压铸件气孔的成因和解决办法
分析铸造过程气孔生成的原因及对策

分析铸造过程气孔生成的原因及对策铸造过程中气孔生成的原因及对策分析铸造是一种重要的金属加工方法,可用于生产各种形状的金属制品。
然而,在铸造过程中,气孔的生成是一个常见的问题,它可能会影响到铸件的质量和性能。
本文将分析铸造过程中气孔生成的原因,并提出相关的对策。
一、原因分析1. 铸造材料的问题在铸造过程中,铸造材料的纯度、含气量和化学成分会直接影响气孔的生成。
杂质和气体在熔融金属中的存在可能会形成气泡,并在凝固过程中被包裹在铸件内部。
此外,如果铸造材料中的挥发性成分含量过高,也容易导致气孔的生成。
2. 模具设计和制造的问题模具的设计和制造不当也是气孔生成的原因之一。
设计不合理的浇口和冷却系统会导致金属在流动过程中吸入空气,形成气孔。
模具的材质和表面处理也会对气孔的生成产生影响,表面粗糙度过高或使用粘结性差的涂料可能会导致铸件表面气孔的形成。
3. 浇注工艺的问题浇注工艺是影响气孔生成的关键因素之一。
浇注温度、浇注速度和浇注角度等工艺参数的控制不当可能导致金属流动不畅,气泡无法完全排出,从而形成气孔。
此外,如果铸件内部存在复杂的几何形状,也会增加气泡在凝固过程中的积累和无法排出的可能性。
二、对策措施1. 提高铸造材料的质量为了减少气孔的生成,需要选用高纯度的铸造材料,并控制好化学成分和气体含量。
可以通过加入脱气剂来减少金属中的气体含量,同时加入合适的合金元素可以改善金属的流动性和凝固性能。
2. 优化模具设计和制造合理的模具设计可以改善金属流动状态,减少气体吸入的可能性。
浇口的设计应考虑到金属的流动路径和速度,确保金属在流动过程中尽量少吸入空气。
此外,模具的材质应选用适合的材料,并进行表面处理以提高其抗粘性和耐腐蚀性能。
3. 控制好浇注工艺参数合理控制浇注温度、浇注速度和浇注角度等参数可以使金属流动顺畅,减少气泡的生成。
同时,在铸造过程中可采用自动浇注系统和真空吸气设备来排除金属中的气体。
对于复杂几何形状的铸件,可以采用分次浇注或采用喷浇工艺来减少气孔的生成。
铸造气孔解决方法

铸造气孔解决方法一、背景介绍铸造是一种常见的制造工艺,但在铸造过程中,气孔是一个常见的缺陷。
气孔会降低铸件的强度和密封性,影响其使用寿命和品质。
因此,解决气孔问题对于提高铸件质量至关重要。
二、气孔的成因1.金属液中溶解氧过多2.熔融金属流动速度过快3.模具表面粗糙或有杂质4.金属液中含有挥发性物质三、预防措施1.减少金属液中溶解氧含量:可通过加入还原剂、增加保温时间等方法来实现。
2.控制熔融金属流动速度:可通过调整浇注系统设计、增加浇注口数量等方法来实现。
3.改善模具表面状态:可通过精密加工模具表面、清洁模具表面等方法来实现。
4.减少挥发性物质:可通过改变熔融金属组成、使用合适的保护剂等方法来实现。
四、处理方法1.机械处理法:包括打磨和修补。
打磨可通过砂轮、砂带等工具进行,修补则可采用填充剂填充气孔。
2.热处理法:包括退火和时效。
退火可使气孔内部的氧分子扩散到金属液中,使气孔逐渐消失;时效则是利用金属在高温下的再结晶过程来消除气孔。
3.化学处理法:包括浸泡、电解和喷涂等方法。
浸泡可将含有铝的溶液浸泡在铸件表面,形成一层保护膜以防止氧化;电解则是利用阳极溶解作用来填补气孔;喷涂则是将特定材料喷涂在铸件表面,形成一层密封膜。
五、常见问题及解决方法1. 气孔数量较多:应从预防措施入手,加强金属液净化、控制熔融金属流动速度等。
2. 气孔回火后仍存在:应采取机械处理法或化学处理法进行修复。
3. 铸件表面存在小气孔:可采用电解或喷涂等化学处理法进行修复。
六、结论气孔是铸造过程中常见的缺陷,但通过预防措施和处理方法,可以有效地减少或消除气孔问题。
在实际生产中,应根据具体情况采取不同的解决方法,以提高铸件质量和使用寿命。
压铸件常见缺陷及改善对策

压铸件常见缺陷及改善对策压铸件是常用的金属制造工艺之一,用于制造各种产品,如汽车零件、电子设备外壳等。
然而,压铸件在制造过程中往往会出现一些常见的缺陷,例如气孔、缩松、热裂纹等。
为了提高压铸件的质量,需要采取适当的改善对策。
首先,气孔是压铸件中常见的缺陷之一、这主要是由于金属液中溶解的气体在凝固时无法完全排除,导致气孔形成。
改善对策包括以下几个方面:1.改善炉内冶炼过程:合理调节熔化温度和熔化时间,增加金属液中的液体相和气体相之间的接触时间,有助于气体的溶解和脱除。
2.调节压铸机参数:增加射压和射速,可以改善金属液流动性,减少气体残留的可能性。
3.优化压铸模具结构:设计合理的浇口和废渣口,有利于气体的排除,减少气孔的生成。
其次,缩松是另一个常见的缺陷。
缩松是指压铸件中因内部金属液冷却不均匀而形成的孔洞或松散区域。
改善对策包括以下几个方面:1.控制金属液的冷却速度:通过调整铸型温度、浇注温度和浇注速度等参数,使金属液冷却均匀,减少缩松的可能性。
2.优化浇口和冷却系统:设计合理的浇口和冷却系统,有利于金属液的流动和冷却,减少缩松的生成。
3.采用适当的金属合金:一些合金具有较好的流动性和凝固性,能够减少缩松的产生。
最后,热裂纹是压铸件常见的缺陷之一、这是由于金属在冷却过程中由于内部应力过大而发生裂纹。
改善对策包括以下几个方面:1.控制冷却速率:通过调节冷却速率,使金属在冷却过程中应力得到释放,减少热裂纹的发生。
2.优化模具设计:设计合理的模具结构,减少金属液在冷却过程中的应力集中,可以减少热裂纹的生成。
3.采用合适的退火工艺:通过合适的退火工艺,使金属在冷却过程中应力得到释放,减少热裂纹的发生。
总之,压铸件常见的缺陷包括气孔、缩松和热裂纹等,需要采取一系列的改善对策来提高压铸件的质量。
通过优化工艺参数、改善模具设计和采用合适的金属合金,可以减少这些缺陷的发生,并提高压铸件的品质。
浅谈铸件气孔的产生及其防止措施

浅谈铸件气孔的产生及其防止措施气孔是铸造生产中常见的铸件缺陷之一。
在铸件的废品中,据统计,由于气孔导致的铸件废品占废品总数的三分之一左右。
气孔是气体聚集在铸件表面、皮下和内部而形成的空洞。
气孔的孔壁光滑,无一定的形状、尺寸和位置。
气孔有各种类型,其产生的原因各不相同,按气体来源,一般将气孔分为三类:侵入性气孔、析出性气孔和反应性气孔。
一、侵入性气孔由于浇注过程中液态金属对铸型激烈的热作用,使型砂和芯砂中的发气物(水分、粘接剂等)气化、分解和燃烧,生成大量气体,加上型腔中原有的气体,这些气体部分侵入液态金属内部而不能逸出所产生的孔洞,称为侵入性气孔。
1.侵入性气孔的形成条件由于浇注时铸型在液态金属的高温作用下产生大量气体,从而使液态金属和铸型界面上的气体压力骤然增加,气体可能侵入液态金属,也有可能从型砂或冒口、出气孔中排出型外,只有在满足下列条件的情况下型(芯)砂中的气体才会侵入液态金属即P气>p液+p阻+p腔式中p气:液态金属和砂型界面的气体压力;P液:液态金属的静压力(p液=ρgh)P阻:气体侵入液态金属时,由于液态金属表面张力而引起的阻力P腔:型腔中液态金属液面上的气体压力2.防止侵入性气孔的主要方法和工艺措施(1)降低砂型(芯)界面的气体压力是最有效的手段。
如选用透气性好,发气量低的造型材料;控制型砂的水分及其它发气附加物;应用发气量低、发气速度慢、发气温度高的粘结剂;砂型(芯)排气要畅通,增加出气孔,提高铸型的排气能力;浇注后及时引火。
引火后可听到气体的爆燃声和砂箱周围燃烧的火焰,砂箱移开后,可看到下部潮湿的痕迹。
说明有大量的气体产生如H2、O2、CO、H2S等气体。
(2)适当提高浇注温度,延迟凝固时间,使侵入的气体有充分的时间从液态金属中上浮和逸出。
(3)加快浇注速度,增加上砂型高度,使有效压力头增加,提高液态金属的静压力。
(4)浇注系统在设置时,应注意液态金属流的平稳,浇注千万不能中断,防止气体卷入金属液中。
铸造气孔解决方法
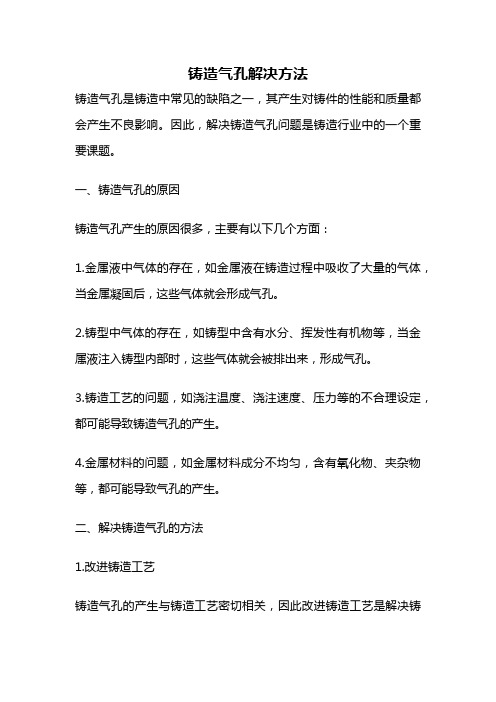
铸造气孔解决方法铸造气孔是铸造中常见的缺陷之一,其产生对铸件的性能和质量都会产生不良影响。
因此,解决铸造气孔问题是铸造行业中的一个重要课题。
一、铸造气孔的原因铸造气孔产生的原因很多,主要有以下几个方面:1.金属液中气体的存在,如金属液在铸造过程中吸收了大量的气体,当金属凝固后,这些气体就会形成气孔。
2.铸型中气体的存在,如铸型中含有水分、挥发性有机物等,当金属液注入铸型内部时,这些气体就会被排出来,形成气孔。
3.铸造工艺的问题,如浇注温度、浇注速度、压力等的不合理设定,都可能导致铸造气孔的产生。
4.金属材料的问题,如金属材料成分不均匀,含有氧化物、夹杂物等,都可能导致气孔的产生。
二、解决铸造气孔的方法1.改进铸造工艺铸造气孔的产生与铸造工艺密切相关,因此改进铸造工艺是解决铸造气孔问题的首要措施。
具体来说,可以采取以下措施:(1)提高浇注温度,减少金属液中气体的溶解度,从而减少气孔的产生。
(2)控制浇注速度和压力,使金属液充分填充铸型,减少气孔的产生。
(3)改进浇注系统,减少金属液的冲击和喷溅,从而减少气孔的产生。
2.改进金属材料金属材料的成分和质量对铸造气孔的产生也有很大的影响。
因此,改进金属材料也是解决铸造气孔问题的重要措施。
具体来说,可以采取以下措施:(1)改进金属材料的制备工艺,减少夹杂物、氧化物等的产生。
(2)优化金属材料的成分和配比,使其成分均匀,减少气孔的产生。
3.改进铸型和模具铸型和模具的质量对铸造气孔的产生也有很大的影响。
因此,改进铸型和模具也是解决铸造气孔问题的重要措施。
具体来说,可以采取以下措施:(1)优化铸型设计,使其能够充分填充金属液,减少气孔的产生。
(2)加强铸型的密封性,减少铸型中气体的存在,从而减少气孔的产生。
(3)采用高质量的模具材料,减少模具中气体的存在,从而减少气孔的产生。
4.采用热处理技术热处理技术可以改变铸件中的组织结构,从而减少气孔的产生。
具体来说,可以采用以下热处理技术:(1)固溶处理:将铸件加热到一定温度,使其中的溶质均匀分布,从而减少气孔的产生。
压铸件气孔产生的原因

压铸件气孔产生的原因产生气孔的原因有以下几点:一、氢气残留。
原材料里面还有氢气,坩埚及环境还有湿气,导致气体加热产生氢气夹裹在原材料里面,容易产生针状气孔。
二、压射室充满度不高。
压射室充满度不高会导致压射室内含空间过大,铝汤在压射前,出现回流撞击,产生涡流。
气泡是模具温度及铝温太高,容易产生气泡。
氢气,压射缸卷起,流道卷起,型腔内压力卷起,水蒸气产生气孔这些都是模具气孔的主因。
产生原因:1、金属液在压射室充满度过低(控制在45%~70%),易产生卷气,初压射速度过高。
2、模具浇注系统不合理,排气不良。
3、熔炼温度过高,含气量高,熔液未除气。
4、模具温度过高,留模时间不够,金属凝固时间不足,强度不够过早开模,受压气体膨胀起来。
5、脱模剂、注射头油用量过多。
6、喷涂后吹气时间过短,模具表面水未吹干。
解决压铸件气孔的办法:先分析出师什么原因导致的气孔,再来取相应的措施。
(1)干燥、干净的合金料。
(2)控制熔炼温度,避免过热,进行除气处理。
(3)合理选择压铸工艺参数,特别是压射速度。
调整高速切换起点。
(4)顺利填充有利于型腔气体排出,直浇道和横浇道有足够的长度(>50mm),有利于合金液平稳流动和气体有机会排出。
可改变浇口厚度、浇口方向、在形成气孔的位置设置溢流槽、排气槽。
溢流品截面积总和不能小于内浇口截面积总和的60%,否则排渣效果差。
(5)选择性能好的涂料及控制喷涂量。
预防措施:1、调整压铸工艺参数、压射速度和高压射速度的切换点。
2、修改模具浇道,增设溢流槽、排气槽。
3、降低缺陷区域模温,从而降低气体的压力作用。
4、调整熔炼工艺、5、延长留模时间,调整喷涂后吹气时间。
6、调整脱模剂、压射油用量。
气孔是压铸件中常见多发的缺陷之一。
气孔呈圆形或扁平椭圆形气泡状,直径为1mm至20mm不等,内表面光滑,覆有一层氧化层,通常分散在加工表面下。
一、气孔缺陷的成因01 金属杂质过多原材料或回收料中含有较多的氧化物和其他杂质,一些杂质(如氧化物、氢化物、油脂)在熔炼过程中会释放气体。
气孔类缺陷牲与防治方法
气孔类缺陷牲与防治方法
气孔是铸件中常见的缺陷之一,主要呈现圆形、椭圆形或不规则形。
气孔形成的原因包括模具预热温度太低,液体金属经过浇注系统时冷却太快;模具排气设计不良,气体不能通畅排出;涂料不好,本身排气性不佳,甚至本身挥发或分解出气体;模具型腔表面有孔洞、凹坑,液体金属注入后孔洞、凹坑处气体迅速膨胀压缩液体金属,形成呛孔;模具型腔表面锈蚀,且未清理干净;原材料(砂芯)存放不当,使用前未经预热;脱氧剂不佳,或用量不够或操作不当等。
防止气孔产生的方法主要包括以下几点:
1. 模具要充分预热,涂料(石墨)的粒度不宜太细,透气性要好。
2. 使用倾斜浇注方式浇注。
3. 原材料应存放在通风干燥处,使用时要预热。
4. 浇注温度不宜过高。
5. 控制金属液的含气量,熔炼金属时,要尽量减少气体元素溶入金属液中,主要取决于所用原材料,合理的熔炼操作和合适的熔炼设备。
以上信息仅供参考,如需了解更多信息,建议查阅相关书籍或咨询专业人士。
压铸件气孔的成因和解决方法2
压铸件气孔的成因和解决方法2一. 人的因素:1. 脱模剂是否噴得太多?因脱模济发气量大,用量过多时,浇注前未燃尽,使挥发气体被包在铸件表层。
所以在同一条件下,某些工人操作时会产生较多的气孔的原因之一。
选用发气量小的脱模济,用量薄而均匀,燃净后合模。
2 未经常清理溢流槽和排气道?3 开模是否过早?是否对模具进行了预热?各部位是否慢慢均匀升温,使型腔、型芯表面温度为150℃~200℃。
4 刚开始模温低时生产的产品有无隔离?5 如果无预热装置时是否使用铝合金料慢速推入型腔预热或用其它方法加热?6 是否取干净的铝液,有无将氧化层注入压室?7 倒料时,是否将勺子靠近压室注入口,避免飞溅、氧化或卷入空气降温等。
8 金属液一倒入压室,是否即进行压射,温度有无降低了?。
9 冷却与开模,是否根据不同的产品选择开模时间?10 有无因怕铝液飞出(飞水),不敢采用正常压铸压力?更不敢偿试当增加比压。
?11 操作员有无严格遵守压铸工艺?12 有无采用定量浇注?如何确定浇注量?二. 机(设备、模具、工装)的因素:主要是指模具质量、设备性能。
1 压铸模具设计是否合理,会否导致有气孔?压铸模具方面的原因:1.浇口位置的选择和导流形状是否不当,导致金属液进入型腔产生正面撞击和产生旋涡。
(降低压射速度,避免涡流包气)2.浇道形状有无设计不良?3.内浇口速度有无太高,产生湍流?4.排气是否不畅?5.模具型腔位置是否太深?6.机械加工余量是否太大?穿透了表面致密层,露出皮下气孔?压铸件的机械切削加工余量应取得小一些,一般在0.5mm左右,既可减轻铸件重量、减少切削加工量以降低成本,又可避免皮下气孔露出。
余量最好不要大于0.5mm,这样加工出来的面基本看不到气孔的,因为有硬质层的保护。
2 排气孔是否被堵死,气排不出来?3 冲头润滑剂是否太多,或被烧焦?这也是产生气体的来源之一。
4 浇口位置和导流形状,有无金属液先封闭分型面上的排溢系统?5 内浇口位置是否不合理,通过内浇口后的金属立即撞击型壁、产生涡流,气体被卷入金属流中?6 排气道位置不对,造成排气条件不良?7 溢气道面积是否够大,是否被阻塞,位置是否位於最后充填的地方?模具排气部位是否经常清理?避免因脱模剂堵塞而失去排气作用。
压铸件气孔标准
压铸件气孔标准压铸件是一种常见的金属零部件制造工艺,它具有成形快、精度高、表面光洁等优点,因此在汽车、航空航天、电子通讯等领域得到了广泛的应用。
然而,由于压铸过程中金属液体在充填模腔时易产生气体,导致压铸件表面和内部产生气孔,影响了其力学性能和外观质量。
因此,对压铸件气孔的标准进行规范是非常必要的。
首先,压铸件气孔的形成原因主要有两个方面,一是金属液体在充填模腔时受到气体的污染,导致气体溶解在金属液中;二是在金属凝固过程中,气体难以完全排出,形成气孔。
因此,要想减少压铸件气孔,就需要从源头上进行控制,保证金属液的纯净度和凝固过程中的气体排出。
其次,压铸件气孔的标准应当包括气孔的数量、大小和分布等方面。
一般来说,气孔的数量应当尽量减少,特别是在表面质量要求较高的地方,如汽车外壳、航空发动机零部件等。
气孔的大小也应当受到限制,过大的气孔会对压铸件的力学性能造成较大影响。
此外,气孔的分布应当均匀,避免出现密集的气孔区域,影响压铸件的整体质量。
再次,对于不同用途的压铸件,其气孔标准也应当有所区别。
例如,一些要求较高表面质量的压铸件,其气孔标准应当更加严格;而一些内部结构较为复杂的压铸件,其气孔标准则可以适当放宽。
这需要制定相关的行业标准和产品标准,以便满足不同压铸件的实际需求。
最后,对于压铸件气孔的检测和控制也是非常重要的。
通过X射线探伤、超声波探伤等无损检测技术,可以对压铸件的气孔进行全面的检测,及时发现问题并进行修复。
此外,在压铸工艺中,还可以通过合理的浇注系统设计、优化的浇注工艺参数等手段,减少气体的混入,从而控制压铸件气孔的产生。
综上所述,压铸件气孔标准的制定是非常重要的,它关系到压铸件的质量和性能。
通过对气孔形成原因的分析,对气孔数量、大小、分布的限制,以及对不同压铸件的不同要求,可以有效地控制压铸件气孔的产生。
同时,通过无损检测技术和优化的工艺手段,可以及时发现和修复气孔问题,保证压铸件的质量和可靠性。
压铸件气孔分析范文
压铸件气孔分析范文压铸件的气孔问题一直是制造业中的常见问题之一,它会影响到产品的质量和性能。
气孔产生的原因多种多样,例如模具设计不合理、材料问题、工艺参数设置不当等。
因此,对压铸件气孔的分析至关重要,本文将以1200字以上的篇幅,详细讨论压铸件气孔的分析。
首先,压铸件气孔的产生原因可以分为以下几个方面:1.模具设计不合理:如果模具设计的流道、浇口位置不合理,会导致金属在充填过程中出现气孔。
此外,模具中的排气系统设计不良也是一个常见问题,排气不畅会导致气体在充填过程中无法及时排出,从而产生气孔。
2.材料问题:材料中的含气量过高,或者材料中含有气孔产生的元素(如硅、锡等),都会导致压铸件中气孔的产生。
3.工艺参数设置不当:工艺参数的设置与压铸件气孔的产生密切相关。
如果充填速度过快,金属进入模腔时会带有气体,造成气孔;如果充填压力过低,金属的充填质量也会受到影响,进而影响到气孔的产生。
针对以上问题,我们可以通过以下分析方法对压铸件气孔进行分析:1.外观检查:首先,对于有气孔的压铸件,可以通过外观检查来确定气孔的分布和形态。
气孔通常呈现出圆形或椭圆形,其大小也有所不同。
通过外观检查,可以初步判断出气孔的原因。
4.化学分析:通过对压铸件中气孔进行化学分析,可以确定气孔中的气体成分。
这可以帮助我们更好地理解气孔的形成机制,并采取相应的对策。
在分析完气孔的产生原因后,我们还需要对气孔进行相应的问题修复措施。
例如,对于模具设计不合理的问题,可以对模具进行改进或优化;对于材料问题,可以选择合适的材料或改变材料的处理方式;对于工艺参数设置不当的问题,可以修改工艺参数。
此外,还可以通过改变压铸设备、优化工艺流程等手段来减少气孔的产生。
综上所述,压铸件气孔的分析是一个复杂而关键的过程,需要多种方法的配合。
通过分析气孔的产生原因,并采取相应的改进措施,可以有效地减少气孔的出现,提高压铸件的质量和性能。
- 1、下载文档前请自行甄别文档内容的完整性,平台不提供额外的编辑、内容补充、找答案等附加服务。
- 2、"仅部分预览"的文档,不可在线预览部分如存在完整性等问题,可反馈申请退款(可完整预览的文档不适用该条件!)。
- 3、如文档侵犯您的权益,请联系客服反馈,我们会尽快为您处理(人工客服工作时间:9:00-18:30)。
压铸件气孔的成因和解决办法
铝压铸是将铝液快速高压充填到模具型腔的铸造。
铝液充填压铸模型腔的时间极短,一般为百分之几秒或千分之几秒。
压铸过程中形成的气孔有光滑的表面,形状多为圆形或椭圆形,其多存在于铸件的表面或皮下针孔,也可能在铸件内部。
气孔的来源主要为压铸过程中卷入的气体或铝液析气。
一、压铸过程中卷气。
1、压铸机压铸现在基本上采取三级压射,在第一级压射时,压射冲头以较慢的速度推进(通常在0.3m/s以内),这有利于将压室中的气体挤出;第二级压射则是按压铸件的结构、壁厚选择适当的流速,内浇口速度极快(一般冲头速度为1~6m/s,薄壁件、高气密性件、镁合金件有可能达到8m/s以上的速度),将铝液把型腔基本充满。
这一级是压铸件产生气孔的关键,速度越高越易产生涡流而形成气孔。
这一过程里,控制压铸件气孔主要通过控制一、二级压射速度和一、二级切换点来实现。
一、二级速度尽量低一点(但太低会影响铸件成型或表面质量,要根据实际情况而定);二级压射的起点可选择在不允许有铸件气孔的部位之后,不同的铸件我们可选择不同的起点。
同时随着压铸机射出速度、增压建压时间、提速时间等工作性能的不断提高和完善,铸件气孔将会越来越少。
2、一套好的压铸模应具备良好的浇注系统、排溢系统。
在压铸过程中要尽量使多股浇道,铝液流与铸件方向保持一致,尽量不互相碰撞而产生涡流及因充填混乱造成卷气;另外使多股浇道充填型腔要注意做到同时填充,不能让一股或几股铝液先到最后端死角后再返回产生涡流。
压铸模上的集渣包和排气道分布要合理。
3、压铸模具的温度对铸件的质量和气孔也有着关键的影响。
当模温过高时,脱模剂在高温下挥发不能形成致密的皮膜,易造成粘膜;而模温过低,则脱模剂形成的皮膜有未挥发的水分,使脱模效果差,导致铸件气孔。
通常模具预热温度为150℃~180℃,工作保持温度为220℃~280℃。
4、涂料产生的气体
a、首先是涂料的性能:挥发点太高,发气量大对铸件气孔有直接影响。
b、从喷涂工艺上看:喷涂使用量过多,喷涂时间过长,易造成气体挥发量大,还会使模具表面温度过低,模具表面水气一时无法蒸发,合模后型腔产生大量气体。
生产过程中我们要选择性能好的涂料,挥发点要低,产生气体量要小。
5、最后由于压铸的特点是以很快的速度充填型腔,铝液在模具内快速凝固形成产品,所以铸件内部一定会有因铝液卷气产生的气孔。
但铸件表层也会因快速凝固形成细晶粒的致密层,这些细晶粒具有较高的机械性能,只要铸件的加工余量尽量小一点,铸件的物理性能也可以得到保证。
过大的加工余量就会把表面致密层加工掉,从而引起内部气孔暴露,铸件的物理性能降低。
下面举例说说我们生产的铝不粘锅的工艺:
1、产品名称:铝不粘锅,铸件轮廓尺寸为Φ250×180的圆锅,壁厚2.5mm。
2、材料:ADC12。
3、压铸机:650T。
4、产品要求:表面质量要求光滑,需在430℃高温下进行特氟隆处理,如果铸件有气孔,表面会鼓包,因此铸件不能有气孔、缩松、夹杂。
5、压铸工艺:
(1)、比压:65MP以上,高比压可使铸件组织致密度高
(2)、慢压射:0.25m/s,以防压室卷气,冲头从0逐渐加速到0.25m/s,尽量把型腔的气体排出
(3)、快压射:5m/s,防止高速太低,铸件壁薄的部位(锅的把手)附近产生流痕。
(4)、脱模剂:脱模剂不能在铸件表面上有任何残留物。
(5)、模温:220℃~280℃,考虑到铸件壁薄,模温稍高有利于成型。
(6)、铝液温度:680℃,铸件壁薄,铝液温度稍高,有利于成型。
(7)、快压射行程尽量短通过这种工艺的控制,铝不粘锅气孔率控制在2%~5%以内。
(8)、浇道的布局和方向对铸件的气孔也起着很关键的作用。
我们有一套模具,生产的铸件加工后40%有气孔,后来通过改变浇道的布局和方向,铸件加工后的气孔减少到5%以内。
二、铝液析出气体
铝液很容易吸收大气、合金锭或工具表面的湿气、也容易吸收燃烧油气中的氢元素。
铝液中的气体主要是氢,氢以原子的形式溶解于铝液中,而它大约占了气体总量的85%。
熔炼温度越高,氢在铝液中溶解的浓度就越高,但在固态铝中氢的溶解浓度非常低。
铸件在凝固时氢气会析出,使内部产生气体。
我们在熔炼回炉料时应该分批分级使用,并且把熔炼温度控制在670℃~760℃范围。
通常压铸时铝液温度控制在640℃~660℃。
实例分析:
某铸件的轮廓尺寸为320×120×80mm,铸件有一平面100×120mm,加工后的气孔率15%。
这是我们生产的一个老产品,出现这种问题肯定是生产工艺的哪个环节出了问题,首先检查:
压铸机(1)压机压力(2)冲头是否平稳推进
压铸模(1)模具分型面是否跑料
(2)平面滑块是否退让,加工余量是否过大
(3)排气、集渣包是否顺畅、完好
(4)浇道开设是否合理
其次检查:
(1)铝合金熔炼质量是否有问题,检查杂质含量
(2)熔炼温度、保温炉温度工艺参数
(3)一速、二速的速度和位置
(4)涂料喷涂时间是否过长
通过检查发现:压铸二快氮气压力偏低,模具分型面有轻微跑料,涂料喷涂时间过长,浇道开设有问题,几股浇道产生涡流,综合上述原因最终在平面形成气孔。
逐一针对性改善后,气孔率得到了有效控制,达到4%以内。
铸件气孔产生和控制气孔的办法,实际生产中还应该根据不同的铸件选定不
同的工艺参数。
如何合理的根据铸件实际情况选择工艺参数,我们还得在实际生产中依据经验判定。