机械加工工艺规程制定(完整版)
机械加工工艺规程制定[完整版]
![机械加工工艺规程制定[完整版]](https://img.taocdn.com/s3/m/b5fb273e7e21af45b207a817.png)
5、定位夹紧可靠方便
图床身导轨面自为基准
课题三 拟定工艺路线
拟定工艺路线,是制订工艺规程时的一项很重要的工 作。工艺路线拟定的是否合理,直接影响到工艺规程的合理 性科学性和经济性。
一、加工方法的选择
1. 所选择的加工方法能否达到零件精度的要求。
2. 零件材料的可加工性能如何。 3. 生产率对加工方法有无特殊要求。
二、工序尺寸与公差的确定
工序尺寸是零件在加工 过程中各工序应保证的加工 尺寸,通常为加工面至定位 基准面之间的尺寸。
1. 无需进行尺寸换算时工序尺寸的确定
2. 需进行尺寸换算时工序尺寸的确定
无需进行尺寸换算时工序尺寸的确定
• 确定加工工序的加工余量; • 从设计尺寸开始,确定工序基本尺寸; • 确定工序尺寸公差; • 按入体原则标注工序尺寸公差。
封闭环:
4、增、减环判别方法
举例:
增环
在尺寸链图中用首尾相接的单向 箭头顺序表示各尺寸环,其中与 封闭环箭头方向相反者为增环, 与封闭环箭头方向相同者为减环。
A1 A0 A2
A3
封闭环
减环
二、尺寸链的分类
1.按不同生产过程来分 (1) 工艺尺寸链:在零件加工工序中,由有关工序尺寸、设
计尺寸或加工余量等所组成的尺寸链。 (2) 装配尺寸链:在机器设计成装配中,由机器或部件内若
L3 L∑ L4 L1
(2) 平面尺寸链: 尺寸键全部尺
A5 A6
寸位于一个或几个平行平面内。 A4
A3
AΣ
A6
A2 A1
A7
AΣ
A5
A4
(3) 空间尺寸链: 尺寸链全部尺
A1
A2 A3
寸位干几个不平行的平面内。
机械加工工艺规程编制
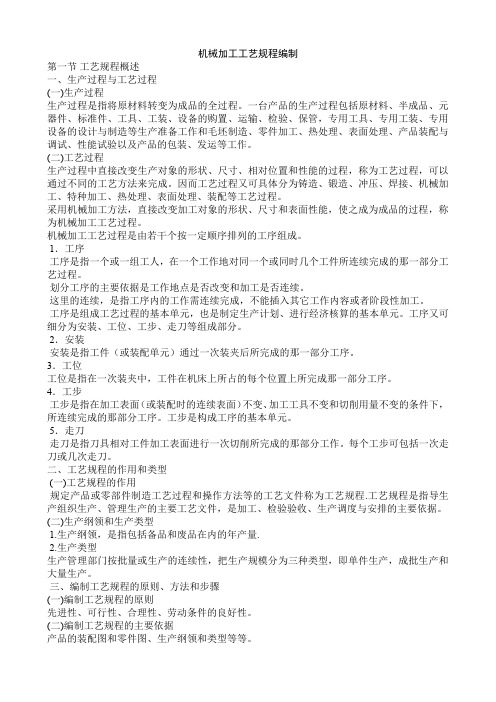
机械加工工艺规程编制第一节工艺规程概述一、生产过程与工艺过程(一)生产过程生产过程是指将原材料转变为成品的全过程。
一台产品的生产过程包括原材料、半成品、元器件、标准件、工具、工装、设备的购置、运输、检验、保管,专用工具、专用工装、专用设备的设计与制造等生产准备工作和毛坯制造、零件加工、热处理、表面处理、产品装配与调试、性能试验以及产品的包装、发运等工作。
(二)工艺过程生产过程中直接改变生产对象的形状、尺寸、相对位置和性能的过程,称为工艺过程,可以通过不同的工艺方法来完成。
因而工艺过程又可具体分为铸造、锻造、冲压、焊接、机械加工、特种加工、热处理、表面处理、装配等工艺过程。
采用机械加工方法,直接改变加工对象的形状、尺寸和表面性能,使之成为成品的过程,称为机械加工工艺过程。
机械加工工艺过程是由若干个按一定顺序排列的工序组成。
1.工序工序是指一个或一组工人,在一个工作地对同一个或同时几个工件所连续完成的那一部分工艺过程。
划分工序的主要依据是工作地点是否改变和加工是否连续。
这里的连续,是指工序内的工作需连续完成,不能插入其它工作内容或者阶段性加工。
工序是组成工艺过程的基本单元,也是制定生产计划、进行经济核算的基本单元。
工序又可细分为安装、工位、工步、走刀等组成部分。
2.安装安装是指工件(或装配单元)通过一次装夹后所完成的那一部分工序。
3.工位工位是指在一次装夹中,工件在机床上所占的每个位置上所完成那一部分工序。
4.工步工步是指在加工表面(或装配时的连续表面)不变、加工工具不变和切削用量不变的条件下,所连续完成的那部分工序。
工步是构成工序的基本单元。
5.走刀走刀是指刀具相对工件加工表面进行一次切削所完成的那部分工作。
每个工步可包括一次走刀或几次走刀。
二、工艺规程的作用和类型(一)工艺规程的作用规定产品或零部件制造工艺过程和操作方法等的工艺文件称为工艺规程.工艺规程是指导生产组织生产、管理生产的主要工艺文件,是加工、检验验收、生产调度与安排的主要依据。
(机械制造行业)第三章机械加工工艺规程的制定

第三章机械加工工艺规程的制定§3-1基本概念一.生产过程与工艺过程(一)生产过程从原材料到机械产品出厂的全部劳动过程。
包括:1)生产技术准备过程2)毛坯的制造3)零件的机械加工及热处理4)产品的装配、检验、试车、油漆、包装等。
5)产品的辅助劳动过程直接生产过程被加工对象的尺寸、形状或性能、位置产生一定的变化。
如:零件的机械加工、热处理、装配等。
间接生产过程:不使加工对象产生直接变化。
如:工装夹具的制造、工件的运输、设备的维护等。
(二)机械加工工艺过程是生产过程的一部分,是对零件采用各种加工方法,直接用于改变毛坯的形状、尺寸、表面粗糙度以及力学物理性能,使之成为合格零件的全部劳动过程。
工艺:使各种原材料、半成品成为成品的方法和过程工艺过程:在生产过程中,凡是改变生产对象的形状、尺寸、相对位置和性质等,使其成为成品和半成品的过程。
二.机械加工工艺过程的组成1.工序一个或一组工人,在一台机床或一个工作地点对一个或同时对几个工件所连续完成的那一部分工艺过程。
划分工序的主要依据:工作地点是否改变和加工是否连续完成。
同一零件,同样的加工内容可以有不同的工序安排。
如图所示的阶梯轴的加工:加工内容:1.加工小端面 2.小端面钻中心孔3.加工大端面 4.大端面钻中心孔5.车大端外圆 6.对大端倒角7.车小端外圆8.对小端倒角9.精车外圆10.铣键槽11.去毛刺工序1:加工内容1到9——车床工序2:加工内容10、11——铣床(手工去毛刺)工序1:加工内容1、2、7、8—加工小端工序2:加工内容3、4、5、6—加工大端工序3:加工内容9工序4:加工内容10、11 第三种工序安排:工序1:加工内容:1、2、3、4—铣两端面打中心孔工序2:加工内容:5、6、7、8—仿形车外圆、倒角工序3:加工内容:9—精车外圆工序4:加工内容:1—铣键槽工序5:加工内容:11—去毛刺2、安装如果在一个工序中要对工件进行几次装夹,则每次装夹下完成的那部分加工内容称为一个安装。
机械制造工艺学第四章 机械加工工艺规程设计
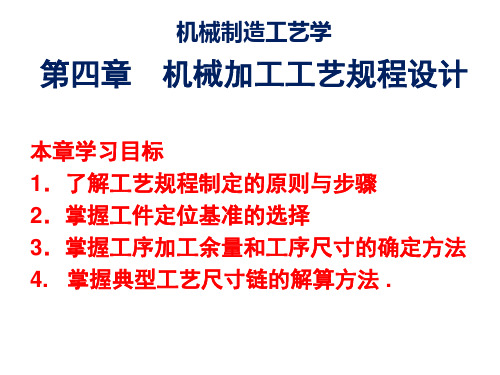
(3)应尽量减小加工面积 支座底面设计为中凹可减少加工量,提高支撑精度和稳定性。
三、要考虑生产类型与加工方法
箱体零件: 单件小批时(a),其同轴孔的直径应设计成单向递减的,以便 在镗床上通过一次安装就能逐步加工出各孔。 大批生产时(b),为提高生产率,一般用双面联动组合机床加 工,这时应采用双向递减的孔径设计,用左、右两镗杆各镗两 端孔,以缩短加工工时。
床身导轨面自为基准
(4)互为基准原则
对工件上的两个相互位置精度要求很高的表面,互相作为 定位基准,反复进行加工。
优点: 可使两个加工表面间获得高的位置精度。 如:内外圆面同轴度要求比较高的套类零件的加工安排
第二节 机械加工工艺路线的制订
一、定位基准的选择
2、粗基准的选择原则 (1)保证位置精度原则
0.16-0.01
加工方法 钻 扩
铰 拉
镗
孔的加工方法
加工性质
加工经济精度(IT)
实心材料
12-11
粗扩
12
精扩
10
半精铰
11-10
精铰
9-8
细铰
7-6
粗拉
10-9
精拉
9-7
粗镗
12
半精镗
11
精镗
10-8
细镗
7-6
表面粗糙度Ra
20-2.5 20-10 10-2.5 10-5 5-1.25 1.25-0.32 5-2.5 2.5-0.63 20-10 10-5 5-1.25 1.25-0.32
加工方法
外圆加工的方法
加工性质
加工经济精度(IT) 表面粗糙度Ra(um)
车 外磨 研磨 超精加工
粗车 半精车
精车 金刚石车
机械加工工艺规程的制定

工艺过程组成
工艺过程组成
2)安装
工件加工前,使其在机床或夹具中相对刀具占 据正确位置并给予固定的过程,称为装夹。(装夹 包括定位和夹紧两过程)
安装是指工件通过一次装夹后所完成的那一部 分工序。
1、生产纲领: 指包括备品、备件在内的该产品 的年产量。产品的年生产纲领就是产品的年生产量。 零件的年生产纲领由下式计算
N=Qn(1+a)(1+b)
式中:
N:零件的生产纲领(件/年); Q:产品的年产量(台/年); n:单台产品该零件的数量(件/年); a:备品率,以百分数计; b:废品率,以百分数计。
第五章 机械加工工艺规程设计
本章主要介绍以下内容: 5.1 零件制造的工艺过程 5.2 工艺规程的作用及设计步骤 5.3 零件工艺性分析与毛坯的选择 5.4 定位基准的选择 5.5 工艺路线的拟定 5.6 加工余量的确定 5.7 尺寸链和工序尺寸的确定 5.8 时间定额和经济分析
重点、难点:定位基准的选择;尺寸链和工序尺寸 的确定
定义:全年中重复制造同一产品。 特点:产品品 种少、产量大,长期重复进行同一产品的加工。
5.2 各种生产类型工艺过程的主要特点
工艺过程特点 工件的互换性
单件生产
一般是配对制造,没有互换 性,广泛用钳工修配
毛坯的制造方 法及加工余量
铸件用木模手工造型;锻件 用自由锻。毛坯精度低,加 工余量大
生产类型
5)走刀
走刀(又称工作行程)是指刀具相对工件加工 表面进行一次切削所完成的那部分工作。每个工步 可包括一次走刀或几次走刀。
机械加工工艺规程的制订

机械加工工艺规程的制订1.工艺规程的作用①工艺规程是指导生产的主要技术条件;②工艺规程是生产组织和生产管理工作的依据;③工艺规程是新建或扩建工厂及车间的基本资料。
2.工艺规程的设计原则①技术上的先进性②经济上的合理性③良好的劳动条件3.制订工艺规程所需的原始资料①产品的全套装配图和零件工作图②产品验收的质量标准③产品的生产纲领④毛坯资料⑤现场生产条件⑥工艺规程设计时应尽可能多了解新工艺、新方法4.工艺规程的制订步骤4.1零件的工艺分析1)零件技术要求分析①加工表面的尺寸精度②主要加工表面的形状精度③主要表面之间的相互位置精度④各加工表面粗糙度以及表面质量方面的其它要求⑤热处理及其它技术要求2)对零件图具体技术分析:①零件的视图、尺寸、公差和技术要求是否齐全②零件图所规定加工要求是否合理③零件的选材是否恰当3)零件结构工艺性分析①机械零件的结构,由于使用要求不同而具有各种形状②在分析零件的结构时,不仅要注意各物体表面本身特征,而且要注意这些表面的不同组合③在研究零件结构时,要注意审查零件的结构工艺性4.2选择毛坯类型1)毛坯种类的选择:由材料的力学性能要求,零件结构形状的尺寸大小,零件的生产纲领以及利用新技术,新工艺的可能性决定。
2)确定毛坯的形状和尺寸,确定毛坯形状和尺寸时应注意以下几个问题:①为使加工时工件安装稳定,有些铸件毛坯,需要铸出工艺凸台②为了保证零件加工质量和加工方便,常将一些零件作成一个整体毛坯,加工到一定形状后再切割分离。
4.3选择定位基准按照基准的选择原则,必须选择好各道工序的定位基准。
4.4工艺路线的拟定要解决的主要问题:零件各表面的加工方法和方案的选择,加工阶段的划分,确定工序的分散与集中,加工顺序安排和热处理安排等。
1)加工方法和加工方案的选择选择表面加工方案时,应注意以下几个问题①根据加工表面的技术要求,尽可能采用经济加工精度方案经济加工精度:是指在正常的加工条件下,(包括完好的机床设备、必要的工艺装备、标准的工人技术等级、标准的耗用时间和生产费用)所能达到的加工精度。
机械加工工艺规程的制定
(二)加工阶段划分的意义
(1)保证加工质量 工件粗加工时,由于加工余量大,因此加工时背吃刀量 和进给量都大,产生的切削力及切削热也大,从而引起工艺系统受力变形、 热变形也大,所以从加工的方式可以看出,粗加工不可能得到高的精度和 小的表面粗糙度值,必须要有后续的、更高级的加工手段,逐步改变切削 用量,减少加工误差,最终满足零件的设计要求。 (2)合理使用机床设备 加工过程按阶段划分后,可合理使用设备,充分发 挥粗、精加工设备的各自特点,使设备得到合理的使用。 (3)方便安排热处理工序和及时发现毛坯缺陷 在加工过程中,如果零件需 要热处理,则加工过程至少需要划分为两个阶段。
四、加工顺序的安排
(一)机械加工工序的安排
1)为了为后续的工序提供合适的定位基准,往往在加工过程的开始,首先加 工出精基准。 2)首先安排加工表面的粗加工,然后安排半精加工,最后安排精加工、光整 加工。 3)根据零件功能和技术要求,一般将零件加工表面区分为主要表面和次要表 面,以主要表面的加工顺序安排为重点,将次要表面加工穿插于主要表面的 加工工序中间,这样有主有次、相得益彰。 4)先面后孔。 5)对于单件、小批量生产的零件,当工厂(车间)的设备按机床功能归类布置时, 为了避免零件的往返搬运费时、碰伤、碰坏的可能,应考虑加工工序集中安 排。
二、表面加工方法的选择 1.外圆表面的加工
1)粗车。 2)粗车→半精车。 3)粗车→半精车→粗磨。 4)粗车→半精车→粗磨→精磨。 5)粗车→半精车→粗磨→精磨→研磨或其他超精加工。 6)粗车→半精车→精车。 7)粗车→半精车→精车→金刚车(细车)。
图5-7 外圆表面加工流程框图
2.孔的加工
图5-8 孔加工流程框图
2.工序过程卡片 为每个工序所编制的卡片称为工序卡片。在每张工序
《机械制造基础》第5章 机械加工工艺规程的制定
河南科技大学教案首页课程名称机械制造基础任课教师邓效忠第五章机械加工工艺规程的制定计划学时14教学的目的和要求:要求学生掌握定位基准和表面加工方法的选择原则,能够拟定工艺路线,会运用工艺尺寸链确定工序尺寸及其公差,使学生具有编制中等复杂零件加工工艺规程的能力。
重点:工件定位基准的选择;工序顺序的确定;工艺尺寸链及其应用。
难点:工艺尺寸链及其应用。
思考题:1.什么叫基准?基准分哪儿种?2.精、粗定位基准的选择原则各有哪些?如何分析这些原则之间出现的矛盾?3.零件表面加工方法的选择原则是什么?4.制定机械加工工艺规程时,为什么要划分加工阶段?5.切削加工顺序安排的原则是什么?6.什么叫工序集中?什么叫工序分散?各用于什么场合?7.什么叫工序余量?影响工序余量的因素是什么?8.什么叫尺寸链?它具有哪些特征?9.什么叫工艺规程?它有什么作用?10.如何确定尺寸链中的增环、减环和封闭环?第5章机械加工工艺规程设计5.1 概述一、机械加工工艺规程及其作用将产品或零部件的制造工艺过程的所有内容用图、表、文字的形式规定下来的工艺文件汇编称为工艺规程。
二、工艺规程设计所需的原始资料⑴零件图和产品整套装配图;⑵产品的生产纲领和生产类型;⑶产品的质量验收标准;⑷毛坯情况;⑸本厂的生产条件和技术水平;⑹国内外生产技术发展情况。
三、工艺规程设计的步骤⑴零件的工艺性分析。
⑵确定毛坯。
⑶拟定工艺路线,选择定位基准。
⑷确定各工序的设备和工装。
⑸确定主要工序的生产技术要求和质量验收标准。
⑹确定各工序的余量,计算工序尺寸和公差。
⑺确定各工序的切削用量。
⑻确定工时定额。
⑼填写工艺卡。
5.2 机械加工工艺规程设计一、零件的结构工艺性分析结构工艺性是指产品的结构是否满足优质、高产、低成本制造的一种性质。
零件结构工艺性举见教材表5-4。
二、确定毛坯三、定位基准的选择粗基准是指未经机械加工的定位基准,而精基准则是经过机械加工的定位基准。
1.粗基准的选择原则粗基准选择的主要目的是:保证非加工面与加工面的位置关系;保证各加工表面余量的合理分配。
(完整版)机械加工工艺规程的制定习题答案
第一章机械加工工艺规程的制定习题答案一、填空题1、生产过程包括:技术准备过程、生产过程、辅助生产过程、生产服务四过程。
在生产过程中与机械加工有关的过程称为机械加工工艺过程,其文件固定形式称为机械加工工艺规程。
2、零件的机械加工工艺过程由若干个工序所组成;在每一个工序中可以包含一个或几个工步;又可以包含一个或几个安装,在每一个安装中可以包含一个或几个工位,每一个工位可能包含一个或几个工作行程。
工序是依据工作地点是否变化和工作过程是否连续来划分的。
3、获得尺寸精度的方法有:试切法、调整法、定尺寸法和自动控制法。
4、机械加工中常用的毛坯有:铸件、锻件、型材、焊接件、冷冲压件毛坯和其它形式的毛坯。
5、根据基础基准的应用场合和作用不同,基准可分为:设计基准和工艺基准两大类。
而工艺基准又可分为:工序基准、定位基准、测量基准和装配基准。
6、精基准的选择原则有:基准重合原则、基准统一原则、作为定位基准应保证工件定位准确,夹紧可靠,夹具结构简单,操作方便、互为基准原则、自为基准原则。
7、在机械加工中,零件的加工阶段通常有:粗加工阶段、半精加工阶段、精加工阶段和光整加工阶段四个加工阶段。
8、机械加工中的预备热处理方法有:退火、正火、调质和时效处理四种。
9、机械加工中的最终热处理方法有:淬火、渗碳淬火和氮化处理三种。
10、在安排机械加工顺序时,一般应遵循的有:“先粗后精” 原则、“先主后次” 原则、“先基面后其它”原则和“先面后孔”的原则。
11、加工余量可分为工序余量和总加工余量。
12、标注工序尺寸公差时,一般毛坯尺寸公差采用双向对称标注;最后一道工序标注设计尺寸公差;而中间工序的工序尺寸公差一般按“入体”原则标注;即对包容表面(孔),其基本尺寸是最小工序尺寸,公差表现为上偏差;对被包容表面(轴),其基本尺寸是最大工序尺寸,公差表现为下偏差。
13、尺寸链由环组成,根据其性质不同可以将尺寸环分为组成环对封闭环;而根据组成环对封闭环的影响情况不同,又可以将组成环分为增环和减环。
机械加工流程规范
机械加工流程规范
1. 工艺准备
- 仔细审阅加工图纸和技术要求
- 选择合适的加工设备和工具
- 确保设备处于良好状态并进行必要的维护保养
- 准备好所需的量具和测量工具
2. 工件装夹
- 正确选择合适的夹具或夹持装置
- 确保工件夹持牢固、无偏移
- 注意工件装夹位置和方向
3. 设备调试
- 根据工艺要求设置切削参数,如主轴转速、进给速度等 - 对刀检测,确保刀具无偏移和损伤
- 进行空运转测试,检查设备运行状态
4. 加工过程
- 严格遵守操作规程和安全要求
- 密切监控加工过程,及时调整参数
- 对加工表面进行清理,防止碎屑影响加工质量
- 定期检查刀具磨损情况,必要时及时更换刀具
5. 质量检验
- 使用合适的测量工具对加工件进行尺寸检测
- 检查加工件表面质量,无缺陷和毛刺
- 核对加工件与图纸要求的一致性
6. 工艺反馈
- 记录加工过程中的任何异常情况
- 及时调整工艺参数以优化加工效果
- 对加工效率和质量问题进行分析并持续改进
以上是一般机械加工流程的规范要求,具体操作还需根据不同工件和加工方式有所调整,同时应严格执行相关安全生产规程。
- 1、下载文档前请自行甄别文档内容的完整性,平台不提供额外的编辑、内容补充、找答案等附加服务。
- 2、"仅部分预览"的文档,不可在线预览部分如存在完整性等问题,可反馈申请退款(可完整预览的文档不适用该条件!)。
- 3、如文档侵犯您的权益,请联系客服反馈,我们会尽快为您处理(人工客服工作时间:9:00-18:30)。
(2)工序余量
工序余量是一道工序内切除的 金属层厚度,为相邻两工序的 工序尺寸之差。
(3)总余量为各工序余量之和
(4)公称余量
(5)余量公差
公称余量是指相邻两 工序的基本尺寸之差。 加工余量分为: 单边余量及双边余量
Tz Z max Z min Ti Ti 1
(6)余量大小对加工精度、生产率、经济 性都有影响
1、基准重合原则
举例
(1)设计基准与定位基准不重合误差只发生在用调整法获得加工尺寸的情况。 (2)基准不重合误差值等于设计基准与定位基准之间尺寸的变化量(公差)。 (3)基准不重合一般发生在下列情况: ①用设计基准定位不可能或不方便; ②在选择精基准时优先考虑了基准统一原则。 (4)设计基准与测量基准不重合也会产生基准不重合误差。 (5)基准不重合误差不仅指尺寸误差,而且对位置误差也要考虑。
干个相关零件构成互相有联系的封闭尺寸链。包含零件尺寸、 间隙、形位公差等。 (3) 工艺系统尺寸链:在零件生产过程中某工序的工艺系统 内,由工件、刀具、夹具、机床及加工误差等有关尺寸所形
成的封闭尺寸链。
2.按照各构成尺寸所处的空间位置,可分为:
(1) 直线尺寸链:尺寸链全部尺寸位于两 根或几根平行直线上,称为线性尺寸链。 (2) 平面尺寸链: 尺寸键全部尺 寸位于一个或几个平行平面内。
0.3 0.1 0.01
50.11 50.01 50
h( 80 0.39)
h( 60 . 0.016)
h(0 0.011)
Ra1.25
Ra 0.16
Ra 0.04.
500 0.011
课题五 工艺尺寸链
一、尺寸链的定义、组成
1、定义
尺寸链就是在零件加工或 机器装配过程中,由相互 联系且按一定顺序连接的 封闭尺寸组合。
AΣ A1 A2 A3
4.按照尺寸键的相互联系的形态,又可分为: (1)独立尺寸链:所有构成尺寸链的环,在同一尺寸链中。 (2)相关尺寸链:具有公共环的两个以上尺寸链组。即构 成尺寸链中的一个或几个环,分布在两个或两个以上的尺寸 链中。
A6 AΣ A4 A1 A2 A3 A5
A4 A3 A2 A1 A5
L2 L3 L∑ L4 L1
A6 AΣ A7
(3) 空间尺寸链: 尺寸链全部尺 寸位干几个不平行的平面内。
3.按照构成尺寸链各环的几何特征,可分为: (1) 长度尺寸链:所有构成尺寸的环,均为直线长度量。 (2) 角度尺寸链:构成尺寸链的各环为角度量,或平行度、 垂直度等。
工序尺寸及公差
56 2
6.01 6 56
4.5 4.49 51.51
1.1 50.41
h13 (0 0.39)
Ra16.
51.510 0.39
.Ra 2.5 h11 (0 0.16)
50.410 0.16
50.110 0.039
50.010 0.016
高频 粗磨 精磨 研磨
产品的生产。
工序集中与分散的选择
工序的集中与分散程度必须根据生产规模、零件的结构
特点和技术要求、机床设备等具体生产条件进行综合分析确 定。 如:a.单件小批:在通用数控机床上实现工序集中 b.成批生产:分散为宜,也可采用一些昂贵设备和工
艺装备使工序集中,或者采用多刀多工位进行工序集中。
四、加工顺序的安排
3. 制订机械加工工艺规程的原始资料
•产品整套装配图、零件图 •质量标准 •生产纲领、生产类型 •毛坯情况 •本厂现有生产条件 •先进技术、工艺 •有关手册、图册
4. 制订机械加工工艺规程的原则及步骤
(1)机械加工工艺规程制定的原则 (1)保证加工质量,保证技术要求 (2)保证生产效率,满足生产纲领 (3)较低制造成本 (4)良好劳动条件,保障生产安全
(2)步
骤
•分析研究产品图纸 •工艺性分析 •选择毛坯 •拟订工艺路线 •选择设备、工装 •技术经济分析 •确定工序余量、工序尺寸 •确定切削用量、工时定额 •填位基准选择
采用毛坯上未经加工 的表面作为定位基准。
定位基准
1、粗基准 2、精基准 3、辅助基准
采用经过加工的表面 作为定位基准。
(1)在加工中形成的尺寸链——工艺尺寸链
2.定位面 3.设计基准
1.加工面
A1
A0
A2
(2)在装配中形成的尺寸链——装配尺寸链
A0
A2
A1
1、封闭性:尺寸链的各尺寸应构成封闭形式
(并且是按照一定顺序首尾相接的)。
2、特征
2、关联性:尺寸链中的任何一个尺寸变化都将 直接影响其它尺寸的变化。 。
环——尺寸链中的每一个尺寸。它可以是长度或角度。
缺点: 设备工艺装备投资大、调整、维护复杂,生产准备工作 量大,更换新产品困难,柔性差。
2)工序分散的特点:
①工序多,工艺过程长,各工序加工内容少,有的情况只
有一 个工步。 ②所使用的设备和工艺装备较简单,易于调整,掌握。 ③有利于选用合理的切削用量,减少工序基本时间 ④设备数量多,生产面积大,人员多,但不易于适应新
5、定位夹紧可靠方便
图床身导轨面自为基准
课题三 拟定工艺路线
拟定工艺路线,是制订工艺规程时的一项很重要的工 作。工艺路线拟定的是否合理,直接影响到工艺规程的合理 性科学性和经济性。
一、加工方法的选择 1. 所选择的加工方法能否达到零件精度的要求。 2. 零件材料的可加工性能如何。 3. 生产率对加工方法有无特殊要求。
检验工序
•质量检验 •特种检验(无损探伤、 磁力探伤、水压、超 速试验) •去毛刺、倒钝锐边 •去磁 •清洗 •涂防锈油
位置:去毛刺、倒钝锐边 应在淬火前 目的:安全
其它工序安排
课题四 加工余量的确定 一、加工余量确定
1. 加工余量概念
(1)总加工余量
总加工余量是指零件加工过 程中,某加工表面所切去的 金属层总厚度。是毛坯尺寸 与零件图样的设计尺寸之差。
举例:
A1
增环
在尺寸链图中用首尾相接的单向 箭头顺序表示各尺寸环,其中与 封闭环箭头方向相反者为增环, 与封闭环箭头方向相同者为减环。
封闭环
A0 A2
A3 减环
二、尺寸链的分类
1.按不同生产过程来分 (1) 工艺尺寸链:在零件加工工序中,由有关工序尺寸、设 计尺寸或加工余量等所组成的尺寸链。
(2) 装配尺寸链:在机器设计成装配中,由机器或部件内若
2. 影响加工余量的因素
1、上工序的表面粗糙度和表面缺陷层(图) 2、上工序的尺寸公差(图) 3、上工序各表面间相互位置的空间偏差(图) 4、本工序安装误差(图)
加工表面的粗糙度与缺陷层
1-缺陷层;2-正常组织
上工序误差
轴的弯曲对加工余量的影响
三爪卡盘上的装夹误差
3. 加工余量的确定
1、计算法 2、查表法 3、经验法
二、加工阶段的划分
粗加工阶段 半精加工阶段
切除大量多余材 料,主要提高生 产率。
完成次要表面加工(钻、 攻丝、铣键槽等)主要表 面达到一定要求,为精 加工作好余量准备安排 在热处理前。
加工阶段
精加工阶段 光整加工阶段
划分加工阶段的原因
主要表面达到图纸要求。 1、保证加工质量 2、合理使用设备 3、便于安排热处理工序 4、便于及时发现毛坯缺陷 5、避免重要表面损伤。 进一步提高尺寸精度 降低粗糙度,但不能 提高形状、位置精度
1、加工顺序安排 (1)遵循四个原则:
a.先粗后精 精度逐步提高; b.先主后次 先行装配基面和主要工作面的加工,与主要表面 有联系的槽、孔等,介于半精加工与精加工之间。 c.基面先行 即首先应加工出选作定位基准的精基准表面, 然后再以精基准定位加工其它表面。如打中心孔。 d.先面后孔 平面轮廓大、定位稳定可靠。
三、工序的集中与分散
1)工序集中的特点 优点:①零件各加工表面的加工集中在少数几道工序内完成,各
工序内容多,工步多。
②有利于采用高效的专用设备和工艺装备,生产效率高。 ③生产面积和操作工人数减少,工艺路线短。 ④可简化生产计划和生产组织工作。 ⑤工件装夹次数减少,辅助时间缩短,加工表面间的位置精
度易于保证。
二、工序尺寸与公差的确定
工序尺寸是零件在加工 过程中各工序应保证的加工 尺寸,通常为加工面至定位 基准面之间的尺寸。
1. 无需进行尺寸换算时工序尺寸的确定 2. 需进行尺寸换算时工序尺寸的确定
无需进行尺寸换算时工序尺寸的确定
• • • •
确定加工工序的加工余量; 从设计尺寸开始,确定工序基本尺寸; 确定工序尺寸公差; 按入体原则标注工序尺寸公差。
例:图示零件加工台阶面
切削平面
A1
A1
A2 A2 δ(本道工序加工精度)
设计基准(定位基准)
若本道工序的加工精度为δ,则只要δ ≤ δA2,即可满 足加工要求
A1
A1
设计基准
A2
A1
A2
A3
定位基准
A1 -称为基准不重合误差
考虑一下:
2、基准统一原则 ①有利于保证各加工表面间的相互位置关系,避免基准 转换所产生的误差。 ②简化夹具的设计与制造。 3、互为基准 4、自为基准
3. 工艺规程是新建或扩建工厂或车间的基本资料
2. 常用工艺文件的种类
(1)机械加工工艺过程卡片
它是以工序为单位说明一个零件全部加工过程的工艺 卡片。这种卡片包括零件各个工序的名称、工序内容,经 过的车间、工段、所用的机床、刀具、夹具、量具,工时 定额等。主要用于单件小批生产以及生产管理中。
(2)机械加工工艺卡
配作加工 当部件精度很高时,某些表面精加工应安排在部件 装配或总装过程中进行,否则将导致零件精度过高而无法加工。
2. 热处理工序的安排