基于有限元的疲劳设计分析系统MSC_FATIGUE_林晓斌
MscFatigue疲劳分析实例指导教程(2024)
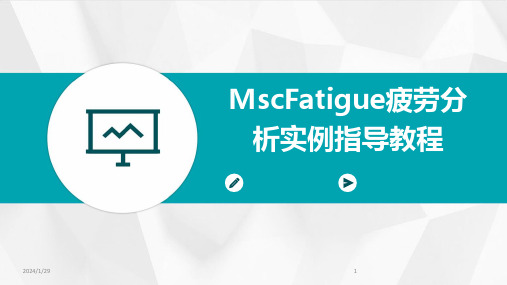
2024/1/29
8
MscFatigue软件介绍与操作
02
指南
2024/1/29
9
软件背景及功能特点
专注于疲劳分析
MscFatigue是一款专业的疲劳分析 软件,适用于各种材料和结构的疲劳
寿命预测。
高效的求解算法
采用先进的疲劳分析算法,能够快速 准确地完成复杂结构的疲劳寿命计算
。
2024/1/29
2024/1/29
求解流程
设置好模型后,即可进行求解。软件支持多种求解方法,如静态分析、模态分析、瞬态 分析等,可根据实际需求进行选择。求解完成后,可查看相应的结果文件。
12
结果查看、后处理及报告生成
结果查看
提供多种结果查看方式,如云图 、等值线、矢量图等,方便用户 直观了解疲劳分析结果。
后处理功能
剩余寿命预测
根据裂纹扩展速率和当前裂纹长度,预测结构的剩余寿命。
2024/1/29
结果分析
对裂纹扩展路径和剩余寿命进行综合分析,评估结构的疲劳性能 和安全性。
24
疲劳分析实例:焊接接头疲
05
劳性能评估
2024/1/29
25
问题描述与模型建立
问题描述:针对某一具体焊接接头,在 循环载荷作用下进行疲劳性能评估。
2024/1/29
复杂环境下的疲劳分析
研究高温、低温、腐蚀等复杂环境下的疲劳 问题,提高分析的实用性。
跨学科合作
加强与其他学科的交叉融合,共同推动疲劳 分析领域的发展。
35
2024/1/29
THANKS
感谢观看
36
损伤曲线
02
03
其他结果
输出构件的损伤曲线,了解构件 在不同循环次数下的损伤累积情 况。
虚拟疲劳分析软件DesignLife应用案例
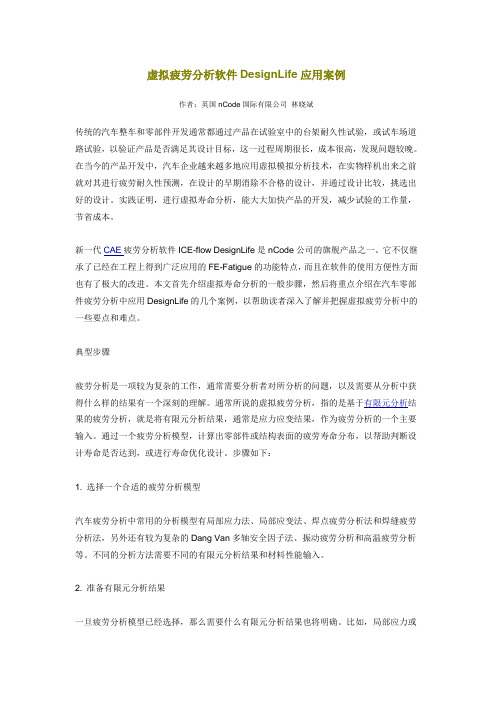
虚拟疲劳分析软件DesignLife应用案例作者:英国nCode国际有限公司林晓斌传统的汽车整车和零部件开发通常都通过产品在试验室中的台架耐久性试验,或试车场道路试验,以验证产品是否满足其设计目标,这一过程周期很长,成本很高,发现问题较晚。
在当今的产品开发中,汽车企业越来越多地应用虚拟模拟分析技术,在实物样机出来之前就对其进行疲劳耐久性预测,在设计的早期消除不合格的设计,并通过设计比较,挑选出好的设计。
实践证明,进行虚拟寿命分析,能大大加快产品的开发,减少试验的工作量,节省成本。
新一代CAE疲劳分析软件ICE-flow DesignLife是nCode公司的旗舰产品之一。
它不仅继承了已经在工程上得到广泛应用的FE-Fatigue的功能特点,而且在软件的使用方便性方面也有了极大的改进。
本文首先介绍虚拟寿命分析的一般步骤,然后将重点介绍在汽车零部件疲劳分析中应用DesignLife的几个案例,以帮助读者深入了解并把握虚拟疲劳分析中的一些要点和难点。
典型步骤疲劳分析是一项较为复杂的工作,通常需要分析者对所分析的问题,以及需要从分析中获得什么样的结果有一个深刻的理解。
通常所说的虚拟疲劳分析,指的是基于有限元分析结果的疲劳分析,就是将有限元分析结果,通常是应力应变结果,作为疲劳分析的一个主要输入。
通过一个疲劳分析模型,计算出零部件或结构表面的疲劳寿命分布,以帮助判断设计寿命是否达到,或进行寿命优化设计。
步骤如下:1. 选择一个合适的疲劳分析模型汽车疲劳分析中常用的分析模型有局部应力法、局部应变法、焊点疲劳分析法和焊缝疲劳分析法,另外还有较为复杂的Dang Van多轴安全因子法、振动疲劳分析和高温疲劳分析等。
不同的分析方法需要不同的有限元分析结果和材料性能输入。
2. 准备有限元分析结果一旦疲劳分析模型已经选择,那么需要什么有限元分析结果也将明确。
比如,局部应力或应变法通常需要应力结果,而焊点分析法则需要焊点单元的力和力矩。
一套完整的疲劳分析设计试验管理系统nSoft

一套完整的疲劳分析设计试验管理系统nSoft林晓斌 博士林晓斌 摘要 介绍了nCode 国际有限公司发展的一套完整的疲劳分析系统nSo ft 。
该系统专门为解决工程系统的疲劳问题而设计,主要由数据分析、数据显示、疲劳分析软件以及其它一些专门软件组成。
可用在数据采集、疲劳设计分析以及实验室疲劳模拟等部门。
关键词 疲劳分析 动态数据处理 工程设计 实验室模拟中国图书资料分类法分类号 T P202收稿日期:1998—09—03 nSo ft 是一个“由工程师为工程师设计”的工程疲劳分析系统,它的功能覆盖了工程抗疲劳设计分析的3个主要领域,即数据采集、疲劳分析以及实验室模拟,并将它们紧密地结合在一起,见图1。
nSoft 集现代疲劳理论、数据信号分析处理和最新的计算机技术于一体,为工程界提供了全套功能强大的抗疲劳设计工具。
图1 工程抗疲劳设计分析中的几个主要步骤1 nSoft 系统简介nSo ft 是由许多独立模块组成的一个开放系统。
每一模块可在计算机操作环境下独立启动,模块之间的传递主要通过数据文件实现。
可处理的数据文件长度没有限制。
nSoft 也有一个独特的管理界面,它可以帮助用户设置操作环境,记录所执行的命令,启动各个模块,查阅在线操作手册,阅读疲劳背景知识电子文件等,nSo ft 配有功能强大的、nCode 自己发展的命令语言nCL ,使用nCL 可以使得繁琐重复的工作自动化,并允许用户进行二次开发,发展出自己所需要的模块。
nSo ft 配置的报告编辑工具,可让用户获得满意的报告格式,并且也能很方便地将nSoft 产生的图形及结果记录文件复制到一般的图文编辑软件里去。
n Soft 当前能在多种操作平台上工作,如DOS 、微软视窗95/NT 、UNIX (SGI 、SPARC 、HP 、IBM )、X 和MOT IF 。
另外,为了帮助用户进图2行疲劳分析,nSoft 还配有丰富的材料性能、应力强度因子和应力集中因子数据库。
基于有限元的缸盖低周疲劳寿命仿真分析

基于有限元的缸盖低周疲劳寿命仿真分析杨林强;钱德猛;路明【摘要】The authors modify the coffin-manson model and analyze the machine model to get the temperature field and stress field distributions of the cylinder head through the finite element method. They use the means of sub-model for further analysis of the combustion chamber, make the simulation calculation of the low cycle fatigue life of the cylinder head combustion chamber under the engine typical working conditions, and find out the main influence factors.%对cofiin-manson模型进行修正,通过有限元的方法对整机模型进行分析,得到缸盖的温度场及应力场分布;运用子模型的方法进一步分析缸盖燃烧室部分,针对发动机的典型工况仿真分析缸盖燃烧室的低周疲劳寿命,并找出主要影响参数。
【期刊名称】《客车技术与研究》【年(卷),期】2015(000)003【总页数】3页(P1-3)【关键词】发动机缸盖;低周疲劳;有限元;coffin-manson模型【作者】杨林强;钱德猛;路明【作者单位】江淮汽车股份有限公司,合肥 230601;江淮汽车股份有限公司,合肥 230601;江淮汽车股份有限公司,合肥 230601【正文语种】中文【中图分类】U464.132缸盖作为发动机的核心零部件,是工作环境最恶劣的部件之一,承受着气体燃烧产生的高温。
多轴疲劳寿命工程预测方法_林晓斌
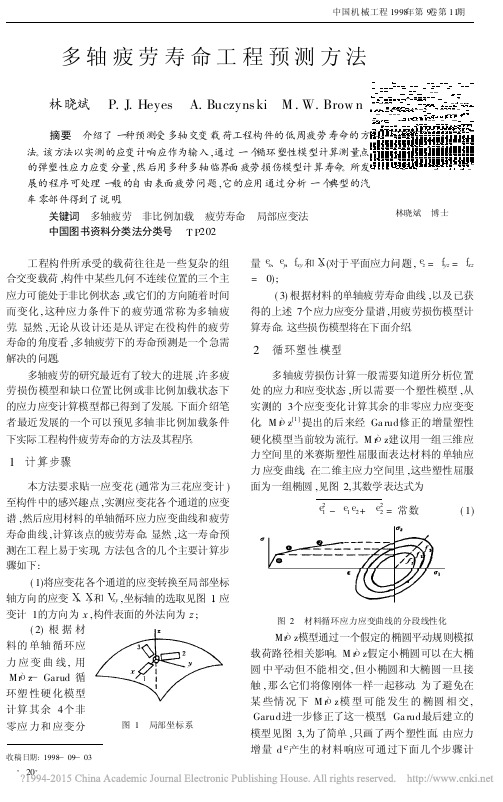
以发现有一 BC时间段。Wang和 Brow n认为 , AD
为一个历程 , 因为若跳过时间段 BC ,那么 AD 内 的等效应变从零一直增加到最大。从图 5b中得到
一个历程 AD 及两个时间段 BC和 D E ,它们至少
也包含一个以上历程。③ 计算相对于时刻 B 的等
效 相对应变 , 假定得到图 5c, 那么 BC 为一个历
3 多轴损伤模型
多轴损伤模型一般可分 3类: 第一类是静态屈 服理论在复杂应力状态下的延伸; 第二类是基于能 量的方法 ; 第三类是“临界面”法。临界面概念最早 为 Fi ndely [4 ]所提 , Findely 认为疲劳失效的主要原 因是临界剪切面上的交变剪应力 ,但垂直于该平面 的正应力对疲劳也有影响。随后 , M cdia rmi d[5 ]和 Brow n— Mi ller[6 ]进一步发展了这一概念 , 并根据 疲劳裂纹形成的机理进行了物理解释。他们从试验 中发现 ,在多轴交变载荷作用下所形成的典型裂纹 有两种 , Brow n和 Mi ller将这两种裂纹定义为 A 型和 B型 ,见图 4。 A型裂纹为沿着表面扩展的浅 长裂纹 ,而 B型裂纹则向深度方向扩展。
续 历程区间 (从起始点至终点 ) 中最大剪应变平
面上的最大正应变变化 ; S 为材料常数 ,可根据多
轴疲劳试验获得 ; V′为有效泊松比。
· 22·
等式的右边和考虑 Mo rrow 平均应力修正的 单轴应变寿命方程是一致的 ,其中的平均应力 en, mean 为最大剪应变平面上的平均法向应力。试验 表明 , 具有独 特历程计 数方法的 W ang— Brow n 模型对于比例或非比例加载条件下的几种材料具 有良好的相关性 。 [10 ]
与 表 面 呈 90°( A 型 裂 纹 )。 但 对 于 剪 应 变 和
ICEflow汽车疲劳耐久性工程解决方案
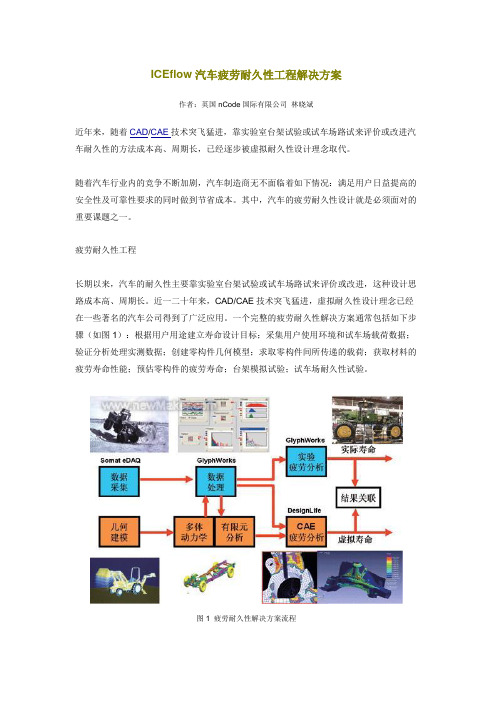
ICEflow汽车疲劳耐久性工程解决方案作者:英国nCode国际有限公司林晓斌近年来,随着CAD/CAE技术突飞猛进,靠实验室台架试验或试车场路试来评价或改进汽车耐久性的方法成本高、周期长,已经逐步被虚拟耐久性设计理念取代。
随着汽车行业内的竞争不断加剧,汽车制造商无不面临着如下情况:满足用户日益提高的安全性及可靠性要求的同时做到节省成本。
其中,汽车的疲劳耐久性设计就是必须面对的重要课题之一。
疲劳耐久性工程长期以来,汽车的耐久性主要靠实验室台架试验或试车场路试来评价或改进,这种设计思路成本高、周期长。
近一二十年来,CAD/CAE技术突飞猛进,虚拟耐久性设计理念已经在一些著名的汽车公司得到了广泛应用。
一个完整的疲劳耐久性解决方案通常包括如下步骤(如图1):根据用户用途建立寿命设计目标;采集用户使用环境和试车场载荷数据;验证分析处理实测数据;创建零构件几何模型;求取零构件间所传递的载荷;获取材料的疲劳寿命性能;预估零构件的疲劳寿命;台架模拟试验;试车场耐久性试验。
图1 疲劳耐久性解决方案流程ICE-flow的功能作为著名的疲劳耐久性技术服务公司之一的英国恩科(nCode)国际有限公司开发了一整套用于汽车耐久性设计、分析、试验及管理的硬件和软件工具——ICE-flow系列产品。
包括:数据采集器SomateDAQ、数据分析处理及实验疲劳软件GlyphWorks、CAE疲劳分析软件DesignLife和耐久性数据管理软件系统Library。
ICE-flow集工程数据采集分析处理、疲劳寿命分析模拟、实验室台架加速和远程数据传递及管理于一身,是进行一体化抗疲劳设计必备的一个分析工具,也是进行异地协同设计的有效工具。
ICE-flow系列产品如图2所示,以下对各功能分别进行介绍。
图2 ICE-flow系列产品1、数据采集道路载荷谱采集是疲劳耐久性设计的基础,我们需要调查用户的使用环境和用途,需要实测数据在实验室台架上做道路模拟试验,也需要为多体动力学分析、有限元分析以及疲劳寿命分析提供输入数据。
疲劳分析软件MSC Fatigue的工程应用

a r e c o mp l e t e d u s i n g t he r e a l me a s u r e d d y n a mi c l o a d a n d ma t e r i a l d a t a . Ap pl y i n g t he no mi na l s t r e s s me t h o d,t h e f a t i g ue l i f e c a l c u l a t i o n o f t h e c r o s s s u s t a i ni n g b a r ha s b e e n p e r f o r me d b a s e d o n MS C F a t i g u e, t h e r e s u l t o f f a t i ue g l i f e i s c o r r e s po n d e n t t o t he r e a l s e r v i c e l i f e .T he f a t i g u e a n a l y s i s me t h o d wi t h v i r t u a l f a t i g u e a n a l y s i s s o f t wa r e i s v e if r ie d,a n d i t p r o v i d e s r e f e r e n c e f o r t h e o p t i mu m d e s i g n a nd f a t i g u e l i f e
a n a l y s i s o n c r o s s s u s t a i n i n g b a r .
Ke y wor ds :c r o s s s us t a i n i f e;n o mi n a l s t r e s s me t h o d;l o a d s p e c t r um ;S— N c u r v e
基于有限元的疲劳分析方法及实践

基于有限元的疲劳分析方法及实践基于有限元的疲劳分析方法及实践疲劳是物体在循环荷载作用下发生的连续循环应力引起的损伤和破坏过程,对于工程结构的安全可靠性至关重要。
为了预测和评估结构在长期使用中的疲劳寿命,我们需要进行疲劳分析。
有限元方法是一种广泛应用的用于疲劳分析的数值模拟方法,它能够预测结构在不同应力循环下的寿命和破坏。
有限元方法基于结构的离散化,通过将结构划分为多个小单元来近似描述结构的力学行为。
在疲劳分析中,有限元方法可以应用于确定结构在复杂载荷历程下的应力和应变分布,并进一步评估结构的寿命。
下面将介绍有限元疲劳分析的基本步骤和实践经验。
首先,进行有限元模型建立。
有限元模型是指根据结构的几何形状和物性参数,以及实际工作条件建立的数值模型。
通过使用计算机辅助设计软件,我们可以将结构的几何形状进行精确建模,并定义结构中的材料参数和加载条件。
其次,确定结构的应力循环历程。
在实际工作中,结构往往会受到多种复杂的载荷作用,在疲劳分析中需要对这些载荷进行定量描述。
一般情况下,我们可以通过实验测量或者数值模拟来获取结构在不同工况下的应力循环历程。
接下来,进行疲劳寿命预测。
通过有限元分析软件,可以计算出结构在不同应力循环下的应力和应变分布。
利用经验公式或者材料的疲劳性能曲线,可以计算出结构在不同应力循环下的疲劳寿命。
疲劳寿命预测是疲劳分析的核心内容,它可以帮助工程师判断结构的安全性,进而进行优化设计。
最后,进行疲劳寿命验证。
在疲劳寿命预测的基础上,需要通过一定的实验验证来确定与有限元分析结果的一致性。
疲劳试验可以使用转子转速、台阶加载或实际工况加载等方法进行,通过实验可以验证有限元模型的准确性和可靠性。
对于疲劳分析的实践经验,有以下几点需要注意:1.准确建立有限元模型。
有限元模型的准确性关系到疲劳分析结果的可靠性。
在建模过程中,需要仔细考虑结构的几何形状、边界条件和材料参数等因素,确保模型与实际工程结构相匹配。
- 1、下载文档前请自行甄别文档内容的完整性,平台不提供额外的编辑、内容补充、找答案等附加服务。
- 2、"仅部分预览"的文档,不可在线预览部分如存在完整性等问题,可反馈申请退款(可完整预览的文档不适用该条件!)。
- 3、如文档侵犯您的权益,请联系客服反馈,我们会尽快为您处理(人工客服工作时间:9:00-18:30)。
3 Ba nnantine J A ,Co mer J J ,Handrock J L .Fundamentals o f M etal Fa tig ue Ana ly -sis.Pretice Hall,1990.4 鲍万年.机械强度有限寿命设计专家工作站配置的疲劳寿命预测和局部应变法.中国机械工程,1997,8(3):25~275 nCode Internatio na l Limited.The n Code Boo k o f Fa-tig ue Theo ry ,1997.6 林晓斌,Hey es P J .多轴疲劳寿命工程预测方法.中国机械工程,1998,9(11):20~237 Halfpenny A ,林晓斌.基于功率谱密度信号的疲劳寿命估计.中国机械工程,1998,9(11):16~198 Austen I M ,林晓斌.加速疲劳试验的疲劳编辑技术.中国机械工程,1998,9(11):27~309 Ensor D F ,林晓斌.关联用户用途的试车技术.中国机械工程,1998,9(11):24~28林晓斌 男,1963年生。
英国n Cod e 国际有限公司高级疲劳工程师、英国Sheffield 大学客座研究员。
1978~1990年在浙江大学学习工作,主要从事压力容器的安全性研究。
1994年获英国Sh effield 大学博士学位,接着做了近两年的博士后研究,在疲劳裂纹形状扩展研究领域取得了国际性领先成果。
1996年加入nCode,从事疲劳新技术的开发研究,已开发了多轴疲劳寿命分析工具。
当前的研究包括多轴疲劳、热机疲劳、疲劳裂纹形状扩展模拟、压力容器及管道的疲劳断裂等。
发表论文40篇。
基于有限元的疲劳设计分析系统M SC /FA TIGU EPete r J .Heyes 博士Peter J .Heyes 林晓斌译 摘要 简单描述了基于有限元分析结果进行疲劳寿命分析的思路,着重介绍了根据时域载荷输入计算构件内各点弹性应力应变响应的各种方法,以及从弹性应力应变结果近似计算弹塑性应力应变历史,并考虑多轴影响的各种途径;简单介绍了几种包含在M SC /FATIGUE 中的疲劳寿命计算方法及其各自的特点;总结了M SC /FA TIGU E 系统的功能和特点,并给出了一个转向节疲劳分析例子。
关键词 疲劳设计 有限元分析 计算机辅助工程中国图书资料分类法分类号 TP202 TB115 产品的疲劳寿命是现代设计的一个重要指标,因为随着市场竞争的日趋激烈,产品的寿命对用户来说显得愈来愈重要。
与传统的静强度设计相比,疲劳寿命设计需要了解产品的使用环境,应用现代疲劳理论,并结合试验验证,以确保所需要的设计寿命。
发达国家目前在产品设计中已大量使用计算机模拟技术,其中的有限元技术已经成为一种不可缺少的分析工具。
根据有限元获得的应力应变结果进行进一步的疲劳寿命设计已经在一些重要的工业领域(如汽车、航空航天和机器制造等)开始得到应用。
因为,与基于试验的传统方法相比,有限元疲劳计算能够提供零部件表面的疲劳寿命分布图,可以在设计阶段判断零部件的疲劳寿命薄弱位置,通过修改设计可以预先避免不合理的收稿日期:1998—09—03寿命分布。
因此,它能够减少试验样机的数量,缩短产品的开发周期,进而降低开发成本,提高市场竞争力。
1 技术背景疲劳寿命计算需要知道载荷的变化历史、结构的几何参数,以及有关的材料性能参数或曲线,疲劳计算的简单流程图见本期第13页。
用有限元计算疲劳寿命通常分为两步:第一步是根据载荷和几何结构计算中的应力应变变化历史,对于一个实验工程构件,通常在多个位置同时承受不同的动态载荷,构件的几何形状也往往很复杂,计算这样一个动态应力应变响应,是有限元分析的主要任务。
一旦获得应力应变响应,结合材料性能参数,我们就可以应用不同的疲劳损伤模型进行寿命计算,这是第二步。
疲劳寿命的理论预测精度既依赖于应力应变响应的正确模·12·中国机械工程1998年第9卷第11期拟,也依赖于损伤模型的合理使用。
1.1 应力应变计算需要什么样的应力应变响应往往取决于使用哪一种疲劳损伤模型。
对于基于名义应力的寿命计算方法(S—N方法),弹性的应力应变响应即可满足需要;而基于局部应变的寿命计算方法却需要弹塑性应力应变结果。
一般来说,弹性应力应变变化可按下列几种方法计算:(1)准静态法[1] 这一方法适用于激励载荷频率远在所分析构件的任何自然(固有)频率之下。
这意味着任一时刻的应力状态可以通过线性叠加各个不同静态载荷的响应来模拟。
这一计算要求定义一组静态载荷,然后使用与之对应的实测的或分析的载荷谱,按下式进行弹性应力应变响应计算e ij,e(t)=∑k P k(t)e ij,e,kP k,FEA(1)式中,k为载荷序号;P k,FEA为所定义的第k种静态载荷;e ij,e,k为第k种载荷所引起的弹性应力; P k(t)为第k种载荷的动态谱;e i j,e(t)为叠加后的弹性应力谱。
M SC/FA TIGU E[2]采用了这样一种线性叠加法,用户可以定义多达100种载荷。
每个载荷谱允许有2×109个数据点。
(2)假如结构有动力响应 即结构的柔度相对较大,或者所施加的载荷频率相对接近于结构的自然频率,那么有可能通过模态或直接的瞬态分析预见应力响应。
因为实际载荷信号一般很长,有限元模型也很大,所以这一方法计算量往往惊人,这给实际应用这一方法带来了一定的困难。
(3)假如问题是动态的 且有一个确定的振动载荷,那么进行一个受迫的振动响应应力分析有可能处理这类问题。
应力响应结果可通过反傅立叶变换计算获得。
(4)假如载荷为一随机振动载荷(严格说来,是一个随机稳态高斯载荷) 那么根据载荷功率谱密度信号,用有限元计算应力范围功率谱密度分布,可能是一种比时域信号计算较为有效的方法。
疲劳寿命可以根据应力范围功率谱密度结果进行预测[3]。
弹塑性的应力应变计算更为复杂。
一种最为直接的方法是用弹塑性有限元进行分析,载荷以增量形式逐步施加到有限元模型上。
显然这种方法目前还难于实际应用,因为有限元分析所需要的计算量太大。
目前工程上常用的一种简便方法是先计算弹性应力应变响应,然后用近似修正法,如Neuber[4]规则或Glinka[5]所建议的方法,将弹性响应修正至弹塑性响应。
M SC/FATIGUE采用了Neuber修正方法。
当屈服程度不大时,Neu-ber方法能给出一个具有合理近似程度的应力应变重新分布结果;对于屈服程度较大的情况,它可能给出一个非保守的结果。
为了解决这一问题, Seeg er和Beste[6],Mertens和Dittma nn[7]对N euber方法进行了修正。
可是他们的方法都只适用于单轴应力状态,而实际构件表面的应力往往处于多轴状态。
Kla nn等人[8],Hoffmann和Seeg er[9]提出了两种考虑多轴应力状态的修正方法,适用于多轴比例加载。
M SC/FATIGU E已经包含了上面所提到的这些弹塑性修正方法,这些方法在文献[1]中已有总结。
1.2 疲劳寿命计算方法(1)名义应力寿命法 以材料或零部件的疲劳寿命曲线为基础,S-N方法用名义应力或局部应力预测实际构件的疲劳寿命,可以选择的应力参数有绝对值最大的主应力、带正符号的V on-Mises应力、带正负号的Tresca应力等。
损伤累积计算可使用常规的Palmg ren-Miner线性法则或Haibach方法(相对Miner法则),用户也可以自己定义Miner常数。
S-N方法能进行Good-ma n和Gerber平均应力修正,也能进行考虑表面加工和表面处理影响的寿命计算。
包含在M SC/ FATIGUE中的基于寿命或应力水平值的安全因子计算使得有限寿命设计更加直观和量化。
新版的M SC/FATIGU E将提供两种无限寿命设计方法。
它们分别由Dang Van[10,11]和M cDi-armid[12,13]所发展,可处理任意非比例多轴加载情况。
Da ng Van建议了“微应力”模型,而M cDi-armid却使用临界面概念。
M SC/FATIGUE中的应力寿命法还包括了英国BS7608焊缝分析标准,以及由德国LBF疲劳试验室发展的焊点疲劳寿命计算方法[14]。
(2)局部应变寿命法 这种方法的主要特点有,包括了Co ffin-Manso n-Basquin、M orro w和Sm oth-Wa tso n-Topper3种具有不同平均应力修正方法;缺口处的弹塑性应力应变计算模型有N euber、Mertens-Dittma nn和Seeg er-Beste,可用Ho ffmann-Seeg er和Klann-Tipton-Cordes方法进行多轴修正;可选择的等效应变参数有绝对值最大的主应变,带正负号的Vo n-Mises应变,带正负号的Tresca应变等;Miner损伤累积常数可以自已定义;可以进行寿命安全因子计算;在·13·基于有限元的疲劳设计分析系统M SC/F A T IGU E——Pe ter J.Heyes新版的M SC/FATIGU E中还包括多轴低周疲劳损伤模型,如Socie-Ba nna ntine[15]和Wa ng-Brow n[16,17]临界面方法。
(3)裂纹扩展计算方法 Paris最早提出的裂纹前沿应力强度因子范围ΔK和裂纹扩展速率d a/d N之间的经验关系是计算疲劳裂纹扩展寿命的基础。
M SC/FATIGU E要求用户提供有限元模型、相关的应力强度因子解、材料性能曲线以及载荷变化历史。
根据这些输入,它可以计算裂纹从某一个初始尺寸一直到构件失效(裂纹失稳)的载荷重复块数目(即寿命)。
因此,M SC/FA-TIGUE既可用于评定含裂纹构件中的安全性,也可用于“损伤容限”设计,使所设计的产品具有良好的抗疲劳性能。
裂纹扩展预估软件的主要特点:有一个丰富的应力强度因子数据库,包括一些表面裂纹和埋藏裂纹;配有丰富的裂纹扩展速率材料性能曲线;对载荷信号进行时间顺序雨流计数;基于有效应力强度因子范围的修正Paris公式进行逐周裂纹扩展模拟;使用了Kitagaw a-Takahashi的最小裂纹尺寸定义;裂纹扩展计算包括了门槛值及断裂韧性失效准则;能进行平均应力和平面应力修正;能模拟由于过载效应所引起的裂纹扩展延滞、闭合以及缺口效应;能模拟腐蚀环境中的裂纹扩展。
2 M SC/FA TIGU E软件框架及特点M SC/FA TIGU E通过有限元分析前后处理器M SC/PATRAN能和许多知名的商用有限元分析软件连接,如M SC/N AST RAN、ABAQ US、AN SYS和M ARC等。