25万吨年丁辛醇工艺分析及优化
丁辛醇生产工艺技术研究

丁辛醇生产工艺技术研究丁辛醇是一种重要的有机化工原料,广泛应用于涂料、溶剂、合成橡胶、树脂、塑料等工业中。
它的生产工艺技术研究对于提高产品质量、降低生产成本、减少对环境的污染具有重要意义。
丁辛醇的生产工艺通常采用乙烯与异癸醇经醇酸发酵和醇醚酸化两个步骤进行。
首先,乙烯和异癸醇经过混合、调温后进入乙烯异癸醇醇酸发酵罐,加入催化剂和适量的酸催化剂,在一定温度和压力下进行反应,产生丁醇、辛醇和副产物。
乙烯异癸醇醇酸发酵反应是一个复杂的过程,其速度受到多种因素的影响,如反应温度、压力、酸催化剂的种类和浓度等。
通过对这些因素进行优化调控,可以提高丁辛醇的产率和选择性。
此外,还可以通过改变酸催化剂的种类和浓度,改变反应的速度和产物的比例。
在丁辛醇的生产过程中,酸醚酸化是一个非常重要的步骤。
酸醚酸化是指将丁醇和辛醇与过量的醋酸和浓硫酸反应,产生醋酸丁酯和醋酸辛酯。
该过程需要控制反应的温度、酸碱度和酸催化剂的浓度等条件,以避免副反应的发生。
在丁辛醇的生产过程中,还需要进行脱硫、脱碱、脱水等后续处理工艺,以提高产品的纯度和质量。
在脱硫工艺中,可以采用加氢脱硫、碳酸氢钠洗涤等方法,以去除硫化物的残留。
在脱碱工艺中,可以使用稀酸洗涤的方法,以去除碱性残留物。
在脱水工艺中,可以通过加热、蒸馏等方法,以去除水分。
丁辛醇的生产工艺技术研究还可从原料选择、反应条件优化、催化剂研究、废水处理等方面展开。
通过改进工艺流程、提高产品质量和选择性、降低生产成本和对环境的污染,可以提高丁辛醇的生产效益和竞争力。
总之,丁辛醇的生产工艺技术研究对于工业生产具有重要意义。
通过优化反应条件、改进工艺流程和后续处理方法,可以提高产品质量、降低生产成本、减少对环境的污染。
随着科学技术的不断进步,相信丁辛醇的生产工艺技术还将不断改进和创新,为相关产业的发展做出更大贡献。
丁醇精馏过程中的安全与环境风险评价
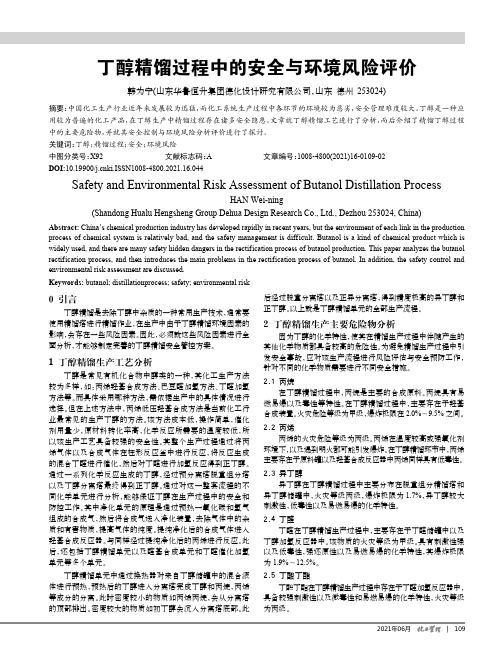
后经过脱重分离塔以及正异分离塔,得到精度极高的异丁醇和正丁醇。
以上就是丁醇精馏单元的全部生产流程。
2 丁醇精馏生产主要危险物分析因为丁醇的化学特性,使其在精馏生产过程中伴随产生的其他化学物质都具备较高的危险性。
为避免精馏生产过程中引发安全事故,应对该生产流程进行风险评估与安全预防工作,针对不同的化学物质需要进行不同安全措施。
2.1 丙烷在丁醇精馏过程中,丙烷是主要的合成原料。
丙烷具有易燃易爆以及毒性等特性。
在丁醇精馏过程中,主要存在于羟基合成装置。
火灾危险等级为甲级,爆炸极限在2.0%~9.5%之间。
2.2 丙烯丙烯的火灾危险等级为丙级。
丙烯在温度较高或强氧化剂环境下,以及遇到明火都可能引发爆炸。
在丁醇精馏环节中,丙烯主要存在于原料罐以及羟基合成反应器中丙烯同样具有低毒性。
2.3 异丁醇异丁醇在丁醇精馏过程中主要分布在脱重组分精馏塔和异丁醇储罐中,火灾等级丙级,爆炸极限为1.7%,异丁醇较大刺激性,低毒性以及易燃易爆的化学特性。
2.4 丁醛丁醛在丁醇精馏生产过程中,主要存在于丁醛储罐中以及丁醇加氢反应器中。
该物质的火灾等级为甲级。
具有刺激性强以及低毒性,强还原性以及易燃易爆的化学特性,其爆炸极限为1.9%~12.5%。
2.5 丁酸丁酯丁酸丁酯在丁醇精馏生产过程中存在于丁醛加氢反应器中,具备较强刺激性以及微毒性和易燃易爆的化学特性,火灾等级为丙级。
0 引言丁醇精馏是去除丁醇中杂质的一种常用生产技术,通常要使用精馏塔进行精馏作业,在生产中由于丁醇精馏环境因素的影响,会存在一些风险因素。
因此,必须就这些风险因素进行全面分析,才能够制定完善的丁醇精馏安全管控方案。
1 丁醇精馏生产工艺分析丁醇是常见有机化合物中醇类的一种,其化工生产方法较为多样,如:丙烯羟基合成方法、巴豆醛加氢方法、丁醛加氢方法等。
而具体采用哪种方法,需依据生产中的具体情况进行选择。
但在上述方法中,丙烯低压羟基合成方法是当前化工行业最常见的生产丁醇的方法。
丁辛醇生产工艺
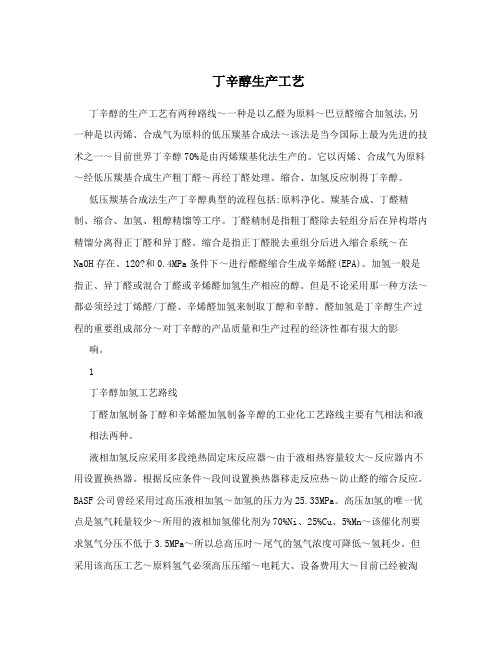
丁辛醇生产工艺丁辛醇的生产工艺有两种路线~一种是以乙醛为原料~巴豆醛缩合加氢法,另一种是以丙烯、合成气为原料的低压羰基合成法~该法是当今国际上最为先进的技术之一~目前世界丁辛醇70%是由丙烯羰基化法生产的。
它以丙烯、合成气为原料~经低压羰基合成生产粗丁醛~再经丁醛处理、缩合、加氢反应制得丁辛醇。
低压羰基合成法生产丁辛醇典型的流程包括:原料净化、羰基合成、丁醛精制、缩合、加氢、粗醇精馏等工序。
丁醛精制是指粗丁醛除去轻组分后在异构塔内精馏分离得正丁醛和异丁醛。
缩合是指正丁醛脱去重组分后进入缩合系统~在NaOH存在、120?和0.4MPa条件下~进行醛醛缩合生成辛烯醛(EPA)。
加氢一般是指正、异丁醛或混合丁醛或辛烯醛加氢生产相应的醇。
但是不论采用那一种方法~都必须经过丁烯醛/丁醛、辛烯醛加氢来制取丁醇和辛醇。
醛加氢是丁辛醇生产过程的重要组成部分~对丁辛醇的产品质量和生产过程的经济性都有很大的影响。
1丁辛醇加氢工艺路线丁醛加氢制备丁醇和辛烯醛加氢制备辛醇的工业化工艺路线主要有气相法和液相法两种。
液相加氢反应采用多段绝热固定床反应器~由于液相热容量较大~反应器内不用设置换热器。
根据反应条件~段间设置换热器移走反应热~防止醛的缩合反应。
BASF公司曾经采用过高压液相加氢~加氢的压力为25.33MPa。
高压加氢的唯一优点是氢气耗量较少~所用的液相加氢催化剂为70%Ni、25%Cu、5%Mn~该催化剂要求氢气分压不低于3.5MPa~所以总高压时~尾气的氢气浓度可降低~氢耗少。
但采用该高压工艺~原料氢气必须高压压缩~电耗大、设备费用大~目前已经被淘汰。
BASF公司和三菱化成工艺中醛的加氢采用中压液相加氢工艺~加氢压力为4.0-5.0MPa~加氢反应器形式采用填充床~反应温度为60-190?。
气相加氢法由于操作压力相对较低~工艺设备简单而被广泛应用。
目前~工业上丁辛醇装置上大多采用铜系催化剂气相加氢工艺。
如U.D.J联合工艺中采用低压气相加氢~压力为0.59-0.69MPa。
安庆曙光25万吨/年丁辛醇装置投料开车一次成功

安庆曙光25万吨/年丁辛醇装置投料开车一次成功
魏永忠
【期刊名称】《化工与医药工程》
【年(卷),期】2017(038)001
【摘要】安庆曙光25万吨/年丁辛醇项目于2016年12月16日9时28分正式开始投料,12月17日7时和17时分别产出合格丁醇和辛醇,开车一次成功。
【总页数】1页(P57-57)
【作者】魏永忠
【作者单位】
【正文语种】中文
【中图分类】TQ223.124
【相关文献】
1.以国际先进水平为目标以企业效益最大化为准绳──上海石化30万吨乙烯主体装置改扩建一次投料开车成功──创造同类型装置改扩建工期最短的国内新纪录[J], 沐晔;竹月;
2.仪化45万吨PTA装置投料开车一次成劝 [J], 无
3.中控在大型炼油装置上再创佳绩——中海油宁波大榭石化800万吨/年常减压蒸馏装置一次开车成功 [J], 无
4.安庆炼化曙光丁辛醇项目尾气和残液回收装置投料开车一次成功 [J], 无;
5.浙江从此产乙烯炼化产能冠全国镇海炼化100万吨乙烯工程投料开车一次成功[J], 杜志炎(等)
因版权原因,仅展示原文概要,查看原文内容请购买。
国内外丁辛醇市场及技术发展分析

国内外丁辛醇市场及技术开展分析随着需求的增长和技术的不断打破,世界丁辛醇产能已经接近800万吨/年,下游产品应用不断拓展和细化,支撑丁辛醇产业的继续开展。
中国是世界上丁辛醇产业开展居前列的国家,2021年产能已达158.5万吨/年,但仍然产缺乏需,国内企业新扩建积极性较高,预计到2021年还将有超过130万吨的新增产能。
中国丁辛醇市场的需求潜力同样让其他消费大国垂涎,因此企业在增产的同时,更应注重低能耗、低本钱、新技术的开发应用,着力进步产品竞争力。
丁辛醇是重要的根本有机化工原料,主要产品是正丁醇和辛醇。
正丁醇主要用于消费丁醛、丁酸、丁胺、醋酸丁酯、丙烯酸丁酯、邻苯二甲酸二丁酯、癸二酸二丁酯等有机化工产品,还被用作油脂、药物、香料的萃取剂,也可直接用作溶剂,在化工、医药、石油化工等方面具有广泛的用途。
异辛醇俗称辛醇,主要用于消费邻苯二甲酸二辛酯〔DOP〕、对苯二甲酸二辛酯〔DOTP〕、己二酸二辛酯〔DOA〕等增塑剂和丙烯酸辛酯、外表活性剂等,可用作照相造纸涂料和纺织等行业的溶剂,柴油和光滑油的添加剂,陶瓷行业釉浆分散剂、矿石浮选剂、消泡剂、清净剂等。
一、世界丁辛醇供需情况〔一〕消费才能2021年,世界丁醇的消费才能为399.5万吨/年。
丁醇产能主要集中在美国、西欧、中国,其中美国是最大的丁醇消费国,产能为110.3万吨/年,占世界产能的27.6%;而中国是丁醇开展最快的地区,产能从2003年的22万吨/年增加到2021年的61.5万吨/年,年均增长率25%.2021年,世界辛醇的消费才能为399.8万吨/年,产能集中在美国、西欧和日本,消费布局较为分散。
世界前4位辛醇消费商是中国石油、美国Oxea集团、韩国LG集团和德国BASF公司,全球98%的辛醇产能采用丙烯羰基合成法消费。
2021年世界正丁醇、辛醇主要消费企业产能情况见表1.〔二〕下游消费世界正丁醇消费比较集中,2021年世界丁醇产量为360.1万吨,需求量为358.3万吨,目前美国、西欧和日本消费量分别占总消费量的比例为34.2%、37.0%和11.3%,这3个国家和地区的丁醇市场已根本成熟,需求增长较缓,亚洲等其它地区由于供应缺口较大,需求增长迅速。
浅析丁辛醇装置的工艺与技术改造
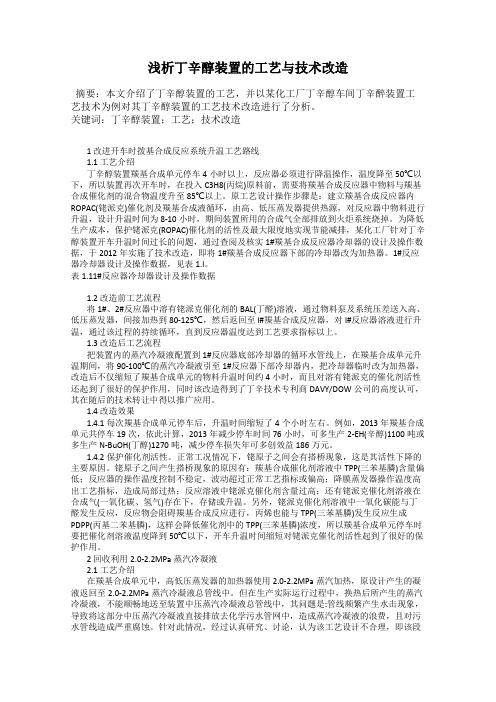
浅析丁辛醇装置的工艺与技术改造摘要:本文介绍了丁辛醇装置的工艺,并以某化工厂丁辛醇车间丁辛醉装置工艺技术为例对其丁辛醇装置的工艺技术改造进行了分析。
关键词:丁辛醇装置;工艺;技术改造1 改进开车时拨基合成反应系统升温工艺路线1.1 工艺介绍丁辛醇装置羰基合成单元停车4小时以上,反应器必须进行降温操作,温度降至50℃以下,所以装置再次开车时,在投入C3H8(丙烷)原料前,需要将羰基合成反应器中物料与羰基合成催化剂的混合物温度升至85℃以上。
原工艺设计操作步骤是:建立羰基合成反应器内ROPAC(铑派克)催化剂及羰基合成液循环,由高、低压蒸发器提供热源,对反应器中物料进行升温,设计升温时间为8-10小时,期间装置所用的合成气全部排放到火炬系统烧掉。
为降低生产成本,保护铑派克(ROPAC)催化剂的活性及最大限度地实现节能减排,某化工厂针对丁辛醇装置开车升温时间过长的问题,通过查阅及核实1#羰基合成反应器冷却器的设计及操作数据,于2012年实施了技术改造,即将1#羰基合成反应器下部的冷却器改为加热器。
1#反应器冷却器设计及操作数据,见表1.l。
表1.11#反应器冷却器设计及操作数据1.2 改造前工艺流程将1#、2#反应器中溶有铑派克催化剂的BAL(丁醛)溶液,通过物料泵及系统压差送入高、低压蒸发器,间接加热到80-125℃,然后返回至l#羰基合成反应器,对l#反应器溶液进行升温,通过该过程的持续循环,直到反应器温度达到工艺要求指标以上。
1.3 改造后工艺流程把装置内的蒸汽冷凝液配置到1#反应器底部冷却器的循环水管线上,在羰基合成单元升温期间,将90-100℃的蒸汽冷凝液引至1#反应器下部冷却器内,把冷却器临时改为加热器,改造后不仅缩短了羰基合成单元的物料升温时间约4小时,而且对溶有铑派克的催化剂活性还起到了很好的保护作用,同时该改造得到了丁辛技术专利商DAVY/DOW公司的高度认可,其在随后的技术转让中得以推广应用。
丁辛醇生产技术及其发展趋势
丁辛醇生产技术及其发展趋势1生产技术及发展趋势1.1生产技术丁辛醇是随着石油化工、聚氯乙烯材料工业以及羰基合成工业技术的发展而迅速发展起来的。
丁辛醇的工业化生产方法主要有乙醛缩合法、发酵法、齐格勒法和羰基合成法等。
1.1.1乙醛缩合法乙醛缩合法是乙醛在碱性条件下进行缩合和脱水生成丁烯醛(巴豆醛),丁烯醛加氢制得丁醇,然后经选择加氢得到丁醛,丁醛经醇醛缩合、加氢制得2-乙基己醇(辛醇)。
由于生产成本高,此方法已基本被淘汰。
1.1.2发酵法发酵法是粮食或其它淀粉质农副产品,经水解得到发酵液,然后在丙酮-丁醇菌作用下,经发酵制得丁醇、丙酮及乙醇的混合物,通常的比例为6:3:1,再经精馏得到相应产品。
由于石油化工业的迅猛发展,发酵法已很难与以丙烯为原料的羰基合成法竞争,因此近年来已很少采用该方法生产丁辛醇产品。
从长远看,发酵法的生存取决于其原料与丙烯的相对价格以及生物工程的发展程度。
1.1.3齐格勒法齐格勒丁辛醇生产方法是以乙烯为原料,采用齐格勒法生产高级脂肪醇,同时副产丁醇的方法。
1.1.4羰基合成法羰基合成法是当今最主要的丁辛醇生产技术。
丙烯羰基合成生产丁辛醇工艺过程:丙烯氢甲酰化反应,粗醛精制得到正丁醛和异丁醛,正丁醛和异丁醛加氢得到产品正丁醇和异丁醇;正丁醛经缩合、加氢得到产品辛醇。
丙烯羰基合成法又分为高压法、中压法和低压法。
丙烯羰基合成法的主流技术专利商如下:高压法:鲁尔 (Ruhr)技术、巴斯夫(BASF)技术、三菱(MCC)技术、壳牌(Shell)技术。
中压法:壳牌(Shell)技术、鲁尔-化学(Ruhr-chemic)技术、三菱(MCC)铑法技术。
低压法:雷普法(Reppe)技术、伊士曼(Eastman)技术、戴维(Davy UCC Johnson Matthey)技术、三菱化成(MCC)技术。
高压的羰基合成技术由于选择性较差、副产品(丙烷和高沸物)多,已被以铑为催化剂的低压羰基合成技术所取代。
丁辛醇的生产现状与供需分析
丁辛醇的生产现状与供需分析目前世界丁辛醇供需基本平衡,未来供需略石油公司或能源公司继续收购。
而以美国银行为代表的分析师认为,此次收购具有较强的战略互补性,显著提升了巴塞尔的竞争力。
无论最终结果如何,此次交易都是世界石化工业在高油价下持续重组的又一例证。
我国由于正丁醇下游市场丙烯酸酯及醋酸丁酯的较快发展、辛醇下游市场DOP随电石乙炔法PVC的快速扩能而需求增长较快。
近年国内丁辛醇年缺口分别保持在25 ~30万吨左右,未来 5 ~10年丁辛醇的投资将略有升温。
标签:丁辛醇;生产方法;供需1 丁辛醇生产方法概述工业上正丁醇有 5 种生产工艺,分别为粮食发酵法、乙醛醇醛缩合法、丙烯羰基合成法、雷珀法和乙烯齐聚制高级脂肪醇副产正丁醇。
辛醇主要有羰基合成法和乙醛缩合法 2 种生产工艺。
目前,羰基合成法是丁辛醇生产的主流工艺,其生产过程为丙烯和合成气羰基合成粗醛,精制得到正丁醛和异丁醛,分别加氢得到产品正丁醇和异丁醇。
根据羰基化反应压力和催化剂的不同,羰基合成法又分为高压钴法、中压法(改良钴法、改良铑法)、低压法(低压铑法、改进铑法)等工艺。
高压钴法由于污染大、能耗高,已被逐渐淘汰;中低压铑法具有温度低、压力低、速度高、正异构比高、副反应少、铑催化剂用量少寿命长、催化剂可回收再用以及设备少、投资省、丁醇和辛醇可切换生产等特点,已成为丁辛醇合成技术的主流。
目前世界主要的丙烯羰基合成法为中压法(以鲁尔技术为代表,1984 年开发,1988 年工业应用)、低压法(以Davy 技术、巴斯夫技术、三菱化成和伊士曼为代表,于1976 年工业应用)。
现今世界液相循环低压改性铑法是最先进、最广泛采用的技术。
2 国内外丁辛醇生产现状2.1 国内丁辛醇生产现状我国从20世纪50年代中期开始用粮食发酵法生产丁醇。
60年代中期吉化公司电石厂从法国引进7 000 t/a乙醛缩合法丁辛醇生产装置,1982年吉化化肥厂从德国BASF公司引进5万t/a高压钴法装置,大庆、齐鲁分别引进英国DA VY公司低压铑气相循环法装置,生产能力各为5万t/a。
年产25万吨丁醇生产工艺
制定具体的养护方案直螺纹接头的加工1.前言丁醇是重要的有机化工原料,广泛用于医药、印染、塑料、有机等领域。
丁醇是生产丁酸、丁胺、醋酸丁酯和丙烯酸丁酯等多种有机化合物的原料。
丁醇分为两类:正丁醇和异丁醇。
正丁醇主要用来生产邻苯二甲酸二丁酯、丙烯酸丁酯等。
可直接作为合成塑料、涂料、助剂等的原料,也是良好的溶剂之一,大部分正丁醇是用来合成酯类,产品有丙烯酸丁酯、醋酸丁酯、乙醇醚、增塑剂DBP 等。
丁醇在许多化工领域得到了广泛应用,在2000年之前,全球丁醇生产主要集中在美国、欧洲、日本等地,这些地区丁醇市场趋于成熟,生产能力过剩,需求增长趋缓,而亚洲等其他地区,由于缺口较大,需求增长较快。
在中国,特别是改革开放以来,随着石化工业的快速发展,对丁醇的需求越来越大,因而引进了国外先进技术,相继建成了一批大型乙烯生产装置,其中有的配套了代表国际先进水平的羰基合成丁醇生产装置,如齐鲁石化公司、吉林化纤工业公司及大庆石油化工总厂、北京化工四厂、扬子巴斯夫公司,总产能为145kt/年,由于下游需求的快速增长,尽管这几套装置都在加大负荷生产,丁醇的产量有很大提高,但一直不能满足下游实际生产的需求,因而对这几套装置进行扩能改造、或新建生产装置势在必行。
2.设计基础条件2.1原料简介丙烯(propylene,CH2=CHCH3)常温下为无色、稍带有甜味的气体。
分子量42.08,密度0.5139g/cm3(20/4℃),冰点-185.3℃,沸点-47.4℃。
易燃,爆炸极限为2%~11%。
不溶于水,溶于有机溶剂,是一种属低毒类物质。
丙烯是三大合成材料的基本原料,主要用于生产丙烯腈、异丙烯、丙酮和环氧丙烷等。
2.2产品简介本项目产品为正丁醇和异丁醇,均为重要的有机化工原料,在医药工业、塑料工业、有机工业、印染等方面具有广泛用途。
2.2.1 正丁醇正丁醇是优良的有机溶剂,也可转化为丁醇衍生物作特种溶剂;可用于生产多种增塑剂,如邻苯二甲酸二丁酯(DBP )、邻苯二甲酸丁苄酯(BBP )、邻苯二甲酸丁辛酯、己二酸二丁酯等;也可用于生产乙酸丁酯、丙烯丁酯、甲基丙烯酸丁酯等化工产品,其主要衍生物系及用途见图1-1。
丁辛醇装置工艺优化策略
丁辛醇装置工艺优化策略摘要:本文介绍低压羰基合成生产丁辛醇的生产工艺进展情况,对比了四种工艺技术。
液相低压羰基合成法是以丙烯、合成气为原料,以铑为催化剂,是低压羰基合成的进一步改进。
具有反应器容积小、产率高、能耗低、反应温度低、原料消耗低等诸多优点,是目前生产丁辛醇的主要方法。
关键词:丁辛醇低压羰基合成液相循环1.丁辛醇装置优化后工艺概述大庆石化公司化工二厂丁辛醇装置采用世界较为先进的LP OxoSM SELECTORSM 10液体循环技术,生产2-乙基己醇(俗称辛醇)和正丁醇,它以丙烯和合成气为原料,在铑、三苯基膦催化剂的作用下,发生羰基合成反应生成混合丁醛,丁醛经过丁醛异构物分离得到高纯度正丁醛,在0.2×10-2mol的NaOH溶液作用下,发生缩合反应生成辛烯醛,辛烯醛在铜基催化剂作用下与H2发生加氢反应生成粗辛醇,再经过精制后得到产品辛醇;丁醛异构物塔顶分离出的混合丁醛再进入丁醇异构物塔精分离正异丁醛,塔顶异丁醛外送至新戊二醇装置,塔底正丁醛经加氢、精制得到正丁醇产品。
2.丁辛醇主要产品的性质与用途丁醇和辛醇(辛醇俗称辛醇,2-乙基己醇)由于可以在同一套装置中用羰基合成的方法生产,故习惯成为丁辛醇。
丁/辛醇是重要的有机化工原料,在医药工业、塑料工业、有机工业、印染等方面具有广泛应用。
①正丁醇分子式:C4H9OH,分子量:74.12。
物理性质:无色透明油状液体,有刺激性气味,与水可形成共沸物。
正丁醇为粘度稍大的无色液体;熔点-89.5℃,沸点117.2℃,相对密度0.8098(20/4℃),临界温度287.10℃、临界压力5×106Pa。
用途:可用作溶剂、生产邻苯二甲酸二丁酯(DBP)、邻苯二甲酸丁苄酯(BBP)等增塑剂及醋酸丁酯、甲基丙烯酸丁酯等化学品。
②辛醇分子式:C8H17OH,分子量:130.23。
物理性质:无色透明油状液体,有刺激性气味,与水可形成共沸物。
冰点-76℃、沸点185℃(标准大气压下)、自燃点270℃、闪点85℃、液体密度832.8kg/m3(20℃)、熔点-70℃、临界温度377℃、临界压力3.53×106Pa、比重0.8340。
- 1、下载文档前请自行甄别文档内容的完整性,平台不提供额外的编辑、内容补充、找答案等附加服务。
- 2、"仅部分预览"的文档,不可在线预览部分如存在完整性等问题,可反馈申请退款(可完整预览的文档不适用该条件!)。
- 3、如文档侵犯您的权益,请联系客服反馈,我们会尽快为您处理(人工客服工作时间:9:00-18:30)。
25万吨/年丁辛醇工艺分析及优化
丁辛醇是重要基本的有机化工原材料,在化工、石油、医药等方面具有非常广泛的用途。
以惠生(南京)化工有限公司年产25万吨丁辛醇装置研究为对象,通过分析比较不同丁辛醇合成工艺及装置的特点和运行要求,选择了 DAVY/DOW 丙烯铑低压羰基合成-液相循环工艺技术,确定了工艺流程,计算该工艺的生产消耗及物料平衡。
根据年产25万吨丁辛醇生产要求,设计了羰基合成反应器,研究了影响羰基合成反应的因素,包括原料杂质、合成气中氢碳比、温度、压力、三苯基膦浓度及铑催化剂失活对羰基合成反应的影响,并提出了相应改善措施,以保证装置安全、稳定、长周期、满负荷、优化运行。
介绍了羰基合成催化剂失活原因,并简单阐述了本装置催化剂回收方式。