炼焦生产工艺
焦炉炼焦工艺
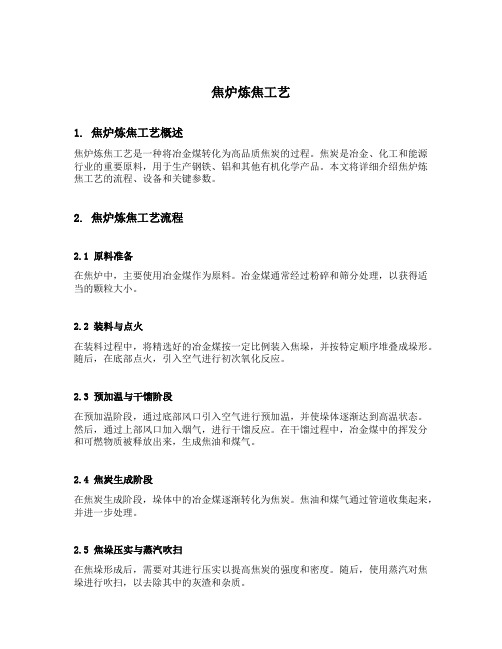
焦炉炼焦工艺1. 焦炉炼焦工艺概述焦炉炼焦工艺是一种将冶金煤转化为高品质焦炭的过程。
焦炭是冶金、化工和能源行业的重要原料,用于生产钢铁、铝和其他有机化学产品。
本文将详细介绍焦炉炼焦工艺的流程、设备和关键参数。
2. 焦炉炼焦工艺流程2.1 原料准备在焦炉中,主要使用冶金煤作为原料。
冶金煤通常经过粉碎和筛分处理,以获得适当的颗粒大小。
2.2 装料与点火在装料过程中,将精选好的冶金煤按一定比例装入焦垛,并按特定顺序堆叠成垛形。
随后,在底部点火,引入空气进行初次氧化反应。
2.3 预加温与干馏阶段在预加温阶段,通过底部风口引入空气进行预加温,并使垛体逐渐达到高温状态。
然后,通过上部风口加入烟气,进行干馏反应。
在干馏过程中,冶金煤中的挥发分和可燃物质被释放出来,生成焦油和煤气。
2.4 焦炭生成阶段在焦炭生成阶段,垛体中的冶金煤逐渐转化为焦炭。
焦油和煤气通过管道收集起来,并进一步处理。
2.5 焦垛压实与蒸汽吹扫在焦垛形成后,需要对其进行压实以提高焦炭的强度和密度。
随后,使用蒸汽对焦垛进行吹扫,以去除其中的灰渣和杂质。
2.6 卸料与冷却最后,在一定时间内完成焦化过程后,将形成的焦炭从焦垛中卸出,并送入冷却塔进行快速冷却。
冷却后的焦炭即可用于下游工艺。
3. 焦炉设备3.1 焦垛焦垛是用于装载冶金煤并进行干馏反应的装置。
它通常由耐火材料构成,具有一定的孔隙结构,以便于煤气和焦油的顺利流出。
3.2 风口风口用于控制空气的进入和排出。
它分为底部风口和上部风口,分别用于预加温和干馏阶段的空气供应。
3.3 管道系统管道系统用于收集焦油和煤气,并将其送往后续处理设备。
它包括主管道、分支管道和收集器等组成部分。
3.4 冷却塔冷却塔用于将炼焦过程中产生的煤气快速冷却,以使其中的焦油凝结并收集起来。
冷却塔通常由多级塞式冷却器组成。
4. 焦炉关键参数4.1 温度在焦炉炼焦过程中,温度是一个重要的参数。
适当的温度可以促进冶金煤中挥发分的释放和焦炭生成反应的进行。
炼焦车间工艺流程

炼焦车间工艺流程炼焦车间是冶金生产过程中的重要环节,主要负责将煤炭转化为高热值焦炭。
本文将介绍炼焦车间的工艺流程,包括煤炭处理、焦炉炼焦、焦炭处理和环保措施等。
一、煤炭处理煤炭是炼焦车间的原料,煤种的选择和煤炭质量的分析十分重要。
首先,通过采样车对原料煤进行采样并送至实验室进行化验,确保煤炭的质量符合炼焦要求。
然后,将煤炭送至煤炭仓库,并采用堆煤或者装车的方式储存。
在进入焦炉炼焦前,还需要对煤炭进行破碎、筛分和除尘等处理。
二、焦炉炼焦1.炉前准备焦炉炼焦过程的开始是进行炉前准备工作。
首先,需要点火炉,使焦炉内部温度升高到适宜的炼焦温度。
然后,将预先破碎和筛分好的煤炭装入焦炉的炉膛中,并通过矿泉水进行浇水封固。
2.爆破与变形在焦炉内,煤炭在高温条件下经历爆破与变形的过程。
首先,煤炭在炉膛中被热融露水气化产生一氧化碳,同时放出大量的热量;然后,在高温下,煤炭中的固定碳燃烧形成煤气;最后,煤气通过炼化管排出焦炉。
3.除渣与配风焦炉内部的煤渣会随着冷凝器中凝结水的排放而流出炉外。
炉渣经后处理可再细化为微粒状焦粉。
配风是为了提供足够的氧气支持煤炭燃烧和蒸发,通过压排风机将新风吹入到炉膛和燃烧室中。
三、焦炭处理经过一定时间的炼焦,焦炉内的煤炭会经过焦化过程变成焦炭。
焦炭处理包括降温、除尘、分级和包装等环节。
首先,焦炭从焦炉中排出后需要进行降温,以防止炭块自燃。
然后,通过除尘设备对炼焦过程中产生的粉尘进行收集和处理。
接下来,焦炭会经过粒度分级,筛分出符合要求的炭块。
最后,经过包装,焦炭可以进行储存和运输。
四、环保措施炼焦车间是一个高污染的作业场所,所以环保措施是必不可少的。
首先,焦炉应配备炉渣处理设备,将产生的炉渣经过除渣设施进行处理,防止对环境造成污染。
其次,焦炉煤气通过炼化管进入冷凝器冷却凝结后,再经过除尘设备进行治理。
此外,焦炉应配备高效的除尘设备,对散发的粉尘进行收集和处理。
另外,焦炭处理环节也需要配备相应的除尘设备。
炼焦车间工艺流程
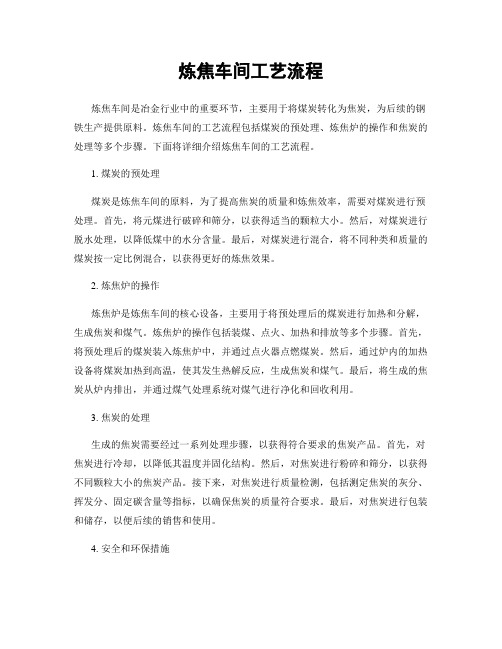
炼焦车间工艺流程炼焦车间是冶金行业中的重要环节,主要用于将煤炭转化为焦炭,为后续的钢铁生产提供原料。
炼焦车间的工艺流程包括煤炭的预处理、炼焦炉的操作和焦炭的处理等多个步骤。
下面将详细介绍炼焦车间的工艺流程。
1. 煤炭的预处理煤炭是炼焦车间的原料,为了提高焦炭的质量和炼焦效率,需要对煤炭进行预处理。
首先,将元煤进行破碎和筛分,以获得适当的颗粒大小。
然后,对煤炭进行脱水处理,以降低煤中的水分含量。
最后,对煤炭进行混合,将不同种类和质量的煤炭按一定比例混合,以获得更好的炼焦效果。
2. 炼焦炉的操作炼焦炉是炼焦车间的核心设备,主要用于将预处理后的煤炭进行加热和分解,生成焦炭和煤气。
炼焦炉的操作包括装煤、点火、加热和排放等多个步骤。
首先,将预处理后的煤炭装入炼焦炉中,并通过点火器点燃煤炭。
然后,通过炉内的加热设备将煤炭加热到高温,使其发生热解反应,生成焦炭和煤气。
最后,将生成的焦炭从炉内排出,并通过煤气处理系统对煤气进行净化和回收利用。
3. 焦炭的处理生成的焦炭需要经过一系列处理步骤,以获得符合要求的焦炭产品。
首先,对焦炭进行冷却,以降低其温度并固化结构。
然后,对焦炭进行粉碎和筛分,以获得不同颗粒大小的焦炭产品。
接下来,对焦炭进行质量检测,包括测定焦炭的灰分、挥发分、固定碳含量等指标,以确保焦炭的质量符合要求。
最后,对焦炭进行包装和储存,以便后续的销售和使用。
4. 安全和环保措施在炼焦车间的工艺流程中,安全和环保是非常重要的考虑因素。
为了确保工人的安全,需要提供必要的个人防护设备,并对操作人员进行培训和指导。
此外,还需要定期检查和维护设备,确保其正常运行。
在环保方面,需要采取措施减少炼焦过程中产生的废气和废水的排放,并对废气和废水进行处理,以符合环保要求。
总结:炼焦车间的工艺流程包括煤炭的预处理、炼焦炉的操作和焦炭的处理等多个步骤。
通过对煤炭的预处理和炼焦炉的操作,将煤炭转化为焦炭和煤气。
焦炭经过冷却、粉碎、筛分和质量检测等步骤后,最终得到符合要求的焦炭产品。
炼焦车间工艺流程

炼焦车间工艺流程炼焦车间是钢铁生产过程中不可或者缺的重要环节,它承担着将原料焦炭转化为高质量冶金焦的关键任务。
下面将详细介绍炼焦车间的工艺流程。
1. 原料准备阶段:在炼焦车间工艺流程中,首先需要准备适量的原料,主要包括煤炭和其他辅助材料。
煤炭是焦炭的主要原料,其品质直接影响最终冶金焦的质量。
因此,在原料准备阶段,需要对煤炭进行筛分、破碎和混合,以确保煤质的均匀性和合理的粒度分布。
2. 炼焦炉装料阶段:在炼焦车间工艺流程中的下一个阶段是炼焦炉的装料。
装料是将预处理好的煤炭和辅助材料按一定的配比装入炼焦炉中。
装料时需要注意控制装料的均匀性和密实度,以确保炼焦炉内的煤炭可以充分反应,同时避免炉内温度分布不均和结焦现象的发生。
3. 炼焦炉炼焦阶段:在炼焦车间工艺流程中的核心阶段是炼焦炉的炼焦过程。
炼焦炉是一个高温、高压的环境,通过控制炉内的温度、压力温和氛等参数,使煤炭在炉内发生热解和化学反应,生成焦炭和煤气。
炼焦炉内的炼焦过程通常分为干燥、预热、软化、焦化和冷却等多个阶段。
在每一个阶段中,需要严格控制炉内的温度、压力温和氛等参数,以确保焦炭的质量和产量达到预期要求。
4. 焦炭处理阶段:在炼焦车间工艺流程的最后阶段是对产出的焦炭进行处理。
焦炭处理主要包括焦炭的降温、除尘、筛分和质量检测等环节。
焦炭降温是将高温焦炭通过冷却设备降温至室温,以便后续的处理和运输。
焦炭除尘是通过除尘设备去除焦炭表面的灰尘和杂质,提高焦炭的纯度和质量。
焦炭筛分是将焦炭按照一定的粒度分布进行分级,以满足不同工艺和应用的需求。
焦炭质量检测是通过各种物理和化学分析方法对焦炭的质量进行检测和评估,以确保焦炭符合生产和应用的要求。
综上所述,炼焦车间的工艺流程包括原料准备、炼焦炉装料、炼焦炉炼焦和焦炭处理等多个阶段。
每一个阶段都需要严格控制各项工艺参数,以确保焦炭的质量和产量达到预期要求。
通过科学的工艺流程和精细的操作管理,炼焦车间能够稳定高效地生产出高质量的冶金焦,为钢铁生产提供可靠的原料保障。
炼焦车间工艺流程
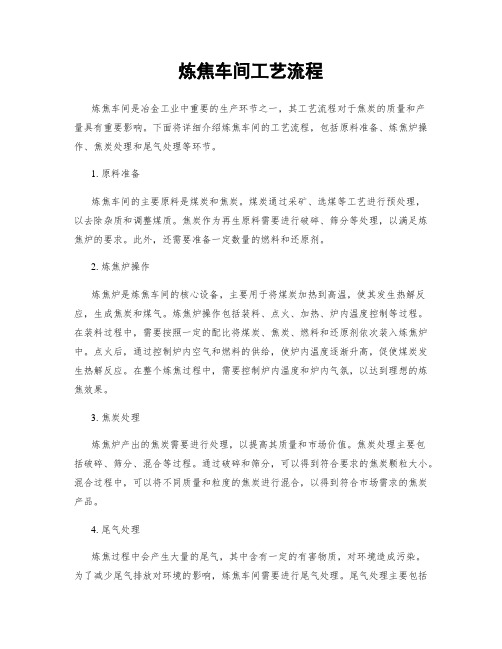
炼焦车间工艺流程炼焦车间是冶金工业中重要的生产环节之一,其工艺流程对于焦炭的质量和产量具有重要影响。
下面将详细介绍炼焦车间的工艺流程,包括原料准备、炼焦炉操作、焦炭处理和尾气处理等环节。
1. 原料准备炼焦车间的主要原料是煤炭和焦炭。
煤炭通过采矿、选煤等工艺进行预处理,以去除杂质和调整煤质。
焦炭作为再生原料需要进行破碎、筛分等处理,以满足炼焦炉的要求。
此外,还需要准备一定数量的燃料和还原剂。
2. 炼焦炉操作炼焦炉是炼焦车间的核心设备,主要用于将煤炭加热到高温,使其发生热解反应,生成焦炭和煤气。
炼焦炉操作包括装料、点火、加热、炉内温度控制等过程。
在装料过程中,需要按照一定的配比将煤炭、焦炭、燃料和还原剂依次装入炼焦炉中。
点火后,通过控制炉内空气和燃料的供给,使炉内温度逐渐升高,促使煤炭发生热解反应。
在整个炼焦过程中,需要控制炉内温度和炉内气氛,以达到理想的炼焦效果。
3. 焦炭处理炼焦炉产出的焦炭需要进行处理,以提高其质量和市场价值。
焦炭处理主要包括破碎、筛分、混合等过程。
通过破碎和筛分,可以得到符合要求的焦炭颗粒大小。
混合过程中,可以将不同质量和粒度的焦炭进行混合,以得到符合市场需求的焦炭产品。
4. 尾气处理炼焦过程中会产生大量的尾气,其中含有一定的有害物质,对环境造成污染。
为了减少尾气排放对环境的影响,炼焦车间需要进行尾气处理。
尾气处理主要包括除尘、脱硫、脱氨等过程。
通过除尘设备,可以去除尾气中的颗粒物;脱硫和脱氨过程则可以去除尾气中的硫化物和氨等有害物质。
总结:炼焦车间的工艺流程包括原料准备、炼焦炉操作、焦炭处理和尾气处理等环节。
在原料准备过程中,需要对煤炭和焦炭进行预处理。
炼焦炉操作是炼焦车间的核心环节,通过控制炉内温度和气氛,使煤炭发生热解反应,生成焦炭和煤气。
焦炭处理过程主要包括破碎、筛分和混合等步骤,以提高焦炭的质量和市场价值。
尾气处理是为了减少炼焦过程中产生的尾气对环境的污染,通过除尘、脱硫和脱氨等过程,去除尾气中的有害物质。
炼焦车间工艺流程
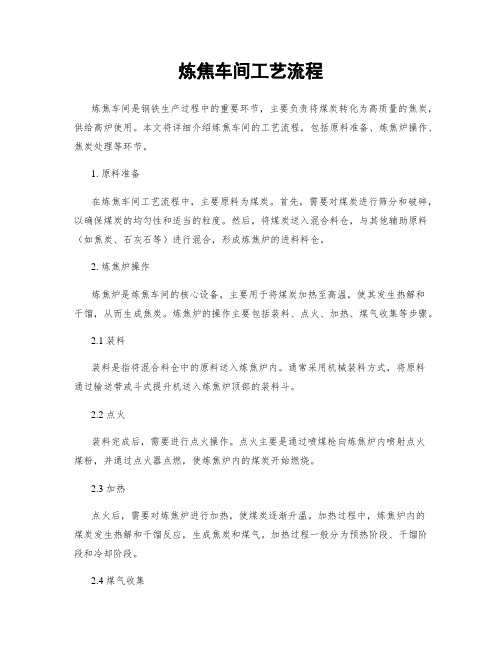
炼焦车间工艺流程炼焦车间是钢铁生产过程中的重要环节,主要负责将煤炭转化为高质量的焦炭,供给高炉使用。
本文将详细介绍炼焦车间的工艺流程,包括原料准备、炼焦炉操作、焦炭处理等环节。
1. 原料准备在炼焦车间工艺流程中,主要原料为煤炭。
首先,需要对煤炭进行筛分和破碎,以确保煤炭的均匀性和适当的粒度。
然后,将煤炭送入混合料仓,与其他辅助原料(如焦炭、石灰石等)进行混合,形成炼焦炉的进料料仓。
2. 炼焦炉操作炼焦炉是炼焦车间的核心设备,主要用于将煤炭加热至高温,使其发生热解和干馏,从而生成焦炭。
炼焦炉的操作主要包括装料、点火、加热、煤气收集等步骤。
2.1 装料装料是指将混合料仓中的原料送入炼焦炉内。
通常采用机械装料方式,将原料通过输送带或斗式提升机送入炼焦炉顶部的装料斗。
2.2 点火装料完成后,需要进行点火操作。
点火主要是通过喷煤枪向炼焦炉内喷射点火煤粉,并通过点火器点燃,使炼焦炉内的煤炭开始燃烧。
2.3 加热点火后,需要对炼焦炉进行加热,使煤炭逐渐升温。
加热过程中,炼焦炉内的煤炭发生热解和干馏反应,生成焦炭和煤气。
加热过程一般分为预热阶段、干馏阶段和冷却阶段。
2.4 煤气收集在加热过程中,煤炭发生热解和干馏反应产生的煤气需要进行收集和处理。
煤气主要通过炼焦炉顶部的煤气管道收集,并经过净化处理后,用于供给其他工序或外部能源利用。
3. 焦炭处理焦炭是炼焦车间的主要产品,需要进行一系列处理操作,以提高其质量和利用价值。
3.1 焦炭出炉在炼焦炉冷却阶段结束后,焦炭会从炼焦炉底部自动排出。
焦炭的出炉温度较高,需要进行冷却处理,以避免自燃。
3.2 焦炭筛分出炉的焦炭通常会经过筛分操作,将不同粒度的焦炭分离。
不同粒度的焦炭可用于不同用途,如高炉煤气化、铁合金生产等。
3.3 焦炭质量检测为确保焦炭质量符合要求,需要进行质量检测。
常见的检测指标包括焦炭灰分、挥发分、固定碳含量等。
检测结果将作为焦炭质量的依据,决定其使用范围和市场价值。
炼焦车间工艺流程
炼焦车间工艺流程炼焦车间是冶金工业中的重要环节,用于将煤炭转化为焦炭,为后续的钢铁生产提供原料。
炼焦车间的工艺流程包括煤炭的选矿、破碎、炼焦和焦炭的处理等多个步骤。
下面将详细介绍炼焦车间的工艺流程。
1. 煤炭选矿:煤炭选矿是将从煤矿中采集的原煤进行筛分和洗选,以去除其中的杂质和硫磷等有害物质。
首先,原煤经过振动筛进行初步的筛分,将大块的煤炭分离出来。
然后,通过浮选机进行浮选,将煤炭和石灰石等杂质分离。
最后,通过重介质分选,根据煤炭的比重差异将煤炭和岩石等进一步分离,得到符合要求的煤炭。
2. 煤炭破碎:经过选矿的煤炭需要进行破碎,以便更好地进行后续的焦化处理。
煤炭破碎一般采用颚式破碎机和辊式破碎机。
首先,将选矿后的煤炭送入颚式破碎机,通过颚板的压力将煤炭破碎成适当的颗粒大小。
然后,将颚碎机破碎后的煤炭送入辊式破碎机,通过辊子的旋转将煤炭进一步破碎成所需的颗粒大小。
3. 炼焦:炼焦是将煤炭在高温下进行加热,使其分解生成焦炭的过程。
炼焦一般分为干炼和湿炼两种方式。
干炼是指将煤炭直接放入焦炉进行加热,湿炼是指将煤炭预先进行水洗后再进行加热。
无论是干炼还是湿炼,炼焦过程中都需要控制温度、时间和煤炭的进料量等参数,以确保焦炭的质量。
炼焦过程中会产生大量的煤气和焦炉煤气,需要进行收集和处理。
4. 焦炭处理:焦炭处理是指对炼焦产生的焦炭进行筛分、冷却和质量检测等工序。
首先,将炼焦产生的焦炭送入筛分机,将焦炭按照不同的颗粒大小进行分级。
然后,将分级后的焦炭送入冷却塔进行冷却,以降低焦炭的温度。
最后,对冷却后的焦炭进行质量检测,包括测定焦炭的灰分、挥发分、固定碳等指标,以确保焦炭的质量符合要求。
总结:炼焦车间的工艺流程包括煤炭选矿、破碎、炼焦和焦炭处理等多个步骤。
通过煤炭选矿,可以去除煤炭中的杂质和有害物质,得到符合要求的煤炭。
煤炭破碎将选矿后的煤炭破碎成所需的颗粒大小。
炼焦过程中,煤炭在高温下分解生成焦炭,需要控制温度、时间和煤炭的进料量等参数。
炼焦工艺及流程
炼焦工艺简介1.备煤2.捣固炼焦由备煤车间来的洗精煤,由输煤栈桥运入煤塔,装煤车行至煤塔下方, 由摇动给料机均匀逐层给料, 用排锤移动捣固机分层捣实, 然后将捣好的煤饼从机侧装入炭化室。
煤饼在950~1050℃的温度下高温干馏, 经过~22.5小时后, 成熟的焦炭从炭化室推出,经干熄焦系统冷却后由专用皮带运输机运出。
干馏过程中产生的荒煤气经炭化室顶部、上升管、桥管汇入集气管,经吸气弯管和吸气管抽吸至冷鼓工段。
在集气管内冷凝下来的焦油和氨水经焦油盒、吸气主管一起至冷鼓工段。
推焦过程中逸散的粉尘由管道抽吸至设在焦侧的预留出焦地面除尘站, 经站内的布袋除尘器除尘后排入大气。
装煤过程中逸散的荒煤气由设在炉顶的消烟除尘车抽吸至车上的燃烧室燃烧, 燃烧后的废气经车上的文丘里洗涤器, 将废气中的粉尘洗下来,排入大气。
洗涤水送至除尘车下水槽至粉焦沉淀池沉淀分离后回用。
焦炉加热用回炉煤气由外管送至焦炉,经煤气总管、煤气预热器、主管、煤气支管进入各燃烧室,在燃烧室内与经过蓄热室预热的空气混合燃烧,混合后的煤气、空气在燃烧室由于部分废气循环,使火焰加长, 使高向加热更加均匀合理,燃烧烟气温度可达~1200℃, 燃烧后的废气经跨越孔、立火道、斜道,在蓄热室与格子砖换热后经分烟道、总烟道,最后从烟囱排出。
3.熄焦4.筛贮焦焦炉生产的焦炭,经干熄焦后由带式输送机送至筛焦楼。
焦炭通过筛分,分为>40mm和<40mm二级,>40mm的焦炭经过溜槽由带式输送机及可逆配仓带式输送机卸入焦仓内贮存。
<40mm 的焦炭则直接经过溜槽进入1530双层振动筛,将其分为40~25mm、25~10mm、<10mm三级,5.冷鼓、电捕脱除焦油及萘焦油产品规格表(表2-2)②煤气干煤气量:45400Nm3/h煤气温度:~34℃煤气压力:~0.017MPa干煤气中的杂质含量表(表2-3)③剩余氨水 (中间产品):产量: 20400kg/h氨水组成表(表2-4)6.脱硫及硫的回收本工段包括脱硫、硫回收及剩余氨水三部分。
炼焦车间工艺流程
炼焦车间工艺流程炼焦车间是钢铁生产过程中的重要环节,它是将煤炭转化为焦炭的关键部门。
炼焦车间工艺流程是指在炼焦车间内进行的一系列操作和步骤,以确保高质量的焦炭产出。
下面将详细介绍炼焦车间工艺流程的标准格式文本。
1. 原料准备炼焦车间的原料主要包括煤炭、蒸汽和空气。
首先,煤炭被送入煤仓,并通过输送带或装载机送入煤炭破碎机进行粉碎。
然后,粉碎后的煤炭被输送到煤炭筛分系统,以去除杂质并分级。
最后,符合要求的煤炭被送入配煤系统,按照一定比例混合。
2. 炼焦炉装料配制好的煤炭混合料被送入炼焦炉,装料过程中需要遵循一定的装料规则和技术要求。
装料时,将煤炭混合料均匀地分布在炉膛内,以确保炉内温度和气体分布的均匀性。
3. 炉内加热装料完成后,炼焦炉被密封,进入加热阶段。
炉内加热是通过燃烧炉内的煤气来提供热量的。
煤气通过炉顶的管道进入炉内,与煤炭混合料反应产生高温,使煤炭逐渐升温,发生干馏反应。
4. 炉内干馏在炼焦炉内,煤炭经历干馏过程,即在高温下分解产生气体、液体和固体产物。
干馏过程中,煤炭中的挥发分被释放出来,形成焦炉煤气。
焦炉煤气主要由一氧化碳、氢气和烃类组成,可以用于发电或其他用途。
5. 焦炭产出在炉内干馏的过程中,煤炭逐渐转化为焦炭。
焦炭是一种坚固、多孔的物质,具有高热值和良好的机械强度。
焦炭通过炉底的焦渣口排出,并经过冷却、处理和筛分等工艺步骤后,最终得到高质量的焦炭产品。
6. 炉内除渣在炉内干馏过程中,煤炭中的杂质和灰分会形成焦渣。
为了保证炼焦炉的正常运行,需要定期进行焦渣清除。
焦渣会通过炉底的渣口排出,然后经过冷却和处理,最终得到焦渣产品。
7. 炉内冷却焦炭产出后,需要进行冷却处理。
冷却过程是通过喷水或喷雾装置将冷却介质喷洒到焦炭表面,以降低焦炭温度。
冷却后的焦炭可以更容易地进行处理和筛分。
8. 焦炭处理和筛分冷却后的焦炭需要进行处理和筛分,以去除杂质并得到符合要求的焦炭产品。
焦炭处理包括焦炭破碎、除尘和炭化等工艺。
炼焦车间工艺流程
炼焦车间工艺流程1. 炼焦车间概述炼焦车间是钢铁生产过程中的重要环节,主要负责将煤炭转化为高质量的焦炭。
炼焦车间工艺流程包括原料准备、炉前操作、炉内炼焦、炉后处理等环节。
2. 原料准备炼焦车间的主要原料是冷煤、热煤和焦炭。
冷煤是指从煤矿中开采出来的原始煤炭,经过破碎、筛分等处理后,成为炼焦炉的原料。
热煤是指经过预处理的冷煤,包括热解、干燥等工序。
焦炭则是炼焦炉产生的终产品。
3. 炉前操作炉前操作是指对原料进行预处理,以确保炼焦过程的顺利进行。
主要包括煤炭的破碎、混合和配料等工序。
破碎是将原料煤炭进行粉碎,以增加其表面积,便于燃烧和气化。
混合是将不同种类和质量的煤炭进行混合,以获得更好的炼焦效果。
配料是按照一定比例将混合后的煤炭送入炼焦炉。
4. 炉内炼焦炉内炼焦是指将配料的煤炭送入炼焦炉内进行加热和气化的过程。
炼焦炉一般采用焦炉煤气和煤气发生炉两种方式进行加热。
在加热过程中,煤炭中的挥发分开始释放,产生的气体经过冷却和净化后,变成焦炉煤气。
同时,煤炭中的焦炭开始形成,经过一段时间的炼焦后,炉内的焦炭达到一定质量和数量。
5. 炉后处理炉后处理是指对炼焦炉产生的焦炭进行处理,以获得高质量的焦炭产品。
主要包括焦炭的冷却、粉碎、筛分和质量检测等工序。
焦炭的冷却是将炉内的焦炭经过冷却器冷却至室温,以防止其继续燃烧。
冷却后的焦炭经过粉碎和筛分,得到不同粒度的焦炭产品。
最后,对焦炭进行质量检测,包括灰分、挥发分、固定碳等指标的检测。
6. 炼焦车间的安全措施炼焦车间是一个高温、高压、易燃易爆的工作环境,需要严格遵守安全规程和操作规范。
炼焦车间应配备消防设备,定期进行消防演习和安全培训。
同时,操作人员应佩戴适当的防护装备,如防火服、安全帽、耐高温手套等。
车间内应设置安全警示标识,明确危险区域和禁止行为。
定期检查和维护设备,确保其正常运行和安全使用。
以上是对炼焦车间工艺流程的详细描述。
炼焦车间的工艺流程涉及到多个环节,每个环节都有其特定的操作和要求。
- 1、下载文档前请自行甄别文档内容的完整性,平台不提供额外的编辑、内容补充、找答案等附加服务。
- 2、"仅部分预览"的文档,不可在线预览部分如存在完整性等问题,可反馈申请退款(可完整预览的文档不适用该条件!)。
- 3、如文档侵犯您的权益,请联系客服反馈,我们会尽快为您处理(人工客服工作时间:9:00-18:30)。
谢谢大家
推焦串序 焦炉推焦要按一定串序进行。推焦串序通常 表示为m——n串序 ,m代表相邻两次推焦间隔 的炉孔数;n 代表两趟笺号对应炭化室号相隔的 数。 生产上采用的串序有9-2串序,5-2串序和2-1串 序。目前我们炼焦车间采用的是5-2串序。
湿法熄焦
本工程采用新型湿法熄焦系统。该湿 法熄焦系统具有如下优点: a)熄焦时间短,熄焦时间可控制在7080s; b)熄焦后的焦炭水分可控制在2-4%而 且水分稳定; c)熄焦塔上设有水雾捕集装置及折流 式木结构的除尘装置,除尘效果好。
经拦焦机导入湿熄焦车内,由电机车牵 引熄焦车至熄焦塔内进行喷水熄焦。熄 焦后的焦炭卸至凉焦台上,冷却一定时 间后送往筛贮焦工段进行筛分。
煤在炭化室干馏过程中产生的荒煤气汇
集到炭化室顶部空间,经上升管、桥管 进入集气管,约800℃左右的荒煤气在 桥管内被氨水喷洒冷却至85℃左右。荒 煤气中的焦油等同时被冷凝下来。煤气 和冷凝下来的焦油同氨水一起经吸煤气 管道送入煤气净化车间。
2 炼焦工艺
由备煤车间送来的能满足炼焦要求 的配合煤装入煤塔。通过摇动给料器 将煤装入装煤车的煤箱内(下煤不畅时, 采用风力震煤措施),并将煤捣固成煤 饼,装煤车按作业计划将煤饼从机侧 送入炭化室内。煤饼在炭化室内经过 一个结焦周期的高温干馏炼制成焦炭 和荒煤气。
炭化室内的焦炭成熟后,用推焦机推出,
1.2 炉体主要尺寸
序号 1 2 3 名称 单位 数量
炭化室全长 炭化室全高
炭化室平均宽 炭化室锥度 炭化室中心距 燃烧室立火道中心距 燃烧室立火道个数 加热水平
mm mm
mm mm mm mm 个 mm
15980 5550
554 20 1350 480 32 806
4
5 6 7
8
1.3炼焦主要设备
炼焦设备主要包括“四车一机”,即: 装煤车、推焦车、拦焦车、熄焦车和交 换机。 分护炉设备和煤气设备两大类,其 中护炉设备包括:保护板、炉门框、炉 柱;煤气设备包括:上升管、集气管、 加热煤气导入系统、废气开闭器、交换 系统等。
Байду номын сангаас
第二节 工艺概况
1 概况 2 炼焦工艺
3推焦串序
1 概况
炼焦生产工艺
梅立军
内容介绍
第一节 焦炉基本结构 与炉体主要尺寸 第二节 工艺概况
第三节 熄焦工艺
第一节 焦炉基本结构 与炉体主要尺寸
焦炉基本结构 焦炉主要尺寸
焦炉主要设备
1.1 焦炉基本结构
炼焦炉由炭化室、燃烧室、蓄热室、斜 道区和炉顶区所组成,蓄热室以下为基础和 烟道。 (1)炭化室和燃烧室 炭化室是煤隔绝空气干馏的地方;燃烧 室是煤气燃烧的地方。两者依次相间。 为顺利推焦,炭化室水平截面呈梯形, 也就是说,从机侧向焦侧看去,焦侧宽度大 于机侧,两侧宽度之差称锥度。
推焦计划系数K1——标志着推焦计划表中的计划结焦时间与 规定结焦时间相吻合的情况。 K1 = (M-A1)/ M 式中:M---班计划推焦炉数。 A1---计划与规定结焦时间相差±5分钟以上的炉数。 推焦执行系数K2——用以评定该班按推焦计划实际执行的情 况。 K2 = (N—A2)/ M 式中:N---班实际推焦炉数 A2---超过计划推焦时间±5分钟的炉数 推焦系数K3——用以评定焦化厂及炼焦车间在遵守规定结焦 时间和实际生产操作方面的管理水平。 K3=K1×K2
湿法熄焦系统包括熄焦泵房、熄焦塔、熄 焦喷洒管、水雾捕集装置、折流板式除尘 装置、粉焦沉淀池、清水池、粉焦脱水台 和双梁抓斗起重机、一点定位熄焦车、高 位槽及自动控制系统等。
湿法熄焦工艺,在整个熄焦过程中下水
量是分段进行的。熄焦过程初期,先用 小水量熄灭熄焦车厢顶层红焦并稳定了 焦炭表面,持续一段时间后,再喷射大 水量,水与炽热焦炭接触后产生的蒸气 “由下至上”地熄灭熄焦车内底部、中 部及中上部的焦炭。这种熄焦方式用大 水流喷射代替了喷洒,改善了熄焦车厢 内沿焦炭深度方向上的水份分布,达到 了缩短熄焦时间、降低焦炭水份的目的。
燃烧室的机、焦侧宽度恰好相反,故机焦 两侧炭化室中心距相同。 燃烧室顶盖高度低于炭化室顶,二者之差 称加热水平高度。
(2)斜道区 位于蓄热室和燃烧室之间,是连接该两者 的通道。
(3)蓄热室 位于焦炉炉体下部,其上经斜道同燃烧 室相连,其下经废气盘分别同分烟道、贫煤 气管道和大气相通。蓄热室用来回收焦炉燃 烧废气的热量并预热贫煤气和空气。 (4)炉顶区 是指炭化室顶盖砖以上的部位,设有装 煤孔、上升管孔、看火孔、烘炉孔和拉条沟 。
焦炉加热用的焦炉煤气,由外部管道架空引 入。分别进入每座焦炉的焦炉煤气经预热器 预热至45℃左右送入地下室,通过下喷管把
煤气送入燃烧室立火道与从废气开闭器进入 的空气汇合燃烧。燃烧后的废气通过立火道 顶部跨越孔进入下降气流的立火道,再经过 蓄热室,由格子砖把废气的部分显热回收后 经过小烟道、废气交换开闭器、分烟道、总 烟道、烟囱,排入大气。上升气流的煤气和 空气与下降气流的废气由交换传动装置定时 进行换向。
炼焦生产中的几个时间概念: 推焦时间:指推焦杆头接触焦饼表面的时间。 装煤时间:平煤杆进入炭化室的时间,平煤在4~6分
钟内完成。 结焦时间:煤料在炭化室停留时间,通常指从开始装 煤到开始推焦的时间间隔。 炭化室处理时间:指炭化室从开始推焦到开始平煤的 时间间隔。 单孔操作时间:焦炉机械完成一孔炭化室全部操作所 需的时间。 周转时间:一个炭化室从本次推焦(或装煤)到下一 次推焦(或装煤)的时间间隔。对全炉而言,周转时 间=全炉操作时间+检修时间;对某个炭化室而言,周 转时间=结焦时间+炭化室处理时间。
宁夏宝丰能源集团有限公司二期焦化新建焦炉及配套工 程设计规模为年产焦炭260万t,采用4×65孔JNDK5507型炭化室高5.5m单热式捣固焦炉。4×65孔焦炉布 置在一条中心线上,采用单集气管(设在焦侧)、双 吸气管。与4×65孔焦炉分别配套各建设一套新型湿 法熄焦系统及迁车台,预留干熄焦位置。装煤除尘采 用双U型管导烟车配合高压氨水,将装煤产生的烟尘 导到第n+2孔和第n-1孔炭化室,并把炉头烟通过机侧 装煤集尘干管送往地面站。出焦除尘和焦侧炉头烟采 用地面站除尘方式。