甲醇合成反应器概述
甲醇的生产—生产工艺流程的组织
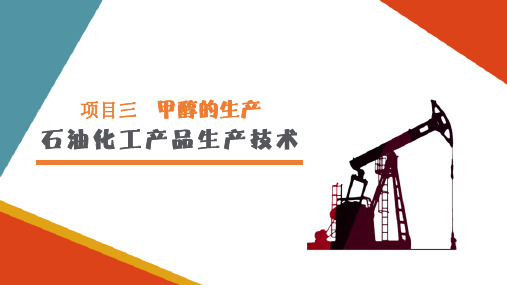
反应器的选用
2、合成反应器的结构和材质 冷激式绝热反应器 优点√:生产能力大,结构简单,催化剂装卸方便; 缺点×:催化剂时空产率不高,用量较大,且仅能 回收低品位的热能。 列管式等温反应器 优点√:温度易于控制,单程转化率较高,循环气 量小,能量利用较经济,反应器生产能力大,设备 结构紧凑。 缺点×:结构相对较复杂,装卸催化剂不方便。
压力要求:能承受高压
材质能防止氢气、一氧化碳、甲醇、有机酸及羰基物的高 温腐蚀;要求出塔气体温度不超过160℃,因此设备结构 上必须考虑高温气体的降温问题。
生产能力与催化剂的装填量成正比例关系,要充分利用合 成塔的容积,装填量尽量多,以提高设备生产能力。
高空速能获得高收率,但气体通过催化剂床层的压力降必然 会增加,应使合成塔的流体阻力尽可能小,避免局部阻力过 大的结构。同时,要求合成反应器结构必须简单、紧凑、 坚固、气密性好,便于拆卸、检修。
项目三 甲醇的生产
石油化工产品生产技术
任 务 四
流 程 的 组 织
生 产 工 艺
知识点1:工艺流程的组织
生产工序
按合成压力分为高压法、中压法和低压法三种工艺。 由于低压法甲醇合成技术经济指标先进,现在世界各国 甲醇合成已广泛采用了低压合成法。低压法合成甲醇主 要工序有制气、净化、压缩、合成、精馏如下图所示。
低压法合成甲醇生产工艺流程
粗甲醇中除含甲醇外,还含有两大类杂质:
一类是溶于其中的气体和易挥发的轻组分,
如氢气、一氧化碳、二氧化碳、二甲醚、乙
醛、丙酮、甲酸甲酯和羰基铁等;
另一类是难挥发的重组分,如乙醇、高级
醇、水等。可用两个塔予以精馏。
杂醇油
由于低压法合成的甲醇杂质含量少,净化
比较容易,利用双塔精制流程,便可以获得纯
甲醇合成反应器
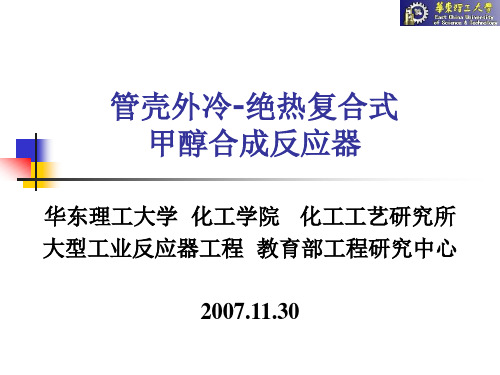
投产运行 2005.10 投产 2005.10 投产 准备投产 2006.12 投产
企业
甲醇规模 kt/a
工艺路线
投产运行
南京惠生 集团公司 宁夏煤业 集团公司
300 250 200
250
水煤浆气化、低温甲醇洗、 2007年4 低压合成、三塔精馏 月投产 水煤浆气化、低温甲醇洗、 2007年1 低压合成、三塔精馏 月投产
管壳外冷-绝热复合式合成反应器特点 6.催化剂装卸、还原方便 (1)上封头设有人孔,催化剂装填方便。 (2)设有卸触媒孔,触媒直接放出。 (3)触媒还原时,只需将原通过冷却介质 侧,改通蒸汽加热即可,十分方便。
管壳外冷-绝热复合式合成反应器特点
7.反应器的操作适应性强 (1)对催化剂的适应性强。 可使用西南化工研究院C302型、XNC-98型; 也可使用南化公司研究院NC-306、307型催化剂,也 可以使用国外催化剂如Johnson Matthey KATALCOTM 51系列催化剂,丹麦MK-121型催化 剂,德国南方公司催化剂等。 (2)对原料气的适应性强 可使用以煤为原料的合成气(新鲜气CO 26~ 28%),也可使用以天然气为原料的合成气(CO 11~13%),还可使用焦炉气转化的合成气(催化 转化和非催化转化)。
新疆克拉玛 依
河南平安化 工有限公司
天然气为原料
2006年8 月投产
间歇煤气、耐硫宽温变换、 准备投 栲胶脱硫、NHD脱碳,三 产 塔精馏
企业
甲醇规模 kt/a
工艺路线
投产运行
河南永城煤 业集团
淮北临涣
500
200 250 200
Shell气化、低温甲醇洗净 准备投 化、低压合成、三塔精馏 产
以焦炉气为原料,转化,低压 合成、三塔精馏
甲醇合成塔介绍

来??源:百川资讯更新时间:2011-09-0116:17【打印】【收藏】
关键字:甲醇?合成塔
摘??要:甲醇合成塔设计的关键技术之一就是要高效移走和利用甲醇合成反应所放出的巨大热量。
甲醇合成塔设计的关键技术之一就是要高效移走和利用甲醇
热性和热稳定性较好,反应温度接近等温,易于控制,一氧化碳与二氧化碳的单程转化率和气相产物中的甲醇百分含量高于传统的气-固相催化法。
及时甲醇市场资讯,欢迎登陆百川资讯甲醇频道。
更多甲醇相关常识,欢迎进入百川资讯甲醇常识中心。
甲醇合成塔介绍
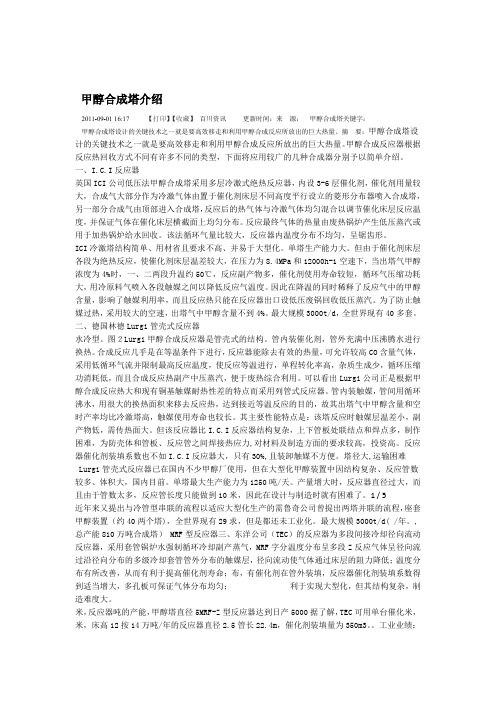
甲醇合成塔介绍2011-09-01 16:17 【打印】【收藏】百川资讯更新时间:来源:甲醇合成塔关键字:甲醇合成塔设计的关键技术之一就是要高效移走和利用甲醇合成反应所放出的巨大热量。
摘要:甲醇合成塔设计的关键技术之一就是要高效移走和利用甲醇合成反应所放出的巨大热量。
甲醇合成反应器根据反应热回收方式不同有许多不同的类型,下面将应用较广的几种合成器分别予以简单介绍。
一、I.C.I反应器英国ICI公司低压法甲醇合成塔采用多层冷激式绝热反应器,内设3-6层催化剂,催化剂用量较大,合成气大部分作为冷激气体由置于催化剂床层不同高度平行设立的菱形分布器喷入合成塔,另一部分合成气由顶部进入合成塔,反应后的热气体与冷激气体均匀混合以调节催化床层反应温度,并保证气体在催化床层横截面上均匀分布。
反应最终气体的热量由废热锅炉产生低压蒸汽或用于加热锅炉给水回收。
该法循环气量比较大,反应器内温度分布不均匀,呈锯齿形。
ICI冷激塔结构简单、用材省且要求不高、并易于大型化。
单塔生产能力大。
但由于催化剂床层各段为绝热反应,使催化剂床层温差较大,在压力为8.4MPa和12000h-1空速下,当出塔气甲醇浓度为4%时,一、二两段升温约50℃,反应副产物多,催化剂使用寿命较短,循环气压缩功耗大,用冷原料气喷入各段触媒之间以降低反应气温度。
因此在降温的同时稀释了反应气中的甲醇含量,影响了触媒利用率,而且反应热只能在反应器出口设低压废锅回收低压蒸汽。
为了防止触媒过热,采用较大的空速,出塔气中甲醇含量不到4%。
最大规模3000t/d,全世界现有40多套。
二、德国林德Lurgi管壳式反应器水冷型。
图2Lurgi甲醇合成反应器是管壳式的结构。
管内装催化剂,管外充满中压沸腾水进行换热。
合成反应几乎是在等温条件下进行,反应器能除去有效的热量,可允许较高CO含量气体,采用低循环气流并限制最高反应温度,使反应等温进行,单程转化率高,杂质生成少,循环压缩功消耗低,而且合成反应热副产中压蒸汽,便于废热综合利用。
合成气制甲醇
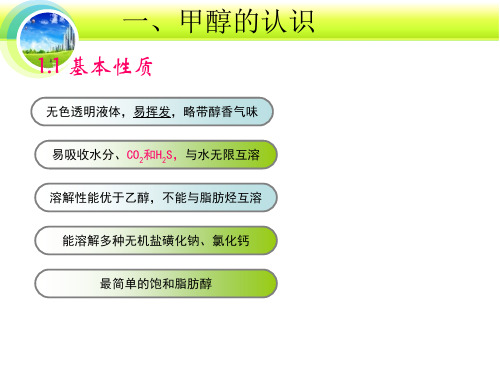
还原过程为活化:氮气流升温、还原
CuO-ZnO-Al2O3 0.4MPa,99%N2
缓慢地升温, 20℃/h
CuO-ZnO-Al2O3
160~170℃
还原性气体(如H2)
Cu-ZnO-Al2O3
②反应条件
a.反应温度及压力:
可逆放热反应,温度升高,反应速率增加,而平衡常数下降
反应温度
反应温度因催化剂种类而异
项 目 高压法
中压法
低压法
压 力 30.0MPa 10.0~15.0MPa 5.0~10.0MPa
温 度 340~380℃ 270℃左右
210~260℃
催化剂 Zn-Cr Cu-Zn-Cr Cu-Zn-Al
低压操作意味着出口气中甲醇的浓度较低,故合成气 的循环量增加,但是, 要提高系统压力, 设备的压力等级 也得相应提高, 这样将会造成设备投资加大和压缩机的功 耗提高,与高压法工艺相比,中、低压法工艺在投资和 综合技术经济指标方面都具有显著优势。以天然气为原 料的甲醇厂,高压法能耗达64.8GJ/t甲醇,而大型低压法 装置为29.5~31.5GJ/t甲醇。
• T<300℃ ,T↓ ,
↑,反应易失控
• P低,T高时,△H变化小,故选择20MPa,300~400℃,反 应易控
平衡常数 a. 温度对平衡常数的影响
Kf只与温度有关
b. 压力对平衡常数的影响
P↑,KN↑ ,xE↑ ,故应在高压下操作。
3.3 合成甲醇的工业催化剂
锌铬催化剂 :1966年以前几乎所有厂家都使用该催化剂,目前逐渐被淘汰 铜基催化剂 : 铜铬铝系和铜锌铬系得到广泛应用 钯系催化剂: 未工业化 低温液相催化剂 : 未工业化
空速:影响选择性和转化率,直接关系到催化剂的生产 能力和单位时间的放热量。
甲醇合成反应器与分离器工艺设计

甲醇合 成反应 器是 低压 合成 甲醇 的关键设 备 之一 。近年 来 , 随 着 甲醇装 置 的 大 型 化 ( 由单 套
3 0 k t / a 发 展 至 目前 的 3 5 0 k t / a , 甚 至更 大 ) , 甲醇
具有设计先进性与可行性。 关 键 词 甲醇 反 应器 分 离器
Pr o c e s s De s i g n o f Me t ha no l Co n v e r t e r a nd Se p a r a t o r
Wa n g B i n g h u a i , Wu S h e n  ̄ u n ( L a n z h o u A e r o s p a c e P e t r o c h e mi c a l E n g i n e e r i n g C o r p o r a t i o n G a n s u L a n z h o u 7 3 0 0 5 0 )
p r e s s u r e s t e a m i s 1 . 0 t p e r t o n o f me t h a n o l ,a n d t h e y a r e h i g h i n o p e r a t i o n a d a p t a b i l i t y a n d i n p r o d u c t q u li a t y .T h e me t h a n o l s e p a r a t o r a d o p t s t h e f u l l r e c o v e r y me t h no a l s e p a r a t i o n t e c h n o l o g y ,i t s r e c o v e r y r a t e i s n e a r l y l 0 o % ,a n d a f t e r s e p ra a t i o n t h e g a s p h a s e c o n t a i n s<0 . 1 % ,v o l u me f r a c t i o n o f me t h a n o 1 . Ac t u l a p r du o c t i o n i n s p e c t i o n s h o w s t h a t t h e t w o p i e c e s o f e q u i p me n t a r e a d v a n c e d i n d e s i g n a n d f e a s i b l第4 0卷
粗甲醇合成—甲醇合成设备(煤制甲醇课件)
内冷冷管连续换热式甲醇合成反应器
催化剂筐是合成塔的内件的核心部件。催化剂筐的外面包有玻璃纤维(或石 棉)保温层,以防止催化剂筐大量散热。上部设有催化剂筐盖,下部有筛孔板, 在筛孔板上放有一层不锈钢网,避免放置在上面的催化剂漏下。在催化剂筐里装 有数根冷管,冷管是由内冷管、中冷管及外冷管所组成的三套管,其中内冷管与 中冷管下端的环缝用满焊焊死,另一端敞开,这样可以使内冷管与中冷管间形成 一层很薄的不流动的滞气层从而起到隔热作用,这样呢,进塔气体自下向上通过 内冷管时,则不与中心管与外冷管内的气体进行换热,故而冷气的温升很小,内 冷管仅起输送气体的作用。冷气经中冷管与外冷管的环隙自上向下流动的过程, 与外部催化剂床层进行热交换作用,带走催化剂床层的热量。
热交换器
开工加热器是为了保证催化剂的升温还原,
内冷冷管连续换热式甲醇合成反应器
使学生掌握不同的内冷冷管连续 换热式甲醇合成反应器的结构及 工原理。
教学目的
教学
重点:三套管并流型甲醇合成反应器内流 程,其他内冷冷管反应器内流体流程。 难点:三套管并流型甲醇合成反应器结构。
教学重点与难点
内冷冷管连续换热式甲醇合成反应器
使学生掌握不同的连续换热式催 化剂筐的结构及换热原理。
教学目的
教学
重点:连续换热式催化剂筐的结构及换 热原理 难点:流体在催化剂筐内的流动方式。
教学重点与难点
连续换热式催化剂筐
根据合成塔内流体流动方式和换热方式不同将合成塔分为以下三类:
连续换热式
合成塔
多段换热式
径向式
连续换热式催化剂筐
根据换热介质的的不同将连续换热式催化剂筐进行分类
连续换热式催化剂筐
催化剂床层的实 际温度分布
甲醇合成的工艺流程和设备
甲醇合成的工艺流程和设备甲醇是一种重要的化工原料,广泛应用于化工、医药、食品等领域。
甲醇的合成工艺流程主要包括天然气制甲醇和煤制甲醇两种。
以下将以天然气制甲醇为例,介绍甲醇的合成工艺流程和设备。
1. 甲醇合成工艺流程甲醇的合成主要通过气相合成法进行,该方法通过一系列复杂的催化反应将一氧化碳和氢气合成甲醇。
具体的工艺流程如下:- 天然气→天然气净化→变化转换反应→合成气→合成气净化→合成气改质→甲醇合成→甲醇回收2. 甲醇合成设备甲醇合成设备主要包括催化反应器、冷凝器、分离塔等:- 催化反应器:将一氧化碳和氢气催化反应生成甲醇,需要具有较高的反应活性和选择性。
- 冷凝器:用于冷却和凝结合成气中的甲醇,使其形成液体甲醇。
- 分离塔:用于将液体甲醇从残余的气相中分离出来,保证甲醇的纯度和回收率。
3. 甲醇生产过程甲醇生产过程主要包括天然气的催化转变、合成气的制备、甲醇的合成和甲醇的回收等环节。
整个过程需要耗费大量的热能和电能,因此需要具备较为完备的能源设施和配套设备。
总的来说,甲醇的合成工艺流程较为复杂,需要涉及多个催化反应和分离过程,所需要的设备也比较繁杂。
企业在进行甲醇合成生产时,需要充分考虑到工艺流程和设备配置,确保生产过程的高效稳定。
甲醇是一种重要的化学品,其合成工艺的复杂性和对能源的依赖性使得甲醇工业在全球范围内备受关注。
天然气制甲醇是目前全球最为主流的甲醇生产工艺。
下面将详细介绍甲醇的合成工艺流程和设备,以及在甲醇生产过程中可能出现的关键技术和挑战。
4. 甲醇合成过程甲醇的合成工艺主要涉及以下几个过程:4.1 天然气制备合成气首先,天然气需要在天然气净化设备中进行净化处理,去除其中的硫化氢、二氧化碳和水等杂质。
通过石灰石和干燥剂的吸附、脱硫等处理,可使天然气达到合成气制备的要求。
然后,经催化转化反应,天然气中的甲烷和水蒸气进行高温反应,生成一氧化碳和氢气,形成合成气。
4.2 合成气的制备合成气是由一氧化碳和氢气所组成的气体混合物,它是甲醇合成的重要中间产物。
低压甲醇合成反应器述评
oie J .o dSa nc,0 3 15 1 :2 —2 8 xd [ ] Sl tt I is2 0 ,6 ( )2 3 2 . i eo [] 7
中图 分 类 号 :Q 2 .2 T 2311
文 献 标 识 码 : A
文 章 编 号 :0 3 4 7 2 0 ) 8 0 1 O 10 —36 (0 7 0 - 0 2一 3
Re iw fLo —Pr sur eha lSy t ssRe co ve o w — e s e M t no n he i a t r
摘
要: 介绍 了甲醇合 成的原理 , 当前 国内外低压 甲醇合成反 应器 , II 对 如 C 低压冷 激式 甲醇合 成塔 、ug 低 压管 L ri
壳式 甲醇合 成塔 、 日本 东洋的 MR F甲醇合成塔等进行 了比较 , 分析 了其优缺点。
关键词 : 甲醇 ; 成塔 ;工 艺 ; 备 合 设
trt so a pi brsno fr yrgnl k J . eii f not a f e e sr o hdoe a [ ] sc c i l e
S n . t t r , 2 03, 3: 42 —1 7. e s Acuao B, 0 s 9 1 4
[] 6
参考 文献 :
[ ] K bysi , au S n e a i:rc T i t 1 oaah T H rt M,aoH,t .n Po .hr I . a 1 d n
M t Che . ns, e e a g. m Se Clv lnd, Ohi USA , 9 o, 1 90, 8. 31
L u P, e T a y C E, ta . lcr c r mi d c e — i L e S, r c e E e t h o ca h mo 1 o n
甲醇合成反应器
包头师范学院本科毕业论文题目:低压法合成甲醇反应器性能比较学生姓名:樊巨强学院:化学学院专业:应用化学班级:08级一班指导教师:李军湘副教授二〇一二年五月摘要随着当今世界石油资源的日益减少和甲醇单位生产成本的降低,发展使用甲醇作为新的替代燃料,已成为一种趋势。
本文概括论述了当今世界工业生产上已应用的各类大型甲醉合成塔,主要对低压法甲醇合成塔在生产甲醇工艺流程中优点,使用条件、范围等做了研究,包括英国的ICI绝热型冷激塔,德国的Lurgi管壳式反应器、林德螺旋管反应器,丹麦的托普索绝热径向合成塔,日本TEC的MRF—Z型反应器、三菱瓦斯/三菱重工的超转化反应器,瑞士卡萨利卧式甲醇反应器,美国的APCI浆态床反应器以及国内林达公司、华南理工研发与改进的甲醇合成反应器。
并且对适宜应于在内蒙古地区的低压法甲醇合成塔类型做出分析。
关键词:甲醇;反应器;低压合成塔AbstractAs the world 's dwindling oil resources and reduce the production cost of methanol unit, development of methanol as a new alternative fuel, has become a trend.This paper briefly discusses the current world industrialproduction has been applied for all kinds of large-scale methanol synthesis tower,Mainly on the low pressure methanol synthesis tower in methanol production process advantages, conditions, scope varied research。
- 1、下载文档前请自行甄别文档内容的完整性,平台不提供额外的编辑、内容补充、找答案等附加服务。
- 2、"仅部分预览"的文档,不可在线预览部分如存在完整性等问题,可反馈申请退款(可完整预览的文档不适用该条件!)。
- 3、如文档侵犯您的权益,请联系客服反馈,我们会尽快为您处理(人工客服工作时间:9:00-18:30)。
甲醇合成反应器概述
现有的工业化甲醇合成工艺基本上是气相合成法。
从上世纪60年代至今,除了在反应器的放大催化剂的研究方面有些进展外。
其合成工艺基本上没有大的突破。
鉴于气相合成存在的一系列问题,从上世纪70年代人们把甲醇合成工艺研究开发重点转移到液相合成法,相初步实现了工业化的生产。
进入上世纪90年代后,我国也将开发高效节能的合成甲醇工艺和装置列为技术开发的重点。
甲醇合成反应器是甲醇合成生产的心脏设备。
设计合理的甲醇合成塔应做到催化剂床的温度易于控制,调节灵活,合成反应的转化率高,催化剂生产强度大,能从较高位能回收反应热,床层中气体分布均匀,低压降。
在结构上要求简单紧凑,高压空间利用率高,高压容器及内件无泄露,催化剂装卸方便。
在材料上要求具有抗羰基化物的生成及抗氢脆的能力。
在制造、维修、运输、安装上要求方便。
1.现有的有工业化的甲醇合成反应器
(1)ICI冷激型甲醇合成塔
ICI冷激型甲醇合成塔是英国ICI公司在1966年研制成功的。
它首次采用了低压法合成甲醇,合成压力为5 MPa,这是甲醇生产工艺上的一次重大变革。
采用固定床4段冷激式绝热轴流动反应器,通过特殊设计的菱形分布系统将冷激气喷人床层中间带走热量,床层多段连续,压降为0.5-0.6 MPa。
反应热预热锅炉水。
该反应器适于大型化,易于安装维修。
上世纪80年代ICI公司又开发出一种新型轴.径向流动的固定床反应器,其直径、壁厚明显减少.操作简单。
已有31个生产能力约1 400 t/d的这种装置运行。
ICI冷激型合成反应器的主要结构为:①塔体。
为单层全焊结构,不分内件、外件,故简体为热壁容器,要求材料抗氧蚀能力强,抗张强度高,焊接性好。
②气体喷头。
为4层不锈钢的圆锥体组焊而成,固定于塔顶气体入口处,使气体均匀分布于塔内。
这种喷头可以防止气流冲击催化床而损坏催化剂。
③菱形分布器。
菱形分布器埋于催化床中,并在催化床的不同高度平面上各安装1组,全塔共装3组,它使冷激气和反应气体均匀混合,以调节催化床层的温度,是塔内最关键的部件。
这样结构的合成塔,装卸催化剂很方便,3 h可卸完30 t的催化剂,装催化剂需10 h可以完成。
(2)Lurgi管壳型甲醇合成塔
Lurgi型甲醇合成塔是德国Lurgi公司研制的一种管束型副产蒸汽合成塔。
操作压力为5MPR,温度为250℃。
Lurgi合成塔既是反应器又是废热锅炉。
合成塔内部类似一般的列管式换热器,列管内装催化剂,管外为沸腾水。
甲醇合成反应放出的热很快被沸水移走。
合成塔壳程的锅炉水是自然循环的,这样通过控制沸腾水的蒸汽压力,可以保持恒定的反应温度,变化0.l MPa相当于l 5"C。
这种合成塔温度几乎是恒定的,有效地抑制了副反应,延长了催化剂的使用寿命。
但该合成塔结构复杂,装卸催化剂不方便。
(3)TEC新型反应器
多年来甲醇合成反应器的设计基本上是ICI冷激式和Lurgi列管式,直到进入上世纪90年代以后,日本TEC公司才在此方面向前迈进一步。
该公司开发的MRF—Z新型反应器的基本结构是反应器为圆筒状,有上下两
个端盖,下端盏可以拆卸以方便催化刺装填和内部设施检修;反应器内装有一直径较小的内胆用以改变物料流向;反应器的中心轴向安装一带外壳的列管式换热器,换热器的外壳上开有直径小于催化剂颗粒的小孔,换热器内管束间设有等距离的折流档板,以使原料气在管间均匀分布,沿径向外壳上的小孔流出,管束内通过反应后的高温气体。
反应器内还设有沿轴心分布的冷却管束和催化剂托架。
冷却管束为双层同心管.沸水从内管导人内外管问的环隙当中;催化剂装填在反应器内零部件的空隙当中。
物料流向是冷的合成气从反应器的上下两个端口同时进入换热器的管束间,受折流板的作用沿径向通过催化剂床层,在催化剂的作用下进行合成反应,反应后温度较高的气体折八催化剂托架与内胆的环隙间,从内胆的下部返回换热器的管束内,在此与温度较低的原料气换热,然后沿着内胆与反器壁的环隙问从反应器的底部流出。
由于气体沿径向流动催化剂床层压降小,气体循环所需要的动力大幅度减小,反应器制作时轴向长度可以加大,由于反应器内设有换热器和冷却器易于使催化剂床层的温度均匀一致,甲酵生成的浓度和速度可大幅度提高,反应温度容易控制,催化剂用量减少,反应器的结构紧凑。
2.正开发的甲醇台成反应器
(1)气相法合成甲醇反应器
国外甲醇合成反应器的发展趋势为:①要适应单系列大型化的要求,如ICI 冷激型已用于75万t/a装置,Lurgi管束型已用于45万t/a装置。
②以较高位能回收反应热,副产蒸汽,如Lurgi型、Linde型副产中压蒸汽。
③催化床层易于控制,可灵活调节,如Lurgi型用壳程的蒸汽压力调节层床温度.ICI型用冷激气量调节温度。
④床层温度尽可能均匀,以延长催化剂使用寿命。
⑤对原料气
组成有较强的适应性,可适用于煤、天然气、石脑油、渣油为原料制甲醇的多种场合。
⑥为降低压降,采用径向或轴径向流动反应器如Topsoe、Casale反应器。
⑦结构紧凑,催化荆装卸方便。
国内依据各种甲醇合成塔在我国使用、消化和国产化程度,提出两种大型易于国产化的甲醇合成塔型式。
一、多段径向冷激型甲醇合成塔
新鲜气与循环气混合后,由上部进气口进入反应器内,经分流流道进入第一段催化剂床层,由外向内向心径向流动,进行绝热反应,温度升高,在合流流道中与第一股冷激气混合降温,向下进入第二床层。
与第一段相同,气体经分流流道,由外向内向心流动边反应边升温,在合流流道中与第二股冷激气温合,向下进入第三段床层。
第三段床层中同样进行径向流动绝热反应。
出第三段床层的气体经合流流道从反应器流出三段床层主体均为向径向流动,三段床层上部用催化剂自封,为轴径向流动。
为使床层内气体均匀径向流动,用集管小孔开孔数来调节流体均布。
二、绝热-管束型甲醇合成反应塔
进塔气由上部进气口进入反应器,由气体分布器先经过绝热段催化剂床层,再流经管内催化层,反应放出热量,反应热被壳程沸腾水吸收,副产中压蒸汽。
反应后气体由下部气体出口流出。
绝热.管束型甲醇合成塔的关键部分为管板上列管的焊接、壳程热水与蒸汽的热力循环等。
由我国华东理工大学开发的绝热管壳外冷复合型甲醇合成反应器已经获得了专利,并在兖矿鲁南化肥厂100 kt/a 甲醇合成装置中成功应用。
以上工艺重在改善反应器的传质、传热性能,达到节能降耗并适度增产甲醇的目的。
但由于合成甲醇反应是一个可逆的放热反应,受热力学平衡的限制,一
般CO的单程转化率都较低,有大量的未反应气体需进行循环反应,一般循环比在5以上,这样就造成了较大的能耗,为了克服传统气相法合成甲醇工艺的的缺点,近10年来开发了几种新型的工艺,比较有代表性的如GSSTFR、RSIPR和气、液相并存反应器。
三、超临界相合成甲醇反应器
超临界相合成甲醇新工艺是一个前人尚未探索过的新过程,属重大原始性创新项目,它彻底打破了甲醇合成反应热力学平衡,把一个理论上的可逆反应变成一个实际上的不可逆过程。
该工艺适用于现有工业化甲醇合成反应器,其特点是在反应器入口处引入一个混合器,用以将原料气与超临界介质充分混合一同进入反应器。
超临界相合成甲醇工艺CO单程转化率达90%以上,原料气空速达4 000~8 000 h-1,甲醇时空产率可达1.2 Meoh/h,goat,因此,合成反应器的体积可大缩小,从而节省了投资和动力消耗。
3.结论
(1)从反应器本身来看,浆态床反应器比固定床反应器结构简单,造价便宜,易于操作、加压、放大以及提高生产能力。
但浆态床反应器涉及到气.液.固三相反应,其液相循环的辅助系统、操作过程中液相性质的改变以及由于三相所引起的更为复杂的问题.都是正在研究和必须解决的。
(2)国内合成甲醇最大装置规模为20万t/a,而国际上目前最大规模为170万t/a,装置大型化可大大降低能耗和生产成本,提高市场竞争力,因此必须发展大甲醇概念。
(3)甲醇合成反应器的反应原理的研究已很透彻,管壳型副产蒸汽反应器在我国均已有工业应用,我国甲醇合成催化剂已有多个得到工业应用的品牌可供选择,尤其是C302催化剂在国内20万t/a大型装置上已经受考验。
因而,研究大型甲醇合成塔已具备良好的工程技术基础。
(4)浆态床和超临界相工艺的甲醇合成反应器只有大型化才能体现出这两种工艺的优越性。
为了尽快实现其产业化,尚需国内的大型企业集团给予大力的支持,调动国内的科技力量,完善工艺,获取大型工业试验装置的数据,为我国天然气化工利用和甲醇工业开创一个新的领域。