数控机床维修案例及分析03
数控车床的常见故障诊断及其维修实例
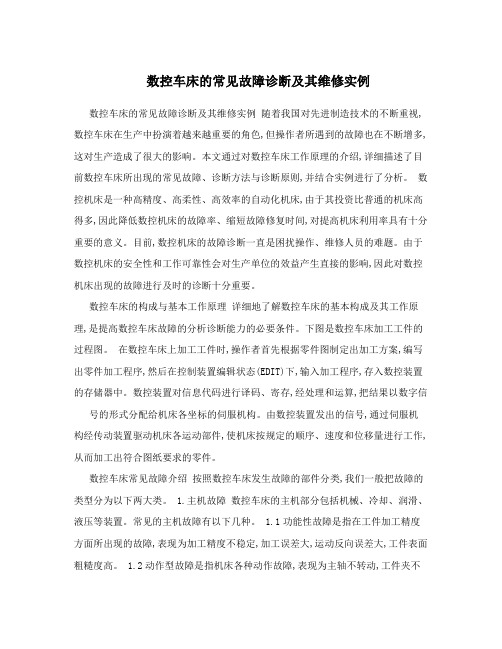
数控车床的常见故障诊断及其维修实例数控车床的常见故障诊断及其维修实例随着我国对先进制造技术的不断重视,数控车床在生产中扮演着越来越重要的角色,但操作者所遇到的故障也在不断增多,这对生产造成了很大的影响。
本文通过对数控车床工作原理的介绍,详细描述了目前数控车床所出现的常见故障、诊断方法与诊断原则,并结合实例进行了分析。
数控机床是一种高精度、高柔性、高效率的自动化机床,由于其投资比普通的机床高得多,因此降低数控机床的故障率、缩短故障修复时间,对提高机床利用率具有十分重要的意义。
目前,数控机床的故障诊断一直是困扰操作、维修人员的难题。
由于数控机床的安全性和工作可靠性会对生产单位的效益产生直接的影响,因此对数控机床出现的故障进行及时的诊断十分重要。
数控车床的构成与基本工作原理详细地了解数控车床的基本构成及其工作原理,是提高数控车床故障的分析诊断能力的必要条件。
下图是数控车床加工工件的过程图。
在数控车床上加工工件时,操作者首先根据零件图制定出加工方案,编写出零件加工程序,然后在控制装置编辑状态(EDIT)下,输入加工程序,存入数控装置的存储器中。
数控装置对信息代码进行译码、寄存,经处理和运算,把结果以数字信号的形式分配给机床各坐标的伺服机构。
由数控装置发出的信号,通过伺服机构经传动装置驱动机床各运动部件,使机床按规定的顺序、速度和位移量进行工作,从而加工出符合图纸要求的零件。
数控车床常见故障介绍按照数控车床发生故障的部件分类,我们一般把故障的类型分为以下两大类。
1.主机故障数控车床的主机部分包括机械、冷却、润滑、液压等装置。
常见的主机故障有以下几种。
1.1功能性故障是指在工件加工精度方面所出现的故障,表现为加工精度不稳定,加工误差大,运动反向误差大,工件表面粗糙度高。
1.2动作型故障是指机床各种动作故障,表现为主轴不转动,工件夹不紧,刀架转动失调,等等。
1.3结构型故障是指主轴发热,主轴箱噪声大,产生切削振动,等等。
数控机床故障维修方法及实例分析
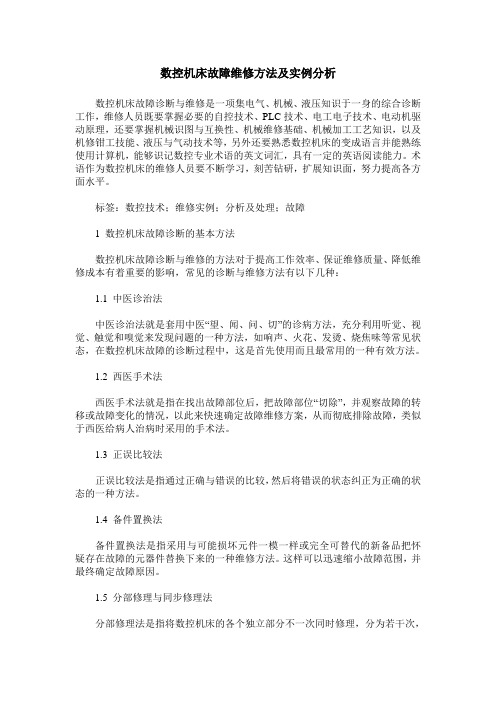
数控机床故障维修方法及实例分析数控机床故障诊断与维修是一项集电气、机械、液压知识于一身的综合诊断工作,维修人员既要掌握必要的自控技术、PLC技术、电工电子技术、电动机驱动原理,还要掌握机械识图与互换性、机械维修基础、机械加工工艺知识,以及机修钳工技能、液压与气动技术等,另外还要熟悉数控机床的变成语言并能熟练使用计算机,能够识记数控专业术语的英文词汇,具有一定的英语阅读能力。
术语作为数控机床的维修人员要不断学习,刻苦钻研,扩展知识面,努力提高各方面水平。
标签:数控技术;维修实例;分析及处理;故障1 数控机床故障诊断的基本方法数控机床故障诊断与维修的方法对于提高工作效率、保证维修质量、降低维修成本有着重要的影响,常见的诊断与维修方法有以下几种:1.1 中医诊治法中医诊治法就是套用中医“望、闻、问、切”的诊病方法,充分利用听觉、视觉、触觉和嗅觉来发现问题的一种方法,如响声、火花、发烫、烧焦味等常见状态,在数控机床故障的诊断过程中,这是首先使用而且最常用的一种有效方法。
1.2 西医手术法西医手术法就是指在找出故障部位后,把故障部位“切除”,并观察故障的转移或故障变化的情况,以此来快速确定故障维修方案,从而彻底排除故障,类似于西医给病人治病时采用的手术法。
1.3 正误比较法正误比较法是指通过正确与错误的比较,然后将错误的状态纠正为正确的状态的一种方法。
1.4 备件置换法备件置换法是指采用与可能损坏元件一模一样或完全可替代的新备品把怀疑存在故障的元器件替换下来的一种维修方法。
这样可以迅速缩小故障范围,并最终确定故障原因。
1.5 分部修理与同步修理法分部修理法是指将数控机床的各个独立部分不一次同时修理,分为若干次,每次修其中某一部分,依次进行。
此法可利用节假日修理,减少停工损失,适用于大型复杂的数控机床。
1.6 原理分析法原理分析法的关键是要掌握廣泛的专业知识,熟悉具体机床的工作特性。
一旦掌握了某一功能的控制原理,就找到了解决故障最根本的出发点。
数控机床维修技术及维修实例

数控机床维修技术及维修实例一、数控机床的维修技术数控机床作为工业生产中不可或缺的设备之一,其维修工作一直备受关注。
下面介绍一些常见的数控机床维修技术。
1. 电气维修数控机床中常见的电气问题包括电机故障、电路故障等。
电机故障可通过检查电机的绝缘电阻、转子线圈是否短路等进行诊断。
而电路故障则需通过检测电路中的保险丝、开关、继电器、电容等元件,找出其中故障元件并进行更换。
2. 机械维修数控机床在长期使用过程中,机械部分如导轨、螺杆等也会存在磨损、松动等问题。
此时需要对数控机床进行机械维修。
机械维修的具体步骤包括:拆卸故障部位、检查问题原因、更换或修复损坏部分、重新安装。
3. 编程维修通常情况下,数控机床使用人员会根据需要自行编写机床的加工程序,但编写程序时也会存在错误导致数控机床不能正常工作。
此时需要进行编程维修,主要包括检查程序语法、修改程序错误等操作。
二、数控机床维修实例下面介绍一则数控机床的维修实例,以便更好理解上述维修技术。
实例背景该台数控机床已运行数年,最近出现报警停机的问题,并出现零件加工不合格等问题。
解决过程1.首先进行电气检查,检查电路和电机连接状态,未发现异常。
2.在机械检查中发现,导轨磨损程度较高,需要对导轨进行更换。
3.更换后的导轨需要重新进行编程设定,此时发现编程语法有误,进行修改后重新设定。
4.重新设定后进行了多次的试车和调试,最终发现并解决了后续加工不合格等问题。
结论通过以上维修过程,我们可以发现,数控机床维修过程中的各项技术都具有一定的综合性,需要将电气、机械和编程等多种技术手段融合运用,全面诊断故障并解决问题。
CNC数控机床检修实例

CNC数控机床检修实例1 CNC数控机床不能起动1.1故障现象一台沈阳第三车床厂sl一296A型数控车床,工作台加工过程中出现CRT无显示(俗称黑屏),当重新按车床NC起动按钮,数控机床也不能恢复正常,各项加工功能均无。
据操作者讲,几天前偶而出现同样故障,但能重新启动且工作如常。
1.2故障检测与分析处理根据图1电气原理,首先检测数控系统的FANUC-0T—MATE—E2电源单元,控制单元的MTEE2ADC一与CRT/MDI部件,采用先易后难方法:a.先查看-SB1,-SB2启动与停止按钮无损坏,触点良好。
b.再查看J37,J27,J38,等多头线电缆与叉头无松动等异常现象。
c.当检测到CRT/MDI单元时发现+24 V供电没有到位。
而电源单元的LED 绿灯已亮,证明AC输入正常,并实测出该输出电压匀在正常范围之内.这说明电源单元本身良好。
d.经检测后分析:可能电源与CNC系统启动电路有故障,按此思路,仔细检查NC电路,怀疑是0N、0FF、COM三条信号线在机床中经多节插头插座串联导致的故障,为快速证明判断证确与否,采用“信号短路法”,将电路图中CP3处的ON、0FF、COM信号在插座XP/S54(1)、XP/S54(2)、XP/S54(3)的三个插孔内,进行短路处理后,合上机床总电源,这时NC立即启动。
CRT/MDI面板显示正常,经试车机床的各项加工功能运转正常;也无其他异常报警。
随后进一步处理;实测经校线(俗称叫线),发现故障点是在XP/S62(2)的插头处,电信号线脱焊所造成CNC程序启动后数控系统不能复位,经焊接处理后故障彻底排除;故障检修完毕。
2主轴电机过热故障2.1故障现象一台s1-296A数控车床在加工运转时发生“啃刀”现象并造成刀具损坏。
2.2故障检测与分析处理a.用手动JVC慢跑模式将车床X,Z轴调至原点,重新启动加工程序,进行试车,当工作台快速进给到加工位置时主轴仍不转,至此确诊为交流变频主轴电机调速系统存在故障。
数控机床故障分析实例

数控机床故障分析实例
数控机床是目前普及度最高、用途最广泛的机床之一,也是制造业中使用频率最高的设备之一。
随着科学技术的发展,数控机床的技术水平日益提高,但偶尔仍会发生故障,影响正常生产,下面我们就以一个实际案例介绍,如何分析数控机床故障。
本案例中,一台数控机床出现故障,主要表现为驱动部件出现异常声响、轴位定位不准,无法正常工作。
首先,必须了解机床的基本结构,以及机床的故障表现。
其次,根据机床的基本结构,分析可疑部件,找出可能引起故障的原因,如驱动部件、主轴等;然后,根据机床的故障表现,详细分析可疑部件,例如确定驱动部件是否可以正常运行,主轴是否有松动等。
通过分析,可以发现可能的故障部位,最终定位故障源。
最后,分析故障源,找出机床故障的原因,比如机床走线不当、碰撞损伤等,并将针对不同原因的解决办法提出。
本案例故障分析的思路可供今后参考,可以有效帮助用户更加容易地解决数控机床故障。
因此,可以结合生产实际,详细准备故障分析流程,提高故障分析效率;此外,还可以建立合理的保养计划,定期检查数控机床重要零部件,及时发现故障,防止机床故障的发生。
总之,提升数控机床的可靠性和安全性需要建立系统的预防技术体系,其内容包括故障预防、故障分析和维修技术等等。
特别是在复杂实际生产中,以故障分析为基础,及时排查故障,可以有效地提高数控机床的工作效率,同时也有助于提升制造业的竞争力和安全性。
通过本案例分析,我们了解到,故障分析是提高数控机床可靠性
和安全性的基础,只有建立健全的故障分析系统,才能保证数控机床的正常运行,同时也可以有效保障安全生产。
数控机床维修实例分析

1某数控车床CAK5085di此车床采用FANUC系统,长期偶发如下故障用换刀指令换刀时偶尔找不到刀位号,在所指定的刀位处刀架有停顿现象,然后刀架继续旋转。
出现“刀位未检测”报警故障。
针对这个故障进行如下分析处理:一般刀架上的刀位检测和刀塔夹紧信号都是通过霍尔元件或者接近开关开反馈的直流信号来确定的。
刀架旋转到位,其相对应的检测原件输出信号,然后通过刀架电机反转,锁紧刀架,并给出刀架锁紧信号完成一个换刀动作。
出现以上报警故障时,检测相应的开关元件对应的输出信号即可。
本机床刀塔采用十芯电缆线,其中一芯为接地,三芯为电机供电,其余六芯为刀塔信号线(四芯刀塔到位信号线、一个刀塔锁紧信号线和一个电源线),刀塔的接线原理图如图1所示。
图1 刀塔接原理线图通过图1可以看出,刀塔的到位信号和锁紧信号全部通过PLC输入进行控制。
开始在检测电源信号时,存在虚接的情况,予以补锡焊接,焊好脱线后,刀架仍然存在以上问题。
排查PLC刀架到位的进线信号,四位信号有两位X3.0和X3.2故障时出现不稳定,电压从24V 瞬间掉至7V,排查有问题信号线,发现有对地短路情况,且更换刀位后,其他的信号线也偶尔出现类似问题,单独给刀位PLC检测端短接24V以模拟到位信号,刀架运转正常。
故可断定以上故障为刀塔到位旋转和刀位检测的模块内部霍尔元件故障引起,更换同型号模块后设备恢复正常运转。
2某DM4800加工中心数控系统此加工中心系1998年采购沈阳机床厂设备,采用三菱M3系列。
该设备前期出现系统软断线,在问题处理过程中相继出现系统黑屏,参数丢失以及换刀不执行等故障。
故障分析处理:按以往经验,在出现软断线故障时,多采用清洁主板和控制板,重新拔插线缆的方法恢复。
但此次出现该故障并对CNC系统主板MC161进行清洁后,主机出现黑屏无显示的状态,拔起紧停开关,系统READY灯不亮,同时CNC系统主板伴随有四个红灯(分别为D.WG、WDOG、LED1、D.AL)和两个绿灯(分别为LED2、LED3)全亮的状态,各轴不可动。
设备维保案例分析及经验总结

检查设备的磨损情况,如轴承、 齿轮、链条等关键部位,以预测 设备可能出现的故障和更换周期 。
维护计划制定
维护周期
根据设备状况评估结果,制定合理的 维护周期,包括定期检查、清洗、润 滑等,以确保设备正常运行。
维护内容
明确每次维护的具体内容,包括需要 更换的部件、需要进行的检查等,以 确保维护工作的全面性和准确性。
运行测试
完成维修后进行负载测试 ,确保设备正常运行
维修效果评估
01
设备恢复正常运行,加工出的零 件尺寸符合要求
02
总结维修经验,对类似故障有了 更快速准确的判断和处理能力
02
案例二:预防性维护的实施
设备状况评估
设备运行状况
评估设备的运行状况,包括设备 的性能、运行时间、故障记录等 ,以确定设备维护的优先级和重 点。
引入先进的维保技术
积极引进先进的维保技术和工具,提高维保 效率和准确性。
提高维保人员素质
加强维保人员的培训和管理,提高其技能水 平和责任心。
加强设备日常巡检
定期对设备进行巡检,及时发现和处理潜在 问题。
THANKS
感谢观看
故障率统计
统计设备在维护后的故障率,以评估预防性维护的效果和必 要性,并根据实际情况调整维护计划。
03
案例三:设备改造与升级
设备现状分析
设备老化
设备使用年限过长,部分元器件 磨损严重,故障率较高。
技术落后
设备采用的技术较落后,生产效率 低下,无法满足生产需求。
能耗高
设备能耗较高,增加了生产成本。
改造与升级方案设计
更新关键元器件
能耗优化
对磨损严重的关键元器件进行更换, 提高设备稳定性和可靠性。
数控机床维修技术及维修实例分析
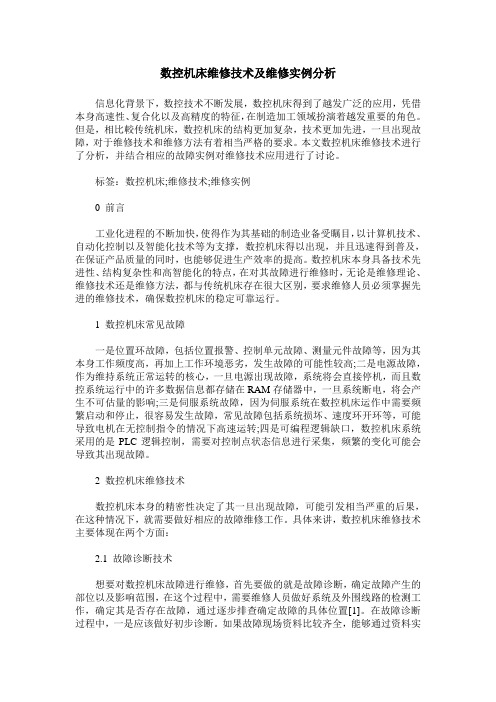
数控机床维修技术及维修实例分析信息化背景下,数控技术不断发展,数控机床得到了越发广泛的应用,凭借本身高速性、复合化以及高精度的特征,在制造加工领域扮演着越发重要的角色。
但是,相比較传统机床,数控机床的结构更加复杂,技术更加先进,一旦出现故障,对于维修技术和维修方法有着相当严格的要求。
本文数控机床维修技术进行了分析,并结合相应的故障实例对维修技术应用进行了讨论。
标签:数控机床;维修技术;维修实例0 前言工业化进程的不断加快,使得作为其基础的制造业备受瞩目,以计算机技术、自动化控制以及智能化技术等为支撑,数控机床得以出现,并且迅速得到普及,在保证产品质量的同时,也能够促进生产效率的提高。
数控机床本身具备技术先进性、结构复杂性和高智能化的特点,在对其故障进行维修时,无论是维修理论、维修技术还是维修方法,都与传统机床存在很大区别,要求维修人员必须掌握先进的维修技术,确保数控机床的稳定可靠运行。
1 数控机床常见故障一是位置环故障,包括位置报警、控制单元故障、测量元件故障等,因为其本身工作频度高,再加上工作环境恶劣,发生故障的可能性较高;二是电源故障,作为维持系统正常运转的核心,一旦电源出现故障,系统将会直接停机,而且数控系统运行中的许多数据信息都存储在RAM存储器中,一旦系统断电,将会产生不可估量的影响;三是伺服系统故障,因为伺服系统在数控机床运作中需要频繁启动和停止,很容易发生故障,常见故障包括系统损坏、速度环开环等,可能导致电机在无控制指令的情况下高速运转;四是可编程逻辑缺口,数控机床系统采用的是PLC逻辑控制,需要对控制点状态信息进行采集,频繁的变化可能会导致其出现故障。
2 数控机床维修技术数控机床本身的精密性决定了其一旦出现故障,可能引发相当严重的后果,在这种情况下,就需要做好相应的故障维修工作。
具体来讲,数控机床维修技术主要体现在两个方面:2.1 故障诊断技术想要对数控机床故障进行维修,首先要做的就是故障诊断,确定故障产生的部位以及影响范围,在这个过程中,需要维修人员做好系统及外围线路的检测工作,确定其是否存在故障,通过逐步排查确定故障的具体位置[1]。
- 1、下载文档前请自行甄别文档内容的完整性,平台不提供额外的编辑、内容补充、找答案等附加服务。
- 2、"仅部分预览"的文档,不可在线预览部分如存在完整性等问题,可反馈申请退款(可完整预览的文档不适用该条件!)。
- 3、如文档侵犯您的权益,请联系客服反馈,我们会尽快为您处理(人工客服工作时间:9:00-18:30)。
数控机床维修案例及分析
林天极、管明炎
摘要:随着我公司生产的发展, 数控设备日益增多;介于航天企业的生产特性,所配备 的数控设备种类多、 数控系统不统一,这就给公司数控设备的日常维护带来不便;
本人从事
数控设备维修工作近二十年,特选择具有代表性的数控维修案例进行分析,与大家共享。
一、数控设备的工作环境要求:
本章节:电源三相五线制、干扰的概念、抗干扰的方式、地线的布置等。
通过
290P 慢 走丝线切割屏幕抖动问题的解决,阐述抗干扰在数控设备中的意义。
我国标准的工业用电源是 380V ,频率50HZ 这是数控机床普遍要使用的电源。
动力电源必须经过稳压,其变化范围在 380 ± 10%之内,稳压电源最好使用净化稳压电 源、车间一个区用一只, 容量合适,动力线按6A/MM 计算,在布线时必须考虑地线并按三相 五线制布线。
充分考虑抗干扰。
为保证数控机床电气控制系统的可靠性, 避免故障的发生,除数控系统本身在电气设计 要对干扰源进行抑制外,在使用上也要考虑提高抗干扰能力和防干扰措施。
数控系统的控制过程是实时处理信息的过程, 内、外部的干扰都会破坏整个系统的稳定
性,因此干扰是影响数控机床系统可靠性的主要问题。
干扰是指有用信号与噪声信号两者之比小到一定程度,
噪声信号影响到系统政策工作这 一物理现象。
案例:一台S-188数控车削中心,开机后机床不能启动,无报警型号。
如图是S-188数控车削中心启动电气图,
二、数控设备电源故障:
不同国家所用的工业用电的电压是不同的, 欧洲国家一般用电为 AC400V ,由于欧洲国 家的电网相当稳定,因此在设计电源部分时就没有过多地关注电源的工作环境问题,
这样一 来从欧洲进口的数控设备,如果配搭的是西门子或海德汉数控系统,工作在我国
AC380V 工业电的情况下,其电源部分就容易出故障。
其故障主要有二大类:1、是功率模块损坏:2、 是继电器触点冷焊。
具体维修案例如下:
1、电源单元内部短路的故障诊断
故障现象:哈莫600U 五轴加工中心,配西门子数控 611U 电源、海德汉530数控系统
,
机床电源指示灯亮而系统显示装置不亮,查电源部分,发现611U无DC530V输出。
图8-3 611U数控加工中心电源单元的连接
图8-3为611U数控电源单元连接图。
当按下NC准备SB2时,CRT无任何显示且CRT 的灯丝不亮。
测量CRT的CP15无24V输出,则说明电源单元没工作,即电源无法接通。
故障分析:在一般的情况下,611U电源的工作情况是:合上主开关,电源状态指示灯
LED (绿色PIL )亮,机床启动,电源输出DC530V ;拉上急停开关,CNC启动,绿色PIL 灭、黄色PIL亮,电源输出DC600V,机床启动完成。
因此当电源状态指示灯LED (绿色PIL )不亮时,则故障原因可能是外部AC输入电路(CP1输入端)故障、熔断器F11、F12故障或辅助电路熔断器F1故障。
当电源单元状态指示灯LED亮时{此时ALM故障状态指示灯不亮},故障原因可能是
CP3外部连接开关SB2、SB3、SQ21及接线故障,也可能是内部电路RY2、RY3、RY4继电器控制电路故障。
当电源单元指示灯和故障状态指示灯都亮时,如果机床断电再送电故障解除,则为电
源单元受到外界的干扰导致。
如果不能解除,则可能是电源单元输出电压+5V、+15V、-15、+24V直流电压异常或内部电路故障。
本次故障为电源不工作,经分析是电源内部故障。
拆开电源模块后发现,电源模块熔
断丝损坏,进一步检查发现电源模块处于短路状态,经万用表检查后发现故障原因是内部启
动继电器的常开因电弧发生触点镀银融化而导致冷焊现象的发生。
更换内部启动继电器等相
关元件后,故障修复。
2、电源单元无法接通的故障诊断故障现象:EMCO332数控车削中心,配西门子840数控系统,西门子驱动。
机床在加工的过程中,突然停机,报警显示伺服无法接通。
如上图机床配西门子611U电源,打开电气控制柜,开机后发现整个数控系统没有电源,进一步检查发现西门子611U电源无任何输出,量输入有AC380V,初步判断为电源
模块故障。
拆开西门子611U电源,发现故障是由于如图电源模块中的驱动模块烧坏,更换驱动模块后,故障修复。
案例分析:通过上述两个案例可以看出在西门子数控系统中,一般配611电源模块,
由于其设计的余量、工作的方式(有两个继电器)等因素,导致在工作过程中,电源模块发生故障的概率比FANUC系统要高,而在611电源模块所发生的故障中,根据故障多发的因素,大部分是因为短路或驱动模块烧坏引起的,如果电源模块熔断丝完好、电路开路,则故
障很可能发生在驱动模块,更换驱动模块;如果电源模块熔断丝烧坏、电路短路,则故障很
可能发生在启动继电器,更换启动模块(单独更换启动继电器很困难)。
三、数控设备换刀系统的故障:
本章节:对于车床、立加,换刀系统的故障是常见的故障之一,通过济南数控车刀塔的故障,分析国产刀塔的工作原理及常见的故障处理方式、通过EMCO332 车刀塔的故障,分析进口车
削中心刀塔的工作原理及常见的故障处理方式、通过VMP32 立加换刀系统的故障,分析台湾产立加换刀系统的工作原理及常见的故障处理方式。
四、数控设备伺服故障:伺服系统是指以机械位置或角度作为控制对象的自动控制系统。
它接受来自数控装置的进给指令信号,经变换、调节和放大后驱动执行件,转化为直线或旋转运动。
伺服系统是数控装置(计算机)和机床的联系环节,是数控机床的重要组成部分。
FANUC 系统由于其电源电压为DC 400 V ,同时其电源的设计余量多,因此FANUC 系统的故障多发生在伺服。
1、台湾省产程泰GLS150 数控车床在加工过程中出现414# 、410#报警,动力停止。
关闭电源再开机,X 轴移动时机床振颤,后又出现报警并动力停止。
查系统维修手册,报警信息为伺服报警、检测到X 轴位置偏差大。
根据现象分析,认为可能有以下原因:(1) 伺服驱动器坏;(2)X 轴滚珠丝杠阻滞及导轨阻滞。
针对原因(1), 调换同型号驱动器后试机,故障未能排除。
针对故障( 2), 进入伺服运转监视画面, 移动轴观察驱动器负载率, 发现明显偏大, 达到250%-300% 。
判断可能为机械故障。
拆开X 轴防护罩, 仔细检查滚珠丝杠和导轨均未发现异常现象。
机床X 轴水平倾斜45o 安装, 应有防止其下滑的平衡块或制动装置,检查中未发现平衡块, 但机床说明书电器资料显示PMC
确有X 轴刹车释放输出接点, 而对比同型机床该接点输出正常。
检查机床厂设置的I/0 转接板, 该点输出继电器工作正常, 触点良好, 可以输出110V 制动释放电压。
据此可断定制动线圈或传输电缆有故障。
断电后, 用万用表检测制动线圈直流电组及绝缘良好, 两根使用的电缆中有一根已断掉。
更换新的电缆后开机试验, 一切正常。
此故障虽然是有系统报警, 但直接原因却是电缆断线。
这一故障并不常见机床厂家在安装整机时处理不当或电器件压接不牢靠通常却都能引起一些故障而此类故障分析查找原因较麻烦。
五、数控设备的润滑故障:本章节:主要讨论中央润滑单元的故障,其故障主要有二大类:1、
中央润滑单元压力
上不去:2、是中央润滑单元在启动时工作一次后,不能自动连续工作;3、GLS200 和S189开关故障说明压力开关如何调整。
六、数控设备的软故障:
本章节:通过1、通过电池的更换说明原点的设定方式和参数的修改;2、通过GLS200机床P代码不认识故障和通讯传输故障说明SET参数(0系统和11系统)的意义。
3、通过
20L 机床G84 功能不工作、风扇功能屏蔽等说明活用系统参赛的意义。
七、位置控制故障:本章节:通过镗铣加工中心、友佳加工中心、DECO2000 送料机故障,说明行程开关、接近开关的工作原理、位置控制的检查方式、位置控制的准确性要求等。
1、在FANUC系统的梯形图编程语言中,F是来自NC侧的输入信号(NC宀PMC), 而G是由PMC输出到NC的信号(PMC T NC)。
其中,G130是PMC输出到NC侧的各轴互锁信号, 当其中某一位被置为"1" 时, 允许对应的伺服轴移动;为"0" 时, 禁止对应的伺服轴移动。
应用实例: W-138 插铣中心使用FANUC 160 系统, 执行原点返回的NC 程序时, 当执行到"G91 G28 G00 XO;" 时,X 轴无动作,CNC 状态栏显示为"MEM STRT MTN ***", 即X 轴移动指令已发出。
用功能键|MESSAGE| 切换屏幕, 并无报警信息。
用功能键|SYSTEM| 切换屏幕, 按“诊断”软键, 这时005(INTERLOCK/START-LOCK) 为"1", 即有伺服轴进入了互锁状态。
故障排除过程: 进入梯形图程序显示功能屏幕, 发现与X 轴对应的互锁信号G130.0 的状态为"0", 即互锁信号被输入至NC, 打开机床盖板,检查其互锁原因, 发现是一传感器被铝屑污染。
擦拭后, 将G130.0 置为"1", 互锁解除, 重新启动原点返回的NC 程序, 动作正常, 故障排除。