磁悬浮主轴设计
混合式永磁型完全磁悬浮电主轴实施步骤与参数设计

• 202•1 混合式永磁型完全磁悬浮电主轴结构及参数设计(1)围绕低能耗、低成本、集成化高速精密电主轴性能要求,分析混合式永磁型完全磁悬浮电主轴的基本结构和运行机理,设计径向承载力400N 与轴向承载力251N 的混合式永磁型完全磁悬浮的电主轴的机械结构和磁路结构,基本机械参数和电磁参数。
(2)采用基于转子旋转的参数设计理念,通过分析转子旋转所引起的磁力线分布发生旋转偏移、定子与转子之间的气隙磁通密度发生畸变及悬浮力减小等因素,在避免磁路饱和及满足性能设计要求的基础上,修改依靠静态工作点设计的参数,使参数设计更加精确且接近转子实际运行情况。
(3)根据混合式永磁型完全磁悬浮电主轴的各种热源及其发热量,建立基于热-结构耦合的有限元分析模型。
(4)采用有限元ANSYS 软件,分析混合式永磁型完全磁悬浮电主轴转子静态悬浮和转动情况下电磁场的非线性、漏磁、磁耦合、边缘效应和涡流等因素,分析磁场的分布规律和变化规律。
(5)采用Matlab 软件及有限元ANSYS 分析软件,对混合式永磁型完全磁悬浮电主轴电流-力-位移关系的空间分布规律和悬浮转子的模态进行分析,结合混合式永磁型完全磁悬浮电主轴电磁场、温度场及其热变形分析结果,基于虚拟样机技术,进一步对混合式永磁型完全磁悬浮电主轴进行多参数协同仿真和优化设计。
2 混合式永磁型完全磁悬浮电主轴系统数学模型和自抗扰非线性解耦控制研究(1)混合式永磁型完全磁悬浮电主轴的径向偏置磁通按矩形规律变化,基于其结构特点和悬浮力产生机理,考虑转子偏心,基于磁路分析,然后采用积分法建立混合式永磁型完全磁悬浮电主轴悬浮力完整的数学模型。
(2)基于上述建立的基本模型,分析悬浮力特性,采用样机动、静态试验和NSYS 有限元分析,研究基本模型随磁饱和、转子偏心位移、电流、转速及温升的变化关系,获取修正模型的约束条件和数据样本。
(3)根据机理建模、实验数据和仿真分析,建立样本数据库,采用多项式拟合的方法,获取相关工作状态下精确的悬浮力数学模型。
水银磁悬浮轴承的结构设计与性能优化

水银磁悬浮轴承的结构设计与性能优化导言磁悬浮技术作为一项高精密度、低摩擦力的新型技术,被广泛应用于飞行器、高速列车等领域。
水银磁悬浮轴承作为磁悬浮技术的一种重要应用,具有较高的性能和稳定性。
因此,本文将着重探讨水银磁悬浮轴承的结构设计与性能优化。
一、水银磁悬浮轴承的工作原理水银磁悬浮轴承是利用水银的液体磁流变性质来实现轴承的稳定悬浮。
水银磁悬浮轴承由轴向磁力平衡系统和径向磁力稳定系统组成。
轴向磁力平衡系统由感应线圈、压力传感器和控制器组成。
当转子受到轴向力作用时,感应线圈将产生感应电流,通过控制器的反馈系统,调节活动磁铁的位置,使得轴向力得到平衡。
径向磁力稳定系统由外磁场线圈、磁导体和液态水银组成。
外磁场线圈产生磁场,磁导体中的液态水银受到磁流变力的作用,形成稳定的磁悬浮力,使得转子在径向方向悬浮。
二、水银磁悬浮轴承的结构设计1. 磁悬浮组件设计磁悬浮组件是水银磁悬浮轴承的核心部分,主要包括外磁场线圈、磁导体和液态水银。
外磁场线圈的设计应考虑磁场的分布均匀性,磁导体的设计应具有高导磁性和高热传导性能,以提高磁悬浮力稳定性。
液态水银的选择需要考虑其电导率和磁流变性能,以满足稳定悬浮的要求。
2. 轴向磁力平衡系统设计轴向磁力平衡系统的设计需要考虑力的平衡性和响应速度。
感应线圈应布置在合适的位置,以使得感应电流与轴向力成正比。
压力传感器的选择需要具有高准确度和快速响应的特性。
控制器的设计需要考虑信号处理和反馈控制算法,以实现轴向力的平衡。
3. 综合结构设计综合结构设计包括回转体、固定体、轴承载荷和密封结构等。
回转体应具有良好的几何形状和轴线的精度,以确保转子在旋转过程中的平衡性。
固定体的设计需要考虑其刚度和稳定性,以提供足够的支撑力。
轴承载荷的设计需要考虑转子的负载和运行速度,以确保轴承的耐用性和可靠性。
密封结构的设计需要防止水银泄漏,保护环境和人身安全。
三、水银磁悬浮轴承的性能优化1. 悬浮力稳定性的优化水银磁悬浮轴承的悬浮力稳定性是其性能的重要指标之一。
主轴磁悬浮轴承的设计
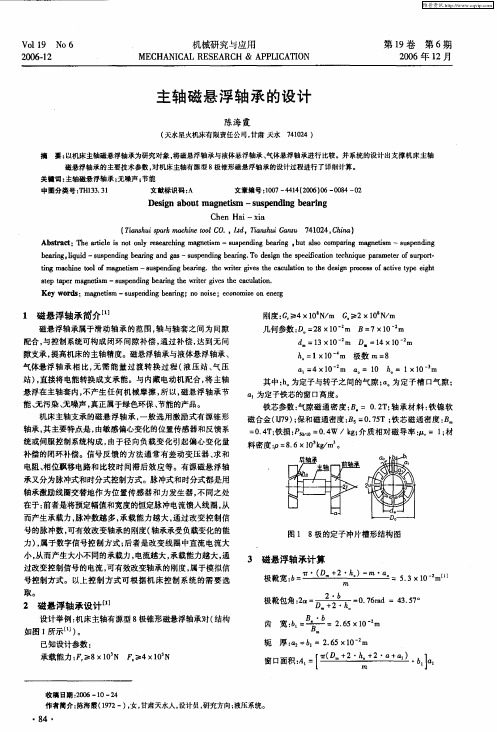
baig l ld— upn i er gadgs up nigbBigT ei es c ct nt h iu aa e r f upr er - qi sse d gba n n a —ss dn er . ods nt i ao c n ep m t rot n jl n i e n g h p f i e q r e i eos -
陈海 霞
( 天水星火机床有 限责任公 司, 甘肃 天水 7 12 4 04)
摘
要: 以机床 主轴磁 悬浮轴 承为研究对象 , 将磁悬浮轴 承与液体悬浮轴承、 气体悬浮轴承进行 比较。并 系统 的设 计出支撑机床主 轴
磁悬浮轴 承的主要技术参数 , 对机床主轴有 源型 8 极锥形磁悬浮轴 承的设计过程进行 了详细计算。
配合, 与控制系统可构成闭环间隙补偿 , 通过补偿 , 达到无间 隙支承, 提高机床的主轴精度。磁悬浮轴承与液体悬浮轴承、 气体悬浮轴承相 比, 无需能量过渡转换过程 ( 液压站、 气压 站)直接将电能转换成支承能。与内藏电动机配合, 主轴 , 将
悬浮在主轴套 内 , 不产生 任何 机械摩擦 , 以, 所 磁悬 浮轴承 节 能、 无污 染 、 无噪声 , 真正属于绿色环保 、 节能的产 品。
=
机床 主轴支 承的磁 悬 浮轴承 , 一般 选用 激励式有 源锥 形
轴承 。 主要特点是 , 其 由敏感 偏心变化 的位置传感器 和反 馈系
04 铁损 : l 04 /k ; 质相对 磁导率 : 1 材 .T; o .W g介 /= ; x
统或伺服控制系统构成 , 由于径向负载变化引起偏心变化量 补偿的闭环补偿。信号反馈的方法通常有差动变压器 、 求和 电阻、 相位飘移电路和比较时间滞后效应等。有源磁悬浮轴 承又分为脉冲式和时分式控制方式。脉冲式和时分式都是用 轴承激励线圈交替地作为位置传感器和力发生器, 不同之处 在于: 前者是将预定幅值和宽度的恒定脉冲电流馈入线圈, 从 而产生承载力, 脉冲数越多, 承载能力越大, 通过改变控制信 号的脉冲数, 可有效改变轴承的刚度( 轴承承受负载变化的能
主轴系统混合磁悬浮轴承的设计

s1
312 计算气隙面积
根据混合磁悬轴承的最大承载力公式 ( 5) 得 2F m ax Λ0 ( 10) S = 2
B
s
当最大负载为已知时, 即可由上式设计气隙磁极 的有效面积。 313 气隙 g 0 的选取 当 x = 0 时, 由式 ( 7) 及 ( 8) 得 2B 0 g 0 ( 11) N Im = Λ0 由上式可看出, 当气隙 g 0 增大时, 电磁铁需要的 安匝数 N Im 就大, 这就需要较大的绕线空间, 其优点 是加工精度相对要求不高; 如果减小气隙 g 0 , 虽然安 匝数 N I m 减小, 但要求更高的加工精度。在工程上, 一 般取 g 0 = 0. 15 ~ 1. 0mm , 转子的直径小时 g 0 取小值。 314 电磁铁参数 由于永久磁铁产生偏置磁场, 电磁铁产生控制磁 场, 取消了轴承中的偏置绕组, 这不仅减小了磁轴承的 体积, 更重要的是只存在控制电磁铁磁场的功耗, 使轴 承的功耗大大降低。 由式 ( 7) 得控制电磁铁所需的安匝数为
吸力又变为 F 1 ≥F 2 , 使得转子重新返回原来的平衡位 置。 如果转子受到一个向左的扰动并向左运动, 则可得 出相反的结论。 因此, 不论转子受到向左或向右的扰 动, 图中的转子始终能处于稳定的平衡状态。
2 混合磁悬浮轴承的承载能力
在只考虑均匀气隙磁通, 不考虑铁芯磁阻、 漏磁及 涡流损耗等情况下, 设转子受到向右的扰动, 则根据前 述混合磁悬浮轴承的工作原理, 转子左右磁极气隙处 的磁感应强度为
N Im = B
= =
(g 0 + x )
F m Λ0
+
N I m Λ0 = B 2g 0
s
s2
F m Λ0 N I m Λ0 = 0 (g 0 - x ) 2g 0
磁悬浮轴承的控制与优化设计

磁悬浮轴承的控制与优化设计磁悬浮轴承作为现代机械工程领域的一项重要技术,具有许多独特的优势。
其悬浮部分完全无接触,没有摩擦产生的热损失,减小了能耗和维护成本。
此外,磁悬浮轴承还能实现快速、精确的轴向位置控制和旋转速度控制,为高速机械系统提供了更好的运动精度和可靠性。
本文将探讨磁悬浮轴承的控制与优化设计。
磁悬浮轴承的控制主要包括控制方法和控制系统的设计。
常用的磁悬浮轴承控制方法有自由控制和主动控制两种。
自由控制是指利用磁悬浮轴承自身的特性来实现稳定悬浮的控制方式。
主动控制则需要利用传感器和反馈控制系统来实现对悬浮部分的控制。
在实际应用中,主动控制更为常见,因为它可以提供更高的控制精度和灵活性。
控制系统的设计是磁悬浮轴承控制的关键。
一般来说,控制系统包括传感器、控制器和电磁部分。
传感器用于测量被控对象的状态,例如轴的位置、速度和振动等。
控制器根据传感器的反馈信息计算出控制信号,用来调节电磁部分的工作状态。
电磁部分则产生磁力,实现对轴的悬浮和运动的控制。
磁悬浮轴承的优化设计可以从多个方面入手。
首先,需要考虑磁悬浮轴承的结构设计。
轴承的结构应该符合被悬浮物体的运动需求,同时减小系统的质量和能耗。
其次,还可以优化控制算法。
随着控制算法的不断改进,磁悬浮轴承的控制性能得以提升。
例如,采用模糊控制、神经网络控制和自适应控制等先进算法,可以实现更高精度的控制。
此外,还可以考虑优化磁悬浮轴承的能量转换效率,以提高系统的整体效能。
针对磁悬浮轴承的控制和优化设计问题,研究者们进行了大量的工作。
例如,一些研究人员提出了基于自适应滑模控制器的磁悬浮轴承控制方法,通过在线调节控制器的参数,实现了对不同工况下的控制性能的优化。
还有一些研究者提出了基于遗传算法的优化设计方法,通过对磁悬浮轴承结构参数进行优化,提高了系统的性能指标。
这些研究工作为磁悬浮轴承的控制和优化设计提供了有益的参考。
总之,磁悬浮轴承的控制与优化设计是实现高速、精密运动的关键环节。
五自由度磁悬浮电主轴的结构设计与仿真

p r f v r e o d ge g ei e rn see ti s i de w r t d c d,whc r h e r e o d g e e — a t o e f d m e r e ma n t b a g l cr p n l e e i r u e s f i e c i c n o ih we et r efe d m e ep r r ma e tma n tb a x d ma n t e r g n w r e o d g e g e i b a i g s n h o o smo o .F r t n n g e is mie g e i b a i sa d t o fe d m e r e ma n t e r sa y c rn u tr i l c n c n s y, t e p oo y e o v re o d g e g ei e r g lcrc s i d ewa e in d,a d t e ema n t o c n h r tt p ff efe d m e r e ma n t b a n see t p n l sd sg e i c i i n h n t g ei f r ea d h c l vtt n fr e b lcr ma n t n lss s f a e As f Ma welw sa ay e e i i o c y ee t ao o g ei a ay i o t r o t c w / x l a n l z d,t u e i i gt e sr c u e a d p — h sv r yn h t t r n a f u r mee ain lt f h r tt p .F n l ,t e smu ai n mo e fc n rls se i t b S mu i k w sc n t c a trrt ai o e p oo y e i al o y t y h i l t d lo o t y t m Mal / i l a o s o o n a n u r — t d a d s me r lt d smu ai n w s d d,w ih l y o n a in f r e tb ih n h o to y t m ft e ma n t e n o ea e i lt a i o h c a s fu d t o sa l i g te c n rl s se o h g ei o s c
磁悬浮轴承的设计和控制

磁悬浮轴承的设计和控制随着科技的不断进步,磁悬浮轴承作为一种新型的轴承技术,逐渐引起了人们的关注。
它的出现不仅提升了机械设备的性能,还改变了传统轴承的运行方式。
本文将探讨磁悬浮轴承的设计原理和控制方法,以及与传统轴承相比的优势。
1. 磁悬浮轴承的设计原理磁悬浮轴承是通过电磁原理实现对轴的支承和稳定。
它由电磁悬浮部分和控制部分组成。
电磁悬浮部分包括固定部分和旋转部分,固定部分由电磁铁和轴承复合体组成,旋转部分则是装载在轴上的磁体。
通过控制电磁悬浮部分的电流,可以调节磁悬浮轴承与轴之间的力的大小和方向。
磁悬浮轴承的设计原理主要包括磁力支撑、磁力定位和磁力恢复三个方面。
磁力支撑是指通过向轴施加一个与重力相等且方向相反的力,使得轴悬浮在空中。
磁力定位则是通过调节支撑力的大小和方向,实现轴在水平方向上的位置控制。
磁力恢复是指通过控制轴与磁体之间的力,使得轴能够在受到外力作用后迅速恢复到平衡位置。
2. 磁悬浮轴承的控制方法磁悬浮轴承的控制方法主要分为闭环控制和开环控制两种。
闭环控制是通过给定轴的位置和速度信号,利用传感器和控制算法计算出合适的电流信号,控制电磁悬浮部分的电流大小和方向,从而实现轴的稳定运行。
开环控制则是通过预先设置电流信号,将其直接送至电磁悬浮部分,忽略轴的位置和速度变化,从而实现对轴的基本控制。
闭环控制是磁悬浮轴承常用的控制方法。
其主要包括位置控制和速度控制两个环节。
位置控制是通过传感器感知轴的位置,并与给定的位置信号进行比较,得出控制误差,然后根据控制算法计算出相应的电流信号。
速度控制是在位置控制的基础上,增加了速度传感器,通过对速度信号进行反馈和控制,实现对轴的更精确控制。
3. 磁悬浮轴承与传统轴承的比较与传统轴承相比,磁悬浮轴承具有许多优势。
首先,磁悬浮轴承没有机械接触,消除了传统轴承由于摩擦和磨损产生的问题,大幅提高了轴承的使用寿命。
其次,磁悬浮轴承具有低摩擦系数和高转速特性,减小了能量损耗和轴向受力,提高了机械设备的效率。
磁悬浮轴承设计方法

磁悬浮轴承设计方法磁悬浮轴承是一种新型的轴承技术,它采用磁力场来支撑转子,避免了传统机械轴承的摩擦和磨损,具有高速、高精度、低噪音、长寿命等优点,被广泛应用于高速列车、风力发电机、航空航天等领域。
本文将介绍磁悬浮轴承的设计方法。
磁悬浮轴承的设计方法主要包括磁路设计、控制系统设计和机械结构设计三个方面。
首先是磁路设计。
磁路是磁悬浮轴承的核心部分,它决定了轴承的性能和稳定性。
磁路设计的关键是确定磁铁的形状、尺寸和磁场分布。
一般来说,磁铁的形状可以是圆形、方形、长方形等,尺寸则根据转子的大小和重量来确定。
磁场分布是指磁铁产生的磁场在空间中的分布情况,它决定了轴承的支撑力和稳定性。
磁场分布可以通过有限元分析软件进行模拟计算,以得到最优的设计方案。
其次是控制系统设计。
磁悬浮轴承的控制系统是保证轴承稳定运行的关键。
控制系统的设计包括传感器选择、控制算法设计和控制器选型等方面。
传感器可以选择位移传感器、速度传感器、加速度传感器等,以实时监测转子的运动状态。
控制算法设计是指根据传感器反馈的信号,通过控制器对磁场进行调节,以保持转子的稳定运行。
常用的控制算法有PID控制、模糊控制、神经网络控制等。
控制器的选型则需要考虑控制精度、响应速度、抗干扰能力等因素。
最后是机械结构设计。
机械结构是磁悬浮轴承的支撑结构,它需要满足轴承的载荷要求和稳定性要求。
机械结构设计的关键是确定支撑结构的形状、尺寸和材料。
一般来说,支撑结构的形状可以是圆形、方形、长方形等,尺寸则根据转子的大小和重量来确定。
材料的选择需要考虑强度、刚度、耐磨性等因素。
磁悬浮轴承的设计方法是一个综合性的工程问题,需要涉及磁路设计、控制系统设计和机械结构设计三个方面。
在实际应用中,还需要考虑轴承的安装、调试和维护等问题。
磁悬浮轴承的设计方法的不断改进和完善,将进一步推动其在各个领域的应用和发展。
- 1、下载文档前请自行甄别文档内容的完整性,平台不提供额外的编辑、内容补充、找答案等附加服务。
- 2、"仅部分预览"的文档,不可在线预览部分如存在完整性等问题,可反馈申请退款(可完整预览的文档不适用该条件!)。
- 3、如文档侵犯您的权益,请联系客服反馈,我们会尽快为您处理(人工客服工作时间:9:00-18:30)。
1前言1.1 高速切削简介高速切削的概念被提出后,经过了长期探索研究与发展后,才在近十几年被广泛应用在机械加工过程中。
高速切削作为一种新兴的先进机械加工技术,与传统的机械加工技术相比,其具有一系列的优点。
它集高效率、高加工精度、低功耗等于一体。
高速切削解决了常规切削加工中一些长期存在而无法解决的问题,例如由于机械加工过程中,刀具的切削量很小,产生的切削热比较少并且绝大部分切削热被切屑及时带走,从而提高了刀具的切削寿命;随着切削速度的提高,在单位时间内被加工材料的去除率有了很大的提高,进而减少了切削时间,提高了工件的加工效率;高速切削的进给量小,因而切削力也就相对要小,而且形成的切屑能够在很短的时间内被排出,切削过程所产生的热量在还没有传导至刀具时,就被切屑带走了,这样就降低了刀具及工件上的切削热;由于高速切削可以达到很高的加工精度,所以在某些场合可以实现以车代铣、以铣代磨等工序。
这些优点极大地缩短了产品的制造周期,这在竞争日益激烈的当代是很有发展前途的。
1.2 磁悬浮轴承简介磁悬浮轴承也被人们称为磁力轴承,它是一种靠磁场力来承受载荷或将转子悬浮起来的一种新型的支承形式,根据不同的工作原理可将磁悬浮轴承系统分为三大类:主动磁悬浮轴承、被动磁悬浮轴承和混合式磁悬浮轴承。
主动磁悬浮轴承是利用可控电磁力来悬浮主轴转子的,它有主动电子控制系统;被动磁悬浮轴承是利用磁场本身的特性使主轴转子悬浮,它没有主动电子控制系统,其应用最多的是永磁轴承;混合式磁悬浮轴承是由主动磁悬浮轴承和被动磁悬浮轴承以及其他一些必要的辅助支撑共同组合而成的,它既有主动磁轴承的优点也有被动磁轴承的优点。
为了便于设计制造,本设计中采用主动磁悬浮轴承磁悬浮轴承具有一系列的优点:定子与转子之间无接触,因而无摩擦,且功耗低,可以使主轴实现高速旋转;无需润滑和密封,因而可以简化系统结构的设计;支撑精度比一般的接触式轴承还高,工作稳定可靠。
但是,其支撑刚度比接触式轴承要低,而且结构复杂,需要专门的控制系统,主轴上还要设计增加位移传感器,成本较高。
虽然磁悬浮轴承由多个磁极构成,但是为便于研究【2】,我们仍然可以将其简化为下图所示结构。
图1.1磁悬浮轴承简化模型根据麦克斯韦电磁力公式,我们可以得到磁悬浮定子与其转子之间的电磁吸引力为F=B02*A0/μ0…………………………………(1.1)式中B0——气隙中的磁感应强度(单位T)A0——定子与转子铁心间气隙的横截面积(单位m2)μ0——空气磁导率(单位H/m,μ0=4 *10-7H/m)由安培环路定理我们可以推出B0=N*i*μ0/(2*x0) ……………..………….. (1.2)式中N——磁悬浮线圈绕组的匝数i——磁悬浮线圈中通过的电流(单位A)x0——磁悬浮轴承定子与其转子铁心间气隙的长度(单位m)将式(2)代入式(1)可得F=μ0N2Ai2/(4 x02)……………..…….….….(1.3)令k=μ0N2A/4………………….……..………..(1.4)则(3)式可写为F= k*i2/x02…………………....….………….(1.5)由式(4)可知,k值完全取决于磁悬浮轴承的结构参数,因此当磁悬浮轴承的结构一定时,k即为常数。
由式(5)可知磁悬浮轴承的定子与转子间的电磁吸力的大小除与其本身结构参数有关外,还与线圈中电流的平方成正比,与气隙值的平方成反比。
1.3 选题目的与意义随着科学技术的进步与发展,高速切削在航空航天,汽车模具等需要高精度的机加工领域得以迅速的发展[3],因为高速切削可以实现工件加工的高精度以及加工过程的干切削,因此它在某种程度上改变了材料加工的现状,极大的提高了材料加工的效率,在许多情况下,其加工精度可以实现以铣代磨、以车代铣[4]。
然而,机床高速切削的实现,不仅需要有高速进给系统和高速切削刀具系统作为支撑,机床主轴的高速化也是一个不可或缺的重要条件。
为了比较容易的获得主轴高速,我们可以用采用了磁悬浮轴承的高速电主轴来实现主轴高速化。
高速切削在工业加工领域的应用,可以提高生产效率,降低生产成本,节约能源,对国民经济起到极大的促进作用。
磁悬浮轴承具有一系列的优点,例如,它无机械接触,因而无磨损且不需润滑,并且轴承功耗低。
但是,我国磁悬浮技术在这方面的应用较少,并且随着十二五规划的实施,高效节能环保的新型工业生产方式,将会有更大的应用与发展的空间。
1.4 主要设计内容及技术要求1.4.1 电磁轴承结构研究电磁悬浮轴承[5]主要由机械部分,气隙检测部分和电磁力控制部分构成。
其机械部分主要由外套筒和转轴两部分组成,外套筒安装在基座上,电磁铁安装在外套筒内部,转轴部分则主要由硅钢片和软铁等铁磁材料制成。
在外套筒内部安装若干个位置传感器,当主轴受到外力作用而偏离中心平衡位置时,位置传感器将主轴的位移量转换成电量,送至控制器,经过数据处理之后,由控制器发出控制信号经由功率放大器放大后驱动电磁线圈改变磁场强度,进而改变电磁力的大小,使主轴返回原来的平衡位置。
1.4.2 电磁轴承控制器设计(承载能力和稳定性)首先要明确磁悬浮轴承需要承受的总的作用力,以保证磁悬浮轴承能够使主轴可靠地悬浮。
然后根据电磁学的基本原理及设计要求,计算出磁悬浮轴承系统中主要的电磁参数,如电磁悬浮线圈匝数、磁极面积、线圈电感等。
再根据需要测量的位移方向来确定位移传感器需要使用的数量及位置分布,同时还要设计一个位移信号处理电路,即控制器,通过它对获得的位移电量进行运算处理,控制器输出的控制信号传送至功率放大驱动电路,由功率放大驱动电路来驱动磁悬浮轴承的悬浮线圈改变磁场强弱,从而使偏离悬浮中心的主轴返回中心位置。
同时为了保证控制的精确性,我们可以在控制电路中增加反馈电路,将功率放大驱动电路的输出信号反馈给控制器,由控制器对反馈信号进行处理,从而调整其对悬浮线圈的控制电流以保证控制精度。
1.4.3掉电保护功能(增加辅助轴承)当系统掉电时,磁悬浮线圈由于失去控制电流而使电磁铁失去磁性,导致磁悬浮主轴由高速悬浮运转变成突然与磁悬浮轴承定子接触的运转,这样就会造成磁悬浮轴承的转子与定子的工作面的接触和摩擦,又由于磁悬浮轴承系统没有润滑装置,就会使得磁悬浮轴承的转子与定子工作面产生磨损甚至烧结。
为了避免此种情况的发生,我们在设计过程中必须在磁悬浮主轴上增加辅助保护轴承。
作为辅助保护轴承,必须要满足能够在高速情况下运转,同时,为了保证加工精度,避免因磁悬浮主轴受热向前伸长,还要在系统中增加轴向固定轴承,为了使其能够满足高速运动,我们可以考虑使用轴向磁悬浮轴承。
1.4.4 电磁轴承临界转速分析临界转速是指当主轴旋转时,会使主轴出现挠度急剧增大、转动失稳现象的旋转速度。
主轴工作转速应远离各阶临界转速,否则主轴将有可能处于共振区而产生剧烈振动,进而对磁悬浮主轴系统的稳定性造成影响。
同时磁悬浮主轴在启停过程中总会经过其一阶临界转速,这仍会使主轴产生振动,因此增加辅助支撑也是有必要的。
1.4.5满足电磁轴承装配要求由于磁悬浮主轴转速很高,所以当磁悬浮轴承装配精度达不到要求时,磁悬浮主轴在高速状态下就会出现振动,因此不仅要保证磁悬浮轴承的装配要求,还要保证磁悬浮主轴的同轴度要求,在主轴零部件装配完成后,还要进行动平衡试验。
为了保证磁悬浮主轴在高速运转时的回转精度和刚度,一些关键零部件必须进行精密加工或超精密加工,其尺寸误差一般要控制在微米级或更小,对同轴度、垂直度和表面粗糙度也都有极严格的要求。
1.4.6机械结构设计参考普通机床主轴设计,磁悬浮主轴采用阶梯轴的结构形式,本设计中采用主轴中空结构,这种结构可以保证主轴在承受相同转矩的条件下,有效地减轻主轴的重量,同时可以为安装刀具拉紧装置等预留出安装空间。
位于磁悬浮轴承处的转子上通常装有由薄层硅钢片叠装而成的套筒,这样可以保证更好的导磁性,已尽最大可能地减小涡流,并使用锁紧螺母固定。
1.5设计要求给定的设计数据为:套筒直径:210mm;最高转速:20000r/min;输出功率:2.5kw;基速:20000r/min;基本转矩:5Nm;润滑:油脂润滑;刀具接口:HSK系列。
2结构设计前基本参数的确定2.1 电机参数的确定由于本设计中电机转子安装在磁悬浮主轴上,且电机定子需要安装在外套筒内部,所以在本设计中选用无外壳内置式电机,为了满足设计要求,即电机的额定功率、额定转矩、最高转速等要大于或等于磁悬浮主轴设计要求的输出功率输、出转矩和最高转速,根据这些条件选定的电机型号为1MB140B,其具体参数见下表:表2.1 1MB140B型内置电机参数2.2 气隙值的确定考虑到对磁悬浮轴承承载能力方面的要求,设计时应尽最大可能减小磁悬浮轴承的定子与其转子之间的气隙值x0,由于在同样的载荷条件下,气隙值x0越小,则磁悬浮轴承的尺寸也就相应的小,或者说在磁悬浮轴承尺寸一定的情况下,气隙值x0越小,其承载能力也就越大,然而,由于加工技术及加工成本,控制系统的性能等方面因素的限制,气隙值x0不能无限制地缩小,一般情况下,设计气隙值x0时应考虑转子的直径,一般当d<100mm时x0=0.3——0.6mm当100mm<d<1000mm时x0=0.6——1.0mm在本设计中,由于对磁悬浮主轴控制系统要求不高,并且由所选电机可知,转子直径小于100mm,所以径向磁悬浮轴承设计的气隙值x0取0.5mm,轴向磁悬浮轴承设计的气隙值x0也取0.5mm。
2.3 磁感应强度B的确定本设计中径向磁悬浮轴承的定子为硅钢片叠压而成,所选用的硅钢片的饱和磁感应强度B s查表可得B s=1.95T,为了保证出现最大电流时,不会使磁感应强度达到硅钢片的饱和磁感应强度,取最大磁感应强度B m=1.4T。
本设计中轴向磁悬浮轴承的定子为软铁材料,查表可得软铁材料的饱和磁感应强度B s=1.5T,同样为了保证出现最大电流时,不会使磁感应强度达到软铁的饱和磁感应强度,取最大磁感应强度B m=1.4T。
2.4 径向磁悬浮轴承定子磁极对数的确定磁悬浮主轴转子在径向X方向和Y方向存在位移[6],即转子其径向平面内能够产生四个方向的位移:X+,X-,Y+,Y-,所以定子在这四个方向都应装有电磁铁,又由于磁力线应形成闭合回路,所以定子的每个方向上至少应有一对磁极,为了设计简单以及经济实用,本设计中定子的磁极数取p=8,同时为了便于制造,每个磁极均采用矩形结构,径向磁悬浮轴承定子结构简图如下图所示:图2.1 径向磁悬浮轴承定子结构简图3磁悬浮主轴机械部分设计3.1磁悬浮转子设计由于设计要求主轴转速为20000r/min,而传统的切削刀具的刀柄接口在主轴转速超过10000r/min时就已经不能满足刀具可靠的连接要求,因此根据设计要求,本设计中选用高速性能优良、连接可靠的HSK-E25系列刀具接口。