1、石灰石的预处理和煅烧
水泥的生产工艺流程
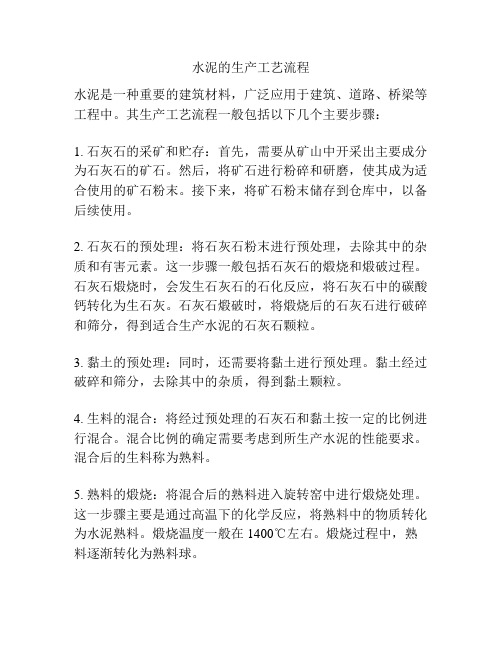
水泥的生产工艺流程水泥是一种重要的建筑材料,广泛应用于建筑、道路、桥梁等工程中。
其生产工艺流程一般包括以下几个主要步骤:1. 石灰石的采矿和贮存:首先,需要从矿山中开采出主要成分为石灰石的矿石。
然后,将矿石进行粉碎和研磨,使其成为适合使用的矿石粉末。
接下来,将矿石粉末储存到仓库中,以备后续使用。
2. 石灰石的预处理:将石灰石粉末进行预处理,去除其中的杂质和有害元素。
这一步骤一般包括石灰石的煅烧和煅破过程。
石灰石煅烧时,会发生石灰石的石化反应,将石灰石中的碳酸钙转化为生石灰。
石灰石煅破时,将煅烧后的石灰石进行破碎和筛分,得到适合生产水泥的石灰石颗粒。
3. 黏土的预处理:同时,还需要将黏土进行预处理。
黏土经过破碎和筛分,去除其中的杂质,得到黏土颗粒。
4. 生料的混合:将经过预处理的石灰石和黏土按一定的比例进行混合。
混合比例的确定需要考虑到所生产水泥的性能要求。
混合后的生料称为熟料。
5. 熟料的煅烧:将混合后的熟料进入旋转窑中进行煅烧处理。
这一步骤主要是通过高温下的化学反应,将熟料中的物质转化为水泥熟料。
煅烧温度一般在1400℃左右。
煅烧过程中,熟料逐渐转化为熟料球。
6. 煤磨和水泥辅料制备:在煅烧过程中,需要使用煤作为主要燃料。
首先,将煤矿从矿井中采出,并进行破碎和粉磨,得到煤粉。
同时,将焚烧废渣等其他材料进行破碎和粉磨,得到适合制备水泥辅料的颗粒。
7. 水泥的制备:煅烧后的熟料球经过冷却和筛分,得到水泥熟料。
然后,将水泥熟料与煤粉、水泥辅料等进行混合和研磨,得到最终的水泥产品。
这个步骤一般通过水泥磨机进行完成。
8. 包装和储存:最后,将制备好的水泥产品进行包装,以便运输和储存。
包装一般采用纸袋或者增塑塑料袋。
包装好的水泥袋使用机器进行堆放和码垛,方便地存放在仓库中。
综上所述,水泥的生产工艺流程主要包括石灰石的采矿和处理、黏土的预处理、生料的混合、熟料的煅烧、煤磨和水泥辅料制备、水泥的制备、包装和储存等步骤。
石灰石的预处理和煅烧

.
煅烧工艺条件
石灰石的粒度、形状、装窑方法
窑气的温度、压力和密封
煅烧的温度、碳酸钙的分 解率和二氧化碳浓度
无烟煤粒 度、配煤
率
预热区: 对流传热。 700-900℃
煅烧区:辐射 为主,传导对 流为辅。1050-
1150℃石灰石的粒度越均 匀,源自烧成的石灰质量 越稳定。.
煅烧工艺条件 ---石灰石的形状:
各边尺寸比 煅烧时间h
1:1:1 1
1:1:2 1.23
1:1.5:2 1.6
1:2:3 2.2
名义尺寸相同,各边尺寸比例不同的石灰石煅烧时间
1:3:4 2.6
球形或者立方形的 石灰石煅烧时间最 短
.
煅烧工艺条件 ---无烟煤的粒度(一):
.
煅烧的原理
煅烧中提供热源的燃料有:煤炭,煤气,天然气 等。
我们选用的是无烟煤,其特点是密度大,含碳量 高,挥发分少,发热量大(约29308KJ/kg),灰分少, 含硫量低。
煤的主要可燃性元素是:碳,其次是氢。
.
煅烧的原理
影响燃料完全燃烧并释放高温的因素之一是空气 的存在和使用。
空气由78%的氮和21%的氧,以及少量的二氧化碳 和二氧化硫等组成。有效助燃的成分是氧气。
石灰石的预处理和煅烧
.
.
煅烧:活性石灰生产 1、石灰石的预处理 2、煅烧原理 3、煅烧石灰石的区段划分 4、煅烧的工艺条件 5、煅烧的工艺流程 6、回转窑煅烧系统工艺及结构
.
石灰石的预处理
根据石灰石的形状和粒度的大小以及污染情况等 各项入窑煅烧的理化指标,必须对石灰石进行预处理。
石灰窑工艺流程

石灰窑工艺流程石灰窑工艺流程石灰是一种广泛应用的建筑材料,可用于制造钢铁、玻璃、水泥等行业。
石灰窑就是将石灰石进行加热和石灰的煮沸过程,从而得到石灰的设备。
以下是石灰窑的工艺流程。
首先,原料准备。
石灰窑的原料主要是石灰石,石灰石首先需要破碎成约25毫米的小颗粒。
然后,将其破碎的石灰石放入储石仓,以备后续使用。
其次,石灰石的预煮处理。
将储石仓中的石灰石通过给料机送入窑前,然后通过预煮器进行预处理。
预煮器内,将石灰石与高温燃烧的气体进行接触,燃烧的气体在窑内上升过程中通过与石灰石的接触,对其进行预煮。
然后,石灰石的加热与煅烧。
经过预煮的石灰石进入石灰窑,窑内通过燃烧煤或天然气等燃料,使窑内温度升高到1200-1400摄氏度,此时的石灰石开始进行热分解。
石灰石中的碳酸钙在高温下分解为氧化钙和二氧化碳。
氧化钙是石灰的主要成分,而二氧化碳则通过排出窑外的气体排放。
接着,石灰的冷却与收集。
经过煅烧的石灰在窑内逐渐冷却。
窑内冷却气通过风机引入,并通过不同位置的喷淋装置对石灰进行冷却处理。
冷却后的石灰进入石灰仓,待用。
最后,石灰的包装和储存。
将冷却后的石灰通过输送带或其他装置运送至包装区,然后将其装入袋子或桶中进行包装。
包装完成后,石灰可通过仓储设备存放在仓库中,待发售或使用。
总结起来,石灰窑的工艺流程包括原料准备、石灰石的预煮处理、石灰石的加热与煅烧、石灰的冷却与收集以及石灰的包装和储存。
这个流程通过破碎、预煮、加热、煅烧、冷却等多个步骤将石灰石转化为石灰,并进行包装和储存,以满足不同行业对石灰的需求。
活性碳酸钙的生产工艺

活性碳酸钙的生产工艺
活性碳酸钙是一种具有高活性的碳酸钙产品,主要用于工业中的涂料、橡胶、塑料、建材等制造过程中的填充剂、增强剂和调节剂。
下面将介绍活性碳酸钙的生产工艺。
1. 原料准备:活性碳酸钙的主要原料包括石灰石和二氧化碳。
石灰石通常经过采矿、破碎、筛分等处理过程后得到。
二氧化碳可以通过氧化石灰或高温煅烧石灰石的方式获取。
2. 石灰石的预处理:将采集得到的石灰石经过清洗和干燥处理,去除其中的杂质和含水分。
3. 石灰石的煅烧:将预处理好的石灰石放入煅烧炉中进行加热。
在适当的温度下,石灰石中的碳酸钙会分解出二氧化碳,生成氧化钙(生石灰)。
4. 氧化钙的水化:生石灰与水反应,生成氢氧化钙(熟石灰)。
这一步骤是将氧化钙转化为水合物,从而提高活性碳酸钙的活性。
5. 二氧化碳和氢氧化钙的反应:将二氧化碳送入水合石灰的反应容器中,与氢氧化钙反应生成碳酸钙。
这是活性碳酸钙的关键步骤,二氧化碳的加入使得碳酸钙具有了更高的活性。
6. 碳酸钙的分级和干燥:将反应生成的活性碳酸钙进行分级筛分,去除不符合规格要求的颗粒。
然后通过干燥设备将碳酸钙中的水分去除,提高其质量稳定性和保存期限。
7. 包装和储存:将干燥好的活性碳酸钙分装到适当的包装容器中,并进行密封和贮存。
在储存过程中,需要注意防潮和避光,以保证活性碳酸钙的质量和活性。
需要注意的是,在生产活性碳酸钙的过程中,需要严格控制反应的条件和物料的质量,以确保产品的品质。
同时,在使用活性碳酸钙时,需要遵循相关的安全操作规程,确保生产过程的安全性。
氢氧化钙的制备方法和工艺流程

氢氧化钙的制备方法和工艺流程氢氧化钙,简称石灰,是一种广泛应用于工业和农业的化学物质。
它的应用范围很广,被用于水处理、金属冶炼和电力产业等。
而在农业方面,氢氧化钙可用于土地改良和酸性土的中和。
本文将介绍氢氧化钙的制备方法和工艺流程。
一、氢氧化钙的制备方法氢氧化钙的制备方法主要有两种,分别是石灰石煅烧法和氢氧化钠水解法。
1. 石灰石煅烧法石灰石煅烧法是最广泛应用的制备氢氧化钙的方法。
该方法的原理是在高温下将石灰石(CaCO3)分解成氧化钙(CaO)和二氧化碳(CO2),然后再通过加水反应生成氢氧化钙(Ca(OH)2)。
石灰石煅烧法的具体步骤如下:(1)将石灰石破碎成小块状。
(2)将破碎后的石灰石放入石灰窑中,采用高温石灰石煅烧法进行加热。
通常,石灰石煅烧的温度在800°C~1000°C之间,具体的温度要根据原料和工艺的具体要求进行调整。
(3)在高温下,石灰石中的CaCO3分解成CaO和CO2。
(4)将CaO与水反应,生成氢氧化钙。
该方法的优点是生产成本较低,适用范围较广。
但是,石灰窑的建设和维护成本较高,而且在煅烧过程中,由于温度高,容易产生粉尘和有害气体,应做好环境保护工作。
2. 氢氧化钠水解法氢氧化钠水解法是一种利用氢氧化钠(NaOH)在水中产生的反应生成氢氧化钙的方法。
具体步骤如下:(1)将一定量的氢氧化钠溶解在水中,得到氢氧化钠溶液。
(2)将氢氧化钠溶液与适量的石灰石混合,再加入适量的水,混合均匀。
(3)将混合液进行反应,产生氢氧化钙。
氢氧化钠水解法的优点是制备过程简单、反应速度快,并且在工艺过程中不会产生有害气体。
但是,由于溶解氢氧化钠所需的能量较高,花费较高,生产成本较高。
二、氢氧化钙的工艺流程1. 石灰石煅烧法工艺流程石灰石煅烧法的工艺流程主要包括石灰石预处理、配料、煅烧、水合和成品加工等步骤。
具体步骤如下:(1)石灰石预处理:将石灰石进行破碎、清洗、筛选等预处理,选择一定尺寸的石灰石,以保证煅烧质量。
石灰窑工艺流程

石灰窑工艺流程
石灰窑是一种用于生产石灰的设备,其工艺流程包括原料准备、石灰石煅烧、石灰石煅烧后处理和成品石灰的包装等环节。
原料准备是石灰窑工艺流程的第一步。
在这一阶段,需要准备石灰石作为主要原料。
石灰石是一种含有高浓度钙碳酸盐的矿石,常见的有方解石和白云石等。
石灰石需要经过采矿、破碎和筛分等工序,以获得适合石灰窑生产的颗粒度。
接下来是石灰石煅烧的过程。
石灰石煅烧是将石灰石加热至高温,使其分解为氧化钙和二氧化碳的过程。
这一过程通常在石灰窑内进行。
石灰窑内部通常由石灰石进料口、燃料进料口、烟气排放口和石灰石产物出口等组成。
石灰石在石灰窑内经过预热、煅烧和冷却等阶段,最终得到煅烧后的石灰石产物。
石灰石煅烧后处理是石灰窑工艺流程的下一步。
煅烧后的石灰石产物需要进行处理,以获得符合要求的成品石灰。
处理过程包括石灰石产物的破碎、筛分和粉碎等工序。
这些工序可以根据不同的产品要求进行调整,以获得不同颗粒度和质量的成品石灰。
最后是成品石灰的包装。
经过煅烧后处理的石灰石产物被称为成品石灰。
成品石灰需要进行包装,以便储存和运输。
常见的包装方式包括袋装、散装和桶装等。
包装过程需要注意保护成品石灰的质量
和安全,以确保其在储存和运输过程中不受损坏。
总结起来,石灰窑工艺流程包括原料准备、石灰石煅烧、石灰石煅烧后处理和成品石灰的包装等环节。
这一工艺流程经过多个步骤,确保了石灰石的高效生产和成品石灰的质量。
石灰窑工艺流程的顺利进行对于石灰生产具有重要意义,同时也为建筑、冶金、化工等行业提供了重要的原材料。
石灰的生产过程

石灰的生产过程1. 石灰的概述石灰是一种常见的化学物质,主要成分是氧化钙(CaO)。
它在建筑、工业和农业领域中有广泛的应用。
石灰的生产过程可以通过不同的方法进行,其中包括石灰石的煅烧和水合。
2. 石灰石的煅烧石灰石的煅烧是生产石灰的主要过程之一。
这个过程中,石灰石被加热到高温,使其分解成氧化钙和二氧化碳。
以下是石灰石煅烧的主要步骤:步骤1:石灰石的选矿和破碎首先,从石灰石矿山中挖掘出石灰石。
然后,石灰石会经历一系列的选矿和破碎过程,目的是去除杂质并将石灰石破碎成适当的颗粒大小。
步骤2:石灰石的预处理在石灰石煅烧之前,有时需要对石灰石进行预处理。
这个过程中,可以通过洗涤和干燥去除石灰石中的一些杂质和水分。
步骤3:石灰石的煅烧将经过预处理的石灰石放入石灰窑中,然后加热。
石灰窑通常使用燃烧器产生高温,并将石灰石加热到约900至1000摄氏度。
在高温下,石灰石分解为氧化钙和二氧化碳。
步骤4:氧化钙的收集和储存分解出的氧化钙会从石灰窑中被收集和储存。
这个过程中,可以使用一些设备和方法来收集氧化钙,例如旋风分离器或电滤袋。
3. 石灰的水合石灰的水合是另一种生产石灰的方法。
这个过程中,氧化钙与水反应,产生氢氧化钙(Ca(OH)2)。
以下是石灰的水合过程的主要步骤:步骤1:氧化钙的准备首先,需要准备足够的氧化钙。
通常可以使用石灰石的煅烧产生的氧化钙。
步骤2:氧化钙与水的反应将氧化钙逐渐添加到水中,并搅拌。
在此过程中,氧化钙与水反应生成氢氧化钙。
这个反应会释放出大量的热。
步骤3:氢氧化钙的收集和储存生成的氢氧化钙可以被收集和储存。
与石灰石的煅烧不同,石灰的水合过程更安全,因为在这个过程中,没有生成二氧化碳等有害物质。
4. 石灰的应用石灰在多个领域中有广泛的应用,下面是其中一些主要的应用:•建筑业:石灰被广泛用于建筑材料,例如砂浆、混凝土和砖块。
它可以用作粘合剂和增强剂,提高建筑材料的强度和耐久性。
•工业领域:石灰被用于许多工业过程中,例如钢铁生产、纸浆和造纸、皮革加工和炼油。
电石渣生产氯化钙工艺

电石渣生产氯化钙工艺
电石渣生产氯化钙的工艺一般包括以下几个主要步骤:
1.石灰石的预处理:
首先,将石灰石(主要成分为氧化钙)进行预处理,通常是在高温下进行煅烧,将其转化为生石灰(氧化钙)。
2.电石的制备:
使用电弧炉对预处理后的石灰石进行电石制备。
在电石炉中,通过电解质(一般是氯化钠溶液)电解的方式,将电石炉中的石灰石转化为电石(主要成分是氢氧化钙)。
3.电石的氯化:
将制备好的电石与盐酸反应,生成氯化钙和氢气。
反应方程式如下:Ca(OH)2+2HCl→CaCl2+2H2↑Ca(OH)2+2HCl→CaCl2+2H2↑
4.氯化钙的沉淀和提取:
氯化钙会沉淀出来,可以通过沉淀、过滤等步骤将其分离提取。
5.氯化钙的结晶和干燥:
对提取得到的氯化钙溶液进行结晶和干燥,得到固体的氯化钙。
6.氯化钙的精制:
对初步提取得到的氯化钙进行精制,以提高氯化钙的纯度。
以上过程描述了电石渣生产氯化钙的一般工艺流程。
这个工艺的关键是通过电石制备得到氢氧化钙,然后再与盐酸反应生成氯化钙。
氯化钙在许多领域中有广泛的应用,包括在化学工业、农业、食品工业等领域。
值得注意的是,这只是一种可能的工艺流程,具体的生产工艺可能因厂家和设备的不同而有所调整。
- 1、下载文档前请自行甄别文档内容的完整性,平台不提供额外的编辑、内容补充、找答案等附加服务。
- 2、"仅部分预览"的文档,不可在线预览部分如存在完整性等问题,可反馈申请退款(可完整预览的文档不适用该条件!)。
- 3、如文档侵犯您的权益,请联系客服反馈,我们会尽快为您处理(人工客服工作时间:9:00-18:30)。
无烟煤的主要组成部分是碳C,其次是氢H,并 含有少量的氧O2,氮N2,硫S。
碳和氢是主要可燃性元素。 氮基本不参与燃烧。 氧会与碳和氢形成氧化物使之失去可燃性。 硫是极为有害的物质,在燃烧后生成的SO2 ,SO3 会危害人体健康和造成大气污染,并造成金属氧化、 脱碳、腐蚀。硫进入金属还会造成金属的物理力学性 能变坏。
过烧:就是石灰石在煅烧过程中,内部温度达到 898℃,碳酸钙完全分解后继续停留在煅烧区,使得 温度持续升高,这样就容易产生过烧石灰,也叫死 烧石灰。其特点是结晶单元逐渐规则排列整齐,体 积比生烧石灰的体积缩小43%,且表面发黑,具有硬 度大,密度大,活性差,消化后的氢氧化钙粒子粗, 生产出来的PCC或纳米碳酸钙的沉降体积值小等。
石过烧甚至导致结瘤事故; 配煤率过低,则会使石灰石生烧。 无烟煤中固定碳含量为78%~82%时,配煤率为
100:12~100:15。
装窑方法有混和装窑法和分层装窑法 混合的优点:石灰石和无烟煤混合比较均匀,
适合于配煤率小,一次加入燃烧量不多的立窑。 分层的优点:便于调节无烟煤在窑截面的分布
状态,适合于配煤率大的立窑。
反应速度与粒度无关, 与温度有关。温度越高,反 应速度越快。因此,一定粒 度的石灰石,煅烧温度越高, 反应速度越快,煅烧时间也 就越短。
△
分解反应式为:MgCO3 === MgO + CO2 ↑ 碳酸镁的分解温度为640 ℃ 。 氧化镁的活性低,因此,氧化镁基本不参与其他
杂质反应,对煅烧过程影响不大。
1、配煤率适当,使碳酸钙充分分解; 2、碳酸钙在煅烧区有足够的停留时间; 3、煅烧温度不能过低。
窑气中CO2含量越高,石灰乳所需碳化时间就越短, 碳化塔生产能力就越大。
维持窑气中CO2浓度高的条件: 1、选用低挥发分的无烟煤; 2、减少热损失,降低配煤率; 3、使空气过剩系数尽可能低; 4、窑顶出气压力维持正压,以免空气漏入窑气中。
同的区段有不同的温度和发生不同的反应。根据物 料和气体所经历的物理、化学过程的不同,将石灰 石在窑内煅烧分为三个区段:
1、预热区 2、煅烧区 3、冷却区
1、窑内燃烧产生的烟气将该区域内的物料预热至 900℃左右;
2、物料中的水分被完全蒸发掉; 3、碳酸镁完全分解并释放出二氧化碳; 4、碳酸钙受热膨胀龟裂,表面部分开始分解反应;
提高煅烧区温度的方法: 1、提高配煤率; 2、加大风量; 3、采用粒度均匀的石
灰石。
相同的煅烧温度下, 石灰石的粒度越小,所 需的煅烧时间越短。
石灰石的粒度越均 匀,所烧成的石灰质量 越稳定。
各边尺寸比 煅烧时间h
1:1:1 1
1:1:2 1.23
1:1.5:2 1.6
1:2:3 2.2
名义尺寸相同,各边尺寸比例不同的石灰石煅烧时间
煅烧中提供热源的燃料有:煤炭,煤气,天然气 等。
我们选用的是无烟煤,其特点是密度大,含碳量 高,挥发分少,发热量大(约29308KJ/kg),灰分少, 含硫量低。
煤的主要可燃性元素是:碳,其次是氢。
影响燃料完全燃烧并释放高温的因素之一是空气 的存在和使用。
空气由78%的氮和21%的氧,以及少量的二氧化碳 和二氧化硫等组成。有效助燃的成分是氧气。
在煅烧过程中,必须有足够的空气参与燃烧。一 是为了保证燃料能完全燃烧释放足够的热量,二是控 制因氧气不足燃料不完全燃烧生成的一氧化碳。
分解反应式为: △ CaCO3 === CaO + CO2 ↑-176.6kj 该反应具有以下特点:
1、是多相反应:固体煅烧后生成固体和气体。 2、是可逆反应: 3、是吸热反应:碳酸钙分解需要吸收热量。
一般预处理的方法是破碎、清洗和分级。
1、对石灰石进行破碎以达到煅烧的要求; 2、对石灰石进行清洗以保证产品的质量;
根据产品质量的要求以及石灰石的污染情况, 对石灰石用水进行清洗。
3、对石灰石进行粒度分级以保证煅烧的质量。
破碎: 常用设备有颚式破碎机、冲击式破碎机和回旋
式破碎机; 常用的二级破碎设备有锤式破碎机、反击式破
氧化钙的结瘤是指在煅烧过程中,温度达到 800℃以上时,二氧化硅,三氧化二铝和三氧化二铁 等杂质会与氧化钙反应生成熔点低而又粘稠的硅酸 钙,铝酸钙,铁酸钙,铁铝酸钙等半融物质,这些 物质会把石灰石粘成大块并烧结成瘤块,部分会黏 在窑壁上,形成结瘤事故。
硅酸钙的生成: SiO2 +xCaO=xCaO·SiO2 铝酸钙的生成: Al2O3+xCaO=xCaO·Al2O3 铁酸钙的生成: Fe2o3+xCaO=xCaO·Fe2O3 铁铝酸钙的生成:
风量是指送入窑内的空气量,风量取决于无烟 煤完全燃烧所需的理论空气消耗量。
根据计算,如果配煤率为100:15,则煅烧1kg 石灰石所需空气量约为1.07m³
风量过小:
1、无烟煤无法完全燃烧,窑气中CO浓度升高, CO2浓度降低;
2、煅烧区温度降低,生烧量增加; 3、煅烧区缺氧,无烟煤在冷却区继续燃烧,使 煅烧区下移,无烟煤消耗增加。
通过计算可以得知,在常压下,温度高于530 ℃时,碳酸钙分解出CO2 的压力等于空气中CO2 的 压力;在898 ℃时,碳酸钙分解出CO2 的压力等于空
气的压力;因此,把898℃ 称为碳酸钙的分解温度。 温度越高,碳酸钙分解 CO2 就越剧烈。
碳酸钙的分解速度用分解反应面的移动速度来
表示。分解反应面是指已分解的氧化钙和未分解的 碳酸钙之间的分界面。
碳燃烧过程的反应式:
C+O2 → CO2↑ ----------氧气充足时的主要反应 2C+O2 → 2CO ↑-----------氧气不足时的主要反应 2CO+O2 → 2CO2 ↑--------------一氧化碳的氧化反应 CO2 +C===2CO ↑--------------二氧化碳的还原反应
1:3:4 2.6
球形或者立方形的 石灰石煅烧时间最 短
无烟煤的粒度应使其燃烧时间和石灰石煅烧时 间相适应,而石灰石的煅烧时间主要取决于石灰石 的粒度。因此,无烟煤的大小与石灰石的大小成正 比。
回转窑使用的燃烧器的燃料是煤粉。无烟煤粒 度在0.08mm,
无烟煤的粒度太小:
1、燃烧时间过短,温度达不到,石灰石易生烧; 2、造成透气性差,通风不良,增加能耗; 3、部分太小的碎粒还可能被吹走或顺缝隙下漏, 造成窑气粉尘含量增加或冷却区温度升高等。
风量过大: 1、空气中过量的O2和N2,也使窑气中CO2浓度
降低, 2、空气不能预热到所需温度,使燃烧区温度下
降,生烧量增加; 3、预热区O2浓度增加,燃煤提前燃烧,使煅烧
区上移,窑气温度升高,空气带走热量增加,使无 烟煤消耗增加。
风压主要取决于立窑的有效高度及石灰石和无 烟煤的粒度。
窑顶出气压力维持在正压,以免空气漏入窑气 中,使窑气中CO2浓度降低。
烧成的石灰离开煅烧区,或者煤中的碳不再燃烧, 石灰石中的碳酸钙不再分解且温度开始下降,这个 区段物料经历的过程主要是冷却。而本阶段的的气 体因为在冷却石灰的同时进行热交换后升温,升温 后的气体导入窑中作为二次风参加燃烧。
1、开始分解前的膨胀; 2、碳酸钙的分解; 3、石灰石的烧结; 4、石灰的冷缩。
1、煅烧的温度 3、石灰石的形状 5、配煤率 7、风量 9、窑顶出气压力 11、碳酸钙的分解率
2、石灰石的粒度 4、无烟煤的粒度 6、装窑方法 8、风压 10、出气、出料温度 12、窑气中CO2的含量
提高煅烧温度可以提高
生产能力,但温度过高容易 导致结瘤事故且热损耗高。 一般控制煅烧区温度为 1050-1150 ℃。
Al2O3+Fe2O3+xCaO=xCaO·Al2O3·Fe2O3 亚硫酸钙的生成: S+O2=SO2 SO2+CaO=CaSO3
1、会使煅烧紊乱,使石灰石或烧成的石灰粘 在窑壁,形成结瘤或者结圈,造成石灰的生烧或者 过烧。
2、会覆盖在烧成的石灰表面,降低石灰的消 化性能。
石灰窑在煅烧ቤተ መጻሕፍቲ ባይዱ灰石时,窑内的物料和气体在不
常用的分级设备是振动筛。
被煅烧的物料是:石灰石。
石灰石的主要成分是碳酸钙CaCO3 ,少量的碳酸 镁MgCO3以及一些二氧化硅SiO2,三氧化二铝Al2O3 和三氧化二铁Fe2O3杂质。
煅烧时,主要是石灰石中碳酸钙CaCO3和碳酸镁 MgCO3的分解反应,无烟煤中碳C的燃烧反应和氧化 物的结瘤反应。
碳燃烧的热力学: 根据碳燃烧的热力学得知,在碳的实际燃烧,氧
气充足时,反应生成的CO会和氧气O2继续反应生成 CO2 。所以氧气充足时碳燃烧得到的气体中CO是少 量的。
碳燃烧的动力学: 影响碳燃烧反应速度的因素: 1、碳与氧气的化学反应速度; 2、氧气向碳表面扩散的速度。 实际生产中,碳的燃烧反应都是在高温下进行,
石灰石持续受热,继续分解,并且速度加快; 煅烧区温度不够,碳酸钙不能完全分解,造成生 烧,反之,碳酸钙完全分解后继续在煅烧区停留, 石 灰会进一步烧结,造成过烧。 过烧石灰不仅浪费原料,降低窑产量,而且本身 质量变差,严重影响纳米碳酸钙的产品质量。
生烧:就是石灰石在煅烧过程中,内部温度没有 达到898℃,碳酸钙没有完全分解就被冷却卸出,这 样的石灰就是生烧石灰,也叫轻烧石灰。其特点是 白度高,活性好,体积收缩性小,易消化,消化后 的氢氧化钙悬浮粒子小,生产出来的PCC或纳米碳酸 钙的沉降体积值高等。
石灰石的粒度、形状、装窑方法
窑气的温度、压力和密封
煅烧的温度、碳酸钙的分 解率和二氧化碳浓度
无烟煤粒 度、配煤
率
预热区: 对流传热。 700-900℃
煅烧区:辐射 为主,传导对 流为辅。1050-
1150℃
冷却区:强 制风冷、对 流传热。 100℃左右
风温、风 压、风量
出料温度