数控加工工艺过程卡
数控车削加工工艺卡片

夹具名称
夹具号
工序名称
工序号
程序编号
材料牌号
换刀方式
序号
工艺内容
刀具号
刀具名称及规格
刀具参数
S
F
ap
刀补
刀偏号
r/min
mm/min
mm
数控车削加工工艺卡片
零件图号
零件名称
毛坯尺寸
毛坯种类
备注
车间名称
设备名称
设备号
夹具名称
夹具号
工序名称
工序号
程序编号
材料牌号
换刀方式
自动换刀
序号
工艺内容
刀具号
刀具名称及规格
刀具参数
S
F
ap
刀补号
刀偏号
r/min
mm/min
mm
数控车削加工工艺卡片-2
零件图号
零件名称
毛坯尺寸
毛坯种类
备注
车间名称
设备名称
机械加工工艺过程卡片与工序卡片
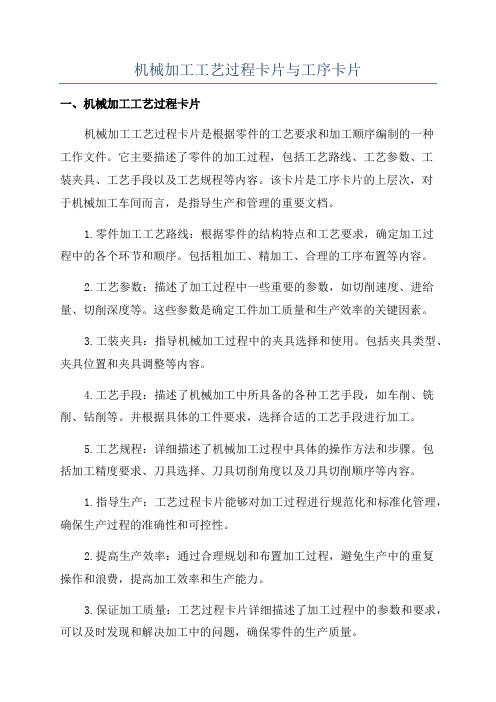
机械加工工艺过程卡片与工序卡片一、机械加工工艺过程卡片机械加工工艺过程卡片是根据零件的工艺要求和加工顺序编制的一种工作文件。
它主要描述了零件的加工过程,包括工艺路线、工艺参数、工装夹具、工艺手段以及工艺规程等内容。
该卡片是工序卡片的上层次,对于机械加工车间而言,是指导生产和管理的重要文档。
1.零件加工工艺路线:根据零件的结构特点和工艺要求,确定加工过程中的各个环节和顺序。
包括粗加工、精加工、合理的工序布置等内容。
2.工艺参数:描述了加工过程中一些重要的参数,如切削速度、进给量、切削深度等。
这些参数是确定工件加工质量和生产效率的关键因素。
3.工装夹具:指导机械加工过程中的夹具选择和使用。
包括夹具类型、夹具位置和夹具调整等内容。
4.工艺手段:描述了机械加工中所具备的各种工艺手段,如车削、铣削、钻削等。
并根据具体的工件要求,选择合适的工艺手段进行加工。
5.工艺规程:详细描述了机械加工过程中具体的操作方法和步骤。
包括加工精度要求、刀具选择、刀具切削角度以及刀具切削顺序等内容。
1.指导生产:工艺过程卡片能够对加工过程进行规范化和标准化管理,确保生产过程的准确性和可控性。
2.提高生产效率:通过合理规划和布置加工过程,避免生产中的重复操作和浪费,提高加工效率和生产能力。
3.保证加工质量:工艺过程卡片详细描述了加工过程中的参数和要求,可以及时发现和解决加工中的问题,确保零件的生产质量。
4.节约成本:通过合理设置工艺参数和工装夹具,可以降低加工成本,提高资源利用率。
二、工序卡片工序卡片是机械加工过程中的一种重要记录和指导工具。
它是对机械加工工艺过程卡片的细化和补充,更加具体地描述了每个工序的加工方法、操作顺序和操作要点等内容。
工序卡片的主要内容包括以下几个方面:1.工序顺序:描述了每个工序的顺序和次序。
2.加工设备:说明了该工序需要使用的设备和机床。
3.刀具选择:选择适合于该工序的刀具,并给出刀具的尺寸和规格。
4.工装夹具:描述该工序中使用的夹具类型和夹具的调整方法。
数控加工工艺过程卡

7、钻2-Ф8的锥销孔
麻花钻Ф8
8、钻螺纹5-M8-6H深18和14-M8-6H深15的中心孔
中心钻Ф6
9、扩螺纹5-M8-6H深18和14-M8-6H深15的中心孔至
扩孔刀Ф7
10、攻螺纹5-M8-6H深18和14-M8-6H深15
Ф8的丝锥
11、钻锥销孔2-Ф12的中心孔
麻花钻Ф10
12、精铰孔2-Ф12的中心孔至尺寸 保证Ra=1.6mm
镗刀Ф78的
3、粗镗孔Ф75J7至Ф73
镗刀Ф73
4、粗镗孔Ф68H7至Ф66
镗刀Ф66
5、粗镗孔Ф62J7至Ф61
镗刀Ф61
6、钻6-M10-6H的中心孔
中心钻Ф8
7、半精镗孔Ф85H7至Ф84.5
镗刀Ф84.5
8、半精镗孔Ф80J7至Ф78.9
镗刀Ф78.9
9、半精镗孔Ф75J7至Ф74.8
镗刀Ф74.8
17、精镗孔Ф62J7至尺寸
镗刀Ф62
18、钻18-Ф6.2的锥孔
麻花钻Ф6.2
19、倒60º的锥角
成形铣刀Ф6.2
数控机
定位、装夹简图及程序原点和对刀说明
工步序号及内容
选用刀具
备注
50
镗各配合孔
钻孔
攻螺纹
一面两孔定位
20、钻2-Ф30的孔
麻花钻Ф30
21、钻Ф6的孔
镗刀Ф67.8
29、攻螺纹6-M10-H7
M10-H7的丝锥Ф10
30、精镗孔Ф80H7至尺寸
镗刀Ф80
31、精镗孔Ф75H7至尺寸
镗刀Ф75
32、精镗孔Ф68J7至尺寸
镗刀Ф68
33、钻Ф14的通孔
数控加工工艺流程
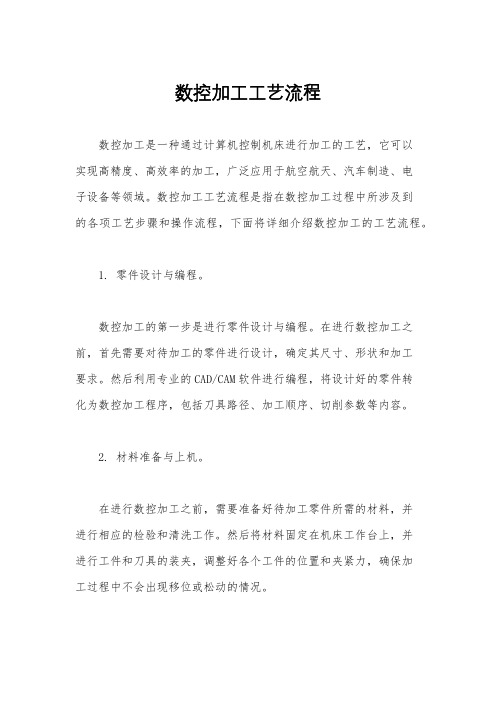
数控加工工艺流程数控加工是一种通过计算机控制机床进行加工的工艺,它可以实现高精度、高效率的加工,广泛应用于航空航天、汽车制造、电子设备等领域。
数控加工工艺流程是指在数控加工过程中所涉及到的各项工艺步骤和操作流程,下面将详细介绍数控加工的工艺流程。
1. 零件设计与编程。
数控加工的第一步是进行零件设计与编程。
在进行数控加工之前,首先需要对待加工的零件进行设计,确定其尺寸、形状和加工要求。
然后利用专业的CAD/CAM软件进行编程,将设计好的零件转化为数控加工程序,包括刀具路径、加工顺序、切削参数等内容。
2. 材料准备与上机。
在进行数控加工之前,需要准备好待加工零件所需的材料,并进行相应的检验和清洗工作。
然后将材料固定在机床工作台上,并进行工件和刀具的装夹,调整好各个工件的位置和夹紧力,确保加工过程中不会出现移位或松动的情况。
3. 加工工艺参数设置。
在上机之后,需要根据零件的材料、形状和加工要求,设置相应的加工工艺参数。
包括切削速度、进给速度、切削深度、切削宽度等参数,这些参数的设置将直接影响到加工质量和加工效率。
4. 数控加工操作。
经过以上准备工作之后,就可以进行数控加工操作了。
操作人员通过数控系统输入预先编好的加工程序,机床将按照程序中设定的路径和参数进行自动加工,实现对工件的精密加工。
在加工过程中,操作人员需要随时监控加工状态,及时调整加工参数,确保加工质量和安全。
5. 加工质量检验。
在数控加工完成之后,需要对加工零件进行质量检验。
通过测量工件的尺寸、形状和表面粗糙度等指标,判断加工质量是否符合要求。
如果发现有缺陷或不合格的地方,需要及时调整加工参数,重新加工或修复工件。
6. 零件清洗与包装。
经过质量检验合格的零件,需要进行清洗和包装工作。
清洗可以去除加工过程中产生的切屑和油污,保持零件的表面清洁。
然后根据客户要求进行包装,以防止零件在运输和储存过程中受到损坏。
7. 加工记录与数据归档。
在数控加工过程中,需要对加工过程进行记录和数据归档。
数控加工工艺卡片(整理)

刀补地址
刀尖半径
刀杆规格
半径
形状
1
T101
95°外圆车刀
YT15
0.4
20×20
01
01
2
T202
4×18槽刀
YT15
0.1
20×20
02
02
设计
审核
共页
第页
五、工艺过程卡
机械加工工艺过程卡
产品名称
零件名称
零件图号
A
塞
A-1
材料
45钢
毛坯
Φ25×45
工时
30min
工序号
工序名称
工序简要内容
设备名称
50
650
0.2
1.5
T101
3
粗车及半精车圆柱面Φ18-0.03×25,留精加工余量0.3;
50
650
0.2
1.5
T101
4
粗车及半精车圆锥面30°,留精加工余量0.3;
50
650
0.2
1.5
T101
5
精车圆柱面Φ24-0.03,Ra1.6;
110
1500
0.2
0.15
T101
YT15 95°外圆车刀
实训报告
班级:姓名:
一、实训课题:实训时间:
实训目的:
二、实训器材设备
1、CK6136数控车床
2、150mm游标卡尺
3、0~25mm、25~50mm千分尺
4、外圆车刀
三、实训过程
1、开机,回参考点。
2、装夹工件毛坯和刀具。
3、试切削对1号刀:
对Z方向----------过程;对X方向---------过程。
数控加工的工艺流程
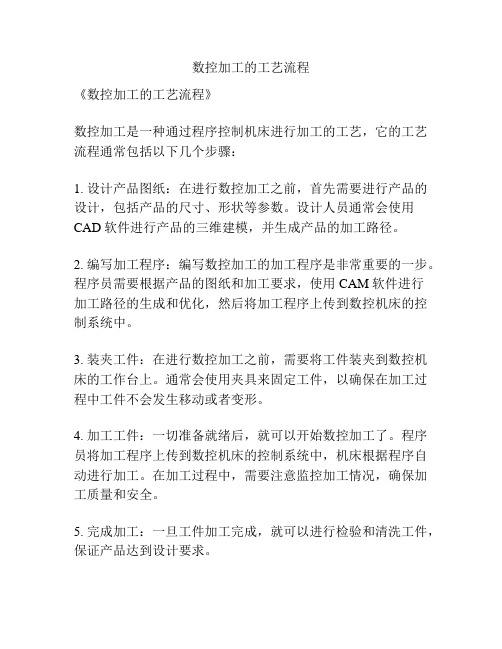
数控加工的工艺流程
《数控加工的工艺流程》
数控加工是一种通过程序控制机床进行加工的工艺,它的工艺流程通常包括以下几个步骤:
1. 设计产品图纸:在进行数控加工之前,首先需要进行产品的设计,包括产品的尺寸、形状等参数。
设计人员通常会使用CAD软件进行产品的三维建模,并生成产品的加工路径。
2. 编写加工程序:编写数控加工的加工程序是非常重要的一步。
程序员需要根据产品的图纸和加工要求,使用CAM软件进行
加工路径的生成和优化,然后将加工程序上传到数控机床的控制系统中。
3. 装夹工件:在进行数控加工之前,需要将工件装夹到数控机床的工作台上。
通常会使用夹具来固定工件,以确保在加工过程中工件不会发生移动或者变形。
4. 加工工件:一切准备就绪后,就可以开始数控加工了。
程序员将加工程序上传到数控机床的控制系统中,机床根据程序自动进行加工。
在加工过程中,需要注意监控加工情况,确保加工质量和安全。
5. 完成加工:一旦工件加工完成,就可以进行检验和清洗工件,保证产品达到设计要求。
总的来说,数控加工工艺流程包括产品设计、加工程序编写、工件装夹、加工和产品检验等步骤。
这种工艺流程不仅提高了加工效率和精度,也极大地减少了人工操作的需求,是现代制造业中不可或缺的一部分。
数控加工电子教案之车削工艺分析过程及工艺卡片和刀具卡片(可编辑)
数控加工电子教案之车削工艺分析过程及工艺卡片和刀具卡片车削工艺分析学习任务一:工艺分析【步骤一】:数控加工内容的选择该零件所有内容选择在同一台数控车床上完成。
零件有内外圆柱面、内外圆锥面和螺纹等,适合在数控车床上完成全部加工。
【步骤二】:零件的工艺性分析该零件表面由圆柱、圆锥等构成。
件1和件2之间1:5锥面配合要求配作,孔与轴为间隙配合,要求两处径向同时配合,轴向配合均允许留有较大间隙,属于“径向过定位”问题。
经分析,本例将采取用修配法首先保证1:5锥面的配合,而孔与轴通过加工过程中的测量来控制其尺寸精度,从而保证其配合精度。
件1和件3是通过螺纹配合。
主要表面粗糙度要求均是Ra1.6。
件1和两圆柱面有同轴度公差要求,件2锥孔和之间也有同轴度公差要求,两端面之间有平行度公差要求。
尺寸标注完整,轮廓描述清楚。
零件材料为45号钢,无其他热处理和硬度要求。
该零件各台阶直径相差不大,力学性能要求不高,并为小批量生产,因此毛坯选用普通型材?50mm×155mm。
学习任务二:工艺路线的设计【步骤一】:加工方法及加工方案的选择本配合零件主要采用车端面、车外圆和车内孔的加工方法,外圆采用采用粗车→精车的加工方案。
内孔加工采用钻→粗镗→精镗的加工方案。
1:5锥面配合采用修配法保证尺寸精度,其他尺寸经粗、精车后能达到加工要求。
零件内、外圆尺寸精度达到IT9级,表面粗糙度要求达到Ra1.6,粗车后余量较均匀,不需安排半精加工。
【步骤二】:加工阶段的划分划分成粗加工和精加工二个加工阶段。
因为粗车时因加工余量大、切削力和夹紧力大等因素造成较大的加工误差,如果粗、精加工混在一起,就无法避免由上述原因引起的加工误差。
划分成粗、精加工二个加工阶段,粗加工造成的加工误差可通过精加工得到纠正,从而保证加工质量。
【步骤三】:工序的划分采用按安装次数来划分工序,共分六个工序。
第一次装夹:夹φ50毛坯,加工零件2外轮廓并切断零点在右端面中心;第二次装夹:夹零件φ50毛坯,加工零件3外轮廓并切断零点在左端面中心;第三次装夹:夹φ50毛坯,加工零件1左端外轮廓并切断;第四次装夹:夹零件1φ35外圆,加工右端外轮廓;第五次装夹:加工零件2内孔至尺寸要求零点在左端面中心;第六次装夹:加工零件3内孔及内螺纹至尺寸要求零点在右端面中心。
数控加工工艺过程卡
数控加工工艺过程卡数控加工是一种通过数控机床实现零件加工的技术,它具有高精度、高效率、高稳定性等优点,在现代制造业中得到广泛应用。
而数控加工工艺过程卡是对数控加工过程的描述和规范,它包含了零件的工艺流程、机床设备的参数设置、刀具的选用和刀具路径规划等信息。
以下是一个关于数控加工工艺过程卡的示例,供参考:零件名称:薄壁零件材料:铝合金6061加工精度:0.01mm加工工艺:铣削、钻孔、螺纹加工设备:数控铣床、数控钻床刀具:铣刀、钻孔刀、螺纹攻丝刀1.工艺流程:1.1首先根据图纸进行零件的准备和标记1.2将工件夹紧于数控铣床工作台1.3调整数控铣床的零点和坐标轴1.4选择合适的铣刀,装夹在数控铣床刀柄上1.5设置加工参数,确定切削速度和进给速度1.6进行主体加工,包括铣削外形和加工孔位1.7检验零件尺寸和形状是否满足要求2.设备参数设置(数控铣床):2.1设置工件夹具和工作台的夹紧力2.2调整数控铣床的零点和坐标轴2.3根据刀具类型和材料确定切削速度和进给速度2.4调整刀具的位置和切削深度2.5检查数控铣床的润滑系统是否正常运行3.刀具选用:3.1铣削外形:选择合适的面铣刀,刀径根据零件尺寸确定3.2钻孔:选择合适的钻孔刀,直径根据零件需求确定3.3螺纹加工:选择合适的螺纹攻丝刀,根据螺纹尺寸和规格确定4.刀具路径规划:4.1铣削外形:根据零件几何形状和加工要求,确定铣刀的切削路径和铣削方向4.2钻孔:根据孔位和孔径确定钻孔的位置和顺序4.3螺纹加工:根据螺纹的要求,确定攻丝刀的加工路径和攻丝顺序5.加工注意事项:5.1在加工过程中,保持加工液的供给和润滑系统的正常工作5.2在加工过程中,及时清理切削屑和切屑槽,以保证切削效果和切屑排出5.3加工前要检查工具刀具是否完好,并及时更换磨损或损坏的刀具通过对数控加工工艺过程的规范和描述,可以确保零件的加工质量和生产效率,提高工艺流程的标准化和规范化,为企业的生产制造提供有力的支持。
数控加工实用工艺卡片、刀具卡片样板
180
2866
0.20
573.2
3
T03
球头铣刀
8
给各孔点窝
H03
D03
80
3184
0.10
318.4
Z-3.0
4
T04
钻头
11
钻孔
H04
D04
80
2316
0.20
463
Z-40.0
11
T11
铰刀
16
铰4×φ16mm孔
H11
D11
15
298
0.16
48
Z-20.0
××零件机械加工工艺规程卡
08数控02-姓名-学号
N200
G40G00X52.
G40G00X52
取消刀具左补偿,快速退刀
××零件数控加工工艺卡
08数控02班-姓名-学号
零件号
零件名称
材料
热处理状态
毛坯尺寸
加工程序号
设备型号
设备名称
夹具编号
第1页
0001
45#
调质
150mm×150mm×100mm
O0001
XK713
数控铣
0001
补偿
切削参数
顺序号
刀具
机械加工工艺规程卡片
产品型号
零(部)件图号
共 页
第 页
产品名称或代号
零(部)件名称
材料牌号
45#
毛坯种类
圆棒料
毛坯外形尺寸
200mm×200mm×100mm
每件毛坯可制件数
3
每台件数
1
备注
工序号
工序名称
工序内容
国家开放大学电大《数控加工工艺》习题及答案
第3章数控加工中工件的定位与装夹作业答案思考与练习题1、车削薄壁零件如何夹紧工件?答:轴向夹紧或增加夹紧力作用点面积。
2、确定工件在夹具中应限制自由度数目的依据是什么?答:根据工件加工精度要求。
3、试简述定位与夹紧之间的关系。
答:任务不同,定位使加工前工件在机床上占有正确的位置,而夹紧则使工件在加工过程中始终保持在原先确定的位置上。
两者相辅相成,缺一不可。
4、采用夹具装夹工件有何优点?答:a. 易于保证工件的加工精度。
b. 使用夹具可改变和扩大原机床的功能,实现“一机多用”。
c. 使用夹具后,不仅省去划线找正等辅助时间,而且有时还可采用高效率的多件、多位、机动夹紧装置,缩短辅助时间,从而大大提高劳动生产率。
d. 用夹具装夹工件方便、省力、安全。
e. 在批量生产中使用夹具时,由于劳动生产率的提高和允许使用技术等级较低的工人操作,故可明显地降低生产成本。
5、当基准重合原则和基准统一原则发生矛盾时,怎么解决?答:以保证工件加工精度为原则,若采用统一定位基准能够保证加工表面的尺寸精度,则应遵循基准统一原则;若不能保证尺寸精度,则应遵循基准重合原则,以免使工序尺寸的实际公差值减小,增加加工难度。
6、什么情况下才需要计算定位误差?答:用夹具装夹、调整法加工一批工件的条件下,基准不重合时,需要计算定位误差。
若采用试切法加工,不存在定位误差,因而也不需要计算定位误差。
7、如何理解定位面与定位基准的区别?答:工件在夹具中的位置是以其定位基面与定位元件的相互接触(配合)来确定的,工件以平面定位时,定位面就是定位基准;工件以内、外圆柱面定位时,定位面是内、外圆柱面,而定位基准则是中心线。
8、车床上装夹轴类零件时,如何找正?答:工件外圆上选择相距较远的两点,用百分表找正。
模拟自测题一、单项选择题1、过定位是指定位时,工件的同一(B)被多个定位元件重复限制的定位方式。
(A)平面(B)自由度(C)圆柱面(D)方向2、若工件采取一面两销定位,限制的自由度数目为( A )(A)六个(B)二个(C)三个(D)四个3、在磨一个轴套时,先以内孔为基准磨外圆,再以外圆为基准磨内孔,这是遵循( D )的原则。
- 1、下载文档前请自行甄别文档内容的完整性,平台不提供额外的编辑、内容补充、找答案等附加服务。
- 2、"仅部分预览"的文档,不可在线预览部分如存在完整性等问题,可反馈申请退款(可完整预览的文档不适用该条件!)。
- 3、如文档侵犯您的权益,请联系客服反馈,我们会尽快为您处理(人工客服工作时间:9:00-18:30)。
20
铣基准平面B
以平面A及铸孔为基准
1、粗铣平面B留余量5mm
Ф70的面铣刀
2、半精铣平面B留余量0.5mm
Ф70的面铣刀
3、精铣平面B至尺寸110mm保证Ra=1.6及0.08的平面度 与A面的垂直度300:0.12
Ф80的面铣刀
30
铣结合面EF平面
以AB平面为基准
1、粗铣平面E、F留余量5 mm
备注
40
铣平面
钻孔
攻螺纹
以平面B F为定位基准
1、粗铣KMN H平面
平面铣刀Ф32
2、半精铣K M N H平面保证Ra=3.2mm
平面铣刀Ф40
3、钻孔5-Ф17.5
麻花钻Ф17、5
4、扩孔5-Ф17.5至Ф28深125mm
扩孔刀Ф28
5、钻锥销孔2-Ф8的中心孔
中心钻Ф6
6、铰锥销孔2-Ф8的中心孔至尺寸 保证Ra=1.6mm
镗刀Ф67.8
29、攻螺纹6-M10-H7
M10-H7的丝锥Ф10
30、精镗孔Ф80H7至尺寸
镗刀Ф80
31、精镗孔Ф75H7至尺寸
镗刀Ф75
32、精镗孔Ф68J7至尺寸
镗刀Ф68
33、钻Ф14的通孔
麻花钻Ф14
数 控 机 床 工 艺 简 卡
序号
工序名称与
加工程序号
定位、装夹简图及程序原点与对刀说明
铰刀Ф8
7、钻2-Ф8的锥销孔
麻花钻Ф8
8、钻螺纹5-M8-6H深18与14-M8-6H深15的中心孔
中心钻Ф6
9、扩螺纹5-M8-6H深18与14-M8-6H深15的中心孔至
扩孔刀Ф7
10、攻螺纹5-M8-6H深18与14-M8-6H深15
Ф8的丝锥
11、钻锥销孔2-Ф12的中心孔
麻花钻Ф10
12、精铰孔2-Ф12的中心孔至尺寸 保证Ra=1.6mm
பைடு நூலகம்镗刀Ф74.8
10、半精镗孔Ф68H7至Ф67.8
镗刀Ф67.8
11、半精镗孔Ф62J7至Ф61.8
镗刀Ф61.8
12、攻螺纹6-M10-6H
M10-H7的丝锥Ф10
13、精镗孔Ф85H7至尺寸
镗刀Ф85
14、精镗孔Ф80J7至尺寸
镗刀Ф80
15、精镗孔Ф75J7至尺寸
镗刀Ф75
16、精镗孔Ф68H7至尺寸
工步序号及内容
选用刀具
备注
60
铣面
铣槽
倒角
钻孔
以平面B F定位
1、粗铣平面G
平面铣刀Ф30
,2、半精铣平面G
平面铣刀Ф40
3、粗铣下底面
立式铣刀Ф25
4、半精铣下底面
立式铣刀Ф25
5、铣5×1有凹槽
铣槽刀Ф5
6、倒2×45 º的倒角
成形铣刀Ф20
7、10×45 º的倒角
成形铣刀Ф20
8、钻14-M6-6H深12的中心孔
21、钻Ф6的孔
麻花钻Ф6
22、粗镗孔Ф80H7至Ф78
镗刀Ф78
23、粗镗孔Ф75H7至Ф73
镗刀Ф73
24、粗镗孔Ф68J7至Ф66
镗刀Ф66
25、钻6-M10-H7的中心孔
中心钻Ф8
26、半精镗孔Ф80H7至Ф78.9
镗刀Ф78.9
27、半精镗孔Ф75H7至Ф74.8
镗刀Ф74.8
28、半精镗孔Ф68J7至Ф67.8
铰刀Ф12
13、铣R102的圆弧段面
立铣刀Ф20
数 控 机 床 工 艺 简 卡
序号
工序名称与
加工程序号
定位、装夹简图及程序原点与对刀说明
工步序号及内容
选用刀具
备注
14、将R102的圆弧段面铣成具有10 º的倾斜面
成形立铣刀Ф30
50
镗各配合孔
钻孔
攻螺
一面两孔定位
1、粗镗孔Ф85H7至Ф83
镗刀Ф83
Ф125的平面铣刀
2、半精铣平面E、F留余量0.5 mm
Ф125的平面铣刀
3、精铣平面E、F加工至要求距离尺寸750匀保证E、F平面Ra=1.6及与平面A、B的垂直度0.1
Ф125的平面铣刀
数 控 机 床 工 艺 简 卡
:
序号
工序名称与
加工程序号
定位、装夹简图及程序原点与对刀说明
工步序号及内容
选用刀具
中心钻Ф5
9、钻Ф7的孔
麻花钻Ф7
2、粗镗孔Ф80J7至Ф78
镗刀Ф78的
3、粗镗孔Ф75J7至Ф73
镗刀Ф73
4、粗镗孔Ф68H7至Ф66
镗刀Ф66
5、粗镗孔Ф62J7至Ф61
镗刀Ф61
6、钻6-M10-6H的中心孔
中心钻Ф8
7、半精镗孔Ф85H7至Ф84.5
镗刀Ф84.5
8、半精镗孔Ф80J7至Ф78.9
镗刀Ф78.9
9、半精镗孔Ф75J7至Ф74.8
镗刀Ф68
17、精镗孔Ф62J7至尺寸
镗刀Ф62
18、钻18-Ф6、2的锥孔
麻花钻Ф6.2
19、倒60º的锥角
成形铣刀Ф6.2
数 控 机 床 工 艺 简 卡
序号
工序名称与
加工程序号
定位、装夹简图及程序原点与对刀说明
工步序号及内容
选用刀具
备注
50
镗各配合孔
钻孔
攻螺纹
一面两孔定位
20、钻2-Ф30的孔
麻花钻Ф30
数 控 机 床 工 艺 简 卡
序号
工序名称与
加工程序号
定位、装夹简图及程序原点与对刀说明
工步序号及内容
选用刀具
备注
10
铣基准平面A
以所铸孔为粗基准
1、粗铣平面A留5mm的加工余量
Ф32的面铣刀
2、半精铣平面A留0.5mm的加工余量
Ф32的面铣刀
3、精铣平面A加工至尺寸 保证Ra=1.6及0.05的平面度