冲压模具检查表
合集下载
冲压模具定期点检表
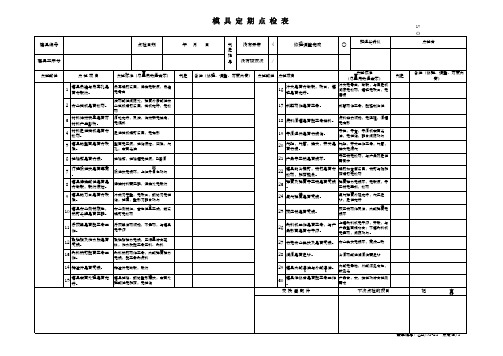
具的各镙钉,销钉是否有 螺钉加套筒紧固,销钉与防脱 落螺钉无松动 松动,脱落现象。 弹簧及弹簧导正销是否受损 弹簧弹力无损坏,无裂痕,导 正销无歪斜,松动 。
氮气弹簧外观完好,气压足 够,定位完好 预压销动作灵活,内部弹簧无 损坏 上模卸料板无干涉,开裂,与
24 氮气弹簧是否受损。 25 预压销是否受损。
模具维修后是否能正常工作 产品首,末,抽检均符合检测 要求 。
交换零部件
下次点检的项目
记 事
表单编号:QR751-21 版本:B/1
NO 修理调整完成 ○
班组长确认 点检者
点检日期
年 月 日
判 定 记 号
没有异常 没有该项次
√
/
点检标准 (尽量用数值表示) 判定 备注(修理、调整、对策内容)
判定
备注(修理、调整、对策内容)
点检部位 点检项目
冲头无弯曲,断裂,与固定板 冲头是否有断裂,缺口,模 间隙无松动,模钮无缺口,无 16 钮是否完好。 磨损
11 12 13
26
卸料板工作是否正常,与产 产品型面相吻合;下模卸料板 品形面是否有干涉。 无晃动,间隙均匀。
27 有无安全垫块及是否受损。 安全垫块无损坏,高度一致 28 润滑是否足够。 29 模具内部清洁与外部清洁。 30
各滑动部位润滑油要足够 内部无异物,外部漆见本色, 铁见光
14 铸造件是否受损。 15 模具表面处理是否完 好。
模 具 定 期 点 检 表
模具编号 模具工序号
点检部位 1 点检项目 模具吊棒与吊耳孔是 否有裂纹。 点检标准(尽量用数值表示)
吊耳螺钉紧固,焊接无裂痕,吊棒 无弯曲 活动部位间隙处,弹簧外露部位安 全档板螺钉紧固,档板完好,无松 动 滑轮完好,灵活,传送架无棱角, 无偏斜 定位挡板螺钉紧固,无变形 型面无压痕,拉伤痕迹,凹陷,气 孔,表面光洁 拉延筋,拉延槽无拉痕,R圆滑 限位块无损坏,上红丹着色均匀 焊接材料要匹配,焊接处无裂纹 冲裁刃平整,无缺口,翻边刃无拉 伤,拉薄,整形刀配合均匀 安全侧销红,黄色位置正确,锁紧 螺钉无松动 浮顶器活动顺畅,不晃动,与模具 无干涉 聚胺脂弹力无损,压缩量符合规 格,优力胶能正常压料、卸料 卸料销钉动作正常,内部弹簧弹力 无损,能正常卸废料 铸造件无断裂,裂纹 模具拉延、翻边整形镶块,表面处 理部位无脱落,无拉伤
氮气弹簧外观完好,气压足 够,定位完好 预压销动作灵活,内部弹簧无 损坏 上模卸料板无干涉,开裂,与
24 氮气弹簧是否受损。 25 预压销是否受损。
模具维修后是否能正常工作 产品首,末,抽检均符合检测 要求 。
交换零部件
下次点检的项目
记 事
表单编号:QR751-21 版本:B/1
NO 修理调整完成 ○
班组长确认 点检者
点检日期
年 月 日
判 定 记 号
没有异常 没有该项次
√
/
点检标准 (尽量用数值表示) 判定 备注(修理、调整、对策内容)
判定
备注(修理、调整、对策内容)
点检部位 点检项目
冲头无弯曲,断裂,与固定板 冲头是否有断裂,缺口,模 间隙无松动,模钮无缺口,无 16 钮是否完好。 磨损
11 12 13
26
卸料板工作是否正常,与产 产品型面相吻合;下模卸料板 品形面是否有干涉。 无晃动,间隙均匀。
27 有无安全垫块及是否受损。 安全垫块无损坏,高度一致 28 润滑是否足够。 29 模具内部清洁与外部清洁。 30
各滑动部位润滑油要足够 内部无异物,外部漆见本色, 铁见光
14 铸造件是否受损。 15 模具表面处理是否完 好。
模 具 定 期 点 检 表
模具编号 模具工序号
点检部位 1 点检项目 模具吊棒与吊耳孔是 否有裂纹。 点检标准(尽量用数值表示)
吊耳螺钉紧固,焊接无裂痕,吊棒 无弯曲 活动部位间隙处,弹簧外露部位安 全档板螺钉紧固,档板完好,无松 动 滑轮完好,灵活,传送架无棱角, 无偏斜 定位挡板螺钉紧固,无变形 型面无压痕,拉伤痕迹,凹陷,气 孔,表面光洁 拉延筋,拉延槽无拉痕,R圆滑 限位块无损坏,上红丹着色均匀 焊接材料要匹配,焊接处无裂纹 冲裁刃平整,无缺口,翻边刃无拉 伤,拉薄,整形刀配合均匀 安全侧销红,黄色位置正确,锁紧 螺钉无松动 浮顶器活动顺畅,不晃动,与模具 无干涉 聚胺脂弹力无损,压缩量符合规 格,优力胶能正常压料、卸料 卸料销钉动作正常,内部弹簧弹力 无损,能正常卸废料 铸造件无断裂,裂纹 模具拉延、翻边整形镶块,表面处 理部位无脱落,无拉伤
冲压模具点检表
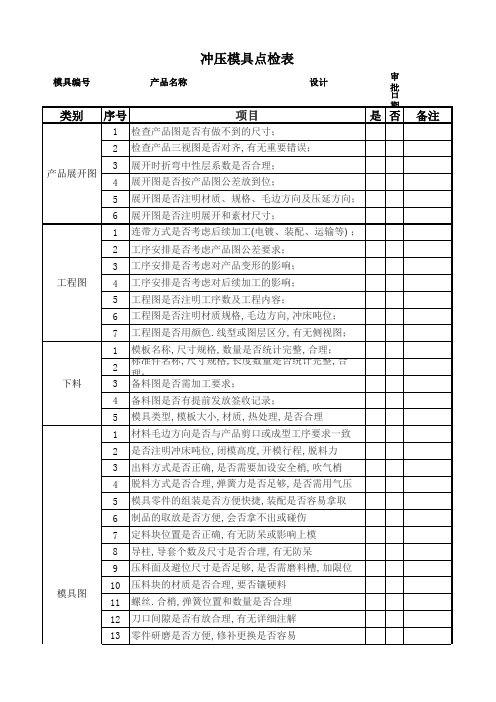
冲压模具点检表
模具编号 产品名称 设计 审批 日期
类别
序号
1 2 3 4 5 6 1 2 3
项目
检查产品图是否有做不到的尺寸; 检查产品三视图是否对齐, 有无重要错误; 展开时折弯中性层系数是否合理; 展开图是否按产品图公差放到位; 展开图是否注明材质、规格、毛边方向及压延方向; 展开图是否注明展开和素材尺寸; 连带方式是否考虑后续加工(电镀、装配、运输等) ; 工序安排是否考虑产品图公差要求; 工序安排是否考虑对产品变形的影响; 工序安排是否考虑对后续加工的影响; 工程图是否注明工序数及工程内容; 工程图是否注明材质规格, 毛边方向, 冲床吨位; 工程图是否用颜色. 线型或图层区分, 有无侧视图; 模板名称, 尺寸规格, 数量是否统计完整, 合理; 标准件名称, 尺寸规格, 长度数量是否统计完整, 合 理; 备料图是否需加工要求; 备料图是否有提前发放签收记录; 模具类型, 模板大小, 材质, 热处理, 是否合理 材料毛边方向是否与产品剪口或成型工序要求一致 是否注明冲床吨位, 闭模高度, 开模行程, 脱料力 出料方式是否正确, 是否需要加设安全梢, 吹气梢 脱料方式是否合理, 弹簧力是否足够, 是否需用气压 模具零件的组装是否方便快捷, 装配是否容易拿取 制品的取放是否方便, 会否拿不出或碰伤 定料块位置是否正确, 有无防呆或影响上模 导柱, 导套个数及尺寸是否合理, 有无防呆 压料面及避位尺寸是否足够, 是否需磨料槽, 加限位 压料块的材质是否合理, 要否镶硬料 螺丝. 合梢, 弹簧位置和数量是否合理 刀口间隙是否有放合理, 有无详细注解 零件研磨是否方便, 修补更换开图
工程图
4 5 6 7 1 2
下料
3 4 5 1 2 3 4 5 6 7 8 9 10 11 12 13
模具编号 产品名称 设计 审批 日期
类别
序号
1 2 3 4 5 6 1 2 3
项目
检查产品图是否有做不到的尺寸; 检查产品三视图是否对齐, 有无重要错误; 展开时折弯中性层系数是否合理; 展开图是否按产品图公差放到位; 展开图是否注明材质、规格、毛边方向及压延方向; 展开图是否注明展开和素材尺寸; 连带方式是否考虑后续加工(电镀、装配、运输等) ; 工序安排是否考虑产品图公差要求; 工序安排是否考虑对产品变形的影响; 工序安排是否考虑对后续加工的影响; 工程图是否注明工序数及工程内容; 工程图是否注明材质规格, 毛边方向, 冲床吨位; 工程图是否用颜色. 线型或图层区分, 有无侧视图; 模板名称, 尺寸规格, 数量是否统计完整, 合理; 标准件名称, 尺寸规格, 长度数量是否统计完整, 合 理; 备料图是否需加工要求; 备料图是否有提前发放签收记录; 模具类型, 模板大小, 材质, 热处理, 是否合理 材料毛边方向是否与产品剪口或成型工序要求一致 是否注明冲床吨位, 闭模高度, 开模行程, 脱料力 出料方式是否正确, 是否需要加设安全梢, 吹气梢 脱料方式是否合理, 弹簧力是否足够, 是否需用气压 模具零件的组装是否方便快捷, 装配是否容易拿取 制品的取放是否方便, 会否拿不出或碰伤 定料块位置是否正确, 有无防呆或影响上模 导柱, 导套个数及尺寸是否合理, 有无防呆 压料面及避位尺寸是否足够, 是否需磨料槽, 加限位 压料块的材质是否合理, 要否镶硬料 螺丝. 合梢, 弹簧位置和数量是否合理 刀口间隙是否有放合理, 有无详细注解 零件研磨是否方便, 修补更换开图
工程图
4 5 6 7 1 2
下料
3 4 5 1 2 3 4 5 6 7 8 9 10 11 12 13
冲压模具检查记录表范例
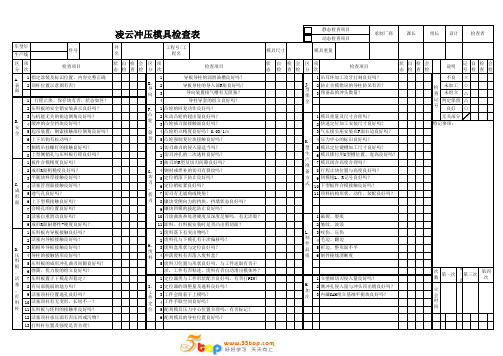
3 预备品的冲头数量?
全
1 模具重量及尺寸合理吗?
2 快速定位加工安装尺寸良好吗?
3 气压接头座安装在F面右边良好吗?
K. 4 压力中心的标识良好吗? 型 5 模具定位键槽加工尺寸良好吗?
生 6 模具锁付用U型槽位置、宽高良好吗?
产 准
7 模具闭合高度合理吗?
备 8 行程止块位置与高度良好吗?
方 9 闭模钮L、R记号良好吗? 式 10 下型板件合模接触良好吗?
12 活塞顶杆承压面有否压凹或污物?
13 打料杆位置及强度是否合理?
1 E. 2 导 向3
4
导板导柱的润滑油槽良好吗? 导板导柱的导入部R角良好吗?
导向装置排气槽有无阻塞? 导柱导套的组立良好吗?
F. 1 凸轮的回复动作良好吗?
凸 2 从动凸轮的超出量良好吗?
轮 、
3 凸轮插刀面接触面良好吗?
斜 4 凸轮组立精度良好吗?0.03/1m
凌云冲压模具检查表
静态检查项目 动态检查项目
承制厂商
课长
组长 设计
检查者
车型年 生产线
件号
件 名
工程号/工 程名
模具尺寸
模具重量
区项 分次
检查项目
状自检会 区项 态检查检 分次
检查项目
状 自 检会 区项 态 检 查检 分次
检查项目
状自检会 态检查检
说明
记自检会 号检查检
A. 1 指定涂装及标识位置、内容完整正确 表 2 顶杆位置示意图有否? 面
11 顶料机构形状、动作、装配良好吗?
1 破裂、裂痕
2 皱纹、波浪
L. 3 咬伤、压伤 制 4 毛边、翻边 件 品 5 折边、整形面不平 质 6 制件棱线清晰度
中日文冲压模具检查表
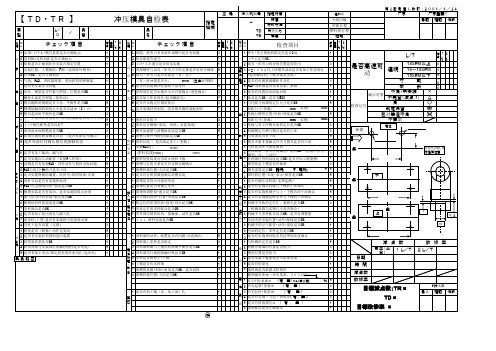
5 mm
3
4 机械侧定位销与模具是否有干涉
3
取 5 与设备是否有干涉
5
L/T
是否高速可 动
連続
18SPM以上 16~18SPM 15SPM以下
寸 動
中 断
减点对象
不良・未安装 不完全(減点 1)
× △
检查记号
良 判定保留
○
○保
已对策但不良
○
不要紧
定位
换模
減1 2 点 L/ L/
TT
0
-
TD
板厚 材料寸法 气垫压力
夹紧内幅 夹紧行程 弹料块行程
承認 確認 作成
TR 模高
送距
分N 类o
检查项目
1 冲头・导正销座的销定位是否2处
減自 1 2 点 主 L/ L/
TT
1
(中心定位NG)
2 切刃・折弯刀的分割位置是否恰当
3
模 具
3
w=10kg以上的模具部品是否有加工作业用孔
1
保 (起吊螺纹孔)(嵌合部品全部)
1 间隙、折弯刀R形状在试模中是否有问题
2 咬合量是否适当
3 2次・3次避让是否切实实施
切
4
背撑钢性与切刃・折弯刀下的支撑是否有充分确保
刃 5 切刃・折弯刀是否有悬挂(有,无)
(有)时⇒量是多少: ・
mm (立会时判断)
6 是否有安装侧冲孔强制下落零件
曲 7 补焊部位是否实施淬火后开裂确认(着色确认)
确 7 防误夹的安装位置・动作・配线是否OK 认 8 机械手的空气配管・动作・强度是否OK
9 空站的定位、零件定位是否OK
1 0
是否有实施相对取出传送带的高度确认
模具设计检查表(冲压)

17.模具的总体结构应便于直接安装、拆卸、使用,并具有足够的刚性,便于维修保养
18.成型(拉深、成形、弯曲、翻边、整形)
A.压边圈设计的合理性(包括拉深筋等)
B.拉深模、成形模排气系统是否适合
C.气垫顶杆的行程长度是否符合要求
D.到位标记或限位装置确保产品压制到位
19.冲裁(落料、冲孔、切边)
A.模具整体、分段修边周界及间隙设计的合理性
11.冲压力是否计算,压力中心位置在设计图纸中是否标注提示
12.上下模具定位及导向的可靠性
13.定位的可靠性;定位基准与产品基准一致性;前道工序的制件,在下道模具中定位的可靠性
14.U型槽、模柄、顶杆位置及孔径等安装尺寸应与选用机床一致
15.模具顶出和卸料装置、易损件和工作部分的合理性与可靠性
16.斜锲和吊锲结构的尺寸是否符合要求
冲压模具设计审核表
DIEDESIGNREVIEW
零件号:
总成号:
工程更改号:
零件名称:
零件图纸或GD&T图纸号:
零件图纸更改级别:
年型/车型:
零件数模版本号:
模具编号/图纸张数:
零件供应商:
产品工程师(新亚通) :
模具工程师(新亚通):
电话:
电话:
DUNS / Z编号:
模具工程师(供应商):
电话:
模具设计公司:
B.工作部分镶块设计的合理性
C.废料系
E:.刃口有效工作长度是否足够
20.模具的部件必须具有安全措施,特别是进料、出料,模具的安装及搬运装置
21.是否规定的对模具部件标识,如:上下模及重量、工序号、标牌、涂色、顶杆位置等
审核及改进意见:(如审核及改进意见此栏写不开,附表于后)审核栏评价结果:此项目不适用打/合格打√不合格打×
18.成型(拉深、成形、弯曲、翻边、整形)
A.压边圈设计的合理性(包括拉深筋等)
B.拉深模、成形模排气系统是否适合
C.气垫顶杆的行程长度是否符合要求
D.到位标记或限位装置确保产品压制到位
19.冲裁(落料、冲孔、切边)
A.模具整体、分段修边周界及间隙设计的合理性
11.冲压力是否计算,压力中心位置在设计图纸中是否标注提示
12.上下模具定位及导向的可靠性
13.定位的可靠性;定位基准与产品基准一致性;前道工序的制件,在下道模具中定位的可靠性
14.U型槽、模柄、顶杆位置及孔径等安装尺寸应与选用机床一致
15.模具顶出和卸料装置、易损件和工作部分的合理性与可靠性
16.斜锲和吊锲结构的尺寸是否符合要求
冲压模具设计审核表
DIEDESIGNREVIEW
零件号:
总成号:
工程更改号:
零件名称:
零件图纸或GD&T图纸号:
零件图纸更改级别:
年型/车型:
零件数模版本号:
模具编号/图纸张数:
零件供应商:
产品工程师(新亚通) :
模具工程师(新亚通):
电话:
电话:
DUNS / Z编号:
模具工程师(供应商):
电话:
模具设计公司:
B.工作部分镶块设计的合理性
C.废料系
E:.刃口有效工作长度是否足够
20.模具的部件必须具有安全措施,特别是进料、出料,模具的安装及搬运装置
21.是否规定的对模具部件标识,如:上下模及重量、工序号、标牌、涂色、顶杆位置等
审核及改进意见:(如审核及改进意见此栏写不开,附表于后)审核栏评价结果:此项目不适用打/合格打√不合格打×
冲压检查表

6
保险盖
1、使用是否完好;2、强度和尺寸是否符合(含备用的)
2、参照说 明书。
2、备用的三个月
7
安全用电
是否有电线破皮、老化以及私拉乱扯现象
1、目测
1个月
8
地脚螺丝
是否有缺失、松动(40T以上的冲床)
1、目测 2、试验
1个月
9
支撑螺丝
是否有缺失、松动(开式可倾冲床)
1、目测 2、试验
1个月
10
电机的固定及支撑螺丝 是否有缺失、松动
1、目测 2、试验
1个月
备注:上表中的各项由安全办全体在冲压部日常巡查或维修工作中安全检查的基本内容。电工负责用电安全及光电保护、双手操作和电机及电箱、操作箱的紧固螺丝
检查; 机修工负责冲床使用(含保险盖)、安全挡板、防护网、地脚螺丝、支撑螺丝的检查。检查出的问题必须有记录、有结果,作为绩效考核的重要依据。
补充说明:
冲压部安全控点检查表
检查日期:
安全控点
检查内容
1
冲床使用
1、是否超负荷;2、螺杆调节是否超出范围
模具安全挡板 1、有否;2、有效性
检查方法
1、检查保 险; 2、目测
1、目测
检查人:
检查周期
现场随时
现场随时
检查结果
2
四要素
防护网 光电保护 双手操作
1、有否;2、有效性 1、有否;2、有效性(含高度调节) 1、有否;2、有效性(16T以上的冲床)
1、目测
1、目测 2、试验 1、目测 2、试验
现场随时 现场随时 现场随时
3
劳保用品
耳塞、眼镜、手套、防护帽、代手工具等是否正确使用
1、目测
冲压模具验收动静态检查表

紧固无松动,无裂纹及破损,重点检查
A
√
/
/
87
安全护板
厚度22∙Omm,操作安全
C
√
/
/
88
销钉
松紧合适,上下各销•半,安装防脱落装置
C
√
√
√
√
89
侧销孔
船销直径+0∙2mm=侧销孔宜径,无兄动
A
/
√
√
Z
90
侧销固定长度
原则上固定25mm根据直径大小现场判定
A
/
√
√
/
91
侧销锁板销钉
锁板按要求安装摞钉孔不允许人工打磨或加工
65
翻边整形刃口面
顺滑,无凸凹不平等缺陷
B
/
/
/
√
66
翻边整形块安装
间隙W0.05mm,无台阶,圆角顺滑一致
B
/
/\
/
√
67
翻边顶出器顶杆
螺钉孔与顶杆壁厚保证3-5M
B
/
/
/
√
冲压模具静态验收检查表
项目
CN200
零件名称
螺母片
备注:符合要求填写,不符合要求填写“X”,不适用填写
*7”具体问题填入“模具问题记录表”
目视
B
/
7
4
/
102
防护板涂黄色
目视
C
√
Z
/
Z
103
取出压料芯前需要先拆除的镶块涂红色
目视
A
/
√
/
/
104
模具存放块外周边涂红色.
目视
A
√
√
A
√
/
/
87
安全护板
厚度22∙Omm,操作安全
C
√
/
/
88
销钉
松紧合适,上下各销•半,安装防脱落装置
C
√
√
√
√
89
侧销孔
船销直径+0∙2mm=侧销孔宜径,无兄动
A
/
√
√
Z
90
侧销固定长度
原则上固定25mm根据直径大小现场判定
A
/
√
√
/
91
侧销锁板销钉
锁板按要求安装摞钉孔不允许人工打磨或加工
65
翻边整形刃口面
顺滑,无凸凹不平等缺陷
B
/
/
/
√
66
翻边整形块安装
间隙W0.05mm,无台阶,圆角顺滑一致
B
/
/\
/
√
67
翻边顶出器顶杆
螺钉孔与顶杆壁厚保证3-5M
B
/
/
/
√
冲压模具静态验收检查表
项目
CN200
零件名称
螺母片
备注:符合要求填写,不符合要求填写“X”,不适用填写
*7”具体问题填入“模具问题记录表”
目视
B
/
7
4
/
102
防护板涂黄色
目视
C
√
Z
/
Z
103
取出压料芯前需要先拆除的镶块涂红色
目视
A
/
√
/
/
104
模具存放块外周边涂红色.
目视
A
√
√
冲压模具动静态检查表

□
□
6
板
位
定隙
▲
匕匕 厶冃 不
-
废料
^1
量
□
▲
视 目
□
□
2-
▲
3
•
□
视 目
□
□
4
□
▲
片
5上量 料 入 落 否 匕匕 厶冃 料
视 目
□
□
5
□
▲
视 目
□
□
、安令
^1
□
刺 毛 破
视 目
□
□
2
•
□
视 目
□
□
3
置 簣
-
□
簣 图 合 符
视 目
n
n
4
•
□
视 目
□
□
5
•
□
孔 吊 起 加 应 上 以
5
在 量T
视 目
□
□
6
•
□
□
□
7
¥ 刍 侧安
▲
靠
视 目
其它
^1
蚀 锈 无
•-
□
视 目
□
□
2
-
□
纸 图 合 符
视 目
□
□
备注:
验收标记:合格O可接受△不合格X无此项目/第一次验收人员
验收1:表示第一次验收2:表示第二次验收
目视
15
料厚》1.2m m板料冲孔
•
冲头应设置垫板
目视
16
刀块有拆卸顺序的警告标志
•
必须先拆卸涂红色刀块
目视
17
退料板与凸模,压料板与凹模 的导正间隙
□
6
板
位
定隙
▲
匕匕 厶冃 不
-
废料
^1
量
□
▲
视 目
□
□
2-
▲
3
•
□
视 目
□
□
4
□
▲
片
5上量 料 入 落 否 匕匕 厶冃 料
视 目
□
□
5
□
▲
视 目
□
□
、安令
^1
□
刺 毛 破
视 目
□
□
2
•
□
视 目
□
□
3
置 簣
-
□
簣 图 合 符
视 目
n
n
4
•
□
视 目
□
□
5
•
□
孔 吊 起 加 应 上 以
5
在 量T
视 目
□
□
6
•
□
□
□
7
¥ 刍 侧安
▲
靠
视 目
其它
^1
蚀 锈 无
•-
□
视 目
□
□
2
-
□
纸 图 合 符
视 目
□
□
备注:
验收标记:合格O可接受△不合格X无此项目/第一次验收人员
验收1:表示第一次验收2:表示第二次验收
目视
15
料厚》1.2m m板料冲孔
•
冲头应设置垫板
目视
16
刀块有拆卸顺序的警告标志
•
必须先拆卸涂红色刀块
目视
17
退料板与凸模,压料板与凹模 的导正间隙
- 1、下载文档前请自行甄别文档内容的完整性,平台不提供额外的编辑、内容补充、找答案等附加服务。
- 2、"仅部分预览"的文档,不可在线预览部分如存在完整性等问题,可反馈申请退款(可完整预览的文档不适用该条件!)。
- 3、如文档侵犯您的权益,请联系客服反馈,我们会尽快为您处理(人工客服工作时间:9:00-18:30)。
10 凹模镶块及废料刀的空刀部分与铸件安装面平齐 11 保证刃口的切入量(有效刃口高度≥8mm)空刀1-2mm 12 压料板、顶出器与凹模镶块间隙<0.5mm,没有油污和刮痕 淬火后模具刃口部位硬度符合图纸要求,不允许有软点、烧伤及 13 裂纹 14 异形凹模及带形状处凹模应有防转装置,并符合图纸要求 15 镶块与窝座、止退键之间不能有间隙 16 凸模的废料刀刃口高度应低于凸模刃口的高度≥4mm 17 凸模废料刀的宽度应符合图纸(冲压件宽+10mm) 18 相邻处的凹模刃口与废料刀刃口相接触的高度应低于t+4mm 19 反侧类模具,接触面深确保进入20mm后工作,接触面无间隙 1 2 3 斜锲的固定应符合图纸,检查定位销松紧及挡块的贴合情况 回程键和回程钩起始部位的圆角及安装应符合图纸 斜锲滑动面的间隙<0.03mm 斜锲弹簧应有预压缩,复位良好 滑动压板的间隙<0.03mm以下无摆动 暴露的斜锲弹簧或其它弹顶器,均应有安全护板 安 装 部 分
斜 锲
其 它
4 5 6
顶出器及活动部位须加装防护板 模块重量超过15公斤时应设起重孔,孔位确保起吊时模 3 块保持平衡 气缸与托料杆之间的连接部分要安全、牢固,运动时平 4 稳 5 平衡块安装面应设有加强筋 U形槽的厚度、宽度、个数、位置及托杆孔位置误差≤ 6 ±0.5mm 7 螺纹深度,应符合图纸和国标要求,同时满足强度要求 翻转孔、起重孔,孔径、孔距应符合图纸(应能满足强 8 度要求) 侧销应保证在3根以上,并应使限位板开口向下,锁板 9 厚度5.0mm,要求用2-M10螺钉紧固 10 在存放状态时,应确保导柱或导板的配合量≥40mm 1 气源固定装置及管接规格是否符合图纸 进气、出气管接头应用颜色来区分,进气红色,出气兰 色,软管应夹头固定不能悬空、缠绕及破裂 2 所有调整垫片的大小应合适,并固定在底板上 3 模具应清洗(模具无切屑、废料、油污、红丹粉等) 4 模具加工基准必须保留,并在底板上刻印出坐标值 铭牌的安装、底板铸字区标识(F标识、送料方向箭头 5 、图号、材料)及镶块的图号、材料与底板安装座对应 的件号 6 模具非工作部位倒角2X45° 模具所有部位须按规定色、涂色,涂色要求参照技术 7 协议
检查次数 检查时间 验收人 备注
1 2 3 4 5 6 7 8 工 作 部 位 9
废料滑槽的固定应稳定,不易晃动,滑槽两侧与模腔的 间隙适当,不允许有废料漏入或卡住 6 废料滑槽滑料面须抛光处理 废料滑槽的板厚应符合要求,具有良好的刚度,料厚≥ 7 2.5mm 8 废料盒应有锁紧装置,防止模具起吊过程中脱落 9 废料盒应与模具腔壁贴合,并且抽拉灵活 折叠式废料滑槽要用链条固定,绝不允许将链条固定在 10 上模,并且折叠固定后废料滑槽不允许超出底板面 1 2 模具非工作部位倒角2X45°
模具静态验收细则
车型 分类 NO. 1 2 模 具 导 向 部 位 3 4 5 6 7 模具号 检查项目 导板及φ 60以上衬套应用铜基自润结构,不允许有拉毛 衬套有无出气孔 导板、导柱的导入部分的倒角(R10) 导柱、衬套与底板的配合是否符合图纸,有无松动情况 导板的止退接触面宽5-15mm,并且与导板的底部及安装面无间隙 导板的导滑面表面粗糙度Ra≤0.8(伤痕面积<5%),可使用石 墨自润滑导板 非装配式导板面必须开油槽,并且油槽沿周及孔边需倒0.5-1mm 的角 整形、翻边类基准件要求:棱线清晰、R一致,型面光顺,无凹 凸缺陷 翻边类、成型处R按图纸要求 冲头固定板垫片要求5mm,HRC50-55度 镶块接缝的间隙(修边、翻边0.05mm以下) 销钉松紧适度、螺纹底孔按标准(国标) 焊接部位的材质、硬度符合要求 刃口锋利、无缺口、崩刃及倒锥,应用直角尺对90° 焊接部位不能有气孔及平行于刃口的焊接裂纹、垂直裂纹应控制 在100≤3条(最好无) 工作部位表面粗糙度Ra≤0.8 废 料 下 滑 部 分 定 位 部 分 1 2 模具名称 分类 NO. 1 2 3 4 5 1 2 3 4 5 零件号 检查项目 1 零件如采用凸模定位时,应保证与凸模的贴合,贴合面 间隙在0.2mm以内 兼作形状定位的废料刀的型面应与上工序冲压件吻合, 不能牵扯冲压件而造成变形 定位块或定位销定位时,应保证定位稳定,便于取件, 与上模应无干涉 定位板的调整范围要足够(调整范围在5-10mm以 内),如果影响强度,则不受此限制 模具定位部分应能满足防反使用要求 废料滑槽角度应≥25° 废料滑槽宽度应满足要求(槽宽=废料宽度+最小 20mm),确保滑槽拐角处角度≥25°,如难以保证模 具强度和U形槽,可不按此规定 为防止废料飞散,滑槽两侧应有翻边,边高度≥50mm 废料孔应畅通,无台阶,并于滑槽的位置无偏移 2 判定 标记 零件名称 合格 ○ 不合格 X 1 未装配 未确认 无此项 △ □ 2 /