焊接细节对气孔的影响(更新)
507焊条为什么焊接时有气孔[J507焊条焊接气孔形成原因及防止措施]
![507焊条为什么焊接时有气孔[J507焊条焊接气孔形成原因及防止措施]](https://img.taocdn.com/s3/m/8b95566d24c52cc58bd63186bceb19e8b8f6ecbc.png)
507焊条为什么焊接时有气孔[J507焊条焊接气孔形成原因及防止措施]气孔就是焊接时,溶池中的气泡在凝固时未能逸出,而留下来形成的孔穴。
J507碱性焊条焊时多为氮气孔、氢气孔和CO气孔。
平焊位置要较其他位置气孔多;打底层要比填充、盖面多;长弧焊要比短弧多;断弧焊要比连弧焊多;引弧、收弧和接头处要比焊缝其它位置多。
由于气孔的存在,不但会降低焊缝的致密性,削弱焊缝的有效截面积,还会降低焊缝的强度、塑性和韧性。
根据J507焊条溶滴过渡的特点、选择焊接电源、合适的焊接电流、合理的引弧和收弧、短弧操作、直线运条等方面加以控制,在焊接生产中得到了很好的质量保证。
气孔;焊接;电弧;熔孔;熔池;焊缝 1.气孔的形成熔化金属在高温时溶解大量气体,随着温度的下降,这些气体以气泡形式逐渐自焊缝中逸出,来不及逸出的气体残留在焊缝内就形成气孔。
形成气孔的气体主要有氢气和一氧化碳。
从气孔的分布状态看有单个气孔、连续气孔、密集气孔;从气孔的部位不同可分为外部气孔和内部气孔;从形状上看有针孔、圆气孔、条状气孔(气孔呈条虫形,是圆气孔的连续)、链状和蜂窝状气孔等。
就目前来说,J507焊条在焊接时产生气孔缺陷更为典型。
因此,以J507焊条焊接低碳钢为例,对产生气孔缺陷的原因与焊接工艺的关系作一些讨论。
2.J507焊条溶滴过渡的特点J507焊条为高碱度的低氢型焊条,该焊条在直流焊机反极性时方可正常使用。
因此无论采用何种类型的直流焊机,其溶滴过渡均由阳极区向阴极区过渡。
在一般手工电弧焊时,阴极区温度略低于阳极区温度。
因此,无论何种过渡形式溶滴到阴极区后温度均会降低,造成了该种焊条各溶滴的聚合过渡到溶池中去,即形成了粗溶滴过渡形式。
但由于手工电弧焊是人为的因素:如焊工熟练程度、电流电压大小等不同,其溶滴的大小也是不均匀的,形成了溶池的大小也是不均匀的。
因此,在外来及内在因素的影响下,形成了气孔等缺陷。
同时,碱性焊条药皮中又含有大量的萤石,在电弧作用之下分解出电离电位较高的氟离子,使得电弧的稳定性变差,进而又造成了电焊时溶滴过渡的不稳定因素。
常见焊接缺陷和产生原因

常见焊接缺陷和产生原因焊接是一种常见的金属加工方式,它通过熔化金属和固态金属的熔温,在熔融状态下加固与连接金属材料。
然而,在焊接过程中往往会出现各种焊接缺陷,这些缺陷会对焊接件的质量和性能产生负面影响。
下面我将就一些常见的焊接缺陷及其产生原因进行详细介绍。
1.焊缝气孔:焊缝气孔是焊接过程中最为常见的缺陷之一,其主要产生原因有以下几个方面:(1)焊接材料中含有水分和气体等插混物质;(2)焊接电流过大,造成焊缝焦化和气泡形成;(3)气体在焊接过程中没有得到有效排除。
2.夹渣:夹渣缺陷是指在焊接过程中残留了未熔化的焊接剂和其他杂质,主要原因有以下几个方面:(1)焊接材料表面不干净,存在脏污物;(2)焊接剂使用不当,或焊接过程中焊接剂分布不均匀;(3)焊接过程中未能有效清除残留的焊接剂和其他杂质。
3.焊缝裂纹:焊缝裂纹是焊接过程中比较严重的缺陷,其产生原因主要有以下几个方面:(1)焊接材料强度不匹配,在焊接过程中受到应力的影响产生裂纹;(2)焊接过程中出现变形,导致焊接材料的局部应力集中;(3)焊接过程中温度控制不当,使得焊接过程中产生热裂纹。
4.焊接变形:焊接变形是指焊接件在焊接过程中由于热应力的影响而发生形变,主要原因有以下几个方面:(1)焊接时温度分布不均匀,导致产生局部过热和冷却不均匀;(2)焊接速度控制不当,导致焊接材料热应力过大;(3)焊接过程中焊接材料热胀冷缩不均匀,产生应力集中。
总的来说,焊接缺陷的产生主要是由于焊接工艺和焊接操作等原因引起的。
为了减少焊接缺陷的产生,我们可以采取以下一些措施:(1)通过合理设计焊接接头和选择适当的焊接材料,尽量减少焊接应力的产生;(2)严格控制焊接工艺参数,如焊接电流、电压、速度等,保证焊接过程的稳定性和一致性;(3)合理选择焊接材料和焊接剂,确保其质量和适用性;(4)加强焊接操作过程中的质量控制,如清洁焊接材料表面、预热焊接材料、采取适当的焊接顺序等;(5)对焊接接头进行适当的热处理,消除或减少焊接应力的存留。
焊接气孔产生的原因和防范措施
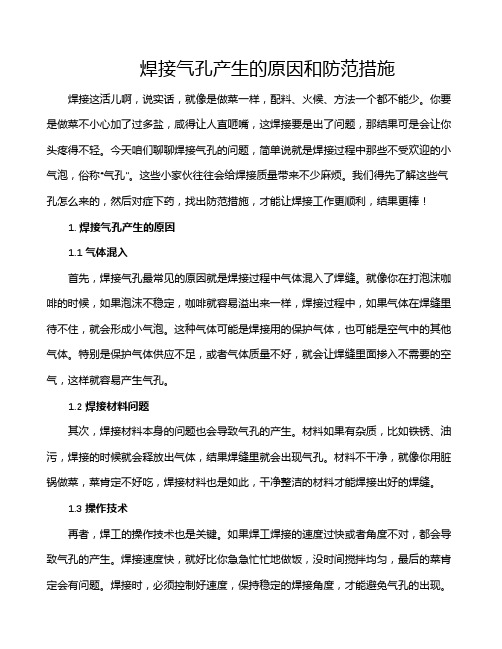
焊接气孔产生的原因和防范措施焊接这活儿啊,说实话,就像是做菜一样,配料、火候、方法一个都不能少。
你要是做菜不小心加了过多盐,咸得让人直咂嘴,这焊接要是出了问题,那结果可是会让你头疼得不轻。
今天咱们聊聊焊接气孔的问题,简单说就是焊接过程中那些不受欢迎的小气泡,俗称“气孔”。
这些小家伙往往会给焊接质量带来不少麻烦。
我们得先了解这些气孔怎么来的,然后对症下药,找出防范措施,才能让焊接工作更顺利,结果更棒!1. 焊接气孔产生的原因1.1 气体混入首先,焊接气孔最常见的原因就是焊接过程中气体混入了焊缝。
就像你在打泡沫咖啡的时候,如果泡沫不稳定,咖啡就容易溢出来一样,焊接过程中,如果气体在焊缝里待不住,就会形成小气泡。
这种气体可能是焊接用的保护气体,也可能是空气中的其他气体。
特别是保护气体供应不足,或者气体质量不好,就会让焊缝里面掺入不需要的空气,这样就容易产生气孔。
1.2 焊接材料问题其次,焊接材料本身的问题也会导致气孔的产生。
材料如果有杂质,比如铁锈、油污,焊接的时候就会释放出气体,结果焊缝里就会出现气孔。
材料不干净,就像你用脏锅做菜,菜肯定不好吃,焊接材料也是如此,干净整洁的材料才能焊接出好的焊缝。
1.3 操作技术再者,焊工的操作技术也是关键。
如果焊工焊接的速度过快或者角度不对,都会导致气孔的产生。
焊接速度快,就好比你急急忙忙地做饭,没时间搅拌均匀,最后的菜肯定会有问题。
焊接时,必须控制好速度,保持稳定的焊接角度,才能避免气孔的出现。
1.4 温度控制不当最后,温度控制也很重要。
焊接的时候,如果温度过高或过低,都可能导致气孔的产生。
温度过高就像把牛奶煮得过热,容易产生很多泡沫,温度过低则会让焊缝的熔合不完全,气体难以逸出,最终也会形成气孔。
2. 如何防范焊接气孔2.1 保障气体供应首先,确保焊接用的气体质量合格,供应稳定。
就像你做菜时要用新鲜的食材一样,焊接用的气体也要确保纯净。
如果气体供应不足,容易出现问题。
浅析焊接工艺参数对焊接缺陷影响

浅析焊接工艺参数对焊接缺陷影响焊接工艺参数对焊接缺陷有着非常重要的影响。
在进行焊接工艺参数的设置时,必须要考虑到焊接材料的性质、焊接对象的形状、应力状态、特殊要求等因素,从而保证焊接质量并避免焊接缺陷的发生。
首先要考虑的是焊接工艺的热输入量。
热输入量是指焊接时会输送到焊接区域的热量。
热输入量的大小会影响焊接接头的熔深度、焊接区域的冷却速率,从而对焊接质量和焊接缺陷产生影响。
如果热输入量过大,会导致焊接池过深,焊接区域的温度变化过剧烈,易造成热裂纹、钢材变形等缺陷;而热输入量过小,则会导致焊缝强度不足,焊接质量差,极易发生间隙气孔、焊接错边等缺陷。
其次是焊接电流和电压的选择。
在焊接的过程中,电流和电压的大小直接影响着焊接质量。
如果电流过大,会导致焊接过程中的蒸汽和气体无法完全排出,从而产生热裂纹和未熔合等缺陷;而电流过小,则会导致焊缝深度不够,质量低,容易出现间隙气孔和熔合不良等缺陷。
焊接电压如果太高,会导致热输出过大产生气孔等缺陷;而太低会导致熔敷量不足。
第三个影响焊接缺陷的因素是焊接速度。
在进行焊接的过程中,焊接速度对焊接缺陷有着直接的影响。
一般来说,焊接速度不宜过快或者过慢,过快的焊接速度会使焊接池不充分熔化,未能完全填满焊缝,导致焊缝质量不高,很容易出现熔合不良和未熔合等缺陷;而过慢的焊接速度会产生过多的热量,导致焊缝过深,形成不必要的熔渣和气孔等缺陷。
最后一个影响焊接缺陷的因素是气体保护。
在进行焊接的过程中,对于不同的焊接材料和对象,需要选择不同的气体保护方式和气体保护剂,以保证焊接过程中不受到氧化或其他物质的影响。
如果气体保护不到位或者保护剂不正确,很容易导致焊缝中的气孔、夹杂物的产生。
综上所述,焊接工艺参数直接影响着焊接质量和焊接缺陷。
在进行焊接时,要根据材料、环境和应力情况等摸清合适的热输入量,电流和焊接时间,保证气体流量和保护剂的正确性,从而尽可能避免焊接缺陷的产生。
不锈钢焊接气孔产生的原因及措施
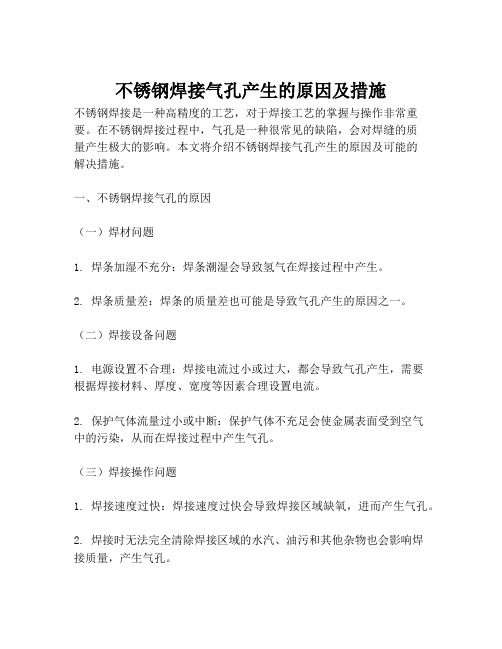
不锈钢焊接气孔产生的原因及措施不锈钢焊接是一种高精度的工艺,对于焊接工艺的掌握与操作非常重要。
在不锈钢焊接过程中,气孔是一种很常见的缺陷,会对焊缝的质量产生极大的影响。
本文将介绍不锈钢焊接气孔产生的原因及可能的解决措施。
一、不锈钢焊接气孔的原因(一)焊材问题1. 焊条加湿不充分:焊条潮湿会导致氢气在焊接过程中产生。
2. 焊条质量差:焊条的质量差也可能是导致气孔产生的原因之一。
(二)焊接设备问题1. 电源设置不合理:焊接电流过小或过大,都会导致气孔产生,需要根据焊接材料、厚度、宽度等因素合理设置电流。
2. 保护气体流量过小或中断:保护气体不充足会使金属表面受到空气中的污染,从而在焊接过程中产生气孔。
(三)焊接操作问题1. 焊接速度过快:焊接速度过快会导致焊接区域缺氧,进而产生气孔。
2. 焊接时无法完全清除焊接区域的水汽、油污和其他杂物也会影响焊接质量,产生气孔。
二、不锈钢焊接气孔的解决措施(一)选择适合的焊接工艺1. 选择正常温度下的焊接工艺,例如TIG焊,这种焊接方式可以有效地减少气孔产生。
2. 选择合适的焊接电流,并通过调整电流达到最佳焊接质量。
(二)控制焊接速度和焊接时间1. 控制焊接速度,让金属处于理想的热固态区域内,以保证焊接质量。
2. 控制焊接时间,让焊缝成形后立即停止焊接,以避免焊接过热和缺氧导致的气孔产生。
(三)加强材料清洁和预处理1. 准备焊接材料前,彻底清洗焊接区域,避免焊接时杂质存在。
2. 选用高质量的保护气体,避免气体流量过小或中断导致的气孔产生。
总之,不锈钢焊接过程中气孔问题是一个需要关注与解决的难点。
只有掌握了正确的处理措施,才能减少不锈钢焊接气孔产生的可能性,保证焊接质量和安全。
焊接气孔和夹杂
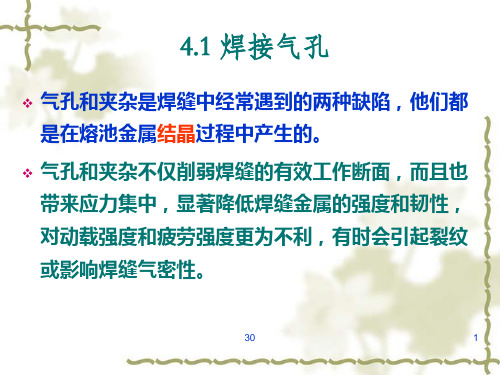
气泡的半径越大,熔池中液态金属的密度越大, 粘度越小时,气泡的上浮速度就越大,焊缝就不 易产生气孔。
综上所述,气孔形成过程与结晶过程有些类似,
也是由生核、核长大组成,当气泡长大到一定程
度便开始上浮,在不利条件下(当气泡的浮出速
度小于结晶速度时)就有可能残留在焊缝中形成
ph>po
式中,ph——气泡内部压力;
ph =pH2+pN2+pCO+pH2O+… po——阻碍气泡长大的外部压力。 在具体条件下,只有一种气体起主要作用,而其它 气体起辅助作用。
外部压力包括:大气压力、液态金属、熔渣的压力 和表面张力引起的附加压力。
若气泡核附着在液固相表面时,表面张力引起的附
加压力将减小,气泡便易30于长大。
[C]+[O]=CO
[FeO]+[C]=CO+Fe
[MnO]+[C]=CO+Mn
[SiO2]+[C]=2CO+Si CO气体不溶于钢,在熔池处于高温时,可以以气泡形 式从熔池中逸出,不会形成气孔。但在熔池凝固阶段一 方面由于成分偏析使液相中局部区域[FeO]和[C]含量提 高,促使CO生成。另一方面,温度降低,金属熔池粘 度加大,在快速结晶下CO来不及逸出变成气孔。
和提高Aa/A比值,使能量30 减少。
9
可以认为,Aa/A的比值最大的地方就是最有 可能产生气泡的地方,树枝晶相邻的凹陷处 和母材金属尚未熔化晶粒的界面上Aa/A的比 值最大,因此,在这些部位最易产生气泡核。
此外,当Aa/A比值一定时,θ角越大,形成 气泡核所需的能量越小。
30
10
保护气体对铝合金焊接气孔敏感性的影响
保护气体对铝合金焊接气孔敏感性的影响铝合金是一种轻质高强度的金属材料,在工业制造和航空航天等领域得到广泛应用。
然而,铝合金的焊接过程中会出现气孔等缺陷,严重影响焊接质量和性能。
保护气体是铝合金焊接中常用的一种手段,通过在焊接过程中提供足够的保护气氛,可以减少氧气等杂质进入焊接区域,减小气孔的形成。
然而,保护气体的种类、流量、气氛稳定度等因素会影响铝合金焊接的气孔敏感性,本文对此进行探讨。
在铝合金的焊接过程中,如果有过多的氧气进入焊接区域,就容易导致气孔的形成,从而影响焊接质量和性能。
保护气体可以在焊接过程中与氧气反应,生成稳定的保护气氛,从而满足焊接区域的保护要求,减小气孔的形成。
不同的保护气体对气孔的影响有所不同,下面分别介绍:1. 纯氩气保护焊纯氩气是铝合金焊接中常用的保护气体,具有较好的保护效果。
在气孔敏感性方面,纯氩气对低温铝合金的气孔抑制效果较好,但对高温铝合金的气孔抑制效果较弱。
第二,保护气流量的影响保护气的流量是影响铝合金焊接气孔敏感性的一个重要因素。
如果保护气流量不足,氧气等杂质容易渗入焊接区域,导致气孔的形成。
但如果保护气流量过大,会导致气泡在焊接池底部产生挥发现象,也会影响焊接质量和性能。
因此,选择合适的保护气流量对焊接质量和性能至关重要。
第三,气氛稳定度的影响保护气的气氛稳定度也是影响铝合金焊接气孔敏感性的一个重要因素。
如果保护气的流量和压力不稳定,就会导致焊接过程中的保护气孔出现激烈的波动和涡流,从而关键时刻无法保护焊缝。
因此,稳定的保护气氛对于铝合金焊接来说至关重要。
综上所述,保护气体对铝合金焊接气孔敏感性的影响取决于很多因素,包括保护气体种类、流量、气氛稳定度等。
在实际焊接过程中,需要根据焊接工艺要求选择合适的保护气体和流量,并注意维持稳定的焊接气氛,从而确保铝合金焊接质量和性能的稳定。
铝/钢CMT焊接工艺参数对界面连接状态及气孔分布的影响
V0 1 . 3l No . 6 No v . 2 01 3
文章编号 : 1 0 0 8—1 4 0 2 ( 2 0 1 3) 0 6-0 9 6 1- 0 3
.
钢
焊接工艺参数对界面j 奎 接状态及 Nhomakorabea孔分布的影Ⅱ
吴 丹, 王 军, 田春英 , 张淑达
( 佳 木斯大学 . 黑龙江 佳木斯 l 5 4 | D 0 r 7 )
表 1 铝 合金 及焊 丝的化 学成 分 ( w t . %)
采用 奥地 利 F r o n i u s 公 司生 产 的 C M T 5 0 0 0 i 系 列焊 机进行 工 艺 试 验 ,焊 前 用 丙 酮 对 工 件 表 面 进
相显微镜下观察气孑 L 形貌及数量 , 获取不同工艺参 数对焊缝气孔数量及分布影响规律 , 结合焊缝的界 面连接状态 , 获得最佳焊接工艺.
的熔化 极气 体保 护 ( G M AW) 相 比金 属 过 渡 温度 更
1 试 验 材 料 及 方 法
焊接材质选择厚度为 l m l n的铝合金板 6 0 6 1 . 浸铝钢板 S A 1 C镀铝层厚度为 2 0— 3 0 t x m, 镀层为 A l — S i 合金 , 其中含铝的质量分数为 9 4 . 2 %, 含S i 的质量 分数 为 5 . 8 %. 焊 丝选 用 1 . 2 m m 直径 的 4 0 4 3 ( A 1 S i 5 ) , 材料 的化 学成 分见 下表 1 .
综上 所述 , 气 孔 数 量 控 制在 了一 个 允 许 范 围 % 内, 且 满足 焊缝 与 母 材 界 面 连接 , 最 佳焊 接 电 流为 8 5 A, 焊 接速 度为 0 . 7 5 r n / mi n .
CO2气体保护焊气孔原因分析
CO2气体保护焊气孔原因分析CO2气体保护焊会发生很强烈的氧化还原化学反应,所以飞溅比较大,损失热量多,只要那一个环节没有控制好,就容易出气孔,出气孔的主要原因如下:1、焊缝没清理干净,存在油污,水,锈等等;2、焊接时没注意防风;3、气管漏气(漏气在焊接时会形成射吸,把周围空气吸进来);4、加热器不工作(纯CO2不加热会带潮气);5、焊接时焊摆过宽;6、焊丝干伸长过大;7、喷嘴飞溅堵赛,变形严重;8、焊丝质量问题;9、气体不纯;10、导电杆烧穿(没装陶瓷气赛烧穿后会造成喷嘴一边气大一边气小);11、送丝小车的电磁阀损坏或者堵塞,导致刚开始焊接时有气,但是气体流量越来越小,直至停止送气;12、二氧化碳减压表损坏,能加热但是流量不可调节;13、气体流量过大也会产生紊流,吸入空气,导致气孔;14、焊道间隙过大,保护气覆盖范围不足也会产生气孔;15、气体流量太小,气流挺度小产生气孔;16、管道输送气体,长时间不用,气包中第一包气没有放出,产生气孔;17、使用不规范的自制绝缘套,长时间使用绝缘套在喷嘴内燃烧,使CO2气体分解,产生气孔;18、喷嘴歪斜安装,导电咀不在喷嘴中心,即焊丝熔滴不在保护气氛围中心,怎么焊都出气孔;19、焊枪(OTC)尾部密封圈失效,产生气孔;20、分流器小孔加工角度不标准,导致保护气在喷嘴内形成紊流,产生气孔;21、加热器进气口堵塞,里面有个小滤网;22、气体管线不应存在较大的泄漏,较大的泄漏会使气体管线渗入少量空气。
这是因为,用于保护焊接区域不受空气侵害的CO2气体大都是酿酒厂或酒精厂的副产品,不可避免地含有或多或少的水分或其它含氢物质,同时混合气体中的氩气也常含有水分。
如果保护气体中的水分和其它含氢物质的总含量超过一定限度,那么焊缝金属中氢气孔的产生将是必然的。
但是,如果保护气体中的水分和其它含氢物质的含量按相关标准要求被控制在一定的范围内,那么CO2气体保护焊和富氩混合气体(80%Ar+20%CO2)保护焊焊缝金属中一般不会产生很多的氢气孔。
焊缝气孔产生原因及改善措施
N气孔(为蜂窝状):主要原因是气体保护效果不好, 保护气层遭到破坏,大量空气侵入焊接区所致。 气路漏气,喷嘴堵塞严重;喷嘴松动,焊枪角度太 大;干伸长度大;规范不对,焊接部位有风。
精品
焊接中常见的气孔缺陷及预防措施
起因
母材污染(附着油、漆、涂料 等)
精品
原因分析
二氧化碳电弧焊时,由于熔池表面没有熔渣盖覆, CO2气流又有较强的冷却作用,因而熔池金属凝固 比较快,但其中气体来不及逸出时,就容易在焊缝 中产生气孔;焊接速度快,熔池结晶快,则气体不 易排出,也易产生气孔 。可能产生的气孔主要有3 种:一氧化碳气孔、氢气孔和氮气孔。 CO气孔(为条虫状):焊丝不合格,工件含碳量大。
焊缝气孔产生原因及改善措施
精品
气孔危害
气孔是指焊接时,熔池中的气体未在金属凝固前 逸出,残存于焊缝之中所形成的空穴。气体是熔 池从外界吸收的,或焊接冶金过程中反应生成的。 气孔可分为氢气孔、氮气孔、二氧化碳气孔、一 氧化碳气孔、氧气孔,熔焊中常见的气孔是氢气 孔、一氧化碳气孔。气孔减少了焊缝的有效截面 积、使焊缝疏松,从而降低了接头的强度,降低 塑性,还会引起泄漏,气孔也是引起应力集中的 因素,氢气孔还可能促成冷裂纹。
防止措施
1)仔细清除坡口面及其两侧的油、锈、 水分、氧化皮等 。
焊丝上附着锈、水分等。
1)往往是某段焊丝有锈,可去掉锈丝段, 再使用。水分要拭去,干燥后再用。
焊接 缺陷 及防 止措 施
受风的影响 喷嘴被飞溅堵塞 喷嘴与母材间距离太大
焊接参ห้องสมุดไป่ตู้不当
保护气体流量太小
1)设置屏风 2)增加保护气体流量。 1)清除飞溅 2)在喷嘴内涂敷防飞溅剂 1)保证喷嘴与母材间距≯25mm 1)增加焊接电流 2)降低焊接速度 1)气压不足0.1MPa时,更换气源 2)为适应有风的场合加大流量 3)检查预热器工作是否正常 精4品)检查气管及接头漏气处
- 1、下载文档前请自行甄别文档内容的完整性,平台不提供额外的编辑、内容补充、找答案等附加服务。
- 2、"仅部分预览"的文档,不可在线预览部分如存在完整性等问题,可反馈申请退款(可完整预览的文档不适用该条件!)。
- 3、如文档侵犯您的权益,请联系客服反馈,我们会尽快为您处理(人工客服工作时间:9:00-18:30)。
焊接细节对气孔的影响:
1.铆接定位的焊点,在焊接时没有去除会引起气孔的产生。
2.碱洗只是把油污去除了,并没有去除氧化膜。
氧化膜会引起气孔的产生。
3.起弧和收弧没有相交,接口处没有烧透,产生气孔
4.焊接厚度大于15MM的需预热,有温度范围150~250℃温度低了易产生气孔,温度高了对材料性能有影响。
5.当气瓶压力表显示<0.1Mpa时应停止焊接更换气瓶,(供气不足还强行焊接,必然会产生气孔等缺陷)
6.气保焊不适合风速大于1.5M/S的环境
7.焊件温度低于5℃
1.铝合金焊接缺陷的种类?
铝及其铝合金MIG焊时,罕见的焊接缺陷可分为外部缺陷和内部缺陷两大类
外部缺陷位于焊缝外表面,罕见的有表面气孔、裂纹、咬边、未焊透和烧穿等;
内部缺陷位于焊缝的内部,需要用破坏性试验或无损探伤等方法才干发现,如内部气孔、裂纹、夹渣及未熔合等。
2.铝合金MIG焊焊接缺陷发生的原因
1气孔焊接时熔池中的气孔在凝固时未能逸出而留下来所形成的空穴称为气孔。
MIG焊接过程中,气孔是不可防止的只能尽量减少它存在培训的过程中,仰角焊、立向上焊气孔傾向尤为明显,根据DIN30042规范规定,单个气孔的直径最大不能超过0.25(为板厚)密集气孔的单个直径最大不超过0.25+0.01(为板厚)氢是铝及铝合金熔化焊产生气孔的主要原因。
氮不溶于液态铝,铝又不含碳,因此铝合金中不会发生氮气孔和一氧化碳气孔;氧和铝有很大的亲和力,总是以氧化铝的形式存在所以也不会发生氧气孔;氢在高温时大量的溶于液态铝,但几乎不溶于固态铝,所以在凝固点溶于液体中的氢几乎全部析出,形成气泡。
但铝和铝合金的比重轻,气泡在熔池中的上升的速度较慢,加上铝的导热能力强凝固,有利于气泡的浮出,故铝和铝合金易产生气孔,氢气孔在焊缝内部一般呈白亮光洁状。
氢的来源比较多,主要来自弧柱气氛中的水、焊丝以及母材所吸附水分对焊缝气孔的发生经常占有突出的地位。
一:防止措施
1厂房环境湿度>70% 及空气的对流
空气中的湿度影响弧柱气氛。
MIG焊接时,焊是以细小熔滴形式通过弧柱而落入熔池的由于弧柱温度最高,熔滴比外表积很大,故有利于熔滴金属吸收氢,发生气
孔的倾向也更大些。
弧柱中的氢之所以能够形成气,与它铝合金中的溶解度变化有。
如前段所说,凝固点时氢的溶解度从0.69突降到0.036ml/100g相差约20倍(钢
中只相差不到2倍)这是氢容易使焊缝产生气孔的重要原因之一。
控制了弧柱气氛中的水分后,母材和焊丝所带的氧化膜所吸附的水分成为生成焊缝气孔的主要原因
另外,维护气体流量缺乏或过量也会引起气孔的呈现。
维护气体流量缺乏不能排除弧柱气氛中的空气,空气中的水分将分解成氢进入熔池中发生氢气孔;反之维护气体流量过
大又会将空气卷入弧柱区和熔池,同样会使焊缝气孔趋势增。
提前送气和焊后延时送气的时间设置对焊接接头气孔的发生也有很大关系。
2.母材的清洁
母材外表通常会有少量油脂、灰尘等杂。
通过经焊前母材清理和未经清理的焊缝对,清理过的焊缝气孔明显少于未经清理的焊缝气孔。
因此如果焊前没有仔细清理母材表面,发生气孔的倾向将加大。
二夹渣:
焊后残留在焊缝中的熔渣称为夹渣。
夹渣会降低焊接接头的塑性韧性,还会引起应力集中,根据DIN30042规范规定,夹渣是绝对不允许存在通过培训,得出这样一个结论,夹渣大多出现在厚板多层焊,比方T10BWPCT10BWPF位置试板焊接,夹渣是其主要的缺陷。
发生夹渣的原因主要是焊接之前没有对前一道焊缝进行仔细的清理,焊层或焊道中仍存在熔渣或氧化物,焊接时用高的行走速度的时候,熔池金属和熔渣得到热量缺乏,熔池冷却速度过快,使得熔渣来不及上浮就已经凝固,焊缝中形成夹渣。
另外焊丝过长和焊嘴角度过大致使维护气体效果降低也会引起夹渣。