超精密微机械制造技术研究及进展参考文本
超精密机械加工技术与发展探讨
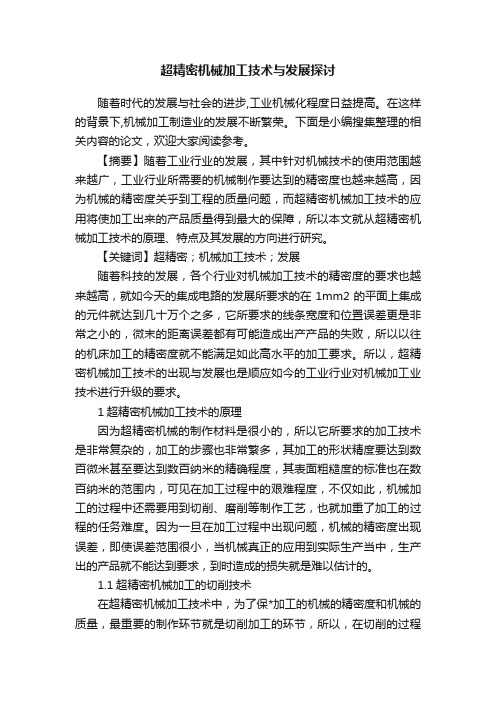
超精密机械加工技术与发展探讨随着时代的发展与社会的进步,工业机械化程度日益提高。
在这样的背景下,机械加工制造业的发展不断繁荣。
下面是小编搜集整理的相关内容的论文,欢迎大家阅读参考。
【摘要】随着工业行业的发展,其中针对机械技术的使用范围越来越广,工业行业所需要的机械制作要达到的精密度也越来越高,因为机械的精密度关乎到工程的质量问题,而超精密机械加工技术的应用将使加工出来的产品质量得到最大的保障,所以本文就从超精密机械加工技术的原理、特点及其发展的方向进行研究。
【关键词】超精密;机械加工技术;发展随着科技的发展,各个行业对机械加工技术的精密度的要求也越来越高,就如今天的集成电路的发展所要求的在1mm2的平面上集成的元件就达到几十万个之多,它所要求的线条宽度和位置误差更是非常之小的,微末的距离误差都有可能造成出产产品的失败,所以以往的机床加工的精密度就不能满足如此高水平的加工要求。
所以,超精密机械加工技术的出现与发展也是顺应如今的工业行业对机械加工业技术进行升级的要求。
1超精密机械加工技术的原理因为超精密机械的制作材料是很小的,所以它所要求的加工技术是非常复杂的,加工的步骤也非常繁多,其加工的形状精度要达到数百微米甚至要达到数百纳米的精确程度,其表面粗糙度的标准也在数百纳米的范围内,可见在加工过程中的艰难程度,不仅如此,机械加工的过程中还需要用到切削、磨削等制作工艺,也就加重了加工的过程的任务难度。
因为一旦在加工过程中出现问题,机械的精密度出现误差,即使误差范围很小,当机械真正的应用到实际生产当中,生产出的产品就不能达到要求,到时造成的损失就是难以估计的。
1.1超精密机械加工的切削技术在超精密机械加工技术中,为了保*加工的机械的精密度和机械的质量,最重要的制作环节就是切削加工的环节,所以,在切削的过程中就需要技术人员投入全部的精力及耐心。
为了减少切削加工过程中产生的误差,不仅要控制好切削环境的温度、切削的锋刃度还要控制好切削的形态,经过数年来*上的很多科学家的不断地实验终于确定了切削加工中所需达到的各种因素的数据,这有效的提高了切削加工技术的水平。
超精密加工技术发展研究及应用
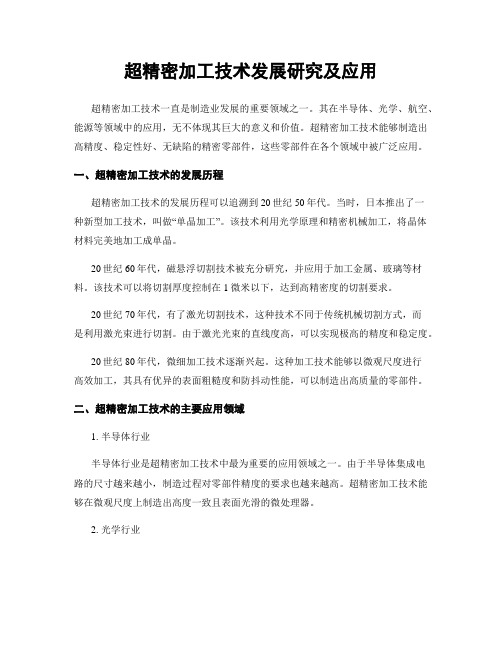
超精密加工技术发展研究及应用超精密加工技术一直是制造业发展的重要领域之一。
其在半导体、光学、航空、能源等领域中的应用,无不体现其巨大的意义和价值。
超精密加工技术能够制造出高精度、稳定性好、无缺陷的精密零部件,这些零部件在各个领域中被广泛应用。
一、超精密加工技术的发展历程超精密加工技术的发展历程可以追溯到20世纪50年代。
当时,日本推出了一种新型加工技术,叫做“单晶加工”。
该技术利用光学原理和精密机械加工,将晶体材料完美地加工成单晶。
20世纪60年代,磁悬浮切割技术被充分研究,并应用于加工金属、玻璃等材料。
该技术可以将切割厚度控制在1微米以下,达到高精密度的切割要求。
20世纪70年代,有了激光切割技术,这种技术不同于传统机械切割方式,而是利用激光束进行切割。
由于激光光束的直线度高,可以实现极高的精度和稳定度。
20世纪80年代,微细加工技术逐渐兴起。
这种加工技术能够以微观尺度进行高效加工,其具有优异的表面粗糙度和防抖动性能,可以制造出高质量的零部件。
二、超精密加工技术的主要应用领域1. 半导体行业半导体行业是超精密加工技术中最为重要的应用领域之一。
由于半导体集成电路的尺寸越来越小,制造过程对零部件精度的要求也越来越高。
超精密加工技术能够在微观尺度上制造出高度一致且表面光滑的微处理器。
2. 光学行业光学行业也是超精密加工技术的主要应用领域之一。
利用超精密加工技术,可以制造出近乎完美的光学元件,其表面粗糙度可以达到亚微米级别,从而实现更高的光学性能。
3. 航空行业超精密加工技术在航空行业的应用也越来越广泛。
航空行业对零部件的精度和稳定性要求非常高,超精密加工技术能够制造出非常高精度的零部件,为飞行器的性能提升做出了很大的贡献。
4. 能源行业能源行业对零部件的精度要求也越来越高,特别是在制造核聚变反应堆等核能设备时,需要使用到超精密加工技术。
该技术能够制造出高精度的零部件,从而提高核反应堆的运行效率和安全性能。
超精密微机械制造技术研究及进展
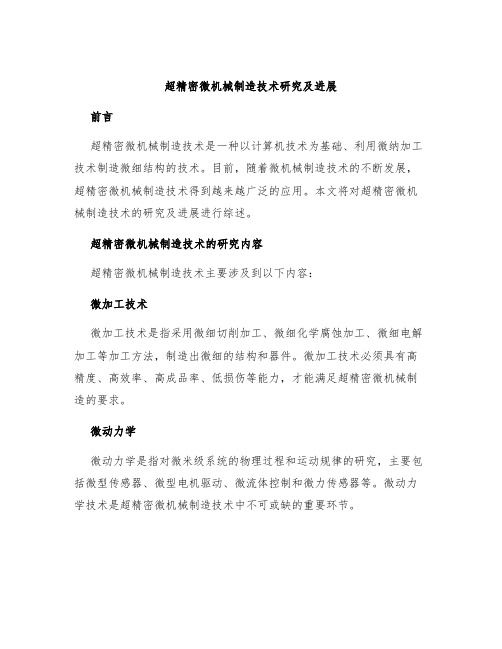
超精密微机械制造技术研究及进展前言超精密微机械制造技术是一种以计算机技术为基础、利用微纳加工技术制造微细结构的技术。
目前,随着微机械制造技术的不断发展,超精密微机械制造技术得到越来越广泛的应用。
本文将对超精密微机械制造技术的研究及进展进行综述。
超精密微机械制造技术的研究内容超精密微机械制造技术主要涉及到以下内容:微加工技术微加工技术是指采用微细切削加工、微细化学腐蚀加工、微细电解加工等加工方法,制造出微细的结构和器件。
微加工技术必须具有高精度、高效率、高成品率、低损伤等能力,才能满足超精密微机械制造的要求。
微动力学微动力学是指对微米级系统的物理过程和运动规律的研究,主要包括微型传感器、微型电机驱动、微流体控制和微力传感器等。
微动力学技术是超精密微机械制造技术中不可或缺的重要环节。
微纳机电系统微纳机电系统(MEMS)是一种能够感知环境、执行指令、传递信息和控制过程的微型化、高度集成化多功能微系统。
它主要包括传感器、执行器、驱动电路和信号处理器等模块。
目前,MEMS作为一种基础技术,已经广泛应用于医学、航空、航天、水利等领域。
超精密微机械制造技术的发展历程超精密微机械制造技术始于20世纪70年代,最初是为了制造高精度光学附属器材。
从20世纪80年代开始,加利福尼亚大学伯克利分校提出了MEMS技术,从而推动了微机械制造技术的发展。
此后,随着微纳技术、纳米技术的兴起,超精密微机械制造技术得到了迅猛发展。
超精密微机械制造技术的应用领域目前,超精密微机械制造技术已经应用到了众多领域,如:医疗保健领域在医疗保健领域,超精密微机械制造技术主要被应用于生物芯片、药物传输等方面。
航空航天领域在航空航天领域,超精密微机械制造技术主要被应用于制造微型仪器、传感器和执行机构等。
机械制造领域在机械制造领域,超精密微机械制造技术主要被应用于制造高性能陶瓷切削刀具、精密机械零件等。
光电子领域在光电子领域,超精密微机械制造技术主要被应用于制造微型光学器件,如光轴往复驱动器、纳米位移传感器等。
《微型精密铣床的研究和设计》范文
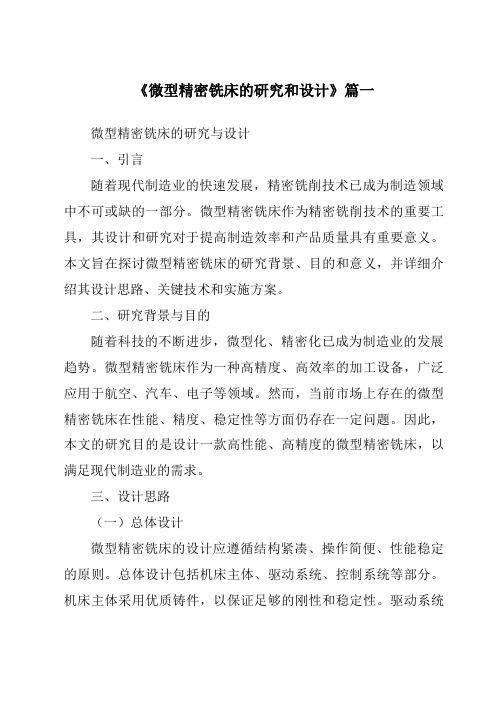
《微型精密铣床的研究和设计》篇一微型精密铣床的研究与设计一、引言随着现代制造业的快速发展,精密铣削技术已成为制造领域中不可或缺的一部分。
微型精密铣床作为精密铣削技术的重要工具,其设计和研究对于提高制造效率和产品质量具有重要意义。
本文旨在探讨微型精密铣床的研究背景、目的和意义,并详细介绍其设计思路、关键技术和实施方案。
二、研究背景与目的随着科技的不断进步,微型化、精密化已成为制造业的发展趋势。
微型精密铣床作为一种高精度、高效率的加工设备,广泛应用于航空、汽车、电子等领域。
然而,当前市场上存在的微型精密铣床在性能、精度、稳定性等方面仍存在一定问题。
因此,本文的研究目的是设计一款高性能、高精度的微型精密铣床,以满足现代制造业的需求。
三、设计思路(一)总体设计微型精密铣床的设计应遵循结构紧凑、操作简便、性能稳定的原则。
总体设计包括机床主体、驱动系统、控制系统等部分。
机床主体采用优质铸件,以保证足够的刚性和稳定性。
驱动系统采用高性能伺服电机和精密丝杠,以确保加工过程中的精度和稳定性。
控制系统采用先进的数控系统,实现自动化加工。
(二)关键技术1. 精密传动技术:采用高精度齿轮和轴承,保证传动精度和稳定性。
2. 数控技术:采用先进的数控系统,实现自动化加工和精确控制。
3. 切削参数优化:通过优化切削参数,提高加工效率和表面质量。
四、关键技术设计与实施方案(一)精密传动系统设计精密传动系统是微型精密铣床的核心部分,其设计直接影响机床的加工精度和稳定性。
设计过程中,应选择高精度齿轮和轴承,以保证传动精度。
同时,采用先进的润滑系统,降低传动系统的摩擦和磨损,延长使用寿命。
(二)数控系统设计数控系统是微型精密铣床的“大脑”,负责自动化加工和精确控制。
设计过程中,应选择性能稳定、功能强大的数控系统,实现加工过程的自动化和智能化。
同时,应具备友好的人机界面,方便操作人员进行参数设置和操作。
(三)切削参数优化设计切削参数的优化对于提高加工效率和表面质量具有重要意义。
超精密加工技术论文【精选文档】
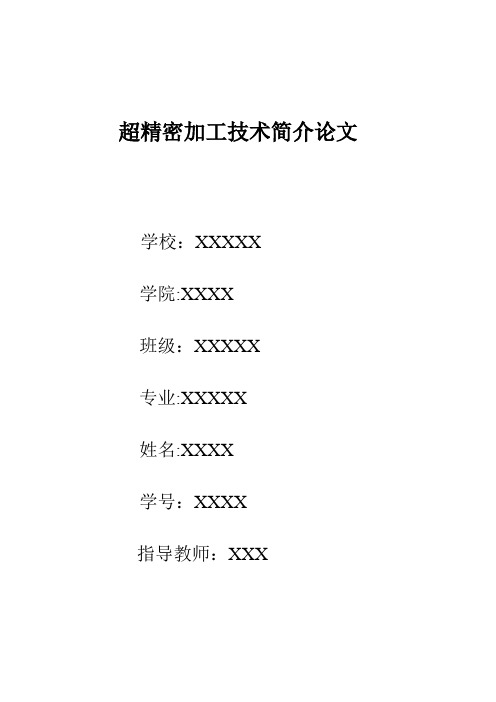
超精密加工技术简介论文学校:XXXXX学院:XXXX班级:XXXXX专业:XXXXX姓名:XXXX学号:XXXX指导教师:XXX目录目录 .......................................................................................................................................... - 1 -一、概述................................................................................................................... - 0 -1、超精密加工的内涵...................................................................................... - 0 -2。
、发展超精密加工技术的重要性................................................................ - 0 -二、超精密加工所涉及的技术范围....................................................................... - 1 -三、超精密切削加工............................................................................................... - 2 -1、超精密切削对刀具的要求.......................................................................... - 2 -2、金刚石刀具的性能特征.............................................................................. - 2 -3、超精密切削时的最小切削厚度.................................................................. - 2 -四、超精密磨削加工............................................................................................... - 3 -1、超精密磨削砂轮.......................................................................................... - 3 -2、超精密磨削砂轮的修整.............................................................................. - 3 -3、磨削速度和磨削液...................................................................................... - 4 -五、超精密加工的设备........................................................................................... - 4 -六、超精密加工的支撑环境................................................................................... - 5 -1、净化的空气环境.......................................................................................... - 5 -2、恒定的温度环境.......................................................................................... - 5 -3、较好的抗振动干扰环境.............................................................................. - 6 -七、超精密加工的运用领域................................................................................... - 6 -八、超精密加工的现状及未来发展....................................................................... - 6 -1、超精密加工的现状...................................................................................... - 6 -2、超精密加工的发展前景.............................................................................. - 7 - 总结:....................................................................................................................... - 8 - 参考文献: ................................................................................................................. - 8 -超精密加工技术一、概述超精密机械加工技术是现代机械制造业最主要的发展方向之一,已成为在国际竞争中取得成功的关键技术。
超精密加工技术在机械加工中的应用研究

超精密加工技术在机械加工中的应用研究一、引言机械加工技术在制造业中扮演着重要的角色,它的精度和效率直接影响着产品的质量和成本。
随着科学技术的不断发展,超精密加工技术应运而生,并在机械加工领域中逐渐得到应用。
超精密加工技术以其高精度、高效率和低成本的特点,改变了传统加工方式,成为了制造业不可或缺的一部分。
本文将重点研究超精密加工技术在机械加工中的应用。
二、超精密加工技术的概述超精密加工技术是一种以纳米级精度进行机械加工的技术。
它通过采用高功率激光、电子束等精确控制加工工具,使其在纳米级范围内进行切削、打磨、刻蚀等工艺,从而实现高精度的加工效果。
超精密加工技术广泛应用于半导体、光学、航天、医疗器械等领域。
三、超精密加工技术在机械加工中的应用案例1. 加工高精度模具超精密加工技术可以用于制造高精度模具,如塑料模具、金属模具等。
传统加工技术在模具制造过程中容易出现形状不一致、尺寸偏差大等问题,而超精密加工技术能够以纳米级精度进行加工,有效解决这些问题,提高模具的加工精度和质量。
2. 光学元件的加工光学元件是一种对光波进行传导、反射、折射和干涉的元件。
超精密加工技术在光学元件制造中具有独特的优势。
例如,在镜面的加工过程中,超精密加工技术可以确保光学元件的平整度和度数非常高,有效提高光学系统的工作效率。
3. 微机电系统(MEMS)的制造微机电系统是一种融合了微观结构和机电系统的微型设备。
超精密加工技术在MEMS制造中可以实现微小尺寸和高精度的要求。
例如,在MEMS传感器中,超精密加工技术可以以纳米级精度制造微机电结构,从而提高传感器的精确性和灵敏度。
四、超精密加工技术的发展趋势随着科学技术的发展,超精密加工技术在机械加工领域中也在不断演进。
未来,超精密加工技术将朝着以下几个方向发展:1. 多工艺融合超精密加工技术在机械加工中的应用需要结合多种加工工艺,如激光切割、电子束加工等。
未来,超精密加工技术将进一步发展,实现多工艺的融合,提高加工的精度和效率。
超精密制造技术论文
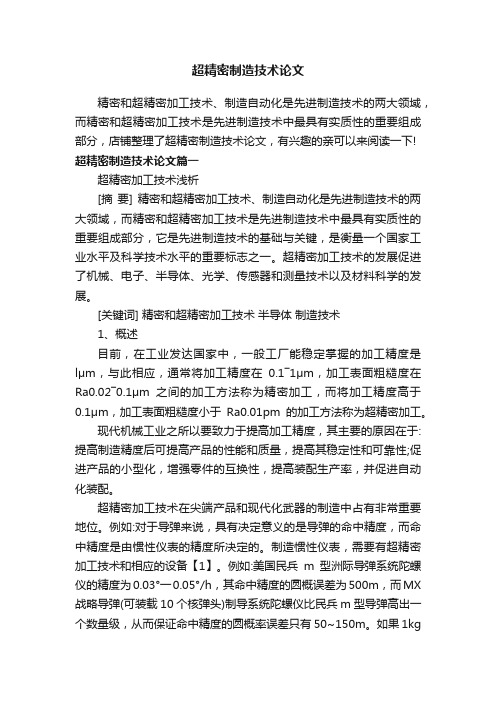
超精密制造技术论文精密和超精密加工技术、制造自动化是先进制造技术的两大领域,而精密和超精密加工技术是先进制造技术中最具有实质性的重要组成部分,店铺整理了超精密制造技术论文,有兴趣的亲可以来阅读一下! 超精密制造技术论文篇一超精密加工技术浅析[摘要] 精密和超精密加工技术、制造自动化是先进制造技术的两大领域,而精密和超精密加工技术是先进制造技术中最具有实质性的重要组成部分,它是先进制造技术的基础与关键,是衡量一个国家工业水平及科学技术水平的重要标志之一。
超精密加工技术的发展促进了机械、电子、半导体、光学、传感器和测量技术以及材料科学的发展。
[关键词] 精密和超精密加工技术半导体制造技术1、概述目前,在工业发达国家中,一般工厂能稳定掌握的加工精度是lμm,与此相应,通常将加工精度在0.1―1μm,加工表面粗糙度在Ra0.02―0.1μm之间的加工方法称为精密加工,而将加工精度高于0.1μm,加工表面粗糙度小于Ra0.01pm的加工方法称为超精密加工。
现代机械工业之所以要致力于提高加工精度,其主要的原因在于:提高制造精度后可提高产品的性能和质量,提高其稳定性和可靠性;促进产品的小型化,增强零件的互换性,提高装配生产率,并促进自动化装配。
超精密加工技术在尖端产品和现代化武器的制造中占有非常重要地位。
例如:对于导弹来说,具有决定意义的是导弹的命中精度,而命中精度是由惯性仪表的精度所决定的。
制造惯性仪表,需要有超精密加工技术和相应的设备【1】。
例如:美国民兵m型洲际导弹系统陀螺仪的精度为0.03°一0.05°/h,其命中精度的圆概误差为500m,而MX 战略导弹(可装载10个核弹头)制导系统陀螺仪比民兵m型导弹高出一个数量级,从而保证命中精度的圆概率误差只有50~150m。
如果1kg重的陀螺转子,其质量中心偏离其对称轴0.5nm,则会引起100m的射程误差和50m的轨道误差。
惯性仪表中有许多零件的制造精度都要求达到小于微米级。
超精密微机械制造技术研究进展

万方数据
第3期
于化东:超精密微机械制造技术研究进展
3
成型机及精密微型零件产品等;欧盟自2004年起 进行一项名为4M.Multi Material Micro Manufacture Network of Excellence的跨国性计划,整合了欧盟 各成员国的研发资源,在2004-2007年问已投入超 过15亿欧元,以期能于最短的时间内获得最大的 技术与应用突破;韩国也于2004年起投入6000万 美元,进行名为Development of Micro-Factory Sys· tern for Next Generation的5年计划。美国在过去投 入了非常多的资源进行MEMS技术的研发,但自 2005年起.亦开始重视精密微机械制造技术的开 发,其国家智库单位WTEC和NSF(National Sci· cuteFoundation)等机构于2002年共同出资,针对 国际上Non—MEMS微型加工技术研究发展现状与 趋势组成考察团,对全世界47个微制造技术相关 研发机构进行调查。其调查报告指出,Non-MEMS 超精密微机械制造技术将成为2 l世纪重要新技术, 它是连接微观与宏观制造领域的桥梁技术,是改变 传统加工理念(加工时间、地点、方式)的技术, 是改变生产力分配方式的技术(微制造成为家庭手 工业);它是增强美国竞争优势的战略性技术。自 2006年起,美国每年举办大型国际研讨会ICOMM
来越高。本文着重对超精密微机械制造技术的内涵、国内外研究现状和发展动态进行整理和描述,并对超精密微机
械制造技术的未来发展趋势进行总结,为我国未来的先进制造技术研究与计划制订提供参考。
关键词:超精密加工;微制造;三维微小零件;微机械
中图分类号:THl6
文献标识码:A
文章编号t 1672—9870(2008)03一0001一08
- 1、下载文档前请自行甄别文档内容的完整性,平台不提供额外的编辑、内容补充、找答案等附加服务。
- 2、"仅部分预览"的文档,不可在线预览部分如存在完整性等问题,可反馈申请退款(可完整预览的文档不适用该条件!)。
- 3、如文档侵犯您的权益,请联系客服反馈,我们会尽快为您处理(人工客服工作时间:9:00-18:30)。
超精密微机械制造技术研究及进展参考文本
In The Actual Work Production Management, In Order To Ensure The Smooth Progress Of The Process, And Consider The Relationship Between Each Link, The Specific Requirements Of Each
Link To Achieve Risk Control And Planning
某某管理中心
XX年XX月
超精密微机械制造技术研究及进展参考
文本
使用指引:此安全管理资料应用在实际工作生产管理中为了保障过程顺利推进,同时考虑各个环节之间的关系,每个环节实现的具体要求而进行的风险控制与规划,并将危害降低到最小,文档经过下载可进行自定义修改,请根据实际需求进行调整与使用。
随着航空航天,国防工业,电子产业,现代医学和生
物工程技术的快速发展,对于三维微小零件的精度(其尺
寸在微米到毫米级)迫切需求。
本文对内涵的整理和叙
述,对超精密微机械制造技术国内外的研究现状和发展趋
势,并对未来的超精密微机械制造技术的发展趋势进行了
总结,为先进制造技术领域的研究和规划我们的未来发展
方向。
超精密微机械制造技术领域是在第二十世纪80年代初
期90年代逐渐发展的新兴科学领域。
它的迅猛发展将在二
十一世纪为几乎为所有的工业领域带来翻天覆地变化。
微
系统与微制造的产品广泛应用于军事,医疗,航空航天,
电子等军用和民用领域。
本文对其内涵的整理和叙述,超精密微机械制造技术的国内外研究现状和发展趋势,为今后我国先进制造技术研究计划提供可参考的意见。
什么是超精密微机械制造技术
微制造系统是针对微小机械零件这个特殊加工对象,采用系统的,集成的理论和技术,根据工件结构和具体要求把供料、加工、检测、搬运等步骤有效的融合起来,在狭小的空间内对微型零件进行制造。
它的目地是实现“小零件用小机床加工”的概念,不同于MEMS微制造技术和方法。
它必将成为非硅材料的加工(如金属,陶瓷等)的最有效的小零件的加工方式,可以从根本上解决了小型零件的加工难题。
超精密微机械制造技术重点研究的对象尺寸在10m~ 10mm,处理复杂的几何形状的小部件。
具有能耗低,体积小,生产灵活,效率高。
降低了制造系统及零件的尺
寸,不仅节省能源,还节省了生产空间和资源,符合节能,环保的生产方式,是绿色制造业的发展方向。
国内及国外研究现状及发展趋势
2.1.微机械加工设备的技术
目前,国内已有多所高校对微小制造系统,微小切削技术领域展开研究。
已获得一些令人可喜的成就。
哈尔滨工业大学精密工程研究所于2007开发的一个小型超精密三轴数控铣床,主轴最高转速160000 RPM,回转精度达到1米,工作台定位精度达到0.5米/±75mm,重复定位精度达±0.25m,刀具采用进口的刀具,最小可达到
0.15mm。
北京理工大学研发的用于引信机构微小型金属承载构件加工的精密微小型车铣加工中心,针对于对微小型构件三维加工和高频群脉冲电加工技术研究,c轴转速8000rpm,铣头主轴转速60000rpm,可以四轴联动,重复定位精度已达到国际先进水平。
清华大学,南京航天航
空大学,北京航空精密机械研究所都积极开展针对微型机床研究。
此外,在香港城市大学开发的建模与西北工业大学合作,对微制造系统仿真进行研究。
长春理工大学一直在精密和超精密加工技术中微细切削加工与微机械制造技术、微磨擦磨损机理、激光精密加工技术、硬脆材料精密加工技术、微光机电一体化技术方面进行长时间的研究,。
在微加工和微摩擦磨损机理的研究的基础上,成功地研发了微切削功能的微摩擦磨损测试机,主轴转速6000rpm,旋转精度达到了±2米,±1米的进给精度,微磨擦测力传感器使用了双平衡机构,从而实现了同时测定正压力和摩擦力;利用仪器的模块化设计,可使摩擦测量头与微切削刀头更换,从而实现微切削作用,对微切削的机理进行研究。
在激光精密加工技术方面,于2005开发出特殊材料的微型零件精密激光去除的装置,机器的加工精度已达到微米级。
在微传感器技术测试
技术和微控制技术等领域开展了一系列的研究,并取得了一系列令人可喜成果,为微处理单元和微制造系统的设计,制造,积累了一定的宝贵经验。
2.2.特殊工艺
超精密加工需要在洁净的环境中才可进行的,其中蚀刻技术的关键特征,一般用在光刻,微机械元件的硅衬底上形成光摄影,生成零件的几何形状,进一步的处理,方法:
2.2.1.刻蚀方法。
腐蚀是形成微机械深加工的主要途径。
首先把光刻之后的硅用腐蚀剂侵蚀,移除牺牲层保留处理层,制作成工件,再经过清洗后得到的工件。
腐蚀法有湿式和干式两种方法,干法分为离子法和激光法,而湿法分为溶液法和阳极法。
而溶液法由于操作简单,使用成本低廉,处理效果好,加工范围广而被广泛使用。
常见的腐蚀剂溶液有EDP,KOH,H2N2三种,按照比例,对腐
蚀速率及温度的控制,使其生成掩膜SiO2或Si3N4,从而满足硅体蚀刻的选择性,掩蔽,超精密的高水平的各向异性。
激光腐蚀法则是通过调整激光蚀刻的辐射剂量,几乎任何形状的微机械结构都可以此方法加工,这是其他腐蚀法所办不到的。
2.2.2.沉积的方法。
沉积过程中,外延生长是一种常见的技术。
此技术的特点是将外延生长层与基底材料保持相同的结晶取向,这极大的提高了材料外延长层纵向或是横向的加工能力,以产生所需的结构,把添加硼技术结合硅外延生长技术结合起来,可以生产高精度立体微机械零件。
三维微机械LIGA技术沉积技术和光刻技术的结晶工艺,它采用X射线,使波长保持在0.1-1纳米,对涂覆在底部上的PMMA感光材料光刻,可达1mm深,电铸金属从而产生感光材料的微观结构,并以其为模具注塑成型塑料产品。
超精密微机械制造技术的发展走势
3.1.微切割技术。
关键技术包括微零件的加工设备,主要是具有高转速的主轴系统,精确定位技术,精密工作台的运动与控制的微机械加工设备与技术;微切削刀具材料和刀具的制造技术;微切削中刀具及工件的快速装夹技术,微切削中和测试监控技术。
3.2.微切削机理。
主要是热——机械耦合应力作用下的不均匀变形,微尺度下的本构方程的工件材料,微切削区的位错应力,尺寸效应,非均匀应变等对剪切变形和剪切效应的影响;最小切削量对切屑形状,已加工的表面形成,切割应力,切削温度的影响,和工件材料的微观结构对表面粗糙度和表面损伤的影响,微切削的模拟仿真技术,微切削理论和技术体系。
3.3.微切削过程。
微机械加工工艺,包括各种新型材料如不锈钢,钛合金,不锈钢,铝合金,陶瓷等非金属材料
及各种复合材料,显微切割的CAD / CAM技术。
3.4.微加工技术,经济和可靠性的评估。
3.5.微加工的研究和设计原理及实用的微制造系统的方法和相关的应用技术。
请在此位置输入品牌名/标语/slogan
Please Enter The Brand Name / Slogan / Slogan In This Position, Such As Foonsion。