精益生产的节拍时间
精益生产知识点

5.加工的Muda。
• Waiting • Manual Touches
6.等待的Muda。
7.搬运的Muda。
消除浪费 持续改善
Tenants of Single Piece Flow
Do Not Make Defects Do Not Pass Along Defects Do Not Accept Defects
Example: 我们正常工作时间为:=5days/week*8h/day*60m/h*60s/m=144000s/w 客户需求:=1000pcs/w 则:takt time=144000/1000=144s/pcs TT是TAKT Time,原本是由音槳上所引用過來的一個概念。 TAKT是德文,它的原意就是節拍的意思,是指在交響樂的演奏過程 中,要將整個樂團導向一個合諧、順暢的結果,變成一個Flow的呈現 。 所以在Lean的想法中,TAKT Time指的就是節拍時間,以客戶的需求 來趨動整個生產線的節奏,達到一個暢流式(Flow)生產的做法。 而最完美的境界是希望能達到One-Piece Flow (單件流)的工作方式。
系数)*(1+宽放),即生产节拍. 2) T.T根据是客户定单而定的节拍时间:T.T=每日的运转时间(定时)/客
户每日需求生产量(由生产计划分解),即客户需求节拍. 2.针对问题:周期时间可分为产品生产周期和单工位作业周期. 1)生产线的节拍时间为8S,周期时间是7+8+7=22S(产品生产周期). 2)生产线的节拍时间为8S,工位作业周期=工位标准工时. 3.了解C.T和T.T的意义在于: 1)当C.T>T.T时,说明生产无法满足客户需求.应进行改善(或加人),降低
精益生产培训之节拍时间
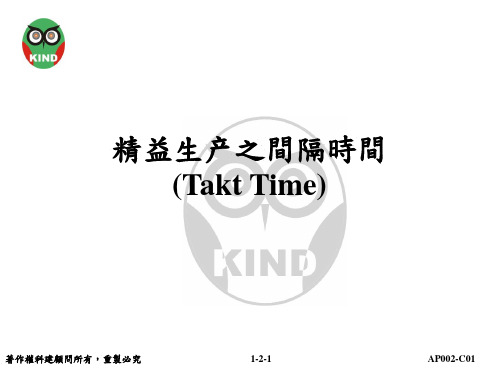
80units / h 1.78 45units / h
(取2个工作台,尚有生产能力剩余)
著作權科建顧問所有,重製必究
1-2-17
AP002-C01
案例分析
现对其进行精益化改造查: 1.铣、钻、磨床尚有剩余生产能力,因此在不影响其它生 产条件下,可进行适当调整。 2.所有装配线和包装依靠手工完成,只需提供工作台和工 具。 3。目前该生产单元按工艺专业化布置。因为加工次序和 优先级别不同,使生产很难达到应有的熟练程度,生产 拖拖沓沓,有时还需推迟交货时间,要么经常加班加点 才能完成任务。
著作權科建顧問所有,重製必究
1-2-7
AP002-C01
間隔時間的應用
A部門每天工作八小時並供應給B部門,一個月 工作25天,B部門一個月的需求數量為24,000個 產品,請問A部門的Takt Time為多少?
Takt Time = 8*25*60/24,000 = 0.5 分/個
著作權科建顧問所有,重製必究
問題四: 所需人員數 = 1.5/0.135 = 11.11≒12位
著作權科建顧問所有,重製必究
1-2-11
AP002-C01
結論
掌握間隔時間就是掌握生產線與產量, 進而達到最少庫存與最短交貨期。
著作權科建顧問所有,重製必究
1-2-12
AP002-C01
案例分析
某企业的生产车间接到任务,要生产一组产品,需要 经过铣、钻、磨、装配和打包等六道工序,每周生产 3200件,所有这些产品的加工过程相似,需要的工人 相同。该企业每周工作5天,每天工作8小时。
著作權科建顧問所有,重製必究
精益生产要素:节拍时间与拉动式排程
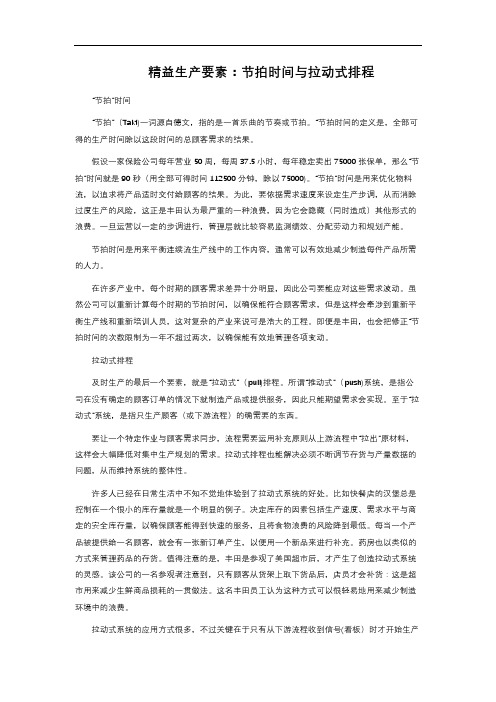
精益生产要素:节拍时间与拉动式排程“节拍”时间“节拍”(Takt)一词源自德文,指的是一首乐曲的节奏或节拍。
“节拍时间的定义是,全部可得的生产时间除以这段时间的总顾客需求的结果。
假设一家保险公司每年营业50周,每周37.5小时,每年稳定卖出75000张保单,那么“节拍”时间就是90秒(用全部可得时间112500分钟,除以75000)。
“节拍”时间是用来优化物料流,以追求将产品适时交付给顾客的结果。
为此,要依据需求速度来设定生产步调,从而消除过度生产的风险,这正是丰田认为最严重的一种浪费,因为它会隐藏(同时造成)其他形式的浪费。
一旦运营以一定的步调进行,管理层就比较容易监测绩效、分配劳动力和规划产能。
节拍时间是用来平衡连续流生产线中的工作内容,通常可以有效地减少制造每件产品所需的人力。
在许多产业中,每个时期的顾客需求差异十分明显,因此公司要能应对这些需求波动。
虽然公司可以重新计算每个时期的节拍时间,以确保能符合顾客需求,但是这样会牵涉到重新平衡生产线和重新培训人员,这对复杂的产业来说可是浩大的工程。
即便是丰田,也会把修正“节拍时间的次数限制为一年不超过两次,以确保能有效地管理各项变动。
拉动式排程及时生产的最后一个要素,就是“拉动式”(pull)排程。
所谓“推动式”(push)系统,是指公司在没有确定的顾客订单的情况下就制造产品或提供服务,因此只能期望需求会实现。
至于“拉动式”系统,是指只生产顾客(或下游流程)的确需要的东西。
要让一个特定作业与顾客需求同步,流程需要运用补充原则从上游流程中“拉出”原材料,这样会大幅降低对集中生产规划的需求。
拉动式排程也能解决必须不断调节存货与产量数据的问题,从而维持系统的整体性。
许多人已经在日常生活中不知不觉地体验到了拉动式系统的好处。
比如快餐店的汉堡总是控制在一个很小的库存量就是一个明显的例子。
决定库存的因素包括生产速度、需求水平与商定的安全库存量,以确保顾客能得到快速的服务,且将食物浪费的风险降到最低。
精益生产名词解释

精益生产名词解释内部时间、外部时间对于作业切换时间,细分为内部切换时间与外部切换时间,内部切换时间主要指的是必须停机切换,外部切换指的是非停机切换,尽量把内部切换转换为外部切换,以此提高设备的生产利用率。
常见的八大浪费在工厂中最为常见的浪费主要有八大类,分别是:不良、修理的浪费,过分加工的浪费,动作的浪费,搬运的浪费,库存的浪费,制造过多?过早的浪费,等待的浪费和管理的浪费。
下面具体分析各类浪费现象。
1.不良、修理的浪费所谓不良、修理的浪费,指的是由于工厂内出现不良品,需要进行处置的时间、人力、物力上的浪费,以及由此造成的相关损失。
这类浪费具体包括:材料的损失、不良品变成废品;设备、人员和工时的损失;额外的修复、鉴别、追加检查的损失;有时需要降价处理产品,或者由于耽误出货而导致工厂信誉的下降。
2.加工的浪费加工的浪费也叫过分加工的浪费,主要包含两层含义:第一是多余的加工和过分精确的加工,例如实际加工精度过高造成资源浪费;第二是需要多余的作业时间和辅助设备,还要增加生产用电、气压、油等能源的浪费,另外还增加了管理的工时。
3.动作的浪费动作的浪费现象在很多企业的生产线中都存在,常见的动作浪费主要有以下12种:两手空闲、单手空闲、作业动作突然停止、作业动作过大、左右手交换、步行过多、转身的角度太大,移动中变换“状态”、不明技巧、伸背动作、弯腰动作以及重复动作和不必要的动作等,这些动作的浪费造成了时间和体力上的不必要消耗。
4.搬运的浪费从JIT的角度来看,搬运是一种不产生附加价值的动作,而不产生价值的工作都属于浪费。
搬运的浪费具体表现为放置、堆积、移动、整列等动作浪费,由此而带来物品移动所需空间的浪费、时间的浪费和人力工具的占用等不良后果。
国内目前有不少企业管理者认为搬运是必要的,不是浪费。
因此,很多人对搬运浪费视而不见,更谈不上去消灭它。
也有一些企业利用传送带或机器搬运的方式来减少人工搬运,这种做法是花大钱来减少工人体力的消耗,实际上并没有排除搬运本身的浪费。
什么是精益生产

精益手册什么是精益生产通过消除企业所有不值活动,来达到降低成本、缩短生产周期和改善质量的目的。
区别精益生产方式与传统生产方式的区别主要表现为:改变了品质控制手段;消灭(减少)了各种缓冲区;增加了职工的参与感和责任感;培训职工并与职工交流;仅在需要的地方采用自动化;精益组织结构。
精益生产方式的主要特征表现为(1)品质——寻找、纠正和解决问题;(2)柔性——小批量、一个流;(3)投放市场时间——把开发时间减至最小;(4)产品多元化——缩短产品周期、减小规模效益影响;(5)效率——提高生产率、减少浪费;(6)适应性——标准尺寸总成、协调合作;(7)学习——不断改善。
精益生产的核心精益生产的核心是通过持续不断滴排除浪费来赢得利润、创造价值。
精益思想五个原则1. 价值——精确地确定特定产品的价值。
2. 价值流——识别出每种产品的价值流。
3. 流动——使价值不间断地流动。
4. 拉动——让用户从生产者方面拉动价值。
5. 尽善尽美——永远追求尽善尽美。
浪费什么是浪费浪费是指生产过程中用户不愿意支付的那部分企业活动。
浪费的种类1、生产过剩:是最坏的浪费,直接导致其他6种浪费。
是指生产出尚未有订单的产品,造成过早的占用资源,同时导致生产部均衡和各工序排队等待,生产周期长。
2、等待:因作业不平衡、安排作业不当、停工待料、品质不良、监看机器而造成的等待的浪费。
3、不必要的加工:加工质量或精度超过了客户的要求而造成的资源浪费,包括浪费了过多的工时、能源,增加了设备损耗,占用了作业空间等。
在制造过程中,为了达到作业的目的,有一些加工程序是可以省略、合并、重排或简化的。
4、搬运:长距离搬运在制品,缺乏效率的运输,进出仓库或在流程之间搬运原材料、零部件或最终成品5、库存过高:因为大量的库存会产生不必要的搬运、堆积、放置、防护、找寻等浪费,日常管理、领用、甚至盘点等也需要增加额外的时间。
既占用生产空间、浪费人力物力,又占用运营资金、损失管理费用。
精益生产之如何理解节拍时间

参考资料:精益六西格玛
在这个复杂多变的世界中,精益六西格玛就像是一把锐利的剑,帮助我们对抗着浪费的敌人,实 现生产力的最大化。它不仅仅是一种工具,更是一种理念,一种对未来的憧憬,一种持续改进的 精神。 让我们一起,用精益六西格玛的力量,去探索、去创新、去实现,让我们的企业走向更加美好的 未来!
谢谢观看
内容介绍
节拍时间是精益生产管理中一个很重要的概念,本文介绍理解使用节拍时间。
方法/步骤
1.节拍时间的涵义:
节拍时间是指生产按照客户要求,有 节奏地平稳地生产出产品,见下图。,见下图。
方法/步骤
3.什么是每班可用工作时间:
每班可用工作时间指:每班总时间休息时间-计划内非工作时间,单位 秒,见下图。
方法/步骤
7.实际计划时间:
由于换型,物料问题,质量问题等原 因,为保证实际产出满足需要,应在 计划时间里预留足够的时间以便应对 异常问题。
方法/步骤
8.如何设定生产节奏: 针对不同情况,设定相应的生产节奏。
参考资料:精益六西格玛
精益六西格玛(Lean Six Sigma,简称LSS)是一场优雅的探索,它以消除浪费为核心,将精益 生产和六西格玛管理融为一体。这个神秘的结合,其深度和广度足以让人惊叹。它的目标,不仅 仅在于提升效率、优化流程、减少浪费,更在于实现更高级别的管理效果,寻求一种更全面的、 更符合现代企业需求的解决方案。 精益六西格玛,并非简单地将精益生产与六西格玛管理拼凑在一起。它更像是一场深入灵魂的对 话,两种生产模式的优点在此交融,弥补了各自的不足。它们相互补充,像两位志同道合的战士, 共同对抗着生产中的种种困难和挑战。 这种有机结合的魅力,不仅仅在于它的高效和实用,更在于它的普遍适应性。无论你的企业规模 如何,无论你的产品类型如何,精益六西格玛都能为你提供一种切实可行的解决方案。
精益生产知识工时节拍
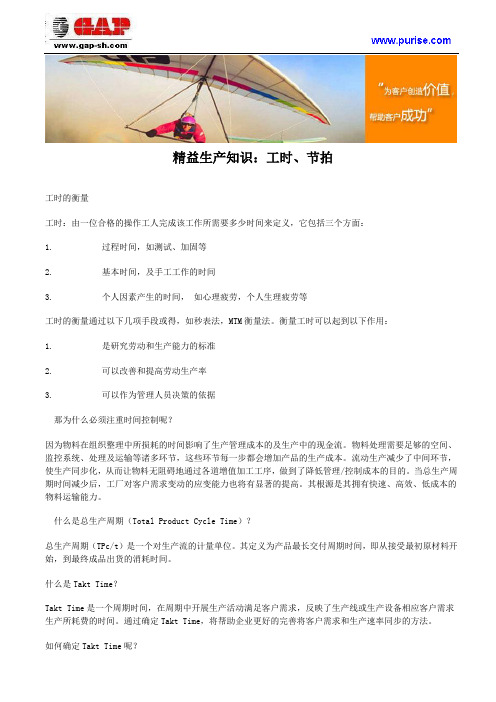
精益生产知识:工时、节拍工时的衡量工时:由一位合格的操作工人完成该工作所需要多少时间来定义,它包括三个方面:1. 过程时间,如测试、加固等2. 基本时间,及手工工作的时间3. 个人因素产生的时间,如心理疲劳,个人生理疲劳等工时的衡量通过以下几项手段或得,如秒表法,MTM衡量法。
衡量工时可以起到以下作用:1. 是研究劳动和生产能力的标准2. 可以改善和提高劳动生产率3. 可以作为管理人员决策的依据那为什么必须注重时间控制呢?因为物料在组织整理中所损耗的时间影响了生产管理成本的及生产中的现金流。
物料处理需要足够的空间、监控系统、处理及运输等诸多环节,这些环节每一步都会增加产品的生产成本。
流动生产减少了中间环节,使生产同步化,从而让物料无阻碍地通过各道增值加工工序,做到了降低管理/控制成本的目的。
当总生产周期时间减少后,工厂对客户需求变动的应变能力也将有显著的提高。
其根源是其拥有快速、高效、低成本的物料运输能力。
什么是总生产周期(Total Product Cycle Time)?总生产周期(TPc/t)是一个对生产流的计量单位。
其定义为产品最长交付周期时间,即从接受最初原材料开始,到最终成品出货的消耗时间。
什么是Takt Time?Takt Time是一个周期时间,在周期中开展生产活动满足客户需求,反映了生产线或生产设备相应客户需求生产所耗费的时间。
通过确定Takt Time,将帮助企业更好的完善将客户需求和生产速率同步的方法。
如何确定Takt Time呢?1. 确定满足客户总需求所涉及到的工艺流程。
仔细认证准确的需求信息,同时考虑批量的增减情况。
如在同一设备上生产进行多样化生产,则这种复合需求也应计算在Takt Time之内。
生产能力计划需于需求量的层次相适应,将生产层次于设备设计产能挂钩。
产能水平以精细产能率(Lean Capacity Rate),最大产能(Max Capacity)和弹性产能率(Flex Capacity Rate)表示。
精益生产各KPI计算公式汇总
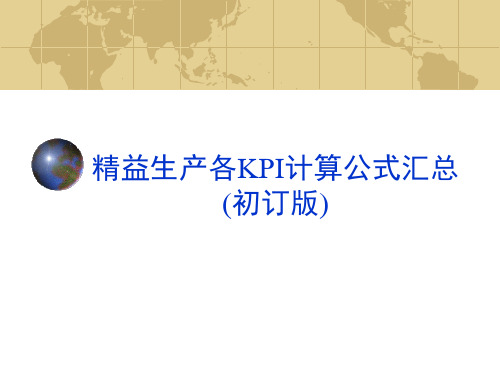
注:總片數=每日目標X每雙片數
面部,半成品&底部的合格率:以半双計算
合格率= 半雙總數-(不合格品+反修品)
半雙的總數
不良品率计算方式:
1 – 合格率 = 不良品率
FTT ---First Time Through 直通率
定义:衡量在第一時間里生產出不用反修的無瑕疵产品的能力。
核心价值流FTT: = 合格率 (裁断)X 合格率(半成品)X 合格率(周边)
依计划尺码实际生產=5+30+50=85,实际生产尺码数量=95 SIZE達成率= 85/95 =0.89
BTS准交率 =(数量达成率)X(SIZE达成率) 数量达成率=0.95 SIZE达成率=0.89
BTS = 0.95 x 0.89 = 0.85 = 85%
LT---Lead time 交期时间
TT---Takt Time節拍時間
定义:也称产距时间,指能满足客户需求的每双制造速度
每月客戶需求 = 每日需求产量 工作日天數
TT节拍时间=
实际工作时间 每日需求产量
举例:某成型线一天目标产量2000双,工作时间8小时, 那么其工序的节拍时间为:
8小时*60分*60秒
2000双
= 14.4 (秒/双)
生产计划 #9
#10