单双螺杆挤出机差别
挤出机单螺杆与双螺杆(精)

挤出机单螺杆与双螺杆挤出机按其螺杆数量可以分为单螺杆、双螺杆和多螺杆挤出机。
目前以单螺杆挤出机应用最为广泛, 适宜于一般材料的挤出加工。
双螺杆挤出机由于具有由摩擦产生的热量较少、物料所受到的剪切比较均匀、螺杆的输送能力较大、挤出量比较稳定、物料在机筒内停留长 , 混合均匀。
SJSZ 系列锥形双螺杆挤出机具有强制挤出、高质量、适应性广、寿命长、剪切速率小、物料不易分解、混炼塑化性能好、粉料直接成型等特点,温度自控,真空排气等装臵。
适用于管、板、异形材等制品的生产。
2001年兰泰塑料机械有限公司开发出高扭矩型 SHJ-92同向双螺杆配混挤出造粒机组,并出口印度尼西亚,产量达 1100公斤 /小时, 355kw, 螺杆转速达 500r/min,在国内机型配臵和性能最高。
在国内率先研制成功双流道液压换网系统, 实现了真正的不停车换网。
混炼转子型螺杆元件等新型元件研制成功并且应用。
单螺杆挤出机无论作为塑化造粒机械还是成型加工机械都占有重要地位, 近几年, 单螺杆挤出机有了很大的发展。
目前德国生产的大型造粒用单螺杆挤出机,螺杆直径达 700mm ,产量为 36t/h。
单螺杆挤出机发展的主要标志在于其关键零件——螺杆的发展。
近几年以来, 人们对螺杆进行了大量的理论和实验研究, 至今已有近百种螺杆,常见的有分离型、剪切型、屏障型、分流型与波状型等。
从单螺杆发展来看, 尽管近年来单螺杆挤出机已较为完善, 但随着高分子材料和塑料制品不断的发展, 还会涌现出更有特点的新型螺杆和特殊单螺杆挤出机。
从总体而言, 单螺杆挤出机向着高速、高效、专用化方向发展。
双螺杆挤出机喂料特性好, 适用于粉料加工, 且比单螺杆挤出机有更好的混炼、排气、反应和自洁功能, 特点是加工热稳定性差的塑料和共混料时更显示出其优越性。
近些年来国外双螺杆挤出机已经有很大的发展, 各种形式的双螺杆挤出机已系列化和商品化, 生产的厂商也较多,大致分类如下:(1按两根轴线相对位臵,有平行和锥形之分;(2按两根螺杆啮合程序,有啮合型和非啮合型之分;(3按两根螺杆的旋转方向, 有同向和异向之分, 在异向中又有向内、向外之分;(4按螺杆旋转速度,有高速和低速之分;(5按螺杆与机筒的结构,有整体和组合之分。
单螺杆挤出机与双螺杆挤出机性能对比分析报告

单螺杆挤出机与双螺杆挤出机性能对比分析报告1. 引言挤出机是一种广泛应用于塑料加工行业的设备,用于将固态塑料熔化并挤出成型,常见的挤出机包括单螺杆挤出机与双螺杆挤出机。
本报告旨在对这两种挤出机的性能进行对比分析,以便用户在选择设备时能够做出合适的决策。
2. 工作原理2.1 单螺杆挤出机工作原理单螺杆挤出机通过一个旋转的螺杆将塑料料柱推向机筒的另一端,同时螺杆沿着机筒的轴向旋转将料柱加热熔融。
最后,在挤出口处,通过模具将熔融的塑料成型为所需的形状。
2.2 双螺杆挤出机工作原理双螺杆挤出机与单螺杆挤出机相似,不同之处在于它使用两个同向旋转的螺杆来完成料柱的加热和推送。
这种设计可以有效提高挤出机的生产能力和混炼效果。
3. 性能对比分析3.1 生产能力单螺杆挤出机由于只有一个螺杆进行推送,因此其生产能力相对较低。
双螺杆挤出机由于采用双螺杆推送,其生产能力通常比单螺杆挤出机高出许多。
因此,在对生产效率有较高要求的情况下,双螺杆挤出机更适合使用。
3.2 混炼效果双螺杆挤出机在料柱的推送过程中,通过两个螺杆的共同作用,能够更好地将料柱翻滚、推拉和折叠,从而提高混炼效果。
而单螺杆挤出机的混炼效果相对较差。
因此,对于要求较高的塑料熔融均匀性的情况,建议选择双螺杆挤出机。
3.3 适用范围由于单螺杆挤出机结构相对简单,维护较为便捷,因此在一些小型塑料加工企业中应用较多。
而双螺杆挤出机由于其较高的生产能力和混炼效果,更适用于大型生产线和对产品质量要求较高的企业。
3.4 成本考虑在经济成本方面,双螺杆挤出机的价格通常高于单螺杆挤出机,且对于维护和操作要求较高。
因此,在预算有限的情况下,单螺杆挤出机可能更适合一些小型企业。
4. 结论本报告对单螺杆挤出机与双螺杆挤出机的性能进行了对比分析。
根据实际需求,用户可以根据生产能力、混炼效果、适用范围和成本考虑等因素,选择适合自己的挤出机。
单螺杆挤出机适用于对生产能力和混炼效果要求较低的场合,而双螺杆挤出机则适用于对这两方面要求较高的场合。
单螺杆双螺杆挤出机基本原理的区别
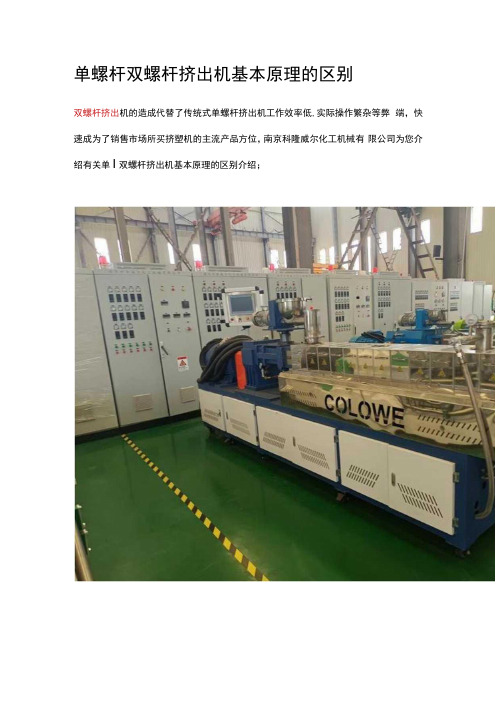
单螺杆双螺杆挤出机基本原理的区别
双螺杆挤出机的造成代替了传统式单螺杆挤出机工作效率低,实际操作繁杂等弊端,快速成为了销售市场所买挤塑机的主流产品方位,南京科隆威尔化工机械有限公司为您介绍有关单I双螺杆挤出机基本原理的区别介绍;
与单螺杆挤出环节相近,双螺杆挤出环节也分为投料和固态运输、熔化及溶体运输三个阶段。
但双螺杆挤出机的基本原理与单螺杆挤出机完全不一样。
区别一:双螺杆挤出机为正方向运输,强制性将原材料引向前行。
区别二:双螺杆挤出机在两根挤出机螺杆的齿合处对原材料造成明显裁切功效,提升原材料的混和与熔融实际效果。
可以看出,单螺杆挤出机合适塑料粒子生产加工,应用的原材料是经制粒后的颗粒物或经破碎的颗粒饲料。
双螺杆挤出机合适颗粒料生产加工,能直接应用混和好的PVC料,减少了制粒的工序,但多了废料的磨粉工序。
例如,当挤出机螺杆同向旋转时,一根挤出机螺杆的螺齿像楔子一样伸入到另一挤出机螺杆的螺糟中,原材料基本不能由该螺槽继续进入到邻近的螺槽中去,而只能被迫地由一根挤出机螺杆的锯槽流到另一根挤出机螺杆的螺槽中去。
这样原材料在两根挤出机螺杆之间反复强迫转向,受到了良好的裁切混和功效。
如果挤出机螺杆是反向旋转的厕原材料必然要经过夹口 ,原材料好像通过两馄的馄隙,所以裁切实际效果会更好。
双螺杆挤出机与单螺杆挤出机的区别
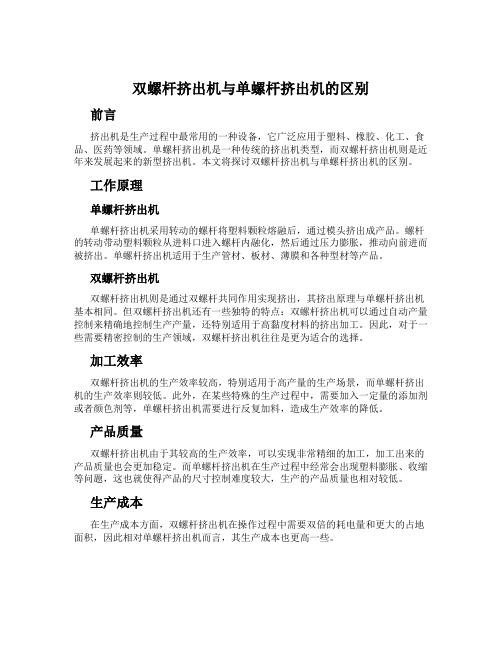
双螺杆挤出机与单螺杆挤出机的区别前言挤出机是生产过程中最常用的一种设备,它广泛应用于塑料、橡胶、化工、食品、医药等领域。
单螺杆挤出机是一种传统的挤出机类型,而双螺杆挤出机则是近年来发展起来的新型挤出机。
本文将探讨双螺杆挤出机与单螺杆挤出机的区别。
工作原理单螺杆挤出机单螺杆挤出机采用转动的螺杆将塑料颗粒熔融后,通过模头挤出成产品。
螺杆的转动带动塑料颗粒从进料口进入螺杆内融化,然后通过压力膨胀,推动向前进而被挤出。
单螺杆挤出机适用于生产管材、板材、薄膜和各种型材等产品。
双螺杆挤出机双螺杆挤出机则是通过双螺杆共同作用实现挤出,其挤出原理与单螺杆挤出机基本相同。
但双螺杆挤出机还有一些独特的特点:双螺杆挤出机可以通过自动产量控制来精确地控制生产产量,还特别适用于高黏度材料的挤出加工。
因此,对于一些需要精密控制的生产领域,双螺杆挤出机往往是更为适合的选择。
加工效率双螺杆挤出机的生产效率较高,特别适用于高产量的生产场景,而单螺杆挤出机的生产效率则较低。
此外,在某些特殊的生产过程中,需要加入一定量的添加剂或者颜色剂等,单螺杆挤出机需要进行反复加料,造成生产效率的降低。
产品质量双螺杆挤出机由于其较高的生产效率,可以实现非常精细的加工,加工出来的产品质量也会更加稳定。
而单螺杆挤出机在生产过程中经常会出现塑料膨胀、收缩等问题,这也就使得产品的尺寸控制难度较大,生产的产品质量也相对较低。
生产成本在生产成本方面,双螺杆挤出机在操作过程中需要双倍的耗电量和更大的占地面积,因此相对单螺杆挤出机而言,其生产成本也更高一些。
总结总体而言,双螺杆挤出机与单螺杆挤出机各有优劣。
单螺杆挤出机广泛应用于各种常规型材和中小型生产场景,而双螺杆挤出机则广泛用于运输、管道、板材、薄膜等较高要求的生产领域。
我们应在选择机器时结合生产需求进行权衡选择,以实现最优的生产效益。
双螺杆挤出机和单螺杆挤出机的优势区别
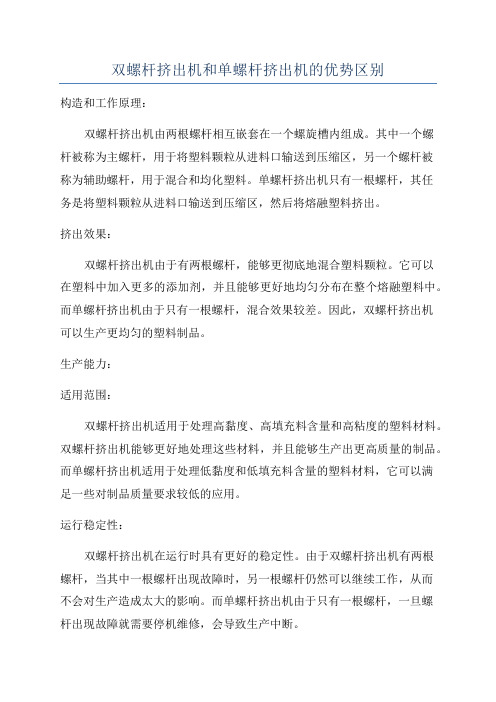
双螺杆挤出机和单螺杆挤出机的优势区别
构造和工作原理:
双螺杆挤出机由两根螺杆相互嵌套在一个螺旋槽内组成。
其中一个螺
杆被称为主螺杆,用于将塑料颗粒从进料口输送到压缩区,另一个螺杆被
称为辅助螺杆,用于混合和均化塑料。
单螺杆挤出机只有一根螺杆,其任
务是将塑料颗粒从进料口输送到压缩区,然后将熔融塑料挤出。
挤出效果:
双螺杆挤出机由于有两根螺杆,能够更彻底地混合塑料颗粒。
它可以
在塑料中加入更多的添加剂,并且能够更好地均匀分布在整个熔融塑料中。
而单螺杆挤出机由于只有一根螺杆,混合效果较差。
因此,双螺杆挤出机
可以生产更均匀的塑料制品。
生产能力:
适用范围:
双螺杆挤出机适用于处理高黏度、高填充料含量和高粘度的塑料材料。
双螺杆挤出机能够更好地处理这些材料,并且能够生产出更高质量的制品。
而单螺杆挤出机适用于处理低黏度和低填充料含量的塑料材料,它可以满
足一些对制品质量要求较低的应用。
运行稳定性:
双螺杆挤出机在运行时具有更好的稳定性。
由于双螺杆挤出机有两根
螺杆,当其中一根螺杆出现故障时,另一根螺杆仍然可以继续工作,从而
不会对生产造成太大的影响。
而单螺杆挤出机由于只有一根螺杆,一旦螺
杆出现故障就需要停机维修,会导致生产中断。
综上所述,双螺杆挤出机相对于单螺杆挤出机具有更好的混合效果、更高的生产能力、更适应处理高黏度塑料以及更好的稳定性。
但是,双螺杆挤出机的成本相对较高,对设备和操作人员的要求也较高。
因此,在选择挤出机时,需要根据实际需要综合考虑各种因素。
单螺杆挤出机与双螺杆挤出机性能对比分析报告

单螺杆挤出机与双螺杆挤出机性能状况分析报告一. 塑料挤出机概述1. 常规单螺杆挤出机现状和技术水平分析在常规单螺杆挤出机的性能方面,我国己能生产螺杆直径为φ12-φ250mm多种规格、门类齐全的挤出机,长径比大多在25-30范围。
一些新型的混炼元件如分离型、屏障型、分流型、变流道型以及流束位置变换型等混炼元件得到了较为广泛的应用:螺杆最高转速:直径φ150-φ200的大型挤出机加工烯烃类物料时为50-75r/min,加工PVC等热敏性物料时为5-42r/min:直径φ30以下的小型机器加工烯烃类物料时为l60-200r/min,加工PVC等热敏性物料时为18-l20r/min:北京化工大学研制成功的φl2mm手提式单螺杆排气挤出机为1200r/min。
而国外单螺杆挤出机螺杆直径最小φ6mm,最大为φ700mm,最大长径比达60。
日本池贝公司φ30单螺杆挤出机最高螺杆转速为300r/min,挤出机300kg/h,远远高于我国同规格机器实际产量l4kg/h的水平。
由于常规单螺杆挤出机与其它挤出机相比,具有结构简单、坚固耐用、维修方便、价格低廉、操作容易等特点。
在我国相当长时间内仍有很大市场,因此如何使常规单螺杆挤出机优质、高效、多功能化,仍然是我国塑机研究工作者的艰巨任务。
2.异向旋转双螺杆挤出成型机的现状与技术水平分析2.1 异向旋转平行双螺杆挤出机异向旋转双螺杆挤出机有许多种类型,可分为平行和锥形两大类,前者两根螺杆的轴线互相平行,后者两根螺杆的轴线相交成一角度。
目前流行的平行异向双螺杆挤出机多为在啮合区纵横向都封闭,即共轭型的。
锥形双螺杆挤出机与啮合型平行异向双螺杆挤出机的工作机理基本相同。
如果将其设计成啮合区螺槽纵横向皆封闭的,则其输送能力和建压能力都很强,因其加料端两螺杆轴线间有较大的空间,可以采用大的止推轴承和扭矩分配齿轮,从而能承受高扭矩和高推力负荷,很适合硬聚氯乙烯类制品的挤出成型。
橡胶挤出机:橡胶挤出机的分类介绍
橡胶挤出机:橡胶挤出机的分类介绍
橡胶挤出机是一种常见的工业生产设备,用于将橡胶原料通过挤压的方式制成
条状或异型的橡胶制品。
根据不同的挤出原理和挤出机构,橡胶挤出机可以分为多种不同类型。
本文将对橡胶挤出机的分类进行介绍。
1. 单螺杆橡胶挤出机
单螺杆橡胶挤出机是一种最常见的橡胶挤出机。
它采用单个螺杆将橡胶原料从
进料口推向挤出头部,通过机器内部的压力和温度控制,将橡胶原料挤压成条状或异型的橡胶制品。
该挤出机结构简单,易于维护和操作,成本相对较低,适用于中小型企业的生产。
2. 双螺杆橡胶挤出机
双螺杆橡胶挤出机采用两个相互旋转的螺杆来推动橡胶原料挤压出来。
相比于
单螺杆挤出机,双螺杆挤出机可以更加均匀地混合原料,并获得更高的生产效率。
双螺杆挤出机结构更加复杂,需要更高的技术水平和成本投入,适用于大型企业或高端橡胶制品生产。
3. 螺杆式橡胶挤出机
螺杆式橡胶挤出机采用横向旋转的螺杆来将橡胶原料压制出来。
该挤出机由于
螺杆的旋转方向与单螺杆和双螺杆挤出机不同,导致其产生的切应力比较大,可以使橡胶原料更加充分的混合,且制品成型效果更加平滑。
螺杆式挤出机适用于复杂形状的橡胶制品生产,并且由于不需要加装混炼机构,整个生产线较为简单,成本相对较低。
总的来说,橡胶挤出机的分类大致可以分为单螺杆、双螺杆和螺杆式三个类型。
不同类型的挤出机适用于不同的橡胶制品生产,企业在选择挤出机时应根据自己的实际需要和经济情况进行选择。
单-双螺杆的差别
双螺杆挤压机生产特种饲料的优势◇武汉工业学院机械工程系李诗龙◇近二十多年以来,双螺杆挤压机已经被广泛用于食品加工业,他们不仅用于谷物食品的加工,而且也越来越多地用于糖果糕点类产品乃至香料等产品的加工。
随着双螺杆挤压机应用领域的拓广,双螺杆挤压机也开始用于宠物饲料、水产饲料、特种经济动物饲料和幼畜哺乳期饲料等特种饲料的生产。
然而,我国现有的饲料加工仍以单螺杆膨化挤压机为主,尽管双螺杆挤压机在饲料加工业有一些应用,但和食品加工业相比则要逊色得多。
为了适应我国饲料工业发展的需要,很有必要重视双螺杆挤压技术在饲料加工中的应用。
◇为什么加工特种饲料要采用双螺杆挤压机而不是价格便宜的单螺杆挤压机呢?为此本文将介绍双螺杆挤压机的工作特性,供新建、扩建和改建企业在拟定设计方案和生产实践上,用作实用的技术参考。
◇ 1 单螺杆挤压机◇单螺杆挤压机优于双螺杆挤压机最主要的一点是其结构简单,价格便宜,因此在食品工业领域有着广泛地应用,只有当单螺杆挤压机在生产中不能得到完全令人满意的效果时,才改用双螺杆挤压机。
◇单螺杆挤压机主要是靠拖曳流来完成输送的装臵。
物料只有粘附在筒壁上才能向前输送,摩擦力越大,则泵送效率越高。
若物料粘附在螺杆上,则不能向前输送。
这就限制了单螺杆挤压机对低粘性原料尤其是高含油脂原料的加工。
单螺杆挤压机的这种输送方式对于高压也很敏感。
压力将产生回流,降低输送效率。
由于输送量等于拖曳流减去压力流,所以高压常会引起总产量的降低。
◇在单螺杆挤压机中,大部分能量在机筒上传导。
这些能量既有通过机筒外热的传导,也有由于螺杆本身的剪切作用所产生的机械能。
其中机械能的大小是由螺杆转速和螺杆结构所决定的,这是因为剪切率与螺杆转速成正比,而对于一台确定的挤压机,螺杆结构一般是预先确定的,修改的可能性很小。
对于大型单螺杆挤压机,热交换及其输送产量和压力的增加都将变得更加困难,因为挤压机的尺寸越大,物料的表面积与体积之比就越小。
单双螺杆挤出机结构特点和工作原理的差异
单双螺杆挤出机结构特点和工作原理的差异单螺杆挤出机和双螺杆挤出机是塑料挤出机中常用的两种类型,它们在结构特点和工作原理方面存在一些差异。
下面将对这两种挤出机进行详细介绍。
一、单螺杆挤出机1.结构特点:单螺杆挤出机只有一个螺杆,在筒体内旋转,将原料推进到机头,通过模具进行挤出。
其结构简单,造价较低。
单螺杆挤出机主要有筒体、螺杆、传动系统和加热系统等部分组成。
2.工作原理:单螺杆挤出机的工作原理是通过螺杆的旋转将原料送入机头,然后通过模具挤出成型。
具体工作流程如下:(1)加料:将塑料颗粒等原料投入到进料斗,由重力自动进入挤出机的进料区。
(2)熔融:原料随着螺杆的旋转进入加热区,在高温下受热熔化。
(3)压力增加:随着螺杆的旋转,原料被推进到机头,同时通过螺杆的螺纹使原料受到压力增加,实现均匀的挤出。
(4)挤出成型:原料在机头通过模具进行挤出成型,形成所需的产品形状。
二、双螺杆挤出机1.结构特点:双螺杆挤出机有两个同心旋转的螺杆,在挤出过程中的加工效果更好,适用于更多复杂的产品加工。
双螺杆挤出机的结构相对复杂,由筒体、螺杆、传动系统和加热系统等多个部分组成。
2.工作原理:双螺杆挤出机的工作原理主要是通过两个同心旋转的螺杆将原料进行挤压。
具体工作流程如下:(1)加料:将原料投入到进料斗,由重力自动进入挤出机的进料区,同时通过螺杆的螺纹将原料向前推进。
(2)熔融:原料在两个螺杆的作用下受到高温加热,快速熔化。
(3)压力和剪切:螺杆的旋转使得原料在其螺纹间经历高压力和高剪切力,从而使得原料更加均匀地混合。
(4)挤出成型:原料在挤出机的机头通过模具进行挤出成型,形成所需的产品形状。
总结起来,单螺杆挤出机相对简单,适用于一些简单的挤出加工;而双螺杆挤出机结构相对复杂,适用于需要更好的加工效果和更复杂形状的产品加工。
双螺杆挤出机设备有哪些优点呢
双螺杆挤出机设备有哪些优点呢双螺杆挤出机是一种常用的塑料加工机械。
它可以通过挤出加工将固体塑料变为流动的塑料熔体,并通过模具成型。
相比于传统的单螺杆挤出机,双螺杆挤出机具有更多的优点。
本文将会就双螺杆挤出机设备的这些优点进行详细探讨。
1. 更好的混合性能因为双螺杆挤出机有两个螺杆,所以它比单螺杆挤出机可以更好地实现材料的混合和分散,这也是它常用于制造复合材料的原因之一。
每个螺杆有不同的功能,以便更好地混合不同类型的材料,例如粘性高的聚合物和相对松散的填充物。
2. 更高的生产效率双螺杆挤出机相对于单螺杆挤出机来说,挤出速度更快,且能够完成在同一时间内更多的工作量。
这意味着生产能力更高,生产效率更高,生产成本也因此降低。
另外,在生产非圆形截面的管道和异型材料时,双螺杆挤出机可以更好地满足生产需求。
3. 更好的温度控制由于塑料在加热过程中容易变形,温度控制非常重要。
在双螺杆挤出机中,由于引入了更多的热源,可以更好地进行加热和冷却控制,确保塑料成型质量更加稳定。
4. 更低的能耗双螺杆挤出机因其更高的生产效率和更好的混合性能,可以更快地完成生产过程,因此更节能。
在同样的生产任务下,双螺杆挤出机的能耗要比单螺杆挤出机要低,而能源消耗的降低也可以带来更低的生产成本。
5. 可适应更广泛的塑料材料双螺杆挤出机通过不同的螺杆设计、旋转速度和其他参数,可以适应不同的熔体黏度、粘度和分布,因此,适用于不同种类的塑料加工。
包括但不仅限于PP、PE、ABS、PC、PMMA、PA、POM等等常用的塑料。
这样,生产方面的灵活性更高,成本更低。
综上所述,双螺杆挤出机的优点主要体现在更好的混合性能、更佳的生产效率、更好的温度控制、更低的能耗以及对多种塑料材料的适应性。
同时,为了保证生产成品质量,我们还需要做好设备的日常维护、保养和注意安全。
- 1、下载文档前请自行甄别文档内容的完整性,平台不提供额外的编辑、内容补充、找答案等附加服务。
- 2、"仅部分预览"的文档,不可在线预览部分如存在完整性等问题,可反馈申请退款(可完整预览的文档不适用该条件!)。
- 3、如文档侵犯您的权益,请联系客服反馈,我们会尽快为您处理(人工客服工作时间:9:00-18:30)。
单、双螺杆挤出机结构特点和工作原理的差异挤出成型工艺是聚合物加工领域中生产品种最多、变化最多、生产率高、适应性强、用途广泛、产量所占比重最大的成型加工方法。
挤出成型是使高聚物的熔体(或粘性流体)在挤出机螺杆的挤压作用下通过一定外形的口模成型,制品为具有恒定断面外形的连续型材。
挤出成型工艺适合于所有的高分子材料。
几乎能成型所有的热塑性塑料,也可用于热固性塑料,但仅限于酚醛等少数几种热固性塑料。
塑料挤出的制品有管材、板材、棒材、片材、薄膜、单丝、线缆包覆层、各种异型材以及塑料与其它材料的复合物等。
目前约50%的热塑性塑料制品是通过挤出成型的。
此外挤出工艺也常用于塑料的着色、混炼、塑化、造粒及塑料的共混改性等,以挤出成型为基础,配合吹胀、拉伸等技术,又发展为挤出一吹塑成型和挤出拉幅成型制造中空吹塑和双轴拉伸薄膜等制品。
可见挤出成型是聚合物成型中最重要的方法。
挤出设备有螺杆挤出机和柱塞式挤出机两大类,前者为连续式挤出,后者为间歇式挤出,主要用于高粘度的物料成型,如聚四氟乙烯、超高分子量聚乙烯。
螺杆挤出机可分为单螺杆挤出机和多螺杆挤出机。
单螺杆挤出机是生产上最基本的挤出机。
多螺杆挤出机中双螺杆挤出机近年来发展最快,其应用日渐广泛。
目前,在PVC塑料门窗型材的加工中,双螺杆挤出机已成为主要生产设备,单螺杆挤出机将被逐步淘汰。
但在其它聚合物的挤出加工中,单螺杆挤出机仍占主导地位。
二者有各自的特点:单螺杆挤出机:●结构简单,价格低。
●适合聚合物的塑化挤出,适合颗粒料的挤出加工。
对聚合物的剪切降解小,但物料在挤出机中停留时间长。
●操纵轻易,工艺控制简单。
双螺杆挤出机:●结构复杂,价格高。
●具有很好的混炼塑化能力,物料在挤出机中停留时间短,适合粉料加工。
●产量大,挤出速度快,单位产量耗能低。
在PVC塑料门窗型材生产中,采用双螺杆挤出机与单螺杆挤出机的生产工艺为见页下):可以看出,单螺杆挤出机适合粒料加工,使用的原料是经造粒后的颗粒或经粉碎的颗粒料。
双螺杆挤出机适合粉料加工,可以直接使用混合好的PVC料,减少了造粒的工序,但多了废物的磨粉工序。
近几年,国产双螺杆挤出机的质量已基本达到进口双螺杆挤出机的水平,价格仅为进口机的1/3~1/5。
由于双螺杆挤出机的产量大,挤出速度快,一般可达到2~4米/分钟,适合PVC塑料门窗型材的大规模生产。
而单螺杆挤出机一般只用作小型辅助型材生产,挤出速度仅为1~2米/分钟,很多的PVC型材加工厂已淘汰了单螺杆挤出机,改用双螺杆挤出机一模多腔生产小型辅助型材。
挤出机的基本工作原理是将聚合物熔化压实,以恒压、恒温、恒速推向模具,通过模具形成产品熔融状态的型坯。
但单螺杆挤出机与双螺杆挤出机结构不同,工作原理不同,其控制的工艺条件也不相同。
单螺杆挤出机结构特点单螺杆挤出机是由传动系统、挤出系统、加热和冷却系统、控制系统等几部分组成(另外还有一些辅助设备)。
其中挤出系统是挤出成型的关键部位,对挤出的成型质量和产量起重要作用。
挤出系统主要包括加料装置、料筒、螺杆、机头和口模等几个部分(如图3所示)。
下面仅就挤出系统讨论挤出机的基本结构及作用。
PVC树脂+—→称量计量—→高速混合—→冷却混合—→双螺杆挤出机挤出—→冷却定型—→各种助剂↓↑单螺杆挤出机造粒—→单螺杆挤出机挤出—┘—→牵引—→切割—→包装—→型材产品↓废物—→粉碎—→与造粒料混合单螺杆挤出机挤出↓磨粉—→与混合的粉料混合双螺杆挤出机挤出1、加料装置挤出成型的供料一般采用粒状料。
加料装置是保证向挤出机料筒连续供料的装置,外形如漏斗,有圆锥形和方锥形,亦称料斗。
其底部与料筒连接处是加料孔,该处有截断装置,可以调整和截断料流。
在加料孔的四周有冷却夹套,用以防止料筒高温向料斗传热,避免料斗内塑料升温发粘,引起加料不均和料流受阻情况发生。
料斗的侧面有玻璃视孔及标定计量装置。
有些料斗还有防止塑料从空气中吸收水分的预热干燥真空减压装置,以及带有能克服粉状塑料产生“架桥”现象的搅拌器和能够定时定量自动加料的装置。
2、料筒料筒又叫机筒,是一个受热受压的金属圆筒。
物料的塑化和压缩都是在料筒中进行的。
挤出成型时的工作温度一般在180~290℃,料筒内压可达60MPa。
在料筒的外面设有加热和冷却装置。
加热一般分三至四段,常用电阻或电感加热器,也有采用远红外线加热的。
冷却的目的是防止塑料的过热或停车时须对塑料快速冷却以免塑料的降解。
冷却一般用风冷或水冷。
料筒须承受高压,要求具有足够的强度和刚度,内壁光滑。
料筒一般用耐磨、耐腐塑料摩擦使塑料过热,同时让螺杆表面温度略低于料筒,防止物料粘附其上,利于物料的输送。
螺杆用止推轴承悬支在料筒的中心,与料筒中心线吻合,不应有明显的偏差。
螺杆与料筒的间隙很小,使塑料受到强大的剪切作用而塑化并推动向前。
螺杆由电动机通过减速机构传动,转速一般为10~120r/min,要求是无级变速。
(1)螺杆的几何结构参数螺杆的几何结构参数有直径、长径比、压缩比、螺槽深度、螺旋角、螺杆与料筒的间隙等(见图4)其中长径比(L/Ds)对螺杆的工作特性有重大的影响。
一般挤出机长径比为15~25,但近年来发展的挤出机有达40的,甚至更大。
L/Ds大,能改善塑料的温度分布,能使混合更均匀,还可减少挤出时的逆流和漏流,进步挤出机的生产能力。
L/Ds过小,对塑料的混合和塑化都不利。
因此,对于硬塑料、粉状塑料要求塑化时间长,应选较大的。
L/Ds大的螺杆适应性强,可用于多种塑料的挤出。
但L/Ds太大,热敏性塑料会因受热时间太长而出现分解,同时增加螺杆的自重,使制造和安装都困难,也会增大挤出机的功率消耗。
目前,L/Ds以25居多。
(2)螺杆的压缩比ε螺杆的压缩比ε是指螺杆加料段第一个螺槽的容积与均化段最后一个螺槽的容积之比,它表示塑料通过螺杆的全过程被压缩的程度。
ε越大,塑料受到挤压的作用也就越大,排除物料中空气的能力就大。
但ε太大,螺杆本身的机械强度下降。
一般压缩比ε在2~5之间。
压缩比ε的大小取决于挤出塑料的种类和形态,如粉状塑料的相对密度小,夹带空气多,其压缩比应大于粒状塑料。
另外挤出薄壁状制品时,压缩比ε应比挤出厚壁制品的大。
(3)螺槽深度H螺槽深度影响塑料的塑化及挤出效率,H较小时,对塑料可产生较高的剪切速率,有利于传热和塑化,但挤出生产率降低。
因此,热敏性塑料宜用。
H大的深槽螺杆宜用熔体粘度低和热稳定性较高的塑料。
在实际生产中,根据工艺需要,螺槽深度往往是变化的,根据螺杆各段的功能不同,螺槽的深度不同,最通用的是渐变螺杆,如:加料段的螺槽深度Hl是个定值,一般H1>0.1Ds;压缩段的螺槽深H2是渐变的,是一个变化值;均化段的螺槽深H3是个定值,按经验H3=0.02~0.06Ds。
螺旋角θ是螺纹与螺杆横截面之间的夹角,随着θ的增大,挤出机的生产能力进步,但螺杆对塑料的挤压剪切作用减少。
出于机械加工的方便,取Ds=Ls,则θ为17.26。
为最常用的螺杆。
(4)螺杆与料筒的间隙δ螺杆与料筒的间隙δ,其大小影响挤出机的生产能力和物料的塑化。
δ值大,热传导差,剪切速率低,不利于物料的熔融和混合,生产效率也不会高。
但δ小时,热传导和剪切率都相应进步。
但δ过于小,就易引起物料降解。
单螺杆挤出机挤出过程和螺杆各段的功能由高分子物理学知道,高聚物存在三种物理状态,即玻璃态、高弹态和粘流态,在一定条件下,这三种物理状态会发生互变。
固态塑料由料斗进人料筒后,随着螺杆的旋转向机头方向前进,在此过程中,塑料的物理状态在不断发生着变化。
根据塑料在挤出机中的三种物理状态的变化过程及对螺杆各部位的工作要求,通常将挤出机的螺杆分成加料段(固体输送区)、压缩段(熔融区)和均化段(熔体输送区)三段。
对于常规渐变螺纹的螺杆来说,塑料在挤出机中的挤出过程可以通过螺杆各段的基本职能及塑料在挤出机中的物理状态变化过程来描述,见图5。
1、加料段塑料自料斗进进挤出机的料筒内,在螺杆的旋转作用下,由于料筒内壁和螺杆表面的摩擦作用向前运动。
在该段,螺杆的职能主要是将塑料压实提供向前输送的动力,物料仍以固体状态存在,固然由于强烈的摩擦热作用,在接近末端时与料筒内壁相接触的塑料已接近或达到粘流温度,固体粒子表面开始发粘,但熔融仍未开始。
这一区域称为迟滞区,是指固体输送区结束到最初开始出现熔融的一为粘流态。
3、均化段从熔融段进人均化段的物料是已全部熔融的粘流体。
向前输送的粘流体在机头口模阻力下,一部分回流被进一步混合塑化,一部分被定量定压地从机头口模挤出。
从以上单螺杆挤出机的工作原理不丢脸出,塑料在挤出机中塑化,向前挤压活动,其主要动力来源于加料段的固体输送,塑化的均匀程度很大程度是由于均化段的结构和机头模具的阻力所造成的回流。
在改善螺杆混炼结构上已经有了很多新型的结构,但其往往适合于热稳定性很好的聚合物,却不适宜PVC树脂的生产,这就不逐一先容了。
双螺杆挤出机随着聚合物加产业的发展,对高分子材料成型和混合工艺提出了越来越多和越来越高的要求,单螺杆挤出机在某些方面就不能满足这些要求。
例如:用单螺杆挤出机进行填充改性和加玻璃纤维增强改性等,混合分散效果就不理想。
另外,单螺杆挤出机尤其不适合粉状物料的加工。
为了适应聚合物加工中混合工艺的要求,特别是硬聚氯乙烯粉料的加工,双螺杆挤出机自20世纪30年代后期在意大利开发出来以后,经过半个多世纪的精益求精和完善,得到了很大的发展。
在国外,目前双螺杆挤出机已广泛应用于聚合物加工领域,已占全部挤出机总数的40%。
硬聚氯乙烯粒料、管材、异型材、板材几乎都是采用双螺杆挤出机加工成型的。
作为连续混合机,双螺杆挤出机已广泛用来进行聚合物共混、填充和增强改性,也有用来进行反应挤出。
近20年来,高分子材料共混和反应挤出技术的发展进一步促进了双螺杆挤出机数目和类型的增加。
双螺杆挤出机的结构与分类双螺杆挤出机由传动装置、加料装置、料筒和螺杆等几个部分组成,各部件的作用与单螺杆挤出机相似。
与单螺杆挤出机区别之处在于双螺杆挤出机中有两根平行的螺杆置于同一的料筒中,如图6所示转下页)。
双螺杆挤出机有很多种不同的形式,主要差别在于螺杆结构的不同。
双螺杆挤出机的螺杆结构要比单螺杆挤出机复杂得多,这是由于双螺杆挤出机的螺杆还有诸如旋转方向、啮合程度等等题目。
常用于PVC型材挤出的双螺杆挤出机通常是紧密啮合且异向旋转的螺杆,少数也有使用同向旋转式双螺杆挤出的,但一般只能在低速下操纵,约在10r/min范围内。
而高速啮合同向旋转式双螺杆挤出机用于混炼、排气造粒或作为连续化学反应器使用,这类挤出机最大螺杆速度范围在300~600r/min。
非啮合型挤出机与啮合型挤出机的输送机理大不相同,比较接近于单螺杆挤出机的输送机理,二者有本质上的差别。
双螺杆挤出机的工作原理双螺杆挤出机的结构尽管与单螺杆挤出机很相似,但工作原理差异却很大。