精益思想与精益生产体制117页PPT
合集下载
精益思想;精益服务概述幻灯片PPT

精益服务的精髓
3、服务效益更佳 服务效益是以服务效率和服务质量为前提的,是服务带给顾客和
企业的双赢。要使服务效益更佳,就要在力求质量和效率更好的基础 上,从顾客的角度出发,消除一切浪费,降低成本,拓宽效益空间。
精益服务的本质
精益服务的本质就是一切从顾客出发,为顾客创造价值。 实现的途径: 1、满足顾客现实需求;
精益服务体系
图1
精益服务的精髓
精益服务的精髓就是使服务更加完美。服务更加完美体现在三个方面 1、服务效率更高
服务效率一方面体现在服务的速度上,另一方面体现在一定时间 内服务的结果。服务流程的优化是提升服务速度的突破口,流程越顺 畅,服务效率越高;同时,服务标准也是提升服务效率的关键,服务 标准越完善,服务效率越高。 2、服务质量更好
精益服务的概念
精益服务是在商业服务环境中,应用精益思想和精益改进方法,在精确的 时间、精确的地点,以精确的方试,把精确定价的精确服务递交给顾客。 精益服务提出的背景: 1、微利时代的到来 随着市场的逐步规范、行业更加成熟、信息更加灵敏、企业数量急剧增加, 中国迎来了一个新的时代——微利时代。 2、市场变化——长尾市场的出现 克里斯·安德森在名著《长尾理论》中把长尾市场概括为:提供所有的产品, 帮我找到它。即在供给上让顾客增加选择(机会),在需求上帮助顾客减 少选择(成本)
3、使价值不间断地流动(Flow)
精益将所有的停滞作为企业的浪费,号召“所有的人都必须和 部门化的、批量生产的思想做斗争”,用持续改进、JIT、单件流 (one-piece flow)等方法在任何批量生产条件下创造价值的连 续流动。
使价值流流动起来,必需具备必要的环境条件。这些条件是: 过失、废品和返工都造成过程的中断、回流。实现连续的流动要求 每个过程和每个产品都是正确的。全面质量管理和6 Sigma都成为 精益思想的重要组成部分。 环境、设备的完好性是流动的保证。3P、5S、全员维修管理 (TPM) 都是价值流动的前提条件之一。
精益生产与精益思想培训课件.pptx

成本中心论实例:生产的成本是100元,利润定为成本的20%,
即20元, 售价就定为120元。
价格中心论实例:商品的售价是100元,现在的成本是90元,那
么利润就是10元。售价若降低至95元,但是成本仍在90元,利润 也就降为5元。
利润中心论实例:公司的目标利润是20元,现在产品的价格是
100元,那么目标成本就是80元。如果市场的售价降至90元,但 目标利润仍是20元,因此必须加倍努力将目标成本降到70元。
现代产品开发的组织方法——并行工程
并行工程是将产品开发过程各个环节的工作,实行平行 交叉作业,如下图所示:
三、Lean Production的特点
1. 是一种强调价值链管理的生产方式; 2. 是一种由需求拉动的的生产方式; 3. 是一种低成本的生产方式; 4. 是一种高效率的生产方式; 5. 是一种准时化和快捷化的生产方式; 6. 是一种强调持续改进、追求卓越的生产方式;
四、精益生产的核心与目标
核心:消除一切浪费!
safety一改善的目的善于发现问题发现问题是改善的前提持续不断改善永无止境全员参与上至总经理下至普通工人关注细节从小处着手形成改善文化本职工作岗位职责改善二改善的基本思想牢固地树立改善意识改善的基础准确地把握现状找准问题改善的前提持续不断持之以恒改善的关键眼睛向内苦练内功深挖潜力改善的着眼点小组活动k小组项目管理改善的技巧三改善的要点四改善的四大原则eeliminate取消ccombine合并rrearrange重排ssimplify简化五改善的金科玉律现场领导要经常去现场了解情况发现问题现状要了解现场的实际状况找到产生问题的根源现策根据存在的问题及原因采取切实有效的对策正本清源不能头痛医头脚痛医脚标准化建立标准和规范防止同类问题反复发生六改善活动的步骤1了解现状找出问题2分析产生问题的原因3确定改善课题4制定改善方案目标措施费用进度计划5改善方案的优化论证审批6实施改善方案7评价改善效果改善成果发表8巩固与标准化奖励精益生产的四大支柱与两大基础1
即20元, 售价就定为120元。
价格中心论实例:商品的售价是100元,现在的成本是90元,那
么利润就是10元。售价若降低至95元,但是成本仍在90元,利润 也就降为5元。
利润中心论实例:公司的目标利润是20元,现在产品的价格是
100元,那么目标成本就是80元。如果市场的售价降至90元,但 目标利润仍是20元,因此必须加倍努力将目标成本降到70元。
现代产品开发的组织方法——并行工程
并行工程是将产品开发过程各个环节的工作,实行平行 交叉作业,如下图所示:
三、Lean Production的特点
1. 是一种强调价值链管理的生产方式; 2. 是一种由需求拉动的的生产方式; 3. 是一种低成本的生产方式; 4. 是一种高效率的生产方式; 5. 是一种准时化和快捷化的生产方式; 6. 是一种强调持续改进、追求卓越的生产方式;
四、精益生产的核心与目标
核心:消除一切浪费!
safety一改善的目的善于发现问题发现问题是改善的前提持续不断改善永无止境全员参与上至总经理下至普通工人关注细节从小处着手形成改善文化本职工作岗位职责改善二改善的基本思想牢固地树立改善意识改善的基础准确地把握现状找准问题改善的前提持续不断持之以恒改善的关键眼睛向内苦练内功深挖潜力改善的着眼点小组活动k小组项目管理改善的技巧三改善的要点四改善的四大原则eeliminate取消ccombine合并rrearrange重排ssimplify简化五改善的金科玉律现场领导要经常去现场了解情况发现问题现状要了解现场的实际状况找到产生问题的根源现策根据存在的问题及原因采取切实有效的对策正本清源不能头痛医头脚痛医脚标准化建立标准和规范防止同类问题反复发生六改善活动的步骤1了解现状找出问题2分析产生问题的原因3确定改善课题4制定改善方案目标措施费用进度计划5改善方案的优化论证审批6实施改善方案7评价改善效果改善成果发表8巩固与标准化奖励精益生产的四大支柱与两大基础1
精益思想介绍课件

定义
起源
价值导向
以客户需求为导向,将价值定义为对客户的增值,而非企业自身的成本。
流动与拉动
通过优化流程,实现各环节的顺畅流动,并采用拉动式生产方式以满足客户需求。
追求完美
不断改进和优化,追求尽善尽美的目标。
03
02
01
精益生产方式广泛应用于制造业,提高生产效率和产品质量。
制造业
服务行业
创新领域
精益思想在服务行业中也有广泛应用,如餐饮、医疗、教育等。
精益工具与技术
04
素养
培养员工养成良好的工作习惯,提高整体素质。
清洁
维护和保持整理、整顿、清扫后的状态,形成制度化、规范化的管理。
清扫
保持工作场所整洁,防止污染和浪费。
整理
区分必需品和非必需品,清理非必需品,为其他工作腾出空间。
整顿
将必需品分类、定位、标识,方便快速取用。
03
标准化
通过目视化管理,将工作流程、操作规范等标准化,提高工作效率和质量。
培养改进文化
培养员工对持续改进的认识和意识,鼓励员工积极参与改进活动,形成良好的改进文化。
精益管理原则
03
识别并分析产品或服务在创造过程中的所有活动是精益管理的重要步骤。
总结词
价值流不仅包括增值活动,还包括非增值活动,如运输、等待、库存等。通过识别这些活动,企业可以消除浪费,提高效率。
详细描述
优化价值流
基于价值流图的分析结果,企业可以针对性地优化不创造价值的环节,提高整体价值流的效率。
精益生产强调产品在价值流中的流动,避免生产过程中的停顿和等待。通过连续流动,企业能够快速响应市场需求,提高生产效率。
流动原则
拉动原则是指生产过程中的需求来自下游环节而非上游环节。通过实施拉动原则,企业能够减少库存积压,降低库存成本,并确保生产与市场需求保持一致。
起源
价值导向
以客户需求为导向,将价值定义为对客户的增值,而非企业自身的成本。
流动与拉动
通过优化流程,实现各环节的顺畅流动,并采用拉动式生产方式以满足客户需求。
追求完美
不断改进和优化,追求尽善尽美的目标。
03
02
01
精益生产方式广泛应用于制造业,提高生产效率和产品质量。
制造业
服务行业
创新领域
精益思想在服务行业中也有广泛应用,如餐饮、医疗、教育等。
精益工具与技术
04
素养
培养员工养成良好的工作习惯,提高整体素质。
清洁
维护和保持整理、整顿、清扫后的状态,形成制度化、规范化的管理。
清扫
保持工作场所整洁,防止污染和浪费。
整理
区分必需品和非必需品,清理非必需品,为其他工作腾出空间。
整顿
将必需品分类、定位、标识,方便快速取用。
03
标准化
通过目视化管理,将工作流程、操作规范等标准化,提高工作效率和质量。
培养改进文化
培养员工对持续改进的认识和意识,鼓励员工积极参与改进活动,形成良好的改进文化。
精益管理原则
03
识别并分析产品或服务在创造过程中的所有活动是精益管理的重要步骤。
总结词
价值流不仅包括增值活动,还包括非增值活动,如运输、等待、库存等。通过识别这些活动,企业可以消除浪费,提高效率。
详细描述
优化价值流
基于价值流图的分析结果,企业可以针对性地优化不创造价值的环节,提高整体价值流的效率。
精益生产强调产品在价值流中的流动,避免生产过程中的停顿和等待。通过连续流动,企业能够快速响应市场需求,提高生产效率。
流动原则
拉动原则是指生产过程中的需求来自下游环节而非上游环节。通过实施拉动原则,企业能够减少库存积压,降低库存成本,并确保生产与市场需求保持一致。
精益生产PPT培训资料
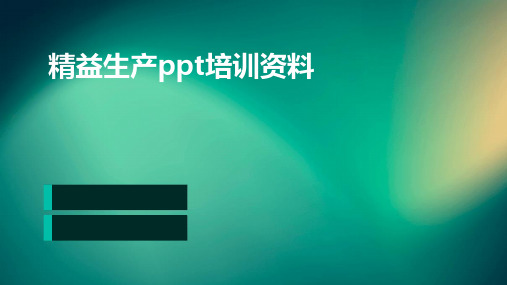
减少浪费
定义
01
浪费是指生产过程中不产生价值的活动或因素,如过度加工、
等待、搬运、库存等。
目的
02
消除浪费,提高生产效率。
步骤
03
通过分析生产过程中的各个环节,找出浪费并采取措施消除或
减少浪费,提高生产效率。
单元化生产
定义
单元化生产是一种将生产线划分为独立的生产单元,每个单元负责特定的产品或工序的生 产方式。
制定具体的目标指标 和时间表,确保目标 的可实现性和可衡量 性。
与员工和利益相关者 沟通,明确精益生产 的期望和要求。
价值流分析
对企业业务流程进行全面梳理, 识别并分析价值流中的浪费和瓶
颈。
运用价值流图等工具,可视化呈 现当前价值流状态,便于发现问
题。
确定关键改善区域,为后续改进 计划提供依据。
制定改进计划
根据价值流分析结果,制定针对性的 改进计划。
对改进计划进行优先级排序,确保资 源合理分配。
确定改进措施、责任人、时间表和预 期成果。
实施改进措施
按照改进计划逐步实施各项措施。 建立跨部门协作机制,确保改进措施的有效执行。
及时跟进并调整计划,确保改进过程中的灵活性。
持续改进与优化
对改进成果进行评估和总结, 确保达到预期目标。
全球化与本地化
全球化战略
随着经济全球化的深入发展,企业将更加注重全球化战略的制定和 实施,以拓展国际市场和提升品牌影响力。
本地化运营
在全球化战略的基础上,企业将更加注重本地化运营,以满足不同 国家和地区的市场需求和文化差异。
跨文化交流与合作
加强跨文化交流与合作,促进不Biblioteka 国家和地区之间的相互理解和合作 共赢。
精益生产方式PPT课件

提升企业竞争力
精益生产方式能够帮助企业快速响应 市场需求,提高产品质量和客户满意 度,从而提升企业竞争力。
精益生产方式的起源与发展
起源
精益生产方式起源于日本丰田汽车公 司的生产方式,旨在消除浪费、提高 效率和效益。
发展
随着精益生产方式的广泛应用和推广 ,其理论和方法不断完善和发展,逐 渐形成了包括精益研发、精益采购、 精益物流等方面的完整体系。
单元化生产
单元化生产是将生产线划分为 若干个独立的单元,每个单元 负责特定的产品或工序。
通过单元化生产,企业可以更 好地组织和管理生产过程,提 高生产效率和产品质量。
单元化生产需要合理规划和管 理,以确保单元之间的协调和 配合。
减少生产浪费
精益生产强调消除浪费,包括减 少不良品、减少库存、减少等待
性,促进企业的可持续发展。
03
精益生产方式的主要工 具和技术
5S管理
5S管理是精益生产中的一项基础工具, 包括整理(Sort)、整顿 (Straighten)、清扫(Sweep)、清 洁(Sanitize)和素养(Sustain)五个 方面。
实施5S管理有助于企业实现标准化、 规范化的管理,提高整体形象和品质。
和全面性。
04
精益生产方式的应用案 例
某汽车制造企业的精益生产实践
总结词:全面优化
详细描述:该汽车制造企业通过精益生产方式,实现了从产品设计、生产计划、 生产流程到供应链管理的全面优化。通过消除浪费、提高生产效率和产品质量, 该企业成功降低了成本并提高了市场竞争力。
某电子制造企业的精益生产实践
精益生产方式ppt课件
目录
• 精益生产方式概述 • 精益生产方式的核心理念 • 精益生产方式的主要工具和技术 • 精益生产方式的应用案例 • 精益生产方式的未来发展 • 结论
精益生产完整PPT教案
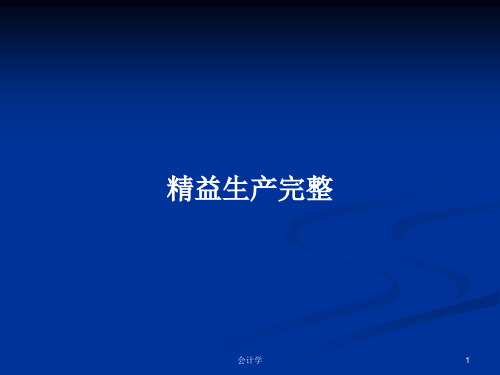
Pull system 相接合,根据准时生产指令进行组装和 生产。 ➢ 持续改善Kaizen,进行专门管理并制定评价奖励方法,
以5S基础推动全员参与的全面改善 ➢ 多能工 ➢ 教导式管理Enlightened management ➢ 平均化和目视化管理
第9页/共142页
10
精益体系
公司整体性利润增加
第14页/共142页
15
Cell/Line Flexibility柔性生产线
•Takt=40 sec •Cycle=120 sec •Operators=3
•Takt=30 sec •Cycle=120 sec •Operators=4
第15页/共142页
16
精益实施曲线 (time to benefit)
精益生产完整
会计学
1
生产方式的变革与精益思维起源
起源于20世纪50年代丰田汽车公司,而在80 年代中期被欧美企业纷纷采用。随着微利个性 化消费时代的来临,精益生产成为企业竞争的 有力武器。
卓越的研究开发可使新产品进入市场 依赖卓越的生产活动,才能立足于市场
第1页/共142页
2
生产方式的变革与精益思维起源
第3页/共142页
4
生产方式的变革主要原因
Shorter lead time and on time delivery 快速并准时交货 Grow the mix special configurations 需求品种增加,特殊定制 Maintain /improve quality and reduce price 不断改进质量及降低销售价格 Life cycle of product becoming shorter and shorter 产品的生命周期越来越短 No boundary ,business globalize village
以5S基础推动全员参与的全面改善 ➢ 多能工 ➢ 教导式管理Enlightened management ➢ 平均化和目视化管理
第9页/共142页
10
精益体系
公司整体性利润增加
第14页/共142页
15
Cell/Line Flexibility柔性生产线
•Takt=40 sec •Cycle=120 sec •Operators=3
•Takt=30 sec •Cycle=120 sec •Operators=4
第15页/共142页
16
精益实施曲线 (time to benefit)
精益生产完整
会计学
1
生产方式的变革与精益思维起源
起源于20世纪50年代丰田汽车公司,而在80 年代中期被欧美企业纷纷采用。随着微利个性 化消费时代的来临,精益生产成为企业竞争的 有力武器。
卓越的研究开发可使新产品进入市场 依赖卓越的生产活动,才能立足于市场
第1页/共142页
2
生产方式的变革与精益思维起源
第3页/共142页
4
生产方式的变革主要原因
Shorter lead time and on time delivery 快速并准时交货 Grow the mix special configurations 需求品种增加,特殊定制 Maintain /improve quality and reduce price 不断改进质量及降低销售价格 Life cycle of product becoming shorter and shorter 产品的生命周期越来越短 No boundary ,business globalize village
精益生产理念及体系简介PPT课件
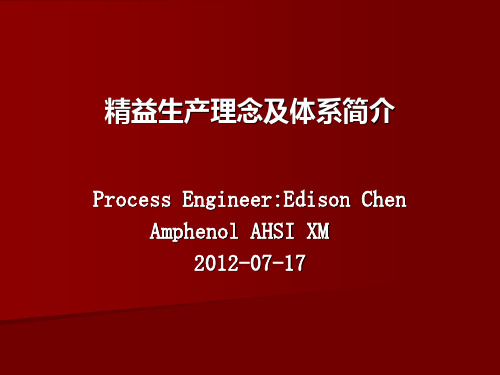
➢哪些是增值的过程?
Amphenol AHSI
精益生产的基本原则
➢流动 (Flow) 产品在工厂里从原料到成品必须经过的路程 及所需的时间
Amphenol AHSI
精益生产的基本原则
➢拉动 (Pull) 以客户的真实需求拉动产品的生产 ➢库存即是浪费 ➢尚未售出的完成品也是浪费 ➢去除过剩的产能 ➢提高客户需求拉动速度
……否则,要检查一下你在哪里做错了!
Amphenol AHSI
精益工具及术语
➢SMED ➢5S ➢TPM ➢Jidoka/自动化 ➢Kaikaku/创新 ➢Kanban/JIT ➢Kaizen/CI
➢定义价值 ➢价值流 ➢均衡、稳定性 ➢拉动 ➢单元布局 ➢标准化作业
Amphenol AHSI
同时,精益生产把责任下放到组织结构的各个层
次,采用小组工作法,充分调动全体职工的积极
性和聪明才智,把缺陷和浪费及时地消灭在每一
ቤተ መጻሕፍቲ ባይዱ个岗位。
Amphenol AHSI
Amphenol AHSI
精益生产的好处
精益生产主要研究时间和效率 , 注重提升 系统的稳定性 ,50多年来精益生产的成功 案例已证实: ●精益生产让生产时间减少 90% ●精益生产让库存减少 90% ●精益生产使生产效率提高 60% ●精益生产使市场缺陷减少 50% ●精益生产让废品率降低 50% ●精益生产让安全指数提升 50%
经过30多年的努力,终于形成了完整的丰 田生产方式,使日本的汽车工业超过了美 国,产量达到了1300万辆,占世界汽车总 量的30%以上。
Amphenol AHSI
精益生产核心
其核心是消除一切无效劳动和浪费,它把目标确 定在尽善尽美上
通过不断地降低成本、提高质量、增强生产灵活 性、实现无废品和零库存等手段确保企业在市场 竞争中的优势
Amphenol AHSI
精益生产的基本原则
➢流动 (Flow) 产品在工厂里从原料到成品必须经过的路程 及所需的时间
Amphenol AHSI
精益生产的基本原则
➢拉动 (Pull) 以客户的真实需求拉动产品的生产 ➢库存即是浪费 ➢尚未售出的完成品也是浪费 ➢去除过剩的产能 ➢提高客户需求拉动速度
……否则,要检查一下你在哪里做错了!
Amphenol AHSI
精益工具及术语
➢SMED ➢5S ➢TPM ➢Jidoka/自动化 ➢Kaikaku/创新 ➢Kanban/JIT ➢Kaizen/CI
➢定义价值 ➢价值流 ➢均衡、稳定性 ➢拉动 ➢单元布局 ➢标准化作业
Amphenol AHSI
同时,精益生产把责任下放到组织结构的各个层
次,采用小组工作法,充分调动全体职工的积极
性和聪明才智,把缺陷和浪费及时地消灭在每一
ቤተ መጻሕፍቲ ባይዱ个岗位。
Amphenol AHSI
Amphenol AHSI
精益生产的好处
精益生产主要研究时间和效率 , 注重提升 系统的稳定性 ,50多年来精益生产的成功 案例已证实: ●精益生产让生产时间减少 90% ●精益生产让库存减少 90% ●精益生产使生产效率提高 60% ●精益生产使市场缺陷减少 50% ●精益生产让废品率降低 50% ●精益生产让安全指数提升 50%
经过30多年的努力,终于形成了完整的丰 田生产方式,使日本的汽车工业超过了美 国,产量达到了1300万辆,占世界汽车总 量的30%以上。
Amphenol AHSI
精益生产核心
其核心是消除一切无效劳动和浪费,它把目标确 定在尽善尽美上
通过不断地降低成本、提高质量、增强生产灵活 性、实现无废品和零库存等手段确保企业在市场 竞争中的优势
精益生产的理念讲解(ppt 105页)
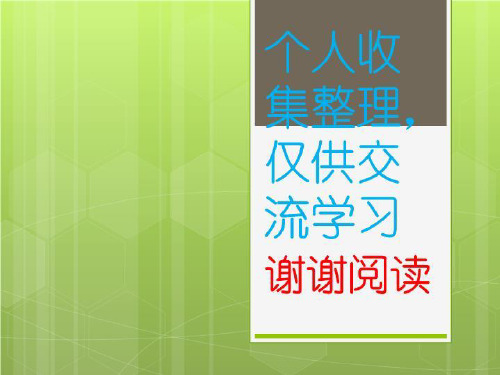
3、搬运的浪费
不符合精 益生产的 一切物料 搬运活动
21
精益生产的理念与浪费
现场浪费
4、作业本身
对最终产品或服务 不增加价值的过程
22
精益生产的理念与浪费
现场浪费
5、动作的浪费
任何不增加产品或服务价值的 人员 和 设备的动作
23
精益生产的理念与浪费
现场浪费
6、等待的浪费
当两个关联要素间 未能完全同步时 所产生的空闲时间
36
精益生产的管理技术
把 P
只把结果拉上来是 不能解决问题的
R
O
C
E
S
S
线
拉
上
来
自働化
↓
结
果
改
原 因
善 案
都也
拉跟
上着
的 话
拉 上
来 结果
原因
改善案① 对策 改善案②
对策
37
精益生产的管理技术
自働化
应用5-WHY快速寻找原因
当场采取应急措施 追查原因时应连续问5个为什么, 直到找到最直接的根本原因。
金属屑被吸入泵中。
第六个为什么:为什么金属屑被吸入泵中 ?
吸油泵没有过滤器
直到找到根本原因为止
。。。。。。
39
精益生产的管理技术
自働化
紧急措施:将出现的问题 临时紧急处理,避免事态 扩大或恶化,紧急措施必 须果断有效。
过渡措施:在对问题产生 的原因充分了解的前提下, 采取措施尽可能挽回造成 的损失,并保证同类问题 不再发生。
技术
稳定 准时生产 自动化 持续改进 生产均衡化
人员
长期资产 机器折旧 人员的增值