射线底片未焊透与未熔合缺陷影像的识别
射线检测底片上各种影像的识别 后附评片口诀
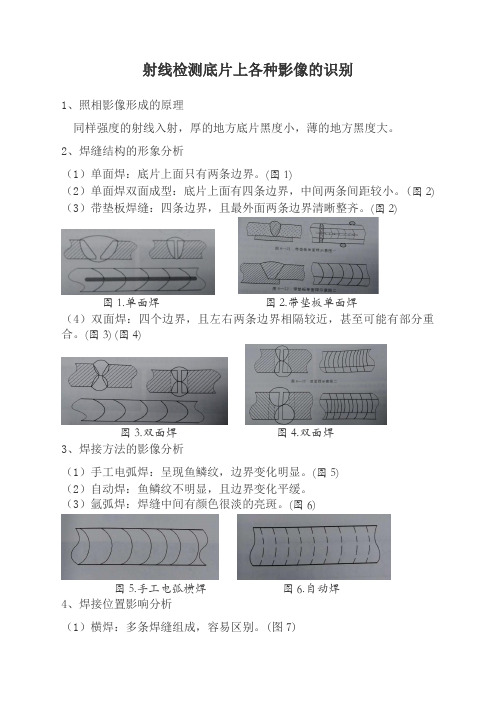
射线检测底片上各种影像的识别1、照相影像形成的原理同样强度的射线入射,厚的地方底片黑度小,薄的地方黑度大。
2、焊缝结构的形象分析(1)单面焊:底片上面只有两条边界。
(图1)(2)单面焊双面成型:底片上面有四条边界,中间两条间距较小。
(图2) (3)带垫板焊缝:四条边界,且最外面两条边界清晰整齐。
(图2)图1.单面焊图2.带垫板单面焊(4)双面焊:四个边界,且左右两条边界相隔较近,甚至可能有部分重合。
(图3) (图4)图3.双面焊图4.双面焊3、焊接方法的影像分析(1)手工电弧焊:呈现鱼鳞纹,边界变化明显。
(图5)(2)自动焊:鱼鳞纹不明显,且边界变化平缓。
(3)氩弧焊:焊缝中间有颜色很淡的亮斑。
(图6)图5.手工电弧横焊图6.自动焊4、焊接位置影响分析(1)横焊:多条焊缝组成,容易区别。
(图7)(2)立焊:鱼鳞纹较密,且焊缝宽度较大,存在亮斑。
(图8)图7.横焊图8.立焊(3)仰焊:与立焊影像难区别,鱼鳞纹密度稍大于立焊,也存在亮斑。
(图9)图9.仰焊5、焊缝中常见缺陷影像分析(1)分析要点:形状、位置、黑度。
(2)常见缺陷:气孔、夹渣、未焊透、未熔合、裂纹、钨夹渣。
其中未焊透、未熔合、裂纹、钨夹渣不参加评定。
a、气孔:(图10)形状:圆形、椭圆形、斜气孔(弥散形气孔),特点是外部轮廓比较规则。
黑度:气孔黑度较大,由中心向四周减淡(大气孔)位置:一般位于焊道投影中心位置。
b、夹渣:(图11) (图12)形状:圆形(点状)、长条形,特点是外部不规则。
黑度:黑度分布比较均匀,且黑度较淡。
位置:一般分布在焊道投影中心线到融合线之间。
图10.气孔图11.夹渣图12.线状夹渣c、未焊透:定义:坡口面没有熔化,该位置没有金属填充物,此类缺陷称为未焊透。
未焊透分为根部未焊透和中间未焊透。
形状:一条直线(存在长度和宽度变化)边界整齐。
黑度:均匀黑色。
位置:在焊道投影中间位置。
d、未熔合:(图13)定义:坡口面未熔化,且有填充金属,此类缺陷称为未熔合缺陷。
未熔合和未焊透缺陷的辨识及预防手段

未熔合和未焊透缺陷的辨识及预防手段摘要本文对焊缝未焊透和未熔合缺陷的原理、无损检测识别及产生的原因进行了浅述,并且提出预防措施。
为焊接作业人员预防这两种焊缝缺陷提供理论支持,为无损检测人员识别这两种焊接缺陷提供参考依据。
关键词未焊透;未熔合;原理;识别;危害;原因;预防1、未焊透和未熔合原理未焊透是指金属母材和焊材金属未充分熔化焊透,母材与焊缝金属未形成充分的联生结晶体,焊缝成形后有缺口,多发生在单层焊缝根部(图1)和双面焊缝的坡口钝边处(图2)。
图1:单面焊根部未焊透图2:双面焊中间未焊透未熔合是焊道之间或焊缝金属与母材之间没有全部熔化结合在一起而产生的缺陷,分为坡口未熔合(图3)、层间未熔合(图4)及焊缝根部未熔合这三种形式。
图3:坡口未熔合图4:层间未熔合2、常规无损检测手段对未焊透及未熔合的辨识2.1射线检测未焊透在射线照相底片上一般呈现的影像为连续或断续的比较有规则的细直黑线。
单面进行焊接的焊缝形成的未焊透缺陷一般位于焊缝的根部,双面进行焊接的焊缝形成的未焊透缺陷则通常位于焊缝中间的连接位置,因为未焊透是焊缝母材加工面和焊缝金属之间没有全部熔透形成缺陷,故未焊透的影像边界清晰、分明。
单面进行焊接、双面成形的焊缝根部未焊透缺陷的影像,在射线底片上一般处于施焊背面成形焊缝中间位置并且于焊缝平行、黑度较为均匀的直线。
双面进行焊接的根部未焊透的缺陷影像,在射线底片上一般也是位于焊缝中间位置且平行与焊缝,影像轮廓较为清晰、黑度较为均匀的黑直线。
在进行开V型坡口的焊缝中,根部未焊透的缺陷影像,一般位于焊缝的中间并且黑度较为均匀,呈现连接或是断续的黑线。
当然,未焊透缺陷在X射线底片上也有可能不在焊缝中间,是偏离中心线黑线等。
未熔合在射线底片上的影像有时不那么清晰,只有当射线正好垂直于未熔合面进行透照时,才有较为清晰的黑化度,均匀的色泽。
单面焊根部未熔合,当靠近母材时同常为黑度均匀的细线,但当在焊缝中心线附近时,则会呈现的影像为不规则齿形块状;单面坡口未熔合缺陷影像通常是一侧平直、另一侧则为不规则曲线,黑度均匀、较淡,有时候会有夹渣影像出现。
焊缝、铸件缺陷及伪缺陷在X射线底片上影像特征的分析

焊缝、铸件缺陷及伪缺陷在X 射线底片上影像特征的分析樊星明一 .单个气孔 (分散气孔 )1.特征和分布状态单个气孔缺陷在焊接内部多呈单一状态均匀分布,在焊缝上部,气孔体积不大 ,呈球状或椭圆形,外表光滑。
2.X 射线检测单个气孔与 X 射线底片上能清晰地显示出气孔的球状,椭圆状轮廓,由于经常采用射线方向与焊缝纵向垂直的透照方法,我们在底片上看到的都是气孔的正投影图象,所以,在 X 射线底片上都不能反映单个气孔缺陷在焊缝横向所处位置,即不能说明单个气孔是在焊缝的上部、中部或下部。
3.形成原因A焊接前未将焊缝坡口处金属上的铁锈、油污和油漆等清理干净。
B电焊条潮湿,水分在电弧高温作用下分解成氢气和氧气等气体,溶解于液态金属中,此时假设焊缝中液态金属凝固过快,熔解气休不能及时自焊缝中逸出。
C由于电弧加热母材温度不够高,焊接速度又过快等不合理工艺因素影响。
二 .链式气孔缺陷1.特征与分布状态链式乞孔在焊缝中呈一直线分布,气孔边沿相互衔接,状如链条,链的中心与焊缝轴线平行。
在埋弧焊中带出现在母材与焊缝之间。
在单面对接焊缝中常出现在焊接底部,链式乞孔缺陷很容易和未焊透缺陷混淆。
为了与未焊透缺陷区别,链状乞孔又称细线气孔。
在焊缝边沿的纵剖面上可以看到链状气孔,在母材与焊缝分界面上呈链环状影像。
在焊缝横剖面上链状气孔是呈单个分布,并有一定距离。
链状气孔之所以有以上所述的分布状态是由于母材与焊缝边界处冷却速度大,液态金属在此处受母材激冷,首先在此处凝固。
而氢气泡在固相外表上形成时消耗的功又小,因此氢气在熔池中析出即在此处元集形成气泡,来不及逸出。
2.X 射线检测链式气孔缺陷在X 射线底片上能清晰地显示出来,有的链环状分布,连续长度有30mm 以上有的那么呈断链状。
一段一段分布在焊缝与母材边沿部位底片上呈暗色图像,在链的边沿可清楚扯到气孔圆形轮廓。
3.形成原因主要是由氢引起的,氢来源于潮湿的助熔剂和没有充分枯燥的焊条涂料中的水分。
浅谈如何识别未焊透与未熔合
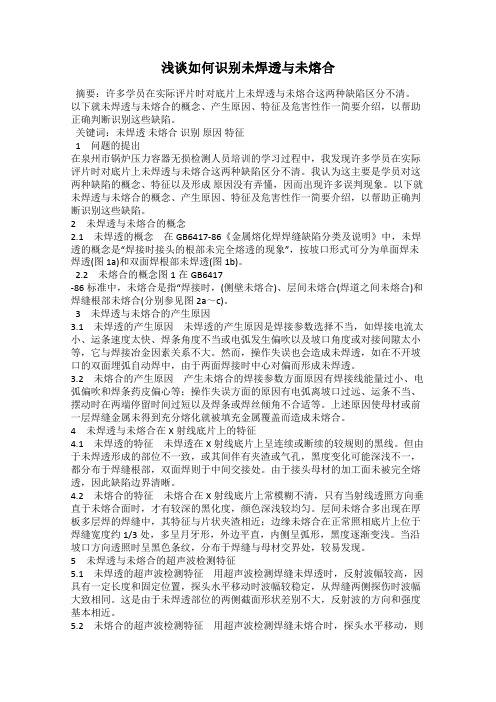
浅谈如何识别未焊透与未熔合摘要:许多学员在实际评片时对底片上未焊透与未熔合这两种缺陷区分不清。
以下就未焊透与未熔合的概念、产生原因、特征及危害性作一简要介绍,以帮助正确判断识别这些缺陷。
关键词:未焊透未熔合识别原因特征1问题的提出在泉州市锅炉压力容器无损检测人员培训的学习过程中,我发现许多学员在实际评片时对底片上未焊透与未熔合这两种缺陷区分不清。
我认为这主要是学员对这两种缺陷的概念、特征以及形成原因没有弄懂,因而出现许多误判现象。
以下就未焊透与未熔合的概念、产生原因、特征及危害性作一简要介绍,以帮助正确判断识别这些缺陷。
2未焊透与未熔合的概念2.1未焊透的概念在GB6417-86《金属熔化焊焊缝缺陷分类及说明》中,未焊透的概念是“焊接时接头的根部未完全熔透的现象”,按坡口形式可分为单面焊未焊透(图1a)和双面焊根部未焊透(图1b)。
2.2未熔合的概念图1在GB6417-86标准中,未熔合是指“焊接时,(侧壁未熔合)、层间未熔合(焊道之间未熔合)和焊缝根部未熔合(分别参见图2a~c)。
3未焊透与未熔合的产生原因3.1未焊透的产生原因未焊透的产生原因是焊接参数选择不当,如焊接电流太小、运条速度太快、焊条角度不当或电弧发生偏吹以及坡口角度或对接间隙太小等,它与焊接冶金因素关系不大。
然而,操作失误也会造成未焊透,如在不开坡口的双面埋弧自动焊中,由于两面焊接时中心对偏而形成未焊透。
3.2未熔合的产生原因产生未熔合的焊接参数方面原因有焊接线能量过小、电弧偏吹和焊条药皮偏心等;操作失误方面的原因有电弧离坡口过远、运条不当、摆动时在两端停留时间过短以及焊条或焊丝倾角不合适等。
上述原因使母材或前一层焊缝金属未得到充分熔化就被填充金属覆盖而造成未熔合。
4未焊透与未熔合在X射线底片上的特征4.1未焊透的特征未焊透在X射线底片上呈连续或断续的较规则的黑线。
但由于未焊透形成的部位不一致,或其间伴有夹渣或气孔,黑度变化可能深浅不一,都分布于焊缝根部,双面焊则于中间交接处。
射线评片技巧焊缝未熔合射线底片影像特点
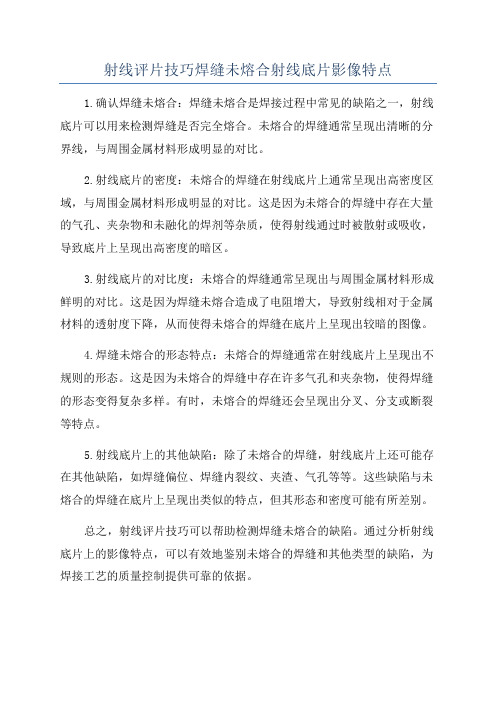
射线评片技巧焊缝未熔合射线底片影像特点
1.确认焊缝未熔合:焊缝未熔合是焊接过程中常见的缺陷之一,射线底片可以用来检测焊缝是否完全熔合。
未熔合的焊缝通常呈现出清晰的分界线,与周围金属材料形成明显的对比。
2.射线底片的密度:未熔合的焊缝在射线底片上通常呈现出高密度区域,与周围金属材料形成明显的对比。
这是因为未熔合的焊缝中存在大量的气孔、夹杂物和未融化的焊剂等杂质,使得射线通过时被散射或吸收,导致底片上呈现出高密度的暗区。
3.射线底片的对比度:未熔合的焊缝通常呈现出与周围金属材料形成鲜明的对比。
这是因为焊缝未熔合造成了电阻增大,导致射线相对于金属材料的透射度下降,从而使得未熔合的焊缝在底片上呈现出较暗的图像。
4.焊缝未熔合的形态特点:未熔合的焊缝通常在射线底片上呈现出不规则的形态。
这是因为未熔合的焊缝中存在许多气孔和夹杂物,使得焊缝的形态变得复杂多样。
有时,未熔合的焊缝还会呈现出分叉、分支或断裂等特点。
5.射线底片上的其他缺陷:除了未熔合的焊缝,射线底片上还可能存在其他缺陷,如焊缝偏位、焊缝内裂纹、夹渣、气孔等等。
这些缺陷与未熔合的焊缝在底片上呈现出类似的特点,但其形态和密度可能有所差别。
总之,射线评片技巧可以帮助检测焊缝未熔合的缺陷。
通过分析射线底片上的影像特点,可以有效地鉴别未熔合的焊缝和其他类型的缺陷,为焊接工艺的质量控制提供可靠的依据。
无损检测射线常见缺陷图集及分析.
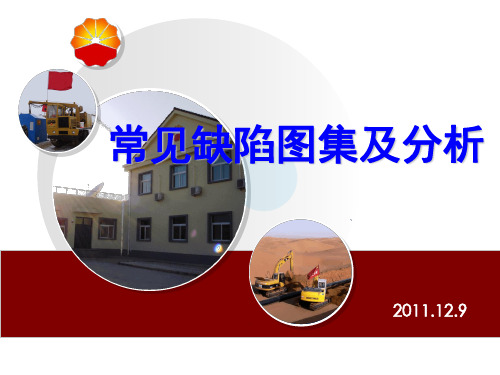
折 痕 曝 光 前
1、折痕的表面现象是什么? 折痕(曝光前)的表征为白月牙状显示,其密度低于邻近的胶片区域(黑度较低)。 2、它们产生的原因是什么? 曝光前弯曲胶片用力过大或过猛都会导致这种类型的折痕。 3、这些现象何时可能发生? 通常出现在从包装盒取出胶片或在曝光前装入暗袋时处理不当的情况下。 4、如何检验曝光前的折痕? 有意识地将某些胶片卷曲或扭折,使其曝光,然后按正常方法冲洗。检验胶片,这时您可 能会在胶片处理不当的地方风到一些颜色较淡的折痕。 5、如何可以避免它们? 严格遵守暗室操作规程,始终小心处理胶片,特别避免手指对胶片施以任何类型的压力。
未融合
边缘未融合
注意:砂轮片磨伤痕迹(不是未融合)
5、裂纹
定义:裂纹是指材料局部断裂形成的缺陷。 影像特征:底片上裂纹和典型影像是轮廓分明的黑线或黑丝。其细节 特征包括:黑线或黑丝上有微小的锯齿,有分叉,粗细和黑度有时有 变化,有些裂纹影像呈较粗的黑线与较细的黑丝相互缠绕状;线的端 部尖细,端头前方有时有丝状阴影延伸。
纵向裂纹
根部裂纹
横向裂纹
6、咬边
一、常见缺陷及示意图
二、其他几种缺陷 三、常见伪缺陷
表 面 内 边
内 咬 边
错 口
接 头 凹 坑
一、常见缺陷及示意图
二、其他几种缺陷 三、常见伪缺陷
1、压痕
1、压痕的表面现象是什么? 压痕的表征为密度明显低于邻近区域的密度。 2、它们产生的原因是什么? 在曝光前某个胶片区域局部受力严重。 3、这些现象何时可能发生? 产生压痕的主要原因在于暗袋准备过程中胶片处理的 方式不当。在处理过程中,胶片某处可能被压(夹)紧 在暗袋中。掉落到暗袋上的物体同样可能造成压痕。 4、如何检验压痕? 直接从同一包装盒中小心准备另一暗袋胶片,曝光并冲 洗胶片,如果未见到与第一次所见一样的暇疵,则第一次所 见的斑痕很可能就是压痕。 5、如何可以避免压痕? 严格遵守暗室操作规程,始终小心处理胶片,避免对胶 片施以任何类型的压力。
焊缝、铸件缺陷及伪缺陷在X射线底片上影像特征的分析

焊缝、铸件缺陷及伪缺陷在X射线底片上影像特征的分析樊星明一.单个气孔(分散气孔)1.特征和分布状态单个气孔缺陷在焊接内部多呈单一状态均匀分布,在焊缝上部,气孔体积不大,呈球状或椭圆形,表面光滑。
2. X射线检测单个气孔与X射线底片上能清晰地显示出气孔的球状,椭圆状轮廓,由于经常采用射线方向与焊缝纵向垂直的透照方法,我们在底片上看到的都是气孔的正投影图象,所以,在X射线底片上都不能反映单个气孔缺陷在焊缝横向所处位置,即不能说明单个气孔是在焊缝的上部、中部或下部。
3.形成原因A焊接前未将焊缝坡口处金属上的铁锈、油污和油漆等清理干净。
B电焊条潮湿,水分在电弧高温作用下分解成氢气和氧气等气体,溶解于液态金属中,此时若焊缝中液态金属凝固过快,熔解气休不能及时自焊缝中逸出。
C由于电弧加热母材温度不够高,焊接速度又过快等不合理工艺因素影响。
二.链式气孔缺陷1.特征与分布状态链式乞孔在焊缝中呈一直线分布,气孔边沿相互衔接,状如链条,链的中心与焊缝轴线平行。
在埋弧焊中带出现在母材与焊缝之间。
在单面对接焊缝中常出现在焊接底部,链式乞孔缺陷很容易和未焊透缺陷混淆。
为了与未焊透缺陷区别,链状乞孔又称细线气孔。
在焊缝边沿的纵剖面上可以看到链状气孔,在母材与焊缝分界面上呈链环状影像。
在焊缝横剖面上链状气孔是呈单个分布,并有一定距离。
链状气孔之所以有以上所述的分布状态是由于母材与焊缝边界处冷却速度大,液态金属在此处受母材激冷,首先在此处凝固。
而氢气泡在固相表面上形成时消耗的功又小,因此氢气在熔池中析出即在此处元集形成气泡,来不及逸出。
2. X射线检测链式气孔缺陷在X射线底片上能清晰地显示出来,有的链环状分布,连续长度有30mm以上有的则呈断链状。
一段一段分布在焊缝与母材边沿部位底片上呈暗色图像,在链的边沿可清楚扯到气孔圆形轮廓。
3.形成原因主要是由氢引起的,氢来源于潮湿的助熔剂和没有充分干燥的焊条涂料中的水分。
焊条地程中在电弧高温作用下水被分解成氢和氧。
射线底片未焊透与未熔合缺陷影像的识别
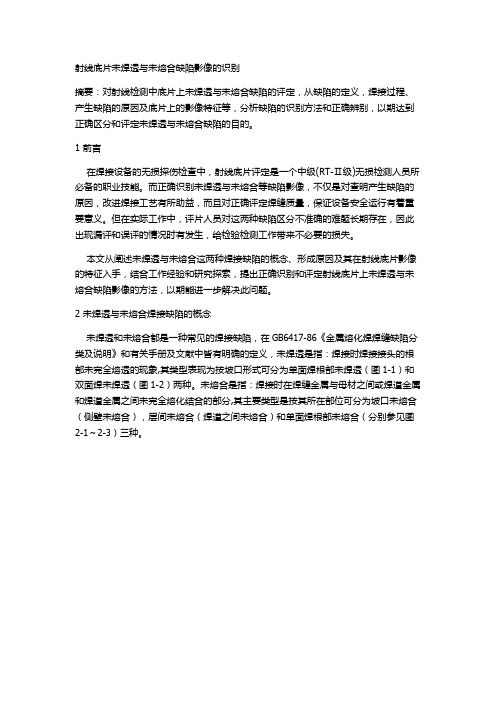
射线底片未焊透与未熔合缺陷影像的识别摘要:对射线检测中底片上未焊透与未熔合缺陷的评定,从缺陷的定义,焊接过程、产生缺陷的原因及底片上的影像特征等,分析缺陷的识别方法和正确辨别,以期达到正确区分和评定未焊透与未熔合缺陷的目的。
1 前言在焊接设备的无损探伤检查中,射线底片评定是一个中级(RT-Ⅱ级)无损检测人员所必备的职业技能。
而正确识别未焊透与未熔合等缺陷影像,不仅是对查明产生缺陷的原因,改进焊接工艺有所助益,而且对正确评定焊缝质量,保证设备安全运行有着重要意义。
但在实际工作中,评片人员对这两种缺陷区分不准确的难题长期存在,因此出现漏评和误评的情况时有发生,给检验检测工作带来不必要的损失。
本文从阐述未焊透与未熔合这两种焊接缺陷的概念、形成原因及其在射线底片影像的特征入手,结合工作经验和研究探索,提出正确识别和评定射线底片上未焊透与未熔合缺陷影像的方法,以期能进一步解决此问题。
2 未焊透与未熔合焊接缺陷的概念未焊透和未熔合都是一种常见的焊接缺陷,在GB6417-86《金属熔化焊焊缝缺陷分类及说明》和有关手册及文献中皆有明确的定义,未焊透是指:焊接时焊接接头的根部未完全熔透的现象,其类型表现为按坡口形式可分为单面焊根部未焊透(图1-1)和双面焊未焊透(图1-2)两种。
未熔合是指:焊接时在焊缝金属与母材之间或焊道金属和焊道金属之间未完全熔化结合的部分,其主要类型是按其所在部位可分为坡口未熔合(侧壁未熔合),层间未熔合(焊道之间未熔合)和单面焊根部未熔合(分别参见图2-1~2-3)三种。
.3未焊透与未熔合的产生原因3.1未焊透的产生原因未焊透的产生原因是焊接参数选择不当而引起,如焊接电流太小、运条速度太快、焊条角度不当或电弧发生偏吹以及坡口角度或焊接间隙太小等,它与焊接冶金因素关系不大。
有时焊工操作失误也会产生未焊透缺陷,如在不开坡口的双面埋弧自动焊中,也会由于两面焊接时中心对偏而形成未焊透。
3.2未熔合的产生原因未熔合的产生原因有焊接参数选择不当,如焊接线能量过小、电弧偏吹和焊条药皮偏心等;也有因焊工操作失误方面的原因,如坡口不够清洁、电弧离坡口过远、运条不当、摆动时在两端停留时间过短以及焊条直径或种类不对和焊丝倾角不合适等;因此使得母材或焊缝层间金属在未得到充分熔化前就被填充金属覆盖而造成未熔合缺陷。
- 1、下载文档前请自行甄别文档内容的完整性,平台不提供额外的编辑、内容补充、找答案等附加服务。
- 2、"仅部分预览"的文档,不可在线预览部分如存在完整性等问题,可反馈申请退款(可完整预览的文档不适用该条件!)。
- 3、如文档侵犯您的权益,请联系客服反馈,我们会尽快为您处理(人工客服工作时间:9:00-18:30)。
射线底片未焊透与未熔合缺陷影像的识别
摘要:对射线检测中底片上未焊透与未熔合缺陷的评定,从缺陷的定义,焊接过程、产生缺陷的原因及底片上的影像特征等,分析缺陷的识别方法和正确辨别,以期达到正确区分和评定未焊透与未熔合缺陷的目的。
1 前言
在焊接设备的无损探伤检查中,射线底片评定是一个中级(RT-Ⅱ级)无损检测人员所必备的职业技能。
而正确识别未焊透与未熔合等缺陷影像,不仅是对查明产生缺陷的原因,改进焊接工艺有所助益,而且对正确评定焊缝质量,保证设备安全运行有着重要意义。
但在实际工作中,评片人员对这两种缺陷区分不准确的难题长期存在,因此出现漏评和误评的情况时有发生,给检验检测工作带来不必要的损失。
本文从阐述未焊透与未熔合这两种焊接缺陷的概念、形成原因及其在射线底片影像的特征入手,结合工作经验和研究探索,提出正确识别和评定射线底片上未焊透与未熔合缺陷影像的方法,以期能进一步解决此问题。
2 未焊透与未熔合焊接缺陷的概念
未焊透和未熔合都是一种常见的焊接缺陷,在GB6417-86《金属熔化焊焊缝缺陷分类及说明》和有关手册及文献中皆有明确的定义,未焊透是指:焊接时焊接接头的根部未完全熔透的现象,其类型表现为按坡口形式可分为单面焊根部未焊透(图1-1)和双面焊未焊透(图1-2)两种。
未熔合是指:焊接时在焊缝金属与母材之间或焊道金属和焊道金属之间未完全熔化结合的部分,其主要类型是按其所在部位可分为坡口未熔合(侧壁未熔合),层间未熔合(焊道之间未熔合)和单面焊根部未熔合(分别参见图2-1~2-3)三种。
.
3未焊透与未熔合的产生原因
3.1未焊透的产生原因未焊透的产生原因是焊接参数选择不当而引起,如焊接电流太小、运条速度太快、焊条角度不当或电弧发生偏吹以及坡口角度或焊接间隙太小等,它与焊接冶金因素关系不大。
有时焊工操作失误也会产生未焊透缺陷,如在不开坡口的双面埋弧自动焊中,也会由于两面焊接时中心对偏而形成未焊透。
3.2未熔合的产生原因
未熔合的产生原因有焊接参数选择不当,如焊接线能量过小、电弧偏吹和焊条药皮偏心等;也有因焊工操作失误方面的原因,如坡口不够清洁、电弧离坡口过远、运条不当、摆动时在两端停留时间过短以及焊条直径或种类不对和焊丝倾角不合适等;因此使得母材或焊缝层间金属在未得到充分熔化前就被填充金属覆盖而造成未熔合缺陷。
4未焊透与未熔合的射线底片影像特征
4.1未焊透的特征未焊透在射线底片上的典型影像是细直黑线,两侧轮廓整齐为坡口钝边痕迹,宽度恰好为钝边间隙宽度;当部分钝边被融化时,影像轮廓就变得不整齐,
线条宽度和黑度也会有局部变化,呈连续或断续且较规则的黑线。
由于未焊透形成的部位不一致,有时还伴有夹渣或气孔,黑度大小不一。
对于双面焊根部未焊透,射线底片上影像一般是在焊缝中间位置,且平行于焊缝,影像轮廓清晰、黑度较为均匀的黑直线,如图3-2。
对于单面焊双面成型焊缝根部未焊透,射线底片影像一般是在施焊背面成型焊缝中间位置且平行于焊缝,黑度较为均匀的黑直线,如图3-1;对于采用砂轮机手工加工坡口的焊缝(如小径管对接焊缝),有时射线底片影像呈部分弯曲的线条,但黑度一定是均匀的。
对于单面焊加垫板焊缝根部未焊透,射线底片影像一般是在焊缝中间位置且平行于焊缝,黑度较为均匀的黑直线,宽度一定不大于坡口间隙。
当采用缩口边做衬垫时未焊透的影像与双面焊相同。
4.2未熔合的特征
未熔合在射线底片上的影像特征因产生的位置而有所不同,只有当射线透照方向垂直于熔合面时,才有明显的特征。
对于双面焊坡口未熔合,射线底片影像一般是在焊缝两侧边缘,位于焊缝宽度约
3/4处,多呈月牙形,靠近母材侧呈直线状,靠近焊缝中心侧呈弧形(有时为曲齿状)黑度逐渐变浅。
当沿坡口方向透照时呈黑色条状影像,如图4-1。
对于双面焊层间未熔合,射线底片影像多呈现黑色不规则的块状,黑度淡且不均匀,一般缺陷中心黑度大边缘渐小,与片状夹渣缺陷影像相近。
对于单面焊根部未熔合,射线底片影像一般是在焊缝根部焊趾线上,靠近母材侧呈直线黑线,靠近焊缝中心侧呈曲齿状;黑度渐淡,如图4-2。
常出现坡口的一边,称根部单边未熔合。
5未焊透与未熔合缺陷的危害性
5.1未焊透的危害性
未焊透在焊缝中的存在,不但大大降低焊缝的机械强度,同时容易延伸为裂纹性缺陷,导致构件的破坏,尤其是连续性未焊透,更是一种极危险的缺陷。
由于未焊透的危害性大,GB3323-2005《钢熔化焊对接接头射线照相及质量分级》和JB4730-2005《承压设备无损检测》标准均规定,所有Ⅰ级对接焊接头内不允许存在未焊透缺陷,对于双面焊和加垫板的单面焊焊缝Ⅱ、Ⅲ级焊缝也不允许存在未焊透。
《压力容器安全技术监察规程》和GB150《钢制压力容器》只是对于设计焊缝系数≤0.75的单面焊,允许存在未焊透缺陷,但对未焊透深度和长度都做了严格的规定。
5.2未熔合的危害性
由于未熔合缺陷本身就是一种虚焊,因此其应力集中系数更高,在交变载荷的作用下,未熔合处极易引起开裂,是焊缝中最危险缺陷之一。
所以,GB3323-2005《钢熔化焊对接接头射线照相及质量分级》和JB4730-2005《承压设备无损检测》规定,Ⅰ、Ⅱ和Ⅲ级焊缝中均不允许存在未熔合缺陷。
6识别未焊透与未熔合缺陷影像的方法
6.1未焊透缺陷影像的识别
对于未焊透缺陷,首先要根据缺陷的影像特征与底片上的实际影像进行对比,判定是否存在未焊透缺陷的可能。
因此,在底片上观察到的缺陷应该是一条黑度均匀且位于焊缝中心部位并平《机电技术》2007年第2期焊接技术74行于焊缝的细直线,若影像特征相同或想似可初步判定可能是未焊透缺陷。
再根据焊缝的坡口形式、焊接方法以及焊接规范的选择等因素,了解是否存在产生该缺陷的原因,最后确定是否为未焊透缺陷,并进一步评定缺陷是在双面焊的根部还是在单面焊的根部。
6.2未熔合缺陷影像的识别
对于未熔合缺陷,同样应先根据缺陷的影像特征与底片上的实际影像进行对比,判定是否有存在未熔合缺陷的可能。
因此,在底片上观察到的缺陷应该是靠近母材侧是一条黑度均匀的细线而靠近焊缝中心侧是曲齿状的块状缺陷,若影像特征相同或相似可初步判定该缺陷可能是未熔合缺陷。
再根据焊缝的坡口形式、焊接方法以及焊接规范的选择等因素,了解可能产生的原因,最后确定是否未熔合缺陷,并进一步评定缺陷是双面焊的坡口未熔合,还是多层焊的层间未熔合或是单面焊的根部未熔合。
6.3未焊透和未熔合缺陷影像的区分
射线底片上未焊透缺陷和未熔合缺陷影像的相同点在于,都有一边是坡口面的影像,且成直线状(层间未熔合除外)。
根本区别在于未焊透是两边坡口面未熔化,使影像呈线状,且位于焊缝的中心部位;未熔合只有一边坡口面未熔化,另一边是焊缝金属,使影像呈块状,位于焊缝边缘或靠近焊缝边缘的3/4处。
7结束语
(1)未焊透和未熔合焊接缺陷的成因及其对焊接接头性能的影响程度是不同的,因此在射线探伤底片上正确识别这两种缺陷,对查明缺陷产生原因,改进焊接工艺和正确评定焊缝质量,保证设备安全运行有重要意义。
(2)本文根据未焊透和未熔合缺陷影像的形状、黑度和位置等特征的观察以及与坡口等焊接因素相关性的探讨,提出了正确识别射线底片上未焊透和未熔合缺陷影像的方法,对提高评片水平,避免错判,误判是有助益的。