二氧化碳脱除方法的分析与比较
原料气中二氧化碳的脱除

6 工艺流程
甲醇 原料气
半贫液 H2S尾气
CO+H2
氨冷
闪蒸
第一吸 收塔
再沸器
H2S再 生塔
CO变换 CO2
甲醇
净化气
富液
氨冷
氮气
气提再 生塔
第二吸 收塔
二、碳酸丙烯酯法
(一)特点:
1 碳酸丙烯酯是具有一定极性的有机溶剂,对二氧化碳、硫化氢
等酸性气体有较大的溶解能力,而氢、氮、一氧化碳等气体在其
4 流程配置原则
保证净化气指标:H2S\CO2
吸收系统 降温系统
保证溶液循环使用:
原
料
再生系统
气
减 压 再 生
净 化 气
吸
收
塔
热量移出
保证低温
气
热
提
源
再
再
生
生
空 气
蒸 气
保证回收二氧化碳的纯度 保证硫化氢满足后工序要求 合理用能 注意溶液中水分对吸收能力的影响 安全措施
5 主要工艺条件 吸收压力 吸收温度 溶液最小循环量和吸收塔液气比 净化气二氧化碳含量 再生条件
CO
0.01
N2
3、因H2\N2溶解能力小,损失小。
H2
0.001
-60 -40 -20
0 20 40
℃
各种气体在甲醇中溶解度系数
3.3 二氧化碳的脱碳—物理方法
低温甲醇洗涤法的特点 可脱除H2S、COS、CS2、RSH、CO2 、HCN、NH3、NO、H2O等 净化度高, H2S<0.1cm3/m3 ,CO2<10cm3/m3 可选择性脱除 H2S,CO2 甲醇热稳定性好,不降解,不起泡,损耗少 和最终净化的液氮洗涤匹配节省投资和动力消耗 流程长、再生复杂,有毒。
几种脱碳方法的分析比较
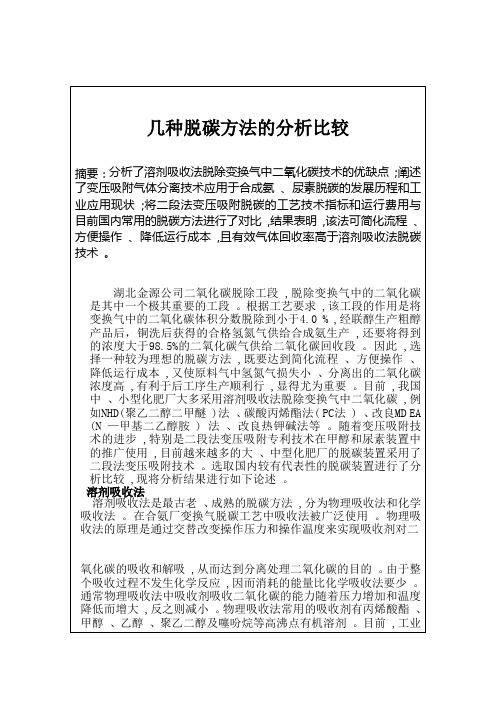
H2回收率,φ/ %≥99. 598. 098. 099. 599. 5
N2回收率,φ/ %≥97≥96≥96≥98≥99
CO回收率,φ/ %≥96≥94≥94≥98≥98
净化气中CO2,φ/ %≤0. 2≤ 0. 2≤0.≥98. 5≥98. 5≥98.5≥98.5≥98.5
外供热能 。
针对化学吸收法存在的缺陷 ,人们相继研究开发出膜分离和变压吸附分离等新型脱碳方法 。20世纪60年代,在美国联合碳化物公司(UCC)首次采用变压吸附技术从含氢废气中提纯氢气获得成功后 ,国内外也先后开发出变压吸附提纯工业级一氧化碳 、变压吸附制富氧 、变压吸附制纯氮 、变压吸附提纯工业级二氧化碳以及变压吸附脱碳 (仅用于精制合成气 、生产液氨 )等技术 从20世纪70年代开始 ,人们一直希望将变压吸附技术应用于合成氨 、尿素生产中 ,从变换气中同时提纯二氧化碳和精制合成气 ,以代替传统的物理吸收法和化学吸收法 。20 世纪70 年代初期 ,美国空气产品和化学品公司就开始把变压吸附气体分离技术用于合成氨变换气 、尿素脱碳的研究 ,并分别于1979年和1988年申请了专利 。在该变压吸附尿素脱碳技术中 ,氢气回收率最高可达95% ,二氧化碳回收率大于94%。该技术已应用于500 t / d的合成氨 、尿素生产装置中 。除了美国空气产品和化学品公司外 ,英国IC I(英国帝国化学公司 )公司 、荷兰KTI公司以及日本东洋工程公司分别于20 世纪80年代开发出了应用于合成氨 、尿素生产装置中的变压吸附技术 ,并分别应用于450 t / d、600 t / d和550 t / d的合成氨 、尿素生产装置中 。但是 ,由于上述各大公司开发的变压吸附尿素脱碳技术 ,其精制的合成气中氢气回收率较低 ,最高只有95%左右 ,而且吨氨电耗比传统的物理吸收法和化学吸收法还高30% ~60% ,总体经济效益远不如传统的物理吸收法和化学吸收法 ,因此国外变压吸附尿素脱碳技术只停留在工业试验装置上 ,无法推广应用 。在国内 ,变压吸附脱碳技术的发展经历了下述3个阶段 。
化学工艺学二氧化碳的脱除
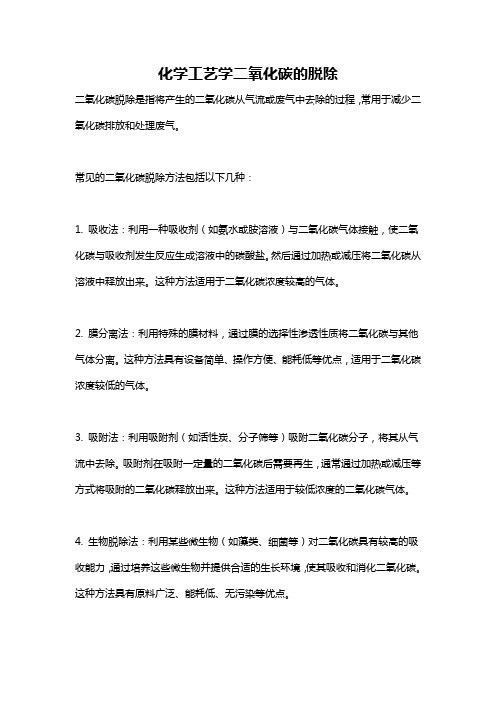
化学工艺学二氧化碳的脱除
二氧化碳脱除是指将产生的二氧化碳从气流或废气中去除的过程,常用于减少二氧化碳排放和处理废气。
常见的二氧化碳脱除方法包括以下几种:
1. 吸收法:利用一种吸收剂(如氨水或胺溶液)与二氧化碳气体接触,使二氧化碳与吸收剂发生反应生成溶液中的碳酸盐。
然后通过加热或减压将二氧化碳从溶液中释放出来。
这种方法适用于二氧化碳浓度较高的气体。
2. 膜分离法:利用特殊的膜材料,通过膜的选择性渗透性质将二氧化碳与其他气体分离。
这种方法具有设备简单、操作方便、能耗低等优点,适用于二氧化碳浓度较低的气体。
3. 吸附法:利用吸附剂(如活性炭、分子筛等)吸附二氧化碳分子,将其从气流中去除。
吸附剂在吸附一定量的二氧化碳后需要再生,通常通过加热或减压等方式将吸附的二氧化碳释放出来。
这种方法适用于较低浓度的二氧化碳气体。
4. 生物脱除法:利用某些微生物(如藻类、细菌等)对二氧化碳具有较高的吸收能力,通过培养这些微生物并提供合适的生长环境,使其吸收和消化二氧化碳。
这种方法具有原料广泛、能耗低、无污染等优点。
需要根据具体的应用情况选择适合的二氧化碳脱除方法,并结合其他工艺进行处理。
二氧化碳分离技术简介

C02分离技术简介工艺及特点1、胺法最普遍的溶剂是胺基溶剂,许多化合物都利用它来脱除酸性气体,如一乙醇胺(MEA)、二乙醇胺(DEA)、三乙醇胺(TEA)和二异丙醇胺(DIPA)他们活性强而不仅限于CO2脱除。
这些胺类溶剂也适合脱除其他酸性种类,如H2S O目前主要溶剂是甲基二乙醇胺(MEDA), 如果其他杂质需要脱除,可以由更具活性的二胺激活。
采用MEDA的其他优点是降低了再生负荷,降低了腐蚀性和提高了抗降解性。
低的胺类蒸汽压可以使其在较高的浓度下操作,因而提高了富胺的负荷。
其他具有位阻效应的胺有二甘醇胺和二异丙醇胺。
基本的工艺是一个两级系统,先是吸收,然后是间接再生。
大多数工艺都达至I」相近的产品规走,但每种工艺略有不同,需要从再生能耗和溶剂受原料气杂质影响的敏感性上去判断。
以MDEA为基础的工艺具有胺类溶剂的低挥发度和可利用中间闪蒸减少再生负荷的优点。
当原料气被吸收塔里产生的流态或胶体的重怪污染时,化学溶剂吸收工艺容易产生发泡问题。
2,热钾碱法另一个主要的脱除CO2的化学溶剂是热碳酸钾, 它与胺系统具有相似的工艺流程,有一个吸收塔和_ 个再生塔,特别适合低含或不含H2S的气体,缺点是气体不仅被加湿,而且还被加热,这可能引起相当大的热量浪费,特别是下游气体要冷却以分离NGL或LPG。
热钾碱也不是很活泼,所以,当产品要求的CO2浓度低时就需要两级吸收。
热钾碱法最适合于从高浓度的原料气中大量脱除CO2,另一个好处是吸收剂成本相对低。
3,物理吸收法物理溶剂吸收CO2没有形成新的化合物。
这种工艺通常采用甲醇作为吸收剂。
工艺特点是不会加湿原料气并且再生能耗低。
在再生段,CO2从物理溶剂中闪蒸出来,贫溶剂用泵打回吸收塔。
物理溶剂吸收法特别适合重怪含量少的贫气,这是因为乙烷在甲醇中的溶解度只是CO2在甲醇中溶解度的40%,而丙烷在甲醇中的溶解度与CO2的相近,因此需要一个循环系统以提高气体的回收率。
物理溶剂吸收法还可采用无水碳酸丙烯脂等溶剂。
二氧化碳脱除方法的分析与比较
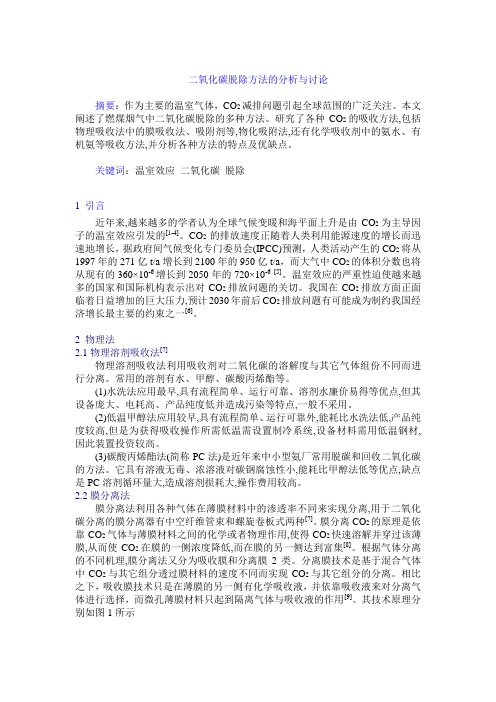
二氧化碳脱除方法的分析与讨论摘要:作为主要的温室气体,CO2减排问题引起全球范围的广泛关注。
本文阐述了燃煤烟气中二氧化碳脱除的多种方法。
研究了各种CO2的吸收方法,包括物理吸收法中的膜吸收法、吸附剂等,物化吸附法,还有化学吸收剂中的氨水、有机氨等吸收方法,并分析各种方法的特点及优缺点。
关键词:温室效应二氧化碳脱除1 引言近年来,越来越多的学者认为全球气候变暖和海平面上升是由CO2为主导因子的温室效应引发的[1-4]。
CO2的排放速度正随着人类利用能源速度的增长而迅速地增长,据政府间气候变化专门委员会(IPCC)预测,人类活动产生的CO2将从1997年的271亿t/a增长到2100年的950亿t/a,而大气中CO2的体积分数也将从现有的360×10-6增长到2050年的720×10-6 [5]。
温室效应的严重性迫使越来越多的国家和国际机构表示出对CO2排放问题的关切。
我国在CO2排放方面正面临着日益增加的巨大压力,预计2030年前后CO2排放问题有可能成为制约我国经济增长最主要的约束之一[6]。
2 物理法2.1物理溶剂吸收法[7]物理溶剂吸收法利用吸收剂对二氧化碳的溶解度与其它气体组份不同而进行分离。
常用的溶剂有水、甲醇、碳酸丙烯酯等。
(1)水洗法应用最早,具有流程简单、运行可靠、溶剂水廉价易得等优点,但其设备庞大、电耗高、产品纯度低并造成污染等特点,一般不采用。
(2)低温甲醇法应用较早,具有流程简单、运行可靠外,能耗比水洗法低,产品纯度较高,但是为获得吸收操作所需低温需设置制冷系统,设备材料需用低温钢材,因此装置投资较高。
(3)碳酸丙烯酯法(简称PC法)是近年来中小型氨厂常用脱碳和回收二氧化碳的方法。
它具有溶液无毒、浓溶液对碳钢腐蚀性小,能耗比甲醇法低等优点,缺点是PC溶剂循环量大,造成溶剂损耗大,操作费用较高。
2.2膜分离法膜分离法利用各种气体在薄膜材料中的渗透率不同来实现分离,用于二氧化碳分离的膜分离器有中空纤维管束和螺旋卷板式两种[7]。
二氧化碳的脱除
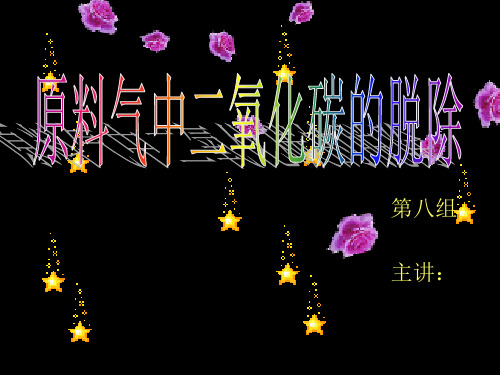
(1)吸收原理 )
1.1.1工艺原理:实质是热碳酸钾法 工艺原理: 工艺原理
化学平衡
CO2(l)+K2CO3+H2O=2KHCO3 || CO2(g) 2(g) 由图可知,出塔溶液转化度越高, 由图可知,出塔溶液转化度越高, 吸收的二氧化碳越多, 吸收的二氧化碳越多,若降低 温度或增加二氧化碳的分压, 温度或增加二氧化碳的分压, 则出塔溶液转化度增加; 则出塔溶液转化度增加;若降 低温度或进塔溶液的转化度, 低温度或进塔溶液的转化度, 出塔气体中二氧化碳的平衡分 压降低,净化度高。 压降低,净化度高。
反应速率
1.1.2本菲尔特法脱碳的工艺流程
热钾碱液吸收CO2
本菲尔特脱碳工艺流程
1.1.3本菲尔特法脱碳的工艺条件 本菲尔特法脱碳的工艺条件
脱碳溶液中吸收组分为碳酸钾。 溶液的组成 脱碳溶液中吸收组分为碳酸钾。为减 轻碳酸钾溶液对设备的腐蚀, 轻碳酸钾溶液对设备的腐蚀,大多以偏钒酸盐作 为缓蚀剂。 为缓蚀剂。 提高吸收压力,可以增加吸收推动力, 吸收压力 提高吸收压力,可以增加吸收推动力, 减少吸收设备的体积,提高气体净化度。 减少吸收设备的体积,提高气体净化度。 吸收温度 提高吸收温度可以使吸收速率系数加 但却使吸收推动力降低。 大,但却使吸收推动力降低。 再生后贫液、 溶液的转化度 再生后贫液、半贫液的转化度大小 是再生好坏的标志。 是再生好坏的标志。 再生过程中, 再生温度和再生压力 再生过程中,提高溶液的温 度可以加快碳酸氢钾的分解速率,对再生有利。 度可以加快碳酸氢钾的分解速率,对再生有利。 由于再生出来的二氧化碳要送到下一个工段继续 加工使用,通常再生压力略高于大气压力, 加工使用,通常再生压力略高于大气压力,一般 控制在0.12—0.14MPa。 控制在 。
变压吸附法脱除二氧化碳的研究

变压吸附法脱除二氧化碳的研究
近年来,全球气候变化和能源危机的加剧,脱除二氧化碳在一定程
度上成为可行的解决方案之一。
变压吸附法脱除二氧化碳是一种很有
前景和价值的技术。
下面,就对变压吸附法脱除二氧化碳的研究进行
详细的论述。
一、变压吸附法的原理
变压吸附法是将二氧化碳通过发生反应来转化成三元(五元)碳醇的
方法,将其吸附在变压吸附剂的表面上。
这种反应的发生,伴随着可
以得到一定数量的甲烷。
然后,在一定压力、温度条件下,将三元
(五元)碳醇和甲烷从吸附剂表面上解吸出来,从而获得三元(五元)碳醇和甲烷。
二、变压吸附法的优势
1.变压吸附法技术具有很强的可操作性:通过调节压力、温度等参数,可以实现对不同特性的氦气的有效吸附,具有较高的吸附率;
2.变压吸附法能够实现安全处理:由于变压吸附法不需要使用毒性物质,所以可以实现安全处理,不会带来环境和健康方面的影响;
3.变压吸附法可以大量收集二氧化碳:变压吸附法可有效收集浓度不
同的二氧化碳,可以实现有效利用和重复利用。
三、变压吸附法的应用
1.工业烟气治理:烟气中的二氧化碳和其他有害物质大部分可以通过变压吸附法有效的脱除,使得其可以进入大气环境中;
2.生物冷冻:变压吸附法可以有效的减少冷冻器中氦气,从而有效减少冷冻方式所需要的能量;
3.新能源应用:通过将二氧化碳转换成液态碳醇,可以被用于各种新能源的研发和应用中。
综上所述,变压吸附法脱除二氧化碳具有很多的优势,并且已经在工业烟气治理、生物冷冻和新能源应用中得到了广泛应用。
它拥有广阔的发展前景,有望成为实现经济可持续发展的重要手段。
原料气中二氧化碳的脱除
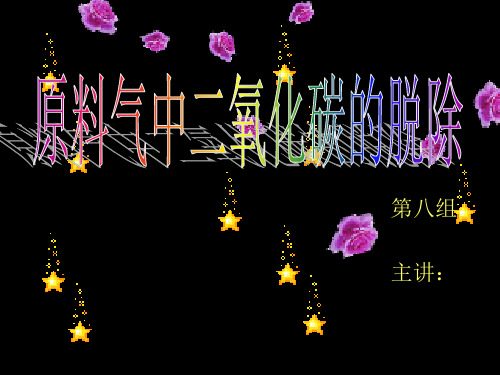
主讲:
1.二氧化碳的脱除
• 一氧化碳变换过程时,生成更多的CO2, 其含量可高达28%~30%。因此也需要脱 除CO2,回收的CO2可加以利用。脱除二氧 化碳的过程通常简称为脱碳。 • 国内外各种脱碳方法多采用溶液吸收剂来 吸收CO2,根据吸收机理可分为化学吸收 和物理吸收两大类。近年来出现了变压吸 附法、膜分离等固体脱除二氧化碳法。 • 方法一般有:1化学吸收法、2物理吸收
MDEA法脱碳
1.2 物理吸收法
目前国内外使用的物理吸收法主要有冷 甲醇法、聚乙二醇二甲醚法和碳酸丙烯 酯法。物理吸收法在加压(2~5MPa) 和较低温度条件下吸收CO2,溶液的再 生靠减压解吸,而不是加热分解,属于 冷法,能耗较低。
1.2.1物理吸收剂的选择
此法选择性较差,且仅采用降压闪蒸再 生,CO2回收率不高,但能耗低一般在合 成氨场使用. 按操作温度分为:常温吸收与低温洗涤法. 低温甲醇洗的优点:具有良好的选择性, 气体净化度高,甲醇的热稳定性和化学稳 定性好.可以串联液氮洗涤,是冷却净化流 程的优化选择.
反应速率 常温下,纯碳酸钾水溶液与二氧化碳
的反应速率较慢,提高反应温度可提高反应速率。 活化剂的加入改变碳酸钾与二氧化碳的反应机理, 从而提高反应速率。 本菲尔特法采用的活化剂为DEA。 (2)碳酸钾溶液对其他组分的吸收 (3)溶液的再生及再生度 碳酸钾溶液吸收二氧化碳后应进行再生以使溶液循 环使用。 溶液中总二氧化碳物质 的量 再生度 fc= 溶液中总氧化钾物质的 量
1.1.2本菲尔特法脱碳的工艺流程
热钾碱液吸收CO2
本菲尔特脱碳工艺流程
1.1.3本菲尔特法脱碳的工艺条件
溶液的组成 脱碳溶液中吸收组分为碳酸钾。为减 轻碳酸钾溶液对设备的腐蚀,大多以偏钒酸盐作 为缓蚀剂。 吸收压力 提高吸收压力,可以增加吸收推动力, 减少吸收设备的体积,提高气体净化度。 吸收温度 提高吸收温度可以使吸收速率系数加 大,但却使吸收推动力降低。 溶液的转化度 再生后贫液、半贫液的转化度大小 是再生好坏的标志。 再生温度和再生压力 再生过程中,提高溶液的温 度可以加快碳酸氢钾的分解速率,对再生有利。 由于再生出来的二氧化碳要送到下一个工段继续 加工使用,通常再生压力略高于大气压力,一般 控制在0.12—0.14MPa。
- 1、下载文档前请自行甄别文档内容的完整性,平台不提供额外的编辑、内容补充、找答案等附加服务。
- 2、"仅部分预览"的文档,不可在线预览部分如存在完整性等问题,可反馈申请退款(可完整预览的文档不适用该条件!)。
- 3、如文档侵犯您的权益,请联系客服反馈,我们会尽快为您处理(人工客服工作时间:9:00-18:30)。
二氧化碳脱除方法的分析与讨论摘要:作为主要的温室气体,CO2减排问题引起全球范围的广泛关注。
本文阐述了燃煤烟气中二氧化碳脱除的多种方法。
研究了各种CO2的吸收方法,包括物理吸收法中的膜吸收法、吸附剂等,物化吸附法,还有化学吸收剂中的氨水、有机氨等吸收方法,并分析各种方法的特点及优缺点。
关键词:温室效应二氧化碳脱除1 引言近年来,越来越多的学者认为全球气候变暖和海平面上升是由CO2为主导因子的温室效应引发的[1-4]。
CO2的排放速度正随着人类利用能源速度的增长而迅速地增长,据政府间气候变化专门委员会(IPCC)预测,人类活动产生的CO2将从1997年的271亿t/a增长到2010年的950亿t/a,而大气中CO2的体积分数也将从现有的360×10-6增长到2005年的720×10-6 [5]。
温室效应的严重性迫使越来越多的国家和国际机构表示出对CO2排放问题的关切。
我国在CO2排放方面正面临着日益增加的巨大压力,预计2030年前后CO2排放问题有可能成为制约我国经济增长最主要的约束之一[6]。
2 物理法`物理溶剂吸收法[7]物理溶剂吸收法利用吸收剂对二氧化碳的溶解度与其它气体组份不同而进行分离。
常用的溶剂有水、甲醇、碳酸丙烯酯等。
(1)水洗法应用最早,具有流程简单、运行可靠、溶剂水廉价易得等优点,但其设备庞大、电耗高、产品纯度低并造成污染等特点,一般不采用。
(2)低温甲醇法应用较早,具有流程简单、运行可靠外,能耗比水洗法低,产品纯度较高,但是为获得吸收操作所需低温需设置制冷系统,设备材料需用低温钢材,因此装置投资较高。
(3)碳酸丙烯酯法(简称PC法)是近年来中小型氨厂常用脱碳和回收二氧化碳的方法。
它具有溶液无毒、浓溶液对碳钢腐蚀性小,能耗比甲醇法低等优点,缺点是PC溶剂循环量大,造成溶剂损耗大,操作费用较高。
膜分离法膜分离法利用各种气体在薄膜材料中的渗透率不同来实现分离,用于二氧化碳分离的膜分离器有中空纤维管束和螺旋卷板式两种[7]。
膜分离CO2的原理是依靠CO2气体与薄膜材料之间的化学或者物理作用,使得CO2快速溶解并穿过该薄膜,从而使CO2在膜的一侧浓度降低,而在膜的另一侧达到富集[8]。
根据气体分离的不同机理,膜分离法又分为吸收膜和分离膜2类。
分离膜技术是基于混合气体中CO2与其它组分透过膜材料的速度不同而实现CO2与其它组分的分离。
相比之下,吸收膜技术只是在薄膜的另一侧有化学吸收液,并依靠吸收液来对分离气体进行选择,而微孔薄膜材料只起到隔离气体与吸收液的作用[9]。
其技术原理分别如图1所示。
图1:膜分离法分离CO2的示意图…目前膜分离法用于分离烟气中的CO2面临以下问题:烟气中CO2浓度太低,烟气处理量巨大;烟气必须冷却到100℃之下以防止高温对膜的破坏;需提前除掉烟气中的化学物质或对膜进行化学处理,以防止膜受到烟气中的化学物质破坏;膜处理烟气前后需要压差,需要耗费额外的能量。
新发展的多种分离膜有碳膜、二氧化硅膜、沸石膜、促进传递膜、混合膜[10]。
低温蒸馏法图2:低温蒸馏法分离CO2的过程示意图CO2临界温度为℃,临界压力为,易于液化。
低温蒸馏法是通过低温冷凝分离CO2的一种物理过程。
低温蒸馏法利用天然二氧化碳气源中主要组份甲烷和二氧化碳间沸点的差异,以蒸馏方法将二氧化碳分离出来,主要应用于一些富含60%~90%的天然二氧化碳气源中回收二氧化碳,供二次采油用。
因此,此法具有一定的局限性[7]。
该方法设备庞大、能耗较高、分离效果较差,因而成本较高,一般情况下不大采用,只有在特殊情况下使用或同其他方法联用。
低温蒸馏法的优点在于能够产生高纯、液态的CO2,以便于管道输送。
在未来的IGCC或者O2/CO2烟气循环系统中,由于烟气中具有高浓度的CO2,低温法就显得比较有前景了[11]。
吸附法吸附技术利用吸附剂对混合气体中的不同组分具有不同吸附容量的特性。
吸附法是利用固态吸附剂对原料混合气中的CO2的选择性可逆吸附作用来分离回收CO2的[12]。
吸附法又分为变温吸附法(TSA)和变压吸附法(PSA),吸附剂在高温(或高压)时吸附CO2,降温(或降压)后将CO2解析出来,通过周期性的温度(或压力)变化,从而使CO2分离出来。
PSA法的再生时间比TSA法短很多,且TSA法的能耗是PSA法的2~3倍[13],因此,工业上普遍采用的是PSA法。
该方法主要是通过加压吸附过程和减压)脱附过程反复进行实现的,为了连续地分离回收CO 2至少要两个吸收塔来交叉的进行吸附和脱附。
其工作原理如图3所示。
图3:变压吸附(PSA )法的示意图常用的吸附剂有天然沸石、分子筛、活性氧化铝、硅胶和活性炭等。
吸附法工艺过程简单、能耗低,但吸附剂容量有限,需大量吸附剂,且吸附解吸频繁,要求自动化程度高。
3 化学法化学循环燃烧法化学循环燃烧法(CLC )最早是在20世纪80年代初期提出的,当时的主要目的是提高电厂热效率[14]。
Ishida 等[15]第一次提出可以应用CLC 从根本上解决分离CO 2的问题。
CLC 不直接使用空气中的氧分子,而是采用载氧剂(金属氧化物)来促进燃烧过程。
最基本的CLC 系统包括串联的空气反应器和燃料反应器。
金属在空气反应器中与空气中的氧气发生氧化反应(1),成为金属氧化物形式的携氧状态,接着燃料和金属氧化物在燃料反应器中发生还原反应(2),生成CO 2、H 2O ,以此循环使用[16]。
空气反应器里的反应: Me+21O 2→MeO (1) 燃料反应器里的反应:}MeO +燃料→Me+H 2O+ CO 2 (2)CLC的主要优点在于:该技术基于两步化学反应,实现了化学能梯级利用,具有更高的能量利用效率;空气反应器排放的主要是N2,不会污染空气;燃料在载氧剂的催进下燃烧,温度较低(600~1 200℃),不会生成氮氧化物;燃料反应器排放的气体主要为CO2和蒸汽,只需要简单的冷凝就可以分离出高纯度的CO2,而无需消耗过多的能量。
Ishida估算该技术可使电厂热效率提高到50%~60%,而CO2排放率降低到0.33 kg/kWh[15]。
电化学法Winnick 等[17]首先利用熔融碳酸盐燃料电池膜(MCFC)从太空飞行舱的空气中分离出CO2,并进行了MCFC 膜分离烟气中CO2的实验研究,此后日本大阪研究社、英国石油(British Petroleum ,简称BP)公司和意大利Ansaldo 公司也对用熔融碳酸盐电化学系统分离捕集烟道气中CO2进行了实验研究[18 - 20 ]。
熔融碳酸盐燃料电池是在闭合电路(应用一个外部电动势)下通过膜传,其反应原理如下[21]:CO-23(3)阴极:O2+2 CO2+4e=2CO-23=2CO2+2H2O+4e (4)阳极:H2+2CO-23总反应:O2+2H2=2H2O(5)熔融碳酸盐电化学电池分离CO2有几个优点:(1)熔融碳酸盐在燃料电池方面的应用有广泛的技术基础;》进行了传输;(2)随着温度的升高,约100%的熔融碳酸盐对CO-23的扩散率相当于10-5cm2/s;(3)在600℃显示了高约1S/cm的电导率,CO-23(4)从电厂烟道气中分离CO2的附加电力费用较低。
但是,熔融碳酸盐电化学电池在电厂烟道气分离CO2的应用中也有缺点:熔融碳酸盐是一种糊状腐蚀剂,其制作和操作都很困难,烟道气中的SO2 也会毒化电池,在高温烟道气环境下,电解质隔离和电极退化也是严重的问题。
而固态电解质比熔融碳酸盐电池的操作温度低,容易处理,腐蚀问题大大减少,比熔融碳酸盐具有更长的使用寿命。
因此,使用固态电解质膜联合熔融碳酸盐从烟道气中分离CO2是具有前景的方向之一[22 ]。
胺法脱碳技术3.3.1一乙醇胺法(MEA法)MEA法回收CO2工艺流程:烟道气经洗涤冷却后由引风机送入吸收塔,其大部分CO2被溶剂吸收,尾气由塔顶排入大气。
吸收CO2后的富液从塔底流出,由塔底经泵送至冷凝器和贫富液换热器,回收热量后送入再生塔。
再生出的CO2经冷凝后分离除去其中的水分,即得到纯度大于%的CO2产品气,送入后续工序。
再生气中被冷凝分离出来的冷凝液送入地下槽,再用泵送至吸收塔顶洗涤段和再生塔作回流液使用。
部分解吸了CO2的溶液进入再沸器,使其中的CO2进一步再生。
由再生塔底部出来的贫液经贫富液换热器后,用泵送至水冷器,最后进入吸收塔顶部。
此溶液往返循环构成连续吸收和再生CO2的工艺过程[23]。
MEA法回收CO2流程图见图4。
》图4:MEA法回收CO2流程图1.冷却塔2.风机3.吸收塔4.富液泵5.冷凝器6.换热器7.再生塔8.贫液泵9,10.水冷器11.再沸器12.分离器13.地下槽,回流泵14.胺回收加热器15.过滤器。
MEA水溶液吸收CO2的效果很好,与CO2反应生成碳酸盐化合物,加热就可使CO2分解出来,其优点是在一个非常简单的装置中就能将合成气中CO2脱除到%左右,但因MEA碱性较强,又能与CO2进一步生成比较稳定的碳酸盐[24]。
MEA法回收CO2的反应原理[23]MEA与CO2的反应式如下:CO2 + HOCH2CH2NH2→HOCH2CH2HNCOO-+ H+(6)H+ + HOCH2CH2NH2→HOCH2CH2NH+(7)3总反应式如下:CO2 + 2HOCH2CH2NH2→HOCH2CH2HNCOO-+ HOCH2CH2NH+(8)3MEA水溶液的缺点是容易发泡及降解变质。
同时,反应(8)生成的氨基甲酸盐的腐蚀性很强,MEA的再生温度较高(约125℃),导致再生系统腐蚀严重,在高酸气负荷下则更甚。
,MEA技术有很大的不足之处:成本较高、吸收率慢、吸收容量小、吸收剂用量大、有高的设备腐蚀率、胺类会被其他烟气成分降解、同时吸收剂再生时能耗高等,因此有必要对该技术进行改进,以降低成本,提高吸收剂的利用效率[25]。
MEA法的主要缺点系再生热耗较高。
为了降低过程的热耗,减少系统的腐蚀,加入一定量的有机溶剂,如N,N-二甲基甲酰胺、N,N-二甲基乙酰胺、β-吡咯烷酮、N-甲基吡咯烷酮、N-甲基-3-吗啉酮、环丁砜、甲醇及某些多元醇或其衍生物,可使再生热耗和腐蚀状况得到好转[26]。
3.3.2二乙醇胺(DEA)法[26]DEA水溶液与CO2的反应机理与MEA水溶液与CO2反应机理类似,DEA作为CO2化学吸收剂得到了广泛应用,其原因是它的沸点较MEA高,因此可以在较高的温度下进行吸收,不易降解。
改良DEA(DEA-SNPA)法,可在~压力下,使DEA溶液的碳化度达mol CO2/ mol DEA。
改良DEA法与DEA法的差别在于DEA 的浓度可增加到25%~30%,碳化度亦可提高。
虽然DEA溶液表面上的CO2分压高于MEA溶液表面上的CO2分压,用DEA溶液净化时不象用MEA溶液净化时那样高的净化度,且DEA溶液的吸收能力又比MEA低,价格又较MEA贵,但由于DEA沸点较高、蒸发损失少、又相应较MEA易于再生,消耗于汽提的热量较小,当饱和溶液中CO2浓度相同时采用DEA溶液净化比采用MEA溶液净化热耗少26%左右,建厂费用与生产费用均较MEA溶液低。