各种加工方法的加工精度
机械加工精度等级表
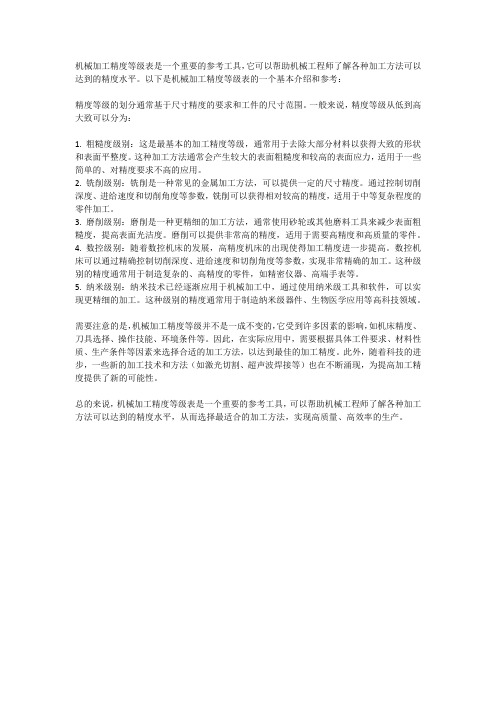
机械加工精度等级表是一个重要的参考工具,它可以帮助机械工程师了解各种加工方法可以达到的精度水平。
以下是机械加工精度等级表的一个基本介绍和参考:精度等级的划分通常基于尺寸精度的要求和工件的尺寸范围。
一般来说,精度等级从低到高大致可以分为:1. 粗糙度级别:这是最基本的加工精度等级,通常用于去除大部分材料以获得大致的形状和表面平整度。
这种加工方法通常会产生较大的表面粗糙度和较高的表面应力,适用于一些简单的、对精度要求不高的应用。
2. 铣削级别:铣削是一种常见的金属加工方法,可以提供一定的尺寸精度。
通过控制切削深度、进给速度和切削角度等参数,铣削可以获得相对较高的精度,适用于中等复杂程度的零件加工。
3. 磨削级别:磨削是一种更精细的加工方法,通常使用砂轮或其他磨料工具来减少表面粗糙度,提高表面光洁度。
磨削可以提供非常高的精度,适用于需要高精度和高质量的零件。
4. 数控级别:随着数控机床的发展,高精度机床的出现使得加工精度进一步提高。
数控机床可以通过精确控制切削深度、进给速度和切削角度等参数,实现非常精确的加工。
这种级别的精度通常用于制造复杂的、高精度的零件,如精密仪器、高端手表等。
5. 纳米级别:纳米技术已经逐渐应用于机械加工中,通过使用纳米级工具和软件,可以实现更精细的加工。
这种级别的精度通常用于制造纳米级器件、生物医学应用等高科技领域。
需要注意的是,机械加工精度等级并不是一成不变的,它受到许多因素的影响,如机床精度、刀具选择、操作技能、环境条件等。
因此,在实际应用中,需要根据具体工件要求、材料性质、生产条件等因素来选择合适的加工方法,以达到最佳的加工精度。
此外,随着科技的进步,一些新的加工技术和方法(如激光切割、超声波焊接等)也在不断涌现,为提高加工精度提供了新的可能性。
总的来说,机械加工精度等级表是一个重要的参考工具,可以帮助机械工程师了解各种加工方法可以达到的精度水平,从而选择最适合的加工方法,实现高质量、高效率的生产。
各种加工方法的经济精度和表面粗糙度

各种加工方法能够达到的尺寸的经济精度表1 孔加工的经济精度表2 圆锥形孔加工的经济精度表3 圆柱形深孔加工的经济精度表4 花键孔加工的经济精度表5 外圆柱表面加工的经济精度表6 端面加工的经济精度(mm)表7 用成形铣刀加工的经济精度(mm)注:指加工表面至基准的尺寸精度。
表8 同时加工平行表面的经刘精度(mm)注:指两平行表面距离的尺寸精度。
表9 平面加工的经济精度注:1 表内资料适用于尺寸<1m,结构刚性好的零件加工,用光洁的加工表面作为定位和测量基准。
2 端铣刀铣削的加工精度在相同的条件下大体上比圆柱铣刀铣削高一级。
3 细铣仅用于端铣刀铣削。
表10 公制螺纹加工的经济精度表11 花键加工的经济精度表12 齿形加工的经济精度各种加工方法能够达到的形状的经济精度表13 平面度和直线度的经济精度表14 圆柱形表面形状精度的经济精度注:形状精度等级的公差值见附表2、3。
表15 曲面加工的经济精度表16 在各种机床上加工时形状的平均经济精度各种加工方法所能够达到的相互位置的经济精度表17 平行度的经济精度表18 端面跳动和垂直度的经济精度表19 同轴度的经济精度表20 轴心线相互平行的孔的位置经济精度注:对于钻、卧镗及组合机床的镗孔偏差同样适用于铰孔。
表21 轴心线相互垂直的孔的位置经济精度注:在镗空间的垂直孔时,中心距误差可按上式相应的找正方法选用。
各种加工方法能够达到的零件表面粗糙度表22 各种加工方法能够达到的零件表面粗糙度各类型面的加工方案及经济精度表23 外圆表面加工方案表24 孔加工方案表25 平面加工方案——机械篇标准公差及形位公差附表1 标准公差值注:基本尺寸小于1mm时,无IT14至IT18。
13 22-4-25 10:32附表2 平面度、直线度公差值附表3 圆度、圆柱度公差值附表4 平行度、垂直度、倾斜度公差值附表5 同轴度、对称度、圆跳动、全跳动公差值参考文献1 《金属机械加工工艺人员手册》修订本上海科学技术出版社1981年2 《机械制造工艺学》顾崇衔等编著陕西科学技术出版社1982年3 《航空机械设计手册》第三机械工业部612所编1979年4 《机械制造工艺学课程设计简明手册》华中工学院机械制造工艺教研室编1981年5 《机械工程手册》第46篇机械工业出版社1981年6 《圆柱齿轮加工》上海科学技术出版社1979年切削用量切削用量的选择原则正确地选择切削用量,对提高切削效率,保证必要的刀具耐用度和经济性,保证加工质量,具有重要的作用。
各种机械加工能达到的精度

表3-31各秒加工方法能沽到的衰面粗植度即工方tt;Q底汽帆、帝锭或四丈便务ttfr军削外IS车电宅面电耕角GL的〉9L矽轮粗车非金艮精卒11•金属50* 12.5ffl较(二次纹)*转合金L6- 0.8精容年(或金网右军)非金厦料车精车"车次行程二次行程《 <】5umj> "5nvn非金/H租《有女.史:,半*铉I-次仗)糟密瞽5.3- 3.2L6-0JC.8~0.2S青掴黄携、,削0.8 —0.40.8-(1.20.8 - 0 40.2-0 1制国咤铢刀饨削精3.2*0.8fi徊爸12 5-3 23.2-0 80.8-0.4o a~u.24逐僚削6 3 ~ 16非金胃金凤0 8-0 4n 3-0.26 3-3.20.8-0 225-6.312.5-6.33.2-1.$6.3~3.26.3- 1.61.6-0.8倩密tfime6.5 -3 2非金僵半精僚琳金偃金n精密惶:疫金朋石噌)金.窝非金属0.4-0.2J2 5~6、36.3 "- I-66.3- 1.60 £^0.20 8-0.216-0 4■ ■、•0.2、。
1注:本表造用干尺寸<浦、佑购对忤好的零件却工.用光洁的E工・*面作为定位海做¥席,2.电恍万饨副的切二糟度在佃可茶件下大体吃圜柱住刀使引药-缘3.精岔供仅格J瑜费刀槌削°表3.10 面加工的经济精度« 3-11司时加工平行表HT 的经济精度(nun)途:括两平仃麦面距离的尺寸槽度.表618成形铢刀次工的经济精度( mn?)注:指加工未而节苏唯的代寸情?拳■兹咨网羽密夏理拳厦M KT・£ 馨加工力.法台差管吸we.全郴石精密珈工,精白1-2研磨.瑞愁.刮、靖容膳3-4 佥.坐栋蚀.怡峦就柄密例5-6蜜、侵.,刨、泣,维.车 5我、作、车.核导食钻、较9~ m各神槌好工]1 - 12 计碧.楚虑庚.金斜嘴、精膺、精府、刮、筋、植廊.费.仞,刮.谜不、半带就.里各声粗加1:表>24平行度的经济精度表32S城面跳动和垂直度的经济精度柬330在钢台机球却白功饶上加工TL的位*精度法;】•友中所列数据法用于灰皆铁.生加工苗含金时.怜言碧芹值要票以2.衰中所死的埼浅应移度适于以下条件:1>刀具檀住夹持在吏归上:2)祐食长度为(7~2.5)心〃具伸出钻套末培的长受为30mm:3)工件敢定<?*«是一平园和屈个度直于炫平肉的协充.。
各种加工方法的经济精度和表面粗糙度

各种加工方法能够达到的尺寸的经济精度表2圆锥形孔加工的经济精度表3圆柱形深孔加工的经济精度表4花键孔加工的经济精度表6端面加工的经济精度(mm)表8同时加工平行表面的经刘精度(mm)表面长度和宽(mm)W120>120〜300加工性质注:指两平行表面距离的尺寸精度。
91<lm2端铣刀铣削的加工精度在相同的条件下大体上比圆柱铣刀铣削高一级。
3细铣仅用于端铣刀铣削。
表10公制螺纹加工的经济精度表11花键加工的经济精度表12齿形加工的经济精度单头滚刀滚齿(m=1〜20mm)滚刀精度等级:AA 6〜7A8B 9C 10 圆盘形插齿刀插齿(m=1〜20mm)插齿刀精度等级:AA 6A 7B 8 磨齿:成形砂轮仿形法5〜6盘形砂轮范成法3〜6 两个盘形砂轮范成法3〜6 蜗杆砂轮范成法4〜6 用铸铁研磨轮研齿5〜6 直齿圆锥齿轮刨齿8螺旋齿圆锥齿轮刀盘铣齿8蜗轮模数滚刀滚蜗轮8 热轧齿轮(m=2〜8mm) 8〜9 热轧后冷校准齿型(m=2〜8mm)7〜8 冷轧齿轮(m W1.5mm) 7圆盘形插齿刀剃齿(m=l〜20mm)剃齿刀精度等级:ABC各种加工方法能够达到的形状的经济精度14231516牛头刨床表17平行度的经济精度表18端面跳动和垂直度的经济精度表19同轴度的经济精度表20轴心线相互平行的孔的位置经济精度最大刨削长度(mm)各种加工方法能够达到的零件表面粗糙度表22各种加工方法能够达到的零件表面粗糙度>20〜160 >20〜80>©150(mm)粗(有表皮)扩孔word格式-可编辑-感谢下载支持砂轮清理>20〜320 >3.2〜80滚压加工>0.2〜3.2钳工锉削各类型面的加工方案及经济精度表23外圆表面加工方案表24孔加工方案word格式-可编辑-感谢下载支持标准公差及形位公差附表1标准公差值1mm IT14IT18附表2平面度、直线度公差值1《金属机械加工工艺人员手册》修订本上海科学技术出版社1981年2《机械制造工艺学》顾崇衔等编著陕西科学技术出版社1982年3《航空机械设计手册》第三机械工业部612所编1979年4《机械制造工艺学课程设计简明手册》华中工学院机械制造工艺教研室编1981年5《机械工程手册》第46篇机械工业出版社1981年6《圆柱齿轮加工》上海科学技术出版社1979年切削用量切削用量的选择原则正确地选择切削用量,对提高切削效率,保证必要的刀具耐用度和经济性,保证加工质量具有重要的作用。
常用加工精度对照表
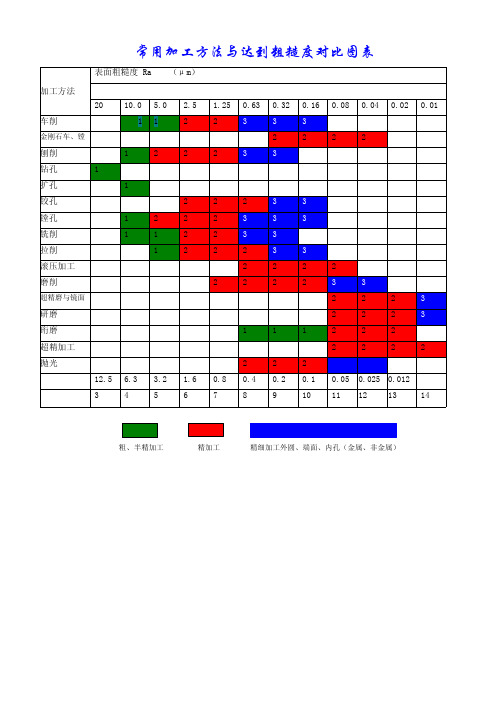
常用加工方法与达到粗糙度对比图表粗、半精加工精加工精细加工外圆、端面、内孔(金属、非金属)孔加工方案与经济公差序号加工方案经济公差等级表面粗糙度Ra(μm)适用范围1钻IT11-1320加工未淬火钢及铸铁的实心毛坯,也可用于加工有色金属(表面粗糙度稍差),孔径<(15-20)mm 2钻-铰IT8-9 5.0-2.53钻-粗铰-精铰IT7-8 2.5-1.254钻-扩IT1120-10.0同上,但孔径>(15-20)mm5钻-扩-铰IT8-9 5.0-2.56钻-扩-粗铰-精铰IT7 2.5-1.257钻-扩-机铰-手铰IT6-70.63-0.1608钻-(扩)-拉IT6-7 2.5-0.160大批大量生产(精度视)9粗镗(或扩孔)IT11-1320-10.0除淬火钢外各种材料,毛坯有铸出孔或锻出孔10粗镗(粗扩)-半精镗(精扩)IT8-9 5.0-2.511粗镗(扩)-半精镗(精扩)-精镗(铰)IT7-8 2.5-1.2512粗镗(扩)-半精镗(精扩)-精镗-浮动镗刀块精镗IT6-7 1.25-0.6313粗镗(扩)-半精镗-磨孔IT7-8 1.25-0.32主要用于加工淬火钢,也可用于不淬火钢,但不宜用于有色金属14粗镗(扩)-半精镗-粗磨-精磨IT6-70.32-0.16015粗镗-半精镗-精镗-金刚镗IT6-70.63-0.080主要用于精度要求较高的有色金属加工16钻-(扩)-粗铰-精铰-珩磨钻-(扩)-拉-珩磨粗镗-半精镗-精镗-珩磨IT6-70.32-0.040精度要求很高的孔17以研磨代替上述方案的珩磨IT6以上0.160-0.010平面加工方案与经济公差序号加工方案经济公差等级表面粗糙度Ra(μm)适用范围1粗车-半精车IT8-910-5.0端面2粗车-半精车-精车IT6-7 2.5-1.53粗车-半精车-磨削IT7-9 1.25-0.324粗刨(或粗铣)-精刨(或精铣)IT7-910.0-2.5一般不淬硬平面(端铣的表面粗糙度较好)5粗刨(或粗铣)-精刨(或精铣)-括研IT5-6 1.25-0.160精度要求较高的不淬硬平面批量较大时宜采用宽刃精刨方案6粗刨(或粗铣)-精刨(或精铣)-宽刃精刨IT6 1.25-0.327粗刨(或粗铣)-精刨(或精铣)-磨削IT6 1.25-0.32精度要求较高的淬硬平面或不淬硬平面8粗刨(或粗铣)-精刨(或精铣)-粗磨-精磨IT5-60.63-0.0409粗铣-拉IT6-9 1.25-0.32大量生产,较小的平面(精度视拉刀的精度而定)10粗铣-精铣-磨削-研磨IT5以上高精度平面外圆表面加工方案与经济公差序号加工方案经济公差等级表面粗糙度Ra(μm)适用范围1.粗车IT11-1380-20适用于淬火钢外的各种金属2.粗车-半精车IT8-910.0-5.03.粗车-半精车-精车IT6-7 2.5-1.254.粗车-半精车-精车-滚压(或抛光)IT6-70.32-0.0405.粗车-半精车-磨削IT6-7 1.25-0.63主要用于淬火钢,也可用于未淬火钢,但不宜加工有色金属6.粗车-半精车-粗磨-精磨IT5-60.63-0.1607.粗车-半精车-粗磨-精磨-超精加工(或轮式超精磨)IT50.160-0.0208.粗车-半精车-精车-金刚石车IT5-60.63-0.040主要用于要求较高的有色金属的加工9.粗车-半精车-粗磨-精磨-超精磨或镜面磨IT5以上0.040-0.010极高精度的外圆加工10.粗车-半精车-粗磨-精磨-研磨IT5以上0.160-0.010各种毛坯表面层厚度(mm)自由锻件模锻件铸件磁钢≤1.5磁钢≤1灰口铸铁1-4合金钢2-4合金钢≤0.5铸钢2-5。
各种加工方法的加工精度

各种加工方法的加工精度一:车削车削中工件旋转,形成主切削运动;刀具沿平行旋转轴线运动时,就形成内、外园柱面;刀具沿与轴线相交的斜线运动,就形成锥面;仿形车床或数控车床上,可以控制刀具沿着一条曲线进给,则形成一特定的旋转曲面;采用成型车刀,横向进给时,也可加工出旋转曲面来;车削还可以加工螺纹面、端平面及偏心轴等;车削加工精度一般为IT8—IT7,表面粗糙度为—μm;精车时,可达IT6—IT5,粗糙度可达—μm;车削的生产率较高,切削过程比较平稳,刀具较简单;二:铣削主切削运动是刀具的旋转;卧铣时,平面的形成是由铣刀的外园面上的刃形成的;立铣时,平面是由铣刀的端面刃形成的;提高铣刀的转速可以获得较高的切削速度,因此生产率较高;但由于铣刀刀齿的切入、切出,形成冲击,切削过程容易产生振动,因而限制了表面质量的提高;这种冲击,也加剧了刀具的磨损和破损,往往导致硬质合金刀片的碎裂;在切离工件的一般时间内,可以得到一定冷却,因此散热条件较好;按照铣削时主运动速度方向与工件进给方向的相同或相反,又分为顺铣和逆铣;顺铣铣削力的水平分力与工件的进给方向相同,工件台进给丝杠与固定螺母之间一般有间隙存在,因此切削力容易引起工件和工作台一起向前窜动,使进给量突然增大,引起打刀;在铣削铸件或锻件等表面有硬度的工件时,顺铣刀齿首先接触工件硬皮,加剧了铣刀的磨损;逆铣可以避免顺铣时发生的窜动现象;逆铣时,切削厚度从零开始逐渐增大,因而刀刃开始经历了一段在切削硬化的已加工表面上挤压滑行的阶段,加速了刀具的磨损;同时,逆铣时,铣削力将工件上抬,易引起振动,这是逆铣的不利之处;铣削的加工精度一般可达IT8—IT7,表面粗糙度为—μm;普通铣削一般只能加工平面,用成形铣刀也可以加工出固定的曲面;数控铣床可以用软件通过数控系统控制几个轴按一定关系联动,铣出复杂曲面来,这时一般采用球头铣刀;数控铣床对加工叶轮机械的叶片、模具的模芯和型腔等形状复杂的工件,具有特别重要的意义;三:刨削刨削时,刀具的往复直线运动为切削主运动;因此,刨削速度不可能太高,生产率较低;刨削比铣削平稳,其加工精度一般可达IT8—IT7,表面粗糙度为—μm,精刨平面度可达1000,表面粗糙度为—μm; 四:磨削磨削以砂轮或其它磨具对工件进行加工,其主运动是砂轮的旋转;砂轮的磨削过程实际上是磨粒对工件表面的切削、刻削和滑擦三种作用的综合效应;磨削中,磨粒本身也由尖锐逐渐磨钝,使切削作用变差,切削力变大;当切削力超过粘合剂强度时,圆钝的磨粒脱落,露出一层新的磨粒,形成砂轮的“自锐性”;但切屑和碎磨粒仍会将砂轮阻塞;因而,磨削一定时间后,需用金刚石车刀等对砂轮进行修整;磨削时,由于刀刃很多,所以加工时平稳、精度高;磨床是精加工机床,磨削精度可达IT6—IT4,表面粗糙度Ra可达—μm,甚至可达—μm;磨削的另一特点是可以对淬硬的金属材料进行加工;因此,往往作为最终加工工序;磨削时,产生热量大,需有充分的切削液进行冷却;按功能不同,磨削还可分为外园磨、内孔磨、平磨等;五:钻削与镗削在钻床上,用钻头旋转钻削孔,是孔加工的最常用方法;钻削的加工精度较低,一般只能达到IT10,表面粗糙度一般为—μm,在钻削后常常采用扩孔和铰孔来进行半精加工和精加工;扩孔采用扩孔钻,铰孔采用铰刀进行加工;铰削加工精度一般为IT9—IT6,表面粗糙度为—μm;扩孔、铰孔时,钻头、铰刀一般顺着原底孔的轴线,无法提高孔的位置精度;镗孔可以较正孔的位置;镗孔可在镗床上或车床上进行;在镗床上镗孔时,镗刀基本与车刀相同,不同之处是工件不动,镗刀在旋转;镗孔加工精度一般为IT9—IT7,表面粗糙度为—0.8mm;钻削加工镗床加工车床加工六:齿面加工齿轮齿面加工方法可分为两大类:成形法和展成法;成形法加工齿面所使用的机床一般为普通铣床,刀具为成形铣刀,需要两个简单成形运动:刀具的旋转运动和直线移动;展成法加工齿面的常用机床有滚齿机、插齿机等;七:复杂曲面加工三维曲面的切削加工,主要采用仿形铣和数控铣的方法或特种加工方法见本节八;仿形铣必须有原型作为靠模;加工中球头仿形头,一直以一定压力接触原型曲面;仿形头的运动变换为电感量,加工放大控制铣床三个轴的运动,形成刀头沿曲面运动的轨迹;铣刀多采用与仿形头等半径的球头铣刀;数控技术的出现为曲面加工提供了更有效的方法;在数控铣床或加工中心上加工时,是通过球头铣刀逐点按坐标值加工而成;采用加工中心加工复杂曲面的优点是:加工中心上有刀库,配备几十把刀具;曲面的粗、精加工,可用不同刀具对凹曲面的不同曲率半径,也可选用适当的刀具;同时,可在一次安装中加工各种辅助表面,如孔、螺纹、槽等;这样充分保证了各表面的相对位置精度;八:特种加工特种加工方法是指区别于传统切削加工方法,利用化学、物理电、声、光、热、磁或电化学方法对工件材料进行加工的一系列加工方法的总称;这些加工方法包括:化学加工CHM、电化学加工ECM、电化学机械加工ECMM、电火花加工EDM、电接触加工RHM、超声波加工USM、激光束加工LBM、离子束加工IBM、电子束加工EBM、等离子体加工PAM、电液加工EHM、磨料流加工AFM、磨料喷射加工AJM、液体喷射加工HDM及各类复合加工等;分类原理原理示意特点应用范围电火花加工电火花加工是利用工具电极和工件电极间瞬时火花放电所产生的高温熔蚀工件表面材料来实现加工的;电火花加工机床一般由脉冲电源、自动进给机构、机床本体及工作液循环过滤系统等部分组成;工件固定在机床工作台上;脉冲电源提供加工所需的能量,其两极分别接在工具电极与工件上;当工具电极与工件在进给机构的驱动下在工作液中相互靠近时,极间电压击穿间隙而产生火花放电,释放大量的热;工件表层吸收热量后达到很高的温度10000℃以上,其局部材料因熔化甚至气化而被蚀除下来,形成一个微小的凹坑;工作液循环过滤系统强迫清洁的工作液以一定的压力通过工具电极与工件之间的间隙,及时排除电蚀产物,并将电蚀产物从工作液中过滤出去;多次放电的结果,工件表面产生大量凹坑;工具电极在进给机构的驱动下不断下降,其轮廓形状便被“复印”到工件上工具电极材料尽管也会被蚀除,但其速度远小于工件材料; 用特殊形的电极工具加工相应工件的电火花成形加工机床————①加工硬、脆、韧、软和高熔点的导电材料;②加工半导体材料及非导电材料;③加工各种型孔、曲线孔和微小孔;④加工各种立体曲面型腔,如锻模、压铸模、塑料模的模膛;⑤用来进行切断、切割以及进行表面强化、刻写、打印铭牌和标记等;用线电极加工二维轮廓形状工件的电火花线切割机床电解加工电解加工是利用金属在电解液中产生阳极溶解的电化学原理对工件进行成形加工的一种方法;工件接直流电源正极,工具接负极,两极之间保持狭小间隙0.1mm~0.8mm;具有一定压力~的电解液从两极间的间隙中高速15m/s~60m/s流过;当工具阴极向工件不断进给时,在面对阴极的工件表面上,金属材料按阴极型面的形状不断溶解,电解产物被高速电解液带走,于是工具型面的形状就相应地“复印”在工件上; ————①工作电压小,工作电流大;②以简单的进给运动一次加工出形状复杂的型面或型腔;③可加工难加工材料;④生产率较高,约为电火花加工的5~10倍;⑤加工中无机械切削力或切削热,适于易变形或薄壁零件的加工;⑥平均加工公差可达±0.1mm左右;⑦附属设备多,占地面积大,造价高;⑧电解液既腐蚀机床,又容易污染环境; 电解加工主要用于加工型孔、型腔、复杂型面、小直径深孔、膛线以及进行去毛刺、刻印等;激光加工对工件的激光加工由激光加工机完成;激光加工机通常由激光器、电源、光学系统和机械系统等组成;激光器常用的有固体激光器和气体激光器把电能转变为光能,产生所需的激光束,经光学系统聚焦后,照射在工件上进行加工;工件固定在三坐标精密工作台上,由数控系统控制和驱动,完成加工所需的进给运动;①不需要加工工具;②激光束的功率密度很高,几乎对任何难加工的金属和非金属材料都可以加工;③激光加工是非接触加工,工件无受力变形;④激光打孔、切割的速度很高,加工部位周围的材料几乎不受切削热的影响,工件热变形很小;⑤激光切割的切缝窄,切割边缘质量好; 激光加工已广泛用于金刚石拉丝模、钟表宝石轴承、发散式气冷冲片的多孔蒙皮、发动机喷油咀、航空发动机叶片等的小孔加工以及多种金属材料和非金属材料的切割加工;超声波加工超声波加工是利用超声频16KHz~25KHz振动的工具端面冲击工作液中的悬浮磨料,由磨粒对工件表面撞击抛磨来实现对工件加工的一种方法;超声发生器将工频交流电能转变为有一定功率输出的超声频电振荡,通过换能器将此超声频电振荡转变为超声机械振动,借助于振幅扩大棒把振动的位移幅值由0.005mm~0.01mm 放大到~0.15mm,驱动工具振动;工具端面在振动中冲击工作液中的悬浮磨粒,使其以很大的速度,不断地撞击、抛磨被加工表面,把加工区域的材料粉碎成很细的微粒后打击下来;虽然每次打击下来的材料很少,但由于打击的频率高,仍有一定的加工速度;由于工作液的循环流动,被打击下来的材料微粒被及时带走;随着工具的逐渐伸入,其形状便“复印”在工件上; ——————————————在加工难切削材料时,常将超声振动与其它加工方法配合进行复合加工,如超声车削、超声磨削、超声电解加工、超声线切割等;这些复合加工方法把两种甚至多种加工方法结合在一起,能起到取长补短的作用,使加工效率、加工精度及工件的表面质量显着提高;九:加工方法的选择选择加工方法主要考虑零件表面形状、尺寸精度和位置精度要求、表面粗糙度要求,以及现有机床、刀具等资源情况、生产批量、生产率和经济技术分析等因素;三.典型表面的加工路线一外圆表面的加工路线1.粗车→半精车→精车:应用最广,满足IT≥IT7,▽≥外圆可以加工2.粗车→半精车→粗磨→精磨:用于有淬火要求IT≥IT6,▽≥的黑色金属;3.粗车→半精车→精车→金刚石车:用于有色金属、不宜采用磨削加工的外用表面;4.粗车→半精车→粗磨→精磨→研磨、超精加工、砂带磨、镜面磨、或抛光在2的基础上进一步精加工;目的为了减少粗糙度,提高尺寸精度,形状和位置精度;二孔的加工路线1.钻→粗拉→精拉:用于大批大量生产盘套类零件的内孔,单键孔和花键孔加工,加工质量稳定,生产效率高;2.钻→扩→铰→手铰:用于中小孔加工,扩孔前纠正位置精度,铰孔保证尺寸、形状精度和表面粗糙度;3.钻或粗镗→半精镗→精镗→浮动镗或金刚镗应用:1单件小批量生产中箱体孔隙加工;2位置精度要求很高的孔系加工;3直径比较大得孔ф80mm以上,毛坯上已有铸孔或锻孔;4有色金属有金刚镗来保证其尺寸,形状和位置精度以及表面粗糙度的要求4./钻粗镗粗磨→半精磨→精磨→研磨或衍磨应用:淬硬零件加工或精度要求高的孔加工;说明:1孔最终加工精度很大程度上取决于操作者的水平;2特小孔加工采用特种加工方法;三平面的加工路线1.粗铣→半精铣→精铣→高速铣平面加工中常用,视被加工面精度和表面粗糙度技术要求,灵活安排工序;2./粗刨→半精刨→精刨→宽刀精刨、刮研或研磨应用广泛,生产率低,常用于窄长面的加工,最终工序安排也视加工表面的技术要求而定; 3.铣刨→半精铣刨→粗磨→精磨→研磨、精密磨、砂带磨、抛光加工表面淬火,最终工序视加工表面的技术要求而定;4.拉→精拉大批量生产有沟槽或台阶表面;5.车→半精车→精车→金刚石车有色金属零件的平面加工;零件表面粗糙度参数值的选择零件表面粗糙度参数的选择既要满足零件表面的功能要求,也要考虑到经济性;具体选择时可参照一些经过验证的实例;用类比法来确定;用类比法来确定;一般选择原则如下;1、在满足表面功能要求的情况下尽量选择较大的表面粗糙度参数值;2、同一零件上,工作表面的粗糙度参数值小于非工作表面的粗糙度参数值;3、摩擦表面比非摩擦表面的粗糙度参数值要小;滚动摩擦表面比滑动摩擦表面的粗糙度参数值要小;运动速度高,单位压力大的摩擦表面应比运动速度低,单位压力小的摩擦表面的粗糙度参数值要小;4、受循环载荷的表面及易引起应力集中的部分如圆角、沟槽,表面粗糙度参数值要小5、配合性质要求高的结合表面、配合间隙小的配合表面以及要求连接可靠、受重载的过盈配合表面等,都应取较小的粗糙度参数值;6、配合性质相同,零件尺寸愈小则表面粗糙度参数值愈小;同一精度等级,小尺寸比大尺寸、轴比孔的表面粗糙度参数值要小;通常尺寸公差、表面形状公差小时,表面粗糙度参数值也小;但表面粗糙度参数值和尺寸公差、表面形状公差之间并不存在确定的函数关系;如手轮、手柄的尺寸公差值较大,但表面粗糙度参数值却较小;一般情况下,它们之间有一定的对应关系;设表面形状公差值为T,尺寸公差值为IT,它们之间可参照以下对应关系:若T≈,则Ra≤;Rz≤T≈, 则Ra≤;Rz≤T≈, 则Ra≤;Rz≤T<, 则Ra≤;Rz≤。
普通车床的加工精度范围表
机械零部件用作不同的机械部位,车床加工精度也是不同的,与其匹配的加工形式和加工工艺也不同。
本文围绕介绍车、铣、刨、磨、钻、镗等常见的几种加工形式所能达到的加工精度。
一、车削工件旋转,车刀在平面内作直线或曲线移动的切削加工。
车削一般在车床上进行,用以加工工件的内外圆柱面、端面、圆锥面、成形面和螺纹等。
车削加工精度一般为IT8—IT7,表面粗糙度为1.6—0.8μm。
1)粗车力求在不降低切速的条件下,采用大的切削深度和大进给量以提高车削效率,但加工精度只能达IT11,表面粗糙度为Rα20—10μm。
2)半精车和精车尽量采用高速而较小的进给量和切削深度,加工精度可达IT10—IT7,表面粗糙度为Rα10—0.16μm。
3)在高精度车床上用精细修研的金刚石车刀高速精车有色金属件,可使加工精度达到IT7—IT5,表面粗糙度为Rα0.04—0.01μm,这种车削称为"镜面车削"。
二、铣削铣削是指使用旋转的多刃刀具切削工件,是高效率的加工方法。
适于加工平面、沟槽、各种成形面(如花键、齿轮和螺纹)和模具的特殊形面等。
按照铣削时主运动速度方向与工件进给方向的相同或相反,又分为顺铣和逆铣。
铣削的加工精度一般可达IT8—IT7,表面粗糙度为6.3—1.6μm。
1)粗铣时的加工精度IT11—IT13,表面粗糙度5—20μm。
2)半精铣时的加工精度IT8—IT11,表面粗糙度2.5—10μm。
3)精铣时的加工精度IT16—IT8,表面粗糙度0.63—5μm。
三、刨削刨削加工是用刨刀对工件作水平相对直线往复运动的切削加工方法,主要用于零件的外形加工。
刨削加工精度一般可达IT9—IT7,表面粗糙度为Ra6.3—1.6μm。
1)粗刨加工精度可达IT12—IT11,表面粗糙度为25—12.5μm。
2)半精刨加工精度可达IT10—IT9,表面粗糙度为6.2—3.2μm。
3)精刨加工精度可达IT8—IT7,表面粗糙度为3.2—1.6μm。
各种机械加工方法的加工精度
各种机械加工方法的加工精度
机械加工方法是指利用机床和切削工具对金属、合金、塑料等材料进行切削、锻造、焊接、抛光等操作,以达到工件设计尺寸、形状和表面粗糙度要求的一系列工艺过程。
不同的机械加工方法有着不同的加工精度,下面将对常见的几种机械加工方法的加工精度进行详细介绍。
1.车、铣、刨、磨加工:
车、铣、刨、磨加工是最常见的机械加工方法之一,其加工精度通常可达到0.01mm级别。
其中,精度最高的是磨加工,其加工精度可达到0.001mm级别。
而车、铣、刨加工的加工精度相对较低,通常在0.01mm 至0.015mm之间。
2.钻削加工:
钻削加工是通过钻头旋转和轴向进给运动,以及工件的切削超前量来进行的。
其加工精度一般可达到0.02mm级别。
3.线切割加工:
线切割是利用金属丝或者金刚线经过电火花腐蚀加工,从而将工件切割成所需形状的加工方法。
其加工精度可达到0.005mm级别。
4.电火花加工:
电火花加工是利用放电现象进行切削的一种加工方法,其加工精度可达到0.001mm级别。
5.冲压加工:
冲压加工是通过冲床对金属板材进行冲裁、弯曲、深冲等形变加工的方法。
其加工精度一般在0.05mm至0.1mm之间。
6.锻造加工:
锻造加工是通过加热和机械力的作用,改变金属原始形状并获得所需形状的一种加工方法。
其加工精度通常为0.2mm至0.5mm之间。
7.激光加工:
激光加工是利用激光束对工件进行切割、焊接等加工的方法。
其加工精度通常可以达到0.01mm级别。
常用加工精度对照表
常用加工方法与达到粗糙度对比图表粗、半精加工精加工精细加工外圆、端面、内孔(金属、非金属)孔加工方案与经济公差序号加工方案经济公差等级表面粗糙度Ra(μm)适用范围1钻IT11-1320加工未淬火钢及铸铁的实心毛坯,也可用于加工有色金属(表面粗糙度稍差),孔径<(15-20)mm 2钻-铰IT8-9 5.0-2.53钻-粗铰-精铰IT7-8 2.5-1.254钻-扩IT1120-10.0同上,但孔径>(15-20)mm5钻-扩-铰IT8-9 5.0-2.56钻-扩-粗铰-精铰IT7 2.5-1.257钻-扩-机铰-手铰IT6-70.63-0.1608钻-(扩)-拉IT6-7 2.5-0.160大批大量生产(精度视)9粗镗(或扩孔)IT11-1320-10.0除淬火钢外各种材料,毛坯有铸出孔或锻出孔10粗镗(粗扩)-半精镗(精扩)IT8-9 5.0-2.511粗镗(扩)-半精镗(精扩)-精镗(铰)IT7-8 2.5-1.2512粗镗(扩)-半精镗(精扩)-精镗-浮动镗刀块精镗IT6-7 1.25-0.6313粗镗(扩)-半精镗-磨孔IT7-8 1.25-0.32主要用于加工淬火钢,也可用于不淬火钢,但不宜用于有色金属14粗镗(扩)-半精镗-粗磨-精磨IT6-70.32-0.16015粗镗-半精镗-精镗-金刚镗IT6-70.63-0.080主要用于精度要求较高的有色金属加工16钻-(扩)-粗铰-精铰-珩磨钻-(扩)-拉-珩磨粗镗-半精镗-精镗-珩磨IT6-70.32-0.040精度要求很高的孔17以研磨代替上述方案的珩磨IT6以上0.160-0.010平面加工方案与经济公差序号加工方案经济公差等级表面粗糙度Ra(μm)适用范围1粗车-半精车IT8-910-5.0端面2粗车-半精车-精车IT6-7 2.5-1.53粗车-半精车-磨削IT7-9 1.25-0.324粗刨(或粗铣)-精刨(或精铣)IT7-910.0-2.5一般不淬硬平面(端铣的表面粗糙度较好)5粗刨(或粗铣)-精刨(或精铣)-括研IT5-6 1.25-0.160精度要求较高的不淬硬平面批量较大时宜采用宽刃精刨方案6粗刨(或粗铣)-精刨(或精铣)-宽刃精刨IT6 1.25-0.327粗刨(或粗铣)-精刨(或精铣)-磨削IT6 1.25-0.32精度要求较高的淬硬平面或不淬硬平面8粗刨(或粗铣)-精刨(或精铣)-粗磨-精磨IT5-60.63-0.0409粗铣-拉IT6-9 1.25-0.32大量生产,较小的平面(精度视拉刀的精度而定)10粗铣-精铣-磨削-研磨IT5以上高精度平面外圆表面加工方案与经济公差序号加工方案经济公差等级表面粗糙度Ra(μm)适用范围1.粗车IT11-1380-20适用于淬火钢外的各种金属2.粗车-半精车IT8-910.0-5.03.粗车-半精车-精车IT6-7 2.5-1.254.粗车-半精车-精车-滚压(或抛光)IT6-70.32-0.0405.粗车-半精车-磨削IT6-7 1.25-0.63主要用于淬火钢,也可用于未淬火钢,但不宜加工有色金属6.粗车-半精车-粗磨-精磨IT5-60.63-0.1607.粗车-半精车-粗磨-精磨-超精加工(或轮式超精磨)IT50.160-0.0208.粗车-半精车-精车-金刚石车IT5-60.63-0.040主要用于要求较高的有色金属的加工9.粗车-半精车-粗磨-精磨-超精磨或镜面磨IT5以上0.040-0.010极高精度的外圆加工10.粗车-半精车-粗磨-精磨-研磨IT5以上0.160-0.010各种毛坯表面层厚度(mm)自由锻件模锻件铸件磁钢≤1.5磁钢≤1灰口铸铁1-4合金钢2-4合金钢≤0.5铸钢2-5。
各种加工方法表面光洁度
1、一般车床的加工精度可达IT8~IT7,表面粗糙度为Ra25~Ra1.6.2、钻床用于钻孔加工精度可达IT13~IT11,表面粗糙度Ra80~Ra20;用于扩孔精度达IT10,表面粗糙度Ra10~Ra5.;用于铰孔精度可达IT7,表面粗糙度Ra5~ra1.25。
3、铣床加工精度一般为IT9~IT8,表面粗糙度为Ra6.3~Ra1.6.4、刨床加工精度为IT9~IT8,表面粗糙度为Ra25~Ra1.6.5、磨床加工精度一般为IT6~IT5,表面粗糙度为Ra0.8~Ra0.1.0.012—花△13(为最精确)0.025—花△120.05—花△110.1—花△100.2—花△90.4—花△80.8—花△71.6—花△63.2—花△56.3—花△412.5—花△325—花△250—花△1100—花△0(为最粗糙)中国与美国的表面粗糙度(光洁度)对照表表面粗糙度有Ra,Rz,Ry 之分,据GB 3505摘录:表面粗糙度参数及其数值(Surface Roughness Parameters and their Values)常用的3个分别是:轮廓算数平均偏差(Ra)--arithmetical mean deviation of the profile;微观不平度十点高度(Rz)--the point height of irregularities;轮廓最大高度(Ry)--maximum height of the profile。
Ra--在取样长度L内轮廓偏距绝对值的算术平均值。
Rz--在取样长度内5个最大的轮廓峰高的平均值与5个最大的轮廓谷深的平均值之和。
Ry--在取样长度L内轮廓峰顶线和轮廓谷底线之间的距离。
如果图面没标注粗糙度选用Ra /Rz /Ry 的情况下默认为Ra。
中美表面粗糙度(光洁度)对照表中国旧标准 ( 光洁度 ) 中国新标准 (粗糙度)Ra 美国标准 (微米)Ra 美国标准(微英寸)Ra▽ 4 6.3 8.00 3206.30 250▽ 5 3.2 5.00 2004.00 1603.20 125▽ 6 1.6 2.50 1002.00 801.60 63▽ 7 0.8 1.25 501.00 400.80 32▽ 8 0.4 0.63 250.50 200.40 16表面粗糙度是指加工表面具有的较小间距和微小峰谷不平度。
- 1、下载文档前请自行甄别文档内容的完整性,平台不提供额外的编辑、内容补充、找答案等附加服务。
- 2、"仅部分预览"的文档,不可在线预览部分如存在完整性等问题,可反馈申请退款(可完整预览的文档不适用该条件!)。
- 3、如文档侵犯您的权益,请联系客服反馈,我们会尽快为您处理(人工客服工作时间:9:00-18:30)。
各种加工方法的加工精度Company number:【WTUT-WT88Y-W8BBGB-BWYTT-19998】各种加工方法的加工精度一:车削车削中工件旋转,形成主切削运动。
刀具沿平行旋转轴线运动时,就形成内、外园柱面。
刀具沿与轴线相交的斜线运动,就形成锥面。
仿形车床或数控车床上,可以控制刀具沿着一条曲线进给,则形成一特定的旋转曲面。
采用成型车刀,横向进给时,也可加工出旋转曲面来。
车削还可以加工螺纹面、端平面及偏心轴等。
车削加工精度一般为IT8—IT7,表面粗糙度为—μm。
精车时,可达IT6—IT5,粗糙度可达—μm。
车削的生产率较高,切削过程比较平稳,刀具较简单。
二:铣削主切削运动是刀具的旋转。
卧铣时,平面的形成是由铣刀的外园面上的刃形成的。
立铣时,平面是由铣刀的端面刃形成的。
提高铣刀的转速可以获得较高的切削速度,因此生产率较高。
但由于铣刀刀齿的切入、切出,形成冲击,切削过程容易产生振动,因而限制了表面质量的提高。
这种冲击,也加剧了刀具的磨损和破损,往往导致硬质合金刀片的碎裂。
在切离工件的一般时间内,可以得到一定冷却,因此散热条件较好。
按照铣削时主运动速度方向与工件进给方向的相同或相反,又分为顺铣和逆铣。
顺铣铣削力的水平分力与工件的进给方向相同,工件台进给丝杠与固定螺母之间一般有间隙存在,因此切削力容易引起工件和工作台一起向前窜动,使进给量突然增大,引起打刀。
在铣削铸件或锻件等表面有硬度的工件时,顺铣刀齿首先接触工件硬皮,加剧了铣刀的磨损。
逆铣可以避免顺铣时发生的窜动现象。
逆铣时,切削厚度从零开始逐渐增大,因而刀刃开始经历了一段在切削硬化的已加工表面上挤压滑行的阶段,加速了刀具的磨损。
同时,逆铣时,铣削力将工件上抬,易引起振动,这是逆铣的不利之处。
铣削的加工精度一般可达IT8—IT7,表面粗糙度为—μm。
普通铣削一般只能加工平面,用成形铣刀也可以加工出固定的曲面。
数控铣床可以用软件通过数控系统控制几个轴按一定关系联动,铣出复杂曲面来,这时一般采用球头铣刀。
数控铣床对加工叶轮机械的叶片、模具的模芯和型腔等形状复杂的工件,具有特别重要的意义。
三:刨削刨削时,刀具的往复直线运动为切削主运动。
因此,刨削速度不可能太高,生产率较低。
刨削比铣削平稳,其加工精度一般可达IT8—IT7,表面粗糙度为—μm,精刨平面度可达1000,表面粗糙度为—μm。
四:磨削磨削以砂轮或其它磨具对工件进行加工,其主运动是砂轮的旋转。
砂轮的磨削过程实际上是磨粒对工件表面的切削、刻削和滑擦三种作用的综合效应。
磨削中,磨粒本身也由尖锐逐渐磨钝,使切削作用变差,切削力变大。
当切削力超过粘合剂强度时,圆钝的磨粒脱落,露出一层新的磨粒,形成砂轮的“自锐性”。
但切屑和碎磨粒仍会将砂轮阻塞。
因而,磨削一定时间后,需用金刚石车刀等对砂轮进行修整。
磨削时,由于刀刃很多,所以加工时平稳、精度高。
磨床是精加工机床,磨削精度可达IT6—IT4,表面粗糙度Ra可达—μm,甚至可达—μm。
磨削的另一特点是可以对淬硬的金属材料进行加工。
因此,往往作为最终加工工序。
磨削时,产生热量大,需有充分的切削液进行冷却。
按功能不同,磨削还可分为外园磨、内孔磨、平磨等。
五:钻削与镗削在钻床上,用钻头旋转钻削孔,是孔加工的最常用方法。
钻削的加工精度较低,一般只能达到IT10,表面粗糙度一般为—μm,在钻削后常常采用扩孔和铰孔来进行半精加工和精加工。
扩孔采用扩孔钻,铰孔采用铰刀进行加工。
铰削加工精度一般为IT9—IT6,表面粗糙度为—μm。
扩孔、铰孔时,钻头、铰刀一般顺着原底孔的轴线,无法提高孔的位置精度。
镗孔可以较正孔的位置。
镗孔可在镗床上或车床上进行。
在镗床上镗孔时,镗刀基本与车刀相同,不同之处是工件不动,镗刀在旋转。
镗孔加工精度一般为IT9—IT7,表面粗糙度为—0.8mm。
钻削加工镗床加工车床加工六:齿面加工齿轮齿面加工方法可分为两大类:成形法和展成法。
成形法加工齿面所使用的机床一般为普通铣床,刀具为成形铣刀,需要两个简单成形运动:刀具的旋转运动和直线移动。
展成法加工齿面的常用机床有滚齿机、插齿机等。
七:复杂曲面加工三维曲面的切削加工,主要采用仿形铣和数控铣的方法或特种加工方法(见本节八)。
仿形铣必须有原型作为靠模。
加工中球头仿形头,一直以一定压力接触原型曲面。
仿形头的运动变换为电感量,加工放大控制铣床三个轴的运动,形成刀头沿曲面运动的轨迹。
铣刀多采用与仿形头等半径的球头铣刀。
数控技术的出现为曲面加工提供了更有效的方法。
在数控铣床或加工中心上加工时,是通过球头铣刀逐点按坐标值加工而成。
采用加工中心加工复杂曲面的优点是:加工中心上有刀库,配备几十把刀具。
曲面的粗、精加工,可用不同刀具对凹曲面的不同曲率半径,也可选用适当的刀具。
同时,可在一次安装中加工各种辅助表面,如孔、螺纹、槽等。
这样充分保证了各表面的相对位置精度。
八:特种加工特种加工方法是指区别于传统切削加工方法,利用化学、物理(电、声、光、热、磁)或电化学方法对工件材料进行加工的一系列加工方法的总称。
这些加工方法包括:化学加工(CHM)、电化学加工(ECM)、电化学机械加工(ECMM)、电火花加工(EDM)、电接触加工(RHM)、超声波加工(USM)、激光束加工(LBM)、离子束加工(IBM)、电子束加工(EBM)、等离子体加工(PAM)、电液加工(EHM)、磨料流加工(AFM)、磨料喷射加工(AJM)、液体喷射加工(HDM)及各类复合加工等。
分类原理原理示意特点应用范围电火花加工电火花加工是利用工具电极和工件电极间瞬时火花放电所产生的高温熔蚀工件表面材料来实现加工的。
电火花加工机床一般由脉冲电源、自动进给机构、机床本体及工作液循环过滤系统等部分组成。
工件固定在机床工作台上。
脉冲电源提供加工所需的能量,其两极分别接在工具电极与工件上。
当工具电极与工件在进给机构的驱动下在工作液中相互靠近时,极间电压击穿间隙而产生火花放电,释放大量的热。
工件表层吸收热量后达到很高的温度(10000℃以上),其局部材料因熔化甚至气化而被蚀除下来,形成一个微小的凹坑。
工作液循环过滤系统强迫清洁的工作液以一定的压力通过工具电极与工件之间的间隙,及时排除电蚀产物,并将电蚀产物从工作液中过滤出去。
多次放电的结果,工件表面产生大量凹坑。
工具电极在进给机构的驱动下不断下降,其轮廓形状便被“复印”到工件上(工具电极材料尽管也会被蚀除,但其速度远小于工件材料)。
用特殊形的电极工具加工相应工件的电火花成形加工机床————①加工硬、脆、韧、软和高熔点的导电材料;②加工半导体材料及非导电材料;③加工各种型孔、曲线孔和微小孔;④加工各种立体曲面型腔,如锻模、压铸模、塑料模的模膛;⑤用来进行切断、切割以及进行表面强化、刻写、打印铭牌和标记等。
用线电极加工二维轮廓形状工件的电火花线切割机床电解加工电解加工是利用金属在电解液中产生阳极溶解的电化学原理对工件进行成形加工的一种方法。
工件接直流电源正极,工具接负极,两极之间保持狭小间隙(0.1mm~0.8mm)。
具有一定压力~的电解液从两极间的间隙中高速15m/s~60m/s)流过。
当工具阴极向工件不断进给时,在面对阴极的工件表面上,金属材料按阴极型面的形状不断溶解,电解产物被高速电解液带走,于是工具型面的形状就相应地“复印”在工件上。
————①工作电压小,工作电流大;②以简单的进给运动一次加工出形状复杂的型面或型腔;③可加工难加工材料;④生产率较高,约为电火花加工的5~10倍;⑤加工中无机械切削力或切削热,适于易变形或薄壁零件的加工;⑥平均加工公差可达±0.1mm左右;⑦附属设备多,占地面积大,造价高;⑧电解液既腐蚀机床,又容易污染环境。
电解加工主要用于加工型孔、型腔、复杂型面、小直径深孔、膛线以及进行去毛刺、刻印等。
激光加工对工件的激光加工由激光加工机完成。
激光加工机通常由激光器、电源、光学系统和机械系统等组成。
激光器(常用的有固体激光器和气体激光器)把电能转变为光能,产生所需的激光束,经光学系统聚焦后,照射在工件上进行加工。
工件固定在三坐标精密工作台上,由数控系统控制和驱动,完成加工所需的进给运动。
①不需要加工工具;②激光束的功率密度很高,几乎对任何难加工的金属和非金属材料都可以加工;③激光加工是非接触加工,工件无受力变形;④激光打孔、切割的速度很高,加工部位周围的材料几乎不受切削热的影响,工件热变形很小。
⑤激光切割的切缝窄,切割边缘质量好。
激光加工已广泛用于金刚石拉丝模、钟表宝石轴承、发散式气冷冲片的多孔蒙皮、发动机喷油咀、航空发动机叶片等的小孔加工以及多种金属材料和非金属材料的切割加工。
超声波加工超声波加工是利用超声频(16KHz~25KHz)振动的工具端面冲击工作液中的悬浮磨料,由磨粒对工件表面撞击抛磨来实现对工件加工的一种方法。
超声发生器将工频交流电能转变为有一定功率输出的超声频电振荡,通过换能器将此超声频电振荡转变为超声机械振动,借助于振幅扩大棒把振动的位移幅值由0.005mm~0.01mm放大到~0.15mm,驱动工具振动。
工具端面在振动中冲击工作液中的悬浮磨粒,使其以很大的速度,不断地撞击、抛磨被加工表面,把加工区域的材料粉碎成很细的微粒后打击下来。
虽然每次打击下来的材料很少,但由于打击的频率高,仍有一定的加工速度。
由于工作液的循环流动,被打击下来的材料微粒被及时带走。
随着工具的逐渐伸入,其形状便“复印”在工件上。
——————————————在加工难切削材料时,常将超声振动与其它加工方法配合进行复合加工,如超声车削、超声磨削、超声电解加工、超声线切割等。
这些复合加工方法把两种甚至多种加工方法结合在一起,能起到取长补短的作用,使加工效率、加工精度及工件的表面质量显着提高。
九:加工方法的选择选择加工方法主要考虑零件表面形状、尺寸精度和位置精度要求、表面粗糙度要求,以及现有机床、刀具等资源情况、生产批量、生产率和经济技术分析等因素。
三.典型表面的加工路线(一)外圆表面的加工路线1.粗车→半精车→精车:应用最广,满足IT≥IT7,▽≥外圆可以加工2.粗车→半精车→粗磨→精磨:用于有淬火要求IT≥IT6,▽≥的黑色金属。
3.粗车→半精车→精车→金刚石车:用于有色金属、不宜采用磨削加工的外用表面。
4.粗车→半精车→粗磨→精磨→研磨、超精加工、砂带磨、镜面磨、或抛光在2的基础上进一步精加工。
目的为了减少粗糙度,提高尺寸精度,形状和位置精度。
(二)孔的加工路线1.钻→粗拉→精拉:用于大批大量生产盘套类零件的内孔,单键孔和花键孔加工,加工质量稳定,生产效率高。
2.钻→扩→铰→手铰:用于中小孔加工,扩孔前纠正位置精度,铰孔保证尺寸、形状精度和表面粗糙度。