机械加工工艺规程设计(PPT 50页)
合集下载
机械加工工艺规程设计教材

第二十三页,共50页。
粗基准的选择(xuǎnzé)原则
3. 对于(duìyú)所有表面都要加工的表面,选取余量和公差最小的表面作 粗基准,以避免余量不足而造成废品。
第二十四页,共50页。
粗基准的选择(xuǎnzé)原则
4.选取光洁、平整、面积大的表面作粗基准; 5.粗基准不应重复使用。一般(yībān)情况下,粗基准只允许使用一次。
➢ 几何关系:视图完整、正确,表达清楚无歧义,几何元素的 关系应明确,避免在图纸上可能出现加工轮廓的数据不充分、 尺寸模糊不清及尺寸封闭干涉等缺陷。
第二页,共50页。
零件(línɡ jiàn)加工工 艺性分析
➢ 精度与技术要求:包括尺寸精度、形位公差和表面粗糙度。 在满足使用要求的前提下若能降低精度要求,则可降低加工 难度,减少加工次数(cìshù),提高生产率,降低成本。
第二十五页,共50页。
精基准的选择(xuǎnzé)原则
对于形位公差精度要求较高的零件,应采用已加工 过的表面作为定位基准。这种定位基准面叫做精基准。 精基准的选择原则(yuánzé): 1. 基准重合原则(yuánzé):选用定位基准与设计基准重 合
的原则(yuánzé)
第二十六页,共50页。
精基准(jīzhǔn)的选择原则
零件(línɡ jiàn) 工零艺件结性构包形括状:的合理性、几何(jǐ hé)图素关系的确定性、精度及
技术要求的可实现性、工件材料的可切削性能等
➢ 结构形状:在满足使用要求的前提下加工的可行性和经济性。 尽量避免悬臂、窄槽、内腔尖角以及刚性不稳的薄壁、细长杆 之类的结构,减少或避免采用成型刀具加工的结构,孔系、内 转角半径等尽量按标准刀具尺寸统一以减少换刀次数,深腔处 窄槽和转角尺寸要充分考虑刀具的刚性等等。
粗基准的选择(xuǎnzé)原则
3. 对于(duìyú)所有表面都要加工的表面,选取余量和公差最小的表面作 粗基准,以避免余量不足而造成废品。
第二十四页,共50页。
粗基准的选择(xuǎnzé)原则
4.选取光洁、平整、面积大的表面作粗基准; 5.粗基准不应重复使用。一般(yībān)情况下,粗基准只允许使用一次。
➢ 几何关系:视图完整、正确,表达清楚无歧义,几何元素的 关系应明确,避免在图纸上可能出现加工轮廓的数据不充分、 尺寸模糊不清及尺寸封闭干涉等缺陷。
第二页,共50页。
零件(línɡ jiàn)加工工 艺性分析
➢ 精度与技术要求:包括尺寸精度、形位公差和表面粗糙度。 在满足使用要求的前提下若能降低精度要求,则可降低加工 难度,减少加工次数(cìshù),提高生产率,降低成本。
第二十五页,共50页。
精基准的选择(xuǎnzé)原则
对于形位公差精度要求较高的零件,应采用已加工 过的表面作为定位基准。这种定位基准面叫做精基准。 精基准的选择原则(yuánzé): 1. 基准重合原则(yuánzé):选用定位基准与设计基准重 合
的原则(yuánzé)
第二十六页,共50页。
精基准(jīzhǔn)的选择原则
零件(línɡ jiàn) 工零艺件结性构包形括状:的合理性、几何(jǐ hé)图素关系的确定性、精度及
技术要求的可实现性、工件材料的可切削性能等
➢ 结构形状:在满足使用要求的前提下加工的可行性和经济性。 尽量避免悬臂、窄槽、内腔尖角以及刚性不稳的薄壁、细长杆 之类的结构,减少或避免采用成型刀具加工的结构,孔系、内 转角半径等尽量按标准刀具尺寸统一以减少换刀次数,深腔处 窄槽和转角尺寸要充分考虑刀具的刚性等等。
机械加工工艺规程的制订 PPT课件
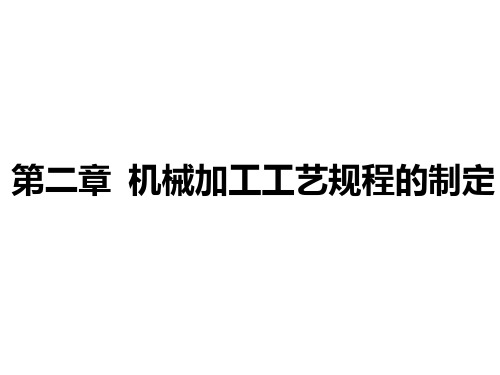
15
二、机械加工工艺过程的组成
5. 工位
例:
工件 机床夹具回转部分 夹具固定部分
分度机构
图7–3 在三个工位上钻、铰圆盘零件上的孔
16
三、生产纲领与生产类型
1. 生产纲领
生产纲领是指企业在计划期内应当生产的产品产量。 零件在计划期一年中的生产纲领N可按下式计算:
NQ(1 na% 1 )b% ( )
7
二、机械加工工艺过程的组成
1. 工序 一个或一组工人在一个工作地(机
械设备)对同一个或同时对几个工件所 连续完成的那一部分工艺过程,称为工 序。
8
图7–1 阶梯轴
讨论:
生产规模 不同,工序 的划分不一 样。
例:
表7-1 单件小批生产的工艺过程
工序号
工序内容
设备
1
车一端面,钻中心孔*;
车床I
调头,车另一端面,钻中心孔
表7-2 大批大量生产的工艺过程
工序内容
设备
铣两端面,钻两端中心孔* 铣端面钻中
一次 心孔机床
车大外圆及倒角
一次 车床 I
车小外圆、切槽及倒角 一次 车床II
铣键槽
一次 专用铣床
去毛刺
钳工台
二、机械加工工艺过程的组成
3. 工步 工步是指在加工表面和加工工具不
变的情况下,所连续完成的那一部分工 序内容。
21
2.生产类型
生产类型
单件生产
成批生 产
小批 中批
大批
大量生产
零件的年产量(件)
重型零件
中型零件
<5
<10
轻型零件 <100
5~100
10~200
100~500
二、机械加工工艺过程的组成
5. 工位
例:
工件 机床夹具回转部分 夹具固定部分
分度机构
图7–3 在三个工位上钻、铰圆盘零件上的孔
16
三、生产纲领与生产类型
1. 生产纲领
生产纲领是指企业在计划期内应当生产的产品产量。 零件在计划期一年中的生产纲领N可按下式计算:
NQ(1 na% 1 )b% ( )
7
二、机械加工工艺过程的组成
1. 工序 一个或一组工人在一个工作地(机
械设备)对同一个或同时对几个工件所 连续完成的那一部分工艺过程,称为工 序。
8
图7–1 阶梯轴
讨论:
生产规模 不同,工序 的划分不一 样。
例:
表7-1 单件小批生产的工艺过程
工序号
工序内容
设备
1
车一端面,钻中心孔*;
车床I
调头,车另一端面,钻中心孔
表7-2 大批大量生产的工艺过程
工序内容
设备
铣两端面,钻两端中心孔* 铣端面钻中
一次 心孔机床
车大外圆及倒角
一次 车床 I
车小外圆、切槽及倒角 一次 车床II
铣键槽
一次 专用铣床
去毛刺
钳工台
二、机械加工工艺过程的组成
3. 工步 工步是指在加工表面和加工工具不
变的情况下,所连续完成的那一部分工 序内容。
21
2.生产类型
生产类型
单件生产
成批生 产
小批 中批
大批
大量生产
零件的年产量(件)
重型零件
中型零件
<5
<10
轻型零件 <100
5~100
10~200
100~500
机械加工工艺规程制定培训课件(共42张PPT)

近净成形技术是指零件成形后,仅需少量加工或不再加工,就可用作机械构件的成形技术。是建立在新材料、新 能源、机电一体化、精密模具技术、计算机技术、自动化技术、数值分析和模拟技术等多学科技术成果根底上,改 造了传统的毛坯成形技术,使之由粗糙成形变为优质、高效、高精度、轻量化、低本钱的成形技术。成形后的机械 构件具有精确的外形、高的尺寸精度、几何精度和好的外表粗糙度。技术包括:近净形铸造成形、精确塑性成形、 精确连接、精密热处理改性、外表改性、高精度模具等专业领域,并且是新工艺、新装备、新材料以及各项新技术 成果的综合集成技术。
(3)机床的生产率应与被加工零件的生产类型相适应。
(4)机床的选择应适应工厂现有的设备条件。
,那么应提出设计任务书,说明与加 工工序内容有关的参数、生产率要求,保证零件质量的条件以及机床 总体布置形式等。
2022/11/27
培训专用
33
2. 工艺装备的选择
选择工艺装备,即确定各工序所用的刀具、夹具、量具和 辅助工具等。
工艺过程设计中,工序的组织遵循两种原 那么:
工序的集中:每个工序的内容和工步都尽可能 多 ,总工序数目减少,夹具的数目和工件的安 装次数都减少。
工序的分散:
2022/11/27
培训专用
15
工序分散的特点
〔1〕 所使用的机床设备和工艺装备都比较简单,容易调整, 生产工人也便于掌握操作技术;
〔2〕有利于选用最合理的切削用量,减少机开工时;
但这些技术要求不一定就是零件图所规定的要 求。有时可能由于工艺上的原因而在某些方面 高于零件图上的要求:
如因基准不重合而提高对某基准外表的加工 要求;或由于被作为精基准而可能对其提出更 高的加工要求(工序基准〕。
2022/11/27
精选工艺规程设计教材PPT99页

重点考虑:加工表面与不加工表面的 相对位置精度;各加工表面有足够的余量
2. 为保证某重要表面余量均匀,则选择该重要表面本身作为粗基准。(图7-12)
(举例)
图7-10 用不需加工的外圆作粗基准
图7-11 用需加工的内孔作粗基准
图7-12 车床床身加工
3. 若每个表面都加工,则以余量最小的表面作为粗基准, 以保证各表面都有足够的余量。(图7-13)
3.成批生产
产品品种基本固定,但数量少,品种较多,需要周期性地轮换生产,大多数工作地点的加工对象是周期性的变换。
计算节拍的公式: t=60Φ/N (3-2) 式中 t——节拍,单位为min/件; Φ——机床每年工作时数,单位为h; N——零件生产纲领,单位为件。 Φ=cmnη 式中 c——每天班次(以2计算); m——每年周数(以51计算); n——每周一班工作时数(以35计算); η——设备利用率,一般取0.94~0.96。
三、节 拍
节拍是指生产每一个零件所规定的时间指标。
1. 工艺规程是指导生产的主要技术文件
2. 工艺规程是组织生产和管理工作的基本依据
3. 工艺规程是新建或扩建工厂或车间的基本资料
四、机械加工工艺规程
机械加工工艺规程简称为工艺规程,是指导机械加工的主要技术文件。
图7-18
图7-19
图7-20
图7-18 以齿形表面定位加工 1-卡盘;2-滚柱;3-齿轮
图7-19 自为基准磨削定子外圆
图7-20 床身导轨面自为基准
二、粗基准选择
1. 选择不加工表面作为粗基准,若有几个不加工表面,选其中与加工表面位置精度要求高的一个,以保证两者的位置精度。
定义——零件结构的工艺性是指所设计的零件在满足要求的前题下,制造的可行性和经济性。功能相同的零件,其结构工艺性可以有很大差异。良好的结构工艺性是指在现有工艺条件下既能方便制造,又有较低的制造成本。零件结构工艺性的分析,包括零件尺寸和公差的标注、零件的组成要素和整体结构等方面的分析。
2. 为保证某重要表面余量均匀,则选择该重要表面本身作为粗基准。(图7-12)
(举例)
图7-10 用不需加工的外圆作粗基准
图7-11 用需加工的内孔作粗基准
图7-12 车床床身加工
3. 若每个表面都加工,则以余量最小的表面作为粗基准, 以保证各表面都有足够的余量。(图7-13)
3.成批生产
产品品种基本固定,但数量少,品种较多,需要周期性地轮换生产,大多数工作地点的加工对象是周期性的变换。
计算节拍的公式: t=60Φ/N (3-2) 式中 t——节拍,单位为min/件; Φ——机床每年工作时数,单位为h; N——零件生产纲领,单位为件。 Φ=cmnη 式中 c——每天班次(以2计算); m——每年周数(以51计算); n——每周一班工作时数(以35计算); η——设备利用率,一般取0.94~0.96。
三、节 拍
节拍是指生产每一个零件所规定的时间指标。
1. 工艺规程是指导生产的主要技术文件
2. 工艺规程是组织生产和管理工作的基本依据
3. 工艺规程是新建或扩建工厂或车间的基本资料
四、机械加工工艺规程
机械加工工艺规程简称为工艺规程,是指导机械加工的主要技术文件。
图7-18
图7-19
图7-20
图7-18 以齿形表面定位加工 1-卡盘;2-滚柱;3-齿轮
图7-19 自为基准磨削定子外圆
图7-20 床身导轨面自为基准
二、粗基准选择
1. 选择不加工表面作为粗基准,若有几个不加工表面,选其中与加工表面位置精度要求高的一个,以保证两者的位置精度。
定义——零件结构的工艺性是指所设计的零件在满足要求的前题下,制造的可行性和经济性。功能相同的零件,其结构工艺性可以有很大差异。良好的结构工艺性是指在现有工艺条件下既能方便制造,又有较低的制造成本。零件结构工艺性的分析,包括零件尺寸和公差的标注、零件的组成要素和整体结构等方面的分析。
机械制造工艺-机械加工工艺规程PPT课件
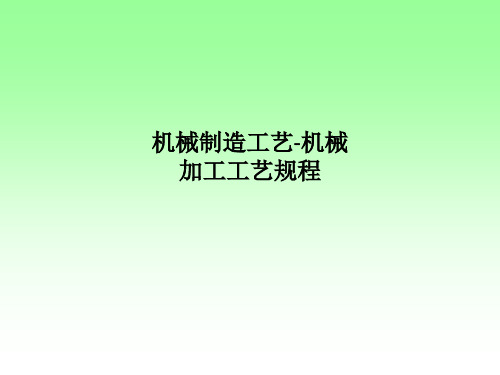
例:连杆的加工。
六、加工阶段的划分 (粗、精加工分开的原则)
1.粗加工——切除大部分余量,以提高生产率为主要 目的。
2.半精加工——完成次要表面加工,为主要表面精加 工做准备。
3.精加工——保证各主要表面的精度和粗糙度。 4.光整加工,超精加工——获得更高的精度和更好 的表面粗糙度。
合理划分加工阶段有利于: 1.减小切削变形的影响。 2.避免浪费工时。 3.合理使用设备、人员。 4.便于热处理工序安排。
大型箱体零件要保证各孔余量均匀,可采取 立体画线方法找正。
保证各加工表面余量充足。
例:阶梯轴,φ100、φ50(毛坯φ108、φ55), 轴线偏心量3mm,应先加工φ100。 (3)便于装夹。 (4)只使用一次(不得重复使用)。
2.精基准选择 (1)基准重合(即定位基准与设计基准重合) 不产生基准不重合误差,定位精度高。 (2)统一基准(各工序定位基准相同) 各工序夹具统一,安装方式统一,易于保证各 表面之间位置精度 例:轴的统一基准:两端中心孔 齿轮的统一基准:内孔 箱体的统一基准:一面两销。(表1-11)中的 箱体顶面和两销孔。
(3)淬火、渗碳等——各表面加工之后主要表面磨削 之前。 (4)表面处理——工艺过程最后。 3.其它工序的安排 (1)检验工序
每道工序之后——自检(首件送检),阶段检验和 终检。
①粗加工之后,精加工之前; ②转到其它车间或工段前后 ③关键工序前后 ④终检 (2)其它:去毛刺、平衡、去磁、清洗等。
五、工序的集中与分散(例如:p8表1-2,表1-3) 两个不同的原则
(3)互为基准 基准→加工面; (加工面)→(基准)。 用于相互位置要求很高的表面,例:主轴的加
工:支承轴径前莫氏锥孔,后锥孔 (4)自为基准 以加工表面本身为基准。 例:床身导轨面的精(刨)工序,加工前用
六、加工阶段的划分 (粗、精加工分开的原则)
1.粗加工——切除大部分余量,以提高生产率为主要 目的。
2.半精加工——完成次要表面加工,为主要表面精加 工做准备。
3.精加工——保证各主要表面的精度和粗糙度。 4.光整加工,超精加工——获得更高的精度和更好 的表面粗糙度。
合理划分加工阶段有利于: 1.减小切削变形的影响。 2.避免浪费工时。 3.合理使用设备、人员。 4.便于热处理工序安排。
大型箱体零件要保证各孔余量均匀,可采取 立体画线方法找正。
保证各加工表面余量充足。
例:阶梯轴,φ100、φ50(毛坯φ108、φ55), 轴线偏心量3mm,应先加工φ100。 (3)便于装夹。 (4)只使用一次(不得重复使用)。
2.精基准选择 (1)基准重合(即定位基准与设计基准重合) 不产生基准不重合误差,定位精度高。 (2)统一基准(各工序定位基准相同) 各工序夹具统一,安装方式统一,易于保证各 表面之间位置精度 例:轴的统一基准:两端中心孔 齿轮的统一基准:内孔 箱体的统一基准:一面两销。(表1-11)中的 箱体顶面和两销孔。
(3)淬火、渗碳等——各表面加工之后主要表面磨削 之前。 (4)表面处理——工艺过程最后。 3.其它工序的安排 (1)检验工序
每道工序之后——自检(首件送检),阶段检验和 终检。
①粗加工之后,精加工之前; ②转到其它车间或工段前后 ③关键工序前后 ④终检 (2)其它:去毛刺、平衡、去磁、清洗等。
五、工序的集中与分散(例如:p8表1-2,表1-3) 两个不同的原则
(3)互为基准 基准→加工面; (加工面)→(基准)。 用于相互位置要求很高的表面,例:主轴的加
工:支承轴径前莫氏锥孔,后锥孔 (4)自为基准 以加工表面本身为基准。 例:床身导轨面的精(刨)工序,加工前用
机械加工工艺规程PPT课件

2021
图7-10 轴套圆跳动检验
27
(d) 装配基准 在机器装配中,用于确定零件或部件在机器中
正确位置的基准。
如图所示轴套,其孔
以一定的配合精度安装在
轴上决定其径向位置,并
以端面A紧贴轴肩决定其轴
向位置,轴套孔的轴线和
2021
端面A即为装配基准。
图7-11 轴套的装配基准
28
二、工件在夹具中的定位
N
x
Aa
③保证加工尺寸C±δc,
需限制工件的
→
Y
y
Bb
M
2021
为保证全部加工要求,该工件定位时, 应限制它所有的六个自由度。
31
如何限制工件的自由度?
z
→↷ X、Z
B
→
Y
C
x
O
2021
y
X↷、Y↷、→Z
A
32
如何限制工件的自由度?
z
4
y
6 5
1 3
2
在夹具中,
限制工件的自由
x
度可用定位支承 点来实现,一个
2
产品设计
总体设计 零部件设计
决定功能 选择材料
决定结构与尺寸
制定技术条件 绘出样图
工 艺准备
决定生产方案 制定工艺规程
及工艺卡 设计并制造
工艺装备
毛坯制造
铸件 锻件 冲压件 焊接件 棒料
非金属材料
毛坯
机械加工 装配调试
粗加工 半精加工
精加工 热处理 表面处理
组件装配 部件装配
总装配
调试 涂
外购件
图7-7按划线找正装夹
21
3).专用夹具安装 利用专用夹具上的定位夹紧元件能使工件迅速
机械加工工艺ppt课件
薄壁套夹紧变形
38
◆ 重力影响 【例】龙门铣横梁
解决:变形补偿
龙门铣横梁变形
龙门铣横梁变形补偿
39
40
◆ 传动力与惯性力影响
➢ 理论上不会产生 圆度误差(但会产 生圆柱度误差) ➢周期性的力易会 引起强迫振动
z
l a)
Fcd
φ Fcd
R Fc yFcd Fp y r
Y
O″ Fp rcd=Fcd / kc
Fc Fc / kc
29
2、工艺系统受力变形对加工精度的影响 (1)切削力作用点位置变化引起工件形状误差 B′
A′
yx
ytj ywz
Δx
A FA
x
C
B
C′
FB
Fp
L
工艺系统变形随受力点变化规律
30
工件刚度小-------腰鼓形 工件刚度大-------马鞍形
31
(2)误差复映规律
切削加工中,由于 毛坯本身的误差(形状 或位置)使切削深度不 断变化,从而引起切削 力的变化,促使工艺系 统产生相应的变形,因 而工件表面上保留了与 毛坯表面类似的形状和 位置误差,但加工后残 留的误差比毛坯误差从 数值上大大减少了,这 一现象称为“误差复映”
16
8)提高主轴回转精度的措施 ➢提高主轴部件的制造精度
首先应提高轴承的回转精度.其次是提高箱体支承孔、 主轴轴颈和与轴承相配合有关表而的加工精度。此外,还 可在装配时先测出滚动轴承及主轴锥孔的径向圆跳动,然 后调节径向圆跳动的方位,使误差相互补偿或抵消,以减 少轴承误差对主轴回转精度的影响。 ➢对滚动轴承进行预紧,消除间隙
③与轴承配合的零件误差的影响 由于轴承内、外圈或轴瓦很薄,受力后容易变形,因此
第二章 机械加工工艺规程的设计
在一个工步中,若被加工表面需切去的金属层很厚, 要分几次切削,每进行一次切削就是一次走刀或工作行程。
图 1-4 以棒料制造阶梯轴的工作行程
注意: 1)构成工步的任一因素改变后,均视为另一工步 2)在工件一次安装中,连续进行若干相同工步,
为简化工艺文件,可视为一个复合工步。 3)采用多刀加工均视为一个复合工步。
X
√
X√
应尽量减少使用刀具的种类
X√
X√
减少加工的安装次数
镗孔
(2)零件结构应便于度量 锥孔两端最好留有圆柱面 花键齿采用偶数
(3)零件结构应有足够的刚度
对该轴类零件进行工艺审查:
生产类型为中批量。 毛坯为锻件, 材料为40Cr, 零件需作调质处理, 硬度HB240-280
多轴肩
粗糙度太低 缺退刀槽
(2)最终热处理 最终热处理安排在半精加工以后和磨削加工之前 (但有氮化处理时,应安排在精磨之后),主要用于提 高材料的强度和硬度。 调质处理:初加工或半精加工以后,使钢材获得一 定的强度、硬度及良好的冲击韧性等; 淬火、渗碳淬火:半精加工以后,提高表面硬度; 氮化、氰化:精加工之后,提高表面的耐磨性、耐 疲劳性、耐蚀性及耐高温性。
一、机械加工工艺规程的作用
1、是生产准备工作的依据 2、是组织生产的指导性文件 3、是新建和扩建工厂(或车间)时的原始资料 4、便于积累、交流和推广行之有效的生产经验
二、 机械加工工艺规程的制订程序
(一)机械加工工艺规程的设计原则
1、确保加工质量,达到产品图样所提出的技术条件。 2、提高生产率,按期完成并力争超额完成生产任务。 3、减少人力和物力的消耗,降低生产成本。 4、降低工人的劳动强度,提供安全良好的工作条件。
所谓经济精度及表面粗糙度是指在正常加工条件 下某一加工方法所能保证的加工精度及表面粗糙度。
图 1-4 以棒料制造阶梯轴的工作行程
注意: 1)构成工步的任一因素改变后,均视为另一工步 2)在工件一次安装中,连续进行若干相同工步,
为简化工艺文件,可视为一个复合工步。 3)采用多刀加工均视为一个复合工步。
X
√
X√
应尽量减少使用刀具的种类
X√
X√
减少加工的安装次数
镗孔
(2)零件结构应便于度量 锥孔两端最好留有圆柱面 花键齿采用偶数
(3)零件结构应有足够的刚度
对该轴类零件进行工艺审查:
生产类型为中批量。 毛坯为锻件, 材料为40Cr, 零件需作调质处理, 硬度HB240-280
多轴肩
粗糙度太低 缺退刀槽
(2)最终热处理 最终热处理安排在半精加工以后和磨削加工之前 (但有氮化处理时,应安排在精磨之后),主要用于提 高材料的强度和硬度。 调质处理:初加工或半精加工以后,使钢材获得一 定的强度、硬度及良好的冲击韧性等; 淬火、渗碳淬火:半精加工以后,提高表面硬度; 氮化、氰化:精加工之后,提高表面的耐磨性、耐 疲劳性、耐蚀性及耐高温性。
一、机械加工工艺规程的作用
1、是生产准备工作的依据 2、是组织生产的指导性文件 3、是新建和扩建工厂(或车间)时的原始资料 4、便于积累、交流和推广行之有效的生产经验
二、 机械加工工艺规程的制订程序
(一)机械加工工艺规程的设计原则
1、确保加工质量,达到产品图样所提出的技术条件。 2、提高生产率,按期完成并力争超额完成生产任务。 3、减少人力和物力的消耗,降低生产成本。 4、降低工人的劳动强度,提供安全良好的工作条件。
所谓经济精度及表面粗糙度是指在正常加工条件 下某一加工方法所能保证的加工精度及表面粗糙度。
- 1、下载文档前请自行甄别文档内容的完整性,平台不提供额外的编辑、内容补充、找答案等附加服务。
- 2、"仅部分预览"的文档,不可在线预览部分如存在完整性等问题,可反馈申请退款(可完整预览的文档不适用该条件!)。
- 3、如文档侵犯您的权益,请联系客服反馈,我们会尽快为您处理(人工客服工作时间:9:00-18:30)。
(3)不便装夹的零件应加设装夹余料,工艺凸台、凸耳, 最后去除。
工艺路线的拟定
经济精度:在正常加工条件下所能达到的加工精度及表面粗糙度
各种表面不同加工方法的经济精度及表面粗糙度
加工 表面
加工 方法
外圆柱面 和端面
粗车 半精车 精车 粗磨 精磨 研磨 超精加工 金刚车
平面
粗刨(铣) 精刨(铣) 粗磨
零件加工工艺性分析
➢ 精度与技术要求:包括尺寸精度、形位公差和表面粗糙度。 在满足使用要求的前提下若能降低精度要求,则可降低加工 难度,减少加工次数,提高生产率,降低成本。
尺寸标注应便于编程且尽可能利于设计基准、工艺基准的统一。
➢ 工件材质:零件毛坯材料及热处理要求,是选择刀具(材料、 几何参数及使用寿命),确定加工工序、切削用量及选择机 床的重要依据。
➢ 结构形状:在满足使用要求的前提下加工的可行性和经济性。 尽量避免悬臂、窄槽、内腔尖角以及刚性不稳的薄壁、细长 杆之类的结构,减少或避免采用成型刀具加工的结构,孔系、 内转角半径等尽量按标准刀具尺寸统一以减少换刀次数,深 腔处窄槽和转角尺寸要充分考虑刀具的刚性等等。
➢ 几何关系:视图完整、正确,表达清楚无歧义,几何元素的 关系应明确,避免在图纸上可能出现加工轮廓的数据不充分、 尺寸模糊不清及尺寸封闭干涉等缺陷。
锻件
机械性能较好,有较高的强度和冲击韧性,但毛坯的形状不 宜复杂,如轴类和齿轮类零件的毛坯常用锻件。
型材 焊接件 工程塑料
包括圆形、方形、六角形及其它断面形状的棒料、管料及板料。 棒料常用在普通车床、六角车床及自动和半自动车床上加工轴类、 盘类及套类等中小型零件。冷拉棒料比热轧棒料精度高且机械性 能好,但直径较小。板料常用冷冲压的方法制成零件,但毛坯的 厚度不宜过大。
定位基准的选择
在机械加工中,无论采用哪种安装方法,都必 须使工件在机床或夹具上正确地定位
六点定位:任何一个未被约束的物体,在空间 有六个自由度。而要使物体在空间有确定的位 置,必须约束这六个自由度
六点定位原理
六点定位原理 一个自由的物体,它对三个相互垂直的坐标系来说,有六个活动可能性, 其中三种是移动,三种是转动。习惯上把这种活动的可能性称为自由度, 因此空间任一自由物体共有六个自由度。如图所示,物体的六个自由 度。欲使工件在空间取得唯一位置,则必须限制六个自由度。这就是六点 定位原理。
装配基准 工序基准
后用来测量工件 时采用的基准
在装配时用来确定零
在工序图上使用的基准。
件或部件在产品中相 对位置所采用的基准
定位基准选择
定位基准
1、粗基准 2、精基准
最初工序中采用毛坯 上未经加工的表面作 为定位基准。
在其后各工序中采用 经过加工的表面 作为定位基准。
工件的装夹
装夹 = 定位 + 夹紧
在满足零件功能的前提下,尽量使用廉价的国产材料,不选贵重紧缺材料。
确定毛坯的种类
与零件的结构形状、尺寸大小、材料的机械性能和零件的生
产类型及毛坯车间的具体生产条件有关。
铸件
包括铸钢、铸铁、有色金属及合金的铸件等。铸件毛坯的 形状可以相当复杂,尺寸可以相当大,且吸振性能较好,但铸
件的机械性能较低,一般壳体零件的毛坯多用铸件。
0.16~1.25 0.16~1.25 0.006~0.1
选择表面加工方法
首先应了解各种加工方法所能达到的经济精度,然后考虑:
1)零件的材料及性质。有色金属的精加工不宜采用磨削,因为有色金
属易使砂轮堵塞,因此常采用高速精细车削或金刚镗等切削加工方法
2)零件的形状与尺寸。形状复杂、尺寸较大的零件,其上的孔一般不
宜采用拉削或磨削;直径大于Φ60mm的孔不宜采用钻、扩、铰等
3)选择的加工方法要与生产类型相适应 。大批量生产应选用高生
产率的和质量稳定的加工方法,而单件、小批生产应尽量选择通用设备 和避免采用非标准的专用刀具来加工。
4)具体的生产条件 。考虑工厂现有的加工设备及其工艺能力、工人的
技术水平,以充分利用现有设备和工艺手段,同时也要注意不断引进新 技术,对老设备进行技术改造,挖掘企业的潜力,不断提高工艺水平
基准及其分类
基准及其分类
基准
用于确定零件上 其它点、线、面 位置所依据的那 些点、线、面。
设计图样上所采 用的基准就是设 计基准。
在加工时用于工件 定位的基准,称为
定位基准。
设计基准 工艺基准
定位基准 测量基准
1、粗基准 2、精基准 3、辅助基准 4、主要基准 5、附加基准
ቤተ መጻሕፍቲ ባይዱ在加工中或加工
加工、测量、 装配过程中使 用的基准。
对尺寸较大、形状较复杂的毛坯,可采用型钢或锻件焊 接成毛坯,但焊接件吸振性能差,容易变形,尺寸误差 大。
它是近年来在机械制造业中普遍推广的一种毛坯,其形
状可以很复杂,尺寸精度高,但机械性能差。
毛坯选择
毛坯种类选择 1)零件的材料及对零件力学性能的要求。铸铁→铸件,高强度
→锻件,一般性能→型材或铸钢
加工 表面
圆柱 孔
平面
加工 方法
钻孔 粗镗 半精镗 精镗、铰 粗磨 精磨 珩磨 研磨
精磨 刮研 研磨
经济精度 等级IT
11~12 11~12 8~9 7~8 7~8 6~7 6~7 5~6
6~7 6~7 5
表面粗 糙度
μm
12.5~25 6.3~12.5 1.6~3.2 0.8~1.6 0.2~0.8 0.1~0.2 0.025~0.1 0.025~0.1
经济精度 等级IT
11~13 9~10 7~8 8~9 6 5 5~6 6
11~13 8~10 8~9
表面粗 糙度
μm
12.5~50 3.2~6.3 0.8~1.6 0.4~0.8 0.1~0.4 0.012~0.1 0.012~0.1 0.025~0.4
12.5~50 1.6~6.3 1.25~5
机械加工工艺规程设计
工艺规程设计的步骤 1)分析零件工艺性。 2)选择毛坯。 3)选择定位基准。 4)拟定工艺路线。 5)确定各工序的设备、刀具、量具和夹具等。 6)确定各工序的切削用量。 7)填写工艺文件。
零件加工工艺性分析
零件工艺性包括: 零件结构形状的合理性、几何图素关系的确定性、精度及技 术要求的可实现性、工件材料的可切削性能等
2)零件的结构形状与外形尺寸。轴→锻件或型材,大件→铸件 3)生产类型和生产条件。小批→砂型铸或自由锻,大批→模锻、
精密铸,减少粗加工量,提高效率
4)充分考虑利用新工艺、新技术和新材料。 毛坯形状和尺寸选择: (1)铸锻件毛坯余量应足够大。铸件有夹渣、疏松,锻件有黑
皮、飞边和凹凸不平。
(2)小、薄或组合件可考虑按多件连体备料,加工完成后 再割开。
工艺路线的拟定
经济精度:在正常加工条件下所能达到的加工精度及表面粗糙度
各种表面不同加工方法的经济精度及表面粗糙度
加工 表面
加工 方法
外圆柱面 和端面
粗车 半精车 精车 粗磨 精磨 研磨 超精加工 金刚车
平面
粗刨(铣) 精刨(铣) 粗磨
零件加工工艺性分析
➢ 精度与技术要求:包括尺寸精度、形位公差和表面粗糙度。 在满足使用要求的前提下若能降低精度要求,则可降低加工 难度,减少加工次数,提高生产率,降低成本。
尺寸标注应便于编程且尽可能利于设计基准、工艺基准的统一。
➢ 工件材质:零件毛坯材料及热处理要求,是选择刀具(材料、 几何参数及使用寿命),确定加工工序、切削用量及选择机 床的重要依据。
➢ 结构形状:在满足使用要求的前提下加工的可行性和经济性。 尽量避免悬臂、窄槽、内腔尖角以及刚性不稳的薄壁、细长 杆之类的结构,减少或避免采用成型刀具加工的结构,孔系、 内转角半径等尽量按标准刀具尺寸统一以减少换刀次数,深 腔处窄槽和转角尺寸要充分考虑刀具的刚性等等。
➢ 几何关系:视图完整、正确,表达清楚无歧义,几何元素的 关系应明确,避免在图纸上可能出现加工轮廓的数据不充分、 尺寸模糊不清及尺寸封闭干涉等缺陷。
锻件
机械性能较好,有较高的强度和冲击韧性,但毛坯的形状不 宜复杂,如轴类和齿轮类零件的毛坯常用锻件。
型材 焊接件 工程塑料
包括圆形、方形、六角形及其它断面形状的棒料、管料及板料。 棒料常用在普通车床、六角车床及自动和半自动车床上加工轴类、 盘类及套类等中小型零件。冷拉棒料比热轧棒料精度高且机械性 能好,但直径较小。板料常用冷冲压的方法制成零件,但毛坯的 厚度不宜过大。
定位基准的选择
在机械加工中,无论采用哪种安装方法,都必 须使工件在机床或夹具上正确地定位
六点定位:任何一个未被约束的物体,在空间 有六个自由度。而要使物体在空间有确定的位 置,必须约束这六个自由度
六点定位原理
六点定位原理 一个自由的物体,它对三个相互垂直的坐标系来说,有六个活动可能性, 其中三种是移动,三种是转动。习惯上把这种活动的可能性称为自由度, 因此空间任一自由物体共有六个自由度。如图所示,物体的六个自由 度。欲使工件在空间取得唯一位置,则必须限制六个自由度。这就是六点 定位原理。
装配基准 工序基准
后用来测量工件 时采用的基准
在装配时用来确定零
在工序图上使用的基准。
件或部件在产品中相 对位置所采用的基准
定位基准选择
定位基准
1、粗基准 2、精基准
最初工序中采用毛坯 上未经加工的表面作 为定位基准。
在其后各工序中采用 经过加工的表面 作为定位基准。
工件的装夹
装夹 = 定位 + 夹紧
在满足零件功能的前提下,尽量使用廉价的国产材料,不选贵重紧缺材料。
确定毛坯的种类
与零件的结构形状、尺寸大小、材料的机械性能和零件的生
产类型及毛坯车间的具体生产条件有关。
铸件
包括铸钢、铸铁、有色金属及合金的铸件等。铸件毛坯的 形状可以相当复杂,尺寸可以相当大,且吸振性能较好,但铸
件的机械性能较低,一般壳体零件的毛坯多用铸件。
0.16~1.25 0.16~1.25 0.006~0.1
选择表面加工方法
首先应了解各种加工方法所能达到的经济精度,然后考虑:
1)零件的材料及性质。有色金属的精加工不宜采用磨削,因为有色金
属易使砂轮堵塞,因此常采用高速精细车削或金刚镗等切削加工方法
2)零件的形状与尺寸。形状复杂、尺寸较大的零件,其上的孔一般不
宜采用拉削或磨削;直径大于Φ60mm的孔不宜采用钻、扩、铰等
3)选择的加工方法要与生产类型相适应 。大批量生产应选用高生
产率的和质量稳定的加工方法,而单件、小批生产应尽量选择通用设备 和避免采用非标准的专用刀具来加工。
4)具体的生产条件 。考虑工厂现有的加工设备及其工艺能力、工人的
技术水平,以充分利用现有设备和工艺手段,同时也要注意不断引进新 技术,对老设备进行技术改造,挖掘企业的潜力,不断提高工艺水平
基准及其分类
基准及其分类
基准
用于确定零件上 其它点、线、面 位置所依据的那 些点、线、面。
设计图样上所采 用的基准就是设 计基准。
在加工时用于工件 定位的基准,称为
定位基准。
设计基准 工艺基准
定位基准 测量基准
1、粗基准 2、精基准 3、辅助基准 4、主要基准 5、附加基准
ቤተ መጻሕፍቲ ባይዱ在加工中或加工
加工、测量、 装配过程中使 用的基准。
对尺寸较大、形状较复杂的毛坯,可采用型钢或锻件焊 接成毛坯,但焊接件吸振性能差,容易变形,尺寸误差 大。
它是近年来在机械制造业中普遍推广的一种毛坯,其形
状可以很复杂,尺寸精度高,但机械性能差。
毛坯选择
毛坯种类选择 1)零件的材料及对零件力学性能的要求。铸铁→铸件,高强度
→锻件,一般性能→型材或铸钢
加工 表面
圆柱 孔
平面
加工 方法
钻孔 粗镗 半精镗 精镗、铰 粗磨 精磨 珩磨 研磨
精磨 刮研 研磨
经济精度 等级IT
11~12 11~12 8~9 7~8 7~8 6~7 6~7 5~6
6~7 6~7 5
表面粗 糙度
μm
12.5~25 6.3~12.5 1.6~3.2 0.8~1.6 0.2~0.8 0.1~0.2 0.025~0.1 0.025~0.1
经济精度 等级IT
11~13 9~10 7~8 8~9 6 5 5~6 6
11~13 8~10 8~9
表面粗 糙度
μm
12.5~50 3.2~6.3 0.8~1.6 0.4~0.8 0.1~0.4 0.012~0.1 0.012~0.1 0.025~0.4
12.5~50 1.6~6.3 1.25~5
机械加工工艺规程设计
工艺规程设计的步骤 1)分析零件工艺性。 2)选择毛坯。 3)选择定位基准。 4)拟定工艺路线。 5)确定各工序的设备、刀具、量具和夹具等。 6)确定各工序的切削用量。 7)填写工艺文件。
零件加工工艺性分析
零件工艺性包括: 零件结构形状的合理性、几何图素关系的确定性、精度及技 术要求的可实现性、工件材料的可切削性能等
2)零件的结构形状与外形尺寸。轴→锻件或型材,大件→铸件 3)生产类型和生产条件。小批→砂型铸或自由锻,大批→模锻、
精密铸,减少粗加工量,提高效率
4)充分考虑利用新工艺、新技术和新材料。 毛坯形状和尺寸选择: (1)铸锻件毛坯余量应足够大。铸件有夹渣、疏松,锻件有黑
皮、飞边和凹凸不平。
(2)小、薄或组合件可考虑按多件连体备料,加工完成后 再割开。