高速柴油机连杆胀断工艺的设计说明书
(完整word版)涨断连杆工艺

连杆分离面的涨断工艺(CRACKING TECHNOLOGY)是把连杆盖从连杆本体上断裂而分离开来。
它不是用铣、锯或拉这类传统切削加工方法,而是对连杆大头孔的断裂线处先加工出两条应力集中槽子(或在毛坯时就做出沟槽),然後带楔形的压头往下移动进入连杆大头孔,连杆大头孔与压头之间还有一对半圆套筒。
当压头往下移动时对连杆大头孔产生径向力,这样就使其在槽子处出现裂缝,在径向力的继续作用下,裂缝也继续扩大,最终把连杆盖从连杆本体上涨断而分离出来.连杆涨断工艺的实用性取决於其分离面的可装配性。
最理想的连杆及连杆盖涨断後的分离面,是不带任何塑性变形的脆性断裂,使其可装配性达致最佳。
影响其脆性断裂的因素很多,如断裂速度及材料等。
至於连杆采用涨断工艺时对其材料的要求,据德国KREBSOEGE公司的研究结果,烧结粉末金属连杆的可涨断性较好,也是连杆涨断工艺首先在粉末金属连杆上推行的原因。
铸铁连杆最适宜的材料是GTS65-70,锻钢连杆的材料是70号钢。
但是,70号钢锻造连杆在涨裂时,不带塑性变形的脆性断裂以及70号钢的切削加工,将是该工艺的难点。
连杆分离面涨断工艺的几个工艺问题*断裂槽的加工工艺连杆断裂槽加工有两种工艺:拉削加工和激光加工)。
采用拉削方法加工连杆大头孔的两条槽子,由於拉刀随着加工时间长而磨损,被拉削的槽子形状也随之而变化。
槽子形状的变化又影响连杆大头孔在涨断後的变形。
由於被拉削的两个断裂槽形状不一样,在连杆分离面断裂时会出现一个分离面已断开,而另一个分离面尚未完全断开的现象。
采用激光加工连杆大头孔的两条槽子,可保持形状一致,也就保证了连杆大头孔在涨断後的变形也是一致。
同时,激光加工的柔性好,加工运行的费用也小。
所以,现在很多汽车公司如上海大众汽车公司等,都倾向采用激光加工连杆断裂槽。
*断裂槽的槽深德国ALFING机床公司的研究表明,连杆大头孔在涨断後的圆度和楔力,与大头孔预加工的槽子深度有关。
由图可知断裂槽的深度大,则连杆大头孔在涨断後的变形小及涨断时的楔力小。
295柴油机连杆工艺规程及工艺说明书
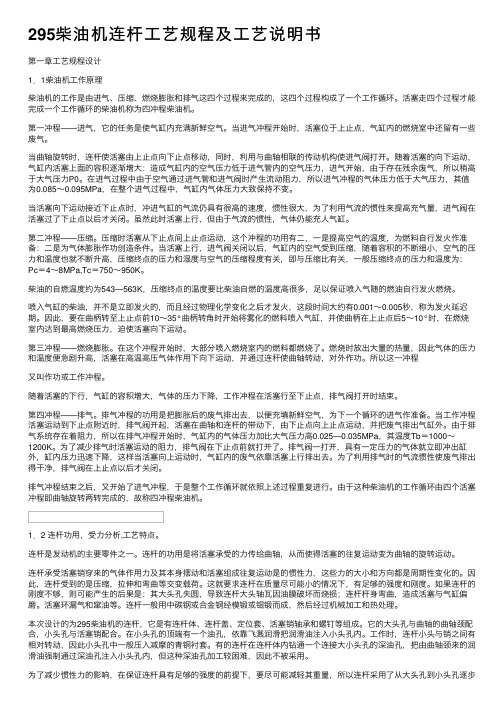
295柴油机连杆⼯艺规程及⼯艺说明书第⼀章⼯艺规程设计1.1柴油机⼯作原理柴油机的⼯作是由进⽓、压缩、燃烧膨胀和排⽓这四个过程来完成的,这四个过程构成了⼀个⼯作循环。
活塞⾛四个过程才能完成⼀个⼯作循环的柴油机称为四冲程柴油机。
第⼀冲程——进⽓,它的任务是使⽓缸内充满新鲜空⽓。
当进⽓冲程开始时,活塞位于上⽌点,⽓缸内的燃烧室中还留有⼀些废⽓。
当曲轴旋转时,连杆使活塞由上⽌点向下⽌点移动,同时,利⽤与曲轴相联的传动机构使进⽓阀打开。
随着活塞的向下运动,⽓缸内活塞上⾯的容积逐渐增⼤:造成⽓缸内的空⽓压⼒低于进⽓管内的空⽓压⼒,进⽓开始,由于存在残余废⽓,所以稍⾼于⼤⽓压⼒P0。
在进⽓过程中由于空⽓通过进⽓管和进⽓阀时产⽣流动阻⼒,所以进⽓冲程的⽓体压⼒低于⼤⽓压⼒,其值为0.085~0.095MPa,在整个进⽓过程中,⽓缸内⽓体压⼒⼤致保持不变。
当活塞向下运动接近下⽌点时,冲进⽓缸的⽓流仍具有很⾼的速度,惯性很⼤,为了利⽤⽓流的惯性来提⾼充⽓量,进⽓阀在活塞过了下⽌点以后才关闭。
虽然此时活塞上⾏,但由于⽓流的惯性,⽓体仍能充⼈⽓缸。
第⼆冲程——压缩。
压缩时活塞从下⽌点间上⽌点运动,这个冲程的功⽤有⼆,⼀是提⾼空⽓的温度,为燃料⾃⾏发⽕作准备:⼆是为⽓体膨胀作功创造条件。
当活塞上⾏,进⽓阀关闭以后,⽓缸内的空⽓受到压缩,随着容积的不断细⼩,空⽓的压⼒和温度也就不断升⾼,压缩终点的压⼒和湿度与空⽓的压缩程度有关,即与压缩⽐有关,⼀般压缩终点的压⼒和温度为:Pc=4~8MPa,Tc=750~950K。
柴油的⾃燃温度约为543—563K,压缩终点的温度要⽐柴油⾃燃的温度⾼很多,⾜以保证喷⼊⽓随的燃油⾃⾏发⽕燃烧。
喷⼊⽓缸的柴油,并不是⽴即发⽕的,⽽且经过物理化学变化之后才发⽕,这段时间⼤约有0.001~0.005秒,称为发⽕延迟期。
因此,要在曲柄转⾄上⽌点前10~35°曲柄转⾓时开始将雾化的燃料喷⼊⽓缸,并使曲柄在上⽌点后5~10°时,在燃烧室内达到最⾼燃烧压⼒,迫使活塞向下运动。
高速柴油机连杆胀断工艺设计说明书

高速柴油机连杆胀断工艺设计说明书1. 引言高速柴油机是一种能够实现高效能和高功率输出的发动机,而连杆是高速柴油机中关键的部件之一。
连杆的胀断是指连杆在工作过程中由于长期受到重压和高温的影响,导致连杆出现断裂现象。
为了避免连杆胀断,需要进行工艺设计和改进。
本文将介绍高速柴油机连杆胀断工艺设计的相关内容。
2. 连杆胀断的原因分析连杆胀断的主要原因是由于连杆工作时受到高温和高压力的冲击,导致连杆内部产生过大的应力,超出材料的承受能力而发生断裂。
常见的原因有以下几个方面:- 过高的工作温度和压力:高速柴油机在工作时,由于燃烧产生的高温和高压力会对连杆产生巨大的冲击力,导致连杆内部应力集中,从而引发胀断。
- 连杆材质问题:连杆的材料不同,其承受能力也不同。
如果选用质量较差的材料,容易导致连杆胀断。
- 连杆设计不合理:连杆设计中的结构和力学参数对于其承受能力有着重要影响。
如果设计不合理,容易造成连杆胀断。
3. 工艺设计改进措施为了解决连杆胀断问题,我们可以采取以下几个方面的改进措施:- 优化材料选择:选择高强度、高硬度和高耐热性的材料作为连杆材料,以增加连杆的承受能力。
- 调整工作温度和压力:通过优化燃烧过程和冷却系统,降低高速柴油机的工作温度和压力,减轻连杆的负荷。
- 设计合理的连杆结构:根据高速柴油机的工作特点和承受力分析,合理设计连杆的结构和几何参数,使其能够承受更大的负荷。
- 强化连杆的加工工艺:在连杆的制造过程中,采用先进的热处理技术、表面处理技术和精密加工工艺,提高连杆的强度和耐磨性。
4. 工艺设计实施过程工艺设计的实施过程包括以下几个步骤:1) 进行材料研究: 对不同材料的机械性能、热处理性能和耐磨性等进行综合评估,选择合适的材料作为连杆材料。
2) 设计连杆结构: 根据高速柴油机的工作参数和力学分析,进行连杆的结构设计,包括长度、直径、连接方式等。
3) 进行热处理和表面处理: 根据选定的材料,使用适当的热处理工艺,提高连杆的硬度和强度;同时,采用表面处理技术,增加连杆的耐磨性和抗腐蚀性。
第二章_发动机连杆胀断工艺内容
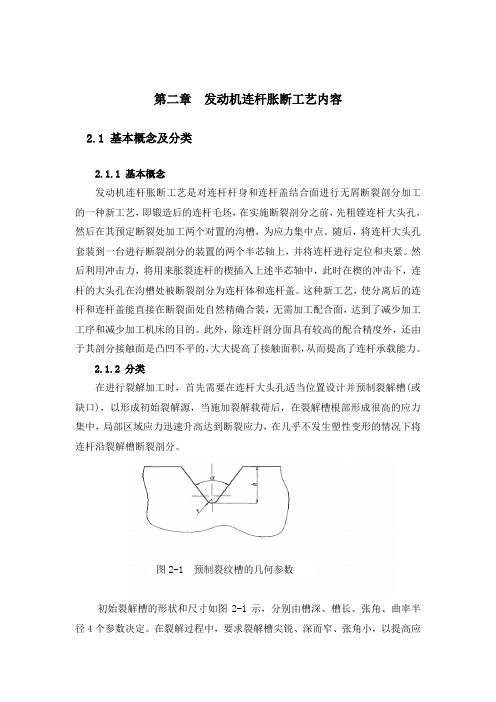
第二章发动机连杆胀断工艺内容2.1 基本概念及分类2.1.1 基本概念发动机连杆胀断工艺是对连杆杆身和连杆盖结合面进行无屑断裂剖分加工的一种新工艺,即锻造后的连杆毛坯,在实施断裂剖分之前,先粗镗连杆大头孔,然后在其预定断裂处加工两个对置的沟槽,为应力集中点。
随后,将连杆大头孔套装到一台进行断裂剖分的装置的两个半芯轴上,并将连杆进行定位和夹紧。
然后利用冲击力,将用来胀裂连杆的楔插入上述半芯轴中,此时在楔的冲击下,连杆的大头孔在沟槽处被断裂剖分为连杆体和连杆盖。
这种新工艺,使分离后的连杆和连杆盖能直接在断裂面处自然精确合装,无需加工配合面,达到了减少加工工序和减少加工机床的目的。
此外,除连杆剖分面具有较高的配合精度外,还由于其剖分接触面是凸凹不平的,大大提高了接触面积,从而提高了连杆承载能力。
2.1.2 分类在进行裂解加工时,首先需要在连杆大头孔适当位置设计并预制裂解槽(或缺口),以形成初始裂解源,当施加裂解载荷后,在裂解槽根部形成很高的应力集中,局部区域应力迅速升高达到断裂应力,在几乎不发生塑性变形的情况下将连杆沿裂解槽断裂剖分。
图2-1 预制裂纹槽的几何参数初始裂解槽的形状和尺寸如图2-1示,分别由槽深、槽长、张角、曲率半径4个参数决定。
在裂解过程中,要求裂解槽尖锐、深而窄、张角小,以提高应力集中系数,有效降低裂解加工载荷,从而减少裂解过程中因塑性变形而导致的连杆大头孔失圆,避免裂解缺陷,保证裂解加工质量。
因此,对初始裂解槽的合理设计,能有效提高缺口效应与应力集中系数,继而降低裂解力,提高裂解效率与质量。
发动机连杆胀断工艺按照裂解槽的加工方式可分为三种:机械加工初始裂解槽、线切割加工初始裂解槽和激光加工初始裂解槽三种。
2.1.2.1 机械加工初始裂解槽机械加工裂解槽是以推/拉削加工为主,如图2-2所示。
在切削过程中,通过刀柄上安装的刀具对裂解槽进行分层切削,从拉刀端头开始刀柄上每层刀具依次递增量为0.1 mm ,刀片数量根据裂解槽的深度来决定,并且裂解槽的张角、曲率半径均由推/拉刀具刃口来决定。
柴油发动机连杆课程设计说明书
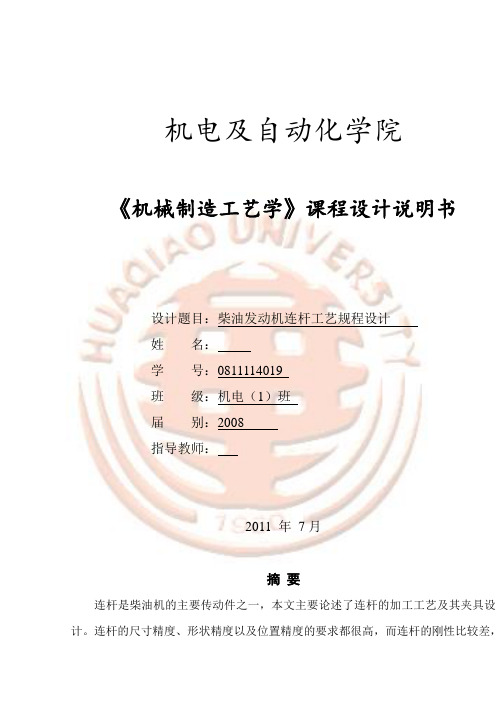
机电及自动化学院《机械制造工艺学》课程设计说明书设计题目:柴油发动机连杆工艺规程设计姓名:学号:0811114019班级:机电(1)班届别:2008指导教师:2011 年7月摘要连杆是柴油机的主要传动件之一,本文主要论述了连杆的加工工艺及其夹具设计。
连杆的尺寸精度、形状精度以及位置精度的要求都很高,而连杆的刚性比较差,容易产生变形,因此在安排工艺过程时,就需要把各主要表面的粗精加工工序分开。
逐步减少加工余量、切削力及内应力的作用,并修正加工后的变形,就能最后达到零件的技术要求。
机械加工工艺是企业上品种、上质量、上水平,加速产品更新,提高经济效益的技术保障。
然而夹具又是制造系统的重要部分,工艺对夹具的要求也会提高,专用夹具、成组夹具、组合夹具和随行夹具都朝着柔性化、自动化、标准化、通用化和高效化方向发展以满足加工要求。
所以对机械的加工工艺及夹具设计具有十分重要的意义。
目录摘要 (I)绪论 (4)第一章机械加工工艺规程的制定 (7)1.1零件的工艺性分析 (7)1.1.1产品结构和工艺分析 (7)1.1.2 平面加工 (7)1.1.3 孔加工 (8)1.1.4 技术要求分析 (8)1.2毛坯的确定 (9)1.2.1 有关设计条件的说明 (9)1.2.2. 毛坯的材料 (10)1.2.3 制坯方法的确定 (10)1.3连杆工件的定位基准和定位方案分析 (12)1.4加工经济精度与加工工序安排 (13)1.4.1加工经济精度 (13)1.4.2连杆加工主要加工表面的工序安排 (13)1.5典型表面的加工方法 (14)1.6连杆加工工艺过程的确定 (15)1.6.1定位基准的选择 (15)1.6.2工艺路线的拟定 (15)1.7加工设备与工艺装备的选择 (18)第二章机械加工工艺卡片的设计 (20)2.1确定加工工艺过程 (20)2.2机械加工余量的确定 (20)2.3各项加工数据的计算 (21)致谢 (28)参考文献 (30)绪论一、连杆的结构特点连杆是发动机的主要零件之一,它连接活塞和曲轴,把作用于活塞顶面的膨胀气体的压力传给曲轴;将活塞的往复运动变为曲柄的旋转运动,又受到曲轴的驱动而带动活塞压缩缩气缸中的气体。
第二章_发动机连杆胀断工艺内容教材

第二章发动机连杆胀断工艺内容2.1 基本概念及分类2.1.1 基本概念发动机连杆胀断工艺是对连杆杆身和连杆盖结合面进行无屑断裂剖分加工的一种新工艺,即锻造后的连杆毛坯,在实施断裂剖分之前,先粗镗连杆大头孔,然后在其预定断裂处加工两个对置的沟槽,为应力集中点。
随后,将连杆大头孔套装到一台进行断裂剖分的装置的两个半芯轴上,并将连杆进行定位和夹紧。
然后利用冲击力,将用来胀裂连杆的楔插入上述半芯轴中,此时在楔的冲击下,连杆的大头孔在沟槽处被断裂剖分为连杆体和连杆盖。
这种新工艺,使分离后的连杆和连杆盖能直接在断裂面处自然精确合装,无需加工配合面,达到了减少加工工序和减少加工机床的目的。
此外,除连杆剖分面具有较高的配合精度外,还由于其剖分接触面是凸凹不平的,大大提高了接触面积,从而提高了连杆承载能力。
2.1.2 分类在进行裂解加工时,首先需要在连杆大头孔适当位置设计并预制裂解槽(或缺口),以形成初始裂解源,当施加裂解载荷后,在裂解槽根部形成很高的应力集中,局部区域应力迅速升高达到断裂应力,在几乎不发生塑性变形的情况下将连杆沿裂解槽断裂剖分。
图2-1 预制裂纹槽的几何参数初始裂解槽的形状和尺寸如图2-1示,分别由槽深、槽长、张角、曲率半径4个参数决定。
在裂解过程中,要求裂解槽尖锐、深而窄、张角小,以提高应力集中系数,有效降低裂解加工载荷,从而减少裂解过程中因塑性变形而导致的连杆大头孔失圆,避免裂解缺陷,保证裂解加工质量。
因此,对初始裂解槽的合理设计,能有效提高缺口效应与应力集中系数,继而降低裂解力,提高裂解效率与质量。
发动机连杆胀断工艺按照裂解槽的加工方式可分为三种:机械加工初始裂解槽、线切割加工初始裂解槽和激光加工初始裂解槽三种。
2.1.2.1 机械加工初始裂解槽机械加工裂解槽是以推/拉削加工为主,如图2-2所示。
在切削过程中,通过刀柄上安装的刀具对裂解槽进行分层切削,从拉刀端头开始刀柄上每层刀具依次递增量为0.1 mm,刀片数量根据裂解槽的深度来决定,并且裂解槽的张角、曲率半径均由推/拉刀具刃口来决定。
柴油机连杆的工艺设计

第1章柴油机连杆分析1.1柴油机连杆零件的作用柴油机连杆由柴油机连杆大头、杆身和柴油机连杆小头三部分组成,柴油机连杆大头是分开的,一半与杆身为一体,一半为柴油机连杆盖,柴油机连杆盖用螺栓和螺母与曲轴主轴颈装配在一起。
柴油机连杆是较细长的变截面非圆形杆件,其杆身截面从大头到小头逐步变小,以适应在工作中承受的急剧变化的动载荷。
其形状也比较复杂,很多表面并不容易加工,不管是在其工作过程之中还是在加工过程中也很容易产生变形。
基本要求如:柴油机连杆杆身不垂直度<0.5,小头、大头两端面对称面与杆身相应对称面之间的偏移<0.6,杆身横向对称面对大小头孔中心偏移<1.首先必须保证大头中心孔中心线和小头孔中心线之间的平行度,这样才能保证柴油机连杆在工作过程中平稳不刮曲轴和轴瓦;第二个就是保证两个端面的平行度,以及两端面中心线与两孔中心线之间的垂直度,用于保证工作中不会刮伤曲轴平衡块,可以减少噪声,保持平稳;第三个要保证的是柴油机连杆体和盖的分和面之间的配合和吻合,以保证大头孔的圆柱度,以免刮伤轴瓦;第四要确保大小头孔中心线之间的距离,如果其得不到保证,将保证不了发动机在工作时的气体压缩比等。
1.2零件的工艺分析由零件图可知:可将其分为三组加工表面。
它们相互间有一定的位置要求。
现分析如下:首先柴油机连杆的加工表面如下:(1)以端面互为基准加工的两端面。
(2)以小头孔为中心的加工有:钻两个Φ4的油孔,加工侧面工艺凸台。
(3)以大头孔为中心的加工表面有:加工M12螺栓孔。
柴油机连杆精度的参数主要有五个:1.柴油机连杆大端中心面和小端中心面相对于柴油机连杆身中心面的对称;2.柴油机连杆大小头空中心距尺寸精度;3.柴油机连杆大小头孔平行度;4.柴油机连杆大小头孔的尺寸精度、形状精度;5.柴油机连杆大头螺栓孔与接合面的垂直度。
其余技术参数如下表:表1技术要求项目具体要求或数值满足的主要性能大、小头孔的椭圆度,锥度椭圆度0.012锥度0.014保证与衬套、轴瓦的良好配合两孔中心距0.030.05 气缸气体的压缩比两孔轴线在同一个平面内在柴油机连杆轴线平面内:0.03,在垂直柴油机连杆轴线平面内:0.06减少气缸壁和曲轴颈磨损大孔两端面对轴线的垂直度0.015 减少曲轴颈边缘磨损两螺孔中心线(定位孔)的位置精度在两个在45方向上的平行度:0.020.04,对结合面的垂直度:0.015保证正常承载和轴颈与轴瓦的良好配合第2章机械加工工艺规程设计2.1生产纲领的确定生产纲领的大小对生产组织和零件加工工艺过程起着重要的作用,它决定了各工序所需专业化和自动化的程度,以及所选用的工艺方法和工艺装备。
柴油机连杆零件毕业设计说明书

连杆是汽车发动机主要的传动机构之一,它将活塞与曲轴连接起来,把作用于活塞顶部的膨胀气体压力传给曲轴,使活塞的往复直线运动可逆的转化为曲轴的回转运动,以输出功率。
是为发动机提供安全可靠、经久耐用、节省能源、满足功用的一个重要零件,它对开发轻型、高速、大功率的柴油机有着密切的关系。
因此,连杆的合理结构设计、加工工艺性设计,保证连杆的加工质量,提高生产效率有这重要意义,它是保证柴油机产品质量的关键所在。
此说明书,对连杆零件进行了详细的分析。
设计出了零件加工的工艺规程。
在工艺规程中涉及到了连杆加工的加工工艺,加工设备的选择,加工余量的确定,毛坯的确定,机床、刀具的确定,夹具的设计一系列与连杆加工有紧密联系的因素。
通过对此次设计,学会对中等难度零件的工艺编制,及其特定工序的夹具设计。
关键词:工艺;毛坯;夹具。
ABSTRACTThe connecting rod module is in the diesel engine essential movement power transmission component. It is affects the gas physical strengthand so on each kind of strength transmits on the piston gives the crank, also transforms the crank rotary motion into the piston reciprocal motion part. Is safely provides reliable, durable, the economical energy, satisfied function important components for the engine, it to develops lightly, is high speed, the high efficiency diesel engine has close relationship. Therefore, the connecting rod reasonable structural design, the processing technology capability design, guaranteed the connecting rod the processing quality, enhances the production efficiency to have this vital significance, it is guaranteed the diesel engine product quality the key is at. This instruction book let, has carried on the detailed analysis to the connecting rod components.Designed the components processing technological process. A series of involved the processing craft in the technological process which the connecting rod processed, the processing equipment choice, the processing remainder determination,the semifinished materials determination, the engine bed, the cutting tool determination, the jig design with the connecting rod processing had the close relation the factor.By the endtime of the densign,learn the technics weave of medium difficultry part,and the holding design of the especially working procedure.Key words:roughcast; craft; jig目录目录绪论 (1)1. 零件的工艺分析 (2)1.1 连杆的工作情况 (2)1.2 连杆的结构特点 (2)1.3 连杆机械加工的主要技术要求 (3)2. 毛坯的确定 (4)2.1生产类型的确定 (4)2.2 材料的选择 (4)2.3 毛坯种类与方法的确定 (4)2.4 确定毛坯尺寸公差和加工余量 (4)2.5 毛坯主要加工表面的尺寸及公差的确定 (6)3. 连杆工艺规程的编制 (7)3.1 定位基准的选择 (7)3.2 拟订工艺路线 (7)3.2.1选择表面加工方法 (7)3.2.2加工阶段的划分 (8)3.2.3加工工序的顺序安排 (8)3.2.4机械加工余量、工序尺寸及其公差的确定 (11)3.2.5加工设备与工艺装备的选择 (22)4. 夹具设计 (26)4.1 夹具体材料及制造方法 (26)4.2 夹具体结构设计 (26)4.3 定位分析与定位误差计算 (26)4.4 导向元件的设计 (26)4.5 螺栓、垫圈选择 (27)4.6 夹具的工作原理 (27)结论 (28)致谢 (29)参考文献 (30)文献综述绪论绪论本课题研究的主要內容是连杆加工工艺过程的编制以及在加工中用到的一些典型夹具的设计。
- 1、下载文档前请自行甄别文档内容的完整性,平台不提供额外的编辑、内容补充、找答案等附加服务。
- 2、"仅部分预览"的文档,不可在线预览部分如存在完整性等问题,可反馈申请退款(可完整预览的文档不适用该条件!)。
- 3、如文档侵犯您的权益,请联系客服反馈,我们会尽快为您处理(人工客服工作时间:9:00-18:30)。
目录摘要ⅢAbstractⅣ第一章绪论11.1 前言11.2 国外发动机连杆工艺发展现状和发展趋势3 1.3 连杆工艺研究方向和研究的关键问题3第二章连杆零件的分析52.1 连杆的结构功能分析52.2 连杆的主要技术要求6第三章连杆零件机械加工工艺规程的编制7 3.1 生产纲领的确定73.2 连杆的工艺分析83.3 连杆的材料选择与毛坯的制造方法83.3.1连杆的材料选择83.3.2 C70S6钢的成分和力学性能103.3.3 毛坯的制造方法113.4 机械加工余量,工序尺寸及毛坯尺寸确定13 3.5 指定工序定位基准的选择133.6 加工工艺阶段的划分和加工顺序的安排153.7 连杆加工工艺过程的拟定163.8填写机械加工工艺过程卡和机械加工工序卡16 第四章指定工序的工装设计174.1 机床夹具设计的基本要求174.2 专用夹具设计步骤174.3激光开应力槽工装设计194.3.1 应力槽的设计194.3.2 设备的选择与改装204.3.3 拟定定位方案204.4胀断工装设计214.4.1 设备选择214.4.2拟定定位方案214.4.3夹具使用说明214.4.4 胀断参数的计算23总结24参考文献25致26105系列高速柴油机连杆工艺总体方案及指定工装设计摘要连杆是柴油发动机的主要部件之一,它决定着发动机的性能和运行的稳定性。
随着科学技术的发展与进步,连杆的制造被注入了现代化的加工手段。
“胀断工艺”成为了连杆工艺中的又一新名词。
连杆胀断工艺的应用,使连杆在加工质量、生产率和生产成本等诸多方面都发生了显著变化,柴油发动机的性能得到了进一步提升。
本文以柴油机连杆制造工艺的总体方案为主要研究容,以连杆的胀断工艺为主要研究方向。
总体方案涉及从连杆材料的选择到加工为成品的全部工艺过程。
方案特别对胀断工艺的原理及过程做了深入浅出的论述,并在认真分析连杆技术要求、广泛查阅相关文献的基础之上,制定出了一条基本适于连杆实际生产的新型工艺方案和路线。
同时,笔者还重点设计了“激光开应力槽”、“胀断”两工序的夹具和工艺装备。
关键词:柴油机连杆,工艺方案,胀断工装The General Planning of 105 Series High Speed Diesel Engine Products’ Conn ect ing Rod’s ProcessingTechnicand the designated Design of Clamping DeviceAbstractLinkage of the diesel engine is one of the main parts of its decision to the engine performance and the stability. With the scientific and technological development and progress of the link was injected into a modern manufacturing processing methods. "Expansion of off" has become a link in the process of yet another new term. Linkage bulging off the application process so that the link in the processing quality, productivity and production costs, and so have undergone significant changes, the diesel engine has been further enhance performance.Diesel link this to the overall manufacturing process for major research programme, to link the expansion of off the main research directions. Linkage of the overall plan from the choice of materials to finished products for processing all the process. Special programmes on the principle of expansion off course and had to learn to do the exposition and careful analysis of technical requirements of connecting rod, widely accessible on the basis of relevant literature, worked out a basic link suitable for the actual production of new programmes and Line. At the same time, the author also focused on the design of the "open laser stress trough," "bulging off" the two processes of the fixture and process equipment.Key words :Diesel engine,Technology of process, Clamping device of the splitting第一章绪论1.1 前言连杆在发动机中作为改变力的传递方向和方式最重要的零部件之一,用于各种发动机上,其大头孔与曲轴连接,小头孔通过活塞销与活塞连接,将作用于活塞的气体膨胀压力的直线运动传给曲轴转变为旋转运动(图1.1)。
在工作过程中,其承受着较高的周期性冲击力、惯性力、压缩应力、纵向弯曲应力、拉应力、动载荷等,因此要求连杆重量要轻,必须有较高的强度、韧性和疲劳性能。
图1.1 连杆动力转化图发动机的可靠性在很大程度上取决于连杆的可靠程度,在连杆的总成可靠性的因素之中分合面质量与定位关系是主要因素,因此解决好连杆体与连杆盖之间的定位问题,可以降低连杆的生产成本,提高发动机的可靠性。
但由于连杆的外形比较复杂、容易变形、刚性差,尺寸精度、位置精度以及表面质量等要求较高,在制造上具有一定难度。
而其连杆制造技术的好坏直接影响着连杆的使用性能和经济性能以及一个企业的生存和发展,随着生产技术的发展,传统的制造技术渐渐不能适应现在生产的要求。
先后在国外很多连杆生产厂家提出了“胀断技术”(又涨断技术或裂解技术),国少部分连杆生产厂家也已采用该技术。
据相关文章介绍,发动机连杆胀断加工技术是目前国际上连杆生产的最新技术,随着连杆生产技术的发展,连杆体与盖的分离不再采用铣、锯或拉这类传统切削加工方法,而是采用了最新的胀断技术。
该技术是以整体加工代替分体加工,用切口(用机械方法或激光技术等方法制造预裂纹) 断裂,使大端连杆盖从连杆体移去,使连杆体与盖的分离达到理想的脆性断裂,并能很容易达到其连杆使用性能要求的一门先进技术(图1.2)。
图 1.2 胀断过程示意简图采用胀断工艺有如下优点:1.简化了连杆及连杆盖的设计要求;2.采用连杆胀断工艺后,连杆与连杆盖的分离面是最完全的啮合,所以其无需再进行机加工,省略了分离面的磨削加工;3.连杆体与连杆盖装配时无需额外的精确定位,如螺栓孔定位(或定位环孔),只需螺栓拉紧即可,这样省去了螺栓孔的精加工(如铰或镗)。
与传统连杆加工方法相比,胀断工艺的优势很大:减少了加工工序、节省精加工设备、节省刀具磨损、节材料和能源、降低生产成本等,连杆胀断加工技术还可提高连杆承载能力、抗剪能力、杆和盖的定位精度及装配质量,对提高发动机生产技术水平和整机性能具有很重要作用。
综上所述,以体现自己大学四年来所学理论知识与实际生产联系的综合,锻炼自己的独立思考、自我创新的意识和能力为目的,在采用胀断技术的基础上,探索和制定出一条能提高连杆的质量和减少连杆制造成本,并基本适应实际生产的方案,故选择该课题作为本次毕业设计的题目。
1.2 国外发动机连杆工艺发展现状和发展趋势在毛坯材料方面:国传统工艺连杆毛坯材料一般采用42CrMo 、35CrMo 、40MnVB、45CrMnB、40Cr 、 40CrMnB S40C等调质钢和S43CVS1 (进口) 、35MnV、40MnS等非调质钢。
康明斯生产线采用调质钢毛坯40MnBH(GB5216-85),1995年全面转用非调质钢材料毛坯38MnV。
60年代中期粉末热锻技术开始发展起来,从80年代以来粉末冶金注射成型(PIM)成功的得到应用,大多数连杆制造中使用的中碳钢和低合金钢逐步由新钢种和粉末冶金的锻造材料所代替。
而德国发动机系统和零部件的专家MahleGmbH公司先后推出了C70S6BY钢、36MnVS4BY钢、 70MnVS4BY钢等可用于胀断的材料。
在加工工艺方面:国外连杆生产方式大致有:锻造、铸造、粉末冶金等,进入90年代后,90%以上的连杆制造都采用了模锻工艺;传统锻造有将连杆体和盖分开锻造、连杆整体锻造两种,连杆体与连杆盖分离方式一般采取锯断、铣断等工艺。
国外很多连杆生产厂家提出关于连杆体与盖分离最新工艺是使用断裂分开,即胀断工艺(又涨断工艺或裂解工艺),该工艺是用切口(用机械方法或用激光等方法制造预裂纹, 国常用的裂解槽加工方法有机械拉削、线切割,国外采用水刀和激光加工),形成应力集中,主动施加垂直预定断裂面载荷进行引裂,在几乎不发生变形的情况之下,在缺口处规则脆性断裂,实现连杆体与连杆盖的无屑断裂剖分,使大端连杆盖从连杆体移去。
国部分汽车厂及设备制造厂如一汽—大众、大众和通用等都采用了该技术。
1.3 连杆工艺研究方向和研究的关键问题本设计的目的主要是制定一条适合胀断工艺的工艺方案,基本需要解决以下问题:首先是要确定毛坯的材料以及其毛坯的制造方法。
目前,绝大多数连杆是由需要淬火和回火的中碳钢和低合金钢经过锻造加工制造的,但正不断由新钢种和粉末冶金的锻造材料所代替。
胀断连杆要求其材料塑性变形小、强度好、脆性适中、工艺性好,即在保证连杆强韧综合性能指标的前提下,限制连杆的韧性指标,使断口呈现脆性断裂特征。
而可用于连杆裂解的材料主要有粉末烧结材料、高碳钢、球墨铸铁、可锻铸铁。