汽车零部件强度分析
探讨汽车副车架强度模态分析及结构优化

探讨汽车副车架强度模态分析及结构优化1. 引言1.1 研究背景汽车副车架是汽车重要的结构部件之一,承担着支撑车身、吸收冲击力、传递动力等重要功能。
随着汽车的发展,人们对汽车副车架的要求也越来越高,希望能够在保证结构强度的前提下减轻重量,提高燃油效率和安全性。
现有汽车副车架结构往往存在过多的冗余部分和设计缺陷,导致结构重量过大、强度不足等问题。
对汽车副车架进行强度模态分析和结构优化显得尤为重要。
通过分析副车架在不同工况下的受力特点和振动模态,可以发现潜在的弱点和瓶颈,从而有针对性地进行结构优化,提高其整体性能。
基于以上背景,本文将针对汽车副车架的强度模态分析和结构优化展开研究,旨在为汽车工程领域提供更有效的设计方案和优化策略,促进汽车轻量化、高效化的发展。
1.2 研究意义汽车副车架是汽车重要的结构部件之一,其负责支撑整车重量并承载各种动态载荷。
对汽车副车架进行强度模态分析和结构优化是非常重要的,具有以下几个方面的研究意义:汽车副车架的强度模态分析可以帮助工程师了解其在不同工况下的受力情况,从而预测可能存在的强度问题,为设计提供参考和改进方向。
通过分析副车架的振动模态,可以确定其固有频率和形态,进而评估结构的动力性能和耐久性。
结构优化可以有效地降低副车架的重量,提高结构的刚度和强度,降低振动和噪音,进而改善车辆的行驶性能和安全性。
通过优化设计,可以有效地降低生产成本和能源消耗,提高汽车整体的竞争力。
研究汽车副车架强度模态分析及结构优化还可以推动汽车工程技术的进步和创新,促进汽车制造业的可持续发展。
通过优化设计,可以提高汽车的整体性能和环保性能,满足不断提升的市场需求和法规标准。
对汽车副车架进行强度模态分析和结构优化具有重要的意义和价值。
1.3 研究目的研究目的是为了深入探讨汽车副车架的强度和振动特性,为设计和优化提供理论支持和技术指导。
具体包括以下几个方面的目标:1. 分析副车架的承载能力和抗疲劳性能,找出存在的弱点和瓶颈,为提高车辆整体结构的稳定性和安全性提供依据。
汽车车身强度分析技术打造坚固安全的驾乘空间

汽车车身强度分析技术打造坚固安全的驾乘空间在汽车设计与制造过程中,确保驾乘空间的坚固安全是至关重要的一环。
汽车车身强度分析技术作为现代汽车制造领域的重要工具,可以帮助工程师们将车辆的结构设计得更加牢固,提供更安全的驾乘环境。
本文将探讨汽车车身强度分析技术的应用,并重点介绍几种常见的分析方法。
1. 强度分析概述汽车车身的强度分析是通过计算和模拟车辆受力情况,评估车身结构的强度和刚度。
这项技术可以为汽车制造商提供关键的工程数据,以确保车辆在不同的受力情况下能够承受压力并保持结构完整性。
强度分析通常包括静态刚度分析、动态强度分析以及车辆碰撞测试等。
2. 静态刚度分析静态刚度分析是评估车辆结构在不同工况下的刚度特性。
通过使用有限元分析方法,可以计算出车辆受到各种载荷(如转矩、相对位移和弯曲力)时产生的刚度响应。
这些数据可以用于优化车辆结构设计,确保车身在正常使用时具有足够的刚度,以提供稳定的驾乘体验和安全性能。
3. 动态强度分析动态强度分析是评估车辆在行驶过程中受到不同路况和振动影响时的强度表现。
通过结合实验数据和计算模拟,可以分析车辆在路况不均匀、制动、悬挂系统振动等情况下的应力分布和变形情况。
这些数据有助于工程师们优化车辆结构,并确保在行驶过程中车身的强度和安全性得到充分保障。
4. 车辆碰撞分析车辆碰撞分析是汽车设计中最重要的一环,也是车辆安全性能的关键评估指标之一。
通过模拟车辆在不同碰撞情况下的响应,可以评估车辆结构所能承受的冲击力和吸能能力,并且预测车辆在各种碰撞条件下的变形和破坏情况。
这些分析结果可以指导车辆设计和制造过程,确保驾乘空间的安全性。
5. 刚性体结构分析刚性体结构分析是一种广泛应用于汽车设计领域的分析方法。
它通过建立汽车车身模型,并应用有限元分析,计算车身结构的应力和应变等物理量。
通过这种分析方法,工程师们可以评估车身结构的刚度、强度和稳定性,并及时发现存在的问题。
这使得设计师们能够针对性地进行结构优化,确保驾乘空间的坚固安全。
探讨汽车副车架强度模态分析及结构优化
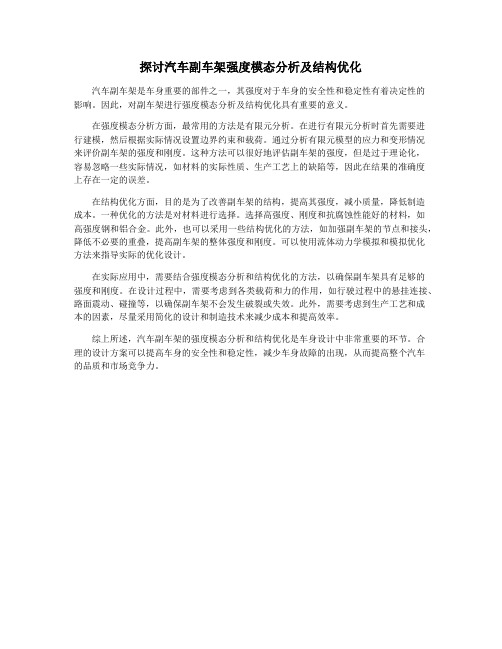
探讨汽车副车架强度模态分析及结构优化汽车副车架是车身重要的部件之一,其强度对于车身的安全性和稳定性有着决定性的影响。
因此,对副车架进行强度模态分析及结构优化具有重要的意义。
在强度模态分析方面,最常用的方法是有限元分析。
在进行有限元分析时首先需要进行建模,然后根据实际情况设置边界约束和载荷。
通过分析有限元模型的应力和变形情况来评价副车架的强度和刚度。
这种方法可以很好地评估副车架的强度,但是过于理论化,容易忽略一些实际情况,如材料的实际性质、生产工艺上的缺陷等,因此在结果的准确度上存在一定的误差。
在结构优化方面,目的是为了改善副车架的结构,提高其强度,减小质量,降低制造成本。
一种优化的方法是对材料进行选择。
选择高强度、刚度和抗腐蚀性能好的材料,如高强度钢和铝合金。
此外,也可以采用一些结构优化的方法,如加强副车架的节点和接头,降低不必要的重叠,提高副车架的整体强度和刚度。
可以使用流体动力学模拟和模拟优化方法来指导实际的优化设计。
在实际应用中,需要结合强度模态分析和结构优化的方法,以确保副车架具有足够的强度和刚度。
在设计过程中,需要考虑到各类载荷和力的作用,如行驶过程中的悬挂连接、路面震动、碰撞等,以确保副车架不会发生破裂或失效。
此外,需要考虑到生产工艺和成本的因素,尽量采用简化的设计和制造技术来减少成本和提高效率。
综上所述,汽车副车架的强度模态分析和结构优化是车身设计中非常重要的环节。
合理的设计方案可以提高车身的安全性和稳定性,减少车身故障的出现,从而提高整个汽车的品质和市场竞争力。
汽车结构强度分析技术的研究

汽车结构强度分析技术的研究一、引言汽车结构强度是指汽车零部件在正常使用中经受各种载荷作用下所能承受的能力。
随着汽车设计和制造技术的不断发展,汽车结构强度分析技术也得到了快速发展,并且逐渐成为了汽车设计和制造的核心技术之一。
本文将从汽车结构强度分析技术的基础知识、分析方法及研究进展三个方面进行介绍。
二、汽车结构强度分析技术的基础知识1、载荷类型汽车零部件在正常使用过程中所受的载荷有很多种,其中包括动态载荷、静态载荷、疲劳载荷等。
不同的载荷类型对汽车零部件的强度要求也不同。
2、强度参数汽车零部件的强度参数包括极限载荷、疲劳极限载荷、刚度、应力、变形等。
不同的零部件在使用过程中所要求的强度参数也不同。
3、材料材料是影响汽车零部件强度的重要因素之一。
常用的汽车零部件材料包括钢铁、铝合金、镁合金等。
选择材料时需要考虑其强度、刚度、韧度等因素。
三、汽车结构强度分析技术的分析方法1、有限元法有限元法是汽车结构强度分析中最常用的分析方法之一。
该方法可以将复杂的汽车结构分割成有限数量的小单元,然后分别进行计算,最终得到整个结构的强度分布情况。
2、刚度法刚度法是基于汽车结构的刚度分析,通过计算汽车结构在不同载荷下的刚度,从而推断出其强度。
该方法适合于简单结构和少量载荷的情况。
3、疲劳分析法疲劳分析法是针对汽车零部件长期工作过程中所受的疲劳载荷进行分析的方法。
通过数学模型的建立,计算出零部件在不同载荷下的疲劳寿命,从而做出对其强度的判断。
四、汽车结构强度分析技术的研究进展随着汽车制造技术的不断发展,汽车结构强度分析技术也在不断创新和发展中。
近年来,越来越多的研究表明,采用优化算法来进行汽车结构强度分析可以大大提高分析的准确度和效率。
1、基于遗传算法的结构优化设计采用遗传算法来进行汽车结构的优化设计可以大大提高汽车结构的强度,同时也可以减小汽车结构的重量和成本。
该方法已经被广泛运用于汽车结构强度分析的研究中。
2、基于神经网络的汽车结构强度预测模型近年来,研究人员也开始采用神经网络的方法来建立汽车结构强度预测模型。
汽车零部件强度分析

雪佛莱C1500皮卡整车分析实例•重力荷载下悬挂臂的应力和变形•刹车分析——惯性平衡•行驶在不平整路面——子结构雪佛来C1500皮卡Copyright 2009 ABAQUS, Inc.雪佛莱C1500皮卡整车分析实例•重力荷载下悬挂臂的应力和变形重力荷载下悬挂臂的应力重力荷载下底盘的应力分布Copyright 2009 ABAQUS, Inc.雪佛莱C1500皮卡整车分析实例maximum stress =193.9 N/mm 2maximum stress = 191.4 N/mm 2静态分析——惯性平衡瞬态动力学分析刹车制动时的两种方法对比分析:•刹车制动时的应力分析(两种方法)Copyright 2009 ABAQUS, Inc.雪佛莱C1500皮卡整车分析实例•路况1结果•卡车以速度7 m/sec (25.2 km/h) 跳过一个颠簸. 车轮与路面有脱离接触的过程•卡车在不平整的路面上行驶(两种工况):Copyright 2009 ABAQUS, Inc.雪佛莱C1500皮卡整车分析实例•卡车在不平整的路面上行驶(两种工况):•路况2结果路况2下四个轮胎上的径向力路况2下纵摆(Pitch) 侧倾(Roll) 偏转(yaw) Copyright 2009 ABAQUS, Inc.雪佛莱C1500皮卡整车分析实例•卡车在不平整的路面上行驶(两种工况):•路况2结果( 子模型)A型臂上的应力分布Copyright 2009 ABAQUS, Inc.减震支架分析(GM)•实验过程中出现异常噪声结构示意图实际装配结构(与设计偏移)SCC2010减震支架分析(GM)•1500N 径向载荷SCC2010传动系统-驱动桥壳后盖失效分析•桥壳的主要损伤形式是在交变载荷作用下发生的疲劳失效•桥壳台架试验中桥壳后盖上部出现裂纹,使用FEA查找失效原因•利用Abaqus模拟整个台架试验,对桥壳进行静强度分析,进而完成疲劳寿命分析CUM2007 一汽汽研Copyright 2009 ABAQUS, Inc.传动系统-驱动桥壳后盖失效分析•模型包括:桥壳、半轴套管、减速器壳体、后盖及螺栓•Load:后盖处螺栓预紧力矩为190~260N.m减速器壳处螺栓预紧力矩为340N.m在装配面定义接触,台架试验载荷为13吨,动载系数为2.5。
汽车机械制造中的零部件强度分析

汽车机械制造中的零部件强度分析在汽车机械制造过程中,强度分析是一个至关重要的环节。
汽车零部件的强度直接关系到汽车的安全性和可靠性。
本文将从材料选择、设计优化以及强度测试三个方面,来详细探讨汽车机械制造中的零部件强度分析。
一、材料选择在汽车零部件的制造过程中,材料选择起着决定性作用。
合适的材料能够保证零部件的强度和耐用性,同时也要考虑成本和可加工性。
对于高强度要求的零部件,一般选择高强度钢材或者铝合金。
这些材料具有良好的强度和耐腐蚀性能,能够满足汽车在不同工况下的使用需求。
二、设计优化针对不同零部件,设计优化是提高其强度的关键。
在设计过程中,需要考虑零部件的几何形状、受力条件以及应力分布等因素。
通过使用CAD等辅助设计工具,可以对零部件进行全方位的强度分析。
根据受力情况进行有限元分析,确定零部件的强度分布,并通过优化设计来提高其强度。
此外,还需要根据实际情况进行合理的工艺设计,确保零部件的制造质量和一致性。
三、强度测试在汽车机械制造中,强度测试是评估零部件性能的重要手段之一。
常用的测试方法包括拉伸试验、压缩试验、弯曲试验等。
通过对零部件在实际工况下的受力测试,可以获得其强度参数,如屈服强度、抗拉强度等。
基于测试结果,可以进行强度分析,判断零部件在设计要求下的强度是否满足,并对设计进行进一步的优化与改进。
综上所述,汽车机械制造中的零部件强度分析是确保汽车安全性和可靠性的重要环节。
通过合理选择材料、优化设计和强度测试,可以提高零部件的强度和耐用性。
随着汽车技术的不断发展,强度分析将在汽车制造中扮演更加重要的角色,为汽车工程师提供更多技术支持,不断提升汽车的品质和性能。
汽车车身零部件强度性能分析与优化研究
AUTO PARTS | 汽车零部件伴随着生活品质的提升,人们的消费需求已不再局限于基本的生活必需品(如衣、食、住、行),而是更注重商品的质量与体验感。
尤其是在交通工具领域,消费者不仅关注车辆的外观设计及品牌形象,还对其驾驶感受和行车安全有较高的期望。
在此背景下,汽车的舒适性和安全性成为了决定其市场表现的关键因素之一。
尤其是汽车车身关键部件,其应用广泛且工作频次较高,因此需要具备良好的机械性能和运动特质。
当前数据研究表明,许多学者已经开始从不同角度探讨,如何通过调整车身设计以满足上述需求,进一步加深了公众对汽车功能及其重要性的认识。
1 汽车车身强度分析目的车辆的主体承担了所有与汽车相关的重量(如停止启动、刹车、转向、爬坡)及其加速情况,同时车身每个部分都承受不同类型的力和压力。
为确保在正常驾驶过程中的安全性和可靠性,需要保障这些部位具有足够的力量,防止任何可能导致损坏或性能下降的情况出现。
因此,在设计初期,就需评估并确认每一个组成部分在各种环境下所受到的力的程度,以确定其是否超过了该组件自身的耐受能力。
如果小于这个数值,就意味着这一区域的车身强度不够,需要进一步强化;反之,如果大于这一数值,则说明这里的车身强度是达标的。
宋涵艺长春市产品质量监督检验院 吉林省长春市 130000摘 要:随着社会的进步与经济发展,汽车已然成为了人们日常生活必需品,其使用率日益增加。
本文聚焦于汽车车身零部件强度性能的研究,并通过各种软件创建模型来对其进行仿真模拟。
同时,还运用新型技术手段对这一结构展开剖析,其中最关键的技术在于对车辆强度的评估。
通过研究得出结论:汽车零部件设计完全满足实际需求,且它与引擎之间的关系密切相关,对此类问题的解决方案已经有了明确的方向。
关键词:汽车零部件 强度性能 优化路径Strength Performance Analysis and Optimization of Automobile Body PartsSong HanyiAbstract: W ith the progress of society and economic development, automobiles have become a necessity in people's daily life, and their use rate is increasing day by day. This paper focuses on the study of the strength performance of automobile body parts, and simulates them by creating models through various software. At the same time, new technical means are used to analyze this structure, the most critical of which is the evaluation of vehicle strength. Through the research, it is concluded that the design of auto parts fully meets the actual needs, and it is closely related to the relationship between the engines, and there is a clear direction for the solution of such problems.Key words: a uto parts, strength performance, optimization path汽车车身零部件强度性能分析与优化研究2 汽车零部件强度研究路线2.1 零部件载荷确定零部件强度分析首先要明确载荷,载荷偏差就会导致分析成果存在一定差异,以此载荷是否准确是分析其正确性的主要因素。
汽车构件的强度分析
Q235 钢:
35 钢: 45 钢:
65Mn:
343
510
2、工作应力
•工作应力——杆件轴向拉压时截面
的应力即构件的工作时的实际应力:
FN A
工作应力仅取决于外力大小和构件的几何尺寸。 只要外力和构件几何尺寸相同,不同材料做成的 构件的工作应力也是相同的。 对于同样的工作应力,为什么有的构件破坏、有 的不破坏?显然这与材料的性质有关。
•一般ns=1.4~1.8,nb=2.0~3.5。特殊情况下可查阅手
册正确选用安全系数,可以设计出安全经济尺寸合理的构 件
塑性材料: 脆 性 材 料 :
s b
nb ns
4、拉压杆的强度条件
轴力
工作应力
FN A
横截面积
材料的 许用应力
max
5、强度条件的工程应用
有三个方面的应用:
max
FN max Amin
# 已知 FN 和 A、 [σ] 可校核强度,
即考察构件是否安全工作;
max
Amin FN max
# 已知 FN 和 [σ],可以设计构
件的截面A(几何形状);
N2= –3P N3= 5P N4= P
轴力图如右图 N
5P
2P + – 3P
+
P
x
轴力图
轴力图的特点:突变值 = 集中载荷 轴力(图)的简便求法: 自左向右: 遇到向左的P ,轴力N 增量为正;
例: 5kN N 5kN
遇到向右的P ,轴力N 增量为负。 8kN 3kN
+
8kN –
基于CAE技术的汽车零部件强度分析研究
基于CAE技术的汽车零部件强度分析研究随着汽车工业的发展,越来越多的关注点被放在汽车的安全和性能上。
在汽车的设计过程中,一个零部件的强度和可靠性是设计师最为关注的问题之一。
传统的汽车零部件强度分析方法依赖于经验和试验,需要耗费大量的时间和资金。
而基于计算机辅助工程(CAE)技术的汽车零部件强度分析则能够更快、更准确地得出各种零部件的强度和可靠性。
本文将探讨基于CAE技术的汽车零部件强度分析研究的意义、方法和应用。
一、CAE技术在汽车零部件强度分析中的意义基于CAE技术的汽车零部件强度分析,相对于传统方法,具有以下几个优点:1. 可以更加准确地预测零部件的强度和可靠性传统的汽车零部件强度分析方法,需要依赖于经验和试验,可能会忽略一些因素,影响分析结果的准确性。
而基于CAE技术的强度分析,可以对不同的工况进行模拟,并考虑不同的材料、结构、约束条件等因素,使得结论更加准确可靠。
2. 可以缩短产品开发周期传统的汽车零部件强度分析方法需要依赖于大量的试验和检验,需要耗费大量的时间和资金,而基于CAE技术的强度分析可以模拟各种工况和性能,加速了产品开发的速度。
3. 可以大幅度降低产品研发成本传统的强度分析方法需要大量的试验和检验,需要耗费大量的时间和资金,而基于CAE技术的强度分析,虽然需要购买专业的软件和硬件设备,但整个研发流程成本可以大幅降低。
4. 可以提高产品的竞争力基于CAE技术的强度分析可以更快速、更准确地得出各种零部件的强度和可靠性结果,使得产品可以更快地投入市场,提升了产品的竞争力。
二、基于CAE技术的汽车零部件强度分析方法基于CAE技术的汽车零部件强度分析方法主要包括以下几个步骤:1. 零部件建模:将零部件的三维模型导入CAE软件中,对零部件进行几何建模和网格划分,以便后续的计算。
2. 负载和边界条件的定义:定义零部件受到的力、热和其他物理因素的作用,以及零部件的约束条件,如固定点和支撑点。
底盘结构件强度分析报告
底盘结构件强度分析报告一、引言底盘结构件是整个车辆底盘的核心组成部分,其强度状况直接影响着整车的安全性和可靠性。
因此,为了确保底盘结构件的强度充足以应对各种道路条件和外部力的作用,本报告对底盘结构件的强度进行了分析和评估,并提出了相应的改进意见。
二、强度分析方法本次强度分析采用有限元分析方法,通过将底盘结构件建模为三维有限元模型,利用有限元软件进行模拟和计算,得出了各个结构件在不同工况下的应力和变形情况。
三、强度分析结果与评估1.后桥后桥是底盘结构件中的重要组成部分,承担装配在车身后部的发动机和驱动系统的重量。
在正常行驶状态下,后桥的变形和应力集中较小。
经过有限元分析,后桥在各个工况下的应力都在允许范围内,并且变形也较小,符合设计要求。
2.制动器制动器是底盘结构件中的重要安全保障部件,其强度状况直接关系到车辆制动性能。
通过有限元分析,制动器在制动过程中的应力和变形较小,符合设计要求。
但需要对制动器材料的选择进行进一步优化,以提高制动器的耐磨性和耐高温性。
3.摆臂摆臂作为车辆底盘的悬挂系统之一,直接影响到车辆的稳定性和操控性。
通过有限元分析,摆臂在悬挂行驶过程中的应力和变形较小,但由于受到道路不平坦情况下的冲击力影响,部分区域应力较高。
建议增加摆臂的加强筋以提高整体刚度和强度。
4.副车架副车架是底盘结构件中的重要组成部分,承受车身和其他重要部件的重量。
经过有限元分析,副车架在各个工况下的应力都在允许范围内,但存在一些局部应力集中的问题。
建议在局部加强区域进行结构设计优化,以提高整体强度和刚度。
四、改进意见1.后桥:无需改进,符合设计要求。
2.制动器:优化制动器材料选择,提高耐磨性和耐高温性。
3.摆臂:增加摆臂的加强筋,提高整体刚度和强度。
4.副车架:在局部加强区域进行结构设计优化,提高整体强度和刚度。
五、总结通过有限元分析,底盘结构件的强度状况得到了评估和分析。
后桥、制动器、摆臂和副车架都在各个工况下符合设计要求,但仍存在一些改进的空间。
- 1、下载文档前请自行甄别文档内容的完整性,平台不提供额外的编辑、内容补充、找答案等附加服务。
- 2、"仅部分预览"的文档,不可在线预览部分如存在完整性等问题,可反馈申请退款(可完整预览的文档不适用该条件!)。
- 3、如文档侵犯您的权益,请联系客服反馈,我们会尽快为您处理(人工客服工作时间:9:00-18:30)。
雪佛莱C1500皮卡整车分析实例•重力荷载下悬挂臂的应力和变形•刹车分析——惯性平衡•行驶在不平整路面——子结构雪佛来C1500皮卡Copyright 2009 ABAQUS, Inc.雪佛莱C1500皮卡整车分析实例•重力荷载下悬挂臂的应力和变形重力荷载下悬挂臂的应力重力荷载下底盘的应力分布Copyright 2009 ABAQUS, Inc.雪佛莱C1500皮卡整车分析实例maximum stress =193.9 N/mm 2maximum stress = 191.4 N/mm 2静态分析——惯性平衡瞬态动力学分析刹车制动时的两种方法对比分析:•刹车制动时的应力分析(两种方法)Copyright 2009 ABAQUS, Inc.雪佛莱C1500皮卡整车分析实例•路况1结果•卡车以速度7 m/sec (25.2 km/h) 跳过一个颠簸. 车轮与路面有脱离接触的过程•卡车在不平整的路面上行驶(两种工况):Copyright 2009 ABAQUS, Inc.雪佛莱C1500皮卡整车分析实例•卡车在不平整的路面上行驶(两种工况):•路况2结果路况2下四个轮胎上的径向力路况2下纵摆(Pitch) 侧倾(Roll) 偏转(yaw) Copyright 2009 ABAQUS, Inc.雪佛莱C1500皮卡整车分析实例•卡车在不平整的路面上行驶(两种工况):•路况2结果( 子模型)A型臂上的应力分布Copyright 2009 ABAQUS, Inc.减震支架分析(GM)•实验过程中出现异常噪声结构示意图实际装配结构(与设计偏移)SCC2010减震支架分析(GM)•1500N 径向载荷SCC2010传动系统-驱动桥壳后盖失效分析•桥壳的主要损伤形式是在交变载荷作用下发生的疲劳失效•桥壳台架试验中桥壳后盖上部出现裂纹,使用FEA查找失效原因•利用Abaqus模拟整个台架试验,对桥壳进行静强度分析,进而完成疲劳寿命分析CUM2007 一汽汽研Copyright 2009 ABAQUS, Inc.传动系统-驱动桥壳后盖失效分析•模型包括:桥壳、半轴套管、减速器壳体、后盖及螺栓•Load:后盖处螺栓预紧力矩为190~260N.m减速器壳处螺栓预紧力矩为340N.m在装配面定义接触,台架试验载荷为13吨,动载系数为2.5。
CUM2007 一汽汽研Copyright 2009 ABAQUS, Inc.后盖应力计算结果486.9472.225454.51538.1540.14396.87434.6304.6 257.7后盖上部最大主应力分布后盖下部最大主应力分布CUM2007 一汽汽研传动系统-驱动桥壳后盖失效分析•桥壳后盖上部最大主应力为487MPa ,后盖下部两侧45°处的最大主应力分别为540、538MPaCopyright 2009 ABAQUS, Inc.台架试验疲劳分析结果•后盖的危险部位主要分布在上部凸起部位、下部两侧45°处。
下部两侧45°处安全系数较小,但下部两侧部位过渡平滑,不容易断裂•上部凸起部位出现裂纹的主要原因为凸起部位引起了应力集中0.6114 0.618 0.649 0.5527 0.55250.7190.661 后盖疲劳安全系数分布CUM2007 一汽汽研传动系统-驱动桥壳后盖失效分析Copyright 2009 ABAQUS, Inc.前悬架几何模型Copyright 2009 ABAQUS, Inc.1,整车撞上路沿时的强度分析2,重点考察前悬架3,采用EXPLICIT 求解器行驶系--利用EXPLICIT 校核悬架的碰撞强度AUC2008 FORD整车实验与分析模型对比Copyright 2009 ABAQUS, Inc.整车实验CAE 模型行驶系--利用EXPLICIT 校核悬架的碰撞强度AUC2008 FORDCopyright 2009 ABAQUS, Inc.车辆碰到路沿时,下控制臂发生了屈曲变形,实验结果与计算结果的对比:实验结果仿真结果下控制臂屈曲行驶系--利用EXPLICIT 校核悬架的碰撞强度AUC2008 FORD Copyright 2009 ABAQUS, Inc.整个悬架最上部撞上防护栏时的分布应力云图行驶系--底盘设计中的系统级结构分析实验验证AUC2007 Fiat Auto SPA仿真与试验对比后,证明是非常有效的!行驶系--某车型下控制臂安装点强度分析•上控制臂、下控制臂、转向节、减震叉、稳定杆、转向机、弹簧、减震器以及副车架•各连接处采用衬套或铰链连接,螺栓连接处采用刚性连接简化。
分析目的:•下控制臂前点与副车架连接的螺栓孔附近出现小面积屈服现象,判断是否存在强度问题CUM2007 奇瑞汽车Copyright 2009 ABAQUS, Inc.行驶系--某车型下控制臂安装点强度分析•副车架计算结果•副车架螺栓孔处最大应力为403Mpa,超过材料的屈服极限380Mpa。
•由于最大应力超过屈服极限不大,屈服面积很小且仅在螺栓孔附近,不能确信该处是否存在强度问题,需做进一步细化分析。
副车架应力分布螺栓孔处应力分布CUM2007 奇瑞汽车Copyright 2009 ABAQUS, Inc.•局部细化分析•采用轴对称模型进行分析,副车架只截取了关于Y 轴对称的一半模型•模型中增加了螺栓、衬套内管和垫圈三个连接件,考虑部件之间的接触•副车架在螺栓连接处的局部区域采用六面体网格划分CUM2007 奇瑞汽车行驶系--某车型下控制臂安装点强度分析Copyright 2009 ABAQUS, Inc.•由结果,可明确判断该副车架螺栓连接处确实存在强度问题•螺栓的最大应力874Mpa ,超过其材料的屈服极限,但实际上螺栓经过一定的工艺处理后屈服极限能提高到1000MPa 以上,因此满足强度要求。
•衬套内管有大面积的屈服区域,不能满足强度要求。
图10副车架细化分析结果衬套内管细化分析结果螺栓细化分析结果CUM2007 奇瑞汽车•局部细化分析结果行驶系--某车型下控制臂安装点强度分析Copyright 2009 ABAQUS, Inc.27•引擎盖不带空气弹簧,有三对缓冲块,内板和外板之间的点胶连接用弹簧模拟•铰链用类型为CONNECTOR 中的HINGE ABAQUS 汽车引擎盖开关耐久性实验中的应用CUM2006 泛亚技术中心•车身侧铰链安装孔1-6个自由度约束•部分前舱的切开处和前保险杠的安装点1-6个自由度约束Copyright 2009 ABAQUS, Inc.28•将引擎盖子系统中可旋转的所有零件一定的初始角速度XXXrad/s ,计算时间为40ms ABAQUS 汽车引擎盖开关耐久性实验中的应用CUM2006 泛亚技术中心•缓冲块用刚性体由SPRINGA 单元连接到缓冲块的安装面上,刚性体位置为缓冲块顶端•用DASHPOTA 来模拟阻尼•用TRANSLATOR 引导缓冲块的运动方向Copyright 2009 ABAQUS, Inc.•三条水平线是引擎盖上关键点在关闭到盖正常关闭位置时的Z 向位移•引擎盖以一定的初速度开始向下运动,达到正常关闭位置后,由于惯性还会继续下行。
当动能完全被吸收转化为势能时,引擎盖到达最低点,然后势能释放转化成动能。
过关量结果输出ABAQUS 汽车引擎盖开关耐久性实验中的应用CUM2006 泛亚技术中心Copyright 2009 ABAQUS, Inc.Copyright 2009 ABAQUS, Inc.目的:1,用准静态方法仿真,并将车门侧碰分析结果(初始、中间和最大耐挤力)和试验结果与评价标准值进行比较,检验其强度2,对原车门结构进行改进,使车门结构能够满足国标要求。
2008CUM 长城汽车模型:Solid element + Shell element+ Connector(Hinge)不放置座椅模型,门锁闭合,压头直径305mm ,其上端面至少高出窗口下边缘13mm 车身-ABAQUS/Explicit 在车门碰撞中的强度分析Copyright 2009 ABAQUS, Inc.车身-ABAQUS/Explicit 在车门强度分析中的应用•车门分析结果(原方案)原车门强度仿真分析结果原车门强度仿真分析计算结果曲线1,初始试验下车门强度只有初始耐挤压力不合格,为6800N 低于10000N ,其他合格。
2,仿真结果为5880.5N ,由于仿真中没有考虑车门玻璃、滑轨、内饰件等的影响,故低于试验测试的6800N 。
3,验证了仿真模型的准确性,进一步改进设计。
2008CUM 长城汽车Copyright 2009 ABAQUS, Inc.车身-ABAQUS/Explicit 在车门强度分析中的应用•车门分析结果(改进方案)改进后车门强度仿真分析结果改进后车门强度仿真分析计算结果曲线改进:1,内圆管防撞梁材料改为高强度钢,屈服强度达到1000MPa 以上;2,添加车门内加强板。
同上,得到车门初始耐挤压力仿真结果为10503N ,完全能够满足国标的要求。
2008CUM 长城汽车通过接触关系模拟人员对车门挤压,得到车门变形,判断车门局部刚度是否满足要求。
车门抗凹性分析模型车门抗凹性分析变形云图车身-ABAQUS 在车门分析中的应用•车门抗凹性能CUM2007 北汽福田Copyright 2009 ABAQUS, Inc.模拟车门打开后,人员在上下车过程中对车门施加载荷,车门保持原有状态的性能。
车门下垂分析有限元模型车门下垂分析变形云图车身-ABAQUS 在车门分析中的应用•车门下垂分析CUM2007 北汽福田检验车门铰链结构以及铰链与车门和门框周围结构的合理性。
Copyright 2009 ABAQUS, Inc.保证车门在开度最大位置时,受到载荷后不发生永久变形,从而保证车门关闭状态下的密封性能。
建模时考虑了限位机构周围各零件之间的接触关系以及材料的非线性性能。
车门过开分析有限元模型车门过开分析变形云图车身-ABAQUS 在车门分析中的应用•车门过开分析CUM2007 北汽福田Copyright 2009 ABAQUS, Inc.感谢上海内燃机研究所考虑模型的真实情况:1. 加入真实爆破力2. 加入离心力3. 加入旋转离心力4. 加入往复惯性力5. 考虑曲轴转两周,模拟旋转720度情况下六缸机的发火次序为1-5-3-6-2-4活塞连杆组机构分析活塞连杆组机构分析曲轴和连杆活塞的协同运动分析结果机构运动机构运动/结构分析耦合。