作业分析-人机
人机联合作业分析表
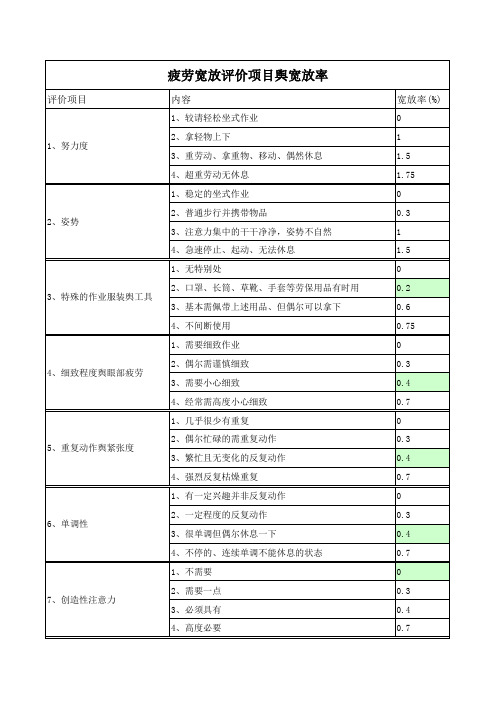
8、对责任舆危险注意度 9、环境 10、噪音 11、温度 12、光照度 13、地面
1、不需要 2、对他人的安全及责任需普通程度的留意 3、对自身及他人的安全责任需特别注意 4、超级危险作业需特别注意自己及他人安全 1、环境清洁 2、有少许烟尘和异味的污染 3、烟、污物、异气、尘灰很多 4、上述污染非常严重 1、没有噪音 2、少许噪音 3、有噪音,但有间隙 4、持续不断强噪音 1、有空调温度正常 2、普通的温度变化 3、有温度变化很大 4、温度变化极大,对人不利 1、光照度在标准之间 2、正常一般照明水平 3、光线弱或过强,影响人的情绪 4、非常弱的光线并且明暗变化剧烈,严重影响情绪 1、地面光洁 2、普通状态地面 3、潮湿不干净 4、潮湿容易滑倒的地面
疲劳宽放评价项目舆宽放率
评价项目 1、努力度 2、姿势 3、特殊的作业服装舆工具 4、细致程度舆眼部疲劳 5、重复动作舆紧张度 6、单调性 7、创造性注意力
内容 1、较请轻松坐式作业 2、拿轻物上下 3、重劳动、拿重物、移动、偶然休息 4、超重劳动无休息 1、稳定的坐式作业 2、普通步行并携带物品 3、注意力集中的干干净净,姿势不自然 4、急速停止、起动、无法休息 1、无特别处 2、口罩、长筒、草靴、手套等劳保用品有时用 3、基本需佩带上述用品、但偶尔可以拿下 4、不间断使用 1、需要细致作业 2、偶尔需谨慎细致 3、需要小心细致 4、经常需高度小心细致 1、几乎很少有重复 2、偶尔忙碌的需重复动作 3、繁忙且无变化的反复动作 4、强烈反复枯燥重复 1、有一定兴趣并非反复动作 2、一定程度的反复动作 3、很单调但偶尔休息一下 4、不停的、连续单调不能休息的状态 1、不需要 2、需要一点 3、必须具有 4、高度必要
人机工程学双手作业

—双手作业分析
学院:现代设计艺术学院 学号: 姓名:
人机工程学
双手作业分析图的作用 双手作业分析图以双手操作为对象,采用 标准流程图符号来记录其动作,表示其关 系,并可指导作业者如何有效地运用双手, 从事生产性的工作,提供一种新的动作观 念,找出一种新的改善途径。
人机工程学
双手作业分析图 图例
右 刷卡
左 拿盘放桌
人机工程学
双手作业分析图 改良
改良后放学食堂吃饭过程 (15步)
右 右 拿卡准备 左 放盘打菜 右 刷卡 左 拿盘放桌 右 拿筷子勺子 左 勺子吃饭 右 筷子挑辣椒 右 放下筷子 左 抬盘走人
刷卡打饭
左 抬盘子 左 放盘打菜 右 手作业 双手作业
人机工程学
双手作业分析图
放学食堂吃饭过程
右 右 右 拿卡准备
(19步) 左 放盘打菜 右 刷卡 左 拿盘 左 放盘打菜 右 右 拿筷子 掰开筷子 拿筷子挑辣椒
刷卡打饭
抬盘子
右 放盘打菜 右 拿盘换手 左 拿盘 右 刷卡 右 拿筷子开始吃饭 右 放下筷子 左 抬盘走人
人机操作分析

人机操作分析区别于流水线作业的另一种作业方式——部组加工作业,常存在着:几台机器能满足生产的需求?一个人能够同时看管几台机器?怎样来提升机器和人的使用率等问题。
对此,我们常用操作分析来进行处理。
操作分析可分为:①人机操作分析;②联合操作分析;③双手操作分析。
我们重点学习在一个看管一台或多台机器情况下的操作分析,即人机操作分析。
人机操作分析的步骤:●首先要明确作业员及机器作业周期的内容●必须明确这些作业的先后顺序及同时关系●测定各作业所需要的时间●寻找作业员与机器的作业在何处同时开始或同时完成,并考虑其先后顺序及同时关系,根据现状绘制人机操作分析图●注意作业员,机器的等待时间,并考虑其先后顺序及同时关系,设法改变作业顺序以减少其等待时间●根据改变的作业顺序作出新的人机操作分析图,再详细予以探讨改善的对策,并预估其改善效果过一定的时间,从机器中取出模具,并从模具中取出成品,然后再装入液体材料……一直反复的作业。
目前,因机器的利用率不高,而未能达成预期的生产量,部如何加以改善。
首先明确作业员与机器的作业内容及同时关系。
A]作业员的作业●把液体材料装入模具 50DM●把模具放进机器中 16DM●开动机器 14DM●等待机器加工●停止机器 10DM●从机器中取出模具 12DM●从模具中取出成品 18DMB]机器的作业●机器中装入模具 16DM●开动机器 14DM●加工 90DM●停机 10DM●取出模具 12DM●等待放入模具C]作业员与机器的同时关系(作业员)(机器)把模具放进机器装入模具开动机器开动机器停止机器停机从机器中取出模具取出模具根据以上的资料,首先决定同时开始的作业,在此以“放入模具”作为整个操作周期的起点。
然后以作业的先后顺序及同时关系绘图:人机操作分析用纸现状的周期时间为210DM,机器等待为68DM,因此,一周期中的机器利用率=(周期时间-等待时间)/周期时间=(210-68)/210=67.6%为减少作业员及机器的“等待”,检讨一下是否可以利用“机器加工”的这段时间。
人机作业分析

人机作业分析特征:
(1)一般用于分析1人操作1台机器或1人操作多台 机器的情况。
(2)人机作业分析借助于人机作业图进行分析。
人机作业分析的主要用途
(1)发现影响人-机作业效率的原因。人-机作业时,若人 与机器的相互关系不协调,人-机分析图能一目了然, 发现产生无效时间的原因。
(2)判断操作者能够同时操作机器的台数,即确定1名操 作者可能操作几台机器,充分发挥闲余能力的作用。
人机作业分析检查与改善表:
项目
内容
1.是否有替代作业可达 到同样目的 2.作业
省略 减轻 合并
3.移动 省略 减轻 组合
1.明确作业目的; 2.其它替代手段;
1.明确有无不必要的东西; 2.变形顺序; 3.使用不同的设备; 4.改变配置(布置); 5.产品设计变更; 6.作业员培训;
1.去除某些作业; 2.改变保管场地; 3.改变配置; 4.改变设备; 5.改变作业程序; 6.设置皮带;
1.材料自动供料; 2.加工的自动化; 3.加工完成后自动卸料; 4.加工完成及产品不良或材料不良时 的自动处理; 5.改善操作者与机械的时间关系;
Check 说明
人机作业分析检查与改善表:
项目
内容
7.机械作业时间的缩短 8.提高械的运转率
1.改良工程; 2.送良提速及高速运转;
1.增加人均数; 2.新型号设备的使用; 3.机械自动运转时间内的作业准备;
序号
12 14 16 18 20
22 24 26 28
30 32 34 36 38 40 42
Check 说明
人机作业分析检查与改善表:
项目
内容
4.检查 省略 减轻 组合
5.等待可否省略
人机操作-分析

移开铣成件
在面板上用模板量深度,成品 放入箱内,取新铸件置机旁
锉锐边,用压缩空气清洁
用压缩空气清洁机器,装铸 件,开动机器精铣
精铣第二面
空闲
人
机
时间(min)
空闲
单独工作
空闲
共同工作
项目
现行方法
改良方法
节省
工作时间 (min)
人
1.2
1.2
--
机
0.8
0.8
--
空闲时间 (min)
人
0.8
3
乙
3
0
3
机
3
0
3
周程时间min
9
6
3
利用率
甲
67%
100%
33%
乙
67%
100%
33%
机
67%
100%
33%
3
运板1
3
装板2
3
0.2
0.6
机
1.2
0.6
0.6
周程时间(min)
2.0
1.4
0.6
利用率
人
60%
86%
26%
机
40%
57%
17%
工作:铣平面 图号:B239/1 产品:B239铸件 机器:4号立铣 速度:80r/min 走刀量:380mm/min 制作: 通力达 日期: 2000/08/18
1.25
工作时间
1.25
2.5
整个周期
3.75
工作 内容
利用率
1.25/3.75=33%
2.5/3.75=67%
比较项目
人的工作(min)
人机联合作业分析

比率 作业 右手次数
符号 比率
TTL
符号
案例
工作:检查轴的长度及装入套筒 开始:双手空时--用品在台上 结束:装好一只放在旁边
左手
至轴
1
拿起一轴
1
检
验 带轴至尺 2
等待测定长度 1
放下装毕之轴及 2 套筒
右手
1
至尺
1 拿起尺
2
带尺至轴
1 测定长度
2 尺放下
3
至套筒
3 拿起一套筒
4
带套筒回原位
4 将套筒装轴上
作业名称
人机联合作业分析表
研究者
No. 人的作业 1
人作业时间 时间min 机器作业 0.1
2
0.2
3
0.3
4
0.4
5
0.5
6
0.6
7
0.7
8
0.8
9
0.9
10
1
11
1.1
12 13 统计分析
人 机
生产周期时间
1.2 1.2
工作时间 空闲时间 利用率
机作业时间
案例
案例
作业名称: 车削零件 编号:
2
空闲时间 2
1.3
利用率 1.3 / 3.3 2 / 3.3 6
日期:
.
研究者:
.
机
.5
空闲
车削
2
空闲 .5
利用率 1.3 / 3.3 39 % 2 / 3.3 61 %
作业名称
双手作业分析表
研究者
No. 左手作业 1
2
3
4
5
6
7
8
9
1.2人机作业图实例分析
依作业程序由上而下记录。如用
或
表示人或机器进行工
作,用
表示人或机器空闲,图形的长短由工作或空闲的时间而定,
并在旁边注明每一操作单元的内容
• 只绘出一个操作周程
3. 统计部分:统计内容包括操作周程,人、机在一周程内的工作时间和空 闲时间,以及人和机器时间的利用率
1.2人机作业图
作业名称:车削零件
开始动作:装夹零件
LM N1
L W
•N1:一个工人操作机器的最低数 •L:装卸工件时间 •M:机器加工时间 •W:工人由一台机器走到另一台机器所需时间 •L+W:为工人操作机器所需时间 •L+M:为一台机器的作业周期
1.2闲余能量分析
作业名称:车削零件
开始动作:装夹零件
人
装夹工件
0.5
编号:
图号: 日期:
结束动作:
车削
0.5
空闲
0.8
车削
1.5
空闲时间 0.2min 0.8min
利用率 92.86% 71.73%
1.2人机作业图实例分析
针对某具体工序的改进
人 装夹工件
空闲 86.4
卸下工件 10
统 计
人
周程 106.4s
机
106.4s
机 空闲 10
车削 86.4
空闲 10
工作时间 20s
空闲时间 86.4s
利用率 18.80﹪
86.4s
20s
81.20﹪
1.2人机作业图实例分析
为了提高人机的操作时间的利用率,我们设计了一人操作三台机床,作业 图如下:
人
装车床1#10s 卸车床2#10s 装车床2#10s
卸车床3#10s 装车床3#10s 空闲46.4s 卸车床1#10s
人机作业分析
1"
1"
1"
1"
裝下一PC面板之透鏡 1"
統計 周期 空閑時間
工作時間
人 5"
0"
5"
機 5"
1"
4"
機 1" 等待
4" 熱熔
利用率 100% 80%
三﹑联合操作分析
在生产现场中,常有两个或两个以上的操作人员同 时对一台设备(或一项工作)进行操作,称为联合 操作作业。
联合操作作业分析常采用“联合操作分析图”。
工作時間 5" 4"
1" 等待 1" 等待 利用率 55.6% 44.4%
二﹑人机操作分析-人机操作图
动作同步进行
改善后﹕ 人机利用率 分别为﹕ 100% 和80%
機種名稱﹕grampus 工站﹕熱熔站 測量日期﹕3/26
人 放面板于治具上
檢查上一產品
放上一產品 取下一PC面板
工段﹕裝配段 測量人﹕ 版本﹕B
机械有闲置现象时 缩短作业者单独作业的时间 改善手工作业时间或使手工作业自动化。
作业者和机械都有等待现象 考虑改变作业顺序;
前两项改善着眼点也可考虑。
作业者和机械几乎没有等待现象
是否有缩短各段作业时间的可能
二﹑人机操作分析-人机操作图
工作任务:PC面板透镜 热熔。
开始:从流水线上取面板。 结束:热熔后放回流水线。
一﹑人机配合法概念
3.意義 以图表的方式,记录操作者与一部机 器或多部机器之操作关系,并以此记录来做进 一步的分析与改善。
4.应用范围 (1)一人操作一部机器或多部机器。 (2)数人操作1部机器或多部机器。 (3)数人操作一共同之工作。
人机操作分析
目
一、什么是人机操作分析 二、人机操作分析的特征和用途
录
三、人机操作分析的主要过程 四、人机操作分析的实例
什么是人机操作分析 人机操作分析是应用于机械作业的一种最常用的
分析技术,通过对某一项作业的现场观察,记录操作 者和机器设备在同一时间内的工作情况,并加以分析, 寻求合理的操作方法,是人和机器的配合更加协调, 以充分发挥人和机器的效率的技术。
人机操作分析通过人机操作图进行。人机操作图描述 了在机器的工作过程中,在一个操作周期 ( 加工完一 个零件的整个过程称为一个操作周期或周程 ) 内机器 操作与工人操作的相互关系,可将生产过程中工人操 作的手动时间和机器的机动时间清楚地显示出来。
目的:充分利用机器与操作工人的闲余时间,提高生产力, 降低成本以及提高工人的收入。
人机作业分析的主要过程
(1)观察和记录操作者与机器设备在一个作业周期 (周 程)内各自的操作步骤和操作内容。
(2) 用作业测定法确定这些操作活动的时间,按照操 作者和机器设备操作活动的时间配合关系,在作业分 析图表中清晰地表示出来; (3) 运用工作简化和合并交叉的原则,研究改进操作 的各种可能性,提出切实可行的改进方案。 (4) 绘出新的操作分析图表。新的操作方法经过现场 验证以后,即应用于生产,并对改进的效果进行评价。
人机作业的案例分析
•
下图为改进后的记录图,由图可见,重新安排工作后,不需增加设备和 工具,仅在2min内就节省了工时0.64min,提高工效32%。
人机作业案例分析
人机作业分析的特征和用途
(3) 判定操作者和机器两方面哪一方对提高工效更为 有利。
实验二 人机作业分析报告
《基础工业工程》实验报告
学院
班级
姓名
学号
温州大学机电工程学院制
实验编号:132114501502
实验二
1实验目的
2现行方法人机作业分析图
时间(min)
人
车床1
车床2
图1-1现行人机作业分析图
代表工作时间
代表空闲时间
3改良方法人机作业分析图
时间(min)
人
图1-2改良方法人机作业分析图
(2)怎样分析人机操作过程中的闲余能力分析?企业中能否达到人机利用率为100%的情况?为什么?
代表工作时间
代表空闲时间
4对比分析
列出现行方法与改良方法统计比较表,并分析改进前后的人、机利用情况。
表1-3现行方法与改良方法统计比较表
项目
现行方法
改良方法
节省
工作时间/min
人
机1
机2
空闲时间/min
人
机1
机2
周程时间/min
利用率(%)
人
机1
机2
5思考题
(1)一名操作者操作一台设备与同时操作多台设备,人机操作图的绘制有什么区别和联系?
- 1、下载文档前请自行甄别文档内容的完整性,平台不提供额外的编辑、内容补充、找答案等附加服务。
- 2、"仅部分预览"的文档,不可在线预览部分如存在完整性等问题,可反馈申请退款(可完整预览的文档不适用该条件!)。
- 3、如文档侵犯您的权益,请联系客服反馈,我们会尽快为您处理(人工客服工作时间:9:00-18:30)。
5.1 5.2 5.3 5.4 作业分析概述 人—机作业分析 联合作业分析 双手作业分析(略)
第一节
作业分析概述
一、作业分析(操作分析)
作业分析:对某道工序中人、机、物的研究,目的是 工作轻松、布置合理、缩短工时。 与程序分析的区别:
分析对象 分析内容 分析基本单元 分析的目的 分析的范围 分析的时间
方 法: 改良方法 机器号码: B3 日 机器 时间 布轮右边 当柱螺栓通过布 轮右边的进料管 即被抛光 期: .
30
30
30
时间单位1=1/1000min 统 工人 空闲时间 工作时间 周 程 利用率 0 30 布轮左边 0 30 计 机 器 布轮右边 0 30
30 / 30 100%
30
30 / 30 100%
去毛刺并检查尺寸(1#)0.5 0.2 空闲 0.3 卸车床1# 空闲 0.3 周程 工作时间 空闲时间 2.6 0.2 2.8 统 人 车床1# 2.8 2 0.8 计 车床2# 2.8 2 0.8
比,工作周程(均为 2.8mi 0.5 车削 空闲 0.5 如果此时工人的空闲时间不足 0.5 n)并未改变,但第二次改 0.3 (<1.3min ), 进方法完成了两件,即单件 空闲 0.8 怎样改进?可以增加其他工作。 0.5 加工时间仅为 1.4min,总产 # 车削 此例说明: 去毛刺并检查尺寸(2 ) 0.5 量增加了50%。 2
改善无止境!
车削
1.5
利用率 2.6/2.8=95% 2/2.8=71% 2/2.8=71%
图5-6 车削时的人机作业图(第二次改进方法)
主要用途:
1.找出影响人机作业效率的因素。 2.确定操作者(单人)能同时操作的机器台数。 3.寻求操作者的安全性和舒适性。
二、人机分析的主要工具
作业分析图: 反映人机工作时间关系的图表。 构成: 1.表头——具体内容视情况而定(建议用excel) 2.图表——画法:
①时间:用适当的“线段”表示(min/cm) ②人机分开记录(一般左右分开)。 空闲用: ③工作状态表示: 工作用:
操作者 移开铣成件以压缩空气 清洗之 量面板深度
问题:铣床的利用 进给量f 铣削深度a 时间利用率/% 83% 改进:重新安排工作后,不 23% 0.64 。 周程时间/min 1.36 率仅为 40% 需增加设备和工具,在 2min 分析:工人的对夹具的操作必须 技术等级 文化程度 0.8 机 工作时间/min 空闲时间/min 0.56 内就节省了工时 0.64 0.64min, 在机床停止时进行,但用压缩空 改进后的 审定者 时间利用率/% 59% 19% 提高工效 32%。 气清洁零件及检验工件的深度等 记录图 改进方法 时间 是否也要机床停止? (min) 机器 机器 操作者
0.2 0.4 移开铣成件 用压缩空气吹净夹具装毛坯 原因:当工人操作 开动铣削 0.6 时,机床停止工作 0.8 锉去毛刺,吹净 (机床自动切削时, 在铣床台上用样板量深度 1.0 工人则无事做) 成品入箱,取毛坯至台面 1.2 1.4 1.6 1.8 2.0
锉锐边,压缩空气清洗之 放入箱内,取新铸件 压缩空气清洗机器 将铸件夹上夹头开机床 进刀
周 程 利用率
53 / 53 100%
14 / 53 26%
2.分析和改进
3.建立新方法
方法改进:安装一个如下图5-3所示的简单夹具。 改进后的人机作业图如下图5-4。
本题的关键:
1.储藏合、2.导管、3.螺栓、4.操作者、 5.电机、6.布轮、7.供给合
பைடு நூலகம்
手段的改进
作业名称: 打光柱螺栓 机器名称: 布 轮 操 作 者: . 研 究 者: . 工人 操作者 双手各拣起一个 柱螺栓,插入进 料管并放手 时间 布轮左边 当柱螺栓通过布 轮左边的进料管 即被抛光
问:为什么布轮右边 时间 布轮左边 操作者 完全没有被利用? 答:因为操作者用双 握紧柱螺栓并把 16 空闲 一端对着布轮 手握着螺栓进行打 磨,只需用一边。
碰着布轮旋转柱 问:为什么布轮左边有那 螺栓 么多空闲时间? 答:因为工人要进行三次 调整柱螺栓另一 端对着布轮 操作:握紧螺栓一端对着 布轮、调换螺栓的另一端 碰着布轮旋转柱 再对着布轮、处理打光的 螺栓 螺栓。此三次动作时,机 处理打光过的柱 器空闲着。 螺栓 7 打光柱螺栓
机的空闲时间多!
16
7 空闲 53
18
空闲
7 5
打光柱螺栓 空闲 代表空闲 统 工人 0 53 53
7 5 时间单位1=1/1000min 计 机 布轮左边 39 14 53 器 布轮右边 53 0 53 0
代表工作
问:有无改进的方法? 答:若采用夹具自动进 料,则省去用人手握(一 种夹具)螺栓,可节省对 空闲时间 调螺栓时间和人力,同时 工作时间 将右边的布轮利用。
空闲
空闲 1.5 0.3 2 0.3
卸下工件 统
计
周程 空闲时间 利用率 工作时 注意:判断一个操作者能否多操作一台设备 1.3 46% 2.8 1.3 1.5 人 2.8 的前提条件是: 2 71% 2.8 2 0.8 工人的空闲时间>一台设备的循环时间。 机 2.8
3.进一步改进
作业名称: 车削零件 研 究 者: . 人 装车床1# 卸车床2 # 装车床2# . . 为改进方法,与图 5-6相 车床2# 车床1# 编号: 日期:
0.5 统 计 工作时 1.3 2
人 机
图5-5
改进后的车削人机作业 进一步的改善:
作业名称: 车削零件 开始动作: 装夹零件 人 编号:
装夹工件 去毛刺并检查尺寸
0.5 0.5
一台机床时工人操作的时间为 问:是否增加了设备和工 图号: 日期: . 1.3min,而目前工人有1.5min 具? 的空闲时间, 结束动作: 卸下零件 研究者: . 没有!只是重新编排了机器 1.5(空闲) > 1.3(工作) 与手工操作的时间。 机 可以增加一台机床。 问:那否进一步改善? 空闲 0.5 答:可以。 通过重排,周程由3.3分钟缩 短为2.8 分钟(人由2分钟空 车削 闲时间变为1.5分钟空闲时 间),提高了人机工效。
本题的关键:
合理排序
应用2.发现影响人机效率的重要原因 例. 打光发动机螺栓
打光用于飞机发动机上的螺栓。 原方法是:操 作者从工作台上的贮藏箱中拿起一个螺栓,用手握 住螺栓的一端靠近布轮(布轮旋转着),用手旋转 去掉毛刺,然后再换螺栓的另一头去掉毛刺。打光 后的螺栓被扔到放在桌上右边贮藏盒内,试绘制人 机作业图并进行改进。
机
改进后的人机作业图如图 空闲 0.5 5-6。
车削
的。
解:
1.绘制人机作业图(图55), 2.用“5W1H”提问技术 和“ECRS”原则进行分 析
卸下工件 去毛刺并检查尺寸 周程 3.3 3.3
2 0.3
人的空闲时间 2 多,利用率仅 空闲 为39%
0.5 空闲时间 2 1.3 利用率 1 . 3 / 3 . 3 39 % 2 / 3 . 3 61 %
应用3.判断操作者同时操作机器的台数 例5-2(p96)某工人操作车床车削工件作业程序及时间值为:
作业名称: 车削零件 装夹工件:0.5min, 开始动作: 装夹零件 车削:2.0min, 人 卸下零件:0.3min, 装夹零件 去毛刺并检查尺寸: 0.5 0.5min, 该车床自动加工。试绘制问:为什么去毛刺、 检查尺寸要在机器停 出此作业的人机作业图,止时做? 空闲 并对其进行改进。 答:过去一直是这样
30
30 / 30 100%
30
图5-4 打光螺栓的人机作业图(改造后)
4.实施:
•改进前每小时只生产: •改进后每小时生产: •工作效率提高:
60 1132件/h 53 / 1000
60 2 4000件 / h 30 / 1000
4000 1132 2.5倍 1132
效果: 减少了空闲时间,提高工效。 工人工作时安全、轻松。
3.统计——人、机的工作及空闲的时间。
具体请看……
三、人—机作业分析图的应用
工作部门 产品名称 作业名称 机器名称 操作者 制表者 现行方法 表号 B239铸件 精铣第二面 速度v 年龄 人
p
应用1.考察人机作业中协调性? 例5-1(p95)在立铣床上精铣铸件平面的人-机操作记录图
统计项目 周程时间/min 工作时间/min 空闲时间/min 现行的 改进的 节省效果 2.0 1.2 0.8 60% 2.0 0.8 1.2 40% 1.36 1.12 0.24 0.64 0.08 0.56
问:能否进行改进? 编号: 答:可以, 图号: 日期: . 机床车削时间为 2分钟, 结束动作: 卸下零件 研究者: . 去毛刺并检查用0.5分钟 时间
(min) 0.2 0.4 0.6 0.8 1.0 1.2 1.4 1.6 1.8 2.0 2.2 2.4 2.6 2.8 3.0
0.5(人)<2(机)
解:
1. 首先绘出原方法的人机作业图(图5-2)
图 打光螺栓的人 机作业图 (原方法)
作业名称: 打光柱螺栓 机器名称: 布 轮 操 作 者: . 研 究 者: . 人
方 法: 现行方法 机器号码: B3 问题:右边布轮没用;左 日 机器 时间 期:
边布轮利用率也仅 14/53=2 . 6%。
布轮右边
程序分析 零部件(物) 工艺流程 工序 工序的流畅 一条线 之前
作业分析 人、机、物 人机的协调 操作 工时的节省 一个点(面) 程序分析之后
二、分类
人机作业分析
(一人)
作业分析
联合作业分析
(多人)
双手作业分析
(左手和右手)
第二节 人—机作业分析