连杆设计的详细计算
连杆计算
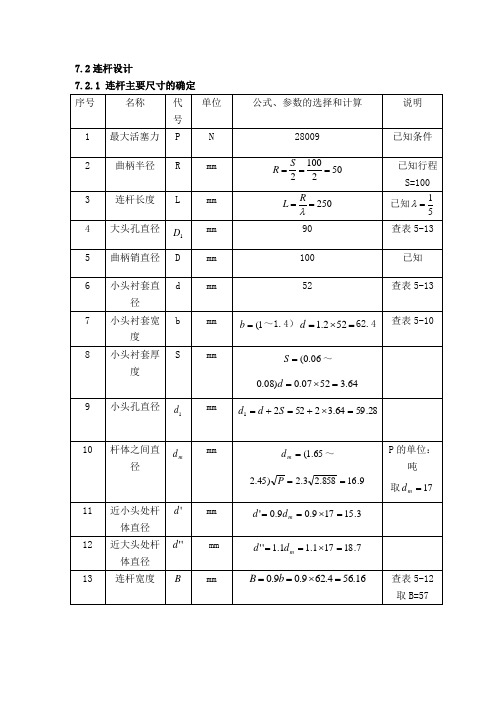
惯性矩
7
连杆摆动平面纵弯应力
8
杆体的长度
mm
9
惯性矩
10
垂直于连杆摆动平面纵弯应力
11
在连杆摆动平面总应力
12
垂直于连杆摆动平面总应力
13
大头盖截面 处抗弯截面模数
14
截面A-A弯曲应力
15
小头处截面C-C抗弯截面模数
16
小头侧壁中心距
mm
17
截面C-C弯曲应力
7.2连杆设计
7.2.1连杆主要尺寸的确定
序号
名称
代号
单位
公式、参数的选择和计算
说明
1
最大活塞力
P
N
28009
已知条件
2
曲柄半径
R
mm
已知行程
S=100
3
连杆长度
L
mm
已知
4
大头孔直径
mm
90
查表5-13
5
曲柄销直径
D
mm
100
已知
6
小头衬套直径
d
mm
52
查表5-13
7
小头衬套宽度
b
mm
~1.4) 62.4
~
20
截面C-C的厚度mm取 Nhomakorabea21
连杆螺栓直径
mm
~
P的单位:吨
22
两螺栓间距离
mm
120
查表5-13
23
螺栓在大头体内长度
mm
~
24
螺栓在大头盖内长度
mm
~
7.2.2连杆的计算
序号
名称
代号
单位
连杆设计方法总结
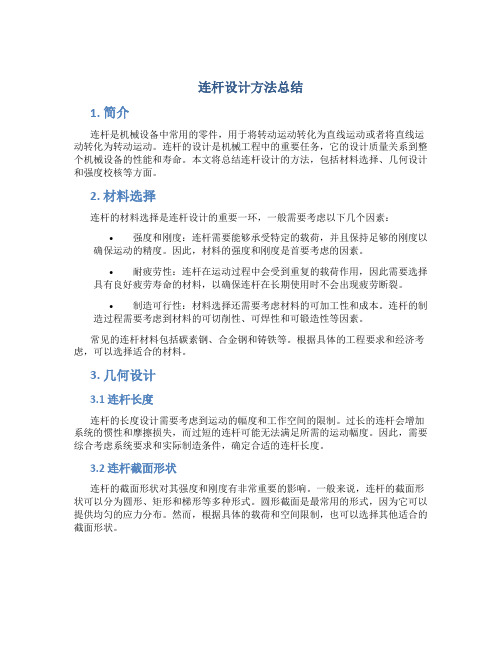
连杆设计方法总结1. 简介连杆是机械设备中常用的零件,用于将转动运动转化为直线运动或者将直线运动转化为转动运动。
连杆的设计是机械工程中的重要任务,它的设计质量关系到整个机械设备的性能和寿命。
本文将总结连杆设计的方法,包括材料选择、几何设计和强度校核等方面。
2. 材料选择连杆的材料选择是连杆设计的重要一环,一般需要考虑以下几个因素:•强度和刚度:连杆需要能够承受特定的载荷,并且保持足够的刚度以确保运动的精度。
因此,材料的强度和刚度是首要考虑的因素。
•耐疲劳性:连杆在运动过程中会受到重复的载荷作用,因此需要选择具有良好疲劳寿命的材料,以确保连杆在长期使用时不会出现疲劳断裂。
•制造可行性:材料选择还需要考虑材料的可加工性和成本。
连杆的制造过程需要考虑到材料的可切削性、可焊性和可锻造性等因素。
常见的连杆材料包括碳素钢、合金钢和铸铁等。
根据具体的工程要求和经济考虑,可以选择适合的材料。
3. 几何设计3.1 连杆长度连杆的长度设计需要考虑到运动的幅度和工作空间的限制。
过长的连杆会增加系统的惯性和摩擦损失,而过短的连杆可能无法满足所需的运动幅度。
因此,需要综合考虑系统要求和实际制造条件,确定合适的连杆长度。
3.2 连杆截面形状连杆的截面形状对其强度和刚度有非常重要的影响。
一般来说,连杆的截面形状可以分为圆形、矩形和梯形等多种形式。
圆形截面是最常用的形式,因为它可以提供均匀的应力分布。
然而,根据具体的载荷和空间限制,也可以选择其他适合的截面形状。
3.3 连杆连接方式连杆的连接方式也是设计中需要考虑的因素之一。
常见的连接方式包括销销和螺栓连接等。
具体选择哪种连接方式需要综合考虑连杆的应力和振动情况,以及连接方式的制造成本和可靠性等因素。
4. 强度校核连杆的强度校核是设计过程中的关键一步。
强度校核的目的是确保连杆在工作过程中不会发生破坏。
常用的强度校核方法包括静态强度校核和疲劳强度校核。
4.1 静态强度校核静态强度校核主要是根据连杆的应力状态和工作载荷,计算连杆的应力和应变,然后与材料的强度和可靠度要求进行比较。
概念设计阶段连杆强度计算规范

CAE 规范第1部分:概念设计阶段连杆强度计算1 范围本部分规定了连杆强度的校核方法。
本部分适用于概念设计阶段连杆强度的校核,以安全系数表示连杆在发动机产品生命周期内的安全裕度。
对船用发动机,需同时采用船检规范进行校核。
2 名称、符号图1 连杆杆身最小截面模型示意图表-1 连杆强度计算参数序号 名称 符号单位 1连杆质量rod m kg2 活塞组质量 pst mkg 3 连杆长度 Lmm 4 缸套内径 D mm 5连杆大头轴瓦宽度ps Lmm6 连杆主轴瓦宽度js Lmm7 杆身最小截面积 A2mm 8 极惯性矩(z 轴) z I 4mm 9极惯性矩(y 轴)y I4mmσMPa10 材料的屈服极限sL mm11 连杆大小头孔中心距y12 连杆杆身长z L mm13 材料的抗拉强度bσMPaσMPa13 材料的疲劳极限1-14 转速n rpm15 最大爆压g p MPa 3 计算流程图2 流程图4 计算原理连杆的设计基于对高应力区域的疲劳安全进行评估。
本规范中的计算基于以下假定:●连杆小头内侧、杆身过渡圆角处、大头盖螺栓台阶面是高应力区域;●活塞组往复惯性力以轴向抛物线、径向120°余弦分布作用在小头衬套和连杆轴瓦上;●爆发压力以轴向抛物线、径向120°余弦分布作用在小头衬套和连杆轴瓦上;●活塞组往复惯性力、爆发压力是引起连杆破坏的主要因素,连杆旋转惯性力产生的影响很小,可以忽略不计。
5 计算工况对长期稳定工作于额定转速的发动机,以全负荷工况为计算工况;对在大转速范围内工作的发动机,以额定转速为计算工况;对船用发动机,以超负荷(110%负荷)工况为计算工况。
通常,一个工作周期内,由燃气压力和惯性力引起的作用在连杆上的径向载荷对所有曲柄位置都应计算。
简单起见,径向力可以采用简化计算,并只计算一个工作周期内的最大受拉和最大受压两种状态。
6 连杆载荷6.1 压杆稳定时连杆载荷连杆属于细长杆件类的柴油机零件,在承受较大爆发压力的工况下须做杆件的稳定性校核:临界载荷由Rankine Gordan 公式计算:p zz F pn = py yF p n =6.2 连杆受到惯性载荷连杆载荷以大小头孔轴向抛物线、径向120°余弦分布的分布力作用在衬套和连杆轴瓦上,作用范围为连杆大头轴瓦宽度(见图3-b ),其大小按以下公式计算:θθ23cos )41(25),(22psps p p p L x L D F x q -⋅=p F :作用在衬套和连杆轴瓦上的径向载荷,N ;对于连杆小头p F 可按曲柄连杆动力学或多体动力学计算得到,对V 型机,p F 应考虑不同的相位和连杆设计(分叉连杆、连接连杆、并列连杆等)分别计算与合成。
02平面连杆机构的设计计算
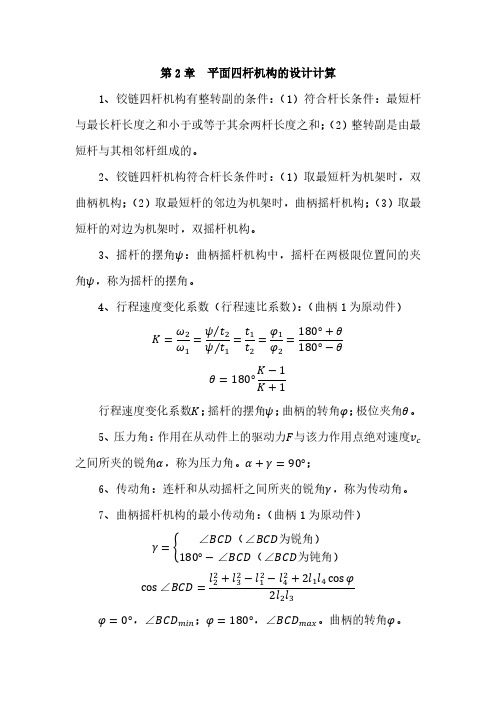
180°+
180°−
= 3.17 ;
摇杆摆角: = ∠ ′ − ∠ " = 90.07° 。
例 2-3 设计一曲柄摇杆机构。已知摇杆长度3 = 100,摆
角 = 30°,摇杆的行程速度变化系数 = 1.2。
(1)用图解法确定其
余三杆的尺寸;
(2)用式(2-6)和式(2-7)确定机构最小传动角(若
第2章
平面四杆机构的设计计算
1、铰链四杆机构有整转副的条件:(1)符合杆长条件:最短杆
与最长杆长度之和小于或等于其余两杆长度之和;
(2)整转副是由最
短杆与其相邻杆组成的。
2、铰链四杆机构符合杆长条件时:(1)取最短杆为机架时,双
曲柄机构;
(2)取最短杆的邻边为机架时,曲柄摇杆机构;
(3)取最
短杆的对边为机架时,双摇杆机构。
位置如题 2-13 图所示,
1 = 45°,
1 = 52°10′;2 = 90°,
2 = 82°10′;
3 = 135°,2 = 112°10′,机架长度 = 50 ,试用解析法求其
余三杆长度。
2-13 解:已知:
1 + 2 = 50 + 3
(b) 最短杆与最长杆长度之和= 45 + 120 = 165
其余两杆长度之和= 100 + 70 = 170
①满足杆长条件:最短杆与最长杆长度之和≤其余两杆长度之和;
②最短杆的邻边为机架;
所以此铰链四杆机构为曲柄摇杆机构。
(c) 最短杆与最长杆长度之和= 60 + 100 = 160
其余两杆长度之和= 70 + 62 = 132
曲轴和连杆的设计与计算
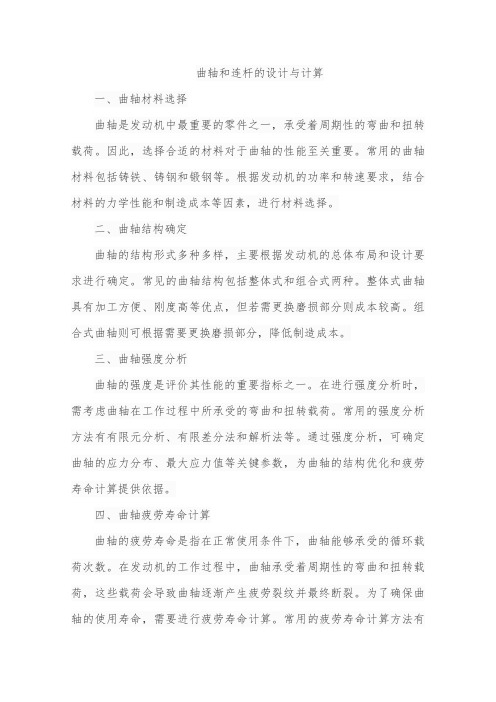
曲轴和连杆的设计与计算一、曲轴材料选择曲轴是发动机中最重要的零件之一,承受着周期性的弯曲和扭转载荷。
因此,选择合适的材料对于曲轴的性能至关重要。
常用的曲轴材料包括铸铁、铸钢和锻钢等。
根据发动机的功率和转速要求,结合材料的力学性能和制造成本等因素,进行材料选择。
二、曲轴结构确定曲轴的结构形式多种多样,主要根据发动机的总体布局和设计要求进行确定。
常见的曲轴结构包括整体式和组合式两种。
整体式曲轴具有加工方便、刚度高等优点,但若需更换磨损部分则成本较高。
组合式曲轴则可根据需要更换磨损部分,降低制造成本。
三、曲轴强度分析曲轴的强度是评价其性能的重要指标之一。
在进行强度分析时,需考虑曲轴在工作过程中所承受的弯曲和扭转载荷。
常用的强度分析方法有有限元分析、有限差分法和解析法等。
通过强度分析,可确定曲轴的应力分布、最大应力值等关键参数,为曲轴的结构优化和疲劳寿命计算提供依据。
四、曲轴疲劳寿命计算曲轴的疲劳寿命是指在正常使用条件下,曲轴能够承受的循环载荷次数。
在发动机的工作过程中,曲轴承受着周期性的弯曲和扭转载荷,这些载荷会导致曲轴逐渐产生疲劳裂纹并最终断裂。
为了确保曲轴的使用寿命,需要进行疲劳寿命计算。
常用的疲劳寿命计算方法有名义应力法和局部应力应变法等。
通过疲劳寿命计算,可确定曲轴的安全系数和疲劳强度等关键参数,为曲轴的材料选择和结构优化提供依据。
五、连杆长度和厚度设计连杆是连接曲轴和活塞的重要零件,其长度和厚度对发动机的性能和可靠性有着重要影响。
在进行连杆长度和厚度设计时,需考虑发动机的整体布局和设计要求。
连杆长度主要根据发动机的燃烧室高度和活塞行程确定,而连杆厚度则根据连杆所承受的弯曲和扭曲载荷进行计算和分析。
六、连杆强度分析连杆在工作过程中所承受的载荷包括气体压力、惯性力、摩擦力和弯曲力矩等。
为了确保连杆的使用寿命和可靠性,需要进行强度分析。
常用的强度分析方法有解析法和有限元法等。
通过强度分析,可确定连杆在工作过程中的应力分布、最大应力值等关键参数,为连杆的材料选择和结构优化提供依据。
机械原理-连杆机构设计图解法_一_
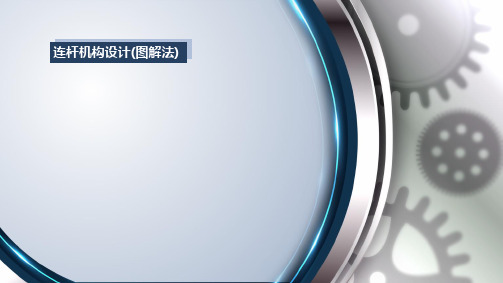
连杆机构设计(图解法)
按给定连杆位置设计四杆机构 按给定两连架杆对应的角位移设计四杆机构
按给定的急回要求设计四杆机构
按给定连杆位置设计四杆机构
按给定连杆位置设计四杆机构
给定连杆三个位置,设计四杆机构
B1
A1
E1
A
2
E2
A3
B2
A0
B0
E3
B3
A0 A1 B1 B0就是所求机构的第一个位置。
m12
N1 M2
n12
M1 M0
动平面上任选两个参考点 M、N——动铰链
N2
12 12
P12
N0
m12上任选M0—定铰链
n12上任选N0—定铰链
引导平面由E1到E2的位置的 四杆机构有无数
两连架杆上动铰链和定铰链与极连线的夹角 相等∠M1 P12 M0= ∠N1 P12 N0= θ 12/2
方法:半角转动法
方法:半角转动法
原理
N1 M1 M2 E1 E2 N2
动平面由E1到E2的位置过程中,动 平面上任意一点都可以视为绕某点 P12转θ 12
P12——转动极(极)
θ 12——有向转动角
E1、E2两个位置一经确定,P12、 θ 12就确定与选择的参考点无关
12
P12
转动极P12 的求法
m12
N1 M2
n12
M1
连接P12M1和P12M2,所夹 的角即为转动角θ 12
N2
12 12
P12
连接P12 N1和P12 N2 ,所 夹的角也为转动角θ 12 ∠M1 P12 M2= ∠N1 P12 N2= θ 12
动平面由E1到E2的位置可由四杆机构实现
02平面连杆机构的设计计算
02平面连杆机构的设计计算设计计算是指根据设计要求和机构参数进行计算,以确定机构的尺寸、材料和工作性能等技术指标的过程。
本文将介绍02平面连杆机构的设计计算,包括机构类型选择、杆件尺寸设计和运动性能分析等。
一、机构类型选择1.传动比要求:根据实际需要确定机构的传动比,即输入与输出杆件的运动比值。
2.运动要求:根据机构所需完成的运动类型和精度要求,选择适合的机构类型。
3.结构紧凑度:考虑机构安装空间、结构合理性和制造工艺等因素,选择紧凑、易制造的机构类型。
二、杆件尺寸设计杆件尺寸设计是机构设计的关键环节,决定着机构的强度、刚度和运动特性。
具体步骤如下:1.确定负荷:根据使用条件和设计要求,确定机构的负荷、转矩和速度等参数。
2.计算受力:根据杆件的位置和受力情况,计算杆件的拉压应力和弯矩等。
3.材料选择:根据受力情况和材料性能,选择合适的材料,如碳钢、合金钢等。
4.尺寸计算:根据受力计算结果,计算杆件的截面尺寸、直径和长度等。
5.强度校核:根据材料强度和尺寸,进行强度校核,确保杆件在工作条件下不发生破坏。
6.刚度分析:根据杆件尺寸和连接方式,计算机构的刚度和变形情况,确保机构的工作精度。
三、运动性能分析运动性能分析是对机构运动特性进行计算和评估的过程,对于确定机构的工作性能和优化设计具有重要意义。
具体步骤如下:1.运动解析:根据机构的运动模式和约束条件,进行运动解析,得到机构的运动方程和转角速度等。
2.运动参数计算:根据机构的运动方程和参数,计算机构的位移、速度、加速度和滑动速度等。
3.动力学分析:对机构的动力学特性进行计算和分析,包括惯性力、弹性力和粘性力等。
4.稳定性分析:对机构的稳定性进行分析,确保机构的运动平稳和可靠性。
5.优化设计:根据运动性能分析结果,对机构的参数和结构进行优化设计,提高机构的工作效率和精度。
总结:02平面连杆机构的设计计算是通过选择合适的机构类型、进行杆件尺寸设计和运动性能分析,来确定机构的尺寸、材料和工作性能等指标。
连杆设计的详细计算
第四章典型零部件(连杆)的设计连杆是发动机最重要的零件之一,近代中小型高速柴油机,为使发动机结构紧凑,最合适的连杆长度应该是,在保证连杆及相关机件运动时不与其他机件相碰的情况下,选取小的连杆长度,而大缸径的中低速柴油机,为减少侧压力,可适当加长连杆。
连杆的结构并不复杂,且连杆大头、小头尺寸主要取决于曲轴及活塞组的设计。
在连杆的设计中,主要考虑的是连杆中心距以及大、小头的结构形式。
连杆的运动情况和受力状态都比较复杂。
在内燃机运转过程中,连杆小头中心与活塞一起作往复运动,承受活塞组产生的往复惯性力;大头中心与曲轴的连杆轴颈一起作往复运动,承受活塞连杆组往复惯性力和不包括连杆大头盖在内的连杆组旋转质量惯性力;杆身作复合平面运动,承受气体压力和往复惯性力所产生的拉伸.压缩交变应力,以及压缩载荷和本身摆动惯性力矩所产生的附加弯曲应力。
为了顺应内燃机高速化趋势,在发展连杆新材料、新工艺和新结构方面都必须既有利于提高刚度和疲劳强度,有能减轻质量,缩小尺寸。
对连杆的要求:1、结构简单,尺寸紧凑,可靠耐用;2、在保证具有足够强度和刚度的前提下,尽可能的减轻重量,以降低惯性力;3、尽量缩短长度,以降低发动机的总体尺寸和总重量;4、大小头轴承工作可靠,耐磨性好;5、连杆螺栓疲劳强度高,连接可靠。
但由于本设计是改型设计,故良好的继承性也是一个考虑的方面。
4.1连杆材料结合发动机工作特性,发动机连杆材料应当满足发动机正常工作所需要的要求。
应具有较高的疲劳强度和冲击韧性,一般选用中碳钢或中碳合金钢,如45、40Cr等,本设计中发动机为中小功率发动机,故选用一般的45钢材料基本可以满足使用要求。
4.2连杆主要尺寸 1、连杆长度l曲柄连杆比λ一般均大于0.3,这样可以使柴油机的机体高度降低,净质量减少,而且连杆长度减小后,其材料也相应减少,从而成本降低。
但是,过小的曲柄连杆比会引起活塞侧压力增加,从而导致柴油机摩擦损失的增加,加速活塞、活塞环、气缸套的磨损,影响可靠性。
汽油机曲柄连杆机构设计—连杆
课程设计任务书学 院 汽车与交通学院专 业 热能与动力工程 学生姓名班级学号课程设计题目 汽油机曲柄连杆机构设计—连杆实践教学要求与任务:1. 设计参数求:Pe=33.5kW/5000rp ;D=65mm ;8.8=c ε(参考)2. 设计内容及要求:1)选取基本参数、热计算、绘制示功图(1)利用EXCEL 或其他程序语言进行近似热计算,得到理论的示功图的数据。
(2)以该数据为依据,在坐标纸01上绘制理论的示功图,并对其进行修正,得到实际的示功图。
(3)将图转换成图,绘制在坐标纸02上。
2)零部件设计(1)独立设计该汽油机的连杆,用CATIA 软件绘出三维实体模型,求出其质心位置和当量质量。
(2)将三维图形转换成二维的工程图,并正确标注尺寸、粗糙度、公差等,并以A1的图纸打印。
3)动力计算(1)计算活塞的位移、速度和加速度,并绘制曲线图附在设计说明书中。
(2)活塞连杆作用力分析,将往复运动惯性力P j 、侧压力P N 、 切向力T 、法向力K 随曲轴转角的变化曲线附在设计说明书中。
(3)计算曲柄销载荷和连杆轴承载荷,并将图形附在设计说明书中。
4)设计说明书。
其中包括:(1)成绩评定表、课程设计任务书;(2)汽油机设计指标及其参数的选定;(2)热计算过程;(3)零部件设计过程;(4)动力计算过程;(5)附录(程序或用EXCEL 的计算表格)工作计划与进度安排:1. 选取基本参数、热计算、绘制示功图 5天2. 零部件设计 6天3. 3D 建模 2天4. 动力计算 2天5. 编写设计说明书 2天6. 答辩 1天指导教师:2012年12月21日专业负责人:2012年12月21日学院教学副院长:2012年 月 日目录1 汽油机设计参数---------------------------------------------------------------------------22 汽油机基本结构参数选用---------------------------------------------------------------33 近似热计算---------------------------------------------------------------------------------43.1燃料燃烧热学计算---------------------------------------------------------------------43.2换气过程计算---------------------------------------------------------------------------43.3压缩过程计算---------------------------------------------------------------------------53.4燃烧过程计算---------------------------------------------------------------------------63.5膨胀过程计算---------------------------------------------------------------------------83.6示功图绘制------------------------------------------------------------------------------93.7汽油机性能指标计算-----------------------------------------------------------------104 连杆三维建模----------------------------------------------------------------------------114.1连杆基本尺寸---------------------------------------------------------------------------114.2连杆的建模过程------------------------------------------------------------------------114.3连杆大头盖的建模过程---------------------------------------------------------------145 动力计算------------------------------------------------------------------------------------175.1活塞位移、速度、加速度------------------------------------------------------------175.2活塞连杆作用力分析------------------------------------------------------------------18 5.3曲柄销载荷和连杆轴承载荷---------------------------------------------------------206 参考文献------------------------------------------------------------------------------------22附录1 汽油机设计参数1、功率Pe有效功率是汽油机基本性能指标。
连杆设计的详细计算
第四章典型零部件(连杆)的设计连杆是发动机最重要的零件之一,近代中小型高速柴油机,为使发动机结构紧凑,最合适的连杆长度应该是,在保证连杆及相关机件运动时不与其他机件相碰的情况下,选取小的连杆长度,而大缸径的中低速柴油机,为减少侧压力,可适当加长连杆。
连杆的结构并不复杂,且连杆大头、小头尺寸主要取决于曲轴及活塞组的设计。
在连杆的设计中,主要考虑的是连杆中心距以及大、小头的结构形式。
连杆的运动情况和受力状态都比较复杂。
在内燃机运转过程中,连杆小头中心与活塞一起作往复运动,承受活塞组产生的往复惯性力;大头中心与曲轴的连杆轴颈一起作往复运动,承受活塞连杆组往复惯性力和不包括连杆大头盖在内的连杆组旋转质量惯性力;杆身作复合平面运动,承受气体压力和往复惯性力所产生的拉伸.压缩交变应力,以及压缩载荷和本身摆动惯性力矩所产生的附加弯曲应力。
为了顺应内燃机高速化趋势,在发展连杆新材料、新工艺和新结构方面都必须既有利于提高刚度和疲劳强度,有能减轻质量,缩小尺寸。
对连杆的要求:1、结构简单,尺寸紧凑,可靠耐用;2、在保证具有足够强度和刚度的前提下,尽可能的减轻重量,以降低惯性力;3、尽量缩短长度,以降低发动机的总体尺寸和总重量;4、大小头轴承工作可靠,耐磨性好;5、连杆螺栓疲劳强度高,连接可靠。
但由于本设计是改型设计,故良好的继承性也是一个考虑的方面。
4.1连杆材料结合发动机工作特性,发动机连杆材料应当满足发动机正常工作所需要的要求。
应具有较高的疲劳强度和冲击韧性,一般选用中碳钢或中碳合金钢,如45、40Cr等,本设计中发动机为中小功率发动机,故选用一般的45钢材料基本可以满足使用要求。
4.2连杆主要尺寸 1、连杆长度l曲柄连杆比λ一般均大于0.3,这样可以使柴油机的机体高度降低,净质量减少,而且连杆长度减小后,其材料也相应减少,从而成本降低。
但是,过小的曲柄连杆比会引起活塞侧压力增加,从而导致柴油机摩擦损失的增加,加速活塞、活塞环、气缸套的磨损,影响可靠性。
- 1、下载文档前请自行甄别文档内容的完整性,平台不提供额外的编辑、内容补充、找答案等附加服务。
- 2、"仅部分预览"的文档,不可在线预览部分如存在完整性等问题,可反馈申请退款(可完整预览的文档不适用该条件!)。
- 3、如文档侵犯您的权益,请联系客服反馈,我们会尽快为您处理(人工客服工作时间:9:00-18:30)。
第四章典型零部件(连杆)的设计连杆是发动机最重要的零件之一,近代中小型高速柴油机,为使发动机结构紧凑,最合适的连杆长度应该是,在保证连杆及相关机件运动时不与其他机件相碰的情况下,选取小的连杆长度,而大缸径的中低速柴油机,为减少侧压力,可适当加长连杆。
连杆的结构并不复杂,且连杆大头、小头尺寸主要取决于曲轴及活塞组的设计。
在连杆的设计中,主要考虑的是连杆中心距以及大、小头的结构形式。
连杆的运动情况和受力状态都比较复杂。
在内燃机运转过程中,连杆小头中心与活塞一起作往复运动,承受活塞组产生的往复惯性力;大头中心与曲轴的连杆轴颈一起作往复运动,承受活塞连杆组往复惯性力和不包括连杆大头盖在内的连杆组旋转质量惯性力;杆身作复合平面运动,承受气体压力和往复惯性力所产生的拉伸.压缩交变应力,以及压缩载荷和本身摆动惯性力矩所产生的附加弯曲应力。
为了顺应内燃机高速化趋势,在发展连杆新材料、新工艺和新结构方面都必须既有利于提高刚度和疲劳强度,有能减轻质量,缩小尺寸。
对连杆的要求:1、结构简单,尺寸紧凑,可靠耐用;2、在保证具有足够强度和刚度的前提下,尽可能的减轻重量,以降低惯性力;3、尽量缩短长度,以降低发动机的总体尺寸和总重量;4、大小头轴承工作可靠,耐磨性好;5、连杆螺栓疲劳强度高,连接可靠。
但由于本设计是改型设计,故良好的继承性也是一个考虑的方面。
4.1连杆材料结合发动机工作特性,发动机连杆材料应当满足发动机正常工作所需要的要求。
应具有较高的疲劳强度和冲击韧性,一般选用中碳钢或中碳合金钢,如45、40Cr等,本设计中发动机为中小功率发动机,故选用一般的45钢材料基本可以满足使用要求。
4.2连杆主要尺寸 1、连杆长度l曲柄连杆比λ一般均大于0.3,这样可以使柴油机的机体高度降低,净质量减少,而且连杆长度减小后,其材料也相应减少,从而成本降低。
但是,过小的曲柄连杆比会引起活塞侧压力增加,从而导致柴油机摩擦损失的增加,加速活塞、活塞环、气缸套的磨损,影响可靠性。
《高速柴油机概念设计及实践》中指出:当曲柄连杆比31.0=λ左右时,对柴油机寿命及可靠性影响不大。
参照原机及总体布置,选择曲柄连杆比为:29.0260/65/,260≈===l r mm l λ。
2、连杆的结构尺寸小头主要尺寸为连杆衬套内径d 和小头宽度1b 。
《柴油机设计手册》中介绍的各个尺寸范围为:由 29.0260/65/≈==l r λ 查 《柴油机设计手册》36.0=Dd40=d 毫米 0625.0=dδ5.2=δ 毫米 小头内径4521=+=δd d 毫米36.112=d d 小头外径612=d 毫米 736.01=DD大头内径811=D 毫米 1.11=db 小头厚度 取 401=b 毫米 65.012=D b 大头厚度 取 532=b 毫米 113.1~2.1D l = 取981=l 毫米12.0=Dd M螺栓直径14=M d 毫米 327.0=D H 78.0=H B 17.0=Ht取36=H 毫米 28=B 毫米 6=t 毫米校核小头轴承的比压:bar db p q x 5336251074.493104010401011010052.80⨯=⨯⨯⨯⨯⨯⨯⨯==--π 《柴油机设计手册》中给出,q 许用值为630bar,可见是在安全范围之内的。
注:式中 24,D p P P zz z π=---最高燃气作用力;;;衬套支承长度衬套内径------b d3、连杆杆身连杆杆身采用典型的工字形截面。
尺寸如图4-1所示。
4、连杆大头定位方式连杆大头定位方式为舌槽定位。
这种定位方式定位可靠,贴面紧密,抗剪切能力强尺寸紧凑。
但要注意舌槽部位要减小应力集中,以防疲劳损坏。
5、连杆大头、小头的结构形式连杆大头的剖面形式:从上面选取的参数70.0~65.069.0>=Dd,所以采用斜切口。
图4-2 衬套承压面段面图图4-1连杆杆身断面示意图连杆盖的定位方式:斜切口连杆盖一般采用止口定位、锯齿定位。
在本设计中采用止口定位 连杆小头的结构形式:由于活塞销的大小一般由活塞设计所决定,所以在连杆的设计中,应尽可能加大连杆小头衬套的承压面积以降低比压,结构设计如图4-2所示。
4.3连杆螺栓连杆螺栓将连杆盖和连杆大头连在一起,它在工作中承受很大的冲击力,如果折断或松脱,将造成严重事故。
因此,连杆螺栓为M14采用标准细牙螺纹,都采用优质合金钢40Cr 制造,并精加工和热处理特制而成。
安装连杆盖拧紧连杆螺栓螺母时,要用扭力板手分2~3次交替均匀地拧紧到规定的扭矩,拧紧后为了防止连杆螺栓松动,还应可靠的锁紧。
连杆螺栓损坏后绝不能用其它螺栓来代替。
连杆螺栓必须用中碳合金钢制造,经调质以保证高强度。
4.4连杆轴瓦为了减小摩擦阻力和曲轴连杆轴颈的磨损,连杆大头孔内装有瓦片式滑动轴承,简称连杆轴瓦。
轴瓦分上、下两个半片。
连杆轴瓦上制有定位凸键,供安装时嵌入连杆大头和连杆盖的定位槽中,以防轴瓦前后移动或转动,有的轴瓦上还制有油孔,安装时应与连杆上相应的油孔对齐。
目前多采用薄壁钢背轴瓦,在其内表面浇铸有耐磨合金层。
耐磨合金层具有质软,容易保持油膜,磨合性好,摩擦阻力小,不易磨损等特点。
连杆轴瓦的背面有很高的光洁度。
半个轴瓦在自由状态下不是半圆形,当它们装入连杆大头孔内时,又有过盈,故能均匀地紧贴在大头孔壁上,具有很好的承受载荷和导热的能力,并可以提高工作可靠性和延长使用寿命。
轴瓦厚度和宽度根据《柴油机设计手册》上提供的范围分别别取2.5mm 和38mm 。
4.5连杆小头的强度计算 4.5.1连杆小头承受的作用力1. 连杆小头在进气和排气冲程中承受活塞组往复惯性力jn P 的拉伸,在上止点附近之值为最大。
jn P =)1(2λω+-r m =-2.05×0.065×162.12×(1+21065)=-4585.3 N式中: m 为活塞组件的质量,其数值为2.05千克。
r 为曲柄半径,其值为65 毫米。
ω为曲柄半径与连杆长之比值31.0==Lrλ 2. 连杆小头在膨胀行程开始点所承受的压缩力 3.705403.458510110410)1052.80(625=-⨯⨯⨯⨯-=+=-πjn F ck P P P N式中:F P 为最高燃气作用力 3. 由于温度过盈和压配衬套而产生的力 (1) 温度过盈量小头衬套有青铜,也可用粉末冶金代之。
现以青铜衬套进行计算。
()()0492.015041101108.155=⨯⨯⨯-⨯=-=∆--dt T B αα 毫米式中: B α为青铜衬套材料的热膨胀系数B α=1.8×105-α为钢的小头材料热膨胀系数 5101-⨯=α t 为连杆小头的温升 推荐 C t ︒=200~100 取 C t ︒=150 d 为小头衬套的外径 d=41 毫米(2)衬套与小头配合面上由总过盈量所决定的单位压力PaB TMP E d d d d E d D d D d p 5.191017.13.05.38415.38411024.23.041604160410492.0068.05222252222212212222222=⎥⎥⎥⎥⎦⎤⎢⎢⎢⎢⎣⎡⨯-+++⨯+-+⨯+=⎥⎥⎥⎥⎥⎦⎤⎢⎢⎢⎢⎢⎣⎡--+++-+∆+∆=μμ 式中: D 2 小头外径 D 2=60 毫米D 小头内径 d=41 毫米 1d 衬套内径 1d =38.5 毫米 μ 泊桑系数 3.0=μE 连杆材料的抗拉弹性模数 E =2.24×105MP aB E 青铜衬套的抗拉弹性模数 B E =1.17×105MP a∆ 衬套装配过盈为 068.0~016.0毫米,可取 068.0=∆毫米。
4.5.2由于装配过盈与温度过盈所产生的应力 1、外表面的应力15.3441604125.1922222222=-⨯⨯=-=dD d p a σ MP a 2、内表面的应力65.53416041605.192222222222=-+⨯=-+=dD d D p i σ MP a 许用值[]a σ和[]i σ在150~100 MP a 故属安全。
4.5.3由活塞的惯性力在连杆小头中引起的拉应力 1、当活塞在上止点时27.24025.2523.458522=⨯⨯===Ar P FP cp jn jn p σ MP a式中:小头平均半径25.254416042=+=+=d D r cp 毫米 小头宽度 A=40 毫米[]58~29=p σ MP a 故安全 2、按小曲率曲杆公式计算弯矩和法向力 计算可作下述假定:① 曲杆固定于小头和杆身的衔接处。
即在连杆小头外圆和过度圆半径R 相切的位置; ② 连杆小头下部支承在刚性很大的杆身上,因而不变形;③ 小头沿连杆的纵向对称线切开,用弯矩0M 和反向力N 代替的小头右半部的作用。
小头Ⅲ—Ⅲ剖面弯矩M 和法向力N (图4-3)。
mN r P r N M M cp jn cp ⋅=⨯-⨯⨯⨯-⨯-⨯⨯+=---+=-︒︒-︒359.410)119cos 119(sin 25.253.45855.010)119cos 1(25.253.2186108.1)cos (sin 5.0)cos 1(3300φφφ式中: 0N 、0M 为当︒=0φ断面上的轴力和弯矩。
0N 和0M 值有下列经验公式求得:3.2186)1190008.0572.0(3.4585)0008.0572.0(0=⨯-⨯=-= φjn P N NmN r P M cp jn ⋅=⨯-⨯⨯⨯=-=-︒108.110)0297.011900033.0(25.253.4585)0297.000033.0(30φ式中:︒-︒-︒=+++=+++=11975307517cos 9022cos 90121R D RHφ25.25=cp r 毫米 41=d 毫米 602=D 毫米图4-3 连杆小头剖面图NP N N jn 6.2057)119cos 119(sin 3.45855.0119cos 3.2186)cos (sin 5.0cos 0=-⨯⨯+⨯=-+=︒︒︒φφφ(3)外侧纤维应力acp cp aj MP AhKN h r h h r M55.11105.9401]6.2057936.0)5.925.252(5.95.925.25610359.42[1])2(62[63=⨯⨯⨯⨯++⨯+⨯⨯⨯⨯=+++=σ 式中: h 为小头计算壁厚 5.92416022=-=-=d D h 毫米 系数936.0405.21017.140)4060(1024.240)4160(1024.255522=⨯⨯⨯+⨯-⨯⨯⨯-⨯⨯=⋅+⋅⋅=B B F E F E F E K (4)内侧纤维应力acp cp ij MP AhKN h r h h r M296.3105.9401]6.2057936.0)5.925.252(5.95.925.25610359.42[1])2(62[63-=⨯⨯⨯⨯+-⨯-⨯⨯⨯⨯-=+---=σ4.5.4由压缩力引起的应力计算假定载荷在连杆小头下部成正弦分布 1、Ⅲ-Ⅲ剖面上的弯矩和法向力)cos sin 2sin ()cos 1(00ππφφφφΦ----+=cp ck cp r P r N M M 式中0M 和0N 由曲线查得0012.00-=cpck r P M m N M ⋅-=⨯⨯⨯-=-14.21025.253.705400012.0300035.00=ckP N 9.2463.705400035.00=⨯=N N 弯矩)cos sin 2sin ()cos 1(00πφπφφφφ----+=cp ck cp r P r N M MmN ⋅-=-+-=--⨯⨯-⨯-⨯+-=︒︒︒--︒59.1971.2626.914.2)119cos 119sin 07.22119sin (1025.253.7054010)119cos 1(25.259.24614.233ππ法向力NN P N cK 1.1058)119cos 119sin 07.22119sin (3.70540cos )cos sin 2sin (0=--⨯=+--=︒︒︒ππφπφπφφφ 2、外侧纤维应力acp cp ac MP AhKN h r h h r M52.26105.9401]1.1058936.0)5.925.252(5.95.925.2561059.192[1])2(62[63-=⨯⨯⨯⨯++⨯+⨯⨯⨯⨯-=+++-=σ3、内侧纤维应力AhKN h r h h r Mcp cp ic 1])2(62[+--=σ aMP 195.40105.9401]1.1058936.0)5.925.252(5.95.925.2561059.192[63=⨯⨯⨯⨯+-⨯-⨯⨯⨯⨯=4.5.5连杆小头的安全系数)2(212a ac aj acaj n σσσψσσσσσ+++-=-连杆小头应力按不对称循环变化,在小头和杆身衔接处(即固定角R 处)的外侧纤维上安全系数最小。