塑料挤出模具的设计准则
塑料加工工艺中的模具设计原则

塑料加工工艺中的模具设计原则引言对于塑料制品的生产而言,其模具设计是至关重要的步骤。
一款均衡、合理的模具设计将能够为塑料加工工艺中的高效、稳定和持续的生产打下基础,同时还能缩短生产周期和降低生产成本。
因此,本文将从以下几个方面入手,谈谈在塑料加工工艺中模具设计的原则。
一、选择合适的模具材料模具材料是模具设计的重要原则之一。
在模具设计中,必须确保所选材料的物理、化学特性满足生产过程的要求。
而对于塑料制品的生产而言,常用的模具材料主要有钢、铝、钛、铸铁、硅铁等。
这些材料各有优缺点,所以在实际生产中要根据产品的需求和生产的要求来选择合适的模具材料。
例如,钢材的硬度高、强度大、耐磨损性能好,能承受高压和高温等极端环境条件,因此在生产大型、复杂、长寿命的产品时,钢模具是最佳选择。
二、模具的结构设计模具结构设计是模具设计的另一个重要原则。
模具的结构应具有足够的强度和稳定性,能够承受生产过程中的高压和高温等极端环境条件,同时还要考虑成形件的尺寸精度、表面质量和竖向尺寸的一致性等要素。
而在选择模具结构时,还要考虑生产成本和加工难度等因素,以便生产过程中的高效、稳定和持续性。
三、模具的加工工艺设计在模具设计中,加工工艺的选择和设计也是非常重要的原则之一。
因为模具的加工精度和外观质量直接决定了成品的质量。
而在选择加工工艺时,也要根据模具的结构特点和生产成本、加工周期等因素来进行综合考虑,以确保生产加工过程的高效、稳定和持续性。
四、模具的维护保养模具的设计是非常关键的,但在生产过程中同样重要的是模具的维护保养。
因为模具的长期使用和高强度的生产加工过程会导致其损耗和磨损,从而影响塑料制品的生产质量。
而为了尽可能地延长模具的使用时间、保证生产效率和成本效益,在生产过程中必须对模具进行定期维修和保养,以确保其长寿命、稳定和持续性。
结论模具设计是塑料制品生产过程中非常重要的环节,也决定了塑料制品的质量和生产效率。
因此在模具设计中,必须依据产品需求和生产要求,选择合适的材料、设计合理的结构、选择合适的加工工艺,并对模具进行定期维修和保养,以确保生产加工过程的高效、稳定和持续性。
塑料成型工艺及模具设计--挤出成型及机头设计
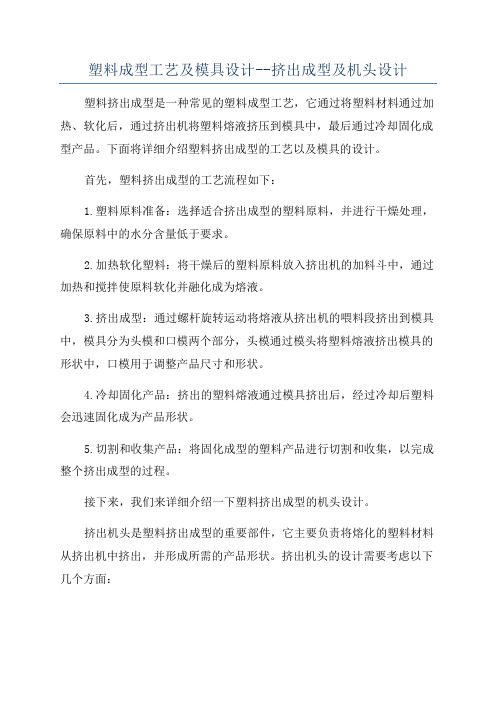
塑料成型工艺及模具设计--挤出成型及机头设计塑料挤出成型是一种常见的塑料成型工艺,它通过将塑料材料通过加热、软化后,通过挤出机将塑料熔液挤压到模具中,最后通过冷却固化成型产品。
下面将详细介绍塑料挤出成型的工艺以及模具的设计。
首先,塑料挤出成型的工艺流程如下:1.塑料原料准备:选择适合挤出成型的塑料原料,并进行干燥处理,确保原料中的水分含量低于要求。
2.加热软化塑料:将干燥后的塑料原料放入挤出机的加料斗中,通过加热和搅拌使原料软化并融化成为熔液。
3.挤出成型:通过螺杆旋转运动将熔液从挤出机的喂料段挤出到模具中,模具分为头模和口模两个部分,头模通过模头将塑料熔液挤出模具的形状中,口模用于调整产品尺寸和形状。
4.冷却固化产品:挤出的塑料熔液通过模具挤出后,经过冷却后塑料会迅速固化成为产品形状。
5.切割和收集产品:将固化成型的塑料产品进行切割和收集,以完成整个挤出成型的过程。
接下来,我们来详细介绍一下塑料挤出成型的机头设计。
挤出机头是塑料挤出成型的重要部件,它主要负责将熔化的塑料材料从挤出机中挤出,并形成所需的产品形状。
挤出机头的设计需要考虑以下几个方面:1.挤出机头的结构:挤出机头通常由挤出机芯、流道和模头组成。
挤出机芯用于将熔化的塑料材料从挤出机中挤出,流道负责将熔液引导到模头当中,模头则通过调整挤出物料的流量和形状来控制最终产品的形状。
2.流道设计:流道的设计需要考虑熔液的流动特性,合理设计流道的尺寸和形状,以确保熔液在流道中流动顺畅,不发生堵塞和死角。
同时,流道的设计还需要考虑产品的外形和尺寸要求,以保证挤出的塑料产品形状准确。
3.模头设计:模头是挤出成型中最重要的部分,它通过模头的形状和结构来决定产品的外形。
模头的设计需要考虑产品的尺寸、形状以及挤出速度等因素,合理设计模头的流道和出口形状,以保证产品的成型质量。
4.温度控制:塑料挤出成型中,温度对产品的成型质量和表面光洁度有很大影响,因此挤出机头的设计需要考虑温度的控制。
塑料制品挤压模具的设计需要注意哪些?
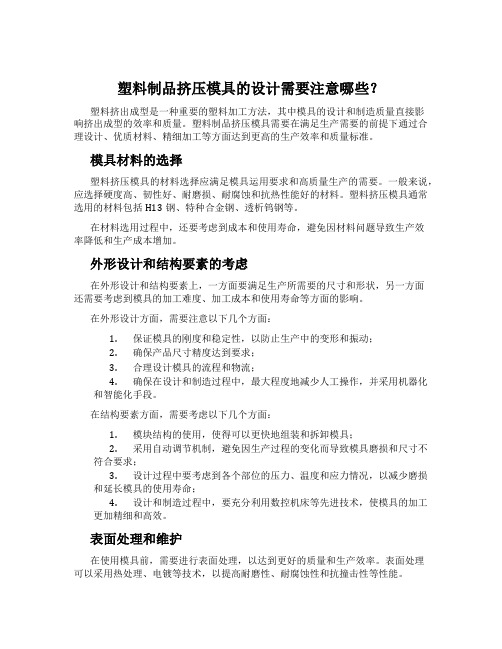
塑料制品挤压模具的设计需要注意哪些?塑料挤出成型是一种重要的塑料加工方法,其中模具的设计和制造质量直接影响挤出成型的效率和质量。
塑料制品挤压模具需要在满足生产需要的前提下通过合理设计、优质材料、精细加工等方面达到更高的生产效率和质量标准。
模具材料的选择塑料挤压模具的材料选择应满足模具运用要求和高质量生产的需要。
一般来说,应选择硬度高、韧性好、耐磨损、耐腐蚀和抗热性能好的材料。
塑料挤压模具通常选用的材料包括H13钢、特种合金钢、透析钨钢等。
在材料选用过程中,还要考虑到成本和使用寿命,避免因材料问题导致生产效率降低和生产成本增加。
外形设计和结构要素的考虑在外形设计和结构要素上,一方面要满足生产所需要的尺寸和形状,另一方面还需要考虑到模具的加工难度、加工成本和使用寿命等方面的影响。
在外形设计方面,需要注意以下几个方面:1.保证模具的刚度和稳定性,以防止生产中的变形和振动;2.确保产品尺寸精度达到要求;3.合理设计模具的流程和物流;4.确保在设计和制造过程中,最大程度地减少人工操作,并采用机器化和智能化手段。
在结构要素方面,需要考虑以下几个方面:1.模块结构的使用,使得可以更快地组装和拆卸模具;2.采用自动调节机制,避免因生产过程的变化而导致模具磨损和尺寸不符合要求;3.设计过程中要考虑到各个部位的压力、温度和应力情况,以减少磨损和延长模具的使用寿命;4.设计和制造过程中,要充分利用数控机床等先进技术,使模具的加工更加精细和高效。
表面处理和维护在使用模具前,需要进行表面处理,以达到更好的质量和生产效率。
表面处理可以采用热处理、电镀等技术,以提高耐磨性、耐腐蚀性和抗撞击性等性能。
在使用模具的过程中,定期的维护和保养也是非常必要的,可以有效减少模具的磨损和延长使用寿命。
以下是模具常见的维护和保养方式:1.定期清洗模具和其周边,并进行润滑;2.定期进行检修和维护,并更换磨损严重的部件;3.对于长时间不使用的模具,需要进行密封和防潮处理;4.废弃模具需要进行妥善处理。
挤出模具设计的规则及步骤

模具,是以特定的结构形式通过一定方式使材料成型的一种工业产品,同时也是能成批生产出具有一定形状和尺寸要求的工业产品零部件的一种生产工具。
模具在很大程度上决定着产品的质量、效益和新产品开发能力。
同样,挤出模具在制造和设计过程中,要兼顾性能和效率,以及成本诸多因素,以下总结了以下挤出模具在设计和制造中涉及到的原则,分享给大家。
挤出模具的设计包括以下诸多内容精度条件、几何形状设计、批量大小、成型设备、尺寸稳定性及表面质量等诸多内容。
第一:几何形状设计方面在设计时,经常要综合考虑尺寸稳定性及表面质量。
例如,制品设计和尺寸稳定性要求采用阴模(凹模),但是表面要求光泽度较高的制品却要求使用阳模(凸模),这样一来,塑件订购方会综合考虑到这两点,制品能在最佳条件下进行生产。
第二:批量的大小方面实验用,模具产量小时,可采用木材或树脂进行制造。
但是,如果实验用模具是为了获得制品有关收缩、尺寸稳定性及循环时间等的数据时,应该使用单型腔模具来实验,且能保证其能在生产条件下运用。
模具一般用石膏、铜、铝或铝-钢合金制造,很少用到铝-树脂。
第三:尺寸公差方面在成型过程中,塑件与模具接触的面要比离开模具部分的尺寸稳定性更好。
如果日后由于材料刚度的需要要求改变材料厚度,可能导致要将阳模转换为阴模。
塑件的尺寸公差不能低于收缩率的10%。
第四:塑件的光洁面就成型材料能够包住的范围而言,塑件可见面的表面结构应在与模具接触处成型。
如果可能的话,塑件的光洁面不要与模具表面接触。
第五:余量的控制如果使用机械式水平锯锯掉塑件的夹持边,在高度方向上,至少要有6~8mm的余量。
其他的修整工作,如磨削、激光切削或射流,也必须留有余量。
刀口模切割线间的间隙最小,冲孔模修整时的分布宽度也很小,这些都是要注意的。
第六:收缩和变形塑料易收缩(如PE) ,有些塑件易变形,无论如何预防,塑件在冷却阶段都会发生变形。
在这种条件下,就要改变成型模具的外形来适应塑件的几何偏差。
塑料挤出模具设计

塑料挤出模具设计塑料挤出模具设计指的是生产各种管道、线条、条形等复杂形状的产品,以满足消费者的需求。
挤出模具设计是塑料成型工艺中最关键的一环。
模具设计要求精度高、生产效率高、工艺优良、耐久性强等多个方面的考量,因此,在设计中需要注意各项要素,以达到预期的效果和质量标准。
首先,塑料挤出模具设计需要结合塑料挤出成型的工艺流程和参数,确保稳定的生产和高效的能源利用。
第一步是从材料入手,确定选用哪种材质,例如,挤出模具通常会使用热工模造型钢,湛江模具钢等合金类材料,这些材料能够提高模具的硬度和耐磨性,满足生产高要求产品的需要。
然后,根据产品形状等要求进行模具的设计,制定模具的大小、形状和几何参数,并结合模具的内部结构和装配装置,以确保正常的生产效果。
其次,在塑料挤出模具设计中需要注意模具的板数、结构和加工工艺。
挤出模具通常采用多板式结构,有顶板、底板、侧板、隔板等部件,用来固定塑料管材的截面形状、支撑挤出的压缩过程和控制形状等方面。
而在制作过程中,需要考虑到精度和几何形状的匹配关系,避免由于制造误差等问题造成挤出过程中的漏斗效应和产品的形状变形问题。
由此可见,塑料挤出模具设计、制造和精密加工是一项极其繁琐的工程。
其次,一个优秀的塑料挤出模具设计还需要考虑到产品配合、冷却和粘连等环节。
对于不同的挤出产品,需要根据其特点和要求进行设计和制作。
例如,在挤出大规格、壁厚较大的产品时,应该考虑到的是冷却和卡边设计,以便解决加热带来的产品变形问题;而在厚度较薄、曲度较大的产品上,需要考虑到的是粘连和多层结构的细致设计,以确保产品的精度和美观度。
最后,优秀的塑料挤出模具设计还需要考虑到制造和维护成本的问题。
制造成本与材料、加工和手工制作等资源的利用效率密切相关;而维护成本则往往与使用寿命相关,需要定期进行检查和维护,切勿忽略隐患和故障点。
这样才能确保模具的长期使用效应和成本效益。
总之,塑料挤出模具设计是制造各类产品的重要前提和要素,需要注重各个方面的细节和技术,以满足消费者的需求和制造公司的要求。
塑料电线挤出模具设计
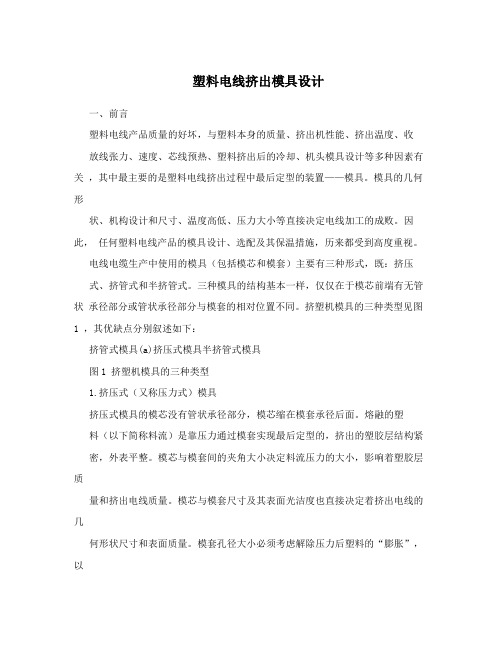
塑料电线挤出模具设计一、前言塑料电线产品质量的好坏,与塑料本身的质量、挤出机性能、挤出温度、收放线张力、速度、芯线预热、塑料挤出后的冷却、机头模具设计等多种因素有关,其中最主要的是塑料电线挤出过程中最后定型的装置——模具。
模具的几何形状、机构设计和尺寸、温度高低、压力大小等直接决定电线加工的成败。
因此,任何塑料电线产品的模具设计、选配及其保温措施,历来都受到高度重视。
电线电缆生产中使用的模具(包括模芯和模套)主要有三种形式,既:挤压式、挤管式和半挤管式。
三种模具的结构基本一样,仅仅在于模芯前端有无管状承径部分或管状承径部分与模套的相对位置不同。
挤塑机模具的三种类型见图1 ,其优缺点分别叙述如下:挤管式模具(a)挤压式模具半挤管式模具图1 挤塑机模具的三种类型1.挤压式(又称压力式)模具挤压式模具的模芯没有管状承径部分,模芯缩在模套承径后面。
熔融的塑料(以下简称料流)是靠压力通过模套实现最后定型的,挤出的塑胶层结构紧密,外表平整。
模芯与模套间的夹角大小决定料流压力的大小,影响着塑胶层质量和挤出电线质量。
模芯与模套尺寸及其表面光洁度也直接决定着挤出电线的几何形状尺寸和表面质量。
模套孔径大小必须考虑解除压力后塑料的“膨胀”,以及冷却后的收缩等综合因素。
由于是压力式挤出,塑料在挤出模口处产生较大的反作用力。
因此,出胶量要较挤管式低的多,目前绝大部分电线电缆的绝缘均用1挤压式模具生产,但也有一些电线绝缘的生产被挤管式和半挤管式模具所代替,挤压式的另一缺点是偏心调节困难,绝缘层厚薄不容易控制。
2.挤管式(又称套管式)模具电线挤出时模芯有管状承径部分,模芯口端面伸出模套口端面或与模套口端面持平的挤出方式称为挤管式。
挤管式挤出时由于模芯管状承径部分的存在,使塑料不是直接压在线芯上,而是沿着管状承径部分向前移动,先形成管状,然后经拉伸在包复在电线的芯线上。
这种形式的模具一直只用于电缆护套挤出,近年来绝缘的挤出也越来越多的加以采用,因为它与挤压式相比有如下的优点:(1)挤出速度快。
典型的挤出模具设计

典型的挤出模具设计挤出模具是一种常用于橡塑制品加工的模具,通过材料在模具中连续挤出,使其形成具有一定形状和尺寸的产品。
挤出模具广泛应用于塑料、橡胶、硅胶、硬质泡沫等各种材料的生产中,能够制造出各种管材、板材、条材、异型材等产品。
典型的挤出模具设计需要考虑材料特性、产品形状和尺寸等多个因素。
首先,挤出模具设计需要根据材料的特性来确定模具的结构和参数。
不同材料具有不同的流动性、熔体温度和粘度,对模具的设计产生不同的要求。
例如,一些材料具有较高的熔体温度和较高的黏度,需要采用加热设备和较大的流道截面积来确保材料能够顺利挤出。
而一些材料具有较低的流动性,需要增加收缩率和壁厚等参数来避免产品出现瑕疵。
因此,设计师需要了解材料的特性,合理确定模具的结构和参数。
其次,挤出模具设计需要考虑产品的形状和尺寸。
不同的产品形状对模具的设计产生不同的要求。
例如,圆形管材的模具需要设计圆形的出模口和流道,以保证挤出的产品具有良好的圆度和尺寸一致性。
而异型材的模具需要根据产品的形状和结构设计复杂的挤出口和流道,以确保产品能够顺利挤出,并且具有良好的表面质量和尺寸精度。
因此,设计师需要根据产品的形状和尺寸,合理确定模具的结构和参数。
再次,挤出模具设计需要考虑模具的制造和使用成本。
模具的制造和使用成本直接影响到产品的竞争力和市场占有率,因此设计师需要在满足产品形状和质量要求的前提下,尽量减少模具的制造和使用成本。
一方面,可以通过合理设计模具的结构和参数,减少模具的复杂度和制造难度。
另一方面,可以选择合适的材料和加工工艺,提高模具的耐磨性和使用寿命,降低维护和更换的频率。
因此,设计师需要综合考虑多个因素,合理选择模具的结构、材料和加工工艺,以实现最佳的经济效益。
最后,挤出模具设计还需要考虑产品的生产效率和质量稳定性。
生产效率和质量稳定性是企业提高竞争力和降低成本的关键。
模具的设计应充分考虑产品的生产工艺和生产效率,提高生产效率和降低不良品率。
挤出成型模具解析
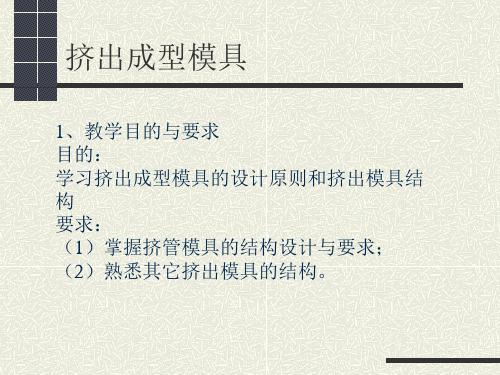
PSU
氯化聚 醚
收缩率 2.5~5 3~6 1~2.5 1~2.5 2.5~4 1~2 1.5~3.5
尼龙-1010棒材定径套尺寸
棒材公 称直径
40 50 60 70 80
(1)口模
定型长度L1 = n t t:制聚氯乙烯 (HPVC)
软聚氯乙烯 (SPVC)
聚酰胺 (PA)
聚乙烯 (PE)
聚丙烯 (PP)
n
18~33
15~25 13~23 14~22 14~22
(1)口模
2°口模内径Dm:
Dm
d k
d:制品管外径,
k:补偿系数。
塑料品种 定型套定管材内径
(2)芯棒
2 °定型长度L2: 定型段长度L2与口模长度L1相等或稍长。 L2 3 °压缩段长度: 压缩段长度与口模中相应的锥面部分构成塑料熔体的压缩区, 使进入定型区之前的塑料熔体的分流痕迹被熔合消除。 L = (0.83~0.94) D0 D0:机头与过滤板连接处的流道直径。 4 °芯棒的压缩角β: 低粘度塑料: β=45 ° ~60 ° ; 高粘度塑料: β=30 ° ~50 ° 。
挤出成型模具
四、管机头的设计 1、结构型式
挤出成型模具
2、零件设计 (1)口模
口模成型制品的外表面。口模的平直部分为定型长度。物料通 过时,料流阻力增加,使制品密实。同时也使料流稳定均匀。
1°定型长度L1: L1=(0.5~3)D D:制品管材外径的公称尺寸。 管径大时取小值。软管取大值,硬管取小值。
五、棒材挤出机头
3、定径套
(1)定径套尺寸 棒材外径<500mm时,定 径套长度200~300mm; 当外径>50~100mm时, 定径套长度300~500mm。 定径套的内径要大于所需 棒材的直径。
- 1、下载文档前请自行甄别文档内容的完整性,平台不提供额外的编辑、内容补充、找答案等附加服务。
- 2、"仅部分预览"的文档,不可在线预览部分如存在完整性等问题,可反馈申请退款(可完整预览的文档不适用该条件!)。
- 3、如文档侵犯您的权益,请联系客服反馈,我们会尽快为您处理(人工客服工作时间:9:00-18:30)。
塑料挤出模具的设计准则
塑料挤出模具的设计准则
筋
在壁厚变化过程中,如果厚度变化太剧烈太大,在平衡流场过程中可能会出现问题。
筋的厚度应该是标称壁厚的50%,半径应该以此为基础设计。
半径
急剧变化的地方要用圆角代替过渡。
挤出部件最小的半径是
0.20mm(0.007”)。
壁厚
均匀的或者近乎均匀的截面厚度将更具备易加工性,降低成本,更好的误差控制,更好的表面光洁度和更复杂的形状。
最小壁厚为0.5毫米(0.02”),而最大壁厚为9.5毫米(0.375”)。
更薄的壁厚是可能的,但需要用到santoprene8000热塑性弹性体系列。
壁厚的变化要光顺平稳,并应尽可能小,因为这将有助于冲压模均衡。
中空
在横截面里可能会有中空截面。
挤压模具可能刚开始便具有中空截面的形状,在冷却的时候可以在中空截面内使用压缩空气以保持形状,另一种方法是在挤出机的外部使用真空来帮助中空截面保持形状。
更多的中空截面使得模具的设计变得更复杂,其轮廓形状的`保持也变得更加困难。
除非是设计要求,中空截面应该尽量减少甚至全部避免。
在挤出的过程中往内吹风是冷却部件内壁的一种手段。
这就需要沿着切割线或冲孔方向有空气可以流通。
发泡挤出
热塑性弹性体tpv可以通过化学和机械方法来起泡。
对化学起泡,可以使用诸如重盐酸盐之类的发泡剂。
可以达到的泡沫密度比重为0.97(典型的未起泡tpv)到0.70。
更低的密度受专利影响。
发泡剂
在180℃到190℃下会退化,因为大部分tpv的基础是在195到215℃条件下进行的。
对于机械方法,水是作用介质。
这里,名为“水起泡”的技术,是一项专利技术。
需要用专门的设备来获得一致的泡沫结构和密度。
密度由0.97减少到0.20。
在这个范围内的密度可以通过控制加工
工艺来获得。
密度的减小会影响机械特性,所以这被归为应用中的
外形设计。
多层挤出
焊接节点
热焊接是比较流行的用来接合用tpv制成的挤出胶的方法。
热量被引入到连接面,使得表面熔解,再将表面贴合到一起,并施加轻
微的压力以保证没有气体进入到接触面间。
冷却之后,结合处与部
件本身强度几乎一样。
另一个接合挤出部件的方法是使用胶粘系统。
需要一些装填物,取决于接合处材料的联合及粘接强度的要求。
唇形密封和球状密封
唇形和球状密封是常见的密封应用。
通常来说,球状密封较好,这是由于其相对唇形密封而言具备更出众的弹性恢复能力。
相对于
唇形密封,球型密封提供了更高的密封力。
这是因为球状密封可以
在每一边都像唇形密封一样,提供密封力。
当然,事情总是公平的,球型密封要求提供比唇形密封更多的力,这些力转变成更高的密封力。
扭折
当挤出部件被安装好后,并以一定的半径弯曲,此时可能出现一种不利的现象,那就是挤出部件的扭折。
扭折可能导致密封不良或
者对水流有限制。
一般来说,弯曲的半径越大,弯角旁边安装的挤
出部件扭折的可能性越小。
为了避免扭折的发生,可以采用两种可行的方法。
第一种是增加部件的壁厚,它将减小扭折。
变大的壁厚,其内径弯曲比外径弯曲的影响更大。
另外一种解决方法就是使部件起泡。
发泡的部件使得材料可以在内部弯曲时压缩。
现在已经知道的是,材料的硬度对扭折有一定的影响。