数控铣齿加工切削力分析及工艺参数优化
机床加工中的切削力分析与优化

机床加工中的切削力分析与优化在机床加工过程中,切削力是一个非常重要的参数。
准确地分析和优化切削力,可以提高机床加工的效率、降低工具磨损、延长工具寿命,并减少对机床表面的损伤。
本文将重点讨论机床加工中的切削力分析与优化方法。
一、切削力的基本概念切削力是指机床在加工过程中,切削刀具对工件所产生的力。
切削力不仅取决于工件材料和机床结构,还与切削参数(如切削速度、切削深度、进给量等)密切相关。
准确地控制切削力,能够提高工件表面质量、减小残余应力,并降低加工成本。
二、切削力的分析方法1. 经验公式法经验公式法是最为常用和简便的切削力分析方法之一。
根据实验数据和经验总结,可以得到一些具有一定准确性的公式,如切削力与进给量、切削深度以及切削速度的关系。
这些公式可以为切削力的估计提供一定的依据,但精确度较低。
2. 力学模型法力学模型法是一种较为精确的切削力分析方法。
通过建立机床切削过程的力学模型,可以计算切削力的大小和方向。
常用的力学模型包括切削力平衡法、有限元法等。
力学模型法可以更加准确地分析切削力,并为进一步的优化提供依据。
三、切削力的优化方法1. 切削参数的优化切削参数的优化是降低切削力的有效方法之一。
通过合理的切削速度、切削深度和进给量的组合,可以使切削力达到最小。
一般原则是,在保证切削效率和工件表面质量的前提下,选择尽可能高的切削速度和尽可能小的切削深度和进给量。
2. 刀具和刀具材料的选择选择合适的刀具和刀具材料也可以有效减小切削力。
一般来说,刀具的刃口角度和刃口弧度越小,刀具对工件的切削力就越小。
此外,采用高硬度、高耐磨性的刀具材料,也可以降低切削力并延长刀具的使用寿命。
3. 切削润滑与冷却适当的切削润滑和冷却措施,也可以对切削力进行优化。
润滑剂的使用可以减小摩擦系数,降低切削力的大小。
同时,冷却剂的喷洒可以有效降低切削区温度,减小切削力。
四、切削力分析与优化在实际应用中的意义切削力分析与优化在机床加工中具有重要意义。
数控机床铣削切削参数的优化与调整技巧
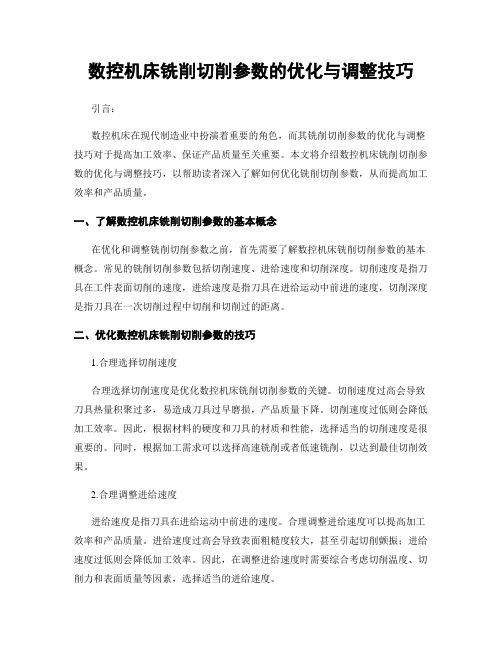
数控机床铣削切削参数的优化与调整技巧引言:数控机床在现代制造业中扮演着重要的角色,而其铣削切削参数的优化与调整技巧对于提高加工效率、保证产品质量至关重要。
本文将介绍数控机床铣削切削参数的优化与调整技巧,以帮助读者深入了解如何优化铣削切削参数,从而提高加工效率和产品质量。
一、了解数控机床铣削切削参数的基本概念在优化和调整铣削切削参数之前,首先需要了解数控机床铣削切削参数的基本概念。
常见的铣削切削参数包括切削速度、进给速度和切削深度。
切削速度是指刀具在工件表面切削的速度,进给速度是指刀具在进给运动中前进的速度,切削深度是指刀具在一次切削过程中切削和切削过的距离。
二、优化数控机床铣削切削参数的技巧1.合理选择切削速度合理选择切削速度是优化数控机床铣削切削参数的关键。
切削速度过高会导致刀具热量积聚过多,易造成刀具过早磨损,产品质量下降。
切削速度过低则会降低加工效率。
因此,根据材料的硬度和刀具的材质和性能,选择适当的切削速度是很重要的。
同时,根据加工需求可以选择高速铣削或者低速铣削,以达到最佳切削效果。
2.合理调整进给速度进给速度是指刀具在进给运动中前进的速度。
合理调整进给速度可以提高加工效率和产品质量。
进给速度过高会导致表面粗糙度较大,甚至引起切削颤振;进给速度过低则会降低加工效率。
因此,在调整进给速度时需要综合考虑切削温度、切削力和表面质量等因素,选择适当的进给速度。
3.合理确定切削深度切削深度是指刀具在一次切削过程中切削过的距离。
合理确定切削深度可以提高加工效率和产品质量。
切削深度过大会增加切削力和切削温度,降低切削稳定性,造成切削颤振,甚至导致刀具断裂;切削深度过小则会降低加工效率。
因此,在确定切削深度时需要综合考虑刀具性能、切削稳定性和加工需求等因素,选择合适的切削深度。
三、常见问题及解决方案1.切削温度过高切削温度过高会导致刀具早期磨损和产品质量下降。
解决方案包括选择适当的切削速度和进给速度,适当降低切削深度和刀具进给量,使用冷却液进行冷却等。
数控加工中的切削力分析与优化

数控加工中的切削力分析与优化数控加工作为现代制造业中的重要工艺之一,广泛应用于各个领域。
而在数控加工过程中,切削力的分析与优化是提高加工质量和效率的关键。
本文将从数控加工的背景、切削力的分析与优化方法以及未来发展趋势等方面进行探讨。
1. 数控加工的背景数控加工是指通过计算机控制机床进行加工的一种方法。
相比传统的手工操作或者传统数控加工,数控加工具有高精度、高效率、高稳定性等优势。
在数控加工中,切削力是影响加工质量和机床寿命的重要参数。
2. 切削力的分析方法切削力的分析是指对切削过程中产生的力进行定量分析和计算。
常见的分析方法包括实验测量和仿真模拟两种。
2.1 实验测量实验测量是通过在实际加工过程中采集数据来分析切削力。
这种方法的优点是直观、准确,能够获得真实的切削力数据。
但是,实验测量需要耗费大量的时间和资源,并且对于复杂的加工过程,很难获得全面的切削力信息。
2.2 仿真模拟仿真模拟是通过建立数学模型,利用计算机软件模拟切削过程,从而得到切削力的分布和变化规律。
这种方法的优点是快速、经济,并且能够提供全面的切削力信息。
但是,仿真模拟需要依赖于准确的切削力模型,对模型的建立和参数的确定有一定的要求。
3. 切削力的优化方法切削力的优化是指通过调整加工参数或者改变切削工具等方式来减小切削力,提高加工效率和质量。
常见的优化方法包括切削参数优化、切削工具优化和切削策略优化等。
3.1 切削参数优化切削参数优化是指通过合理调整切削速度、进给速度、切削深度等参数来减小切削力。
在优化过程中,需要综合考虑加工质量、加工效率、刀具寿命等因素,并通过实验或者仿真模拟来确定最佳的切削参数组合。
3.2 切削工具优化切削工具是影响切削力的重要因素之一。
通过选择合适的切削工具材料、刀具形状和刀具涂层等方式,可以减小切削力。
切削工具优化需要综合考虑切削力、切削温度、刀具寿命等因素,并通过实验或者仿真模拟来评估切削工具的性能。
3.3 切削策略优化切削策略是指在加工过程中选择合适的切削路径和切削方式。
数控木工铣床的数控系统参数调整和优化方法

数控木工铣床的数控系统参数调整和优化方法数控木工铣床是一种先进的木工加工设备,具有高精度、高效率和灵活性好的特点。
而数控系统是数控木工铣床的核心部件,其参数的调整和优化对于提高加工质量和效率至关重要。
本文将介绍数控木工铣床的数控系统参数调整和优化方法,帮助您更好地利用数控系统来实现木工加工的优化。
首先,我们需要了解数控系统的参数调整和优化的基本原则。
数控系统的参数调整是指根据加工要求和机械特性,对系统的相关参数进行调整,以达到最佳的加工效果。
而数控系统的优化则是针对整个加工过程进行全面分析和调整,以提高加工精度、加工速度和加工质量。
下面,我们将具体介绍数控木工铣床的数控系统参数调整和优化方法:1. 自动调整刀具补偿值刀具补偿值是指在加工过程中,为了弥补刀具的磨损、热胀冷缩等因素对加工精度的影响,通过调整补偿值来实现加工尺寸的控制。
因此,自动调整刀具补偿值是数控木工铣床参数调整和优化的重要一步。
可以通过加工试件测量和修正的方式,根据实际加工尺寸和理论加工尺寸之间的差异,自动调整刀具补偿值,以提高加工精度和稳定性。
2. 优化进给速度和切削速度进给速度和切削速度是数控木工铣床加工中的两个重要参数,对加工效率和加工质量有着直接的影响。
通过对进给速度和切削速度的调整和优化,可以提高加工速度和加工质量。
在进行参数调整时,需要根据加工材料的硬度、刀具的特性和加工要求来选择合适的进给速度和切削速度,以实现最佳的加工效果。
3. 调整切割参数和工作台参数数控木工铣床的切割参数包括切削深度、进给量和切削速度等。
切削深度的调整应根据加工材料的硬度、加工质量要求和刀具的特性来确定。
进给量则需要根据加工要求和机械特性来进行调整,以提高加工效率和加工质量。
此外,还需要注意调整工作台参数,如工作台的速度和位置,以满足不同加工要求,并保证加工的稳定性和精度。
4. 优化程序设计和加工路径数控木工铣床的数控系统还包括程序设计和加工路径的优化。
数控机床铣削切削参数的优化方法

数控机床铣削切削参数的优化方法数控机床是现代制造业中不可或缺的重要设备,而铣削是数控机床的一项常见加工工艺。
优化数控机床铣削切削参数,可以提高加工效率、降低生产成本,并且保证零件的质量。
本文将介绍数控机床铣削切削参数的优化方法。
首先,在选取数控机床铣削切削参数时,需要考虑工件材料的性质以及加工要求。
工件材料的硬度、韧性和切削性是影响切削参数选择的关键因素。
硬度高的材料需要选用较低的切削速度和切削深度,以减小切削力和切削温度,保证刀具寿命和工件表面质量。
韧性较高的材料则需要较大的切削速度和切削深度,以提高切削效率。
此外,加工要求也是选择切削参数的重要参考,比如加工精度要求高的零件需要选用较小的进给速度和进给量。
其次,合理选择刀具和切削液也是数控机床铣削切削参数优化的关键。
刀具的几何形状、材料和涂层会直接影响到切削力、表面粗糙度和加工效率。
在选择刀具时,应根据加工材料的不同选用合适的刀具材料和涂层,比如硬质合金刀具适用于铸铁和普通钢的铣削,而涂层刀具则适合高硬度材料的加工。
切削液的选择也十分重要,它可以降低切削温度、减小切削力、延长刀具寿命和提高表面质量。
常用的切削液有水溶性切削液和油基切削液,选择时需根据材料和加工要求综合考虑。
此外,切削力的控制也是数控机床铣削切削参数优化的重要环节。
切削力的大小直接关系到刀具的寿命和加工精度。
过大的切削力会导致刀具的磨损加剧,降低加工质量,甚至损坏刀具。
因此,在选取切削参数时,应尽量控制切削力的大小。
切削力与切削速度、进给速度和切削深度有关,一般来说,切削速度和进给速度越小,切削力也会相应减小。
同时,还可以采用刀具径向远离刀尖的切削方式,以减小切削力,提高切削稳定性。
此外,根据实际加工情况,需要通过试切试验来确定最佳的切削参数组合。
试切试验是通过不断调整切削速度、进给速度和切削深度,观察工件表面粗糙度、刀具磨损情况和加工前后尺寸误差的变化,从而找到最佳的切削参数组合。
数控机床切削参数的选择与优化
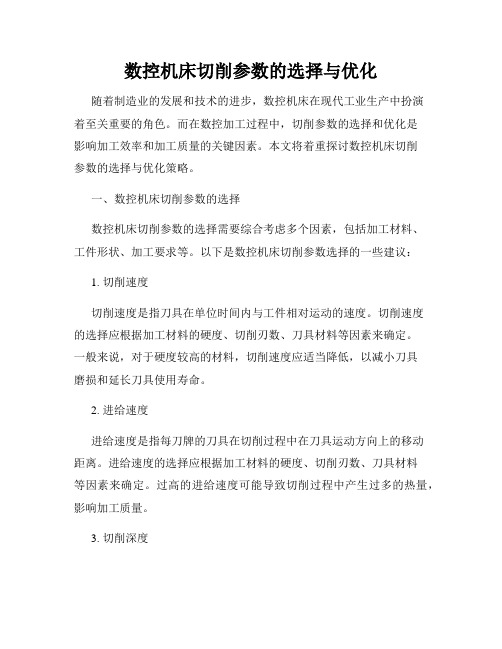
数控机床切削参数的选择与优化随着制造业的发展和技术的进步,数控机床在现代工业生产中扮演着至关重要的角色。
而在数控加工过程中,切削参数的选择和优化是影响加工效率和加工质量的关键因素。
本文将着重探讨数控机床切削参数的选择与优化策略。
一、数控机床切削参数的选择数控机床切削参数的选择需要综合考虑多个因素,包括加工材料、工件形状、加工要求等。
以下是数控机床切削参数选择的一些建议:1. 切削速度切削速度是指刀具在单位时间内与工件相对运动的速度。
切削速度的选择应根据加工材料的硬度、切削刃数、刀具材料等因素来确定。
一般来说,对于硬度较高的材料,切削速度应适当降低,以减小刀具磨损和延长刀具使用寿命。
2. 进给速度进给速度是指每刀牌的刀具在切削过程中在刀具运动方向上的移动距离。
进给速度的选择应根据加工材料的硬度、切削刃数、刀具材料等因素来确定。
过高的进给速度可能导致切削过程中产生过多的热量,影响加工质量。
3. 切削深度切削深度是指刀具在切削过程中与工件接触的最大深度。
切削深度的选择应考虑加工材料的硬度、切削刃数、刀具材料等因素。
较小的切削深度可以减小切削力和切削温度,提高加工精度。
4. 切削方式切削方式包括铣削、车削、钻削等。
选择合适的切削方式可以提高加工效率和加工质量。
对于不同形状的工件,应选择适合的切削方式,以确保切削过程的稳定和切削力的均匀分布。
二、数控机床切削参数的优化除了选择合适的切削参数外,优化切削参数也能提高加工效率和加工质量。
以下是一些常用的数控机床切削参数优化策略:1. 刀具润滑刀具润滑是切削过程中的重要环节,它能减小切削力和摩擦,并提高刀具的使用寿命。
选择合适的切削液类型和使用方法有助于减少切削过程中的热量积累和切削力的产生。
2. 切削力监测与控制通过切削力的监测和控制,可以实时了解加工过程中的切削负荷情况,从而优化切削参数的选择。
采用合适的传感器和控制系统,能够更好地预测和调节切削过程中的切削力,提高加工效率和加工质量。
数控机床铣削切削参数的动态调整与最优化方法

数控机床铣削切削参数的动态调整与最优化方法摘要:数控机床在现代制造中起着重要的作用,而铣削是其常用的加工方式之一。
铣削切削参数对加工效果有重要影响,因此动态调整和最优化切削参数成为提高铣削加工效率和质量的关键。
本文将针对数控机床铣削切削参数的动态调整与最优化方法进行探讨,并提出一种可行的方案。
关键词:数控机床、铣削、切削参数、动态调整、最优化方法引言:数控机床的出现极大地提高了制造业的生产效率和加工质量。
在数控机床的加工过程中,铣削是一种经常使用的加工方式,因此铣削切削参数的调整和优化对于提高加工效率和质量至关重要。
本文将探讨数控机床铣削切削参数的动态调整与最优化方法,并提出一种可行的方案。
一、动态调整切削参数的必要性与挑战动态调整铣削切削参数对于实现高效率、高质量的加工具有重要意义。
传统的切削参数调整方法往往是经验性的,存在着固定的参数设置,难以针对不同的加工情况进行优化。
而现代制造中常遇到的零件形状复杂、加工精度要求高等问题使得切削参数的优化变得更为复杂。
因此,动态调整切削参数的方法迫在眉睫。
二、动态调整切削参数的方法(一)实时监测与反馈控制:通过现代传感器技术,实时监测铣削过程中的关键参数,如切削力、切削温度等。
根据监测到的参数,利用反馈控制方法实现切削参数的动态调整。
例如,当切削力过大时,可以自动降低进给速度来达到稳定切削的目的。
这种方法可以实现对切削参数的实时调整,提高加工质量和稳定性。
(二)数学模型的建立与仿真:通过对铣削过程进行数学建模,可以通过计算机仿真的方法探究不同切削参数对加工效果的影响。
通过对不同切削参数进行仿真分析,找出最佳参数组合,优化铣削加工过程中的产品质量和加工效率。
(三)人工智能算法的应用:近年来,人工智能算法在加工制造领域得到了广泛的应用。
利用人工智能算法,可以通过大量数据的学习和训练,快速找到最佳的切削参数组合。
例如,可以通过遗传算法、模糊逻辑控制等方法自动调整切削参数,在保证加工质量的前提下提高加工效率。
数控机床铣床的切削力计算与优化

数控机床铣床的切削力计算与优化数控机床铣床是现代制造业中不可或缺的重要设备之一。
在加工过程中,切削力是一个重要的参数,它直接影响着加工的质量和效率。
因此,对数控机床铣床的切削力进行准确计算与优化是提高加工效率和质量的关键。
首先,计算数控机床铣床的切削力是进行优化的前提。
切削力的计算可以基于理论和实验两种方法。
理论计算方法主要是基于数学模型和力学原理,通过建立切削力模型和选择适当的切削力系数来计算切削力。
实验方法则是通过在实际加工中测量切削力来进行计算。
常用的实验方法包括力传感器和动态切削力测量系统。
理论计算方法能够提供更准确的切削力数据,但需要准确的刀具和工件材料参数;实验方法则能够直接测量切削力,但需要实际加工过程中的测量设备。
其次,优化数控机床铣床的切削力是提高加工效率和质量的关键一步。
根据切削力的计算结果,可以对数控机床铣床进行优化,以减小切削力、降低能耗,提高加工质量。
优化切削力的方法包括以下几个方面。
首先,选择合适的刀具和刀具参数。
刀具的材料、刃数、刃口角和刃尖圆角等参数会影响切削力的大小。
选择适当的刀具和刀具参数,能够减小切削力,并提高切削效率。
其次,优化切削参数。
切削参数包括进给速度、主轴转速、切削深度和切削宽度等。
合理选择切削参数,可以减小切削力和切削温度,提高加工效率和质量。
第三,采用适当的切削液。
切削液在切削过程中起到冷却、润滑和除屑的作用。
选择适当的切削液可以降低切削温度,减小切削力,并延长刀具的使用寿命。
最后,进行工艺优化。
合理设计工艺流程,减少刀具在切削过程中的停滞时间和闲置时间,优化切削路径和切削次序,可以有效减小切削力、降低切削温度,并提高加工效率和精度。
总之,数控机床铣床的切削力计算与优化是提高加工效率和质量的关键。
通过准确计算切削力,并通过合理选择刀具和刀具参数、优化切削参数、选择适当的切削液以及进行工艺优化等方法,可以有效减小切削力、降低切削温度,并提高加工效率和质量。
- 1、下载文档前请自行甄别文档内容的完整性,平台不提供额外的编辑、内容补充、找答案等附加服务。
- 2、"仅部分预览"的文档,不可在线预览部分如存在完整性等问题,可反馈申请退款(可完整预览的文档不适用该条件!)。
- 3、如文档侵犯您的权益,请联系客服反馈,我们会尽快为您处理(人工客服工作时间:9:00-18:30)。
数控铣齿加工切削力分析及工艺参数优化
摘要:高速铣削加工要求切削速度快,加工效率高。
对成型铣齿加工过程及铣削力进行理论分析,建立以最高工作效率为评价标准的目标函数,以进给速度和主轴转速为切削参数的优化模型,利用matlab软件编写程序求得优化结果。
关键词:成型铣齿加工参数铣削力优化
高速铣削加工是近几十年来广泛应用与发展的一种先进制造技术。
在实际生产过程中,对于高速铣齿加工用传统的方法难以确定最合理的切削用量。
为了获得机床最大的工作效率对铣削力性质进行分析,结合实验与主要切削参数优化研究获取最优切削参数组合。
1、切削力模型分析
高速成形铣削加工的加工过程为粗加工,所以对表面质量要求不高。
机床工作时,刀盘对准齿廓位置由上至下进给加工齿廓,每完成一次走刀即完成一个齿廓的加工。
2、铣削参量的分析
通过实验数据分析找出切削参量对机床受力的影响,引用文献[2]实验所获得的数据利用statistica软件对各参数与切削力关系分析。
(如表1图1图2)
由图(1)可知铣削力随着z轴进给量的增大呈增大趋势,但是随主轴转速的增加而减少。
由图(2)可知z轴进给量对铣削力的影响要比主轴转速对铣削力的影响大。
在进行参数优化时,应尽量避免切
削力过大,主轴转速的升高会减小切削力,但是随着主轴转速的增加机床的振动也随着增加,因此在不使机床产生过大振动前提下应该尽量使用较大的主轴转速。
机床主轴额定转速范围为87.16rpm,根据对图1和2的分析,确定机床主轴转速范围[75,87],z轴进给量范围为[70,130],刀盘切削力控制在12000n以下。
3、优化模型的数学模型
在激烈的市场竞争中,产品更新速度很快,对于一个企业而言,以最少时间作为切削用量优化标准更具实用价值。
完成一道铣削工序的加工工时,++
式中—单件工序的切削时间,为刀具走过总路线l与进给量的比值即;
—换刀一次所消耗的时间;—除换刀时间外的其他辅助时间;—换刀次数;
4、数学模型的约束条件
4.1 确定切削参量的约束
数控铣齿加工关键参数包括主轴转速,和进给速度,对于进给速度又有每转进给量(mm/r),每齿进给量(mm/z)。
4.2 机床的约束
(1)机床实际功率必须小于机床的最大功率,约束可表示为。
(2)实际扭矩不能超过主轴的最大扭矩约束表示为:。
4.3 铣刀刀片耐用度的约束
过大的磨损会使刀具使用寿命过短从而增加了加工成本,利用度
约束为。
式中—刀具耐用度系数;—刀具耐用度指数。
5、优化模型的求解
5.1 机床参数
机床型号为skxc2000数控调整铣齿机床;加工材料为50mn;材料硬度为200hb;加工工作齿厚为90mm;工件齿数z为110;铣刀模数;铣刀直径;铣刀总齿数z=36;机床的额定功率为30kw。
5.2 优化结果的分析
应用matlab所得优化结果为:主轴转速为85.15rpm;z轴进给量为122.04mm/min。
优化后的主轴转速将近机床的额定转速,说明主轴转速对于铣削效率的影响较大,因此在工件加工时主轴转速采用优化值,对于材料硬度大的工件减小进给量即可。
6、结语
通过对铣齿加工过程和铣刀实际受力情况分析选取铣削力的计算公式。
根据实验分析确定主要切削参数对铣削力的影响,获得对主轴转速,进给量及铣削力的约束。
在保证机床的功率满足刀具耐用度的基础上,以最大加工效率为目标建立数学数学模型。
参考文献
[1]胡家国,杨志刚,李迎.高速铣削铝合金切削力研究[j].工具技术,2003,37(11):33-36.
[2]席平原.应用matlab工具箱实现机械优化设计[j].机械设计与研究,2003,19(3):40-42.
个人简介
刘芳(1984-),女,助理讲师。
从事机械相关教学与研究工作。