金属切削过程及其控制
第一章 金属切削过程及其控制(第一节)

轨迹法:利用切削运动中刀尖的运动轨迹形成被加工表面的形状。
轨迹法形成发生线需要一个独立的成形运动。
第一章 金属切削过程及其控制
第一节 金属切削过程的基本知识 发生线的形成方法——轨迹法
轨迹法:利用切削运动中刀尖的运动轨迹形成被加工表面的形状。
刀具切削刃与工件表面之间为点接触,通过刀具与工件之 间的相对运动,由刀具刀尖的运动轨迹来实现表面的成形。 被加工表面的形状精度主要取决于机床切削运动的精度。 刀尖轨迹法是利用非成形刀具,在一定的切削运动下,由刀尖 轨迹获得零件所需表面的方法。
第一章 金属切削过程及其控制
1.2 加工表面和切削用量三要素 一、基本概念
(二)切削层及切削用量三要素——切削层 切削层是指在切削过程中,刀具的切削刃一次走刀所切
除的工件材料层。切削层的截面尺寸参数称为切削层参数。
切削层形状、尺寸直接影响着切削过程的变形、刀具承 受的负荷以及刀具的磨损。
第一章 金属切削过程及其控制
为:简单成形运动和复合成形运动。
简单成形运动:如果一个独立的成形运动,是由单独的旋转运
动或直线运动构成的,则此成形运动称为简单成形运动。
一般以主轴的旋转,刀架或工作台的直线运动的形式出现,
用A表示直线运动,用B表示旋转运动。
第一章 金属切削过程及其控制
第一节 金属切削过程的基本知识 表面成形运动
的,也可以是断续进行的,可以由工件完成,也可以由刀具完成,可
以是简单运动,也可以是复合运动。
第一章 金属切削过程及其控制 (一)切削成形运动与加工表面 按作用来分,切削运动可分为主运动和进给运动。 主运动:提供切削可能性的运 动。(速度最高,动力消耗最 大,有且只有一个) 进给运动:提供继续切削可能 性的运动。(速度低,有一个 或几个)
金属切削过程及控制

3.1 切削过程与切屑类型
切削变形实验设备与录像装置
安徽工程大学
教案九
3.1 切削过程与切屑类型
直角切削
没有副刃参加切削,且λs = 0°。
a)直角切削
b)斜角切削
c)不自由切削
直角、斜角自由切削与不自由切削
安徽工程大学
教案九
3.1 切削过程与切屑类型
切屑 M 终滑移线
一、切屑成形过程及切削变形区的划分
安徽工程大学
教案九
3.1 切削过程与切屑类型
晶粒滑移示意图
安徽工程大学
教案九
3.1 切削过程与切屑类型
二、变形程度的表示方法
——变形系数Λh ◆ 厚度变形系数
hch cos( ) h hD sin
Lch LD
切屑与切削层尺寸
◆ 长度变形系数
LD L Lch
变形系数Ah的计算
二、刀具磨损过程及磨钝标准 1、刀具磨损过程
后刀面磨损量VB 初期磨损 正常磨损 急剧磨损
切削时间 刀具磨损过程
安徽工程大学
3.4 刀具的磨损和刀具耐用度
2、磨钝标准
安徽工程大学
3.4 刀具的磨损和刀具耐用度 三、刀具耐用度及其经验公式
1、刀具寿命(耐用度)概念
◆ 刀具从切削开始至磨磨损量达到钝标准的切削时间, 用T 表示。 ◆ 刀具总寿命 —— 一把新刀从投入切削开始至报废为止 的总切削时间,其间包括多次重磨。
安徽工程大学
教案十
3.1 切削过程与切屑类型
影响切削变形的因素
1、切削厚度 2、刀具角度 3、切削速度
安徽工程大学
教案十
3.1 切削过程与切屑类型
三、积屑瘤的形成及其对切削过程的影响
《机械制造技术》切削过程及其控制
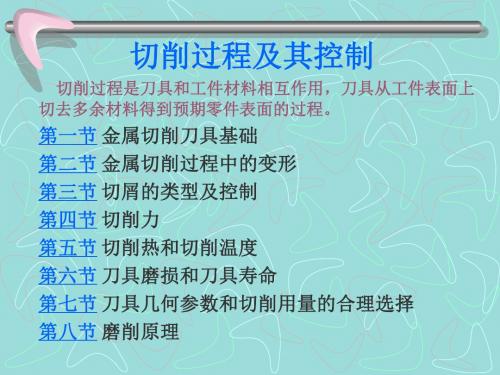
氮化硅( Si3 N4)基陶瓷,具有较高的抗弯性和
韧性 。
立方氮化硼(CBN)是一种新型刀具材料;
立方氮化硼是由六方氮化硼经高温高压处理转化 而成,硬度到达8000HV,仅次于金刚石;
立方氮化硼的化学稳定性好,高温下不与铁产生 化学反应;
硬质合金是用高硬度、难熔的金属化合物和金属 粘结剂在高温条件下烧结而成的粉末冶金制品;
硬质合金的常温硬度达89~93HRA,在高温800~ 1000°C还能进行切削,刀具寿命比高速钢高几 倍至几十倍;
硬质合金的强度和韧性差,常温下冲击韧性是高 速钢1/8~1/30,承受切削振动和冲击的能力较差;
值,刀尖为最低点时刃倾角为负值;主切削 刃与基面平行时,刃倾角为零。
外圆车刀的上述六个标注角度是独立的,它 们的大小会之间影响切削过程。
刀具角度标注图
Po-Po
P´o - P´o
' o
Ps
Po
r
vf
o P´o o
o
r
' r
P´o
Po
Ps向
s
横向进给运动对工作角度的影响:
切削平面的夹角; 副正交平面为垂直于副切削刃在基面上投影的
平面。
主偏角 k r :在基面内测量的主切削刃在基面
上的投影与进给运动方向的夹角。
副偏角
k
' r
:在基面内测量的副切削刃在基
面上的投影与进给运动反方向的夹角。
刃倾角 s:在切削平面内测量的主切削刃与
基面之间的夹角; 在主切削刃上,刀尖为最高点时刃倾角为正
金属切削过程及控制

1. 第一变形区
塑性变形从始滑移面OA开始至终滑移面OM终了,之间 形成AOM塑性变形区,由于塑性变形的主要特点是晶格间 的剪切滑移,所以AOM叫剪切区,也称为第一变形区 (Ⅰ)。
图3-2 金属切削过程中的滑移线和流线示意图
2. 第二变形区
切屑沿刀具前面排出时会进一步受到前刀 面的阻碍,在刀具和切屑界面之间存在强烈的 挤压和摩擦,使切屑底部靠近前刀面处的金属 发生“纤维化”的二次变形。这部分区域称为 第二变形区(Ⅱ)。
图3-18
切削力的来源
2.切削力的分解
切削力Fz(Fc)
通常将合力F分解 为相互垂直的三个分 力:切削力 Fc 、进 给力 Ff 、背向力 Fp (图3-19)。 (旧称主切削力,用Fz表 示)——总切削力在主运动 方向的分力,是计算机床切 削功率、选配机床电机、校 核机床主轴、设计机床部件 及计算刀具强度等必不可少 的参数。
图3-8 作用在切屑上的力
a) 切屑受到来自工件和刀具的作用力
b) 切屑作为隔离体的受力分析
2. 前刀面上的摩擦
在粘结区,切屑的底层与前面呈现冷焊状态,切屑与前面之间不是一般的外
摩擦,这时切屑底层的流速要比上层缓慢得多,从而在切屑底部形成一个滞流 层。 所谓“内摩擦”就是指滞流层与上层流屑层内部之间的摩擦,这种内摩擦也 就是金属内部的剪切滑移。其摩擦力的大小与材料的流动应力特性及粘结面积 的大小有关。 切屑离开粘结区后进入滑动区。在该区域内刀屑间的摩擦仅为外摩擦。 刀屑接触面间有二个摩擦区域:粘结(内摩擦)区和滑动(外摩擦)区。 金属的内摩擦力要比外摩擦力大得多,因此,应着重考虑内摩擦。
图3-19 切削力的分解
3.切削功率
计算切削功率
Pc是用于核算加工成本和计算能量消
第三章 金属切削过程及其控制(1-4)
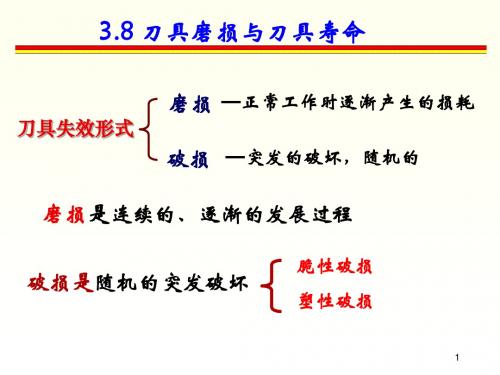
39
1. 调整化学成分
如在钢中加入少量的硫、硒、铅、铜、磷等,虽略降低钢的强
度,但同时降低钢的塑性,对加工性有利。
2. 材料加工前进行合适的热处理
低碳钢通过正火处理后,细化晶粒、硬度提高、塑性降低, 有利于减小刀具的黏结磨损,减小积屑瘤,改善工件表面粗糙 度; 高碳钢球化退火后,硬度下降,可减小刀具磨损; 不锈钢以调质到HRC28为宜,硬度过低,塑性大,工件表面 粗糙度差,硬度高则刀具易磨损;
16
(3)自动化生产标准
自动化生产中的精加 工刀具,则常以沿工件
径向的刀具磨损尺寸作
为刀具的磨钝标准,称
为径向磨损量NB。
17
刀具磨钝标准选取原则:
1)工艺系统刚性差, VB取小些;反之,取大些。 2)难加工材料, VB取小些。(防止温度升高)
3)加工精度高, VB取小些。 4)大型工件, VB取大些(防中途换刀)。
21
制订刀具耐用度时,应具体考虑的问题: ① 刀具构造复杂、制造和磨刀费用高时,刀具耐用度 应规定得高些。 ② 多刀车床上的车刀,组合机床上的钻头、丝锥和铣 刀,自动机床及自动线上的刀具,因为调整复杂,刀具 耐用度应规定得高些。 ③ 某工序的生产成为生产线上的瓶颈时,刀具耐用度 应定得低些。某工序单位时间的生产成本较高时刀具耐 用度应规定得低些。 ④ 精加工大型工件时,刀具耐用度应规定得高些,至 少保证在一次走刀中不换刀。
1
2
3
易切削钢
较易 切削钢 一般钢、 铸铁 稍难切削 材料 较难切削 材料 难切削 材料 很难切削 材料
2.5~3
1.6~ 2.5 1.0~ 1.6 0.65~ 1.0 0.5~ 0.65 0.15~ 0.5 <0.15
金属切削过程分析与控制
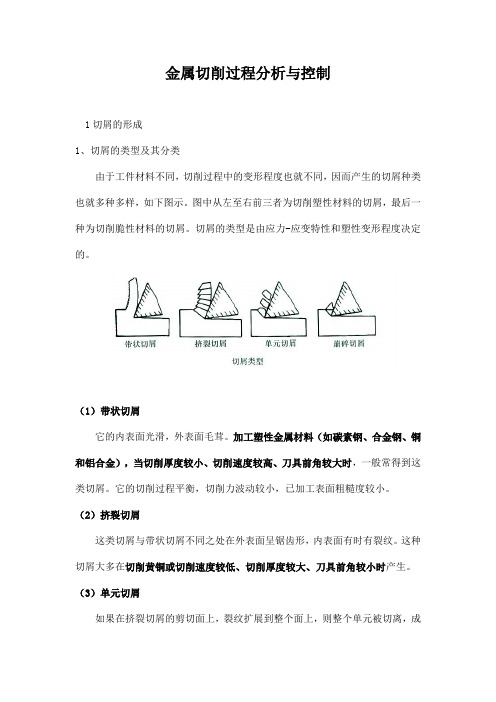
金属切削过程分析与控制1切屑的形成1、切屑的类型及其分类由于工件材料不同,切削过程中的变形程度也就不同,因而产生的切屑种类也就多种多样,如下图示。
图中从左至右前三者为切削塑性材料的切屑,最后一种为切削脆性材料的切屑。
切屑的类型是由应力-应变特性和塑性变形程度决定的。
(1)带状切屑它的内表面光滑,外表面毛茸。
加工塑性金属材料(如碳素钢、合金钢、铜和铝合金),当切削厚度较小、切削速度较高、刀具前角较大时,一般常得到这类切屑。
它的切削过程平衡,切削力波动较小,已加工表面粗糙度较小。
(2)挤裂切屑这类切屑与带状切屑不同之处在外表面呈锯齿形,内表面有时有裂纹。
这种切屑大多在切削黄铜或切削速度较低、切削厚度较大、刀具前角较小时产生。
(3)单元切屑如果在挤裂切屑的剪切面上,裂纹扩展到整个面上,则整个单元被切离,成为梯形的单元切屑,如图c所示。
切削铅或用很低的速度切削钢时可得到这类切屑。
以上三种切屑只有在加工塑性材料时才可能得到。
其中,带状切屑的切削过程最平稳,单元切屑的切削力波动最大。
在生产中最常见的是带状切屑,有时得到挤裂切屑,单元切屑则很少见。
假如改变挤裂切屑的条件,如进一步减小刀具前角,减低切削速度,或加大切削厚度,就可以得到单元切屑。
反之,则可以得到带状切屑。
这说明切屑的形态是可以随切削条件而转化的。
掌握了它的变化规律,就可以控制切屑的变形、形态和尺寸,以达到卷屑和断屑的目的。
如果在挤裂切屑的剪切面上,裂纹扩展到整个面上,则整个单元被切离,成为梯形的单元切屑,如图c所示。
切削铅或用很低的速度切削钢时可得到这类切屑。
以上三种切屑只有在加工塑性材料时才可能得到。
其中,带状切屑的切削过程最平稳,单元切屑的切削力波动最大。
在生产中最常见的是带状切屑,有时得到挤裂切屑,单元切屑则很少见。
假如改变挤裂切屑的条件,如进一步减小刀具前角,减低切削速度,或加大切削厚度,就可以得到单元切屑。
反之,则可以得到带状切屑。
这说明切屑的形态是可以随切削条件而转化的。
第二章-金属切削过程及其控制

2.3 金属切削用的刀具
-磨料与磨具
系列
氧化物系
碳化物系
磨料名 称
棕刚玉
代号
A
白刚玉
WA
黑碳化硅 C
绿碳化硅 GC
高硬磨料系 人造金刚石 D
立方氮化硼 CBN
显微硬度 特性
刀具与工件之间的相对运动,即表面成形运动,分为 主运动和进给运动。
主运动: 使工件与刀具产生相对运动以进行切削的最基本运动。
主运动速度最高,消耗功率最大,且只有一个 。 进给运动:
不断把被切削层材料投入到切削过程中,以便形成全 部已加工表面的运动。
2.2 金属切削加工的基本概念
加工表面:
2.2 金属切削加工的基本概念
J
强度最高,型面保持性好,磨耗少, 自锐性差
适用于金刚石砂轮
2.3 金属切削用的刀具
-磨料与磨具
硬度 磨粒在磨削力作用下,从砂轮表面上脱落的难易程度。
软中硬
大级名称 超软
软
中软
中
中硬
硬
超硬
小级名称 超软
123 1 2 1 2 123 1 2
超硬
代号 D E F G H J K L M N P Q R S T
副切削刃
前刀面
刀体
刀头 副后刀面
刀尖
主切削刃 主后刀面
2.3 金属切削用的刀具
-确定刀具角度的参考平面
正交平面参考系: 基面 切削平面 正交平面
基面
切削平面 正交平面
2.3 金属切削用的刀具
-刀具标注角度
金属切削过程及其控制概要
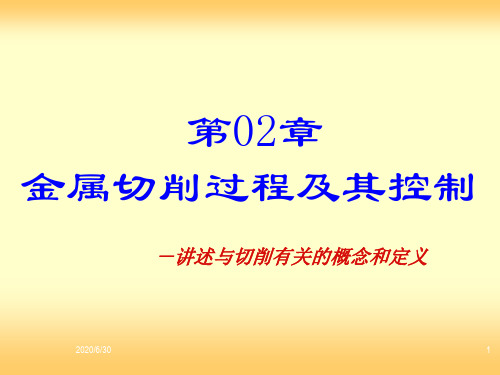
母线:渐开线—展成法
• 滚刀的旋转B11 • 工件的旋转B12
导线:直线—相切法
• 滚刀的上下 进给运动A2
例2.4 用螺纹车刀加工锥螺纹
锥形螺纹面
母线:螺纹轮廓线
• 不需要成形运动
导线:圆锥螺旋线—轨迹 法
• 工件的旋转运动B11 • 刀具纵向直线运动A12 • 刀具横向直线运动A13
4 表面成形运动
切削速度vc:切削刃上选定点相对工件沿主运动方向的瞬时
速度;
vc
dn
1000
(m
/
s或m /
min)
vc
2Lnr 1000
(m / min)
进给运动
进给运动:配合主运动依次或连续不断地切除多余 材料,同时形成一定要求的已加工表面;
特点:一个或多个 间歇或连续
• 如:外圆车削时车刀的连续纵向直线运动 • 刨削时工件的间歇直线运动
2 刀具标注角度参考系
主剖面参考系:Pr、Ps、正交平面Po
正交平面Po:过主切削刃上选定点垂直于切削平面和基面的平面;
法剖面参考系: Pr、Ps、法平面Pn
法平面Pn:过主切削刃上选定点并垂直于主切削刃或其切线的平面
进给、切深剖面参考系: Pr、进给剖面Pf 、切深剖面Pp
进给剖面Pf:过主切削刃上选定点平行于进给方向q且垂直于基面的 平面 切深剖面Pp:过主切削刃上选定点垂直于进给方向且垂直于基面的 平面
基面Pr内测量的角度
• 主偏角κr —主切削刃在基面上的投影与进给运动方向的夹角; • 副偏角κr´—副切削刃在基面上的投影与进给运动反方向的夹角
; • 刀尖角ε r —主切削刃与副切削刃在基面上投影的夹角;
ε r = 180°-(κr + κ'r )
- 1、下载文档前请自行甄别文档内容的完整性,平台不提供额外的编辑、内容补充、找答案等附加服务。
- 2、"仅部分预览"的文档,不可在线预览部分如存在完整性等问题,可反馈申请退款(可完整预览的文档不适用该条件!)。
- 3、如文档侵犯您的权益,请联系客服反馈,我们会尽快为您处理(人工客服工作时间:9:00-18:30)。
切削 速度
同YT15 进给 量
碳素钢、合金钢的粗加工,也可以用于断续切削
硬度 抗弯 高温合金、高锰钢、不锈钢等难加工材料及普通钢料、铸铁、
YW2 、 强度 有色金属及其合金的半精加工和精加工
耐磨 、
YW1
性、 切削
韧性 、
高温合金、高锰钢、不锈钢等难加工材料及普通钢料、铸铁、
进给 有色金属及其合金的粗加工和半精加工
TiC含量↑→耐磨性↑ 抗弯强度↓ 、韧性↓。
用途:高速切削结构钢和合金钢等塑性材料。
➢常用硬质合金的牌号及其应用范围
牌号
应用范围
YT30 YT15
硬度 、
耐磨 性、
抗弯 强度 、 韧性
碳素钢、合金钢的精加工
碳素钢、合金钢在连续切削时的粗加工、半精加工,亦可用于断 续切削时的精加工
YT14 YT5
6)良好的工艺性和经济性
刀具材料应具有好的锻造性能、热处理性能、焊接性 能、磨削加工性能等。而且要追求高的性能价格比。
切削速度(m/min)
2000 1000
500
200 100
50 碳素工具钢
20
聚晶金刚石 (PCD) 陶瓷
TiAlN涂层 硬质合金 涂层硬质合金
WC-TiC系硬质合金
WC系硬质合金
精品课件
5
2.高速钢
高速钢是一种加入了较多的钨、钼、铬、钒等 合金元素的高合金工具钢。
➢ 特点:
1)强度高(抗弯强度为硬质合金的2~3倍,陶瓷的5~6倍);
2)韧性高(比硬质合金高几十倍);
3)具有一定的硬度(HRC63~70),且有较好的耐 磨性;
4)且有较好的耐热性(500℃~600℃);
5)可加工性好,热处理变形较小。
韧性 普通铸铁、冷硬铸铁、高温合金的连续切削时的精加工、间断切 、 削时的半精加工
进给 铸铁、有色金属及其合金的半精加工和粗加工 量
铸铁、有色金属及合金、非金属材料粗加工,也可用于断续切削
②钨钛钴类硬质合金 P( YT )类(WC+TiC
+Co)
牌号: YT5、YT14、YT15、YT30 特点:耐磨性、耐热性好,强度、韧性较差。
➢适合在钻头、丝锥、成形铣刀和切齿刀具上 应用。
精品课件
11
常用高速钢牌号及其应用范围
类别
牌号
主要用途
普通 高速钢
W18Cr4V
广泛用于制造加工一般钢材和铸铁的钻头、 铰、铣刀、拉刀、丝锥、齿轮刀具等整体刀 具。切削速度低。
W6Mo5Cr4V2
用于制造要求热塑性好和受较大冲击载荷的 刀具,如轧制钻头等,用于加工奥氏体不锈 钢、高温合金、钛合金。
精品课件
26
(3)金刚石烧结体
在硬质合金基体上烧结一层约0.5mm厚的聚晶金 刚石。
➢特点:强度较好,能进行断续切削,可多次刃磨。
主要用于有色金属的高速精细切削。
金刚石不是碳的稳定状态,遇热易氧化和石墨化, 用金刚石刀具进行切削时须对切削区进行强制冷却。
金刚石刀具不宜加工铁族元素,因为金刚石中的碳 原子和铁族元素的亲和力强,刀具寿命低。
粉末冶金高速钢 适用于制造精密刀具、大 尺寸(滚刀、插齿刀)刀具、复杂成形刀具、拉刀 等。
牌号
W18Cr4V2 W6Mo5Cr4V2 W6Mo5Cr4VCo8 W6Mo5Cr4V2Al
(表3—2)常用高速钢的力学性能
常温硬 度/HRC
抗弯强 度/GPa
冲击韧 性/ MJ/ m2
63~66 63~66 66~68 67~69
陶瓷 基
Si3N4
√
√
基
金刚石
超硬 材料
立方氮 化硼
√
√
√
√
√
√
√
应当指出,加工一般材料大量使用 的仍是普通高速钢及硬质合金,只有在 加工难加工材料时,才考虑选用新牌号 合金或高性能高速钢,在加工高硬度材 料或精密加工时,才考虑选用超硬材料。
精品课件
27
刀具材料
常用刀具材料可切削的主要工件材料
结构钢 合金钢 铸铁
镍基高
铜铝等
淬硬钢 冷硬铸 温合金 钛合金 有色合 非金属
铁
钢
金
高速钢
√
√
√
√
√
√
√
硬
K类
√
质 合
(YG) P类 (YT)
√
√
金 M类
√
√
√
(YW)
涂层硬质合金 √
√
√
√
√
√
√
√
√
√
√
Ti(N) 基硬质 √
√
√
合金
√
√
√
√
Al2O3
牌号: YN05、YN10 特点:高硬度、高耐磨性、高耐热性和抗氧化性,
但强度和韧性降低。
用途:高速精加工钢材。
4. 涂层刀具材料
在韧牲较好的刀具基体上,涂覆一层 耐磨性好的难熔金属化合物,既能提高刀具材 料的耐磨性,又不降低其韧性。
涂层方法:化学气相沉积法(CVD法,1000℃)和
物理气相沉积法(PVD法,500℃)。
1) 高的硬度
常温硬度HRC60以上。刀具硬度>工件的硬度
2)高的耐磨性 → 保证刀具的尺寸精度↑
3)足够的强度与韧性
能承受切削力、冲击和振动,防止刀具脆性断裂和 崩刀。
精品课件
2
4)高的耐热性(热稳定性)
在高温下保持: 硬度、耐磨性、强度、韧性、化学稳定性。
5)良好的热物理性能和耐热冲击性能
刀具材料的导热性要好,不会因受到大的热冲击,产 生刀具内部裂纹而导致刀具断裂。
聚晶立方 氮化硼
(PCBN) DLC涂层 硬质合金
TiC-TiN金属陶瓷
高速钢
合金工具钢
10
1800
1850
1900
1950
2000 年代
刀具材料的发展与切削加工高速化的关系
精品课件
4
常用刀具材料
工具钢(包括碳素工具钢、合金工具钢和高速钢) 硬质合金、 陶瓷、 金刚石(天然和人造) 立方氮化硼等。 碳素工具钢和合金工具钢,因其耐热性很差,目 前仅用于手工工具。
精品课件
21
用途: 适用于高速精细加工硬材料,新型的陶瓷刀具也 能半精、粗加工多种难加工材料。
与传统硬质合金相比,有下列优点:
①可加工硬度高达65HRC的高硬度难加工; ②可进行扒荒粗车及铣、刨等大冲击间断切削; ③刀具寿命可提高几倍至几十倍; ④切削效率提高3~10倍,可实现以车铣代磨。
精品课件
主要用于非铁材料及非金属的精密加工。 ➢特点:单晶金刚石结晶界面有一定的方向,不同晶面上硬度 与耐磨性有较大的差异,刃磨时须注意选择刃磨平面。 (2)人造聚晶金刚石 (PCD) 人造金刚石是通过合金触媒的作用,在高温高压下由石墨转化 而成。 ➢特点:人造聚晶金刚石抗冲击强度高,可选用较大的切削用 量。结晶面无固定方向,可自由刃磨。
3~3.4 3.5~4 3.0 2.9~3.9
0.18~0.32 0.3~0.4 0.3 0.23~0.3
高温硬度
/HRC
500 °C
600 °C
56 55~56 --60
48.5
47~48
54 55
涂层高速钢。是采用物理气相沉积(PVD)
方法,刀具表面生成TiN,其厚度一般为2~ 8m。 ➢特点:切削力、切削温度约下降25%,切削 速度、进给量和刀具寿命显著提高。
2)高温合金、热喷涂材料、硬质合金及其它难加工
材料的高速切削。
精品课件
23
聚晶立方氮化硼 (PCBN)
聚晶立方氮化硼(PCBN)是由CBN作为主要成分 与结合剂在高温高压下烧结而成的聚晶体,结合 剂主要有金属型(以CO、Ni为代表)或陶瓷型(以 TiC、TiN、Al2O3为代表)。
特点:
1. 具有较高的硬度和耐磨性
Co含量↑→抗弯强度↑、韧性↑、耐磨性↓。
用途:加工铸铁和有色金属等脆性材料。
精品课件
14
➢常用硬质合金的牌号及其应用范围
牌号
应用范围
YG3X 硬度 、
YG3 耐磨 性、
YG6X 切削 速度
YG6
YG8
抗弯 铸铁、有色金属及其合金和合金淬火钢高速精加工 强度 、 铸铁、有色金属及其合金精加工、半精加工,不能承受冲击载荷
高硬度(HRA89~93相当于HRC 74~82);
高耐磨性,高耐热性(850~1000℃),切削速度 可达100~300m/min;
抗弯强度低和抗冲击振动性能差,很少用于制造 整体刀具。
精品课件
13
分类
①钨钴类硬质合金 K( YG )类(WC+Co) 牌号:YG8、YG6、YG6X 、YG3、YG3X 特点: 强度、韧性好,耐磨性、耐热性稍差。
速度 量
精品课件
17
③钨钛钽(铌)类硬质合金 M ( YW )类(WC+
TiC+TaC(碳化钽)(NbC(碳化铌))+Co)
牌号: YW1 (M10)、YW2 (M20)
特点:强度、韧性↑,耐热性↑,耐磨性↑。
用途:即可加工铸铁和有色金属,又可加工钢材及高
温合金和不锈钢等难加工材料。
④镍钼钛类硬质合金YN类(TiC+Ni+Mo)
精品课件
6
➢ 应用:
常用于制造各种复杂刀 具(如钻头、丝锥、拉 刀、成型刀具、齿轮刀 具等)。
➢分类
按用途可分为: 通用高速钢和高性能高速钢。
按制造工艺可分为: 熔炼高速钢、粉末冶金高速 钢和表面涂层高速钢。
通用型高速钢(含碳量0.7~0.9%,62~66 HRC) ✓钨系高速钢 W18Cr4V