电解加工机床
电解磨削的原理及加工

电解磨削的原理及加工电解磨削顾名思义就是电解作用机床和机械磨削相结合的一种复合工艺方法。
目录∙1基本原理∙2产生∙3加工特点∙4应用∙5电解磨床∙6影响加工质量因素∙7工艺试验基本原理/电解磨削电解磨削图册电解磨削顾名思义就是电解作用机床和机械磨削相结合的一种复合工艺方法。
磨削时,工件接直流电源正极,电解磨轮接直流电源的负极,车床在二者之间供给电解液。
当直流电源接通时,工件表面将产生电化学反应,表层金属原子变成离子并形成阳极膜。
这层膜钝化作用强,又称为钝化膜。
它覆盖在工件表面,阻止电化学反应的继续进行。
当工件进一步向电解磨轮靠近并接触时,电解磨轮表面凸出的磨料高速运动,将钝化膜刮除,基体金属外露,继续产生电化学反应。
如此反复进行,工件材料被一层层地去除,从而达到加工的目的。
工件与电解磨轮接触时,磨轮表面凸出的车床磨料使二者保持一定的间隙,机床不致发生短路,且间隙中的电解液因磨轮的高速旋转不断被更新,使得阳极溶解反应能持续进行。
产生/电解磨削电解作用与机械磨削相结合的一种特种加工,又称电化学磨削,英文简称ECG。
电解磨削是20世纪50年代初美国人研究发明的。
图为电解磨削的原理。
工件作为阳极与直流电源的正极相连;导电磨轮作为阴极与直流电源的负极相连。
磨削时,两者之间保持一定的磨削压力,凸出于磨轮表面的非导电性磨料使工件表面与磨轮导电基体之间形成一定的电解间隙(约0.02~0.05毫米),同时向间隙中供给电解液。
在直流电的作用下,工件表面金属由于电解作用生成离子化合物和阳极膜。
这些电解产物不断地被旋转的磨轮所刮除,使新的金属表面露出,继续产生电解作用,工件材料遂不断地被去除,从而达到磨削的目的。
电解液一般采用硝酸钠、亚硝酸钠和硝酸钾等成分混合的水溶液,不同的工件材料所用电解液的成分也不同。
导电磨轮由导电性基体(结合剂)与磨料结合而成,主要为金属结合剂金刚石磨轮、电镀金刚石磨轮、铜基树脂结合剂磨轮、陶瓷渗银磨轮和碳素结合剂磨轮等,按不同用途选用。
2万安培大型电解加工机床结构设计与分析

s t a t i c a n a l ys i s a f t e r s i mp l i f i e d. 0bt a i n t h e r i g i d i t y of t h e ma c h i n e t oo l by t h e mi s e s s h a p e a n d d e f o r me d s h a p e. Th e n a t ur a l f r e q u e n c i e s o f t he ir f s t f o ur v i b r a t i o n m od e s we r e g a i n e d a f t e r mo d a l a na l y s i s .P r o v i — d i n g a t h e o r e t i c a l ba s i s or f t h e d e s i g n o f ma c h i n e t o o l b y t h e c ha r a c t e r i s t i c s o f ma c hi n e t o o 1 . Ke y wo r d s:e l e c t r o c he mi c a l ma c hi ne t o o l ;s t r u c t u r a l d e s i g n; s t a t i c a na l y s i s ;m o d a l a n a l ys i s
电化学加工机床的表面质量与电解电流密度的关系研究

电化学加工机床的表面质量与电解电流密度的关系研究引言:电化学加工是一种能够高效且精确地加工金属材料的技术,它利用电化学原理在材料表面形成氧化膜或者在金属之间的间隙产生金属溶解作用。
本文将就电化学加工机床的表面质量与电解电流密度的关系展开详细的研究,旨在探索电流密度对加工表面质量的影响及其机制,为加工工业提供理论指导。
一、电化学加工机床的工作原理电化学加工机床是利用电化学原理与机械传动结合的加工设备。
其工作原理是通过在工作液中引入电解质,形成电解池,并通过控制流经工作液中的直流电流来实现材料的加工。
在加工过程中,工作件作为阳极或者阴极,与电解质之间的电流密度决定了加工速度和表面质量。
二、电解电流密度对加工表面质量的影响2.1 加工速度与电解电流密度电解电流密度是指通过导电体截面的电流与电解质表面积的比值。
实验研究表明,加工速度与电解电流密度呈正相关关系,即电解电流密度越大,加工速度越快。
这是因为在电化学加工过程中,电流密度的增大会促进阳极处的金属离子溶解,从而加速材料的切削和溶解。
2.2 表面粗糙度与电解电流密度表面粗糙度是衡量材料表面质量的一个重要指标,它直接影响着材料的功能和性能。
研究发现,表面粗糙度与电解电流密度存在一定的关联性。
对于粗糙度较大的工件,随着电解电流密度的增加,表面粗糙度会逐渐减小。
这是因为较高的电流密度可以提供更大的电解反应速度,使得金属的切削速度增加,从而改善表面的粗糙度。
2.3 表面质量与电解电流密度除了表面粗糙度外,表面质量对于电化学加工的应用也非常重要。
一般来说,较低的电解电流密度可以得到更好的表面质量。
这是因为过高的电流密度会导致电解反应过于激烈,产生气泡和电光效应,从而影响表面的光洁度和一致性。
而较低的电解电流密度则可以减少这些不良效应,得到更加光滑和均匀的表面。
三、电解电流密度与电化学加工参数的关系3.1 电解电流密度与电极间距电解电流密度与电极间距之间存在一定的关系。
7.3 电解加工

增液孔 Φ1mm
零件尺寸精
度由阴极片 内腔口保证,
偶尔短路烧
伤时,只需 更换阴极片。
5. 叶片加工
叶片型面复杂,精度要求较高, 加工批量大,电解加工效果好。 加工方式有单面加工和双面加工。 机床有立式和卧式两种。 多用NaCl电解液混气加工。
机械加工设备——第7章
电解加工整体叶轮已普遍应
用,直接在轮坯上套料加工叶
精度控制在±0.1~0.2mm。
也采用端面进给法。
阴极设计制造是关键。用成型
精度高的电解液或混气加工时,阴
极设计较易。为使流场均匀,阴极 对应处加开增液孔。 近年发展用简单形状电极的数 控电解加工,柔性好,减少准备时
间,电源容量小,但加工速度降低
机械加工设备——第7章
4. 套料加工
用于等截面的大面积异 型孔或异型零件的加工,端 面进给加工方式。
图7-9 电解加工示意图 1-直流电源 2-工具电极 3-工件阳极 4-电解液泵 5-电解液
机械加工设备——第7章
7.3.2 电解加工特点:
1、优点:
1)可加工任何硬度的金属材料 2)加工叶片、锻模等型面,加工易变形或薄壁零 件 3)加工表面质量好,无毛刺、变质层、残余应力 4)生产率约为电火花加工的5~10倍 5)阴极工具无损耗可长期使用
机械加工设备——第7章
2.缺点:
1) 加工精度(±0.03 mm)及稳定性不易提高
2) 小孔、窄缝及棱角清晰零件难加工
3) 电极设计制造较麻烦,需多次修整 4) 附属设备多,一次性投资大 5) 防腐蚀及电解泥渣、废液处理问题
机械加工设备——第7章
7.3.3.电解加工工艺选用原则
1. 难加工材料的加工
机械加工设备——第7章
电解加工及基本原理
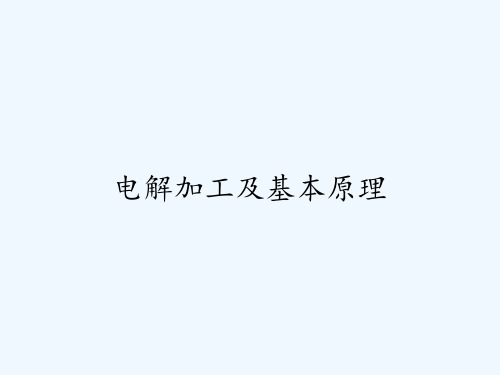
d、对机床、工具腐蚀相对较小
由于电解磨削就是靠砂轮磨粒来刮除具 有一定硬度和粘度得阳极钝化膜,由此电 解液中不能含有活化能力很强得活性离 子(如Cl-离子),一般使用腐蚀能力较弱 得NaNO3、NaNO2等为主得电解液,以提高 电解成形精度和有利于机床、工具得防 锈、防蚀。
2、复合电解磨削得特点
a、加工范围广、加工效率高 由于电解作用和工程材料得机械性能关
系不大,因此,只要选择合适得电解液就 可以用来加工任何高硬度、高韧性得金 属材料。 加工硬质合金时,与普通得金刚石砂轮磨 削相比,电解磨削得加工效率要高3~5倍。
b、工件得加工精度和表面质量高
由于砂轮只起刮除阳极薄膜得作用,磨削 力和磨削热都很小,不会产生磨削裂纹和 烧伤现象,因而能提高加工表面质量和加 工精度,一般表面粗糙度可优于Ra0、 16μm。
(2)工艺参数 :电流密度、电解液得流 速大小和温度高低
(3)工具阴极得表面质量 (4)工件表面必须除油去锈 (5)电解液必须经过滤沉淀,不含固体颗
粒杂质。
四、电解加工的应用
1、型腔加工 对模具消耗较大、精度要求不太高得矿
山机械、农机、拖拉机等所需得锻模已 逐渐采用电解加工。
2、型面加工
机械加工中去毛刺得工作量很大,尤其就 是去除硬而韧得金属毛刺,需要很多得人 力,电解倒棱去毛刺可以大大提高工效。
4、 深孔扩孔加工
深径比大于5得深孔,用传统切削加工方法加工, 刀具磨损严重,表面质量差,加工效率低。目前
采用电解加工方法加工φ4×2000mm、 φ100×8000mm得深孔,加工精度高,表面粗糙
电流从工件3通过电解液5而流向 磨轮,形成通路,于就是工件(阳 极)表面得金属在电流和电解液 得作用下发生电解作用(电化学 腐蚀),被氧化成为一层极薄得氧 化物或氢氧化物薄膜4(阳极薄 膜)。但阳极薄膜迅速被导电砂 轮中磨粒刮除,在阳极工件上又 露出新得金属表面并被继续电解。 这样电解作用和刮除薄膜得磨削 作用交替运行,工件被连续加工, 直至达到一定得尺寸精度和表面 粗糙度。
电解加工参考文献

参考文献《《电化学加工技术》》朱树敏化学工业出版社P39~81页摘要:电化学加工基本原理在阴、阳极表面发生得失电子的化学反应即称为电化学反应,利用这种电化学反应作用加工金属的方法就是电化学加工。
其中,阳极上为电化学溶解,阴极上为电化学沉积。
电解加工是利用金属在电解液中产生阳极溶解的电化学原理对工件进行成形加工的一种方法。
电解加工是特种加工技术中应用最广泛的技术之一,尤其适合于难加工材料、形状复杂或薄壁零件的加工。
电解加工基本原理基本原理:金属在电解液中的“电化学阳极溶解”。
在工件(阳极)与工具(阴极)之间接上直流电源(如图),使工具阴极与工件阳极间保持较小的加工间隙(0.1~0.8 mm),间隙中通过高速流动的电解液。
这时,工件阳极开始溶解。
开始时,两极之间的间隙大小不等,间隙小处电流密度大,阳极金属去除速度快;而间隙大处电流密度小,去除速度慢。
随着工件表面金属材料的不断溶解,工具阴极不断地向工件进给,溶解的电解产物不断地被电解液冲走,工件表面也就逐渐被加工成接近于工具电极的形状,如此下去直至将工具的形状复制到工件上。
1.电解加工的特点(1) 加工范围广(不受金属材料硬度和强度限制)。
(2) 生产率高,约为电火花的5-10倍,有时比切削高。
(3) 加工质量好,无切削力和切削热,表面无残余应力。
(4) 可用于加工薄壁和易变形零件。
(5) 工具阴极无损耗。
电解加工的问题电解加工当前存在的主要问题是加工精度难以严格控制,尺寸精度一般只能到0.15~0.30 mm 。
附属设备多,造价贵,占地面积大。
电解液腐蚀机床,电解液的处理也较困难,污染环境。
电解加工机理电解加工是利用金属在电解液中发生电化学阳极溶解的原理将工件加工成形的一种特种加工方法。
电解加工中的电极反应标准电极电位的高低决定在一定条件下对应金属离子参与电极反应的顺序。
电解加工工艺需考虑生产率、加工精度和表面质量三个方面。
(1)生产率电解加工的生产率以单位时间去除的金属体积或质量衡量。
电解加工

前言随着高精度复杂零件的不断出现,传统的加工方法越来越难满足工程上的需要。
从而特种加工方法产生了。
电解加工作为先进制造技术中的一支重要方面军,在制造业中发挥着重要的作用。
它对难加工的材料可以以柔克刚,对形状复杂的零件可以一次成型,并以表面质量好、生产率高、无工具损耗、无切削应力等优点。
我国最早研究并成功应用电解加工技术是原兵器工业部西安昆仑机械厂的深孔和膛线加工。
从1958年建立第一个研究基地至1965年全国首届电解加工学术会议召开,电解加工在航空、航海、航天及部分民用工业迅速推广。
20世纪70年代进入“爬坡”阶段,为了解决加工精度的问题,国内外先后提出混气电解加工、钝性电解液、工频脉冲电流、振动进给等工艺措施。
90年代后,华南理工大学在近代功率电子技术发展基础上研究的高频窄脉冲电流电解加工电源,进一步强化了电解加工系统的“非线形”。
西安昆仑机械厂和西安工业学院联合研制的CNC同步控制电解加工参数和阴极运动轨迹解决了大缠角混合膛线的加工难问题。
但是由于加工间隙的电场、流场、磁场及阴极溶解动力学因素的交互影响,电解加工过程十分复杂,阻碍着该项技术想纵深发展,比如对其过程的监测和控制非常困难,迄今为止,除了在个别应用对象上有所突破外,还没有通过的在线直接测量加工间隙的有效手段。
不均匀的间隙分布使工具阴极设计成为一项难度很大的工作,在对新的加工对象进行阴极研制的过程中往往要对阴极进行多次修正。
此外,从绿色制造的角度,电解加工产生的大量产物和废液需要处理。
随着21世纪信息、生物、微纳技术的发展及其对制造技术不断增长的需求,微细加工将成为制造相应装备的重要手段,电解加工进行材料去除是以离子溶解的形式进行的,这种去除方式使得电解加工具有微细加工的可能。
目前国内外制造业均十分关注微细电化学加工的发展,将电解加工高速去除金属的理念用到传统电化学过程中,是促进该项技术进步的有效途径,微细电化学加工就不仅仅指静态条件下的掩膜电化学刻蚀了。
电解加工

电解加工班级:机械0811 姓名:徐锋电解加工电解加工是一种电化学加工,是继电火花加工之后发展较快,应用较广的一种特殊加工技术。
广泛应用于兵器、航空等工业部门的难切削加工材料的加工。
八十年代后,电解加工开始应用于油泵油嘴行业的泵体,喷油器体进油管路二孔交接处,柱塞套,油嘴盛油槽及其压力室喷孔交界处超声波电解的去毛刺加工上。
多年来的实践证明:电解加工工艺合理,先进,质量稳定,效率高。
一、电解加工原理及特点:电解加工是利用金属中含有的其他元素或杂质。
接触电解液后会形成许多“微电池”而放电,从而形成电化学腐蚀来去除工件材料的一种特殊加工方法。
加工时以工件为阳极,工具电极为阴极。
在两极之间狭窄的间隙内强迫电解液通过,与此同时,两极之间施加直流电压,由于电化学反应的作用,靠近电极导电端的工件毛刺及棱角处电流密度最高,从而毛刺很快被除掉,棱边也形成圆角。
一般电解加工常用的电解质是NaC1,NaNO3,溶液,亦用NaOH,Na2SO4 溶液,使电解质形成14%一18%的水溶液。
当加工材料时,被加工材料接正极,工具电极接于负极。
化学反应如下:工件正极:工件负极:电解加工的基本原理结合实际的生产状况,有下述特点:(1)、不受材料硬度限制,适用于热处理后的零件。
(2)、保证零件原有精度不变,适用于精加工后的零件。
(3)、工具电极不易损耗。
(4)、可多件同时加工,实行批量生产。
(5)、选择性去毛刺,适用于形状复杂的深狭窄处,交叉孔等难以去除的内毛刺。
(6)、加工电压DC6 V一24 V。
二、加工工艺:电解加工工艺包括:加工间隙的计算与控制、电解液与工艺参数的选择、阴极的设计与制造。
加工间隙:阳极与阴极的距离。
决定加工精度,是电解加工水平的表征。
加工间隙愈小,愈均匀,加工精度愈高。
早期:加工间隙为0.2~0.5mm;目前:加工间隙为0.05~0.1mm;间隙的影响因素:①被加工材料的性质。
材料不同,体积电化当量不同,同时阳极溶解的电流效率也变化。
- 1、下载文档前请自行甄别文档内容的完整性,平台不提供额外的编辑、内容补充、找答案等附加服务。
- 2、"仅部分预览"的文档,不可在线预览部分如存在完整性等问题,可反馈申请退款(可完整预览的文档不适用该条件!)。
- 3、如文档侵犯您的权益,请联系客服反馈,我们会尽快为您处理(人工客服工作时间:9:00-18:30)。
一:电解加工机床:是利用金属在电解液中发生电化学阳极溶解的原理将工件加工成形的一种特种加工方法。
加工时,工件接直流电源的正极,工具接负极,两极之间保持较小的间隙。
电解液从极间间隙中流过,使两极之间形成导电通路,并在电源电压下产生电流,从而形成电化学阳极溶解。
随着工具相对工件不断进给,工件金属不断被电解,电解产物不断被电解液冲走,最终两极间各处的间隙趋于一致,工件表面形成与工具工作面基本相似的形状。
二:电解加工设备:是一个完整的配套系统,由机床、电源、输液系统以及控制系统四大部分组成,机床是设备的主体,进行电解加工的场域,其主要功能除安装、定位工件和工具电极并按需要送进工具电极外,还必须将加工电流和电解液输送到加工区。
本次设计的主要内容是完成该机床的机械本体、主传动系统、主轴系统、引电系统的三维造型设计。
并使电源以一定的方式提供工件发生阳极溶解需要的电能;电解液系统存储电解液。
三:机床在进行总体设计时:必须以该设备的工作条件,加工对象的特点和加工的基本要求作为总体设计的基础和出发点;同时要确定机床主要部分的功能、组成、基本方案和相互间的匹配关系,然后,一次为基础进行总体布局。
根据设计任务书的要求选定设备的总体规格、性能、技术要求;最后定出总体方案。
由于电解设备各部分的相对独立性较大且专业领域各异,因此总体设计对于确保设备的整体性能和水平是极为重要的一环,特别是各组成部分之间的相互匹配、协调尤为重要,这是电解加工设备设计的独特之处。
电解加工机床的各部分的选用是综合考虑了设计任务书提出的加工条件和工艺参数以及加工对象的精度、粗糙度、效率的要求之后确定的。
有些参数定量的计算主要是根据经验公式估算的,其中的经验系数均选自国内外先进机床的设计数据,有些已在设计过程及验算过程中被证实。
四设计内容:1)主轴系统设计:步进电机、轴承座、主轴、电刷等组成。
因此,主轴系统的设计主要是完成驱动主轴运动的电机的选型,减速器、联轴器的确定以及丝杠、轴承、导轨等主要零部件的设计计算及校核。
2)工作台设计:。