来料异常处理流程
来料异常制程物料异常及制程工艺异常处理控制程序
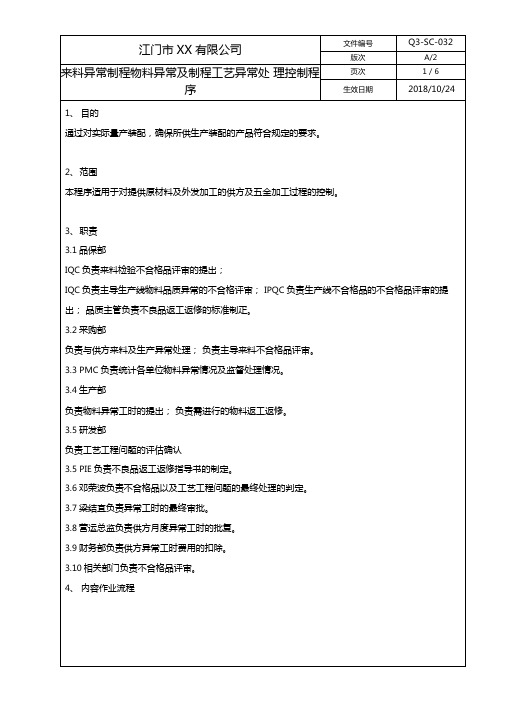
文件编号
Q3-SC-032
版次
A/2
来料异常制程物料异常及制程工艺异常处 理控制程序
页次
1 / 6
生效日期
2018/10/24
1、目的
通过对实际量产装配,确保所供生产装配的产品符合规定的要求。
2、范围
本程序适用于对提供原材料及外发加工的供方及五金加工过程的控制。
3、职责
3.1品保部
PMC
跟踪采购对供应商的扣款处理情况
品保
跟踪供方的改善情况。
《纠正预防措施报告》
5
费用处理
采购
交财务进行扣款。
《异常工时申请表》
6
统计分析
PMC
知会采购,财务。
《每月异常工时统计表》
江门市XX有限公司
文件编号
Q3-SC-032
版次
A/2
来料异常制程物料异常及制程工艺异常处 理控制程序
页次
3 / 6
生效日期
IQC负责来料检验不合格品评审的提出;
IQC负责主导生产线物料品质异常的不合格评审;IPQC负责生产线不合格品的不合格品评审的提出; 品质主管负责不良品返工返修的标准制疋。
3.2采购部
负责与供方来料及生产异常处理; 负责主导来料不合格品评审。
3.3 PMC负责统计各单位物料异常情况及监督处理情况。
3.4生产部
《退货单》
处理 返工返修
采购
由本厂进行,采购即时通 知供方洽谈相关费用。
《返工申请单》
PIE
即时制定返工返修作业指 导书。
《返工返修作业指导书》
品保
制定返工返修的判定标 准,并对返工返修的物料 再次检杳确认。
来料检验及异常处理流程

编制:张德江审核:批准:1目的对供应商提供的物料进行检验和试验,保证物料符合规定的要求,防止不合格物料投入生产2适用范围适用于本公司所有用于生产的物料和外协加工件的检验和试验。
3职责3.1 仓管:负责物料的点收、保管并办理不合格物料的退货工作。
3.2 采购部:负责将来料的不合格情况通报给供应商,。
3.4MRB评审小组:负责对来料不合格之评审、判定。
3.3 品管部:负责物料的检验、不合格物料最终判定及其品质改善状况的跟进。
4.作业程序4.1 来料接收供应商交货时,仓管员依订单资料对照供应商的“送货单”核对品名、料号、规格、数量。
仓管将所收物料放入待检区,然后填写《送检单》交品管部IQC进行验收,特急物料应在《送检单》上注明“特急”字样4.2 来料检验4.2.1 IQC接到“送检单”后,查核来料实物是否与“送检单”相符,若来料实物与“送检单”不符时,IQC应及时知会仓库进行处理。
4.2.2 IQC按《来料检验规范》、《来料检查方案》、样板、《样品承认书》等进行检验。
并将检验结果应填入《IQC检验报告》。
4.3 检验与判定:4. 3 .1 正常物料IQC应在2个工作日内给出检验结果,单款特急物料应在2个小时内检验完毕.4.3.2判定合格:检验员按《产品标识和可追溯性控制程序》的规定在来料货物外包装上粘贴合格标签,标签内容包括,物料编号、品名规格、数量、检验日期、检验员、供应商名称,并在《IQC检验报告》上签上检验员的名字,通知仓库将合格物料入库。
4.3.3判定不合格检验不合格:IQC将检验报表连同不合格物料样本交MRB评审小组评审。
MRB小组根据实际所需做出:挑选、加工、特采、退货等处理意见,最终由品质经理做最后判定。
再由IQC将不合格处理报表分发给计划、采购各1份。
MRB评审判定为生产加工的物料,需由生产技术部提供追加工方法和技术指导.对于MRB判定加工或者挑选的物责任方应在判定后的两个工作日内完成,并将结果反馈IQC进行重新检验。
来料不良反馈流程

东莞林积为实业投资有限公司来料不良反馈流程一、目的:规范来料品质异常处理流程,便于不良状况的及时有效改善。
二、适用范围:适用于所有部品来料异常的反馈。
三、具体内容:3.1、部门职责:1、品质职责:⑴IQC负责对来料按AQL水准抽检,判定,有异常时,需填写《品质异常联络单》交SQE 工程师联络供应商处理。
⑵IPQC负责产线反馈部品异常时的确认,判定,联络SQE与供应商处理不良。
⑶反馈后,SQE工程师应收集好不良品,便于供应商来厂确认,分析。
⑷SQE负责与供应商一起确认不良,并让供应商给出改善措施报告,在供应商需求技术协助时,由SQE负责人联络PE工程师。
2、生产职责:在生产中发现部品来料不良异常时,需及时填写《部品质量情况紧急反馈表》,联络PE 工程师、SQE工程师界定,处理。
3、PE工程师职责:生产反馈,供应商处理问题时,涉及到技术问题(性能),需工程解决。
4、SQE工程师职责:根据反馈,将反馈表以邮件发送供应商,并且联络供应商处理,在3个工作日内将供应商回复的处理方式,结果以邮件形式发送到生产,品质,工程,仓库,各负责人邮箱。
5、仓库职责:负责将品质判定NG的货物隔离放置,待处理,不允许再发料。
3.2、反馈注意事项:1、所有部品不良反馈,需确认清楚,必须是事实,有实物,有《品质异常联络单》。
反馈后,必须保留不良品,以供供应商处理问题时确认,分析使用。
2、IPQC对产线反馈问题,不能做出有效判定,需技术支持时,需找PE工程师协助处理。
对于反馈不良,SQE工程师需确认清楚反馈内容,不良率,是否如报告所写。
3.3、品质抽检来料异常反馈流程:a.品质来料抽检超出AQL接收水准,填写《品质异常联络单》,异常联络单内容应描述出来料数量,日期批量,抽检水准,抽检数,不良数,不良率等,同时应注明该批货物的处理方式,退货或选别使用。
b.《品质异常联络单》经品质主管审核后,交SQE工程师处理。
同时不良图片发给SQE工程师,以便于SQE工程师联络供应商处理c.SQE工程师收到信息后,在2小时内应将异常反馈到供应商,要求供应商在3个工作日内作出处理方案。
生产异常处理流程

3、装配部----每月初提交上月扣供应商的工时费用明细至副总助理处。
采购部----每月初提交罚供应商款项明细至副总助理处。
由总经办分析供应商当月因异常致罚款情况。
版本:
A
文件编号:
ZJB-06
生效日期:
2012.3.17
制作:
朱秀秀
审核:
批准:
生产异常处理规定
异常单处理流程图
规定
一、所有异常单任部门完成,否则发生的费用协助部门与责任部门各承担50%。
二、来料问题责任界定(品管部):
1、装配部所发出的来料异常(一个人能加工的可不写异常),PE通知品管及采购人员现场分析处理,责任则判定为品管部,但异常单上“责任部门确认和回复”一栏则填写供应商名称。
4、奖罚规定:
A、对于重复性发生的异常:每次罚款100元;
B、对于批量型不能生产的异常:当月只限3次机会,超过3次,罚款50元/次;
C、当月异常次数(A、B项总次数)合计在3次范围内,当月给予奖励150元。
三、设计问题责任界定(工程部):
1、生产线所出现设计异常,责任部门则判定为属工程部责任,PE协助改善;
2、责任人必须去跟踪落实到位并结案,处理方案必须注明协助部门需配合完成哪些具体事项;
3、奖罚规定:
A、老产品上线后设计问题出现的异常:当月只限3次机会,超过3次,罚款50元/次
B、新产品:不计罚款。(注:新产品涉及到的模具报废需进行处罚)
来料检验及异常处理流程

来料检验及异常处理流程 This model paper was revised by the Standardization Office on December 10, 2020编制:张德江审核:批准:1目的对供应商提供的物料进行检验和试验,保证物料符合规定的要求,防止不合格物料投入生产2适用范围适用于本公司所有用于生产的物料和外协加工件的检验和试验。
3职责仓管:负责物料的点收、保管并办理不合格物料的退货工作。
采购部:负责将来料的不合格情况通报给供应商,。
MRB评审小组:负责对来料不合格之评审、判定。
品管部:负责物料的检验、不合格物料最终判定及其品质改善状况的跟进。
4.作业程序来料接收供应商交货时,仓管员依订单资料对照供应商的“送货单”核对品名、料号、规格、数量。
仓管将所收物料放入待检区,然后填写《送检单》交品管部IQC进行验收,特急物料应在《送检单》上注明“特急”字样来料检验4.2.1 IQC接到“送检单”后,查核来料实物是否与“送检单”相符,若来料实物与“送检单”不符时,IQC应及时知会仓库进行处理。
4.2.2 IQC按《来料检验规范》、《来料检查方案》、样板、《样品承认书》等进行检验。
并将检验结果应填入《IQC检验报告》。
4.3 检验与判定:4. 3 .1 正常物料IQC应在2个工作日内给出检验结果,单款特急物料应在2个小时内检验完毕.4.3.2判定合格:检验员按《产品标识和可追溯性控制程序》的规定在来料货物外包装上粘贴合格标签,标签内容包括,物料编号、品名规格、数量、检验日期、检验员、供应商名称,并在《IQC检验报告》上签上检验员的名字,通知仓库将合格物料入库。
4.3.3判定不合格检验不合格:IQC将检验报表连同不合格物料样本交MRB评审小组评审。
MRB小组根据实际所需做出:挑选、加工、特采、退货等处理意见,最终由品质经理做最后判定。
再由IQC将不合格处理报表分发给计划、采购各1份。
来料检验及异常处理流程

来料检验及异常处理流程一、来料检验流程:1.接收原材料:当供应商将原材料送到公司时,接收人员负责接收原材料。
他们会核对送货单和实际接收数量,确保一致性。
如果发现数量不一致,则会与供应商协商解决。
2.样品收集:接收人员从接收的原材料中抽取一定数量的样品,确保样品能够全面代表整批原材料。
3.检验依据:根据公司的检验标准和规定,制定检验计划和检验依据,明确要求的检验项目和标准。
4.检验方法选择:根据检验项目的不同性质和要求,选择合适的检验方法,如外观检查、物理性质测试、化学成分分析等。
5.执行检验:根据检验计划和检验依据,实施相应的检验活动。
检验员按照检验方法和标准,对原材料进行检验,并记录检验结果。
6.检验结果评定:根据检验结果和标准,评定原材料是否合格。
如果原材料符合要求,则通过;如果不符合要求,则判定为不合格。
7.合格原材料处理:对于合格的原材料,将其进行封存,并进行标识。
符合要求的原材料可以进入下一道工序使用。
8.不合格原材料处理:对于不合格的原材料,根据具体情况,采取以下措施:返回供应商、报废、返工等。
同时,需要记录不合格原材料的情况并进行归档,以便后续处理。
二、异常处理流程:1.异常检测和发现:在来料检验过程中,如果发现原材料存在异常情况,如外观缺陷、超出标准范围的物理性质、化学成分分析结果与标准不符等,应立即停止检验过程,将异常情况进行记录和报告。
2.异常情况分类:根据异常情况的性质和严重程度,将异常情况进行分类。
如严重影响生产的异常、有风险的异常、可修复的异常等。
3.处理方案制定:根据异常情况的分类和具体情况,制定相应的处理方案。
对于严重影响生产的异常,需要立即停止生产并与供应商协商解决;对于有风险的异常,需要进行风险评估并采取合适的措施进行处理;对于可修复的异常,需要返工或者重新采购原材料。
4.异常情况解决:根据制定的处理方案,采取相应的措施解决异常情况。
如与供应商协商解决问题、制定修复方案并进行返工、重新采购原材料等。
来料异常处理

深圳市保凌影像科技有限公司来料异常处理制度一、目的1. 针对来料异常能快速判定,快速处理2. 明确各责任人,做到事事有人跟进,事事能结案3..做到能事前预防的绝不事后补救4. 不因来料问题处理耽搁而影响生产销售出货二、职责及权力(由各部自行主张填写)职责:IQC:采购:PMC:仓管:权力:IQC:采购:PMC:仓管:三.来料检验及异常判定1.正常来料检验3天内完成检验入库,加急物料及1天内完成检验/判定入库。
2.来料有异常的3天内完成判定并及时出《来料检验报告单》给技转/采购/PMC及品质部签名各自意见,由品质部负责人最终决定如何处理。
3. 针对特殊物料的检测应在做试产及转产时就要提前确认相关准备工作,不可因此而推延做批量生产的来料检验时间4.对于来料不良可挑选/返工使用的来料,由PMC根据生产排期及订单交期进行判定确认是否挑选及退货。
5..来料外观异常因订单交期等需要特采的,由PMC主导协同品质/销售进行确认判定。
涉及功能及结构问题需要特采使用的,由PMC主导协同品质/技转/生产/采购进行确认判定。
6..涉及到退货的必须要有品质/采购/计划/技转签名确认方可执行。
7.每月通报一次所有来料的合格与不合格的批次数据四.来料异常及过程处理的信息传递1.最终确认判定结果的来料异常涉及到挑选/返工/特采的物料IQC需要将《来料检验报告单》分别发送给采购/PMC/技转及生产的对应负责人。
2.最终确认判定结果的来料异常涉及到退货的物料IQC需要将《来料检验报告单》发送给采购/PMC及仓库的对应人3.任何异常来料在处理过程中的异常及结果需及时通报至各对应负责人。
五.来料异常处理的进度跟进1.涉及退货的采购在接到品质部的《来料检验报告单》必须在3天内完成退货事宜,按照PMC要求的返回日期要求供应商进行补货。
2.涉及挑选/返工的采购根据《来料检验报告单》上PMC的要求时间联系供应商来我司按品质要求进行挑选/返工。
供应商来料异常处理程序

供应商来料异常处理程序东莞市安哲罗电子科技有限公司供应商材料异常处理管理流程1. 目的:规范来料产品的异常处理流程控制,提高来料合格率。
2. 范围:本规范适用于所有外购零部件及外包加工件。
3. 职责与权限:3.1生技部:负责检测治具的制作。
3.2质量中心:负责来料异常的提出、分析、处理。
3.3生产部:负责来料异常协助处理。
3.4研发部:负责来料异常的分析、处理。
3.5生管部:负责确认来料品上线使用时间。
3.6采购部:负责来料异常与供应商的纠通取得异常的处理。
4. 名词定义:4.1不合格:未满足产品的质量要求。
4.2 A类:单位产品的极重要质量特性不符合规定,或者单位产品的质量特性极严重不符合规定。
4.3 B类:单位产品的重要质量特性不符合规定,或者单位产品的质量特性严重不符合规定。
4.4 C类:单位产品的一般质量特性不符合规定,或者单位产品的质量特性轻微不符合规定。
5、异常处理流程控制5.1 IQC依据检验指导书、封样、评估报告等资料检验,发现来料品不满足质量要求。
5.2 IQC将自已判定为不合格的产品经工程师、部门主管核对确实为不合格品。
5.3 IQC 立即填写《供应商异常矫正单》进行处理。
5.4 质量中心主管主导组织针对异常讨论,参与人员:采购、PIE、质量中心经理、研发工程师、研发、厂部经理及其相关人员。
6、异常分类:6.1 外观不良:变形,表面有划痕、水印、字体不清、表面气泡、砂眼、黑点、缺料、油污、毛刺、变形、色差、氧化及电镀层脱落、标识规格错误、无料号贴纸、无出厂检验报告等。
6.2性能不良:尺寸与图纸不符、适配过大,过小、色温,波长,亮度不符、电压,电流不符等。
6.3来料不良纠正及预防措施要求6.4非电子件出现功能及其尺寸结构不良超过5%,外观不良超过10%,可靠性不良等于或者超过1PCS。
6.5 电子件出现功能不良及其尺寸不良超过千分之三,外观不良超过1%,可靠性不良等于或者超过1PCS。
- 1、下载文档前请自行甄别文档内容的完整性,平台不提供额外的编辑、内容补充、找答案等附加服务。
- 2、"仅部分预览"的文档,不可在线预览部分如存在完整性等问题,可反馈申请退款(可完整预览的文档不适用该条件!)。
- 3、如文档侵犯您的权益,请联系客服反馈,我们会尽快为您处理(人工客服工作时间:9:00-18:30)。
5.2.3不良物料责任判别为生产损坏。如IQC退料员进行外观检验没有发现外观不良则判定为来料不良,同时将相关记录于《四大件退料报表》。
5.2.4无法进行判定的问题需呈报直属上司MQE进行确认。
本文件属惠州市华屹电子有限公司所有。未经管理者代表批准,禁止复制、泄露和使用。
5.3.4物料数量在15PCS以下,IQC退料员检验员执行全检动作,如物料数量在15PCS以上,则IQC退料员检验员按照GB/T2828.1(0.65/1.0)执行抽检动作;
5.3.5如IQC退料员检验员在退套料过程中发现产线有退混料的情况,立即将套料退产线重新区分;
5.4 检验结果处理
5.4.1IQC退料员退料员依据检验结果,在生产退料单上如实填写相关数据,并加盖IQC退料员退料专用章并在判定好的物料上加贴不合格品标签,须注明料号、不良现象、责任别归属。
5.4.2检验完成后,IQC退料员退料员需将记录的《四大件退料报表》做成电子档,并于每周一早上通过邮件发往相关人员,同时将纸档归档。
5.5 PCBA&LCD、TP、摄像头退料
5.5.1 PCBA退料
5.5.1.1 原则上要求供应商到现场判定;如果供应商到不了,那么就由华屹IQC来判定,IQC判定后需由驻厂客户确认,如驻厂客户不能现场确定,需要支持华屹IQC的决定判定结果。
李田/向科源/贺自洋
□整机生产部
胡碧
□SMT/测试工程部
鲍新峰/章翔
□整机工程部
黄良洪/何昌军
□采购部
任辉
□ 人力资源部
郑娟
□ 财务部
刘庆
□IT部
易建成
文件批准表
姓 名
签 署
日 期
姓 名
签 署
日 期
□ 总经理
肖绪名
□ 环境管理代表
肖绪名
□ 品质管理代表
肖绪名
□部门主管
本文件属惠州市华屹电子有限公司所有。未经管理者代表批准,禁止复制、泄露和使用。
3.2生产损坏
因生产过程中操作不当,造成物料存在缺陷不符合产品质量标准或生产工艺要求。
4职责
4.1IQC退料员负责退料的检验,并及时准确地做好检验的相关记录。
4.2IQC退料员负责退料检验后的责任状态标识。
5内容
5.1 一般物料检验
5.1.1产线执行退料作业,须确认物料实物物料代码、机型、数量,不良内容,供应商,且不良物料本体上必须有不良标识。
5.7.3生产作业导致电子器件装配、使用性能不良做报废。
6相关记录
6.1 《四大件退料报表》
本文件属惠州市华屹电子有限公司所有。未经管理者代表批准,禁止复制、泄露和使用。
文件名称:组装退料流程图
页 次:4/4
文件编号:WI-ZQA-012
生效日期:2014年5月7日
本文件属惠州市华屹电子有限公司所有。未经管理者代表批准,禁止复制、泄露和使用。
文件名称:组装退料检验规定
页 次:4/3
文件编号:WI-ZQA-012
生效日期:2014年5月7日
5.3 套料(良品)退库检验
5.3.1产线执行退料动作,需区分机型,料号。
5.3.2IQC退料员检验员对物料进行外观检验,确认物料是否为良品;
5.3.3IQC退料员检验员在确认套料退库时,首先需要确认此机型是否有替代料的存在,如果存在替代料,则IQC退料员检验员需确认单据上料号,物料上标示料号,实物料号是否一致来判定产线退料是否正确。
5.1.2产线人员输出生产退料单,交送IQC退料员。
5.1.3IQC退料员检验员根据退料单核对实际物料标识及实物,并根据部品上标识的不良现象来判定为何方责任,若发现实际物料不良原因与退料单不符则退回产线重新确认。
5.2四大件退料检验
5.2.1产线执行退料作业,需区分机型,料号,供应商、数量,工程部确认不良现象,并确认签字。
5.5.2LCD退料
5.5.2.1 当不良LCD累积到一定数量后,由IQC工程师通知供应商前来我司进行现场确认。
5.6 不良物料警戒线
5.6.1来料不良警戒线:非让步使用的物料不良>3%
对于来料不良超过警戒线的物料,需通知IQC工程师,由IQC工程师开出《厂商品质改进联络单》知会供应商,并对库存物料进行处理。
文件名称:组装退料检验规定
页 次:4/2
文件编号:WI-ZQA-012
生效日期:2014年5月7日
1目的
为规范本公司IQC退料员退料检验作业方法和流程,对生产过程中不良物料进行有效管制,保证生产顺畅和客户满意,特订此标准。
2适用范围
本作业指导书适用于本公司所有退料检查
3定义
3.1来料不良
客户或供应商提供的物料本身存在缺陷,不符合产品质量标准或生产工艺要求。
文件名称:组装退料检验规定
页 次:4/1
文件编号:WI-ZQA-012
生效日期:2014年5月7日
版本
原作者
生效日期
版本
原作者
生效日期
A0
刘洪锋
2014.5.7
以下由文件编写者填写
以下由文控中心填写
部门
姓 名
签署
日 期
网上更新
姓名
签署
日 期
ZQA
刘洪锋
修 改 记 录
序
页次
最新
版本
修改内容记要
修改者
审核
5.6.2作业不良警戒线:四大物料>0.05%
对于作业不良超过警戒线的物料,IQC知会责任单位和工程部门要求其分析改善。
5.7物料报废基准
5.7.1生产作业导致四大件有以下不良做报废:显示屏破裂、焊接金手指排线掉铜箔、FPC断裂、明显的表面硬划伤;
5.7.2生产作业导致壳料类有以下不良做报废:打花、断裂、穿孔、严重变形、扣位断;
批准
生效
日期
1
2
3
4
5
文件审核表(即需分发的对象部门)
部 门
姓 名
签署
日 期
部 门
姓名
签署
日 期
□总经理
肖绪名
□管理者代表
肖绪名
□PCBA事业部长
袁佑胜
□整机事业部长
□总务部
杨新液
□业务部
Hale Waihona Puke 万科□SMT质量管理部钟德诚
□整机质量管理部
吴能
□SMT计划物控部
尚珍/梁师科
□整机计划物控部
谢治华
□SMT/测试生产部