价值流程图分析实例
3价值流程图范例

价值流程图(一) (改善前)
公式:①TT (日目标时间)=
②作业人数(n )= = 四舍五入
③加工时间(PT )=人工时间+机器时间-重叠时间 ④设备台数(m )= 加工时间÷加工批量÷目标时间
该工序总人工时
目标时间 每日投产时间
日目标量
⑤周期时间(CT )= 加工时间÷加工批量÷设备台数
⑥等待时间(WT )= 搬运批量×周期时间 ⑦停滞时间(ST )= 多余批量×周期时间
⑧生產交期 (LT) = 加工時間總和+等待時間總和+停滯時間總和
⑧附加价值V A(%)=
加工时间总和÷生產交期
价值流程图(一) (改善后)
公式:①TT (日目标时间)=
②作业人数(n )= = 四舍五入
③加工时间(PT )=人工时间+机器时间-重叠时间 ④设备台数(m )= 加工时间÷加工批量÷目标时间
该工序总人工时
目标时间 每日投产时间
日目标量
⑤周期时间(CT )= 加工时间÷加工批量÷设备台数 ⑥等待时间(WT )= 搬运批量×周期时间 ⑦停滞时间(ST )= 多余批量×周期时间
⑧生產交期 (LT) = 加工時間總和+等待時間總和+停滯時間總和
⑧附加价值V A(%)=
加工时间总和÷生產交期。
价值流程图
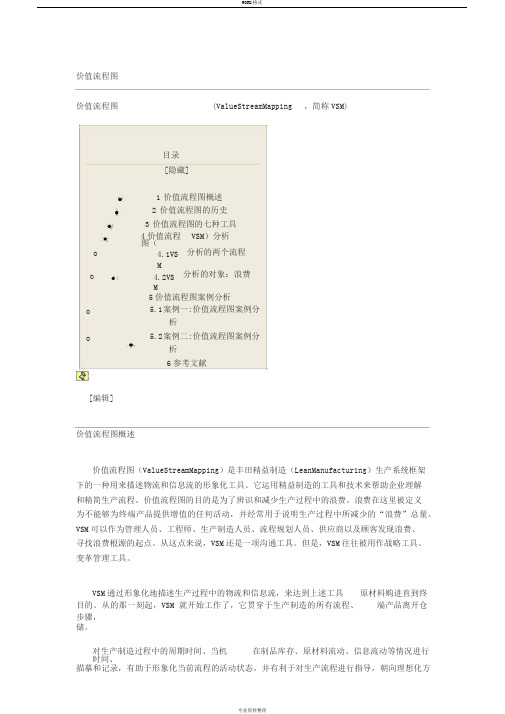
价值流程图价值流程图(ValueStreamMapping ,简称VSM)目录[隐藏]1价值流程图概述2价值流程图的历史3价值流程图的七种工具4价值流程图(VSM)分析o 4.1VSM分析的两个流程o 4.2VSM分析的对象:浪费5价值流程图案例分析o 5.1 案例一:价值流程图案例分析o 5.2 案例二:价值流程图案例分析6参考文献[编辑]价值流程图概述价值流程图(ValueStreamMapping)是丰田精益制造(LeanManufacturing)生产系统框架下的一种用来描述物流和信息流的形象化工具。
它运用精益制造的工具和技术来帮助企业理解和精简生产流程。
价值流程图的目的是为了辨识和减少生产过程中的浪费。
浪费在这里被定义为不能够为终端产品提供增值的任何活动,并经常用于说明生产过程中所减少的“浪费”总量。
VSM可以作为管理人员、工程师、生产制造人员、流程规划人员、供应商以及顾客发现浪费、寻找浪费根源的起点。
从这点来说,VSM还是一项沟通工具。
但是,VSM往往被用作战略工具、变革管理工具。
VSM通过形象化地描述生产过程中的物流和信息流,来达到上述工具目的。
从的那一刻起,VSM就开始工作了,它贯穿于生产制造的所有流程、步骤,原材料购进直到终端产品离开仓储。
对生产制造过程中的周期时间、当机时间、在制品库存、原材料流动、信息流动等情况进行描摹和记录,有助于形象化当前流程的活动状态,并有利于对生产流程进行指导,朝向理想化方向发展。
VSM通常包括对“当前状态”和“未来状态”两个状态的描摹,从而作为精益制造战略的基础。
价值流程图(VSM)分析的是两个流程:第一个是信息(情报)流程,即从市场部接到客户订单或市场部预测客户的需求开始,到使之变成采购计划和生产计划的过程;第二个是实物流程,即从供应商供应原材料入库开始,随后出库制造、成品入库、产品出库,直至产品送达客户手中的过程。
此外,实物流程中还包括产品的检验、停放等环节。
2024版价值流程图VSM案例分析PPT课件

价值流程图VSM案例分析PPT课件目录•引言•案例分析:某制造企业生产流程优化•案例分析:某电商平台订单处理流程改进•案例分析:某医院患者就诊流程优化•总结与展望01引言提高生产效率降低成本提升产品质量目的和背景通过价值流程图VSM分析,识别生产过程中的浪费环节,优化生产流程,提高生产效率。
减少生产过程中的非增值活动,降低生产成本,提高企业竞争力。
通过价值流程图VSM分析,发现生产过程中的问题点,改进生产工艺,提升产品质量。
价值流程图VSM简介定义价值流程图VSM是一种可视化工具,用于描述产品或服务的整个价值流,包括从原材料到最终产品或服务的所有活动。
作用帮助企业识别生产过程中的浪费环节,优化生产流程,提高生产效率和质量。
适用范围适用于制造业、服务业等各个领域的企业。
02案例分析:某制造企业生产流程优化当前生产流程存在过多的环节和等待时间,导致生产效率低下。
生产流程繁琐资源浪费严重质量问题突出生产过程中的物料、人力和时间等资源未能得到充分利用,造成资源浪费。
产品质量不稳定,客户投诉率高,影响企业声誉和市场竞争力。
030201企业现状及问题分析深入企业生产现场,全面了解现有生产流程、设备、人员配置等情况。
流程调研收集生产过程中的关键数据,如生产周期、在制品数量、设备利用率等。
数据收集基于调研和收集的数据,绘制价值流程图VSM ,直观展示生产过程中的价值流动情况。
VSM 绘制价值流程图VSM 构建识别并消除生产过程中的浪费环节,如减少等待时间、降低库存等。
消除浪费优化生产流程,合并或取消不必要的环节,提高生产效率。
简化流程加强产品质量控制,采用先进的质量管理方法和技术手段,提高产品质量稳定性。
强化质量控制生产流程优化方案设计01020304生产效率提升资源利用率提高产品质量改善企业竞争力增强实施效果评估通过优化生产流程,提高生产效率,缩短生产周期。
充分利用物料、人力和时间等资源,降低生产成本。
通过生产流程优化,提高企业市场竞争力,实现可持续发展。
价值流程图
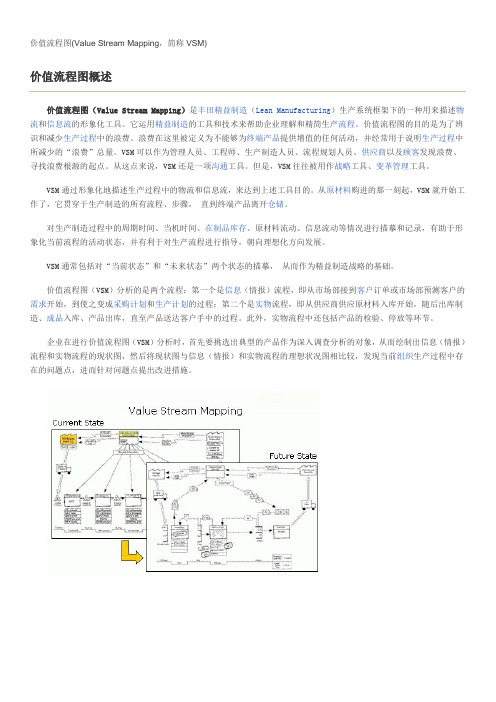
价值流程图(Value Stream Mapping,简称VSM)价值流程图概述价值流程图(Value Stream Mapping)是丰田精益制造(Lean Manufacturing)生产系统框架下的一种用来描述物流和信息流的形象化工具。
它运用精益制造的工具和技术来帮助企业理解和精简生产流程。
价值流程图的目的是为了辨识和减少生产过程中的浪费。
浪费在这里被定义为不能够为终端产品提供增值的任何活动,并经常用于说明生产过程中所减少的“浪费”总量。
VSM可以作为管理人员、工程师、生产制造人员、流程规划人员、供应商以及顾客发现浪费、寻找浪费根源的起点。
从这点来说,VSM还是一项沟通工具。
但是,VSM往往被用作战略工具、变革管理工具。
VSM通过形象化地描述生产过程中的物流和信息流,来达到上述工具目的。
从原材料购进的那一刻起,VSM就开始工作了,它贯穿于生产制造的所有流程、步骤,直到终端产品离开仓储。
对生产制造过程中的周期时间、当机时间、在制品库存、原材料流动、信息流动等情况进行描摹和记录,有助于形象化当前流程的活动状态,并有利于对生产流程进行指导,朝向理想化方向发展。
VSM通常包括对“当前状态”和“未来状态”两个状态的描摹,从而作为精益制造战略的基础。
价值流程图(VSM)分析的是两个流程:第一个是信息(情报)流程,即从市场部接到客户订单或市场部预测客户的需求开始,到使之变成采购计划和生产计划的过程;第二个是实物流程,即从供应商供应原材料入库开始,随后出库制造、成品入库、产品出库,直至产品送达客户手中的过程。
此外,实物流程中还包括产品的检验、停放等环节。
企业在进行价值流程图(VSM)分析时,首先要挑选出典型的产品作为深入调查分析的对象,从而绘制出信息(情报)流程和实物流程的现状图,然后将现状图与信息(情报)和实物流程的理想状况图相比较,发现当前组织生产过程中存在的问题点,进而针对问题点提出改进措施。
价值流程图的历史1980年代,丰田公司的首席工程师Taiichi Ohno与sensei Shigeo Shingo率先运用去除生产浪费的方法来获取竞争优势,他们的主要出发点是提高生产效率,而非提高产品质量。
价值流程图【范本模板】
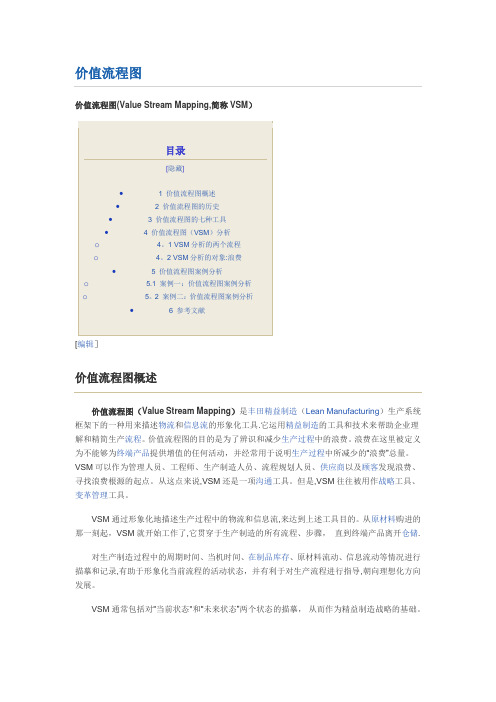
价值流程图价值流程图(Value Stream Mapping,简称VSM)[编辑]价值流程图概述价值流程图(Value Stream Mapping)是丰田精益制造(Lean Manufacturing)生产系统框架下的一种用来描述物流和信息流的形象化工具.它运用精益制造的工具和技术来帮助企业理解和精简生产流程。
价值流程图的目的是为了辨识和减少生产过程中的浪费。
浪费在这里被定义为不能够为终端产品提供增值的任何活动,并经常用于说明生产过程中所减少的“浪费”总量。
VSM可以作为管理人员、工程师、生产制造人员、流程规划人员、供应商以及顾客发现浪费、寻找浪费根源的起点。
从这点来说,VSM还是一项沟通工具。
但是,VSM往往被用作战略工具、变革管理工具。
VSM通过形象化地描述生产过程中的物流和信息流,来达到上述工具目的。
从原材料购进的那一刻起,VSM就开始工作了,它贯穿于生产制造的所有流程、步骤,直到终端产品离开仓储.对生产制造过程中的周期时间、当机时间、在制品库存、原材料流动、信息流动等情况进行描摹和记录,有助于形象化当前流程的活动状态,并有利于对生产流程进行指导,朝向理想化方向发展。
VSM通常包括对“当前状态"和“未来状态”两个状态的描摹,从而作为精益制造战略的基础。
价值流程图(VSM)分析的是两个流程:第一个是信息(情报)流程,即从市场部接到客户订单或市场部预测客户的需求开始,到使之变成采购计划和生产计划的过程;第二个是实物流程,即从供应商供应原材料入库开始,随后出库制造、成品入库、产品出库,直至产品送达客户手中的过程。
此外,实物流程中还包括产品的检验、停放等环节。
企业在进行价值流程图(VSM)分析时,首先要挑选出典型的产品作为深入调查分析的对象,从而绘制出信息(情报)流程和实物流程的现状图,然后将现状图与信息(情报)和实物流程的理想状况图相比较,发现当前组织生产过程中存在的问题点,进而针对问题点提出改进措施。
价值流程图绘制方法(精益生产)

对工作流程进行优化,消除浪费,提高生产效率。
引入新技术
引入新技术和设备,提高生产过程的自动化和智能化水平。
培养员工的价值流意识与能力
培训员工
对员工进行价值流相关培训,提高其对价值流 的认识和理解。
鼓励员工参与
鼓励员工参与到价值流改进过程中,发挥其主 动性和创造性。
建立激励机制
建立激励机制,对在价值流改进中做出贡献的员工给予奖励和表彰。
05
价值流程图的持续改进
定期审查与更新价值流程图
定期审查
价值流程图绘制完成后,应定期进行审 查,以确保其与实际生产过程保持一致 。
VS
更新价值流程图
随着生产过程的改进和变化,价值流程图 也应随之更新,以反映最新的生产状况。
持续改进的策略与方法
识别瓶颈
通过价值流程图,识别生产过程中的瓶颈,并制定相应的改进措 施。
非价值流
描述生产过程的原材料、组件、 信息和能源的来源。
描述生产过程中的浪费环节,如 等待、库存、搬运、重复作业等。
价值流程图的作用
识别生产过程中的浪费
提高生产效率
通过绘制价值流程图,企业可以清晰地看 到生产过程中的浪费环节,从而有针对性 地采取措施消除浪费。
价值流程图可以帮助企业优化生产流程, 减少不必要的环节和等待时间,提高生产 效率。
增强了企业的竞争力。
THANK YOU
服务流程梳理
利用价值流程图对服务流程进行全面梳理,包括客户需求、服务 提供、售后支持等环节。
服务效率提升
基于价值流程图的分析结果,优化服务提供方式,提高服务效率和 质量。
服务创新
通过价值流程图发现服务中的瓶颈和浪费,实施服务创新,如开发 新的服务项目、优化服务流程等。
精益生产-价值流程图分析及设计
为什么要研究价值流
从这里开始
客户至上 贡献为本
价值流的层次
加工工序层次
单个工厂(车间)
多个工厂(车 间)
跨公司(建 造精益生产
的链)
江苏爱康科技股份有限公司
为什么要研究价值流
价
值
流
图
包
价值流图
含
的
内
容
客户至上 贡献为本
• --按顺序表达各工序 不要暴露出包
含的子工序
• -- 同时画出分支工序
•4)记录工序(过程)所需的测量指标
• --将重要信息记录在过程方块图的下
面
• --注意使用合适的单位
•
江苏爱康科技股份有限公司
建立价值流程图的4个步骤 画出基本的生产过程
客户至上 贡献为本
江苏爱康科技股份有限公司
建立价值流程图的4个步骤
客户至上 贡献为本
添加原材料及成品的移 动路线
周一及 周四
1X 每日
江苏爱康科技股份有限公司
建立价值流程图的4个步骤
8 周的 预测
每周 传真
生产控制
MRP
建周计划
周一及 周四
添加信息流:
客户至上 贡献为本
90/60/30 预测
每日 订单
每日装运 计划
设立目标价 值流图
创建实施计 划
江苏爱康科技股份有限公司
建立价值流程图的4个步骤
客户至上 贡献为本
产品数据分析及产品族选定案例
产品系列 工序1
工序2
工序3
工序4
A
注塑
抛光
打孔
装配
B
注塑
打孔
价值流图的一个案例分析
一、 VSM及其应用方法:五月底去珠海参加了由美国顾问公司主导的为期5天的VSM Kaizen,让我对VSM的认识又加深了一层,在这里,我很愿意分三个部分来分享我对VSM的认识:一.什么是VSM?二.VSM的组成。
三.如何应用VSM,它的步骤与方法。
一.什么是VSMVSM是Value Stream Mapping的简称,通常译为:价值流程图,是丰田精益生产系统框架下的一种用来描述物流和信息流的形象化工具;是精益生产用来识别目前和未来的价值状况,寻求改善机会,设定改善方向和愿景以及行动计划的工具。
VSM运用精益生产的工具和技术来帮助企业理解和精简生产流程,它的目的是为了辨识和减少生产过程中的浪费。
VSM 往往被用作战略工具、变革管理工具。
从购进原材料的那一时刻,VSM就开始工作了,它贯穿于生产制造所有流程、步骤,直到终端产品离开仓储。
不仅如此,服务业亦可使用VSM进行改善活动。
二.VSM的组成VSM的基本构成有四大部分(无先后):1. 顾客部分。
顾客发出信息,可能是订单,新产品,等等;2. 公司系统部分。
可能是ERP, SAP任何系统,顾客信息进入公司系统;3. 供应商部分。
4. 内部物料流。
主要指产线部分,至少需要人机料(Man, Machine, Material)VSM关注的重点部分(有次序):1.原材料到成品整个制程、工艺上的信息;2.成品到顾客;3.关注信息流部分。
顾客—〉公司系统〈--供应商4.计算Lean Time, 同时包含VA(有价值),NVA(无价值)部分及VA R atio(有价值比例)。
VAM常用图标:三.VSM的应用(实战应用)要素:1. 职位功能交叉的团队成员。
确保管理层支持,至少需要采购物流经理,生产计划经理,生产经理,工艺经理等部门参加;2.确保参加组员受到良好的精益知识,VSM概念培训;3.最好3天全职参与改善。
开始要点:1.选择一个产品系列,具有订单量大而稳定的特点的系列产品;2.需要一个有执行力和领导力的小组领导;3.彻彻底底的开始,从原料进到成品出,所有工序都要关注到;4.同时关注物流和信息流。
价值流程图(VSM)案例分析ppt课件
3
二、价值流程图
价值流程图(Value Stream Mapping,VSM)是丰 田精益制造(Learn Manufacturing)生产系统框架下 的一种用来描述物流和信息流的形象化工具。目的是 为了辨识和减少生产过程中的浪费,并用于说明生产 过程中所减少的“浪费”总量。
目前生产中钻孔和检验工序生产能力得不到发挥,存在很大 浪费。因此,可以考虑减少一个作业者。因为钻孔和检验总共 用时35s+25s=60s,可以考虑将这两道工序合并。
同时,可以考虑采用流水线生产和拉式生产相结合的生产 和管理方式。因为这样不仅有利于减少在制品库存,缩短提前 期,也非常有利于对装配工位需求的响应。此外,由于定拍工 序粗车节拍为60s,采取拉式生产有利于为减少生产过多过早的浪 费。
20
设备布置也应作相应调整,具体布置如图所示
21
未来价值流程图
22
需要注意的是,由于钻孔、精车抛光、检验三道工序是2个 人在U形生产线中完成的,如采用逐兔式完成,因此每人115s完 成三道工序的生产即115s共完成两个工件的加工,同时粗车工 人120s完成两个毛坯加工,因此相当于U形生产线中57.5s完成 一个零件的加工。因此,图3-2中后面三道工序的加工周期标注 57.5s。
价值流程图
1
主要内容
一、价值流概念 二、价值流程图 三、价值流程图案例分析
2
一、价值流的概念
价值流是制造产品所需一切活动的总和,包含了增 值活动和不增值活动。
使用价值流分析意味着对全过程进行研究,而不 只是研究单个过程;改进全过程,而不是仅仅优化局 部。
据统计,增值活动约占企业生产和经营活动的5%, 不增值活动约占95%。因此,应在价值流中识别不增 值活动,通过持续不断地开展价值流改进,消除各种 浪费,降低成本。
价值流程图(VSM)案例分析27页PPT
价值流程图 价值流程图( Value stream mapping,WSM)是丰 田精益制造( Learn Manufacturing)生产系统框架 的一种用来描述物流和信息流的形象化工具。目的是 为了辨识和减少生产过程中的浪费,并用于说明生产 过程中所减少的“浪费”总量。 VSM对生产制造过程中的周期时间、待机时间、在 制品库存、原材料流动、信息流动等情况进行描摹和 记录,有助于形象化当前流程的活动状态,并有利于 对生产流程进行指导,朝向理想化方向发展。 VSM通常包括对“当前状态”和“未来状态”两 状态的描摹
价值流程图
主要容 价值流概念 二、价值流程图 三、价值流程图案例分析
、价值流的概念 价值流是制造产品所需一切活动的总和,包含了增 值活动和不增值活动。 使用价值流分析意味着对全过程进行研究,而不 只是研究单个过程;改进全过程,而不是仅仅优化局 部 据统计,增值活动约占企业生产和经营活动的5%, 不增值活动约占95%。因此,应在价值流中识别不增 值活动,通过持续不断地开展价值流改进,消除各种 浪费,降低成本。 价值流改进重点在于物流和信息流。
VSM分析的两个流程 第一个是信息流程,即从市场部接到客户订单或市场部预测 客户的需求开始,到使之变成采购计划和生产计划的过程 第二个是实物流程,即从供应商供应原材料入库开始,随后 出库制造、成品入库、产品出库,直至产品送达客户手中的过 程。此外,实物流程中还包括产品的检验、停放等环节。 企业在进行VSM分析时,首先要挑选出典型的产品作为深入 调查分析的对象,从而绘制出信息流程和实物流程的现状图, 然后将现状图与信息和实物流程的理想状况图相比较,发现当 前组织生产过程中存在的问题点,进而针对问题点提出改进措 施
ቤተ መጻሕፍቲ ባይዱ
- 1、下载文档前请自行甄别文档内容的完整性,平台不提供额外的编辑、内容补充、找答案等附加服务。
- 2、"仅部分预览"的文档,不可在线预览部分如存在完整性等问题,可反馈申请退款(可完整预览的文档不适用该条件!)。
- 3、如文档侵犯您的权益,请联系客服反馈,我们会尽快为您处理(人工客服工作时间:9:00-18:30)。
种钉
单位 Sec H/月 %
Sec sec
装配
信息 / / / 单位 Sec H/月 %
Sec sec
接线
信息 / / / 单位
Sec/次
套壳/测试
信息 / / / 单位 Sec/次 H/月 %
Sec sec
包装
单位 Sec/次 H/月 %
Sec sec
代号 C/O ADT ED TT CT BT PC UPH WE PY
名称 换线/模时间 异常停机时间 设备稼动率
代号 C/O ADT ED TT CT BT PC UPH WE PY
名称 换线/模时间 异常停机时间 设备稼动率
代号 C/O ADT ED TT CT BT PC UPH WE PY
名称 换线/模时间 异常停机时间 设备稼动率
代号 C/O ADT ED TT CT BT PC UPH WE PY
Sec/次
1
下工序
人
1220 M2
处理时间
N0.5
H/Lot
领料单
处理时间
N 0.7
7
H/Lot
ADT ED TT CT
H/月 %
Sec sec
客户订单节拍 714.3 单站作业时间 1200.0 瓶颈工序时间 单站人力配置 每小时产能 工作效率 产品良率 900 2
制程检验
8
车型 手推车 物料 距离 批次 面板 80 M 车型 物料 距离 批次 时间 频率 无
单位 % % % H Min Min % H H Min Min %
300 900 0.5 12 100 100
客户订单节拍 714.3 单站作业时间 瓶颈工序时间 单站人力配置 每小时产能 工作效率 产品良率
300
客户订单节拍 714.3 单站作业时间 1800 瓶颈工序时间 单站人力配置 每小时产能 工作效率 产品良率 900 2
客户订单节拍 714.3 单站作业时间 1500 瓶颈工序时间 单站人力配置 每小时产能 工作效率 产品良率 900 2
名称 换线/模时间 异常停机时间 设备稼动率
信息 / / /
代号 C/O ADT ED TT CT BT PC UPH WE PY
名称 换线/模时间 异常停机时间 设备稼动率
信息 / / /
单位 Sec/次 H/月 %
Sec sec
H/月 %
Sec sec
客户订单节拍 714.3 单站作业时间 瓶颈工序时间 单站人力配置 每小时产能 工作效率 产品良率
900
加工 完成 300
300
-
操纵箱
客户交货周期(计划生产需求) 7 714
cs(Sec)
10
检验时间
0.75 H/Lot H/Lot 人 % M2
N 搬运时间 N 人数 N 批退率
面积
N N0
1
0.1 10
9
N 68
0.5 0.5 0.5 1 10
Lot/天
库量
业时间
H/Lot 天 H/Lot 人 M2
WIP信息 pcs Sec/pcs QTY 数量 4 ### pcs Sec/pcs QTY 数量
WIP信息 4 ### pcs Sec/pcs QTY 数量
WIP信息 34 10,200 pcs Sec/pcs
Time 时间
Time 时间
Time 时间
Time 时间
Time 时间
7
0.7
6
15.2
滞时间
运时间
人数
面积
管控信息
9
13.0
10
0.8
代号 TED TGR FPY L/T PT: ∑ST LB IMF MF VAP NVAP UI
名称 设备综合嫁动率 总良率 一次直通率 订单周期时间 各工序总和时间 总工作时间 平衡率 信息流 物料流 增值加工 非增值加工 增值流利用率
信息 / 99 95 135 105.0 135 77.8 114 19 87.5 17.5 1.08
N 68
0.1
Lot/天
检验时间 停滞时间
打<工令单>
处理时间
N 0.5
处理时间
N 1.5
H/Lot
N
处理时间
N8
H/Lot
H/Lot
0.625 天 0.1 1
H/Lot
6
搬运时间 作业人数 批退率 面积
5
开<领料单>
3
2
做线
代号 C/O 名称 换线/模时间 异常停机时间 设备稼动率 信息 / / / 单位
sec 人
sec 人
sec 人
12 pcs 100 100 % %
2 pcs 100 100 % %
2.4 pcs 100 100 % %
4 pcs 100 95 % %
12 pcs 100 100 % %
WIP信息 QTY 数量 20 ### pcs Sec/pcs QTY 数量
WIP信息 20
#####
5
1.9
8
0.5
4
72.0
3
0.5
2
1.5
1
8.0
6,000 加工 完成 零件 运输
1,600
36,000 加工 完成 零件 运输 300 零件 运输
1,800
6,000 加工完 成 1,800 零件 运输
600
3,600 加工完 成 2,700 零件 运输
900
10,200 加工完 成 900 零件 运输
H/次
自制组合件
车型 手推车 纸箱 80 M
30 pcs/L
1,800
Sec
H/次
手推车 底盒 80 M
物料 距离 批次 时间 频率
2
60 pcs/L 900 8 Sec
H/次
入库量 作业时间 停滞时间 搬运时间 人数 面积
工单
批次 时间 频率
60 pcs/L 900 8 Sec
H/次
画面板
代号 C/O ADT ED TT CT BT PC UPH WE PY 名称 换线/模时间 异常停机时间 设备稼动率 信息
按钮、显示器
BT PC
sec 人
B
M
S S
先进先出
FIFO
车型 物料 距离 批次 时间 频率
手推车 预制线 40 M
OPH
3 pcs 100 100 % %
自制组合件
B B
车型 物料 距离
WE
S S
PY
20 pcs/L Sec
H/次
时间 0 pcs/L 600 3 Sec
客户订单节拍 714.3 单站作业时间 900.0 瓶颈工序时间 单站人力配置 每小时产能 工作效率 产品良率 900 1
客户订单节拍 714.3 单站作业时间 300.0 瓶颈工序时间 单站人力配置 每小时产能 工作效率 产品良率 420 1
sec 人 pcs % %
900 0.5
sec 人
sec 人
采购部
生产管理部
制造部
仓库
品质部 生产计划 采购计划 物料计划
大客户部
客户
零件 仓
入库量 作业时间 停滞时间 搬运时间 人数 面积
进料检验
N N 0.75
1 0.1 1 0.1 100 H/Lot H/Lot H/Lot 人 % M2
出货计划
处理时间
N72
H/Lot
采购单
物料请购
H/Lot
生产计划
4
杭州优迈科技有限公司
操 纵 箱 产线
我司每月计划工作日(天数) 22 我司每日工作时(H) 8 我司每日班次 (班/日)
价值流程图Value Stream Mapping(VSM)
机种名称:
订单流 L/T 客户订单量(P/O QTY:pcs) 887
XCP4操纵
1
供应商
客户产能需求TT/pcs(Sec