精益思想(Lean Thinking)与五项原则(Five Principles)
精益工作推进的核心理念
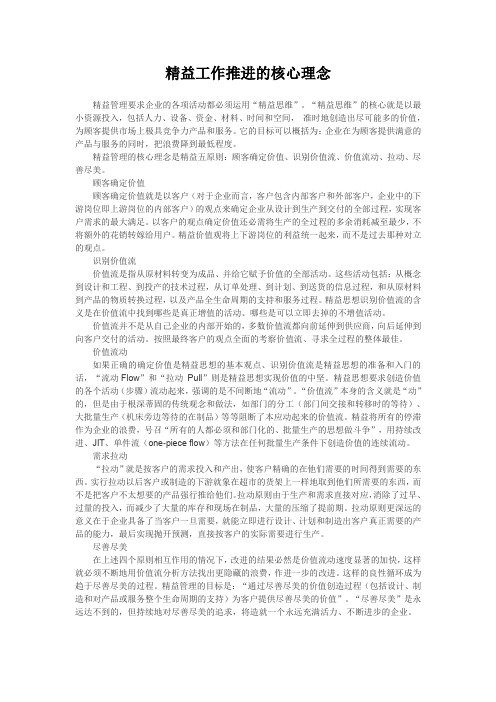
精益工作推进的核心理念精益管理要求企业的各项活动都必须运用“精益思维”。
“精益思维”的核心就是以最小资源投入,包括人力、设备、资金、材料、时间和空间,准时地创造出尽可能多的价值,为顾客提供市场上极具竞争力产品和服务。
它的目标可以概括为:企业在为顾客提供满意的产品与服务的同时,把浪费降到最低程度。
精益管理的核心理念是精益五原则:顾客确定价值、识别价值流、价值流动、拉动、尽善尽美。
顾客确定价值顾客确定价值就是以客户(对于企业而言,客户包含内部客户和外部客户,企业中的下游岗位即上游岗位的内部客户)的观点来确定企业从设计到生产到交付的全部过程,实现客户需求的最大满足。
以客户的观点确定价值还必需将生产的全过程的多余消耗减至最少,不将额外的花销转嫁给用户。
精益价值观将上下游岗位的利益统一起来,而不是过去那种对立的观点。
识别价值流价值流是指从原材料转变为成品、并给它赋予价值的全部活动。
这些活动包括:从概念到设计和工程、到投产的技术过程,从订单处理、到计划、到送货的信息过程,和从原材料到产品的物质转换过程,以及产品全生命周期的支持和服务过程。
精益思想识别价值流的含义是在价值流中找到哪些是真正增值的活动、哪些是可以立即去掉的不增值活动。
价值流并不是从自己企业的内部开始的,多数价值流都向前延伸到供应商,向后延伸到向客户交付的活动。
按照最终客户的观点全面的考察价值流、寻求全过程的整体最佳。
价值流动如果正确的确定价值是精益思想的基本观点、识别价值流是精益思想的准备和入门的话,“流动Flow”和“拉动Pull”则是精益思想实现价值的中坚。
精益思想要求创造价值的各个活动(步骤)流动起来,强调的是不间断地“流动”。
“价值流”本身的含义就是“动”的,但是由于根深蒂固的传统观念和做法,如部门的分工(部门间交接和转移时的等待)、大批量生产(机床旁边等待的在制品)等等阻断了本应动起来的价值流。
精益将所有的停滞作为企业的浪费,号召“所有的人都必须和部门化的、批量生产的思想做斗争”,用持续改进、JIT、单件流(one-piece flow)等方法在任何批量生产条件下创造价值的连续流动。
精益生产的五大原则是什么
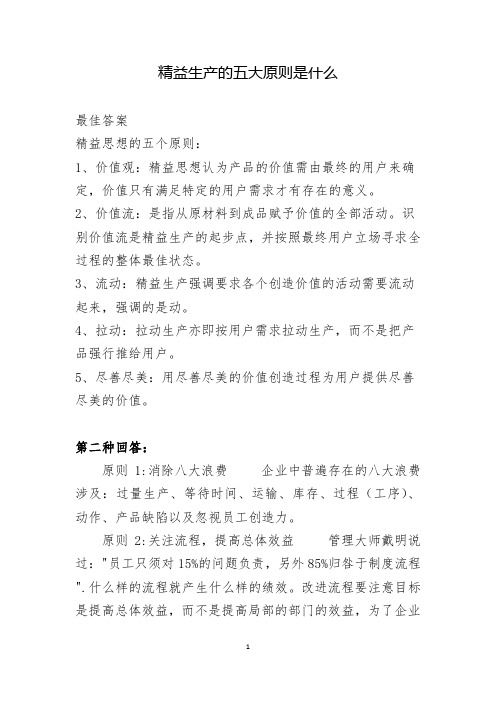
精益生产的五大原则是什么最佳答案精益思想的五个原则:1、价值观:精益思想认为产品的价值需由最终的用户来确定,价值只有满足特定的用户需求才有存在的意义。
2、价值流:是指从原材料到成品赋予价值的全部活动。
识别价值流是精益生产的起步点,并按照最终用户立场寻求全过程的整体最佳状态。
3、流动:精益生产强调要求各个创造价值的活动需要流动起来,强调的是动。
4、拉动:拉动生产亦即按用户需求拉动生产,而不是把产品强行推给用户。
5、尽善尽美:用尽善尽美的价值创造过程为用户提供尽善尽美的价值。
第二种回答:原则1:消除八大浪费企业中普遍存在的八大浪费涉及:过量生产、等待时间、运输、库存、过程(工序)、动作、产品缺陷以及忽视员工创造力。
原则2:关注流程,提高总体效益管理大师戴明说过:"员工只须对15%的问题负责,另外85%归咎于制度流程".什么样的流程就产生什么样的绩效。
改进流程要注意目标是提高总体效益,而不是提高局部的部门的效益,为了企业的总体效益即使牺牲局部的部门的效益也在所不惜。
原则3:建立无间断流程以快速应变建立无间断流程,将流程中不增值的无效时间尽可能压缩以缩短整个流程的时间,从而快速应变顾客的需要。
原则4:降低库存需指出的是,降低库存只是精益生产的其中一个手段,目的是为了解决问题和降低成本,而且低库存需要高效的流程、稳定可靠的品质来保证。
很多企业在实施精益生产时,以为精益生产就是零库存,不先去改造流程、提高品质,就一味要求下面降低库存,结果可想而知,成本不但没降低反而急剧上升,于是就得出结论,精益生产不适合我的行业、我的企业。
这种误解是需要极力避免的。
原则5:全过程的高质量,一次做对质量是制造出来的,而不是检验出来的。
检验只是一种事后补救,不但成本高而且无法保证不出差错。
因此,应将品质内建于设计、流程和制造当中去,建立一个不会出错的品质保证系统,一次做对。
精益生产要求做到低库存、无间断流程,试想如果哪个环节出了问题,后面的将全部停止,所以精益生产必须以全过程的高质量为基础,否则,精益生产只能是一句空话。
精益生产五大原则

精益生产五大原则精益生产(Lean Production)是一种以提高生产效率和质量为目标的生产管理方法,由日本丰田汽车公司创始人之一,著名企业家丰田太郎提出。
它以节约资源、降低浪费、提高员工参与度和持续改善为核心原则。
精益生产有五大原则,分别是价值流思维、流程的流动、拉动生产、零库存和持续改善。
第一,价值流思维(Value Stream Thinking)。
价值流是指顾客购买产品时愿意为之付费的所有活动的集合。
价值流思维的目标是通过分析生产过程中各个环节的价值流,消除不必要的环节和浪费,最大限度地提升价值创造的效率。
价值流思维强调整个价值链的优化,关注价值的流动而非单个环节的效率。
通过全面理解价值流程,找出不增值的环节并削减,将生产过程中的各个环节无缝连接起来,使价值在生产过程中能够顺畅地流动。
第二,流程的流动(Flow)。
流程的流动强调的是产品在生产过程中的流动,要求消除所有阻碍产品流动的因素。
流动原则要求缩短产品从原材料到最终成品的生产周期,减少产品的停滞和等待时间,从而提高生产效率。
流程的流动中还强调对生产过程中的瓶颈环节进行监控和管理,确保每个环节都能够顺畅流动,以保证整个生产过程的连续性。
第三,拉动生产(Pull Production)。
拉动生产原则是指在生产过程中,根据顾客需求,通过减少库存和根据实际需求实时生产,实现生产活动的“拉动”。
相较于推动式生产,拉动式生产更加灵活,能够根据市场需求来调整生产计划,减少库存积压,降低库存成本。
拉动式生产也能够有效避免过量生产和“刷单”等现象,提高资源利用效率。
第四,零库存(Zero Inventory)。
零库存是指在供应链中减少或消除库存的原则。
零库存原则的目标是通过减少库存数量和减少库存滞留时间,减少资金占用和库存积压的问题。
零库存原则在精益生产中十分重要,它通过拉动式生产、批量生产、精确计划等手段,保持库存的最低水平,以减少非价值增加的资金、时间和空间的浪费。
精益思想

精 益 思 想
Lean Thinking
2、精益思想的价值观 “ 价值 ” 的通常定义:
古典主义经济学:认为价值和价格并不等同。按照马克思主义
政治经济学的观点,价值就是凝结在商品中无差别的人类劳动,即商 品价值。
新古典主义经济学:物体的价值就是该物体在一个开放和竞争
的交易市场中的价格,因此,价值主要决定于对于该物体的需求,而 不是供给。
精 益 思 想
Lean Thinking
浪费的种类 (2) 等待的浪费 两个相互依存的变量不完全同步导致的时间等待
生产线上不同品种之间的切换,每天的工作 量变动幅度过大,有时很忙,有时造成人员和设 备闲置不用;上游的工序出现问题,导致下游工
序无事可做;生产线劳逸不均。
精 益 思 想
Lean Thinking
1. 生产过剩的浪费
2. 等待的浪费 3. 搬运的浪费
4. 过度加工的浪费
5. 库存的浪费 6. 动作的浪费
7. 纠正错误的浪费
精 益 思 想
Lean Thinking
工作中识别浪费的思维模式
思维模式
工作中有哪些浪费现象 ?
1、人: 2、机: 3、料: 4、法: 5、环: 6、
“ 每时每处都存在浪费
• 不能创造价值而且可以立即去除的活动(Muda2)
精 益 思 想
Lean Thinking
2、价值流图
价值流图是丰田精益生产系统框架下的一种用来描述物流 和信息流的形象化工具,是精益生产用来识别目前和未来的价 值状况,寻求改善机会,设定改善方向和愿景以及行动计划的 工具。
价值流图,是查找和发现浪费的基本工具!
精 益 思 想
Lean Thinking
精益生产的五项原则—精益思想
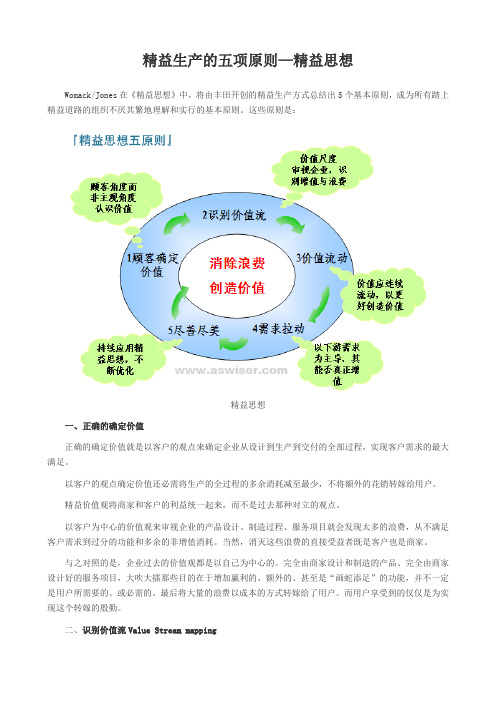
精益生产的五项原则—精益思想Womack/Jones在《精益思想》中,将由丰田开创的精益生产方式总结出5个基本原则,成为所有踏上精益道路的组织不厌其繁地理解和实行的基本原则。
这些原则是:精益思想一、正确的确定价值正确的确定价值就是以客户的观点来确定企业从设计到生产到交付的全部过程,实现客户需求的最大满足。
以客户的观点确定价值还必需将生产的全过程的多余消耗减至最少,不将额外的花销转嫁给用户。
精益价值观将商家和客户的利益统一起来,而不是过去那种对立的观点。
以客户为中心的价值观来审视企业的产品设计、制造过程、服务项目就会发现太多的浪费,从不满足客户需求到过分的功能和多余的非增值消耗。
当然,消灭这些浪费的直接受益者既是客户也是商家。
与之对照的是,企业过去的价值观都是以自己为中心的。
完全由商家设计和制造的产品、完全由商家设计好的服务项目,大吹大擂那些目的在于增加赢利的、额外的、甚至是“画蛇添足”的功能,并不一定是用户所需要的、或必需的。
最后将大量的浪费以成本的方式转嫁给了用户。
而用户享受到的仅仅是为实现这个转嫁的殷勤。
二、识别价值流Value Stream mapping价值流是指从原材料转变为成品、并给它赋予价值的全部活动。
这些活动包括:从概念到设计和工程、到投产的技术过程,从订单处理、到计划、到送货的信息过程,和从原材料到产品的物质转换过程,以及产品全生命周期的支持和服务过程。
精益思想识别价值流的含义是在价值流中找到那些是真正增值的活动、那些是可以立即去掉的不增值活动。
精益思想将所有业务过程中消耗了资源而不增值活动叫做浪费。
识别价值流就是发现浪费和消灭浪费。
识别价值流的方法是“价值流分析Value Stream map Analysis”——首先按产品族为单位画出当前的价值流图,再以客户的观点分析每一个活动的必要性。
价值流分析成为实施精益思想最重要的工具。
价值流并不是从自己企业的内部开始的,多数价值流都向前延伸到供应商,向后延长到向客户交付的活动。
精益思想五原则
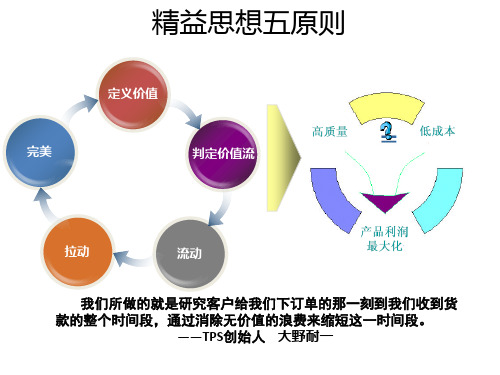
•每家公司都只是从内部看到自己的营运效益,而根本没有人 看到客户眼中的完整产品。
•总计旅行时间:13小时 •实际旅途时间:7小时(占54%) •排队与等候时间:6小时 •排队次数:10次 •行李拿上拿下:7次 •检查:8次
精益思想五原则
判定价值流 从货架通道里观察
•在货架通道里我们可以观察到上千种价值流流进客户手中。当购物者的决定拉动起来,物质产 品流在超市的货架通道里到达了终点,而且在新产品推出时,产品开发的过程也告终。 •大野耐一,在现代超市受到启发,而创造了我们现在称之为及时生产(JIT)的流动管理系统。
*
•买主讨厌和新房建筑商谈判时的争论; •讨厌要长时间地等待完工才能搬入新居; •讨厌入住以后还有一堆不可避免的未完事项 •。。。
(听取客户声音:客户不喜欢麻烦)
重新思考
客户价值
客户只要付款买他 认为真正需要的东西
•让买主可以清楚地看到他们想要 的东西(40种不同的砖、3000种 壁纸、4种家庭办公样式等); •开设一条龙销售中心,所有的事 情均可在销售后中心解决; •交货期由6个月缩短到30天。
一提盒可乐的价值流
铝土矿
玉米地
甜菜地
还原厂
玉米仓储
冷杉树林 纸厂
冶炼厂 制盒厂
焦糖厂
热轧厂
焦糖仓储
冷轧厂
制罐厂
原浆厂
甜菜仓储 炼糖厂 食糖仓储
盒制品仓库
灌装厂
灌装厂 仓库
乐购 仓库
乐购 商店
消费 者家
精益思想五原则
判定价值流 可乐的价值流分析---发现浪费
●分析可乐的价值流,实际创造价值的时间为3天,整个价值流时间为319天,价值流上99%的时间中, 价值一点也没有流动:等待中的浪费。 ●罐子和制罐用的铝被拿起、放下30次。从客户观点看,这样做不增加任何价值:搬运中的浪费。 ●铝和罐子要经过14个储存点和仓库,罐子装上、卸下货盘4次:库存的浪费。 ●24%从冶炼厂出来变成废料:残次品的浪费。
精益思想五原则
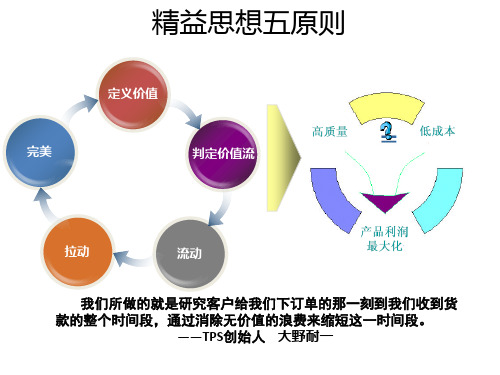
*
Process Process Process “A” “B” “C”
Elapsed Time: 01 Minute
精益思想五原则
流动
从批量生产到流动生产
Batch Process
I
Process “A”
I
Process “B”
Process “C”
Elapsed Time: 60 Minutes
•外出旅行想要的是一项没有麻烦的整体服务:把人和行李运到机场、坐飞机到达目 的地、坐车到别墅,还有别墅本身的服务。
1.打电 话给旅 行社预 约
2.收到 寄来的 机票
3.电话 预约出 租车
4.等候 出租车
5.装行 李
6.开车 到机场
7.卸行 李
8.排队 换外汇
9.排队 登记
10排 队过安 检
20.排 队过海 关
精益思
• 产品和服务应该按客户需要他们的速度流过一个精益机构。既不能 有在制品,也不能迟交付。 • 工序流程应该仅仅包含增值的操作工序。 • 通常需要根据重新设计程序来重新设计平面布置以保证平滑流动。
*
精益思想五原则
流动
批量生产的世界-去看医生的例子
1.打电 话预约 医生
*
精益思想五原则
●用户有需求才生产
拉动
●不是把用户不需要的产品强推给他们
推动
产生问 题
拉动
精益思想五原则
拉动
拉动生产的简单示意
Supplier Process
Supermarket
Customer Process
精益思想五原则
拉完动美
追求完美适用于价值流的所有方面。
在所有程序中存在的不定性应该消除和被控制,以帮助该机 构变得越来越精益,直到完美。这样才能向客户交付高质量的 产品。
Lean thinking

Muda Vs. Value 浪费和价值的对比
Examples •Machine parts •Weld parts together •Attached parts to vehicle
Value Added
Action
Examples •Waiting •Sorting •Rework
Muda
确定每个产品族的价值流 让产品流动起来 于是客户可以拉动 面向完美的管理
Value 价值
按最终客户的立场来说明价值 判断现有产品和流程如何无法满足客户的价值期望: 价格? 质量?
可靠的交付?
对变动需求的快速响应? ??? 还是其他的?
Value Stream价值流
确定将产品从订单到交付所需要的当前的所有的步骤
Pull拉动
通过压缩供货时间并改正价值说明,实现客户在确切需要的 时间获得确切所需。
对短期:平滑的拉动回路来降低库存
对近期:通过互联网用快速的响应时间实现按订单生产
对长期:在稳定关系中进行诊断和预诊断来消除消费者 和生产者之间的不理解
Pull - The Continuing Need! 拉动-连续的需求
Value Add is small, all else is Muda Elபைடு நூலகம்minate it! 增加价值是少的,其他是浪费消除它们
What To Do? 做什么?
• Reduce Lead Time!减少供货时间
– Get each process to produce only what the next process needs when it needs it.让每个流程只在下个流程的需要时生产下一流程的产品 – Orchestrate (control, manage, regulate) operations to get ever closer to this ideal, ever shortening the lead time. 协同(控制,管理,规范)运作 以更接近这一理念,更缩短供货时间
- 1、下载文档前请自行甄别文档内容的完整性,平台不提供额外的编辑、内容补充、找答案等附加服务。
- 2、"仅部分预览"的文档,不可在线预览部分如存在完整性等问题,可反馈申请退款(可完整预览的文档不适用该条件!)。
- 3、如文档侵犯您的权益,请联系客服反馈,我们会尽快为您处理(人工客服工作时间:9:00-18:30)。
精益思想(Lean Thinking)与五项原则(Five Principles)
“精益思想”一词源于James P. Womack和Daniel T. Jones1996年的名著《精益思想》。
该书在《改变世界的
机器》的基础上,更进一步集中、系统地阐述了关于精益的一系列原则和方法,使之更加理论化。
精益思想要求企业找到最佳的方法确立提供给顾客的价值,明确每一项产品的价值流,使产品在从最初的
概念到到达顾客的过程中流动顺畅,让顾客成为生产的拉动者,在生产管理中精益求精、尽善尽美。
价值、价值流、流动、拉动和尽善尽美的概念进一步发展成为应用于产品开发、制造、采购和服务顾客各个方面的精益方法(Lean Techniques)。
精益的5项原则
1价值观(Value)
精益思想认为企业产品(服务)的价值只能由最终用户来确定,价值也只有满足特定用户需求才有存在的意义。
精益思想重新定义了价值观与现代企业原则,它同传统的制造思想,即主观高效率地大量制造既定产品向用户推销,是完全对立的。
2价值流(Value Stream)
价值流是指从原材料到成品赋予价值的全部活动。
识别价值流是实行精益思想的起步点,并按照最终用户的立场寻求全过程的整体最佳。
精益思想的企业价值创造过程包括:从概念到投产的设计过程;从定货到送货的信息过程;从原材料到产品的转换过程;全生命周期的支持和服务过程。
3流动(Flow)
精益思想要求创造价值的各个活动(步骤)流动起来,强调的是“动”。
传统观念是“分工和大量才能高效率”,但是精益思想却认为成批、大批量生产经常意味着等待和停滞。
精益将所有的停滞作为企业的浪费。
精益思想号召“所有的人都必须和部门化的、批量生产的思想做斗争,因为如果产品按照从原材料到成品的
过程连续生产的话,我们的工作几乎总能完成得更为精确有效”。
4拉动(Pull)
“拉动”的本质含义是让用户按需要拉动生产,而不是把用户不太想要的产品强行推给用户。
拉动生产通过
正确的价值观念和压缩提前期,保证用户在要求的时间得到需要的产品。
实现了拉动生产的企业具备当用户需要时,就能立即设计、计划和制造出用户真正需要的产品的能力;最后实现抛开预测,直接按用户的实际需要进行生产。
实现拉动的方法是实行JIT生产(Just-in-time)和单件流(One-Piece Flow)。
JIT和单件流的实现必须对原
有的制造流程做彻底的改造。
流动和拉动将使产品开发周期、定货周期、生产周期降低50~90%。
5尽善尽美(Perfection)
精益思想定义企业的基本目标是:用尽善尽美的价值创造过程为用户提供尽善尽美的价值。
James P. Womack阐述精益制造的目标是“通过尽善尽美的价值创造过程(包括设计、制造和对产品或服务整个生命周期
的支持)为用户提供尽善尽美的价值”。
精益制造的“尽善尽美”有3个含义:用户满意、无差错生产和企业自身
的持续改进。