在最大範圍內保證已充分地考慮到工藝過程 設計和列出各種潛在的失效模式及其相關的起因, 並評估其對最後的產品影響 它並不依靠改變產品設計來克服過程缺陷,是要 考慮製造
1
甚麼是潛在失效模式及後果分析?
F M E A ----Failure (潛在失效) Mode (模式) Effects (後果) Analysis (分析)
五大工具潜在失效模式与效果分析FMEA
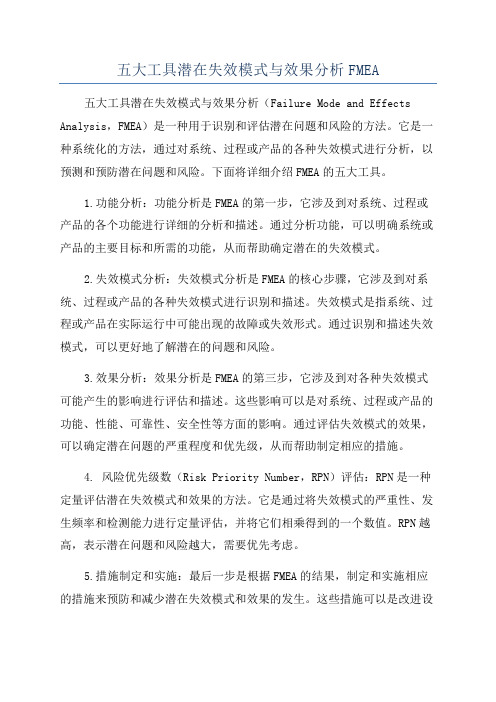
五大工具潜在失效模式与效果分析FMEA 五大工具潜在失效模式与效果分析(Failure Mode and Effects Analysis,FMEA)是一种用于识别和评估潜在问题和风险的方法。
它是一种系统化的方法,通过对系统、过程或产品的各种失效模式进行分析,以预测和预防潜在问题和风险。
下面将详细介绍FMEA的五大工具。
1.功能分析:功能分析是FMEA的第一步,它涉及到对系统、过程或产品的各个功能进行详细的分析和描述。
通过分析功能,可以明确系统或产品的主要目标和所需的功能,从而帮助确定潜在的失效模式。
2.失效模式分析:失效模式分析是FMEA的核心步骤,它涉及到对系统、过程或产品的各种失效模式进行识别和描述。
失效模式是指系统、过程或产品在实际运行中可能出现的故障或失效形式。
通过识别和描述失效模式,可以更好地了解潜在的问题和风险。
3.效果分析:效果分析是FMEA的第三步,它涉及到对各种失效模式可能产生的影响进行评估和描述。
这些影响可以是对系统、过程或产品的功能、性能、可靠性、安全性等方面的影响。
通过评估失效模式的效果,可以确定潜在问题的严重程度和优先级,从而帮助制定相应的措施。
4. 风险优先级数(Risk Priority Number,RPN)评估:RPN是一种定量评估潜在失效模式和效果的方法。
它是通过将失效模式的严重性、发生频率和检测能力进行定量评估,并将它们相乘得到的一个数值。
RPN越高,表示潜在问题和风险越大,需要优先考虑。
5.措施制定和实施:最后一步是根据FMEA的结果,制定和实施相应的措施来预防和减少潜在失效模式和效果的发生。
这些措施可以是改进设计、优化工艺、加强检测和监控等。
通过实施这些措施,可以避免或降低潜在问题和风险的发生。
FMEA是一种非常实用的分析工具,广泛应用于各个行业和领域。
它可以帮助组织识别和评估潜在问题和风险,从而采取预防措施,提高系统、过程或产品的质量和可靠性。
质量管理体系(16949)的五大工具

质量管理体系(16949)的五⼤⼯具要实现质量管理体系(ITAF16949)离不开五⼤⼯具的⽀持,五⼤⼯具分别是:统计过程控制(SPC,Statistical Process Control)、测量系统分析(MSA,Measurement System Analyse)失效模式和效果分析(FMEA,Failure Mode & Effect Analyse)、产品质量先期策划(APQP,Advanced Product Quality Planning)、⽣产件批准程序(PPAP,Production Part Approval Process)。
1 SPC 是⼀种制造控制⽅法,是将制造中的控制项⽬,依其特性所收集的数据,通过过程能⼒的分析与过程标准化,发掘过程中的异常,并⽴即采取改善措施,使过程恢复正常的⽅法。
利⽤统计的⽅法来监控制造过程的状态,确定⽣产过程在管制的状态下,以降低产品品质的变异 SPC能解决之问题:a.经济性:有效的抽样管制,不⽤全数检验,不良率,得以控制成本。
使制程稳定,能掌握品质、成本与交期。
b.预警性:制程的异常趋势可即时对策,预防整批不良,以减少浪费。
c.分辨特殊原因:作为局部问题对策或管理阶层系统改进之参考。
d.善⽤机器设备:估计机器能⼒,可妥善安排适当机器⽣产适当零件。
5.改善的评估:制程能⼒可作为改善前後⽐较之指标。
2 MSA 是对每个零件能够重复读数的测量系统进⾏分析,评定测量系统的质量,判断测量系统产⽣的数据可接受性。
MSA使⽤数理统计和图表的⽅法对测量系统的分辨率和误差进⾏分析。
以评估测量系统的分辨率和误差对于被测量的参数来说是否合适,并确定测量系统误差的主要成分。
3 FMEA 在设计和制造产品时,通常有三道控制缺陷的防线:避免或消除故障起因、预先确定或检测故障、减少故障的影响和后果。
FMEA正是帮助我们从第⼀道防线就将缺陷消灭在摇篮之中的有效⼯具。
IATF16949标准五大工具简介
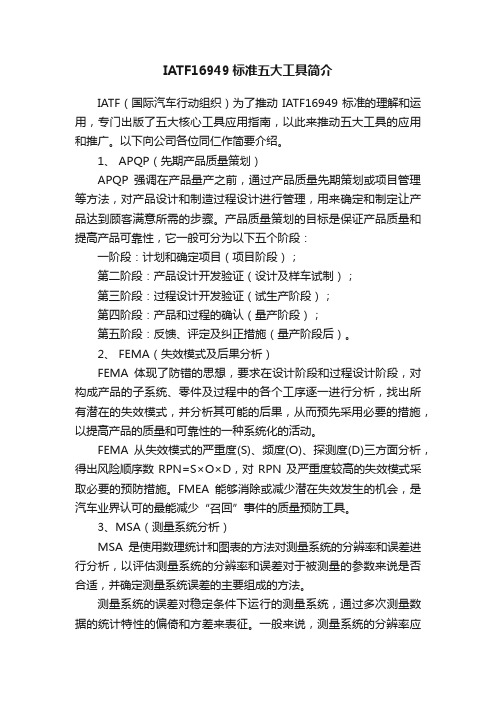
IATF16949标准五大工具简介IATF(国际汽车行动组织)为了推动IATF16949标准的理解和运用,专门出版了五大核心工具应用指南,以此来推动五大工具的应用和推广。
以下向公司各位同仁作简要介绍。
1、 APQP(先期产品质量策划)APQP强调在产品量产之前,通过产品质量先期策划或项目管理等方法,对产品设计和制造过程设计进行管理,用来确定和制定让产品达到顾客满意所需的步骤。
产品质量策划的目标是保证产品质量和提高产品可靠性,它一般可分为以下五个阶段:一阶段:计划和确定项目(项目阶段);第二阶段:产品设计开发验证(设计及样车试制);第三阶段:过程设计开发验证(试生产阶段);第四阶段:产品和过程的确认(量产阶段);第五阶段:反馈、评定及纠正措施(量产阶段后)。
2、 FEMA(失效模式及后果分析)FEMA体现了防错的思想,要求在设计阶段和过程设计阶段,对构成产品的子系统、零件及过程中的各个工序逐一进行分析,找出所有潜在的失效模式,并分析其可能的后果,从而预先采用必要的措施,以提高产品的质量和可靠性的一种系统化的活动。
FEMA从失效模式的严重度(S)、频度(O)、探测度(D)三方面分析,得出风险顺序数RPN=S×O×D,对RPN及严重度较高的失效模式采取必要的预防措施。
FMEA能够消除或减少潜在失效发生的机会,是汽车业界认可的最能减少“召回”事件的质量预防工具。
3、MSA(测量系统分析)MSA是使用数理统计和图表的方法对测量系统的分辨率和误差进行分析,以评估测量系统的分辨率和误差对于被测量的参数来说是否合适,并确定测量系统误差的主要组成的方法。
测量系统的误差对稳定条件下运行的测量系统,通过多次测量数据的统计特性的偏倚和方差来表征。
一般来说,测量系统的分辨率应为获得测量参数的过程变差的十分之一,测量系统的相关指标有:重复性、再现性、线性、偏倚和稳定性等。
4、PPAP(生产件批准程序)PPAP是指在产品批量生产前,提供样品及必要的资料给客户承认和批准,来确定是否已经正确理解了顾客的设计要求和规范。
FMEA培训课件(五大工具)
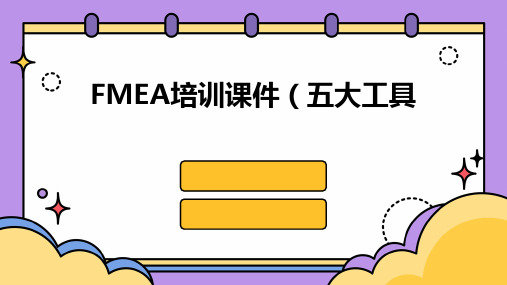
FMEDA不仅关注故障模式的影响,还特别强调对检测性的评估,以便更全面地了解潜在问题的影响以及在出现故障时能否及时发现并进行修复。
在FMEDA中,检测性的评估通常采用量化的方式进行,以便更准确地确定故障模式的可检测性。通过提高检测性,可以降低因未及时发现故障而导致的事故风险。
详细描述
在FMESi中,严重度评估通常采用量化的方式进行,以便更准确地确定故障模式对系统性能的影响程度。
总结词:故障模式、影响与风险优先数分析(FMERP)是一种综合性的质量工具,旨在识别、评估和解决潜在的故障模式及其对系统性能的影响。
总结词
故障模式、影响与检测性分析(FMEDA)是一种质量工具,用于评估潜在的故障模式及其对系统性能的影响以及检测的可能性。
详细描述
DFSS(Design for Six Sigma)是一种设计方法论,旨在提高产品的设计质量和可靠性。通过结合FMEA,可以对产品设计中的潜在失效模式进行分析和预防,从而提高产品的设计质量和可靠性。这种结合有助于在设计阶段就考虑产品的性能、可靠性和安全性,从而减少后期的改进成本和时间。
THANKS
总结词
电子产品行业对质量和可靠性要求极高,FMEA在此领域的应用同样广泛且重要。
在电子产品案例中,FMEA被用于分析电子产品的设计和生产过程。通过FMEA分析,可以发现潜在的故障模式,并采取相应的预防措施,提高产品的可靠性和稳定性。此外,FMEA还可以帮助企业优化产品设计,降低生产成本,提高市场竞争力。
FMEA培训课件(五大工具
FMEA基础介绍FMEA实施流程FMEA分析方法FMEA应用案例FMEA与其他工具的结合应用
五大工具第五版FMEA手册六步法与AP优先级表

一.五大工具之AIAG-VDA FMEA手册(很多场合被称第五版FMEA)六步法新版FMEA开发的方法进行了结构化的定义,即六步法。
六步法适用于所有FMEA的开发,如SFMEA/DFMEA/PFMEA,分为两大部分:步骤1-3为系统分析部分,主要是为FMEA分析做好前期准备;步骤4-6为失效分析和风险降低部分,主要是进行失效分析并进行改进活动。
步骤一:范围定义分析范围的主要工具为Boundary Diagram框图,主要目的是界定FMEA分析的边界,定义在 FMEA 中包含和排除的内容。
步骤二:结构分析结构分析的目的是可视化设计或过程元素之间的关系和相互作用。
AIAG-VDA在结构上至少需要3个层次:Higher Level 直接上一层级> Focus Level 聚焦分析层级> Lower Level直接下一层级。
结构分析的常用工具是结构树。
1. 对于 DFMEA,项目被扩展为系统、系统组件和零部件2. 对于 PFMEA,项目被扩展为过程、过程步骤和过程元素3. 添加过程工作元素标签4. 人、机器、间接材料、环境步骤三:功能分析功能分析的目的是识别功能与要求,并分配给系统结构元素,然后向下分配到下层级元素,进行功能分析时,需明确区分产品的基本功能、详细要求和设计约束条件和假设,可使用Function Worksheet功能分析表的工具进行,也可以使用P图及接口矩阵等工具进行功能分析。
1. 对于 DFMEA,功能/要求是系统功能的扩展功能,系统组件的要求或预期功能,以及组件元素的性能和功能,以及要求的预期输出或特性;2. 对于 PFMEA,功能/要求是焦点组件、功能过程步骤和工作功能的扩展功能。
步骤四:失效分析新版FMEA最有特色的地方是将失效影响FF、失效模式FM和失效起因FC的逻辑关系以“瀑布模型的方式”进行了有效的展示,即上一层级的失效模式即为下一层级的失效影响,而下一层的失效模式即为上一层级的失效起因,在进行失效分析时,需同时进行三个层级的分析,并在FMEA表中体现出三者的逻辑性。
五大工具手册APQP、PPAP、SPC、MSA、FMEA

五大工具手册APQP、PPAP、SPC、MSA、FMEA1.产品质量先期策划(APQP)、2.测量系统分析(MSA)、3.统计过程控制(SPC)、4.生产件批准(PPAP)5.潜在失效模式与后果分析(FMEA)一、APQP(Advanced Product Quality Planning)即产品质量先期策划,是一种结构化的方法,用来确定和制定确保某产品使顾客满意所需的步骤。
产品质量策划的目标是促进与所涉及的每一个人的联系,以确保所要求的步骤按时完成。
有效的产品质量策划依赖于公司高层管理者对努力达到使顾客满意这一宗旨的承诺。
产品质量策划有如下的益处:◆引导资源,使顾客满意;◆促进对所需更改的早期识别;◆避免晚期更改;◆以最低的成本及时提供优质产品二、PPAP:生产件批准程序(Production part approval process)ppap生产件提交保证书:主要有生产件尺寸检验报告,外观检验报告,功能检验报告,材料检验报告;外加一些零件控制方法和供应商控制方法;主要是制造形企业要求供应商在提交产品时做ppap文件及首件,只有当ppap文件全部合格后才能提交;当工程变更后还须提交报告。
ppap是对生产件的控制程序,也是对质量的一种管理方法。
三、SPC(Statistical Process Control)即统计过程控制,主要是指应用统计分析技术对生产过程进行适时监控,科学区分出生产过程中产品质量的随机波动与异常波动,从而对生产过程的异常趋势提出预警,以便生产管理人员及时采取措施,消除异常,恢复过程的稳定从而达到提高和控制质量的目的。
SPC非常适用于重复性的生产过程,它能够帮助组织对过程作出可靠的评估,确定过程的统计控制界限判断过程是否失控和过程是否有能力;为过程提供一个早期报警系统,及时监控过程的情况,以防止废品的产生,减少对常规检验的依赖性,定时以观察以及系统的测量方法替代大量检测和验证工作。
- 1、下载文档前请自行甄别文档内容的完整性,平台不提供额外的编辑、内容补充、找答案等附加服务。
- 2、"仅部分预览"的文档,不可在线预览部分如存在完整性等问题,可反馈申请退款(可完整预览的文档不适用该条件!)。
- 3、如文档侵犯您的权益,请联系客服反馈,我们会尽快为您处理(人工客服工作时间:9:00-18:30)。
研究失效,首先要得到失效的真实状况, 比如失效出现的部位,发生的时间、失效模式、 失效原因、失效产生的影响、失效改正方法、 修复方式及修复成本等。
19
一、基本概念 (续)
失效原因就是引起失效的物性、化性 原因,也就是引起失效模式的原因,例如:
失效模式:A断裂 失效原因:B穿晶断裂、沿晶断裂、脆 性断裂、韧性断裂
a)造成人员伤亡 b)造成设备和环境的损失 c)造成直接和间接的损失 失效等级的划分,因产品种类与企业政策、国 家法令之不同,而有不同的划分方法,常用的划分 方法如下 :
17
一、基本概念 (续)
常用的失效等级划分
失效等级
Ⅰ级 并(或)
Ⅱ级 失,不造
Ⅲ级 均无显著
Ⅳ级
严重程度
能导致系统功能失效,造成系统或环境重大损失, 导致人员伤亡。
能导致系统功能失效,造成系统或环境的重大损 成人员伤亡。
能导致系统功能下降,对系统或周围环境或人员 损害。
能导致系统功能下降,对系统、环境、人员无害。
18
一、基本概念 (续)
8.失效的判定
不同的产品,不同的使用状况,不同的 失效模式,失效的判定很难统一规定。例如: 齿轮出现蚀点,对精密仪器而言即为失效, 但对重型机械,则不算失效,除非腐蚀到一 定的程度。
6
一、基本概念
1.FMEA的定义与目的: a)对产品进行分析,找出零组件潜在之失效 模式,鉴定出它的失效原因,研究该项失效 模式对系统会产生什么的影响,采取对策预 防。
7
一、基本概念
b)失效分析在找出零组件或系统的潜在弱 点,提供设计、制造、品保等单位采取 可行之对策
8
一、基本概念 (续)
⒉.FMEA的类型 DFMEA 设计失效模式与效应分析 PFMEA 过程失效模式与效应分析 SFMEA 服务失效模式与效应分析 AFMEA 应用失效模式与效应分析 PFMEA 采购失效模式与效应分析 SFMEA 子系统失效模式与效应分析 MFMEA 机器失效模式与效应分析
3
失效模式及後果分析
根據經驗分析
產品設計與生產工藝中存在的弱點和可能產 生的缺陷 這些缺陷產生的後果與風險
決策過程中採取措施加以消除、並幫助 消除潛在隱患;事前花些時間地進行 FMEA,便可減輕事後修改的危機
4
FMEA潛在失效模式及後果分析
兩種FMEAs
設計FMEA:
由設計工程師/小組在設計初期採用的一種分析 技術,以系統、子系統或另件為分析對象 用來在最大範圍內保證已充分地考慮到相關的系 統、子系統和另部件和列出各種潛在的失效模式 及其相關的起因,並評估其對最後的產品影響
不影响产品安全,造成性能下降,但一般不会导致主要总成及零 部件损坏,并可用简易工具和备件在短时间内(30min)修复。
一般不会导致性能下降,不需要更换零件,用简易工具在短时间 (5min)内能轻易排除。
ห้องสมุดไป่ตู้16
一、基本概念 (续)
7.失效的等级划分
进行失效定性与定量分析时,要区分失效的危 害程度,因此要把失效划分等级,划分的原则是:
13
一、基本概念 (续)
典型的失效链:
路面不平
水箱支架断裂
(不是内在原
因是环境条件) 水箱后倾
…… 根源模式
产生异响 (伴生模式)
水箱与风扇皮带碰 水箱水管断
中间模式
水箱水泄漏
发动机损坏
冷却系过热
最终模式
停车
14
一、基本概念 (续)
支架断,因强度不足,为失效的根本原因 不要把环境条件列入失效原因,FMEA要找内在原因 中间模式:上一个模式是下一个模式的原因 失效链若能及时采取措施,可在中间截断
5
FMEA潛在失效模式及後果分析
兩種FMEAs
過程FMEA:
由製造工程師/小組採用的一種分析技術,以加 工工藝過程的每道工序為分析對象 用來在最大範圍內保證已充分地考慮到工藝過程 設計和列出各種潛在的失效模式及其相關的起因, 並評估其對最後的產品影響 它並不依靠改變產品設計來克服過程缺陷,是要 考慮製造
1
甚麼是潛在失效模式及後果分析?
F -- Failure (潛在失效) M -- Mode (模式) E -- Effects (後果) A -- Analysis (分析)
2
潛在失效模式及後果分析的發展
20世紀50年代,美國格魯曼公司開發了FMEA, 用於飛機制造業的發動機故障防範,取得很好 的成果 類似形式的分析方法,在六十年代中期航天工 業首次應用 - 美國航空及太空總署(NASA) 實施阿波羅登月計劃,在合約中明確要求實施 FMEA FMEA現已被廣泛用于飛機製造、汽車製造等多 個領域
20
潛在失效模式及後果分析
1. FMEA編號- 填入FMEA文件編號,以便查詢 2. 項目名稱 - 分析的系統、子系統或另件的過程名稱
15
一、基本概念 (续)
6.失效的分类
失效的分类应根据失效原因、危害程度、失效 程度与产生的频率加以分类,一般的分类原则如下:
失效类别 1 致命失效 2 严重失效 3 一般失效
4 轻微失效
分类原则 危及产品安全,可能导致人身伤亡,或引起重要总成报废,造成 重大经济损失或对周围环境造成重大危害。 影响产品安全,可能导致主要总成、零部件损坏或性能显著下降 且不能用简易工具和备件在短时间(约30min)内修复。
预 失效是指:
a)在规定条件下(环境、操作、时间)不能完成既定
期 功能。
功
能
11
一、基本概念 (续)
b)在规定条件下,产品参数值不能维持在规 定的上下限之间。 c)产品在工作范围内,导致零组件的破裂、 断裂、卡死等损坏现象。
12
一、基本概念 (续)
5.失效链的定义与例子
定义:一个失效事件发生,若没有采取或不及时 采取或事实上不可能采取的措施, 而引起下游 系统或相关系统失效的现象。 例子:由于有了失效链的概念就有了根源失效模 式、伴生模式、中间式及最终模式的失效。故制 作DFMEA、PFMEA 时要运用失效链的思想。
9
一、基本概念 (续)
⒊FMEA与FTA FMEA是具有质量分析的事先分析工
具,自下而上分析 FTA是事后的失效模式分析,即失
效树自上而下分析 类似的产品的FTA是其FMEA的重要
输入
10
一、基本概念 (续)
⒋失效的定义 在失效分析中,首先要明确产品的失效是什么,否 则产品的数据分析和可靠度评估结果将不一样,一般而言,