【机械类文献翻译】车床与铣削加工
机械专业外文文献翻译

翻译部分英文原文High-speed machining and demand for the development ofHigh-speed machining is contemporary advanced manufacturing technology an important component of the high-efficiency, High-precision and high surface quality, and other features. This article presents the technical definition of the current state of development of China's application fields and the demand situation.High-speed machining is oriented to the 21st century a new high-tech, high-efficiency, High-precision and high surface quality as a basic feature, in the automobile industry, aerospace, Die Manufacturing and instrumentation industries gained increasingly widespread application, and has made significant technical and economic benefits. contemporary advanced manufacturing technology an important component part.HSC is to achieve high efficiency of the core technology manufacturers, intensive processes and equipment packaged so that it has a high production efficiency. It can be said that the high-speed machining is an increase in the quantity of equipment significantly improve processing efficiency essential to the technology. High-speed machining is the major advantages : improve production efficiency, improve accuracy and reduce the processing of cutting resistance.The high-speed machining of meaning, at present there is no uniform understanding, there are generally several points as follows : high cutting speed. usually faster than that of their normal cutting 5 -10 times; machine tool spindle speed high, generally spindle speed in -20000r/min above 10,000 for high-speed cutting; Feed at high velocity, usually 15 -50m/min up to 90m/min; For different cutting materials and the wiring used the tool material, high-speed cutting the meaning is not necessarily the same; Cutting process, bladed through frequency (Tooth Passing Frequency) closer to the "machine-tool - Workpiece "system the dominant natural frequency (Dominant Natural Frequency), can be considered to be high-speed cutting. Visibility high-speed machining is a comprehensive concept.1992. Germany, the Darmstadt University of Technology, Professor H. Schulz in the 52th on the increase of high-speed cutting for the concept and the scope, as shown in Figure 1. Think different cutting targets, shown in the figure of the transition area (Transition), to be what is commonly called the high-speed cutting, This is also the time of metal cutting process related to the technical staff are looking forward to, or is expected to achieve the cutting speed.High-speed machining of machine tools, knives and cutting process, and other aspects specific requirements. Several were from the following aspects : high-speed machining technology development status and trends.At this stage, in order to achieve high-speed machining, general wiring with high flexibility of high-speed CNC machine tools, machining centers, By using a dedicated high-speed milling, drilling. These equipment in common is : We must also have high-speed and high-speed spindle system feeding system, Cutting can be achieved in high-speed process. High-speed cutting with the traditional cutting the biggest difference is that "Machine-tool-workpiece" the dynamic characteristics of cutting performance is stronger influence. In the system, the machine spindle stiffness, grip or form, a long knife set, spindle Broach, torque tool set, Performance high-speed impact are important factors.In the high-speed cutting, material removal rate (Metal Removal Rate, MRR), unit time that the material was removed volume, usually based on the "machine-tool-workpiece" whether Processing System "chatter." Therefore, in order to satisfy the high-speed machining needs, we must first improve the static and dynamic stiffness of machine spindle is particularly the stiffness characteristics. HSC reason at this stage to be successful, a very crucial factor is the dynamic characteristics of the master and processing capability.In order to better describe the machine spindle stiffness characteristics of the project presented new dimensionless parameter - DN value, used for the evaluation of the machine tool spindle structure on the high-speed machining of adaptability. DN value of the so-called "axis diameter per minute speed with the product." The newly developed spindle machining center DN values have been great over one million. To reduce the weight bearing, but also with an array of steel products than to the much more light ceramic ball bearings; Bearing Lubrication most impressive manner mixed with oil lubrication methods. In the field of high-speed machining. have air bearings and the development of magnetic bearings and magnetic bearings and air bearings combined constitute the magnetic gas / air mixing spindle.Feed the machine sector, high-speed machining used in the feed drive is usually larger lead, multiple high-speed ball screw and ball array of small-diameter silicon nitride (Si3N4) ceramic ball, to reduce its centrifugal and gyroscopic torque; By using hollow-cooling technology to reduce operating at high speed ball screw as temperature generated by the friction between the lead screw and thermal deformation.In recent years, the use of linear motor-driven high-speed system of up to'' Such feed system has removed the motor from workstations to Slide in the middle of all mechanical transmission links, Implementation of Machine Tool Feed System of zero transmission. Because no linear motor rotating components, from the role of centrifugal force, can greatly increase the feed rate. Linear Motor Another major advantage of the trip is unrestricted. The linear motor is a very time for a continuous machine shop in possession of the bed. Resurfacing of the very meeting where avery early stage movement can go, but the whole system of up to the stiffness without any influence. By using high-speed screw, or linear motor can greatly enhance machine system of up to the rapid response. The maximum acceleration linear motors up to 2-10G (G for the acceleration of gravity), the largest feed rate of up to 60 -200m/min or higher.2002 world-renowned Shanghai Pudong maglev train project of maglev track steel processing, Using the Shenyang Machine Tool Group Holdings Limited McNair friendship company production plants into extra-long high-speed system for large-scale processing centers achieve . The machine feeding system for the linear guide and rack gear drive, the largest table feed rate of 60 m / min, Quick trip of 100 m / min, 2 g acceleration, maximum speed spindle 20000 r / min, the main motor power 80 kW. X-axis distance of up to 30 m, 25 m cutting long maglev track steel error is less than 0.15 mm. Maglev trains for the smooth completion of the project provided a strong guarantee for technologyIn addition, the campaign machine performance will also directly affect the processing efficiency and accuracy of processing. Mold and the free surface of high-speed machining, the main wiring with small cut deep into methods for processing. Machine requirements in the feed rate conditions, should have high-precision positioning functions andhigh-precision interpolation function, especially high-precision arc interpolation. Arc processing is to adopt legislation or thread milling cutter mold or machining parts, the essential processing methods. Cutting Tools Tool Material developmenthigh-speed cutting and technological development of the history, tool material is continuous progress of history. The representation ofhigh-speed cutting tool material is cubic boron nitride (CBN). Face Milling Cutter use of CBN, its cutting speed can be as high as 5000 m / min, mainly for the gray cast iron machining. Polycrystalline diamond (PCD) has been described as a tool of the 21st century tool, It is particularly applicable to the cutting aluminum alloy containing silica material, which is light weight metal materials, high strength, widely used in the automobile, motorcycle engine, electronic devices shell, the base, and so on. At present, the use of polycrystalline diamond cutter Face Milling alloy, 5000m/min the cutting speed has reached a practical level. In addition ceramic tool also applies to gray iron of high-speed machining; Tool Coating : CBN and diamond cutter, despite good high-speed performance, but the cost is relatively high. Using the coating technology to make cutting tool is the low price, with excellent mechanical properties, which can effectively reduce the cost. Now high-speed processing of milling cutter, with most of the wiring between the Ti-A1-N composite technology for the way of multi-processing, If present in the non-ferrous metal or alloy material dry cutting, DLC (Diamond Like Carbon) coating on thecutter was of great concern. It is expected that the market outlook is very significant;Tool clamping system : Tool clamping system to support high-speed cutting is an important technology, Currently the most widely used is a two-faced tool clamping system. Has been formally invested as a commodity market at the same clamping tool system are : HSK, KM, Bigplus. NC5, AHO systems. In the high-speed machining, tool and fixture rotary performance of the balance not only affects the precision machining and tool life. it will also affect the life of machine tools. So, the choice of tool system, it should be a balanced selection of good products.Process ParametersCutting speed of high-speed processing of conventional shear velocity of about 10 times. For every tooth cutter feed rate remained basically unchanged, to guarantee parts machining precision, surface quality and durability of the tool, Feed volume will also be a corresponding increase about 10 times, reaching 60 m / min, Some even as high as 120 m / min. Therefore, high-speed machining is usually preclude the use of high-speed, feed and depth of cut small cutting parameters. Due to the high-speed machining cutting cushion tend to be small, the formation of very thin chip light, Cutting put the heat away quickly; If the wiring using a new thermal stability better tool materials and coatings, Using the dry cutting process for high-speed machining is the ideal technology program. High-speed machining field of applicationFlexible efficient production lineTo adapt to the needs of new models, auto body panel molds andresin-prevention block the forming die. must shorten the production cycle and reduce the cost of production and, therefore, we must make great efforts to promote the production of high-speed die in the process. SAIC affiliated with the company that : Compared to the past, finishing, further precision; the same time, the surface roughness must be met, the bending of precision, this should be subject to appropriate intensive manual processing. Due to the extremely high cutting speed, and the last finishing processes, the processing cycle should be greatly reduced. To play for machining centers and boring and milling machining center category represented by the high-speed machining technology and automatic tool change function of distinctions Potential to improve processing efficiency, the processing of complex parts used to be concentrated as much as possible the wiring process, that is a fixture in achieving multiple processes centralized processing and dilute the traditional cars, milling, boring, Thread processing different cutting the limits of technology, equipment and give full play to the high-speed cutting tool function, NC is currently raising machine efficiency and speed up product development in an effective way. Therefore, the proposed multi-purpose tool of the new requirements call for a tool to complete different partsof the machining processes, ATC reduce the number of ATC to save time, to reduce the quantity and tool inventory, and management to reduce production costs. More commonly used in a multifunctional Tool, milling, boring and milling, drilling milling, drilling-milling thread-range tool. At the same time, mass production line, against the use of technology requires the development of special tools, tool or a smart composite tool, improve processing efficiency and accuracy and reduced investment. In the high-speed cutting conditions, and some special tools can be part of the processing time to the original 1 / 10 below, results are quite remarkable. HSC has a lot of advantages such as : a large number of materials required resection of the workpiece with ultrafine, thin structure of the workpiece, Traditionally, the need to spend very long hours for processing mobile workpiece and the design of rapid change, short product life cycle of the workpiece, able to demonstrate high-speed cutting brought advantages.中文译文高速切削加工的发展及需求高速切削加工是当代先进制造技术的重要组成部分,拥有高效率、高精度及高表面质量等特征。
文献翻译-五种基本机械加工技术
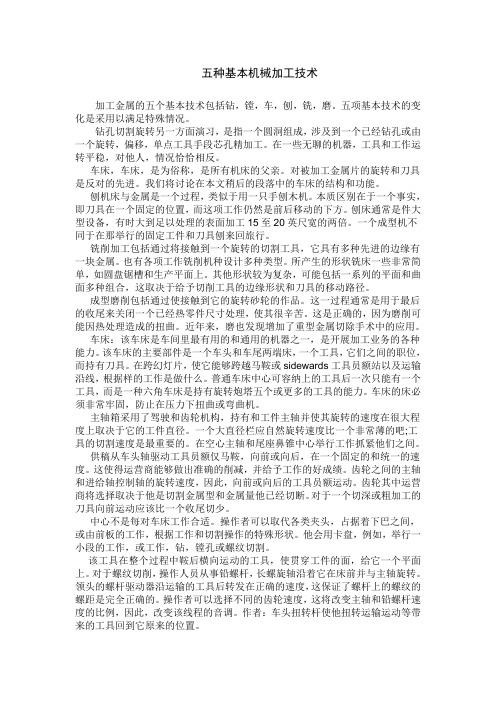
五种基本机械加工技术加工金属的五个基本技术包括钻,镗,车,刨,铣,磨。
五项基本技术的变化是采用以满足特殊情况。
钻孔切割旋转另一方面演习,是指一个圆洞组成,涉及到一个已经钻孔或由一个旋转,偏移,单点工具手段芯孔精加工。
在一些无聊的机器,工具和工作运转平稳,对他人,情况恰恰相反。
车床,车床,是为俗称,是所有机床的父亲。
对被加工金属片的旋转和刀具是反对的先进。
我们将讨论在本文稍后的段落中的车床的结构和功能。
刨机床与金属是一个过程,类似于用一只手刨木机。
本质区别在于一个事实,即刀具在一个固定的位置,而这项工作仍然是前后移动的下方。
刨床通常是件大型设备,有时大到足以处理的表面加工15至20英尺宽的两倍。
一个成型机不同于在那举行的固定工件和刀具刨来回旅行。
铣削加工包括通过将接触到一个旋转的切割工具,它具有多种先进的边缘有一块金属。
也有各项工作铣削机种设计多种类型。
所产生的形状铣床一些非常简单,如圆盘锯槽和生产平面上。
其他形状较为复杂,可能包括一系列的平面和曲面多种组合,这取决于给予切削工具的边缘形状和刀具的移动路径。
成型磨削包括通过使接触到它的旋转砂轮的作品。
这一过程通常是用于最后的收尾来关闭一个已经热零件尺寸处理,使其很辛苦。
这是正确的,因为磨削可能因热处理造成的扭曲。
近年来,磨也发现增加了重型金属切除手术中的应用。
车床:该车床是车间里最有用的和通用的机器之一,是开展加工业务的各种能力。
该车床的主要部件是一个车头和车尾两端床,一个工具,它们之间的职位,而持有刀具。
在跨幻灯片,使它能够跨越马鞍或sidewards工具员额站以及运输沿线,根据样的工作是做什么。
普通车床中心可容纳上的工具后一次只能有一个工具,而是一种六角车床是持有旋转炮塔五个或更多的工具的能力。
车床的床必须非常牢固,防止在压力下扭曲或弯曲机。
主轴箱采用了驾驶和齿轮机构,持有和工件主轴并使其旋转的速度在很大程度上取决于它的工件直径。
一个大直径栏应自然旋转速度比一个非常薄的吧;工具的切割速度是最重要的。
机床的论文中英文资料外文翻译文献
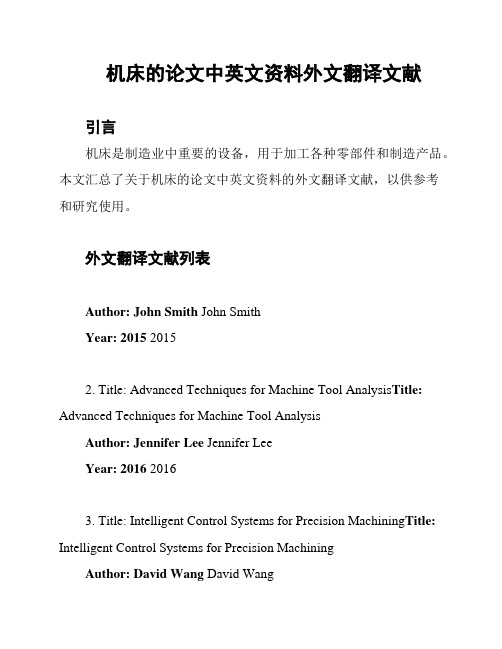
机床的论文中英文资料外文翻译文献引言机床是制造业中重要的设备,用于加工各种零部件和制造产品。
本文汇总了关于机床的论文中英文资料的外文翻译文献,以供参考和研究使用。
外文翻译文献列表Author: John Smith John SmithYear: 2015 20152. Title: Advanced Techniques for Machine Tool Analysis Title: Advanced Techniques for Machine Tool AnalysisAuthor: Jennifer Lee Jennifer LeeYear: 2016 20163. Title: Intelligent Control Systems for Precision Machining Title: Intelligent Control Systems for Precision MachiningAuthor: David Wang David WangYear: 2018 2018Abstract: This paper focuses on intelligent control systems for precision machining. It discusses the integration of artificial intelligence and control algorithms to enhance the precision and performance of machine tools. The paper presents case studies on the application of intelligent control systems in precision machining processes. This paper focuses on intelligent control systems for precision machining. It discusses the integration of artificial intelligence and control algorithms to enhance the precision and performance of machine tools. The paper presents case studies on the application of intelligent control systems in precision machining processes.4. Title: Advances in Machining Processes for Hard-to-Machine Materials Title: Advances in Machining Processes for Hard-to-Machine MaterialsAuthor: Emily Chen Emily ChenYear: 2019 2019Abstract: This paper reviews recent advances in machining processes for hard-to-machine materials. It discusses the challenges associated with machining materials such as titanium, nickel-basedalloys, and ceramics. The paper highlights the development of new cutting tools, machining strategies, and technologies to improve the machinability of these materials. This paper reviews recent advances in machining processes for hard-to-machine materials. It discusses the challenges associated with machining materials such as titanium, nickel-based alloys, and ceramics. The paper highlights the development of new cutting tools, machining strategies, and technologies to improve the machinability of these materials.5. Title: Optimization of Machining Parameters for Energy Efficiency Title: Optimization of Machining Parameters for Energy EfficiencyAuthor: Michael Liu Michael LiuYear: 2020 2020Abstract: This paper explores the optimization of machining parameters for energy efficiency. It discusses the impact of machining parameters, such as cutting speed, feed rate, and depth of cut, on energy consumption in machining processes. The paper presents optimization techniques and case studies on reducing energy consumption in machining operations. This paper explores theoptimization of machining parameters for energy efficiency. It discusses the impact of machining parameters, such as cutting speed, feed rate, and depth of cut, on energy consumption in machining processes. The paper presents optimization techniques and case studies on reducing energy consumption in machining operations.结论以上是关于机床的论文中英文资料的外文翻译文献,希望对研究和了解机床技术的人员有所帮助。
机械加工毕业论文中英文资料外文翻译文献
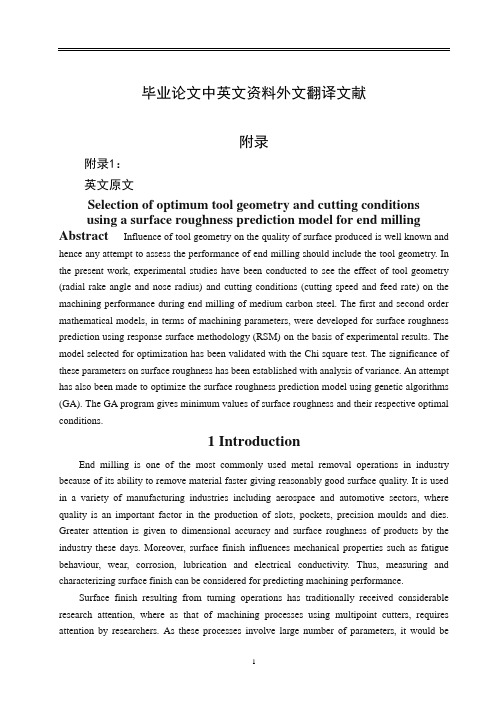
毕业论文中英文资料外文翻译文献附录附录1:英文原文Selection of optimum tool geometry and cutting conditionsusing a surface roughness prediction model for end milling Abstract Influence of tool geometry on the quality of surface produced is well known and hence any attempt to assess the performance of end milling should include the tool geometry. In the present work, experimental studies have been conducted to see the effect of tool geometry (radial rake angle and nose radius) and cutting conditions (cutting speed and feed rate) on the machining performance during end milling of medium carbon steel. The first and second order mathematical models, in terms of machining parameters, were developed for surface roughness prediction using response surface methodology (RSM) on the basis of experimental results. The model selected for optimization has been validated with the Chi square test. The significance of these parameters on surface roughness has been established with analysis of variance. An attempt has also been made to optimize the surface roughness prediction model using genetic algorithms (GA). The GA program gives minimum values of surface roughness and their respective optimal conditions.1 IntroductionEnd milling is one of the most commonly used metal removal operations in industry because of its ability to remove material faster giving reasonably good surface quality. It is used in a variety of manufacturing industries including aerospace and automotive sectors, where quality is an important factor in the production of slots, pockets, precision moulds and dies. Greater attention is given to dimensional accuracy and surface roughness of products by the industry these days. Moreover, surface finish influences mechanical properties such as fatigue behaviour, wear, corrosion, lubrication and electrical conductivity. Thus, measuring and characterizing surface finish can be considered for predicting machining performance.Surface finish resulting from turning operations has traditionally received considerable research attention, where as that of machining processes using multipoint cutters, requires attention by researchers. As these processes involve large number of parameters, it would bedifficult to correlate surface finish with other parameters just by conducting experiments. Modelling helps to understand this kind of process better. Though some amount of work has been carried out to develop surface finish prediction models in the past, the effect of tool geometry has received little attention. However, the radial rake angle has a major affect on the power consumption apart from tangential and radial forces. It also influences chip curling and modifies chip flow direction. In addition to this, researchers [1] have also observed that the nose radius plays a significant role in affecting the surface finish. Therefore the development of a good model should involve the radial rake angle and nose radius along with other relevant factors.Establishment of efficient machining parameters has been a problem that has confronted manufacturing industries for nearly a century, and is still the subject of many studies. Obtaining optimum machining parameters is of great concern in manufacturing industries, where the economy of machining operation plays a key role in the competitive market. In material removal processes, an improper selection of cutting conditions cause surfaces with high roughness and dimensional errors, and it is even possible that dynamic phenomena due to auto excited vibrations may set in [2]. In view of the significant role that the milling operation plays in today’s manufacturing world, there is a need to optimize the machining parameters for this operation. So, an effort has been made in this paper to see the influence of tool geometry(radial rake angle and nose radius) and cutting conditions(cutting speed and feed rate) on the surface finish produced during end milling of medium carbon steel. The experimental results of this work will be used to relate cutting speed, feed rate, radial rake angle and nose radius with the machining response i.e. surface roughness by modelling. The mathematical models thus developed are further utilized to find the optimum process parameters using genetic algorithms.2 ReviewProcess modelling and optimization are two important issues in manufacturing. The manufacturing processes are characterized by a multiplicity of dynamically interacting process variables. Surface finish has been an important factor of machining in predicting performance of any machining operation. In order to develop and optimize a surface roughness model, it is essential to understand the current status of work in this area.Davis et al. [3] have investigated the cutting performance of five end mills having various helix angles. Cutting tests were performed on aluminium alloy L 65 for three milling processes (face, slot and side), in which cutting force, surface roughness and concavity of a machined plane surface were measured. The central composite design was used to decide on the number of experiments to be conducted. The cutting performance of the end mills was assessed usingvariance analysis. The affects of spindle speed, depth of cut and feed rate on the cutting force and surface roughness were studied. The investigation showed that end mills with left hand helix angles are generally less cost effective than those with right hand helix angles. There is no significant difference between up milling and down milling with regard tothe cutting force, although the difference between them regarding the surface roughness was large. Bayoumi et al.[4] have studied the affect of the tool rotation angle, feed rate and cutting speed on the mechanistic process parameters (pressure, friction parameter) for end milling operation with three commercially available workpiece materials, 11 L 17 free machining steel, 62- 35-3 free machining brass and 2024 aluminium using a single fluted HSS milling cutter. It has been found that pressure and friction act on the chip – tool interface decrease with the increase of feed rate and with the decrease of the flow angle, while the cutting speed has a negligible effect on some of the material dependent parameters. Process parameters are summarized into empirical equations as functions of feed rate and tool rotation angle for each work material. However, researchers have not taken into account the effects of cutting conditions and tool geometry simultaneously; besides these studies have not considered the optimization of the cutting process.As end milling is a process which involves a large number f parameters, combined influence of the significant parameters an only be obtained by modelling. Mansour and Abdallaet al. [5] have developed a surface roughness model for the end milling of EN32M (a semi-free cutting carbon case hardening steel with improved merchantability). The mathematical model has been developed in terms of cutting speed, feed rate and axial depth of cut. The affect of these parameters on the surface roughness has been carried out using response surface methodology (RSM). A first order equation covering the speed range of 30–35 m/min and a second order equation covering the speed range of 24–38 m/min were developed under dry machining conditions. Alauddin et al. [6] developed a surface roughness model using RSM for the end milling of 190 BHN steel. First and second order models were constructed along with contour graphs for the selection of the proper combination of cutting speed and feed to increase the metal removal rate without sacrificing surface quality. Hasmi et al. [7] also used the RSM model for assessing the influence of the workpiece material on the surface roughness of the machined surfaces. The model was developed for milling operation by conducting experiments on steel specimens. The expression shows, the relationship between the surface roughness and the various parameters; namely, the cutting speed, feed and depth of cut. The above models have not considered the affect of tool geometry on surface roughness.Since the turn of the century quite a large number of attempts have been made to find optimum values of machining parameters. Uses of many methods have been reported in the literature to solve optimization problems for machining parameters. Jain and Jain [8] have usedneural networks for modeling and optimizing the machining conditions. The results have been validated by comparing the optimized machining conditions obtained using genetic algorithms. Suresh et al. [9] have developed a surface roughness prediction model for turning mild steel using a response surface methodology to produce the factor affects of the individual process parameters. They have also optimized the turning process using the surface roughness prediction model as the objective function. Considering the above, an attempt has been made in this work to develop a surface roughness model with tool geometry and cutting conditions on the basis of experimental results and then optimize it for the selection of these parameters within the given constraints in the end milling operation.3 MethodologyIn this work, mathematical models have been developed using experimental results with the help of response surface methodolog y. The purpose of developing mathematical models relating the machining responses and their factors is to facilitate the optimization of the machining process. This mathematical model has been used as an objective function and the optimization was carried out with the help of genetic algorithms.3.1 Mathematical formulationResponse surface methodology(RSM) is a combination of mathematical and statistical techniques useful for modelling and analyzing the problems in which several independent variables influence a dependent variable or response. The mathematical models commonly used are represented by:where Y is the machining response, ϕ is the response function and S, f , α, r are milling variables and ∈is the error which is normally distributed about the observed response Y with zero mean.The relationship between surface roughness and other independent variables can be represented as follows,where C is a constant and a, b, c and d are exponents.To facilitate the determination of constants and exponents, this mathematical model will have to be linearized by performing a logarithmic transformation as follows:The constants and exponents C, a, b, c and d can be determined by the method of least squares. The first order linear model, developed from the above functional relationship using least squares method, can be represented as follows:where Y1 is the estimated response based on the first-order equation, Y is the measured surface roughness on a logarithmic scale, x0 = 1 (dummy variable), x1, x2, x3 and x4 are logarithmic transformations of cutting speed, feed rate, radial rake angle and nose radiusrespectively, ∈is the experimental error and b values are the estimates of corresponding parameters.The general second order polynomial response is as given below:where Y2 is the estimated response based on the second order equation. The parameters, i.e. b0, b1, b2, b3, b4, b12, b23, b14, etc. are to be estimated by the method of least squares. Validity of the selected model used for optimizing the process parameters has been tested with the help of statistical tests, such as F-test, chi square test, etc. [10].3.2 Optimization using genetic algorithmsMost of the researchers have used traditional optimization techniques for solving machining problems. The traditional methods of optimization and search do not fare well over a broad spectrum of problem domains. Traditional techniques are not efficient when the practical search space is too large. These algorithms are not robust. They are inclined to obtain a local optimal solution. Numerous constraints and number of passes make the machining optimization problem more complicated. So, it was decided to employ genetic algorithms as an optimization technique. GA come under the class of non-traditional search and optimization techniques. GA are different from traditional optimization techniques in the following ways:1.GA work with a coding of the parameter set, not the parameter themselves.2.GA search from a population of points and not a single point.3.GA use information of fitness function, not derivatives or other auxiliary knowledge.4.GA use probabilistic transition rules not deterministic rules.5.It is very likely that the expected GA solution will be the global solution.Genetic algorithms (GA) form a class of adaptive heuristics based on principles derived from the dynamics of natural population genetics. The searching process simulates the natural evaluation of biological creatures and turns out to be an intelligent exploitation of a random search. The mechanics of a GA is simple, involving copying of binary strings. Simplicity of operation and computational efficiency are the two main attractions of the genetic algorithmic approach. The computations are carried out in three stages to get a result in one generation or iteration. The three stages are reproduction, crossover and mutation.In order to use GA to solve any problem, the variable is typically encoded into a string (binary coding) or chromosome structure which represents a possible solution to the given problem. GA begin with a population of strings (individuals) created at random. The fitness of each individual string is evaluated with respect to the given objective function. Then this initial population is operated on by three main operators – reproduction cross over and mutation– to create, hopefully, a better population. Highly fit individuals or solutions are given theopportunity to reproduce by exchanging pieces of their genetic information, in the crossover procedure, with other highly fit individuals. This produces new “offspring” solutions, which share some characteristics taken from both the parents. Mutation is often applied after crossover by altering some genes (i.e. bits) in the offspring. The offspring can either replace the whole population (generational approach) or replace less fit individuals (steady state approach). This new population is further evaluated and tested for some termination criteria. The reproduction-cross over mutation- evaluation cycle is repeated until the termination criteria are met.4 Experimental detailsFor developing models on the basis of experimental data, careful planning of experimentation is essential. The factors considered for experimentation and analysis were cutting speed, feed rate, radial rake angle and nose radius.4.1 Experimental designThe design of experimentation has a major affect on the number of experiments needed. Therefore it is essential to have a well designed set of experiments. The range of values of each factor was set at three different levels, namely low, medium and high as shown in Table 1. Based on this, a total number of 81 experiments (full factorial design), each having a combination of different levels of factors, as shown in Table 2, were carried out.The variables were coded by taking into account the capacity and limiting cutting conditions of the milling machine. The coded values of variables, to be used in Eqs. 3 and 4, were obtained from the following transforming equations:where x1 is the coded value of cutting speed (S), x2 is the coded value of the feed rate ( f ), x3 is the coded value of radial rake angle(α) and x4 is the coded value of nose radius (r).4.2 ExperimentationA high precision ‘Rambaudi Rammatic 500’ CNC milling machine, with a vertical milling head, was used for experimentation. The control system is a CNC FIDIA-12 compact. The cutting tools, used for the experimentation, were solid coated carbide end mill cutters of different radial rake angles and nose radii (WIDIA: DIA20 X FL38 X OAL 102 MM). The tools are coated with TiAlN coating. The hardness, density and transverse rupture strength are 1570 HV 30, 14.5 gm/cm3 and 3800 N/mm2 respectively.AISI 1045 steel specimens of 100×75 mm and 20 mm thickness were used in the present study. All the specimens were annealed, by holding them at 850 ◦C for one hour and then cooling them in a furnace. The chemical analysis of specimens is presented in Table 3. Thehardness of the workpiece material is 170 BHN. All the experiments were carried out at a constant axial depth of cut of 20 mm and a radial depth of cut of 1 mm. The surface roughness (response) was measured with Talysurf-6 at a 0.8 mm cut-off value. An average of four measurements was used as a response value.5 Results and discussionThe influences of cutting speed, feed rate, radial rake angle and nose radius have been assessed by conducting experiments. The variation of machining response with respect to the variables was shown graphically in Fig. 1. It is seen from these figures that of the four dependent parameters, radial rake angle has definite influence on the roughness of the surface machined using an end mill cutter. It is felt that the prominent influence of radial rake angle on the surface generation could be due to the fact that any change in the radial rake angle changes the sharpness of the cutting edge on the periphery, i.e changes the contact length between the chip and workpiece surface. Also it is evident from the plots that as the radial rake angle changes from 4◦to 16◦, the surface roughness decreases and then increases. Therefore, it may be concluded here that the radial rake angle in the range of 4◦to 10◦would give a better surface finish. Figure 1 also shows that the surface roughness decreases first and then increases with the increase in the nose radius. This shows that there is a scope for finding the optimum value of the radial rake angle and nose radius for obtaining the best possible quality of the surface. It was also found that the surface roughness decreases with an increase in cutting speed and increases as feed rate increases. It could also be observed that the surface roughness was a minimum at the 250 m/min speed, 200 mm/min feed rate, 10◦radial rake angle and 0.8 mm nose radius. In order to understand the process better, the experimental results can be used to develop mathematical models using RSM. In this work, a commercially available mathematical software package (MATLAB) was used for the computation of the regression of constants and exponents.5.1 The roughness modelUsing experimental results, empirical equations have been obtained to estimate surface roughness with the significant parameters considered for the experimentation i.e. cutting speed, feed rate, radial rake angle and nose radius. The first order model obtained from the above functional relationship using the RSM method is as follows:The transformed equation of surface roughness prediction is as follows:Equation 10 is derived from Eq. 9 by substituting the coded values of x1, x2, x3 and x4 in termsof ln s, ln f , lnαand ln r. The analysis of the variance (ANOV A) and the F-ratio test have been performed to justify the accuracy of the fit for the mathematical model. Since the calculated values of the F-ratio are less than the standard values of the F-ratio for surface roughness as shown in Table 4, the model is adequate at 99% confidence level to represent the relationship between the machining response and the considered machining parameters of the end milling process.The multiple regression coefficient of the first order model was found to be 0.5839. This shows that the first order model can explain the variation in surface roughness to the extent of 58.39%. As the first order model has low predictability, the second order model has been developed to see whether it can represent better or not.The second order surface roughness model thus developed is as given below:where Y2 is the estimated response of the surface roughness on a logarithmic scale, x1, x2, x3 and x4 are the logarithmic transformation of speed, feed, radial rake angle and nose radius. The data of analysis of variance for the second order surface roughness model is shown in Table 5.Since F cal is greater than F0.01, there is a definite relationship between the response variable and independent variable at 99% confidence level. The multiple regression coefficient of the second order model was found to be 0.9596. On the basis of the multiple regression coefficient (R2), it can be concluded that the second order model was adequate to represent this process. Hence the second order model was considered as an objective function for optimization using genetic algorithms. This second order model was also validated using the chi square test. The calculated chi square value of the model was 0.1493 and them tabulated value at χ2 0.005 is 52.34, as shown in Table 6, which indicates that 99.5% of the variability in surface roughness was explained by this model.Using the second order model, the surface roughness of the components produced by end milling can be estimated with reasonable accuracy. This model would be optimized using genetic algorithms (GA).5.2 The optimization of end millingOptimization of machining parameters not only increases the utility for machining economics, but also the product quality toa great extent. In this context an effort has been made to estimate the optimum tool geometry and machining conditions to produce the best possible surface quality within the constraints.The constrained optimization problem is stated as follows: Minimize Ra using the model given here:where xil and xiu are the upper and lower bounds of process variables xi and x1, x2, x3, x4 are logarithmic transformation of cutting speed, feed, radial rake angle and nose radius.The GA code was developed using MATLAB. This approach makes a binary coding system to represent the variables cutting speed (S), feed rate ( f ), radial rake angle (α) and nose radius (r), i.e. each of these variables is represented by a ten bit binary equivalent, limiting the total string length to 40. It is known as a chromosome. The variables are represented as genes (substrings) in the chromosome. The randomly generated 20 such chromosomes (population size is 20), fulfilling the constraints on the variables, are taken in each generation. The first generation is called the initial population. Once the coding of the variables has been done, then the actual decoded values for the variables are estimated using the following formula: where xi is the actual decoded value of the cutting speed, feed rate, radial rake angle and nose radius, x(L) i is the lower limit and x(U) i is the upper limit and li is the substring length, which is equal to ten in this case.Using the present generation of 20 chromosomes, fitness values are calculated by the following transformation:where f(x) is the fitness function and Ra is the objective function.Out of these 20 fitness values, four are chosen using the roulette-wheel selection scheme. The chromosomes corresponding to these four fitness values are taken as parents. Then the crossover and mutation reproduction methods are applied to generate 20 new chromosomes for the next generation. This processof generating the new population from the old population is called one generation. Many such generations are run till the maximum number of generations is met or the average of four selected fitness values in each generation becomes steady. This ensures that the optimization of all the variables (cutting speed, feed rate, radial rake angle and nose radius) is carried out simultaneously. The final statistics are displayed at the end of all iterations. In order to optimize the present problem using GA, the following parameters have been selected to obtain the best possible solution with the least computational effort: Table 7 shows some of the minimum values of the surface roughness predicted by the GA program with respect to input machining ranges, and Table 8 shows the optimum machining conditions for the corresponding minimum values of the surface roughness shown in Table 7. The MRR given in Table 8 was calculated bywhere f is the table feed (mm/min), aa is the axial depth of cut (20 mm) and ar is the radial depth of cut (1 mm).It can be concluded from the optimization results of the GA program that it is possible toselect a combination of cutting speed, feed rate, radial rake angle and nose radius for achieving the best possible surface finish giving a reasonably good material removal rate. This GA program provides optimum machining conditions for the corresponding given minimum values of the surface roughness. The application of the genetic algorithmic approach to obtain optimal machining conditions will be quite useful at the computer aided process planning (CAPP) stage in the production of high quality goods with tight tolerances by a variety of machining operations, and in the adaptive control of automated machine tools. With the known boundaries of surface roughness and machining conditions, machining could be performed with a relatively high rate of success with the selected machining conditions.6 ConclusionsThe investigations of this study indicate that the parameters cutting speed, feed, radial rake angle and nose radius are the primary actors influencing the surface roughness of medium carbon steel uring end milling. The approach presented in this paper provides n impetus to develop analytical models, based on experimental results for obtaining a surface roughness model using the response surface methodology. By incorporating the cutter geometry in the model, the validity of the model has been enhanced. The optimization of this model using genetic algorithms has resulted in a fairly useful method of obtaining machining parameters in order to obtain the best possible surface quality.中文翻译选择最佳工具,几何形状和切削条件利用表面粗糙度预测模型端铣摘要:刀具几何形状对工件表面质量产生的影响是人所共知的,因此,任何成型面端铣设计应包括刀具的几何形状。
机械类数控车床外文翻译外文文献英文文献数控

数控加工中心技术发展趋势及对策原文来源:Zhao Chang-ming Liu Wang-ju (CNC Machining Process and equipment, 2002,China)一、摘要Equip the engineering level, level of determining the whole national economy of the modernized degree and modernized degree of industry, numerical control technology is it develop new developing new high-tech industry and most advanced industry to equip (such as information technology and his industry, biotechnology and his industry, aviation, spaceflight, etc. national defense industry) last technology and getting more basic most equipment. Numerical control technology is the technology controlled to mechanical movement and working course with digital information, integrated products of electromechanics that the numerical control equipment is the new technology represented by numerical control technology forms to the manufacture industry of the tradition and infiltration of the new developing manufacturing industry,Keywords:Numerical ControlTechnology, E quipment,industry二、译文数控技术和装备发展趋势及对策装备工业的技术水平和现代化程度决定着整个国民经济的水平和现代化程度,数控技术及装备是发展新兴高新技术产业和尖端工业(如信息技术及其产业、生物技术及其产业、航空、航天等国防工业产业)的使能技术和最基本的装备。
[铣削机械加工外文翻译、中英文翻译、机械类外文文献翻译]外文翻译
![[铣削机械加工外文翻译、中英文翻译、机械类外文文献翻译]外文翻译](https://img.taocdn.com/s3/m/87d8048903d276a20029bd64783e0912a2167ca2.png)
[铣削机械加工外文翻译、中英文翻译、机械类外文文献翻译]外文翻译本科毕业论文〔设计〕相关中英文翻译资料资料题目:铣削学生姓名:所在院系:机电学院所学专业:机电技术教育MILLING Milling is bsic mchining process in which the surfce is generted by the progressive formtion nd removl of chips of mteril from the workpiece s it is fed to rotting cutter in direction perpendiculr to the xis of the cutter. In some cses the workpiece is sttionry nd the cutter is fed to the work. In most instnces multiple-tooth cutter is used so tht the metl removl rte is high, nd frequently the desired surfce is obtined in single pss of the work. The tool used in milling is known s milling cutter. It usully consists of cylindricl body which rottes on its xis nd contins eqully spced peripherl teeth tht intermittently engge nd cut the workpiece. 1 In some cses the teeth extend prt wy cross one or both Ends of the cylinder. Becuse the milling principle provides rpid metl removl nd cn produce good surfce finish, it is prticulrly well-suited for mss-production work, nd excellent milling mchines hve been developed for this purpose. However, very ccurte nd verstile millingMchines of generl-purpose nture lso hve been developed tht re widely used in jobshop nd tool nd die work. shop tht is equipped with milling mchine nd n engine lthe cn mchine lmost ny type of product of suitble size. Types of Milling Opertions. Milling opertions cn be clssified into two brod ctegories, ech of which hs severl vritions: 1. In peripherl milling surfce is generted by teeth locted in the periphery of the cutter body; the surfce is prllel with the xis of rottion of the cutter. Both flt nd formed surfces cn be produced by this method. The cross section of the resulting surfce corresponds to the xil contour of the cutter. This procedure often is clled slb milling. 2. In fce milling the generted flt surfce is t right ngles to the cutter xis nd is the combined result of the ctions of the portions of the teeth locted on both the periphery nd the fce of the cutter. 2 The mjor portion of the cutting is done by the peripherl portions of the teeth with the fce portions providing finishing ction. The bsic concepts of peripherl nd fce milling re illustrted in Fig. 16-1. Peripherl milling opertions usully re performed on mchines hving horizontl spindles, wheres fce milling is done on both horizontl- nd verticl-spindle mchines.Surfce Genertion in Mimng. Surfces cn be generted in milling by two distinctly different methods depicted in Fig. 16-2. Note tht in up milling the cutter rottes ginsi the direction of feed the workpiece, wheres in down milling the rottion is in the sme direction s the feed. s shown in Fig. 16-2, the method of chip formtion is quite different in the two cses. In up milling the c hip is very thin t the beginning, where the tooth first contcts the work, nd increses in thickness, becoming mximum where the tooth leves the work. The cutter tends topush the work long nd lift it upwrd from Tool-work reltionshios in peripherl nd fce milling the tble. This ction tends to eliminte ny effect of looseness in the feed screw nd nut of the milling mchine tble nd results in smooth cut. However, the ction lso tends to loosen the work from the clmping device so tht greter clmping forcers must be employed. In ddition, the smoothness of the generted surfce depends gretly on the shrpness of the cutting edges. In down milling, mximum chip thickness cecum close to the point t which the tooth contcts the work. Becuse the reltive motion tends to pull the workpiece into the cutter, ll possibility of looseness in the tble feed screwmust be eliminted if down milling is to be used. It should never be ttempted on mchines tht re not designed for this type of milling. Insmush s the mteril yields in pproximtely tngentil direction t the end of the tooth enggement, there is much less tendency for the mchined surfce to show tooth mrks thn when up milling is used. nother considerble dvntge of down milling is tht the cutting force tends to hold the work ginst the mchine tble, permitting lower clmping force to be employed. 3 This is prticulrly dvntgeous when milling thin workpiece or when tking hevy cuts. Sometimes disdvntge of down milling is tht the cutter teeth strike ginst the surfce of the work t the beginning of ech chip. When the workpiece hs hrd surfce, such s cstings do, this my cuse the teeth to dull rpidly. Milling Cutters. Milling cutters cn be clssified severl wys. One method is to group them into two brod clsses, bsed on tooth relief, s follows: 1.Profile-cutters hve relief provided on ech tooth by grinding smll lnd bck of the cutting edge. The cutting edge my be stright or curved.2.In form or cm-reheved cutters the cross section of ech tooth is n eccentric curve behind the cutting edge, thus providing relief. ll sections of the eccentric relief, prllel withthe cutting edge, must hve the sme contour s the cutting edge. Cutters of this type re shrpened by grinding only the fce of the teeth, with the contour of the cutting edge thus remining unchnged. nother useful method of clssifiction is ccording to the method of mounting the cutter. rbor cutters re those tht hve center hole so they cn be mounted on n rbor. Shnk cutters hve either tpered or stright integrl shnk. Those with tpered shnks cn be mounted directly in the milling mchine spindle, wheres stright-shnk cutters re held in chuck. Fcing cutters usully re bolted to the end of stub rbor. The common types of milling cutters, clssified by this system re s follows: Types of Milling Cutters. Hin milling cutters re cylindricl or disk-shped, hving stright or helicl teeth on the periphery. They re used for milling flt surfces. This type of opertion is clled pli n or slb milling. Ech tooth in helicl cutter engges the work grdully, nd usully more thn one tooth cuts t given time. This reduces shock nd chttering tendencies nd promotes smoother surfce. Consequently, this type of cutter usully is preferred over one with stright teeth. Side milling cutters re similr to plin milling cutters except tht the teeth extend rdilly prt wy cross one or both ends ofthe cylinder towrd the :center. The teeth my be either stright or helicl. Frequently these cutters re reltively nrrow, being disklike in shpe. Two or more side milling cutters often re spced on n rbor to mke simultneous, prllel cuts, in n opertion clled strddle milling. Interlocking slotting cutters consist of two cutters similr to side mills, but mde to operte s unit for milling slots. The two cutters re djusted to the desired width by inserting shims between them. Stggered-tooth milling cutters re nrrow cylindricl cutters hving stggered teeth, nd with lternte teeth hving opposite helix ngles. They re ground to cut only on the periphery, but ech tooth lso hs chip clernce ground on the protruding side. These cutters hve free cutting ction tht mkes them prticnlrly effective in milling deep slots. Metl-slitting sws re thin, plin milling cutters, usully from 1/32 to 3/16 inch thick, which hve their sides slightly "dished" to provide clernce nd prevent binding. They usully hve more teeth per inch of dimeter thn ordinry plin milling cutters nd re used for milling deep, nrrow slots nd for cutting-off opertions. 铣削铣削是机械加工的一个基础方法。
机械制造专业外文翻译--车床实践及CAD--CAM
外文原文:ADVANCED MACHINING PROCESSESAs the hardware of an advanced technology becomes more complex, new and visionary approaches to the processing of materials into useful products come into common use. This has been the trend in machining processes in recent years.. Advanced methods of machine control as well as completely different methods of shaping materials have permitted the mechanical designer to proceed in directions that would have been totally impossible only a few years ago.Parallel development in other technologies such as electronics and computers have made available to the machine tool designer methods and processes that can permit a machine tool to far exceed the capabilities of the most experienced machinist.In this section we will look at CNC machining using chip-making cutting tools. CNC controllers are used to drive and control a great variety of machines and mechanisms, Some examples would be routers in wood working; lasers, plasma-arc, flame cutting, and waterjets for cutting of steel plate; and controlling of robots in manufacturing and assembly. This section is only an overview and cannot take the place of a programming manual for a specific machine tool. Because of the tremendous growth in numbers and capability of computers ,changes in machine controls are rapidly and constantly taking place. The exciting part of this evolution in machine controls is that programming becomeseasier with each new advanced in this technology.Advantages of Numerical ControlA manually operated machine tool may have the same physical characteristics as a CNC machine, such as size and horsepower. The principles of metal removal are the same. The big gain comes from the computer controlling the machining axes movements. CNC-controlled machine tools can be as simple as a 2-axis drilling machining center (Figure O-1). With a dual spindle machining center, the low RPM, high horsepower spindle gives high metal removal rates. The high RPM spindle allows the efficient use of high cutting speed tools such as diamonds and small diameter cutters (Figure O-2). The cutting tools that remove materials are standard tools such as milling cutters, drills, boring tools, or lathe tools depending on the type of machine used. Cutting speeds and feeds need to be correct as in any other machining operation. The greatest advantage in CNC machining comes from the unerring and rapid positioning movements possible. A CNC machine does dot stop at the end of a cut to plan its next move; it does not get fatigued; it is capable of uninterrupted machining error free, hour after hour. A machine tool isproductive only while it is making chips.Since the chip-making process is controlled by the proper feeds and speeds, time savings can be achieved by faster rapid feed rates. Rapid feeds have increased from 60 to 200 to 400 and are now often approaching 1000 inches per minute (IPM). These high feed rates can pose a safety hazard to anyone within the working envelope of the machine tool.Complex contoured shapes were extremely difficult to product prior to CNC machining .CNC has made the machining of these shapes economically feasible. Design changes on a part are relatively easy to make by changing the program that directs the machine tool.A CNC machine produces parts with high dimensional accuracy and close tolerances without taking extra time or special precautions, CNC machines generally need less complex work-holding fixtures, which saves time by getting the parts machined sooner. Once a program is ready and production parts, each part will take exactly the same amount of time as the previous one. This repeatability allows for a very precise control of production costs. Another advantage of CNC machining is the elimination of large inventories; parts can be machined as needs .In conventional production often a great number of parts must be made at the same time to be cost effective. With CNC even one piece can be machined economically .In many instances, a CNC machine can perform in one setup the same operations that would require several conventional machines.With modern CNC machine tools a trained machinist can program and product even a single part economically .CNC machine tools are used in small and large machining facilities and range in size from tabletop models to huge machining centers. In a facility with many CNC tools, programming is usually done by CNC programmers away from the CNC tools. The machine control unit (MCU) on the machine is then used mostly for small program changes or corrections. Manufacturing with CNC tools usually requires three categories of persons. The first is the programmer, who is responsible for developing machine-ready code. The next person involved is the setup person, who loads the raw stork into the MCU, checks that the correct tools are loaded, and makes the first part. The third person is the machine and unloads the finished parts. In a small company, one person is expected to perform all three of these tasks.CNC controls are generally divided into two basic categories. One uses a ward address format with coded inputs such as G and M codes. The other users a conversational input; conversational input is also called user-friendly or prompted input. Later in this section examples of each of these programming formats in machining applications will be describes.CAD/CAMAnother method of creating toolpath is with the use of a Computer-aided Drafting (CAD) file. Most machine drawings are createdusing computers with the description and part geometry stored in the computer database. SmartCAM, though its CAM CONNECTION, will read a CAD file and transfer its geometry represents the part profile, holes, and so on. The programmer still needs to prepare a JOBPLAN with all the necessary tools, but instead of programming a profile line by line, now only a tool has to be assigned to an existing profile. Again, using the SHOWPATH function will display the toolpath for each tool and their sequence. Constant research and developments in CAD/CAM interaction will change how they work with each other. Some CAD and CAM programs, if loaded on the same computer, make it possible to switch between the two with a few keystrokes, designing and programming at the same time.The work area around the machine needs to be kept clean and clear of obstructions to prevent slipping or tripping. Machine surfaces should not be used as worktables. Use proper lifting methods to handle heavy workpieces, fixtures, or heavy cutting tools. Make measurements only when the spindle has come to a complete standstill. Chips should never be handled with bare hands.Before starting the machine make sure that the work-holding device and the workpiece are securely fastened. When changing cutting tools, protect the workpiece being machined from damage, and protect your hands from sharp cutting edges. Use only sharp cutting tools. Check that cutting tools are installed correctly and securely.Do not operate any machine controls unless you understand their function and what they will do.中文译文:车床实践随着先进科技的硬件变得复杂化,把原料加工成为有用产品的理想的、新的加工手段得到了普遍应用。
基本的加工工序—切削,镗削和铣削外文文献翻译、中英文翻译、外文翻译
-2-
内。这种方法牢固地夹持工件并且把功率平稳地传送到工件上;由卡盘提供的额 外支撑减少了车削作业时发生震动的倾向。如果仔细地将工件精确的固定在卡盘 上,用这种方法将获得精密的结果。 通过将工件支撑在两个顶尖之间可以获得非常精确的结果。一个车床夹头夹 在工件上;然后由安装在主轴前端的拨盘一起带动。先加工工件的一端,然后可 以在车床上将工件掉头加工另一端。工件上的顶尖孔是用作精确定位面以及承受 工件重量和抵抗车削力的支撑面。在工件被拆下后,顶尖孔可以精确地将其装回 机床。工件千万不要同时通过卡盘和顶尖安装在主轴箱一端。虽然这样似乎是一 种快捷方法,但是这样做使得工件受力不均匀,顶尖的对正作用不能维持,而且 爪的压力可能损坏顶尖孔、车床顶尖甚至车床主轴。几乎被独自用在大量生产工 件上的补偿或浮动爪式卡盘是上述的一个例外。这些卡盘是自动偏心夹紧卡盘不 能起到普通三爪或四爪卡盘同样的作用。 直径非常大的工件虽然有时安装在两个顶尖上,但是最好用花盘把它们固定 在主轴箱端以获得流畅的动力传输;此外,可以把它们制造成专用部件,但是一 般不能提供足够大的车床夹头来传输动力。除非是安装在花盘上,其主轴轴承上 的外伸要比大卡盘上的少一些。 镗削 在车床上镗孔的目的是: 1、扩孔; 2、把孔加工到所需直径; 3、精确的为孔定位; 4、在孔内获得好的表面粗糙度。 当刀具径向溜板纵向移动而工件绕车床的轴线旋转时, 镗刀的运动平行于车床 上的轴线。当两种运动结合起来镗孔时,就会与车床的旋转轴同心。通过把工件固 定在车床上可以精确定位孔的位置以使待加工孔所环绕的轴与车床的旋转轴一致。 当镗削工序与用于车削和刮削工序的设置相同时, 实际上可以达到理想的同心与垂 直。 镗刀固定在一根通过刀具径向溜板进给的镗杆上。根据待做的工作来使用这 一设计的变化形式。如果有的话,所用的倒角总是应该小些。而且,镗刀前端的 半径一定不能太大。用于镗孔的切削速度可以等于车削速度。但是,在计算车床 主轴速度时,应当使用完成后的或最大的孔径。镗削的进刀速度通常比车削的小 一点以补偿镗杆刚性的不足。 镗削工序一般分两步完成,即粗镗和精镗。粗镗工序的目的是快速、高效地 去除多余的金属;而精镗工序的目的是获得所需的尺寸、表面粗糙度和孔的位置。
机械加工外文翻译、中英文翻译、机械类外文文献翻译
机械加工外文翻译、中英文翻译、机械类外文文献翻译The engine lathe is an old but still useful metal removal machine with many desirable attributes。
While it is no longer commonlyXXX。
In today's n shops。
it has largely been XXX。
turret lathes。
and automatic XXX of single-point tooling for maximum metal removal。
and the use of form tools for finished products that are on par with the fastest processing XXX.When it XXX for the engine lathe。
it largely depends on the skill of the operator。
Design XXX part for n。
it is XXX.XXX cutting tools。
XXX ns。
as the machine can perform these ns in one setup。
They are also capable of producing parts with high n and accuracy。
XXX industries.Now more than ever。
n machining XXX of a specific method。
the XXX.When designing for low quantities。
such as 100 or 200 parts。
it is most cost-effective to use a XXX。
designers should aim to minimize the number of ns required.Another n for n XXX。
High-speed milling——高速铣削(机械工程毕业设计英文文献及翻译)
High-speed milling——高速铣削(机械工程毕业设计英文文献及翻译)High-speed milling——高速铣削High-speed machining is an advanced manufacturing technology,different from the traditional processing methods. The spindle speed, cutting feed rate, cutting a small amount of units within the time of removal of material has increased three to six times. With high efficiency, high precision and high quality surface as the basic characteristics of the automobile industry, aerospace, moldmanufacturing and instrumentation industry, such as access to a widerange of applications, has made significant economic benefits, is the contemporary importance of advanced manufacturing technology. For a long time, people die on the processing has been using a grinding or milling EDM (EDM) processing, grinding, polishing methods. Although the high hardness of the EDM machine parts, but the lower the productivity of its application is limited. With the development of high-speed processing technology, used to replace high-speed cutting, grinding and polishing process to die processing has become possible. To shorten the processing cycle, processing and reliable quality assurance, lower processing costs.1 One of the advantages of high-speed machiningHigh-speed machining as a die-efficient manufacturing, high-quality, low power consumption in an advanced manufacturing technology. Inconventional machining in a series of problems has plagued by high-speed machining of the application have been resolved.1.1 Increase productivityHigh-speed cutting of the spindle speed, feed rate compared withtraditional machining, in the nature of the leap, the metal removal rate increased 30 percent to 40 percent, cutting force reduced by 30 percent, the cutting tool life increased by 70% . Hardened parts can be processed, a fixture in many parts to be completed rough, semi-finishing and fine, and all other processes, the complex can reach parts of the surface quality requirements, thus increasing the processingproductivity and competitiveness of products in the market.1.2 Improve processing accuracy and surface qualityHigh-speed machines generally have high rigidity and precision, and other characteristics, processing, cutting the depth of small, fast and feed, cutting force low,the workpiece to reduce heat distortion, and high precision machining, surface roughness small. Milling will be no high-speed processing and milling marks the surface so that the parts greatly enhance the quality of the surface. Processing Aluminum when upRa0.40.6um, pieces of steel processing at up to Ra0.2 ~ 0.4um. 1.3 Cutting reduce the heatBecause the main axis milling machine high-speed rotation, cutting a shallow cutting, and feed very quickly, and the blade length of the workpiece contacts and contact time is very short, a decrease of bladesand parts of the heat conduction. High-speed cutting by dry milling or oil cooked up absolute (mist) lubrication system, to avoid thetraditional processing tool in contact with the workpiece and a lot of shortcomings to ensurethat the tool is not high temperature under the conditions of work, extended tool life.1.4 This is conducive to processing thin-walled partsHigh-speed cutting of small cutting force, a higher degree of stability, Machinable with high-quality employees compared to the company may be very good, but other than the company's employees may Suanbu Le outstanding work performance. For our China practice, we use the models to determine the method of staff training needs are simple and effective. This study models can be an external object, it can also be a combination of internal and external. We must first clear strategy for the development of enterprises. Through the internal and external business environment and organizational resources, such as analysis, the future development of a clear business goals and operational priorities. According to the business development strategy can be compared to find the business models, through a comparative analysis of the finalization of business models. In determining business models, a, is the understanding of its development strategy, or its market share and market growth rate, or the staff of the situation, and so on, according to the companies to determine the actual situation. As enterprises in different period of development, its focus is different, which meansthat enterprises need to invest the manpower and financial resources thefocus is different. So in a certain period of time, enterprises should accurately selected their business models compared with the departments and posts, so more practical significance, because the business models are not always good, but to compare some aspects did not have much practical significance, Furthermore Thiscan more fully concentrate on the business use of limited resources. Identify business models, and then take the enterprise of the corresponding departments and staff with the business models for comparison, the two can be found in the performance gap, a comparative analysis to find reasons, in accordance with this business reality, the final identification of training needs. The cost of training is needed, if not through an effective way to determine whether companies need to train and the training of the way, but blind to training, such training is difficult to achieve the desired results. A comparison only difference between this model is simple and practical training. 1.5 Can be part of some alternative technology, such as EDM, grinding high intensity and high hardness processingHigh-speed cutting a major feature of high-speed cutting machine has the hardness of HRC60 parts. With the use of coated carbide cutter mold processing, directly to the installation of a hardened tool steel processing forming, effectively avoid the installation of several parts of the fixture error and improve the parts of the geometric location accuracy. In the mold of traditional processing, heat treatment hardening of the workpiece required EDM, high-speed machining replacethe traditional method of cutting the processing, manufacturing process possible to omit die in EDM, simplifying the processing technology and investment costs .High-speed milling in the precincts of CNC machine tools, or for processing centre, also in the installation of high-speed spindle on the general machine tools. The latter not only has the processing capacity of general machine tools, but also for high-speed milling, a decrease of investment in equipment, machine tools increased flexibility. Cutting high-speed processing can improve the efficiency, quality improvement, streamline processes, investment and machine tool investment and maintenance costs rise, but comprehensive, can significantly increase economic efficiency.2 High-speed millingHigh-speed milling the main technical high-speed cutting technology is cutting the development direction of one of it with CNC technology, microelectronic technology, new materials and new technology, such as technology development to a higher level. High-speed machine tools and high-speed tool to achieve high-speed cutting is the prerequisite and basic conditions, in high-speed machining in the performance of high-speed machine tool material of choice and there are strict requirements. 2.1 High-speed milling machine in order to achieve high-speed machining General use of highly flexible high-speed CNC machine tools, machining centers, and some use a dedicated high-speed milling, drilling. At the same time a high-speed ma chine tool spindle system andhigh-speed feeding system, high stiffness of the main characteristics of high-precision targeting and high-precision interpolation functions, especially high-precision arc interpolation function. High-speed machining systems of the machine a higher demand, mainly in thefollowing areas:General use of highly flexible high-speed CNC machine tools, machining centers, and some use a dedicated high-speed milling, drilling. At the same time a high-speed machine tool spindle system and high-speed feeding system, high stiffness of the main characteristics of high-precision targeting and high-precision interpolation functions,especially high-precision arc interpolation function. High-speed machining systems of the machine a higher demand, mainly in thefollowing areas: High-speed milling machine must have a high-speed spindle, the spindle speed is generally 10000 ~ 100000 m / min, power greater than 15 kW. But also with rapid speed or in designated spotsfast-stopping performance. The main axial space not more than 0 .0 0 0 2 m m. Often using high-speed spindle-hydrostatic bearings, air pressure-bearing, mixed ceramic bearings, magnetic bearing structure of the form. Spindle cooling general use within the water or air cooled.High-speed processing machine-driven system should be able toprovide 40 ~ 60 m / min of the feed rate, with good acceleration characteristics, can provide 0.4 m/s2 to 10 m/s2 acceleration and deceleration. In order to obtain goodprocessing quality, high-speed cutting machines must have a high enough stiffness. Machine bed materialused gray iron, can also add a high-damping base of concrete, to prevent cutting tool chatter affect the quality of processing. A high-speed data transfer rate, can automatically increase slowdown. Processing technology to improve the processing and cutting tool life. At present high-speed machine tool manufacturers, usually in the general machine tools on low speed, the feed of the rough and then proceed to heat treatment, the last in the high-speed machine on the half-finished and finished, in improving the accuracy and efficiency at the same time, as far as possible to reduce processing Cost.2.2 High-speed machining toolHigh-speed machining tool is the most active one of the important factors, it has a direct impact on the efficiency of processing, manufacturing costs and product processing and accuracy. Tool in high-speed processing to bear high temperature, highpressure, friction, shock and vibration, such as loading, its hardness and wear-resistance, strength and toughness, heat resistance, technology and economic performance of the basic high-speed processing performance is the key One of the factors. High-speed cutting tool technology development speed, the more applications such as diamond (PCD), cubic boron nitride (CBN), ceramic knives, carbide coating, (C) titanium nitride Carbide TIC (N) And so on. CBN has high hardness, abrasion resistance and the extremely good thermal conductivity, andiron group elements between the great inertia, in 1300 ? would not have happened significant role in thechemical, also has a good stability. The experiments show that with CBN cutting tool HRC35 ~ 67 hardness of hardened steel can achieve very high speed. Ceramics have good wear resistance and thermal chemical stability, its hardness, toughness below the CBN, can be used for processing hardness of HRC <5 0 parts. Carbide Tool good wear resistance, but the hardness than the low-CBN and ceramics. Coating technology used knives, cutting tools can improve hardness and cutting the rate, for cutting HRC40 ~ 50 in hardness between the workpiece. Can be used toheat-resistant alloys, titanium alloys, hightemperature alloy, cast iron, Chungang, aluminum and composite materials of high-speed cutting Cut,the most widely used. Precision machining non-ferrous metals or non-metallic materials, or the choice of polycrystalline diamond Gang-coated tool.2.3 High-speed processing technologyHigh-speed cutting technology for high-speed machining is the key. Cutting Methods misconduct, will increase wear tool to less than high-speed processing purposes. Only high-speed machine tool and not a good guide technology, high-speed machining equipment can not fully play its role. In high-speed machining, should be chosen with milling, when the milling cutter involvement with the workpiece chip thickness as the greatest, and then gradually decreased. High-speedmachining suitable for shallowdepth of cut, cutting depth of not more than 0.2 mm, to avoid the location of deviation tool to ensure that the geometric precisionmachining parts. Ensure that the workpiece on the cutting constant load, to get good processing quality. Cutting a single high-speed millingpath-cutting mode, try not to interrupt the process and cutting tool path, reducing the involvement tool to cut the number to be relatively stable cutting process. Tool to reduce therapid change to, in other words when the NC machine tools must cease immediately, or Jiangsu, and then implement the next step. As the machine tool acceleration restrictions, easy to cause a waste of time, and exigency stop or radical move would damage the surface accuracy. In the mold of high-speed finishing, in each Cut, cut to the workpiece, the feed should try to change the direction of a curve or arc adapter, avoida straight line adapter to maintain the smooth process of cutting.3 Die in high-speed milling processing ofMilling as a highly efficient high-speed cutting of the newmethod,in Mould Manufacturing has been widely used. Forging links in the regular production model, with EDM cavity to be 12 ~ 15 h, electrodes produced 2 h. Milling after the switch to high-speed, high-speed milling cutter on the hardness of HRC 6 0 hardened tool steel processing. The forging die processing only 3 h20min, improve work efficiency four to five times the processing surface roughness of Ra0.5 ~ 0.6m, fully in line with quality requirements.High-speed cutting technology is cutting technology one of the major developments, mainly used in automobile industry and die industry, particularly in the processing complex surface, the workpiece itself orknives rigid requirements of the higher processing areas, is a range of advanced processing technology The integration, high efficiency and high quality for the people respected. It not only involves high-speed processing technology, but also including high-speed processing machine tools, numerical control system, high-speed cutting tools and CAD / CAM technology. Die-processing technology has been developed in the mold of the manufacturing sector in general, and in my application and the application of the standards have yet to be improved, because of its traditional processing with unparalleled advantages, the future will continue to be an inevitable development of processing technologyDirection.高速铣削高速切削加工是一种先进制造技术,不同于传统加工方式。
- 1、下载文档前请自行甄别文档内容的完整性,平台不提供额外的编辑、内容补充、找答案等附加服务。
- 2、"仅部分预览"的文档,不可在线预览部分如存在完整性等问题,可反馈申请退款(可完整预览的文档不适用该条件!)。
- 3、如文档侵犯您的权益,请联系客服反馈,我们会尽快为您处理(人工客服工作时间:9:00-18:30)。
附件1:外文资料翻译译文车床与铣削加工车床用与车外圆、端面和镗孔等加工的机床叫车床。
车削很少在其他种类的机床上进行,某些机床不能像车床那样方便地进行车削加工。
由于车床除了用于车外圆外还能用于镗孔、车端面、钻孔和铰孔,车床的多功能性可以使工件在一次定位安装中完成多种加工。
这就是在生产中普遍使用各种车床比其他种类的机床都要多的原因。
很早就已经有了车床。
现代车床可以追溯到大约17世纪,那时亨利·莫德斯利发明了一种具有丝杠的车床。
这种车床可以控制工具的机械进给。
聪明的英国人还发明了一种把主轴和丝杠相连接的变速装置,这样就可以切削螺纹。
车床的主要部件:床身、主轴箱组件、尾架组件、拖板组件、变速齿轮箱、丝杠和光杠床身是车床的基础件。
它通常是由经过正火处理的灰铸铁或者球墨铸铁制成,它是一个坚固的刚性框架,所有其他主要部件都安装在床身上。
通常在床身上面有内外两组平行的导轨。
一些制造厂生产的四个条导轨都采用倒“V”形,而另一些制造厂则将倒“V”形导轨和平面导轨相结合。
由于其他的部件要安装在导轨上或在导轨上移动,导轨要经过精密加工,以保证其装配精度。
同样地,在操作中应该小心,以避免损伤导轨。
导轨上的任何误差,常常会使整个机床的精度破坏。
大多数现代车床的导轨要进行表面淬火处理,以减小磨损和擦伤,具有更大的耐磨性。
主轴箱安装在床身一端内导轨的固定位置上。
它提供动力,使工件在各种速度下旋转。
它基本上由一个安装在精密轴承中的空心主轴和一系列变速齿轮,通过变速齿轮,主轴可以在许多种转速下旋转。
大多数车床有8—18种转速,一般按等比级数排列。
在现代车床上只需扳动2~4个手柄,就能得到全部挡位的转速。
目前发展的趋势是通过电气的或机械的装置进行无级变速。
由于车床的精度在很大程度上取决于主轴,因此主轴的结构尺寸较大,通常安装在紧密配合的重型圆锥滚子轴承或球轴承中。
主轴中有一个贯穿全长的通孔。
主轴孔的大小是车床的一个重要尺寸,因为当工件通过主轴孔供料时,它确定了能够加工棒料毛坯的最大外径尺寸。
主轴的内端从主轴箱中凸出,其上可以安装多种卡盘、花盘和挡块。
而小型的车床常带有螺纹截面供安装卡盘之用。
很多大车床使用偏心夹或键动圆锥轴头。
这些附件组成了一个大直径的圆锥体,以保证对卡盘进行精确地装配,并且不用旋转这些笨重的器件就可以锁定或松开卡盘和花盘。
主轴由电动机经V带或无声链装置提供动力。
大多数现代车床都装有5—15马力的电动机,为硬质合金和金属陶瓷合金刀具提供足够的动力,进行高速切削。
尾座组件主要由三部分组成。
底座与床身的内侧导轨配合,并可以在导轨上做纵向移动,底座上有一个可以使整个尾座组件夹紧的装置。
尾座安装在底座上,可以沿键槽在底座上横向移动,使尾座与主轴箱中的主轴对正并为切削圆锥体提供方便。
尾座组件的第三部分是尾座套筒,它是一个直径通常在2~3英寸之间的钢制空心圆柱轴。
通过手轮和螺杆,尾座套筒可以在尾座体中纵向移入和移出几英寸。
活动套筒的开口一端具有莫氏锥度,可以用于安装顶尖或其他刀具。
通常在活动套筒的外表面刻有几英寸长的刻度,以控制尾座的前后移动。
锁定装置可以使套筒在所需要的位置上夹紧。
拖板组件用于安装和移动切削工具。
拖板是一个相对平滑钓H形铸件,安装在床身外侧导轨上,并可在上面移动。
大拖板上有横向导轨,使横向拖板可以安装在上面,并通过丝杠使其运动,丝杠由一个小手柄和刻度盘控制。
横拖板可以带动刀具垂直于工件的旋转轴线切削。
铣削加工铣削是机械加工的一个基础方法。
在这一加工过程中,当工件沿垂直于旋转刀具轴线方向进给时,在工件上去除切屑从而逐渐地铣出表面。
有时候,工件是固定的,而刀具处于进给状态。
在大多数情况下,使用多齿刀具,金属切削量大,只需一次铣削就可以获得所期望的表面。
在铣削加工中使用的刀具称做铣刀。
它通常是一个绕轴线旋转并且周边带有同间距齿的圆柱体,铣刀齿间歇性接触并切削工件。
在某些情况下,铣刀上的刀齿会高出圆柱体的一端或两端。
由于铣削切削金属速度很快,并且能产生良好的表面光洁度,故特别适合大规模生产加工。
为了实现这一目的,已经制造出了质量一流的铣床。
并且在机修车间和工具模具加工中也已经广泛地使用了非常精确的多功能通用的铣床。
车间里拥有一台铣床和一台普通车床就能加工出具有适合尺寸的各种产品。
铣削操作类型:铣削操作可以分成两大种类,每一类又有多种类型。
1.圆周铣削在圆周铣削中,使用的铣刀刀齿固定在刀体的圆周面上,工件铣削表面与旋转刀具轴线平行,从而加工表面。
使用这种方法可以加工出平面和成型表面,加工中表面横截面与刀具的轴向外轮廓相一致。
这种加工过程常被称为平面铣削。
2.端面铣削铣削平面与刀具的轴线垂直,被加工平面是刀具位于周边和端面的齿综合作用形成的。
刀具周边齿完成铣削的主要任务,而端面齿用于精铣。
圆周铣削和端面铣削的基本概念,圆周铣削通常使用卧式铣床,而端铣削则既可在卧式铣床又可以在立式铣床上进行。
铣削面的形成:铣削时可以采用两种完全不同的方法。
应注意的是,在逆向铣削时,铣刀旋转方向与工件进给方向相反,而在顺铣时铣刀旋转与工件进给方向相同。
在逆铣过程中,当铣刀齿刚切人工件时,切屑是非常薄的,然后渐渐增厚,在刀齿离开工件的地方,切屑最厚。
在两种铣削方法中,切屑的形成是不同的,逆铣过程中,刀具有推动使工件从工作台提升的趋势,这种作用有助于消除铣床工作台进给螺杆和螺母间的间隙,从而形成平稳的切削。
然而,这种作用也有造成工件与夹紧装置之间的松动的趋势,这时应施加更大的夹紧力。
此外,铣削表面的平整度主要取决于切削刃的锋利程度。
顺铣时,最大切屑厚度产生于靠近刀具与工件接触点处。
由于相对运动把工件拉向铣刀,如果采用顺铣法,要消除工作台进给时螺杆可能产生的松动。
因此,对于不能用于顺铣的铣床,应不采用顺铣方法。
因为在铣刀结束切削时,处于切线方向的被切材料发生屈服,所以与逆铣相比,顺铣的被加工表面没有什么切痕。
顺铣的另一个优势是切削力趋于将工件压紧在工作台上,因此对工件的夹紧力可以小于逆铣。
这一优势可以用于铣削较薄的工件或进行强力切削。
顺铣的弱点是铣刀齿刚一切削每片铁屑时,刀齿会撞击工件的表面。
如果工件表面坚硬,像铸件,就会使刀齿迅速地变钝。
铣刀铣刀分类有多种方法,一种方法是根据刀具后角将铣刀分为两大类:1.仿形铣刀每个刀齿在切削刃的背面磨了一个很小的棱面形成后角,切削刃可以是直线或曲线的。
2.凸轮形后角铣刀每个齿的横截面在切削刃的背面呈偏心曲线状,以产生后角。
偏心后角的各面与切削刃平行,具有切削刃的相同形状。
这种类型的铣刀仅需磨削齿的前刀面就可以变得锋利,只要切削刃的外形保持不变,铣刀的另一种分类方法是根据铣刀安装的方法进行分类。
心轴铣刀带有一个中心孔以使铣刀安装在心轴上。
带柄铣刀有一锥柄或直柄轴,含锥形轴柄的铣刀可以直接安装在铣床的主轴上,而直柄轴的铣刀则是夹持在卡盘里。
平面铣刀通常用螺栓固定在刀轴的末端上。
根据这种分类方法,通用型的铣刀可分类如下:心轴铣刀:圆柱形铣刀,角度铣刀,侧刃铣刀,嵌齿铣刀,错齿铣刀,凸轮形后角铣刀,开槽铣刀,高速切削刀。
带柄铣刀:端面铣刀,T形槽铣刀,整体式铣刀,半圆键座铣刀,套式铣刀,高速切削刀,空心铣刀。
铣刀的类型圆柱形铣刀是在圆周上有直的或螺旋形的齿的圆柱形或盘形铣刀。
它们可以用来铣削平面,这种铣削称做平面铣削。
螺旋形的铣刀上的每个齿是逐渐地接触工件,在给定的时间内,一般有多齿进行铣削,这样可以减少震动,获得一个较平滑的表面。
因此,与直齿铣刀相比,这种类型的铣刀,通常使用得更多。
侧刃铣刀的齿除了在圆柱刀体的一端或两端向径向延伸之外,与圆柱形铣刀是相似的。
侧刃铣刀的刀齿既可以是直线的,也可以是螺旋形的,这种铣刀一般较窄小,具有盘形的形状。
在跨式铣削加工中,常常将两个或更多的侧刃铣刀同时相间地安装在一个刀杆上同步并行切削。
双联槽铣刀是由两个侧刃铣刀组成,但是在铣槽时,作为一组铣刀进行操作。
在两个铣刀之间添加一些薄垫片,以调整之间的间距。
错齿铣刀是较薄的圆柱形铣刀,刀上有相互交错的刀齿,相邻刀齿具有相反的螺旋角。
这种铣刀经研磨后仅用于周铣,在每个齿突出的一边,留有供切屑排出的缝隙。
这种类型的铣刀可用于高速切削,在铣削深槽时可以发挥独特的作用。
开槽铣刀是一种薄型的圆柱形铣刀,厚度一般为1/32—3/16英寸。
这种铣刀的侧面呈盘状,有间隙,可以防止粘连。
与圆柱形铣刀相比,这种类型的铣刀每英寸直径上的齿数更多,通常用于铣削较深的、狭窄的槽,并可用于切割加工。
附件2:外文原文(复印件)LATHE AND MILLINGThe basic machines that are designed primarily to do turning, facing and boring are called lathes. Very little turning is done on other types of machine tools, and none can do it with equal facility. Because lathe can do boring, facing, drilling, and reaming in addition to turning, their versatility permits several operations to be performed with a single setup of the workpiece. These accounts for the fact that lathes of various types are more widely used in manufacturing than any other machine tool.Lathes in various forms have existed for more than long long age. Modem lathes date from about 1797, when Henry Maudsley developed one with a lea&crew. It provided controlled, mechanical feed of the tool. This ingenious Englishman also developed a changegear system that could connect the motions of the spindle and lea&crew and thus enable threads to be the Construction. The essential components of a lathe are depicted in the block diagram.These are the bed, headstock assembly, tailstock assembly, carriage assembly, quick-change gear box, and the lea&crew and feed rod.The bed is the backbone of a lathe. It usually is made of well-normalized or aged gray or nodular cast iron and provides a heavy, rigid frame on which all the other basic components are mounted. Two sets of parallel, longitudinal ways, inner and outer, are contained on the bed, usually on the upper side. Some makers use an inverted V-shape for all four ways, whereas others utilize one inverted V and one flat way in one or both sets. Because several other components are mounted and/or move on the ways they must be made with precision to assure accuracy of alignment. Similarly, proper precaution should be taken in operating a lathe to assure that the ways are not damaged. Any inaccuracy in them usually means that the accuracy of the entire lathe is destroyed. The ways on most modem lathes are surfacehardened to offer greater resistance to wear and abrasion.The headstock is mounted in a fixed position on the inner ways at one end of the lathe bed. It provides a powered means of rotating the work at various speeds. It consists, essentially, of a hollow spindle, mounted in accurate bearings? And a set of transmission gears similar to a truck transmission through which the spindle can be rotated at a number of speeds. Most lathes provide from eight to eighteen speeds, usually in a geometric ratio, and on modem lathes all the speeds can be obtained merely by moving from two to four levers.An increasing trend is to provide a continuously variable speed range through electrical or mechanical drives.Because the accuracy of a lathe is greatly dependent on the spindle, it is of heavy construction and mounted in heavy bearings, usually preloaded tapered roller or ball types, a longitudinal hole extends through the spindle so that long bar stock can be fed through it. The size of this hole is an important size dimension of a lathe becauseit determinesthe maximum size of bar stock that can be machined when the material must be fed through the spinale.The inner end of the spindle protrudes from the gear box and contains a means for mounting various types of chucks, face plates, and dog plates on it. Whereas small lathes often employ a threaded section to which the chucks are screwed, most large lathes utilize either cam-lock or key-drive taper noses. These provide a large-diameter taper that assures theaccurate alignment of the chuck, and a mechanism that permits the chuck or face plate to be locked or unlocked in position without the necessity of having to rotate these heavyattachments.Power is supplied to the spindle by means of an electric motor through a V-belt or silent-chain drive. Most modem lathes have motors of from 5 to15 horsepower to provide adequate power for carbide and ceramic tools at their high cutting speeds.The tailstock assembly consists, essentially, of three parts. A lower casting fits on the inner ways of the bed and can slide longitudinally thereon, with a means for clamping the entire assembly in any desired location. An upper casting fits on the lower one and can be moved transversely upon it on some type of keyed ways. This transverse motion pemfits aligning the tailstock and headstock spindles and provides a method of tuming tapers. The third major component of the assembly is the tailstock quill. This is a hollow steel cylinder, usually about 2 to sinches in diameter, that can be moved several inches longitudinally in and out of the upper casting by means of a handwheel and screw. The open end of the quill hole terminates in a morse. Taper in which a lathe center, or various tools such as drills, can be held. A graduated scale, several inches in length, usually is engraved on the outside of the quill to aid in controlling its motion in and out of theupper casting. A locking device permits clamping the quill in any desired position.The carriage assembly provides the means for mounting and moving cutting tools. The carriage is a reianvely fiat H-shaped casting that rests and moves on the outer set of ways on the bed. The transverse bar of the carriage contains ways on which the cross slide is mounted and can be moved by means of a feed screw that is controlled by a small handwheel and agraduated dial. Through the cross slide a means is provided for moving the lathe tool in the direction normal to the axis of rotation of the work.On most lathes the tool post actually is mounted on a compound rest. This consists of a base, which is mounted on the cross slide so that it can be pivoted about a vertical axis, and an .upper casting. The upper casting is mounted on ways on this base .so that it can be moved back and forth and controlled by means of a short lead screw operated by a handwheel and a calibrated dial.Manual and powered motion for the carriage, and powered motion for the cross slide, is provided by mechanisms within the apron,attached to the front of the carriage. Manual movement of the carriage along the bed is effected by turning a handwheel on the front ofthe apron, which is geared to a pinion on the back side. This pinion engages a rack that is attached beneath the upper front edge of the bed in an inverted position.MILLINGMilling is a basic machining process in which the surface is generated by the progressive formation and removal of chips of material from the workpiece as it is fed to a rotating cutter in a direction perpendicular to the axis of the cutter. In some cases the workpiece is stationary and the cutter is fed to the work. In most instances a multiple-tooth cutter is used so that the metal removal rate is high, and frequently the desired surface is obtained in a single pass of the work.The tool used in milling is known as a milling cutter. It usually consists of a cylindrical body which rotates on its axis and contains equally spaced peripheral teeth that intermittently engage and cut the workpiece. 1 In some cases the teeth extend part way across one or both Ends of the cylinder.Because the milling principle provides rapid metal removal and can produce good surface finish, it is particularly well-suited for mass-production work, and excellent milling machines have been developed for this purpose. However, very accurate and versatile milling Machines of a general-purpose nature also have been developed that are widely used in jobshop and tool and die work. A shop that is equipped with a milling machine and an engine lathe can machine almost any type of product of suitable size.Types of Milling Operations. Milling operations can be classified into two broad categories, each of which has several variations:1. In peripheral milling a surface is generated by teeth located in the periphery of the cutter body; the surface is parallel with the axis of rotation of the cutter. Both flat and formed surfaces can be produced by this method. The cross section of the resulting surface corresponds to the axial contour of the cutter. This procedure often is called slab milling.2. In face milling the generated flat surface is at right angles to the cutter axis and is the combined result of the actions of the portions of the teeth located on both the periphery and the face of the cutter. 2 The major portion of the cutting is done by the peripheral portions of the teeth with the face portions providing a finishing action.The basic concepts of peripheral and face milling are illustrated in Fig. 16-1. Peripheral milling operations usually are performed on machines having horizontal spindles, whereas face milling is done on both horizontal- and vertical-spindle machines.Surface Generation in Mimng. Surfaces can be generated in milling by two distinctly different methods depicted in Fig. 16-2. Note that in up milling the cutter rotates againsi the direction of feed the workpiece, whereas in down milling the rotation is in the same direction as the feed. As shown in Fig. 16-2, the method of chip formation is quite different in the two cases. In up milling the c hip is very thin at the beginning, where the tooth first contacts the work, and increases in thickness, becoming a maximum where the tooth leaves the work. The cutter tends to push the work along and lift itupward from Tool-work relationshios in peripheral and face milling the table. This action tends to eliminate any effect of looseness in the feed screw and nut of the milling machine table and results in a smooth cut. However, the action also tends to loosen the work from the clamping device so that greater clamping forcers must be employed. In addition, the smoothness of the generated surface depends greatly on the sharpness of the cutting edges.In down milling, maximum chip thickness cecum close to the point at which the tooth contacts the work. Because the relative motion tends to pull the workpiece into the cutter, all possibility of looseness in the table feed screw must be eliminated if down milling is to be used. It should never be attempted on machines that are not designed for this type of milling. Inasmush as the material yields in approximately a tangential direction at the end of the tooth engagement, there is much less tendency for the machined surface to show tooth marks than when up milling is used. Another considerable advantage of down milling is that the cutting force tends to hold the work against the machine table, permitting lower clamping force to be employed. 3 This is particularly advantageous when milling thin workpiece or when taking heavy cuts.Sometimes a disadvantage of down milling is that the cutter teeth strike against the surface of the work at the beginning of each chip. When the workpiece has a hard surface, such as castings do, this may cause the teeth to dull rapidly.Milling Cutters. Milling cutters can be classified several ways. One method is to group them into two broad classes, based on tooth relief, as follows:1. Profile-cutters have relief provided on each tooth by grinding a small land back of the cutting edge. The cutting edge may be straight or curved.2. In form or cam-reheved cutters the cross section of each tooth is an eccentric curve behind the cutting edge, thus providing relief. All sections of the eccentric relief, parallel with the cutting edge, must have the same contour as the cutting edge. Cutters of this type are sharpened by grinding only the face of the teeth, with the contour of the cutting edge thus remaining unchanged.Another useful method of classification is according to the method of mounting the cutter. Arbor cutters are those that have a center hole so they can be mounted on an arbor. Shank cutters have either tapered or straight integral shank. Those with tapered shanks can be mounted directly in the milling machine spindle, whereas straight-shank cutters are held in a chuck. Facing cutters usually are bolted to the end of a stub arbor.The common types of milling cutters, classified by this system are as follows: Types of Milling Cutters. Hain milling cutters are cylindrical or disk-shaped, having straight or helical teeth on the periphery. They are used for milling flat surfaces. This type of operation is called plai n or slab milling. Each tooth in a helical cutter engages the work gradually, and usually more than one tooth cuts at a given time. This reduces shock and chattering tendencies and promotes a smoother surface. Consequently, this type of cutter usually is preferred over one with straight teeth.Side milling cutters are similar to plain milling cutters except that the teeth extend radially part way across one or both ends of the cylinder toward the :center. The teeth may be either straight or helical. Frequently these cutters are relativelynarrow, being disklike in shape. Two or more side milling cutters often are spaced on an arbor to make simultaneous, parallel cuts, in an operation called straddle milling.Interlocking slotting cutters consist of two cutters similar to side mills, but made to operate as a unit for milling slots. The two cutters are adjusted to the desired width by inserting shims between them.Staggered-tooth milling cutters are narrow cylindrical cutters having staggered teeth, and with alternate teeth having opposite helix angles. They are ground to cut only on the periphery, but each tooth also has chip clearance ground on the protruding side. These cutters have a free cutting action that makes them particnlarly effective in milling deep slots.。