ⅢJD2000型-φ2200氨合成塔
氨合成双塔串并联技术应用总结

氨合成双塔串并联技术应用总结(河北东光化工有限责任公司徐希江、黄志宏)摘要:河北东光化工有限公司对700t/d氨合成系统进行增产节能改造,采用南京国昌化工科技有限公司“氨合成双塔串并联工艺技术”,改造后装置产能增加以及节能降耗效果明显。
本文介绍了该项目改造概况、工艺改造流程和运行情况。
关键词:氨合成技术改造串并联应用1概况我国国民经济的发展表明,化肥在农业中所占的地位越来越重要,需求量也逐渐增加,很多化肥企业正在扩大或准备扩大生产能力,以满足市场需求和提高企业市场竞争力。
河北东光化工有限责任公司(以下简称东光化工)目前一套2009年7月投产的φ2000氨合成系统生产能力为日产700吨,2012年初开始筹备对该系统挖掘生产潜力、通过增产进一步实现节能降耗,最终形成年产24万吨合成氨能力。
2012年4月,东光化工经充分调研,选择采用南京国昌化工科技有限公司(以下简称国昌公司)开发的“氨合成双塔串并联工艺技术”(以下简称“串并联工艺”),对原有φ2000氨合成系统进行增产节能改造,即在原有氨合成塔后,合成废锅前串入一台GC型φ2000轴径向氨合成塔,原来各设备的工艺条件基本不变。
改造仅增加一台氨合成塔和一台循环机,其它设备均利用原有合成系统的设备,体现了投资省、建设周期短、见效快、占地面积少的特点。
并委托国昌公司进行改造部分的工程设计和GC 型轴径向氨合成塔内件的设计制造。
2串并联工艺流程串并联工艺流程如图1所示:改造后整个系统中需要增加10个阀门V1-10,2个8字盲板。
(1)串联运行合成塔部分流程简述循环机油分(S1001)出口管线分三路,分别进入1#合成塔环隙冷却塔壁、2#合成塔环隙冷却塔壁(新增PG1101)、塔前换热器与出塔气换热。
塔前换热器冷气出口进入1#合成塔反应出口~300℃进入2#合成塔继续反应,~350℃出口进入废锅副产蒸汽。
串联流程阀门的控制:阀门V1、V2、V3、V5打开,V4、V6-10关闭,盲板1关闭,盲板2打开。
DN1600多层直接冷激式氨合成塔结构设计要点

1绪论现今氨合成工艺在我国氮肥厂得到广泛的应用。
展望国内氨合成塔内件可以说种类繁多,绝大多数的氨厂合成操作压力为31.36MPa。
合成塔内件为传统的冷管型内件。
其中三套管、单根并流、双套管式内件占大多数。
此外,另有一批冷管改进型内件:比如ⅢJ型、YD型、NC型、轴径向、副产蒸汽式等。
塔内换热器大部分为列管式,还有少数为螺旋式、波纹板式。
小型氨厂大部分采用φ600、φ800直径塔。
日产合成氨达80t、100t、150t不等。
中型氨厂大多采用φ1000、φ1200直径塔。
高压筒体高度为13.5~16m。
日产氨200t 、250t、 290t不等。
传统型内件氨净值大部分为9%~12%之间,改进型内件在12%~16%之间。
合成塔,阻力降0.6~1.2MPa。
配置的余热回收装作吨氨副产蒸汽为600~800kg/t NH3压力为1.3~2.5MPa。
下面简单介绍两种内件:全冷激式内件全冷激式内件是一种在中小型氨厂推广使用的新型内件,它与传统内件(内冷式内件)有本质区别,将圆催化剂中的冷管取消,将一个大的催化剂反应床分割为若干个小的催化剂反应床,床层之间采取冷激换热的方式将反应热一直,以便将反应能继续进行下去。
冷激式内件是多层绝热、层间换热式内件中最简单的一种。
它与层间水冷式内件几乎同时应用与多种合成氨厂。
它具有结构简单,运行可靠的特点。
此种内件根据合成系统工作压力、催化剂活性温度、催化剂温区范围、反应热回收方式等因素以及要达到的氨净值来确定催化剂床的数量。
多层换热式内件具有三大特点:(1)多层绝热,层间换热。
用未反应的气体作为冷源,一方面将反应后的热气体热量移走;另一方面自身温度提高达到第一绝热床时的零米温度。
(2)催化剂筐采用径向型(3)宽温区催化剂对于整台合成塔,需设计和制造外壳,所设计的外壳具有一下特点:(1)球形封头结构成熟,使用材料较省,若采用锻件,则将增加一倍以上的重量。
(2)多层包扎筒体国内制造经验丰富。
氨合成塔吊装受力计算

氨合成塔吊装受力计算一、受力计算利用氨合成框架吊装氨合成塔,设计院给定了条件:1、指定吊点,且吊点处受力不得大于900KN;2、作用在框架的总垂直压力不得大于设备重量的1.2倍;3、要尽可能的减少框架的水平力,框架偏移量不得大于55㎜。
为此,采取如下措施:1、为了减轻吊装重量去掉合成塔大盖及螺栓,2、设备送尾到垂直状态。
1、计算重量P=(Q+g)·K·K1=(2200+400)×1.1×1.2=3432KNQ——去掉大盖后合成塔自重Q=2200KNg——吊装索具及假裙座重g=400KNK——动载系数不清取:K=1.1K1——不均衡系数K=1.22、抬头时垂直提升力XP′=P·Xc / n=3432×11.23 / 18.51=2082.2KNXc——重心到设备底大法兰距离Xc=11.2mn ——吊耳到设备底大法兰距离n=18.51m3、抬头时合力PH与滑车组P1·P4、P2·P3垂直平面的夹角,设备抬头时设备吊点在框架内1.8m处(见抬头吊装示意图)。
αH = tg-1[(1.84-1.4)/36.3 ] = 0.6945°4、合力PH = P′/2cosαH=2082.2/2cos0.6945°=1041.2KN5、滑车组P1、P2与合力的夹角φ1=φ2= tg-1(1.8/ 36.32+(1.84-1.4)2 )=2.8383°6、滑车组P2、P3与合力夹角φ4=φ3= tg-1(6.2/ 36.32+(1.84-1.4)2 )=9.69°7、滑车组受力a、P1=P2=PHs inφ4/sin(φ1+φ4)=1041.2s in9.69°/ s in(2.8383°+9.69°)=808KNb、P3=P4=PHs inφ2/sin(φ2+φ3)=1041.2s in2.8383°/ s in(2.8383°+9.69°)=238KN二、设备在1的位置时受力计算设备在1的位置即设备在进入框架3米处悬空吊起时的各处受力。
2200整体锻焊式氨合成塔设计解析

本次设计是在合成氨工业的基础上,对合成氨工业中的核心设备——氨合成塔进行设计。要求设计的氨合成塔,直径为2200毫米,筒体为整体锻焊式,内部换热器类型为固定管板式换热器。本次设计的最大特点为在常规设计的基础上筒体采用分析设计的方法,更好的节约了材料,降低了生产成本,且更加安全可靠。
关键词:氨;氨合成塔;工艺设计;结构设计;专题讨论
ABSTRACT
Ammonia is one of important inorganic chemical industry product,which occupyimportant position in national economy.And ammonia converter is the key equipment in the process of compound-ammonia production.
4.3内件材料选择及论证26
4.3.1内件用材的基本要求26
4.3.2内件各零部件材料的选择及论证27
4.3.3内件焊接材料的选择28
4.3.4保温铁皮材料的选择28
4.3.5保温层材料的选择28
第5章触媒的选择及要求30
5.1.2触媒的类型选择30
第6章电加热器设计36
6.1电加热器的作用及其结构36
6.1.1电加热器设计的一般要求36
6.1.2电加热器结构型式选择36
6.2电加热器材料的选择37
6.2.1电热元件材料的一般要求37
氨合成塔内件改造运行总结

氨合成塔内件改造运行总结徐严伟;王攀;樊安静;宋仁委【摘要】介绍了DN2500氨合成塔内件改造运行情况,改造后塔压差(含热交)、系统压差均有明显下降,分别达到0.46、1.11MPa,氨净值有所提高.正常工况下工艺对比显示,改造后节能降耗效果明显,达到了预期的目的.【期刊名称】《河南化工》【年(卷),期】2015(032)002【总页数】3页(P46-48)【关键词】氨合成塔;内件改造;运行情况【作者】徐严伟;王攀;樊安静;宋仁委【作者单位】河南心连心化肥有限公司,河南新乡453731;河南心连心化肥有限公司,河南新乡453731;河南心连心化肥有限公司,河南新乡453731;河南心连心化肥有限公司,河南新乡453731【正文语种】中文【中图分类】TQ050.7河南心连心化肥有限公司“24·40”项目(24万t/a合成氨,40万t/a尿素);氨合成工段DN2500氨合成塔已运行五年,2012年对合成塔内件进行过改造,虽有效果,但是合成塔压差(含热交)仍在上限0.99 MPa运行(指标<1.0 MPa),因此合成塔阻力还存在较大的问题[1]。
2014年7月公司对氨合成塔内件进行降阻改造,成功投运且运行节能降阻效果明显。
在氨合成系统中氮氢循环压缩机是主要的直接能耗来源,系统压力的高低、塔压差的大小等都直接影响着氨合成系统能耗的高低。
在氨合成辅助系统中,冰机、氮氢压缩机等是系统的间接能耗来源。
从能耗来源上分析循环机、氮氢压缩机都是由压力决定了其能耗的高低,因此在内件改造时选取降低系统压力、氨合成塔阻力及提高氨净值为主攻方向。
经过DN2500合成塔内三个催化剂床反应后的合成出口气体(温度445 ℃),通过合成塔下部换热器换热降温后(温度320 ℃)经管线进入合成系统废热锅炉,移出部分合成反应热后的气体(温度约200 ℃)进入塔外的热交换器管程中,与壳程的未反应气体进行换热后,从热交换器管程的下部出来,这时的反应气温度85 ℃,再进入软水加热器后,进入合成水冷却器,这时合成循环气的温度降至20 ℃,进入到冷交换器的壳程继续冷却,经过壳程冷却后的气体温度16 ℃,进入到下部冷交换器分氨段进行液氨的初级分离,分氨后气体再进入氨冷器进行进一步冷却,冷却后的气体出来后在管线中补入合成新鲜气,补入新鲜气后合成气(温度-5 ℃)后进入第二级氨分离器中进一步分离液氨,气体中氨含量为2.5%,氨分离器后气体再进入冷交换器管程与壳程气换热后(温度22 ℃),进入循环机系统。
20万吨合成氨项目节能流程方案选择
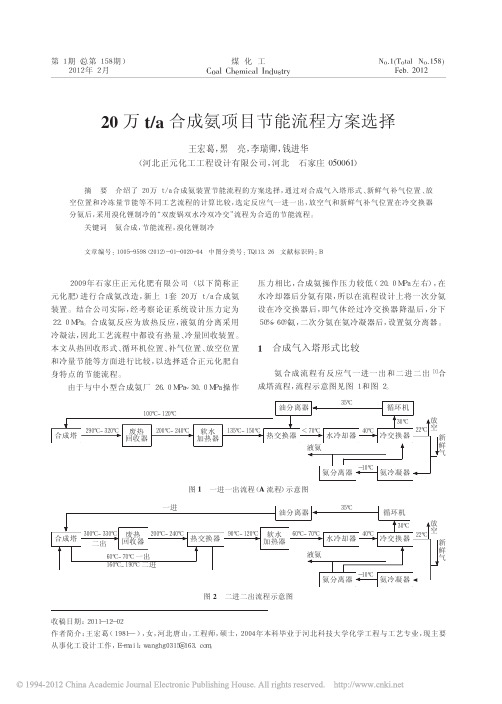
20万t/a 合成氨项目节能流程方案选择王宏葛,黑亮,李瑞卿,钱进华(河北正元化工工程设计有限公司,河北石家庄050061)摘要介绍了20万t/a合成氨装置节能流程的方案选择,通过对合成气入塔形式、新鲜气补气位置、放空位置和冷冻量节能等不同工艺流程的计算比较,选定反应气一进一出,放空气和新鲜气补气位置在冷交换器分氨后,采用溴化锂制冷的“双废锅双水冷双冷交”流程为合适的节能流程。
关键词氨合成,节能流程,溴化锂制冷文章编号:1005-9598(2012)-01-0020-04中图分类号:TQ113.26文献标识码:B收稿日期:2011-12-02作者简介:王宏葛(1981—),女,河北唐山,工程师,硕士,2004年本科毕业于河北科技大学化学工程与工艺专业,现主要从事化工设计工作,E-mail:wanghg0315@163.com。
2009年石家庄正元化肥有限公司(以下简称正元化肥)进行合成氨改造,新上1套20万t/a合成氨装置。
结合公司实际,经考察论证系统设计压力定为22.0MPa。
合成氨反应为放热反应,液氨的分离采用冷凝法,因此工艺流程中都设有热量、冷量回收装置。
本文从热回收形式、循环机位置、补气位置、放空位置和冷量节能等方面进行比较,以选择适合正元化肥自身特点的节能流程。
由于与中小型合成氨厂26.0MPa~30.0MPa操作压力相比,合成氨操作压力较低(20.0MPa左右),在水冷却器后分氨有限,所以在流程设计上将一次分氨设在冷交换器后,即气体经过冷交换器降温后,分下50%~60%氨,二次分氨在氨冷凝器后,设置氨分离器。
1合成气入塔形式比较氨合成流程有反应气一进一出和二进二出[1]合成塔流程,流程示意图见图1和图2。
第1期(总第158期)2012年2月煤化工Coal Chemical IndustryNo.1(Total No.158)Feb.2012合成塔废热回收器290℃~320℃软水加热器200℃~240℃热交换器135℃~150℃液氨<70℃冷交换器40℃22℃循环机油分离器35℃100℃~120℃氨分离器氨冷凝器-10℃水冷却器放空新鲜气图1一进一出流程(A 流程)示意图合成塔废热回收器300℃~330℃软水加热器200℃~240℃二出90℃~120℃液氨60℃~70℃冷交换器40℃22℃循环机油分离器35℃氨分离器氨冷凝器-10℃水冷却器放空新鲜气图2二进二出流程示意图30℃热交换器一进60℃~70℃一出160℃~190℃二进30℃2012年2月一进一出流程和二进二出流程的区别在于塔前预热器和软水加热器的位置及气体入塔次数不同。
Φ2000合成工段工艺操作规程
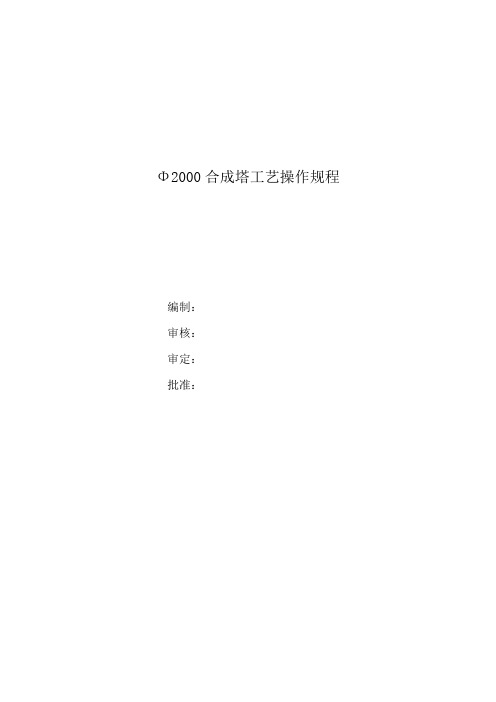
Φ2000合成塔工艺操作规程编制:审核:审定:批准:一、岗位任务合成工序的任务就是把经过净化的氢氮气,在适当的温度、压力条件下,借助催化剂的作用进行化合反应生产氨,经过冷凝分离后得到液氨产品。
二、工艺流程压缩六段来的精炼气经新鲜气阀进入新鲜气氨冷器冷却,冷却后的气体经新鲜气油分分离油水与循环气氨冷器出口冷却后的循环气混合进入氨分离器,分离氨后的气体进入冷交换器管内,冷却管件的热气提,同时温度提高到20℃以上进入透平机。
由透平机提压后的气体进入循环气油分,经油水分离后的气体分成两股:一股约10%的冷气由合成塔下部进入合成塔的内外筒环隙由下至上冷却塔壁后,与塔外热交换器加热的气体混合后进入冷管束,还有小部分冷气引入零米冷激分布器和冷气调温器;其余的冷气通过塔外热交换器预热后分成两股,一股约30—35%的气体由塔上部入塔后与塔壁环隙冷却气混合进入冷管束,通过冷管束与塔内触媒层换热提温后出来气体进入触媒床层表面;另一股约50—55%的气体由塔底入塔,在塔下部换热器内与出塔气体换热后,经中心管进入触媒床层表面,与冷管束出来的气体汇合,在上绝热层一段反应。
反应后的气体在冷气调温器中与塔外引入的少量冷气混合,进入上绝热层二段反应。
出上绝热层二段的气体进入混合分布器,再进分气筒,经过径向绝热段,径向通过段间冷却器。
从中部径向筐出来的气体,受支架套筒锥型筒的作用,沿径向筐与内同的环隙向下进入下绝热层,气体由圆周方向径向通过下绝热层流向径向筐中心的换热器,从换热器外壳进入换热器管间,由上折流而下,与进塔气体换热后温度降至310-350℃出塔。
出塔气经废热锅炉进热交换器管内,与管间进塔冷气换热后进入第一水冷器、第二水冷器,从第二水冷器出来的气体进入冷交换器的管间,在冷交换器管间与管内冷气体换热并分离氨后,进入循环气氨冷器进行冷却,冷却后的与新鲜气混合后进入氨分离器,继续下一轮循环。
三、工艺指标1、压力(表压、MPa)循环机出口压力≤31.4 系统升、降压速率≤0.5/min系统压差≤2.5 塔压差≤1.0脱氧水压力≥2.5 废热锅炉蒸汽压力≤4.0加氨压力≤2.2 输氨压力≤2.1气氨总管压力≤0.2 仪表空气压力≥0.52、温度(℃)热点温度零米温度 360—380 塔壁温度≤120主进气温度 180—200 二次出塔温度 310—350废锅出口气体温度 <250 水冷出口气体温度≤45氨冷出口气体温度 -10—-15 升降温速率 40—45/h3、气体成分循环气H2/N2 2.2—2.8 新鲜气H2含量 70—75%循环气CH4含量 12—15% 合成进口气NH3含量≤2.5%新鲜气微量CO含量≤15ppm 新鲜气微量CO2含量≤5ppm4、液位氨分液位 1/3—2/3 氨冷液位 1/3—2/3中锅液位 1/3—2/3 闪蒸槽液位 1/3—1/25、废热锅炉水质总固体 500—1000mg/l 总碱度 5—10mgN/l6、其他电炉功率 2500KW 电压 0—650V四、微量讯号五、系统主要设备1、氨合成塔 DN2000 H(净)=20000(1)外筒Φ2462×24187 容积63.5M³设计压力:31.4MPa 设计温度:筒体200ºC 底部锻件420ºC工作压力:≤31.4MPa 工作温度:筒体≤200ºC 底部出口≤420ºC(2)内件 IIIR2000型Φ2000 触煤框触煤容积41.3M³设计压力:1.0MPa 设计温度:530ºC工作温度: 工作温度200-485ºC 筒体≤200ºC(3)换热器换热面积::278M³设计压力:1.0MPa (外压) 工作温度:管程380ºC 壳程:480ºC2、合成直通或废热锅炉Φ1200 L=8428 换热面积:390M2设计压力:壳程4.0MPa 管程31:41.0MPa 设计温度:壳程队250ºC 管程399ºC工作压力:≤壳程4.0MPa 管程≤31:41.1MPa 工作温度:壳程85ºC /250ºC 管程:350ºC/ 250ºC3、热交换器 DN1400 H(净)=16000(1)外筒Φ1480/Φ1212×19675 容积18M³设计压力:31.4MPa 设计温度:筒体200ºC 顶部锻件300ºC工作压力:≤31.4MPa 工作温度:筒体≤200ºC 顶部锻件≤300ºC(2)内件Φ1182×18022 换热面积:2032M2设计压力:管程1.0MPa(外压) 壳程:0.2MPa(外压)工作温度: 壳程:40-195ºC 管程210-80ºC4、冷交换器 DN1400 H(净)=16000(1)外筒Φ1728/Φ1212×19800设计压力:31.4MPa 设计温度:50ºC工作压力:≤31.4MPa 工作温度:-15~40ºC(2)内件Φ1328×17790 换热面积:2032M2设计压力:管程1.0MPa(外压) 壳程:0.09MPa(外压) 设计温度:管程-8℃壳程:35℃5、16m3闪蒸槽 DN2000 L=5800mm设计压力:2.5MPa 设计温度:-19℃工作压力:0.2MPa 工作温度:-19~50℃6、氨冷器Φ1600/Φ1632 L=12264mm 换热面积:1000M2设计压力:管程31.4MPa 壳程:2.5MPa 设计温度:管程-19~30℃壳程:-19~40℃工作压力:管程:≤31.4MPa 壳程:0.2MPa工作温度:管程-3/-17℃壳程:-15/25℃7、补气氨冷器Φ1836/Φ1800 L=9702mm 换热面积:240M2设计压力:管程31.4MPa 壳程:2.5MPa 设计温度:管程40℃壳程:-15℃工作压力:管程:≤31.4MPa 壳程:0.2~0.6MPa 工作温度:管程40~8℃壳程:0℃8、合成油分 DN1400 H(净)=7500(1)外筒Φ1725/Φ1409×10426 容积:11.5M3设计压力:31.4MPa 设计温度:100ºC工作压力:≤31.4MPa 工作温度:筒体<100℃(2)内件Φ1374×9269 设计压力:≤0.1MPa 设计温度:50ºC9、合成补气油分 DN1400 H(净)=7500(1)外筒Φ1482/Φ1214×10200 容积:30M3设计压力:31.4MPa 设计温度:100ºC工作压力:≤31.4MPa 工作温度:筒体<100℃(2)内件Φ1170×8893 设计压力:≤0.1MPa 设计温度:50ºC10、合成水冷器换热面积:800M2设计压力:管程31.4MPa 壳程:1.0MPa 设计温度:管程110/40℃壳程:50℃工作压力:管程≤31.4MPa 壳程:0.6MPa 工作温度:管程110/40℃壳程:30/40℃11、氨分离器 DN1400 H(净)=7500(1)外筒Φ1725/Φ1409×11094 容积:12.3M3设计压力:31.4MPa 设计温度:100ºC工作压力:≤31.4MPa 工作温度:筒体-16~100℃(2)内件Φ1350×9269设计压力:≤0.1MPa 设计温度:-19ºC12、循环机 TC620-32-12 型透平循环机入口压力:29.20MPa 出口压力:31.36MPa Q=620m3/h电机功率:680KW 电压:380V六、工艺操作1、正常开车(1)开车前的准备工作1)确认系统检修盲板已全部抽出,检修敞口处已全部恢复联口;2)检查各设备、管道、阀门、分析取样点、电器、仪表等,必须正常完好;3)检查系统内所有阀门的开关情况,应符合开车要求;应处于关闭状态的阀门:新鲜气阀,透平机进出口阀、透平机进口放空阀、环隙阀及环隙调节阀组、各冷激阀组、冷管阀、主线阀、热副阀、水冷器进口阀、新鲜气放空阀、塔后放空阀、吹除气阀、各放氨阀、各加氨阀、副产蒸汽出口阀、废锅加水旁路阀、开工蒸汽阀、水冷器冷却水进出口阀、各排油阀、仪表流量计及取样根部阀应处于打开状态的阀门:新鲜气充压截止阀、输氨总阀、软水调节阀前后截止阀、气氨总阀、各压力表根部阀4)联系仪表检查仪表已打开处于备用状态,联系电工检查电器设备确认备用;5)检查防护、消防器材、工具已准备齐全,消除现场杂物,准备好报表记录;6)联系生产调度,准备开塔;7)开塔前,废热锅炉加水至1/3液位,并煮锅。
DC—C型Φ2200氨合成塔内件改造优化的总结

DC—C型Φ2200氨合成塔内件改造优化的总结随着化工工艺技术的发展,氨合成塔内件使用DC-C型已经是一种普遍的趋势。
本文结合对湖北三宁化工股份有限公司生产使用的DN2200氨合成塔内件更换为DC-C型Φ2200氨合成塔内件的技术改造过程,对于如何进一步降低能源消耗的基础上不断提高氨的产量进行了分析,并提出了一些切实可行的优化措施。
经过实际应用发现,通过优化后氨的产量明显提高,而且电能消耗大大降低,远远低于设计标准,而起整体的运行状况也得到较好的改善。
标签:DC-C型Φ2200内件优化;技术改造;应用分析一方面随着当前社会技术的发展,尤其是在化工工艺技术领域内取得的重大技术突破,另一方面也由于当前的人们的环保理念的提高以及环境问题的突出,对化工企业的生产要求提出更高的标准,所以对于氨合成塔的内部构件进行优化改造是社会发展的必然要求。
本文针结本公司(湖北三宁化工股份有限公司)生产使用的DN2200氨合成塔内件更换为DC-C型Φ2200氨合成塔内件的技术改造过程,对于DC-C型Φ2200氨合成塔内件的改造应用进行了分析。
1 改造现状情况概述1.1 改造情况介绍我公司是湖北三宁化工股份有限公司尿素厂“40.30”工程,(40万t/a合成氨,30万t/a尿素)于2008年11月一次性开车成功,由于该装置已经运行7年有余,催化剂也到了使用后期(塔上层利用停车期间间断加触媒10余吨),催化剂活性降低,造成氨产量下降,触媒层热点温度分布不合理,中下层温度偏高,平面温差大,无法合理调节温度,氨合成塔压差大,高达0.7MPa,系统阻力偏高,造成循环机功耗大,氨净值偏低等等一系列问题。
为进一步节能降耗、提高氨产量,所以公司决定在2015年12月DN2200氨合成塔内件更换为DC-C型2000氨合成塔内件,同时包括直通式废热锅炉换热段、及对部分管道现场系统的优化,进而达到公司所要求的DC-C型Φ2200氨合成系统运行水平以及节能水平的提高。
- 1、下载文档前请自行甄别文档内容的完整性,平台不提供额外的编辑、内容补充、找答案等附加服务。
- 2、"仅部分预览"的文档,不可在线预览部分如存在完整性等问题,可反馈申请退款(可完整预览的文档不适用该条件!)。
- 3、如文档侵犯您的权益,请联系客服反馈,我们会尽快为您处理(人工客服工作时间:9:00-18:30)。
概述湖南安淳高新技术有限公司(以下简称安淳公司)从上世纪80年代起,在分析了国际国内氨合成塔内件优缺点的基础上,独创了ⅢJ型氨合成塔内件,取得了国家专利,是国内数种氨合成塔内件中唯一经原化工部鉴定的内件,鉴定结论是,该内件为国内首创,主要技术指标取得突破性进展,达到国际先进水平。
安淳公司不断创新、不断进取,随后又推出了ⅢJ99型氨合成内件,包含3个新的国家专利技术。
ⅢJ型、ⅢJ99型氨合成内件经由φ800、φ1000到φ1200;后又开发了ⅢJD2000型φ1400、φ1600、φ1800、φ2000氨合成内件。
单塔年产氨能力由20 kt(φ600塔)发展到180 kt、200 kt。
近几年开发的ⅢJD2000型-φ2200氨合成塔,在技术上又有较大的提升;单塔生产能力日均达850~910 t,受到了用户的青睐。
2 ⅢJD2000型-φ2200氨合成塔的设计思想为实现单系统生产能力规模化和进一步降低能耗,安淳公司在ⅢJD2000型-φ1800、φ2000氨合成内件的基础上,引入新的理念,设计了ⅢJD2000型-φ2200氨合成内件,具体如下。
(1)充分发挥第一绝热层的作用。
进入零米未反应气氨含量低,距离反应平衡很远,反应速度很快,尽量在开始反应的第一层多产氨,使第一层之氨净值达到8%~9%,即第一绝热层温升110~133 ℃。
具体措施如下。
①增加第一绝热层的高度,第一绝热层设计高度2.5~3.1 m。
②降低零米温度,提高热点温度。
进第一绝热层零米点的循环气,氨含量最低(约2.16%),温度低(370~380 ℃),离反应平衡点最远;如零米温度为380 ℃,将第一绝热层反应终点温度设计为490~513 ℃,则第一绝热层的氨含量增加8%~9%(氨净值),即第一绝热层完成氨合成反应的50%。
(2)第一层绝热反应后的热气体,不再采取冷激,而是用塔内换热器间接冷却后再进入第二层,这样更有利于氨合成反应温度接近最适宜温度曲线。
(3)冷管束(段间冷却器)的气体出口设在催化剂床层表面,使进塔气体100%地通过第一层催化剂,有利于降低零米温度,提高氨净值。
(4)分流气占到近50%,使通过中心管和换热器的气体由原来的65%~70%减少至50%,降低塔阻力。
(5)提高出塔温度。
设计最高出塔温度为380 ℃,产生3.0~4.0 MPa过热蒸汽,使回收蒸汽的利用价值更高。
(6)大幅度提高出塔氨含量。
3 ⅢJD2000型-φ2200氨合成塔的结构特点(1)塔结构为三层四段,两径一轴。
径向段占床层高的70%~80%;第一层为轴向绝热段,为了使第一层反应温度不致超高,在第一层中部设一个冷气调温器;第二层包含径向绝热段和径向间冷段;第三层为径向绝热段。
(2)冷管束的气体出口在催化剂床层表面,使进塔气体100%地通过第一层催化剂,提高第一层催化剂的利用率。
(3)第一层绝热反应后的热气体被塔内换热器间接冷却后再进入第二层径向绝热段和径向内冷段,这样更有利于氨合成反应温度接近最适宜温度曲线。
(4)采用分流工艺。
(5)结构简单,催化剂可自卸。
ⅢJD2000型-φ2200氨合成内件结构示意见图1。
图1 ⅢJD2000型-φ2200氨合成内件结构示意图4 ⅢJD2000型-φ2200氨合成工艺流程4.1 塔内气体流程气体分两股进塔。
一股约45%的气体直接进入冷管束(段间冷却器)。
这股气体由两部分组成:一是由循环机出口油分来的约30%的冷气,由合成塔下部环隙进入,在塔顶引出;二是塔外热交换器加热的、约15%的气体。
两部分气体在塔顶汇合引进冷管束,冷管束出来的气体进入催化床层表面(零米冷激气和第一绝热层冷气调温器的冷气约占5%)。
另一股约50%、由塔外热交换器加热的循环气,进入塔内下部换热器管内,与出塔气体换热以后,进入上部换热器管内,与在上绝热段反应后出混合分布器Ⅰ的气体换热后,从换热器与中心管之间的环隙向下进入中心管,经中心管进入催化剂床层表面与冷管束出来的气体汇合,在第一绝热层反应;反应气体在第一层中部冷气调温器中与从塔外引入的少量冷气混合后,继续反应;出第一绝热层的气体进入气体混合分布器Ⅰ,再进入塔内上部换热器管间,与进塔气体换热后,从上部换热器的外壳出去,进入第二层。
气体由圆心向圆周方向经过径向绝热段,径向通过段间冷却器。
从中部径向筐即第二层出来的气体,受支架套筒的作用,沿径向筐与内筒的环隙向下,在内外筒环隙间接降温10~15 ℃,进入第三层。
气体由圆周方向径向通过下绝热层流向径向筐中心的换热器,从换热器外壳进入塔内下部换热器管间,由上折流而下,与进塔气体换热,温度降到约380 ℃出塔。
4.2 系统流程出合成塔的气体直接进入废锅,产生3.0~4.0 MPa的蒸汽,出废锅的气体进入热交换器,温度降至70 ℃左右进入水冷器;出水冷器的气体温度降到35 ℃以下,进入冷交管间冷却分离氨后,温度降到16 ℃以下进入一级氨冷器,经一级氨冷冷却至-5 ℃,再经二级氨冷冷却到-10~-12 ℃,进入氨分离器分离氨后进冷交管内,冷却管间的热气体,本身温度提高到25 ℃左右出冷交,与新鲜气汇合后进循环机,开始新一轮循环。
ⅢJD2000型-φ2200氨合成系统流程示意见图2,流程设计特点如下。
(1)充分利用反应热,反应气出塔温度高,出塔气温度约380 ℃,可产生3.0~4.0 MPa的中压蒸汽。
(2)加大热交面积,将进塔未反应气预热至200~240 ℃,省去一个软水加热器,简化流程,减少系统阻力。
(3)设两级氨冷,一级氨冷冷至-5℃,二级冷至-10~-12 ℃,在22 MPa 压力下,氨含量降至2.2%以下,进塔氨含量低,且节约冷冻量。
(4)进水冷器气体温度低,节约冷却水。
(5)补气补在冷交冷气出口、循环机进口,以降低补气压力,节约压缩机电耗,节省冷冻量。
循环机设在塔前,循环机出口压力处于系统压力最高点。
(6)放空点设在冷交冷气出口、补气接点以前,此处氨含量最低,惰气浓度高,可节约冷冻量,没有放掉新鲜气。
(7)设补气氨冷,降低补气温度,有利于油水分离,减少带入合成系统的油水杂质。
图2 ⅢJD2000型-φ2200氨合成系统流程示意图1—合成塔;2—废锅;3—热交;4—水冷;5—冷交;6—二级氨冷;7—氨分;8—循环机;9—油分;10—补气氨冷;11—补气油分5 催化剂的装填和升温还原5.1 催化剂的装填ⅢJD2000型-φ2200氨合成内件催化剂的装填,按分段装填的原则,下绝热层装填少量φ4.7~φ6.7 mm的催化剂垫底,此占总装量的2.5%,其余装φ2.5~φ3.3 mm颗粒,占总装量的38.2%;第二层全部装φ4.7~φ6.7 mm的催化剂,占总装量的39.3%。
第一层,混合分布器Ⅰ用少量φ4.7~φ6.7 mm的催化剂盖面,占总装量的2.1%;冷气调温器用少量φ4.7~φ6.7 mm的催化剂盖面,占总装量的2.4%;其余装φ3.3~φ4.7 mm的催化剂,占总装量的15.5%。
5.2 催化剂的升温还原5.2.1 “三高”、“三低”的操作原则(1)“三高”,即高氢气浓度,高空速,高电炉功率。
高氢气浓度,增加反应物浓度,有利于还原反应进行。
氢气浓度要求在75%~80%;还原后期不低于72%。
高空速,把还原反应生成的水汽和反应生成的氨尽快带走,降低水汽浓度。
高电炉功率,是高空速的前提,还原过程中,绝大多数情况下电炉功率都是100%。
(2)“三低”,即低压力,低水汽浓度,低还原温度。
压力虽然对还原反应没有直接的影响,但压力低,空速一定时,气流线速度快,生成的水汽和氨很容易被气流带走,降低水汽浓度;压力低,轴向段轴向温差小,是缩小同平面温差的最有效操作手段。
还原的起始压力以3.5~4.0 MPa 为宜。
催化剂的还原反应是一个可逆反应,低水汽浓度可以减少逆反应,防止还原好了的催化剂被氧化。
低氨冷温度,是低水汽浓度的保证。
进入还原主期的氨冷温度,必须控制-10~-15 ℃。
催化剂的还原反应是一个吸热反应,提高反应温度,可明显加快还原反应速度,但同时也加快了活性α-Fe的烧结速度,反应温度提高过快,活性铁晶粒长大的速度随之加快,引起活性下降。
还原温度440~450 ℃时,控制催化剂出水量达到80%左右为宜。
5.2.2 分层还原大塔催化剂数量多,应严格地实行分层还原,拉开层与层之间的温差。
上层在进行还原反应时,中下层温度还很低,多数催化剂还处于氧化态,不会受上层产生的水汽影响。
这样才能保证催化剂的还原质量。
5.2.3 轴向段同平面温差的控制轴向段的同平面温差要严格控制。
轴向段在升温还原时,如果出现同平面温差大,必须在催化剂还原进入主期之前,把同平面温差消除(筐盖泄漏造成的温差要揭大盖处理),即催化剂温度在410 ℃左右,就要把温差缩小到5 ℃之内。
同平面温差大,会造成催化剂温差高低两面的还原程度不一样,还原程度低的部分,在正常生产中活性差,且同样会出现同平面温差,影响生产,影响内件的安全。
不能等到温差大了才采取措施,还原主期之后拉小的温差,同样存在还原程度不一样的问题。
因此,轴向段的同平面温差控制,是还原过程一个不可忽视的重要控制环节。
5.2.4 还原终点判断(以XA201型催化剂为例)(1)底点催化剂温度470 ℃以上,维持 8 h;水汽浓度连续3~4 h在0.2 g/m3以下。
(2)零米温度485~490 ℃维持 8 h以上,同平面温差≤10 ℃。
(3)除零米和底点以外的各点达495 ℃以上的时间均在8 h以上。
符合以上三条,催化剂便基本还原彻底,可切电降温转轻负荷生产。
6 ⅢJD2000型-φ2200氨合成的生产实践ⅢJD2000型-φ2200氨合成已在山东鲁西化工集团工业园、湖北三宁化工有限责任公司、江苏恒盛化肥有限公司投入使用。
为鲁西化工集团工业园设计制造的ⅢJD2000型-φ2200氨合成塔配套系统,完全按照“低零米温度、高热点温度、高出塔温度、高氨净值、高产量、大分流”的思想设计。
2007年6月13日投入生产,日产氨860~920 t,最高达960 t。
系统惰性气体含量约20%,系统压力24.0~25.0 MPa,塔出口氨含量高达15%~17%。
催化床层温度,零米温度380 ℃;热点温度515 ℃。
塔出口温度356 ℃。
实际生产能力260 kt/a。
存在的不足之处是,塔内分流未能真正达到50%,塔阻力1.5~1.6 MPa。
湖北三宁化工有限责任公司φ2200氨合成系统,于2008年12月正式投入生产。
该装置设计压力26.0 MPa;设计生产能力220 kt/a。
目前实际日产液氨控制在18.0%~850~880 t,最高日产928 t;循环气氢53.0%~57.0%;CH421.0%,总惰性气体达22%~24%;循环机开3×13.7 m3/min;系统压力23.0~24.0 MPa,塔阻力0.7~0.8 MPa,系统阻力1.5~1.7 MPa。