精馏过程节能技术综述
精馏过程节能技术综述

精馆过程节能技术综述石油化工是我国国民经济发展的支柱产业,据统计其能耗占全国工业总能耗的15%左右,而化工过程中40%〜70%的能耗用于分离,精镭能耗乂占其中的95%。
分离是非常重要的单元操作过程,是石油化工生产过程中必不可少的操作,它直接决定了最终产品的质量和收率,而精镭乂是占据着主导地位的分离方法,所以在当今世界能源日益短缺的情况下研究和探讨精镭过程的节能原理、节能技术,并使其应用于工业生产,就显得十分重要。
精谓是化工及燃油工业中的主要分离技术,技术成熟可幕,投资相对较低, 所以在石油化工生产过程中应用广泛,但现有精谓技术在热力学上是低效的耗能过程,有极高的热力学不可逆性,分离lkg产品所需能量(比能耗)相当高,所以寻找精憎工程中有效可行的节能途径显得至关重要。
通过对精镭塔传热过程的分析可以得到如下节能途径:优化操作条件、塔系的热集成技术、内部能量热集成以及加强操作控制管理。
优化操作条件精懈塔的主要操作条件包括操作压力、操作温度、塔板压降,进料位置及温度、理论板数、回流比以及回流温度、塔顶塔底采出量、关键组份的清晰分割程度,塔顶塔底热负荷,塔类型及填料类型等等。
下面从充分利用精憎系统的热能、减少对热负荷的需求和提高精镭系统热力学效率三方面进行介绍。
充分利用精憎系统的热能精谓系统中,所需的热量全部山加热蒸气经再沸器输人,分离后的余热山冷却介质从冷凝器移出。
若能合理利用精镭过程中本身的能量,就能降低整个过程对能量的需求。
可通过采取保温、热量回收、强化换热器以及夹点技术的措施来实现。
在精懈过程中使用的设备主要为精憎塔和换热器,同时还有各种管道,这些设备的材质导热系数较高,若对其釆取保温隔热的措施就可大大降低设备与环境之间的热传递作用,以达到节能降耗的目的。
高温物料携带大量热量可在塔外吸收利用,比如回收塔顶物料蒸气的潜热和回收塔釜废液的显热,使其用于工艺流程的其他需要加热的操作;使塔顶、塔釜物料与原料液进行换热,对原料液进行预热。
精馏过程节能技术综述

精馏过程节能技术综述现代工业生产过程中,精馏过程是十分常见的一种操作,用于从混合物中分离出不同组分。
然而,传统的精馏过程存在能源浪费的问题,因为它需要大量的能源来进行加热和冷却。
因此,如何降低精馏过程的能源消耗成为了一个重要的研究方向。
在过去的几十年里,研究人员提出了多种节能技术,以下综述了一些常见的节能技术。
首先,改进传统精馏塔的设计是一种简单但有效的节能方法。
例如,使用多级精馏塔可以增加分馏塔的效率,减少需加热和冷却的动力。
此外,增加塔内的换热面积也可以改善能量利用率。
此外,通过使用先进的塔内填料和分布器,可以提高物质的传质效率,从而减少所需的塔高和物料回流比例。
其次,热力耦合是另一种常用的节能技术。
该技术通过将不同温度的流体进行热交换,来降低能源消耗。
例如,实施热力耦合可以将进出精馏塔的气体进行热交换,从而降低所需的加热和冷却负荷。
此外,热力耦合还可以用于塔内热交换,例如通过使用塔内回流来预热进入精馏塔的物料。
另外,采用较低的工艺温度和压力也可以有效地减少精馏过程的能耗。
降低工艺温度可以减少所需的加热负荷,而降低工艺压力可以减少所需的冷却负荷。
因此,在设计和操作精馏过程时,应考虑选取较低的工艺温度和压力,以降低能源消耗。
此外,使用较低的辅助能源,如太阳能、余热等,也是一种常用的节能技术。
太阳能可以用于提供所需的加热或冷却能量,从而降低对传统能源的依赖。
余热是指在其他工艺过程中产生的废热,在精馏过程中可以被回收利用,用于提供所需的加热或冷却能源,进一步减少能源消耗。
最后,引入新的分离技术也是提高精馏过程能耗效率的一种途径。
例如,膜分离技术被广泛应用于分离混合物中的气体或液体组分,并且其能耗通常较低。
相比传统的蒸馏过程,膜分离技术不需要额外的加热和冷却能源,因此能够有效地节约能源。
总的来说,精馏过程节能技术的研究和应用对能源的合理利用具有重要意义。
通过改进传统精馏塔的设计、热力耦合、降低工艺温度和压力、使用低辅助能源和引入新的分离技术等方法,可以有效地降低精馏过程的能耗。
精馏过程的节能降耗

精馏过程的节能降耗精馏过程在化工产业中是一项重要的分离技术,但是它也是能耗较高的过程。
为了降低能耗,节能降耗已经成为精馏技术的一个重要研究方向。
本文将介绍几种精馏过程的节能降耗技术。
首先,提高精馏塔的热效率是提高精馏过程的一个关键。
一种常见的做法是引入换热器网络来最大程度地利用出塔冷凝液和进塔蒸汽之间的热量传递。
这种方法可以降低所需的蒸汽量,从而降低了能耗。
此外,还可以使用多效精馏、热泵或采用废热回收技术进一步提高热效率。
其次,提高精馏过程的物质效率也是节能降耗的一个重要途径。
物质效率是指在精馏过程中使用的干燥剂或者吸附剂能够更有效地去除杂质,从而减少能耗。
通过改进精馏塔的操作条件,如温度、压力和液体流速等参数,可以提高物质效率。
同时,使用高效的精馏填料或者塔板也能够提高分离效果,减少杂质的含量。
此外,使用先进的辅助技术可以进一步降低精馏过程的能耗。
例如,在精馏过程中引入膜分离技术可以减少能源消耗。
膜分离技术是一种基于材料表面或孔隙的选择性渗透性原理分离混合物的方法。
与传统的溶剂萃取或者蒸馏技术相比,膜分离技术具有能耗低、操作简单、体积小等优点。
通过将膜分离技术与精馏过程相结合,可以实现更高效的分离效果。
最后,优化精馏过程的操作策略也是节能降耗的一个重要途径。
通过优化参数设定和控制策略,可以使精馏过程更加稳定和高效。
例如,采用先进的控制算法,如模型预测控制或者模糊控制算法,可以实现对精馏过程的快速响应和精确控制,从而降低了能耗和运行成本。
总的来说,精馏过程的节能降耗是一个涉及多个方面的工程问题。
通过提高热效率、物质效率,使用先进的辅助技术和优化操作策略,可以有效地降低精馏过程的能耗。
这些节能降耗技术不仅可以减少环境污染,还可以提高精馏过程的经济效益。
因此,精馏过程的节能降耗在工业应用中具有重要的意义。
化工精馏高效节能技术的开发及应用
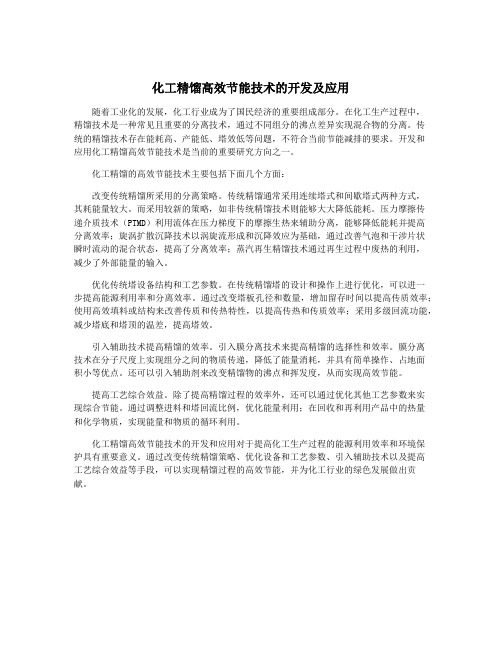
化工精馏高效节能技术的开发及应用随着工业化的发展,化工行业成为了国民经济的重要组成部分。
在化工生产过程中,精馏技术是一种常见且重要的分离技术,通过不同组分的沸点差异实现混合物的分离。
传统的精馏技术存在能耗高、产能低、塔效低等问题,不符合当前节能减排的要求。
开发和应用化工精馏高效节能技术是当前的重要研究方向之一。
化工精馏的高效节能技术主要包括下面几个方面:改变传统精馏所采用的分离策略。
传统精馏通常采用连续塔式和间歇塔式两种方式,其耗能量较大。
而采用较新的策略,如非传统精馏技术则能够大大降低能耗。
压力摩擦传递介质技术(PTMD)利用流体在压力梯度下的摩擦生热来辅助分离,能够降低能耗并提高分离效率;旋涡扩散沉降技术以涡旋流形成和沉降效应为基础,通过改善气泡和干涉片状瞬时流动的混合状态,提高了分离效率;蒸汽再生精馏技术通过再生过程中废热的利用,减少了外部能量的输入。
优化传统塔设备结构和工艺参数。
在传统精馏塔的设计和操作上进行优化,可以进一步提高能源利用率和分离效率。
通过改变塔板孔径和数量,增加留存时间以提高传质效率;使用高效填料或结构来改善传质和传热特性,以提高传热和传质效率;采用多级回流功能,减少塔底和塔顶的温差,提高塔效。
引入辅助技术提高精馏的效率。
引入膜分离技术来提高精馏的选择性和效率。
膜分离技术在分子尺度上实现组分之间的物质传递,降低了能量消耗,并具有简单操作、占地面积小等优点。
还可以引入辅助剂来改变精馏物的沸点和挥发度,从而实现高效节能。
提高工艺综合效益。
除了提高精馏过程的效率外,还可以通过优化其他工艺参数来实现综合节能。
通过调整进料和塔回流比例,优化能量利用;在回收和再利用产品中的热量和化学物质,实现能量和物质的循环利用。
化工精馏高效节能技术的开发和应用对于提高化工生产过程的能源利用效率和环境保护具有重要意义。
通过改变传统精馏策略、优化设备和工艺参数、引入辅助技术以及提高工艺综合效益等手段,可以实现精馏过程的高效节能,并为化工行业的绿色发展做出贡献。
化工精馏节能技术探讨

化工精馏节能技术探讨化工精馏是一种广泛的分离技术,广泛应用于炼油、化工、精细化工、制药等行业。
由于化工精馏的能耗和排放量较高,为了减少对环境的影响以及降低生产成本,探究化工精馏节能技术的应用显得十分重要。
一、精馏原理精馏是一种将混合物中的组分分离为一系列固定沸点组分的方法。
在一个精馏塔中,混合物在塔底蒸发后升往塔顶,通过多级板或者填料进一步蒸馏和分离。
不同沸点的组分会在不同的塔板或填料层凝结、液化分离出来。
经过多次分离,可以得到高纯度的分离产物。
二、节能措施1. 优化工艺参数通过客观分析和实验对化工精馏的工艺参数进行优化,可以达到节能的目的。
优化参数包括塔径、进料温度、进料速率、再沸点的选择等。
优化参数的主要目的是降低热量的损耗,提高再沸进料的回收,提高产品的纯度。
2. 应用热力学分析方法化工精馏通过热量供给来产生馏出性的分级蒸馏过程。
对于具有相同沸点的混合物,应用热力学分析方法来计算馏出程度,优化精馏条件,可达到节约热量、降低气体排放的目的。
3. 利用先进的装置技术采用先进的塔板、塔壳、填料技术,可以优化气液流动、充分利用热量,提高馏分的产量和质量。
例如,采用结构平面装置来提高塔顶的分馏效果,以及选用有效的填料来提高再沸孔的分馏效果等,都是有效的节能措施。
4. 优化回收系统采用高效的回收系统能够有效地提高化工精馏的再利用效益。
例如,实施热回收技术来回收热量和回收常温下的再沸馏分等都能达到节能的目的。
三、总结化工精馏在工业生产和人类生活中有着广泛的应用,同时其高耗能、高排放的特点也给环境带来了不小的影响。
为了减少对环境的影响,降低生产成本,我们需要探究化工精馏的节能降耗技术。
采取以上措施,能够有效地降低化工精馏的能耗和排放,提高生产效益,是企业可持续发展的重要措施。
精馏节能减耗总结

精馏节能减耗总结引言在许多化学工艺中,精馏作为一种常见的分离技术,广泛应用于石油化工、化学制药、能源等行业。
然而,传统的精馏过程存在能源消耗大的问题。
为了减少精馏过程中的能源消耗,提高能源利用率,许多节能减耗技术被引入并逐渐得到应用。
本文将对精馏节能减耗的相关技术进行总结,包括辅助加热装置、改进的精馏塔结构以及新型精馏塔填料等。
通过这些节能减耗技术的应用,精馏过程的能耗问题可以得到一定程度的改善,从而实现能源的可持续利用。
辅助加热装置传统的精馏过程中,常常需要大量的蒸汽或热能来提供塔底部的加热需求。
为了减少能源的消耗,引入一些辅助加热装置可以起到节能降耗的效果。
多效加热器多效加热器是一种高效的辅助加热装置,能够通过热传递的方式将高温废热回收利用。
其原理是在精馏塔的塔顶和塔底之间设置多级的加热器,利用顶部产生的低温蒸汽将底部的高温液体加热,从而实现能量的再利用。
热泵热泵是另一种常用的辅助加热装置,通过将低温的热能转移到高温区域,从而实现能量的传递和利用。
在精馏过程中,可以利用热泵将废热转化为可用的热能,供给精馏塔的加热需求。
这样不仅可以减少能源的消耗,还可以达到能源利用的最大化。
改进的精馏塔结构传统的精馏塔结构存在一些不利于能源节约的问题,如传质效率低、压力损失大等。
通过改进精馏塔的结构,可以减少能源的消耗,提高精馏效率。
塔板结构优化传统的精馏塔中,常见的结构是塔板结构,它的主要问题是传质效率低。
为了提高传质效率,可以引入一些新的塔板结构,如泡沫塔板、视窗塔板等。
这些新型塔板结构具有更大的表面积和更好的传质性能,能够有效地提高精馏效率,降低能源消耗。
塔内增加填料层除了改进塔板结构,也可以在精馏塔内部增加填料层,以增加界面面积,提高传质效果。
常见的填料包括金属填料、陶瓷填料、塑料填料等。
这些填料具有较大的表面积和较好的传质性能,能够增加相接触的机会,从而提高传质效率,减少能源消耗。
新型精馏塔填料塔填料作为精馏过程中的重要组成部分,对其传质效率和能源消耗有着直接的影响。
精馏过程节能技术综述
精馏过程节能技术综述摘要:精馏是化学工业中高能耗的操作单元,在当今能源紧缺的情况下, 对精馏过程的节能技术进行研究具有重要的社会意义和实际意义。
本文从精馏过程中热能的充分利用,提高精馏系统的热力学效率以及减少精馏过程对能量的需要这三大主要方面介绍了精馏过程的节能措施,对各个类型的主要节能方法、优缺点和适用范围进行了较为详细的叙述,并介绍了我国精馏过程节能技术的发展现状与趋势。
关键词:精馏节能前言:精馏过程是一个伴随传热和传质的复杂过程,被广泛应用于石油化工和精细化工等领域,是化学生产中主要的能源消耗环节,具有变量多、机理复杂等特点。
据相关资料统计,化工生产过程中有40%~70%的能耗用于分离过程,而精馏所消耗的能量就占据了其中的95%。
自从世界性的能源危机爆发以来,精馏过程的节能问题已经引起了人们的广泛重视。
因而降低精馏过程中的能耗,对于节约能源,降低生产成本有着至关重要的作用,本文就精馏过程中的节能措施进行了详细的介绍。
1.精馏过程节能技术现状:目前,随着化工生产中分离物料的组分不断增多,对产品纯度的要求也不断提高,但精馏装置操作往往偏于保守,操作方法、操作参数设置不尽合理。
典型的单级精馏装置中,混合物料从某一中间位置进入塔内,塔内设有塔板或填料促进汽液两相之间的相互接触,塔底液相在再沸器中被加热,塔顶的蒸汽在冷凝器中冷凝为馏出液。
在该精馏过程中所消耗的绝大部分能量被冷却水或分离组分带走,并非用于实际的组分分离,因此精馏过程的节能技术具有广阔的发展空间。
近年来,世界能源短缺状况加剧,各国对精馏节能技术的研究都很重视,以精馏过程节能技术为中心的研究和应用得到了飞速的发展。
据统计,我国的炼油厂消耗的原油占其炼油量的8%~10%,其中很大一部分消耗在了精馏过程中。
在现今能源资源紧缺的情况下,对精馏过程的节能研究就变得十分重要。
2. 充分利用精馏系统的热能:这类节能技术主要包括保温隔热,回收物料的部分显热或潜热,优化热交换器这三种方法。
精馏的节能技术
精馏作为化工、石化、医药、食 品、冶金等行业生产过程的重要单元 操作,其能耗约占化工生产的40%-70 %。
故采取措施降低蒸馏过程中的能 耗日益重要,成为研究的重点所在。
二、精馏节能技术介绍
精馏过程净功消耗的降低:
要使精馏过程的净功消耗降低,可以降低流体流动 过程产生的压力降,减小传热过程的温度差,减小传 质过程的两相浓度与平衡浓度的差别。
对于减压操作的塔, 纸然进一步降低操 作压力可减少回流比, 但减压下塔板效率降 低,节能效果不一定显著, 必须慎垂对待。
3、热能的充分利用
(1)热交换系统
精馏系统是由塔体和热交换器组成。在 再沸器、冷凝器、进料顶热器和成晶冷却 器系统中, 热交换器最佳化是节能的重要 环节, 因为它决定了热能是否得到充分利 用的问题。
(2)多效精馏系统
多效精馏系统是由 若干压力不同的精馏塔 构成,而且依据压力高 低的顺序,相邻两个塔 的高压塔塔顶蒸汽作用 为低压塔再沸器的热源, 换言之,高压塔塔顶蒸 汽的冷凝潜热均被精馏 系统自身回收利用,使 热能得到充分有效地利 用。
图4顺流和逆流三效工艺流程图
采用两效或多效精馏是充分利用能级 的一个方法。不论采用哪种方式,其精馏 操作所需的热量与单塔精馏相比较,都可 以减少30~40%。
选择最优操作压力,是 精馏系统节能的一项有力措 施。事实证明,在一定分离 精度要求下,对某些物系降 低精馏分离塔的操作压力, 可增加被分离各组分的相对 挥发度,从而减少回流比, 降低塔釜温度,尤以沸点相 近的物系,其节能效果更为 显著。
图3操作压力对气液 平衡的影响
脱甲烷塔在5~6kg/cm2压力下操作与 30~35kg/cm2压力下操作相比,回流比可下降 1/9~1/10,一个40万吨的乙烯装置,即可节 约压缩功率3600千瓦,而且投资也可减少。
化工精馏高效节能技术的开发及应用
化工精馏高效节能技术的开发及应用化工精馏是一种关键的工艺流程,通常用于分离混合物中的化学物质。
在化工过程中,精馏过程的能源消耗非常高,并且对生产率和资源利用效率产生了重要影响。
因此,开发和应用高效的精馏技术是化工工业的重要任务之一。
本文将探讨化工精馏高效节能技术的开发和应用。
一、精馏技术的常见问题精馏过程引起的能源消耗主要包括两个方面:蒸汽的需求和冷却水的需求。
目前,一些主要的精馏技术常见的问题如下:1. 能源消耗高。
由于大量的蒸汽和冷却水的需求,精馏过程的能源消耗非常高。
这导致成本增加,并且可能降低生产率。
2. 对环境的影响。
大量的能源消耗和排放对环境产生了负面的影响,包括温室气体排放和水消耗等。
3. 设备的维护和操作成本。
由于精馏设备经常需要定期维护和检修,因此这些成本也会对生产带来一定的影响。
为了提高精馏过程的效率和减少能源消耗,许多高效节能的精馏技术已经被研究和开发,其中包括以下几种。
1. 蒸汽回收技术蒸汽回收技术是通过回收已经使用的蒸汽,将其转化为高温高压蒸汽,从而降低热能的损失和能源消耗。
该技术可以在许多化工生产过程中实现节能,并且能够提高生产效率和产量。
例如,在石油炼制和化学合成过程中,蒸汽回收可以节省大量能源。
2. 热泵技术热泵技术通过利用高温低压的工艺余热或环境热源,提高压缩蒸汽的温度和压力,从而达到节能的效果。
热泵技术可以应用于各种类型的精馏过程中,包括蒸馏、萃取、吸附过程等。
3. 超声波技术超声波技术可以在不需要大量能量的情况下加速分子的移动速度,从而提高精馏效率。
同时,由于该技术能够降低温度和压力,因此可以减少能源消耗和排放。
4. 多级精馏技术多级精馏技术通过增加精馏塔的级数,减少塔内的压力差,从而降低能源消耗。
该技术可以在不影响分离效果的情况下减少能源和资源的消耗。
三、结论随着绿色低碳发展的大势所趋,高效节能的精馏技术将成为化工工业的主要发展方向之一。
通过研究和开发上述的高效节能精馏技术,我们可以更好地满足市场需要,并且为未来的环境和资源保护作出贡献。
精馏过程的节能降耗
炼油、石化生产过程中大量存在的分离、换热和反应工序,节能潜力巨大.能源是社会发展和进步的重要物质基础。
我国的能源储量以及一次能源的开发和消费量居世界前列,而能源的总利用率则远低于欧美和日本。
化学工业是个耗能大户,能耗量约占全国能源总消费的9%—10%,占工业用能的13%-15%,因此,化工节能对缓解我国能源的供需矛盾影响很大。
在当前世界性的能源危机面前,化学工业必须首先关注节能降耗和节能新技术的研究应用。
本文就我国化学工业中最普通也是能耗较多的分离过程这一领域中的一些节能现状作一粗略介绍。
一精馏过程的节能降耗精馏技术是化工领域中最为成熟,应用最为广泛且必不可少的单元操作,同时也是工业过程中能耗和设备投资高的设备,在炼油、石化等行业中,其能耗占全过程总能耗的一半以上。
因此对精馏过程节能技术的研究具有极其重要的意义。
国内外已开发并应用了一些节能型耦合精馏塔,如反应精馏塔(Reactive Distillation Column)、热耦合精馏塔(Petlyuk Column)、隔板精馏塔(Dividi Wall Column,简称DWC)等。
精馏过程的节能主要有以下几种基本方式:提高塔的分离效率,降低能耗和提高产品回收率;采用多效精馏技术;采用热泵技术等.1.1板式塔1。
1.1高效导向筛板高效导向筛板具有生产能力大、塔板效率高、塔压降低、结构简单、造价低廉、维修方便的特点,目前已广泛应用于化学工业、石油化工、精细化工、轻工化工、医药工业、香料工业、原子能工业等.1。
1。
2板填复合塔板板填复合塔板充分利用板式塔中塔板间距的空隙,设置高效填料,以降低雾沫夹带,提高气体在塔内的流速和塔的生产能力。
同时气液在高效填料表面再次传质,进一步提高了塔板效率.由于负荷下限未变而上限大幅度提高,因此塔的操作弹性也大为提高。
板填复合塔板已在石化、化工中的甲苯、氯乙烯等多种物系中得到成功应用。
1.1。
3复杂精馏塔传统的精馏塔及其精馏序列已不适应当前过程集成、设备集成的发展趋势。
- 1、下载文档前请自行甄别文档内容的完整性,平台不提供额外的编辑、内容补充、找答案等附加服务。
- 2、"仅部分预览"的文档,不可在线预览部分如存在完整性等问题,可反馈申请退款(可完整预览的文档不适用该条件!)。
- 3、如文档侵犯您的权益,请联系客服反馈,我们会尽快为您处理(人工客服工作时间:9:00-18:30)。
精馏过程节能技术综述石油化工是我国国民经济发展的支柱产业,据统计其能耗占全国工业总能耗的15%左右,而化工过程中40%~70%的能耗用于分离,精馏能耗又占其中的95%。
分离是非常重要的单元操作过程,是石油化工生产过程中必不可少的操作,它直接决定了最终产品的质量和收率,而精馏又是占据着主导地位的分离方法,所以在当今世界能源日益短缺的情况下研究和探讨精馏过程的节能原理、节能技术,并使其应用于工业生产,就显得十分重要。
精馏是化工及燃油工业中的主要分离技术,技术成熟可靠,投资相对较低,所以在石油化工生产过程中应用广泛,但现有精馏技术在热力学上是低效的耗能过程, 有极高的热力学不可逆性,分离lkg产品所需能量(比能耗)相当高,所以寻找精馏工程中有效可行的节能途径显得至关重要。
通过对精馏塔传热过程的分析可以得到如下节能途径:优化操作条件、塔系的热集成技术、内部能量热集成以及加强操作控制管理。
优化操作条件精馏塔的主要操作条件包括操作压力、操作温度、塔板压降,进料位置及温度、理论板数、回流比以及回流温度、塔顶塔底采出量、关键组份的清晰分割程度,塔顶塔底热负荷,塔类型及填料类型等等。
下面从充分利用精馏系统的热能、减少对热负荷的需求和提高精馏系统热力学效率三方面进行介绍。
充分利用精馏系统的热能精馏系统中,所需的热量全部由加热蒸气经再沸器输人,分离后的余热由冷却介质从冷凝器移出。
若能合理利用精馏过程中本身的能量,就能降低整个过程对能量的需求。
可通过采取保温、热量回收、强化换热器以及夹点技术的措施来实现。
在精馏过程中使用的设备主要为精馏塔和换热器,同时还有各种管道,这些设备的材质导热系数较高,若对其采取保温隔热的措施就可大大降低设备与环境之间的热传递作用,以达到节能降耗的目的。
高温物料携带大量热量可在塔外吸收利用,比如回收塔顶物料蒸气的潜热和回收塔釜废液的显热,使其用于工艺流程的其他需要加热的操作;使塔顶、塔釜物料与原料液进行换热,对原料液进行预热。
这样就避免了额外能量的消耗以达到节能目的,且操作简单,控制方便,投资费用也很小。
精馏系统的合理用能主要由换热器来体现,强化再沸器和冷凝器中的传热可使传热温差下降,同时还可提高塔顶冷却剂温度,降低塔釜的加热温度。
因而采用高效的换热设备或元件可大大提高传热系数,节约能量。
比如采用多孔相变化传热面积,包括微孔沸腾表面及特殊处理的冷凝表面,均可使沸腾或冷凝给热系数比光管提高10~30倍;增大传热面积,包括采用翅片管或开槽沟,可以使传热系数提高不少。
亦可采用更有效的换热介质来提高传热系数。
当有多股热流冷流进行换热时,可将所有的热流合并成一根热复合曲线,所有的冷流合并成一根冷复合曲线,然后将两线表示在温一焓图上,冷、热复合温度曲线在某点重合,当系统内部换热的极限,即该重合点的传热温差为最小,该点即为夹点。
在夹点为零下操作时,需要无限大的传热面积,可以通过技术经济评价而确定一个系统最小的传热温差——夹点温差,在精馏换热网络的合成中,利用夹点技术考虑各种物流匹配,可使换热网络的热量利用达到最优。
减少对热负荷的需求 在精馏过程中,若要减少对热负荷的需求,考虑精馏操作的气液平衡状态是非常重要的。
通过操作线的改进来接近气液平衡线、通过添加第三组分或降低操作压力来改进气液平衡状态等来实现。
减小回流比是一种容易使操作线接近于平衡线的方法。
回流比越接近于最小回流比,则操作线就越接近于平衡线,系统节能效果就更加明显。
所谓最小回流比就是在某种情况下,使平衡线组成(e X ,e Y )接近于进料浓度(f X )处,从而使进料板至其上一块塔板没有发生增浓现象。
当系统回流比最小时,虽然系统节能效果显著,即操作费用(主要由塔内水蒸汽和冷却水消耗来决定)较小.但是塔设备费用(塔板数增加)却迅速增加.蒸馏总费用(设备费用和操作费用之和)也随着增加。
通常,回流比选择应使设备费用和操作费用之和最小,即最佳经济回流比。
其实际值一般为最小回流比的1.1-1.5倍。
为了确保得到纯度合格的产品,设计时都有一定的回流余量。
余量越大,能耗越高。
对于回流余量较大的精馏塔,在不降低产品质量等级的情况下,只要在R 附近适当降低回流比,就可使操作线更接近于平衡线,即可大大降低塔底再沸器的能耗。
对于某些装置,也可通过适当地增加一些塔板数以减小R 。
但用增加板数以降低热负荷是有限度的,当塔板数增大到无穷多时,回流比将趋近最小回流比,适宜值为塔板数增加10% 一30%。
进料状态将直接影响到精馏塔能耗的大小,选择适宜的进料状态,可以使操作线更接近于气液平衡线可节省蒸汽能耗。
当塔主要受提流段支配时,进料的预热将使q 变小.使操作线更接近于汽液平衡线,使提馏段塔板数减少.提馏段的蒸汽负荷减少,从而可节省蒸汽。
当塔主要受精馏段支配时,进料的冷却将使得q 增大,从而使精馏段塔板数降低,提流段数增加,蒸汽量增加,但分离效果得到改善。
当组分的含量差异较大时,可将混合物料进行单塔处理或一塔多股进料,一般多股进料完成相同的分离任务时,能耗较低。
因此在一定的操作条件下,通过改变进料热状况,某些情况下可取得良好的节能效果。
另外在保证产品质量的前提下,如果进料中重组分增加,可降低进料口位置,从而可降低所需的加热热量。
改变气液平衡状态可降低精馏过程的能耗。
气液平衡状态的改进是通过添加第三组分或降低操作压力来实现的。
添加第三组份,使要分离的两组份的相对挥发度增加,破坏或利用共沸,来使组份变得更加容易分离,降低能耗。
一般在分离较困难的系统中采用,但如果第三组份回收困难,或分离所需能耗很大,或混入成品第三组分对成品纯度影响较大的场合,其应用往往受到限制。
降低操作压力被分离物系各组分间的相对挥发度增加,分离效果得到了改善,在热能利用效果和效率方面,达到了节能目,若同时采用较低压差.使平均相对挥发度增加,塔底温度下降,达到节能的效果。
特别引人注目的是采用高效填料时,节能效果更加明显。
选择适宜的进料板位置也可降低能耗。
在精馏操作条件不变的情况下,若进塔物料组成与加料板的组成差别较大,则应更换进料位置,在保持产品同一质量品质的前提下,进料中重组分增加,可降低进料口位置,减小提馏段;或被分离的物料来源不同,各组分的含量差异较大,可将各种物料进行一塔多股进料。
实际证实调节进料口位置或多股进料完成相同的分离任务,能耗较低。
这是因为混合过程是增熵过程,各组分不同的几股物料的混合,增加了过程的不可逆性,这必然增加精馏过程的能耗。
提高精馏系统热力学效率主要是提高产品的分离效率和产品回收率,可通过采用新型塔板和高效填料,以及加中间换热器等方式来提高分离效果和降低能耗。
塔板和填料是精馏塔最为重要的传质内件,新型塔板和高效填料具有效率高、压降低的优点。
如采用伞形气帽、浮动筛板、新垂直筛板及穿流式浮板等新型塔板,可以降低精馏塔的操作压力,使被分离物系各组分间的相对挥发度增大,有利于提高分离效率和降低能耗。
填料性能主要取决于填料表面的湿润程度和气液两相流体分布的均匀程度。
目前的高效填料有:新型高效规整填料;新型高效散堆填料;阶梯填料;金属环矩鞍填料等。
新型高效填料在精馏塔器中的应用,均可以达到扩产、节能、降耗的效果。
中间换热器可用来节省或回收热量(冷量)。
在塔顶和塔釜的温度差较大的情况下可在精馏段中间设置冷凝器,在提馏段中间设置再沸器,可降低精馏操作费用。
这是因为精馏过程的热能费用取决于传热量和所用热载体的温位。
在传热量一定的条件下,设置中间冷凝器,可用温位较高、价格较便宜的冷却剂,使上升蒸汽部分冷凝,以减少塔顶低温冷却剂用量。
中间再沸器则同理。
对塔底再沸器来说,中间冷凝器是回收热量,中间再沸器是节省热量;而对于塔顶冷凝器来说,中问冷凝器是节省冷量,中间再沸器是回收冷量。
塔系的热集成技术热集成精馏系统综合的目标就是寻找既能够按要求实现组分分离,又能使年度总费用达到最小的精馏序列及热集成结构。
通过精馏塔间的热集成,可以用温位较高的冷凝物流来加热温位较低的再沸物流,这样就可同时节约冷却和加热的公用工程,且所节省的潜热远大于换热网络所回收的流股间的显热。
通过对普通精馏塔热量和冷量回收利用的方式和途径以及分离物系的不同,就形成了许多不同的节能型精馏流程。
下面将主要介绍多塔分离序列、多效精馏、热泵精馏和热偶精馏。
多塔分离序列当采用精馏塔将多个组分进行分离时,精馏塔的排列顺序可以有多种方案,也必然存在一个最优的方案使得耗能最小,根据前人经验我们得到了以下规则:对易造成系统腐蚀或结焦的组分应首先除去,以降低后续设备的材质要求或稳定操作;再把进料分成分子数接近的两股流,按塔顶与塔底各占50%的分馏比例安排;根据气液平衡常数的大小进行排序,把轻组分逐个脱除,即采取顺序流程;最难分离的组分或对回收率要求高的组分放在最后。
实验验证简单精馏流程采用热集成技术比无热集成的可节约操作费用50%,可见塔系热集成技术对于分离过程能耗的影响往往比单个塔的优化更显著。
多效精馏在工业发达国家,多效精馏已成为一种规范性节能系统,广泛应用于工业生产中。
多效精馏是一种充分利用能量品位的有利措施。
通过扩展工艺流程来节减精馏操作能耗的,它是以多塔代替单塔,各塔的能位级别不同,能位较高的塔排出的能量用于较低的塔,从而达到节能的目的。
即多效精馏将前级塔顶冷凝器与次级塔底再沸器合二为一,将前级塔顶蒸汽冷凝所放出的热量用作次级塔液的汽化,操作压力逐效降低,前面较高压力塔的塔顶蒸汽作为后面较低压力的塔底再沸器的加热介质,在其中冷凝。
换言之除压力最低塔外,其余塔顶蒸气的冷凝潜热均被精馏系统自身回收利用,减少了传热的不可逆性,减少了公用工程消耗,从而降低能耗。
由于多效精馏随效数增加,加热蒸气用量减少产生的节能效果开始不断下降,且受到第一级加热蒸气压力及末级冷却介质种类的限制,操作愈发困难,,所以工业上一般都采用双效精馏。
多效精馏的节能效果,除受效数影响外,还受到分离物系的性质、易挥发组分的含量、工艺流程等因素影响,其节能效果已为实践所证实,双效精馏操作所需热量与单效精馏比可减少30%~40%。
热泵精馏热泵技术是用压缩式冷冻机将塔顶蒸汽直接加压升温,或将与塔顶蒸汽进行热变换的介质加压升温,使塔顶蒸汽(或其介质)作为高位热源,在再沸器进行热交换,来作为塔釜的加热热源。
热泵实质上是一种单效精馏,把冷凝器的热“泵送”到再沸器里去,使精馏能耗减少的制冷系统。
因回收的潜热用于过程本身,又省去了塔顶冷凝器冷却水和塔釜加热蒸气,热泵系统中压缩消耗的能量,是唯一由系统外提供的,相当于只有再沸器直接加热消耗能量的20%一40%,故可使精馏的能耗明显减少。
节能效果一般由供热系数COP来衡量,它表示加入1kJ的压缩功可提供给再沸器多少kJ的热量,其值越大,效果越好。