化学气相沉积
第10章化学气相沉积
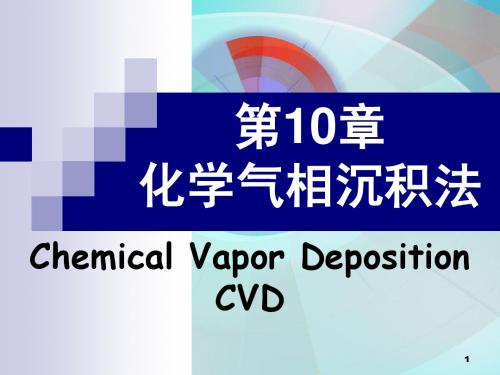
18
(4)
金属的羰基化合物 金属薄膜
(180 oC)
Ni(CO)4
Ni(s) + 4CO(g)
Pt(CO)2Cl2 Pt(s) + 2CO(g)+Cl2
19
(600 oC)
(5)
金属的单氨配合物
氮化物
GaCl3· NH3 GaN + 3HCl (800~900 oC)
AlCl3· NH3 AlN + 3HCl oC) (800~1000
28
5. 等离子体增强的反应沉积
低真空,利用直/交流电、射频、微波
等实现气体放电产生等离子体
PECVD大大降低沉积温度 例
SiH4+ x N2O
~350º C
通常850º C 350º C
–– SiOx+…
SiH4 ––– -Si + 2H2 用于制造非晶硅太阳能电池
29
6. 其他能源增强的反应沉积
超纯多晶硅的CVD生产装置
37
超纯多晶硅的沉积生产装置
沉积反应室: 钟罩式的常压装置,中间是由三段 硅棒搭成的倒u型,从下部接通电源使硅棒保持 在1150℃左右,底部中央是一个进气喷口,不断 喷人三氯硅烷和氢的混合气,超纯硅就会不断被 还原析出沉积在硅棒上; 最后得到很粗的硅锭或硅块用于拉制半导体硅单 晶。
31
CH4
800~1000º C
–––
C (碳黑)+ 2H2
CH4
热丝或等离子体 800~1000º C
–––
C (金刚石)+ 2H2
32
其它能源增强的反应沉积
其它各种能源,例如: 火焰燃烧法,或热丝法都可以实现增强沉 积反应的目的。 燃烧法主要是增强反应速率。利用外界能 源输入能量,有时还可以改变沉积物的品 种和晶体结构。
化学气相沉积

现代表面工程技术
CVD技术的热动力学
物体因 自身温度 而
具有向外发射能量的 本领,这种热传递的 方式叫做热辐射。利 用热源的热辐射来加 热,是另一种常用的 方法 .
单位面积的能量辐射=Er=hr(Ts1- Ts2)
材料科学与工程学院 现代表面工程技术
CVD技术的热动力学
两种常见的流体流动方式
热传导是固体中热传递的主要方式,是将基 片置于经加热的晶座上面,借着能量在热导 体间的传导,来达到基片加热的目的
材料科学与工程学院 现代表面工程技术
CVD技术的热动力学
热能传递主要有传导、对流、辐射三种方式
热传导是固体中 热传递的主要方 式,是将基片置 于经加热的晶座 上面,借着能量 在热导体间的传 导,来达到基片 加热的目的
热传导方式来进行基片加热的装置
单位面积能量传递=
Ecod
T kc X
材料科学与工程学院
材料科学与工程学院 现代表Sh « 1所发生的情形, 决 于 CVD 反 应 的 速 率 ,所以称为“表面反 应限制”
Sh
» 1所繁盛的情形,因
涉及气体扩散的能力 ,故称为“扩散限制 ”,或“质传限制”
(a) CVD反应为表面反应限制时和 (b)当CVD反应为扩散限制时,反应气 体从主气流里经边界层往基片表面扩 散的情形
材料科学与工程学院 现代表面工程技术
返回
CVD物理化学基础
CVD反应方式:
热分解反应 氧化还原反应 化学合成反应 化学输运反应 等离子增强反应 其他能源增强增强反应
材料科学与工程学院
Cd(CH3 )2 +H2S CdS+2CH4
4750C
325~475 C SiH4 +2O2 SiO2 +2H 2O
化学气相沉积

缓且不明显。
4.2 化学气相沉积原理
CVD反应的进行涉及到能量、动量及质量的传递。反应气体是 借着扩散效应来通过主气流与基片之间的边界层,以便将反学气相沉积合成方法发展
20世纪50年代 主要用于道具
涂层
古人类在取暖 或烧烤时在岩 洞壁或岩石上
的黑色碳层
近年来PECVD 、LCVD等高
速发展
20世纪60-70 年代用于集成
电路
80年代低压 CVD成膜技术 成为研究热潮
2
4.2 化学气相沉积原理
一、基本概念
化学气相沉积(CVD):
14
4.2 化学气相沉积原理
二、化学气相沉积法原理
2、CVD技术的热动力学原理
CVD反应结构分解:
不同物质状态的边界层对CVD沉积至关重要。所谓边界层,就是流体及物 体表面因流速、浓度、温度差距所形成的中间过渡范围。 (a)反应物已扩散通过界面边界层; (b)反应物吸附在基片的表面; (c)化学沉积反应发生; (d) 部分生成物已扩散通过界面边界层; (e)生成物与反应物进入主气流里,并离开系统 。
流速与流向均 平顺者称为 “层流”;
流动过程中产 生扰动等不均 匀现象的流动 形式,则称为
其中,d为流体流经的管径,ρ为流体的密度,
“湍流”。
ν为流体的流速,μ则为流体的粘度
两种常见的流体流动方式
20
4.2 化学气相沉积原理
假设流体在晶座及 基片表面的流速为 零,则流体及基片 (或晶座)表面将 有一个流速梯度存 在,这个区域便是 边界层。
其中:hc为“对流热传系数”
19
4.2 化学气相沉积原理
二、化学气相沉积法原理 2、CVD技术的热动力学原理
化学气相沉积

集成电路芯片工艺化学气相沉积(CVD)化学汽相淀积(CVD)化学汽相淀积是指通过气态物质的化学反应在衬底上淀积一层薄膜材料的过程。
CVD膜的结构可以是单晶、多晶或非晶态,淀积单晶硅薄膜的CVD过程通常被称为外延。
CVD技术具有淀积温度低、薄膜成分和厚度易于控制、均匀性和重复性好、台阶覆盖优良、适用范围广、设备简单等一系列优点。
利用CVD方这几乎可以淀积集成电路工艺中所需要的各种薄膜,例如掺杂或不掺杂的SiO:、多晶硅、非晶硅、氮化硅、金属(钨、钼)等。
一:化学气相沉积方法常用的CVD方法主要有三种:常压化学汽相淀积(APCVD)、低压化学汽相淀积(LPCVIi~)和等离子增强化学汽相淀积(PECVD).APCVD反应器的结构与氧化炉类似,如图1-1所示,该系统中的压强约为一个大气压,因此被称为常压CVD。
气相外延单晶硅所采用的方法就是APCVD。
图1-1APCVD反应器的结构示意图,LPCVD反应器的结构如图1-2所示,石英管采用三温区管状炉加热,气体由一端引入,另一端抽出,半导体晶片垂直插在石英舟上。
由于石英管壁靠近炉管,温度很高,因此也称它为热壁CVD装置,这与利用射频加热的冷壁反应器如卧式外延炉不同.这种反应器的最大特点就是薄膜厚度的均匀性非常好、装片量大,一炉可以加工几百片,但淀积速度较慢.它与APCVD的最大区别是压强由原来的1X10SPa降低到1X102Pa左右。
图1-2LPCVD反应器的结构示意图图1-3平行板型PECVD反应器的结构示意图PECVD是一种能量增强的CVD方法,这是因为在通常CVD系统中热能的基础上又增加了等离子体的能量.图1-3给出了平行板型等离子体增强CVD反应器,反应室由两块平行的金属电极板组成,射频电压施加在上电极上,下电极接地。
射频电压使平板电极之间的气体发生等离子放电。
工作气体由位于下电极附近的进气口进入,并流过放电区。
半导体片放在下电极上,并被加热到100—400;C左右.这种反应器的最大优点是淀积温度低。
化学气相沉积法
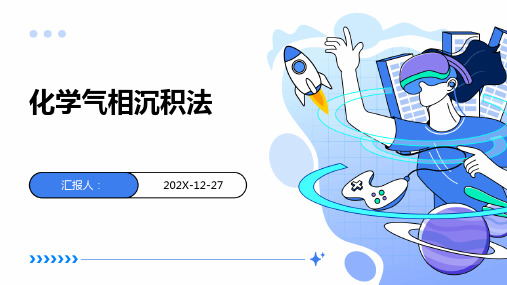
时间与速率
要点一
总结词
时间和沉积速率在化学气相沉积过程中具有重要影响,它 们决定了薄膜的厚度和均匀性。
要点二
详细描述
时间和沉积速率决定了化学气相沉积过程中气体分子在反 应器中的停留时间和沉积时间。较长的停留时间和较慢的 沉积速率有利于气体分子充分反应和形成高质量的薄膜。 然而,过长的停留时间和过慢的沉积速率可能导致副反应 或降低沉积速率。因此,选择合适的时间和沉积速率是实 现均匀、高质量薄膜的关键。
05
化学气相沉积法优 缺点
优点
适用性广
涂层性能优良
化学气相沉积法适用于各种材料表面改性 和涂层制备,如金属、陶瓷、玻璃等。
通过控制化学气相沉积的条件,可以制备 出具有高硬度、高耐磨性、高抗氧化性的 涂层。
环保
高效
化学气相沉积法使用的原料在高温下分解 ,不会对环境造成污染。
化学气相沉积法具有较高的沉积速率,可 实现快速涂层制备。
应用领域
半导体产业
用于制造集成电路、微 电子器件和光电子器件
等。
陶瓷工业
制备高性能陶瓷材料, 如氧化铝、氮化硅等。
金属表面处理
在金属表面形成耐磨、 防腐、装饰等功能的涂
层。
其他领域
在航空航天、能源、环 保等领域也有广泛应用
。
02
化学气相沉积法分 类
热化学气相沉积法
原理
在较高的温度下,使气态的化 学反应剂与固态表面接触,通 过气相反应生成固态沉积物。
缺点
高温要求
化学气相沉积法需要在高温下进行,这可能会对 基材产生热损伤或变形。
操作难度大
化学气相沉积法需要精确控制反应条件,操作难 度较大。
ABCD
设备成本高
化学气相沉积(CVD)技术梳理

化学气相沉积(CVD)技术梳理1. 化学气相沉积CVD的来源及发展化学气相沉积(Chemical Vapor Deposition)中的Vapor Deposition意为气相沉积,其意是指利用气相中发生的物理、化学过程,在固体表面形成沉积物的技术。
按照机理其可以划分为三大类:物理气相沉积(Physical Vapor Deposition,简称PVD),化学气相沉积(Chemical Vapor Deposition,简称CVD)和等离子体气相沉积(Plasma Chemical Vapor Deposition,简称PCVD)。
[1]目前CVD的应用最为广泛,其技术发展及研究也最为成熟,其广泛应用于广泛用于提纯物质、制备各种单晶、多晶或玻璃态无机薄膜材料。
CVD和PVD之间的区别主要是,CVD沉积过程要发生化学反应,属于气相化学生长过程,其具体是指利用气态或者蒸汽态的物质在固体表面上发生化学反应继而生成固态沉积物的工艺过程。
简而言之,即通过将多种气体原料导入到反应室内,使其相互间发生化学反应生成新材料,最后沉积到基片体表面的过程。
CVD这一名称最早在Powell C F等人1966年所著名为《Vapor Deposition》的书中被首次提到,之后Chemical Vapor Deposition才为人广泛接受。
[2]CVD技术的利用最早可以被追溯到古人类时期,岩洞壁或岩石上留下了由于取暖和烧烤等形成的黑色碳层。
现代CVD技术萌芽于20世纪的50年代,当时其主要应用于制作刀具的涂层。
20世纪60~70年代以来,随着半导体和集成电路技术的发展,CVD技术得到了长足的发展和进步。
1968年Nishizawa课题组首次使用低压汞灯研究了光照射对固体表面上沉积P型单晶硅膜的影响,开启了光沉积的研究。
[3] 1972年Nelson和Richardson用CO2激光聚焦束沉积碳膜,开始了激光化学气相沉积的研究。
化学气相沉积CVD
3. PECVD装置 普通CVD+高频电源(用于产生等离子体)
图8.3.4 卧式管状PECVD装置
用高频产生辉光放电等离子体的卧式反应 器,用于沉积氮化硅等薄膜。
在 350~400℃的低温下,以50~ 100nm/min的沉积速率进行成膜。
图8.3.5 立式PECVD反应器
SiH4生长Si外延层的立式管状 PECVD反 应器,当T=650℃,P<1.3Pa时,可得 到均匀优质的硅外延层。
(3) PECVD工艺的主要缺点是:由于等离子体轰击,使沉 积膜表面产生缺陷,反应复杂,也会使薄膜的质量有 所下降。
PECVD是20世纪80年代崛起的新沉积制膜
技术,特别适用于金属化后钝化膜和多层布 线介质膜的沉积!
18
三、光CVD(PCVD)
光化反应:用光束来激活反应物,促进生成物形成的化学反 应。
相沉积中的最简单形式,例如:
SiH4 (气) 800℃~1200℃ Si(固)+2H2 ↑
2
Ni(CO)4(气) 190~240℃ Ni(固)+4 CO↑ CH4(气) 900~1200℃ C(固)+2H2 ↑ TiI4(气) 加热 Ti(固)+2I2 ↑
用作热分解反应沉积的气态化合物原料主要有: 硼的氯化物,氢化物; 第IV族大部分元素的氢化物和氯化物; VB、VIB族的氢化物和氯化物; 铁、镍、钴的羰基化合物和羰基氯化物; 以及铁、镍、铬、铜等的金属有机化合物等。
12
2024/10/15
13
5. CVD的优缺点
(1)优点: ① 膜层纯度一般很高,很致密,容易形成结晶定向好的材料;
例如:用蓝宝石作基片,用CVD制备的-Al2O3单晶材料, 其杂质含量为30~34ppm,远小于蓝宝石本身的杂质含量; ② 能在较低温度下制备难熔物质;
5.5.2-化学气相沉淀法
ZnI2(g)+1/2Se2(g)
二、化学气相沉积的工艺方法
不同的涂层,其工艺方法一般不相同。但他们有一些共性,即每一 个CVD系统都必须具备如下功能: ①将反应气体及其稀释剂通入反应器,并能进行测量和调节; ②能为反应部位提供热量,并通过自动系统将热量反馈至加热源,以控制 涂覆温度。 ③将沉积区域内的副产品气体抽走,并能安全处理。 此外,要得到高质量的CVD膜,CVD工艺必须严格控制好几个主要参量: ①反应器内的温度。 ②进入反应器的气体或蒸气的量与成分。 ③保温时间及气体流速。 ④低压CVD必须控制压强。
原理:CVD是利用气态物质在固体表面进行化学 反应,生成固态沉积物的过程。
三个步骤
3.挥发性物质
在基体上发生 化学反应
1.产生挥发 性物质
2.将挥发性物质 运到沉积区
CVD化学反应中须具备三个挥发性条件: (1)反应产物具有足够高的蒸气压 (2)除了涂层物质之外的其他反应产物必须是挥发性的
(3)沉积物具有足够低的蒸气压
1 、热分解:
SiH4
>500℃
Si + H2
﹙在800—1000℃成膜﹚
CH3SiCl3 1400℃
SiC+3HCl
2 、还原反应:
WF6+3H2 SiCl4+2Zn W+6HF
﹙氢还原﹚
Si+2ZnCl2 ﹙金属还原﹚
3 、氧化反应:
SiH4+O2 SiCl4+O2 SiO2+2H2 SiO2+2Cl2 Ge﹙s,g﹚+GeI4﹙g﹚
特点:反应气体混合物能够连续补充,同时废弃的
反应产物能够不断地排出沉积室,反应总是处于 非平衡状态。
化学气相沉积CVD
围以及避免了基片变形问题。
SEIEE
化学气相沉积——基本原理
(3)氢化物和金属有机化合物系统
630 675℃ Ga(CH3 )3 + AsH3 GaAs + 3CH4 475℃ Cd(CH3 )2 + H2S CdS + 2CH4
广泛用于制备化合物半导体薄膜。 ( 4 )其它气态络合物、复合物(贵金属、过渡金属沉积)
原则上可制备任一种无机薄膜。
SEIEE
化学气相沉积——基本原理
化学输运反应
将薄膜物质作为源物质(无挥发性物质),借助适当 的气体介质(输运剂)与之反应而形成气态化合物,这种 气态化合物经过化学迁移或物理输运到与源区温度不同的 沉积区,在基片上再通过逆反应使源物质重新分解出来, 这种反应过程称为化学输运反应。
1000 ℃ SiCl 2 H Si 4HCl 4 2
H、Cl、Si三元体系
SEIEE
化学气相沉积——基本原理
CVD的(化学反应)动力学
反应动力学是一个把反应热力学预言变为现实,使反 应实际进行的问题;它是研究化学反应的速度和各种因素 对其影响的科学。 动力学的因素决定了上述过程发生的速度以及他在有限时 间内可进行的程度 CVD 反应动力学分析的基本任务是:通过实验研究薄 膜的生长速率,确定过程速率的控制机制,以便进一步调 整工艺参数,获得高质量、厚度均匀的薄膜。
其自由能变化
ΔGr=cGc-bGb-aGa
Gi Gi0 RT ln ai
SEIEE
化学气相沉积——基本原理
Gr 与反应系统的化学平衡常数K有关
G RT ln K
K Pi (生成物)iBiblioteka 1 n或m j 1 j
化学气相沉积CVD
化学气相沉积1 前言化学气相沉积CVD(Chemical Vapor Deposition)是利用加热,等离子体激励或光辐射等方法,使气态或蒸汽状态的化学物质发生反应并以原子态沉积在置于适当位置的衬底上,从而形成所需要的固态薄膜或涂层的过程。
一般地说,化学气相沉积可以采用加热的方法获取活化能,这需要在较高的温度下进行;也可以采用等离子体激发或激光辐射等方法获取活化能,使沉积在较低的温度下进行。
另外,在工艺性质上,由于化学气相沉积是原子尺度内的粒子堆积,因而可以在很宽的范围内控制所制备薄膜的化学计量比;同时通过控制涂层化学成分的变化,可以制备梯度功能材料或得到多层涂层。
在工艺过程中,化学气相沉积常常在开放的非平衡状态下进行,根据耗散结构理论,利用化学气相沉积可以获得多种晶体结构。
在工艺材料上,化学气相沉积涵盖无机、有机金属及有机化合物,几乎可以制备所有的金属(包括碳和硅),非金属及其化合物(碳化物、氮化物、氧化物、金属间化合物等等)沉积层。
另外,由于气态原子或分子具有较大的转动动能,可以在深孔、阶梯、洼面或其他形状复杂的衬底及颗粒材料上进行沉积。
为使沉积层达到所需要的性能,对气相反应必须精确控制。
正是由于化学气相沉积在活化方式、涂层材料、涂层结构方面的多样性以及涂层纯度高工艺简单容易进行等一系列的特点,化学气相沉积成为一种非常灵活、应用极为广泛的工艺方法,可以用来制备各种涂层、粉末、纤维和成型元器件。
特别在半导体材料的生产方面,化学气相沉积的外延生长显示出与其他外延方法(如分子束外延、液相外延)无与伦比的优越性,即使在化学性质完全不同的衬底上,利用化学气相沉积也能产生出晶格常数与衬底匹配良好的外延薄膜。
此外,利用化学气相沉积还可生产耐磨、耐蚀、抗氧化、抗冲蚀等功能涂层。
在超大规模集成电路中很多薄膜都是采用CVD方法制备。
经过CVD 处理后,表面处理膜密着性约提高30%,防止高强力钢的弯曲,拉伸等成形时产生的刮痕。
- 1、下载文档前请自行甄别文档内容的完整性,平台不提供额外的编辑、内容补充、找答案等附加服务。
- 2、"仅部分预览"的文档,不可在线预览部分如存在完整性等问题,可反馈申请退款(可完整预览的文档不适用该条件!)。
- 3、如文档侵犯您的权益,请联系客服反馈,我们会尽快为您处理(人工客服工作时间:9:00-18:30)。
化学气相沉积作为一种非常有效的材料表 面改性方法,具有十分广阔的发展应用前景。 随着工业生产要求的不断提高, CVD 的工艺 及设备得到不断改进, 现已获得了更多新的 膜层, 并大大提高了膜层的性能和质量,它 对于提高材料的使用寿命、改善材料的性 能、节省材料的用量等方面起到了重要的 作用,下一步将向着沉积温度更低、有害生 成物更少、规模更大等方向发展。随着各 个应用领域要求的不断提高, 对化学气相沉 积的研究也将进一步深化,CVD 技术的发展 和应用也将跨上一个新的台阶。
2、CVD过程 反应气体向基体表面扩散
反应气体吸附于基体表面
在基体表面上产生的气相副产物脱离表面
留下的反应产物形成覆层
3、CVD几种典型化学反应
1)热分解
SiH4 >500℃ Si + 2H2 (在900-1000℃成膜) CH3SiCl3 1400℃ SiC + 3HCl
2)还原
WF6 +3H2 SiCl4 + 2Zn WF6 + 3 Si 2 W + 6HF (氢还原) Si + 2ZnCl2 (金属还原) SiF4 (基体材料还原) W+3 2
反应沉积成膜 反应沉积成膜
3、PCVD的特点
成膜温度低
沉积速率高 膜层结合力高
膜层质量好 能进行根据热力学规律难以发生的反应
4、PCVD与CVD装置结构相近, 只是需要增加能产生等离子体 的反应器。用于激发CVD反应 的等离子体有: 直流等离子体 射频等离子体 微波等离子体 脉冲等离子体
直流等离子体法(DCPCVD)
2、PCVD的成膜步骤 等离子体产生 等离子体产生
辉光放电的压力较低,加 速了等离子体的质量 输送和扩散
外电场提高能量,利用低压 气体的辉光放电产生等 离子体
等离子体扩散 等离子体扩散
气相物质被激活 气相物质被激活
活体粒子在基体表面发 生化学反应,形成膜 层 利用直流、射频、激光 等手段,激活反应 气体
金刚石
5、PCVD的重要应用 • 绝缘薄膜的PCVD沉积
在低温下沉积氮化硅、氧 化硅或硅的氮氧化物一类的绝缘薄膜,对于超大规模集 成芯片(VLSI)的生产是至关重要的。
• 非晶和多晶硅薄膜的PCVD沉积 • 金刚石和类金刚石的PCVD沉积 • 等离子体聚合 等离子体聚合技术正越来越广泛的应
用于开发具有界电特征、导电特性、感光特性、光电转 换功能或储存器开关功能的等离子体聚合膜和一些重要 的有机金属复合材料。
Ⅰ
热化学气相沉积(TCVD)
热化学气相沉积是指采用衬底表面热催 化方式进行的化学气相沉积。 一般在800~2000℃的高温反应区,利 用电阻加热,高频感应加热和辐射加热的 化学气相沉积。这样的高温使衬底的选择 受到很大限制,但它是化学气相沉积的经 典方法。 应用于半导体和其他材料。
TCVD装置包括三个 相互关联的部分: 气体供应系统、反 应室及排气系统
特点
反应温度低 膜均匀 附差性良好 反应温度低 相同温度比CVD沉 积速度快近2倍 反应气体活化程度 高
沉积膜
TiC
TiC(500℃) TiN(300℃) Si2N4
脉冲等离子 体
沉积温度:室温 激发温度10000K
脉冲半周能耗1800-2700J
沉积温度低 膜厚均匀 附着性良好 膜硬度高、光滑, 纯度不高
MWPCVD装置示意图
可进一步降低基材温度、原子的扩散能力,减少空位、错位等缺陷
电极不会受到污染,受等离子体的破坏小,薄膜的完整性高 适于制备低熔点和高温下不稳定的化合物薄膜
PCVD的激发方式的工作参数及特性
激发方式 直流等离子 体 射频等离子 体 微波等离子 体
工艺参数
沉积温度/速率500-600℃/ 2-5µ m/h 直流电压/4000V/16-49A•mˉ² 真空1.33×10ˉ²-100Pa 沉积温度/速率300-500℃/ 1-3µ m/h 频率13.56MHz 射频功率500W 磁控管 2450MHz微波
• MOCVD可构成复合结构的表面膜,创造出 新的功能材料。 • 与常规CVD相比,MOCVD的特点主要是:
①沉积温度低 ②能沉积单晶、多晶、非晶的多层和超薄膜 ③可大规模低成本制备复杂组分的薄膜和化合物 半导体材料 ④沉积速度慢,仅适宜沉积微米级的表面层
⑤原料的毒性较大
• MOCVD的应用 MOCVD作为气相外延独特的沉积技术, 主要应用于Ⅲ~Ⅴ族及Ⅱ~Ⅵ族半导体化合 物材料的气相外延。除此之外,当衬底不 能承受热CVD所需要的高温时,MOCVD也 用于沉积各种金属、氧化物、硅化物和碳 化物等涂层。
TCVD系统
典型的TCVD装 置示意图
Ⅱ
低压化学气相沉积(LPCVD)
LPCVD压力范围一般在1Pa~4×10000Pa之 间。由于低压下分子平均自由程增加,因而加快 了气态分子的运输过程,反应物质在工件表面的 扩散系数增大,使薄膜均匀性得到改善。对于表 面扩散动力学控制的外延生长,可增大外延层的 均匀性,这在大面积大规模外延生长中(例如大 规模硅器件工艺中的介质膜外延生长)是必要的。 但对于由质量输送控制的外延生长,上述效应并 不明显。
微波等离子体法(MWPCVD)
• 用微波放电产生等离子体激活化学反应进 行气相沉积的技术。 • 微波放电无电极,放电气压范围宽,能量 转换率高,能产生高密度等离子体。 • 微波等离子体比射频等离子体气体离子化 高,放电非常稳定,等离子体可以不与器 壁接触,有利于制备高质量薄膜。 • 微波等离子体可在10¯ ³ Pa至大气压的压力范 围内产生。
化学气相沉积
Chemical Vapor Deposition , CVD
主要内容:
CVD的基本原理 CVD的特点 CVD方法 CVD的现状和展望
一、CVD的基本原理
化学气相沉积(Chemical Vapor Deposition ,CVD ) 利用气态物质在一固体表面上进行化学反应,生成 固态沉积物的过程。
LPCVD适于单晶 硅、多晶硅和氮化 硅等超大规模集成 电路的制造 可精确控制膜层 的成分和结构
对设备要求高,须 有精确的压力控制 系统,成本高
LPCVD装置示意图
Ⅲ
等离子体化学气相沉积(PCVD)
1、基本原理 PCVD是将低压气体放电等离子体应用于化 学气相沉积中的技术,它是用辉光放电产生的等 离子体激活气体分子,使化学气相的化学反应在 低的温度下进行,因而也称等离子增强化学气相 沉积(PECVD)。 这是一种高频辉光放电物理过程与化学反应 相结合的技术。
激光热解机制示意图
大多要求能打断反应气 体分子化学键的足够 能量的光子紫外光
激光光解机制示意图
与常规CVD相 比,LCVD可大 大降低基材的温 度,可在不能 承受高温度基 材上合成薄膜
LCVD装置示意图
与PCVD相比,LCVD可避免高能粒子辐照对薄膜 的损伤,更好的控制薄膜的结构,提高薄膜的纯度
LCVD的应用 LCVD是近年来迅速发展的先进表面沉 积技术,其应用前景广阔。在太阳能电池、 超大规模集成电路、特殊的功能膜及光学 膜、硬膜及超硬膜等方面都有重要的应用。
四、CVD的现状和展望
气相沉积膜附着力强,厚度均匀,质量好, 沉积速率快,选材广,环境污染轻,可以 满足许多现代工业、科学发展提出的新要 求,因而发展相当迅速。它能制备耐磨膜、 润滑膜、耐蚀膜、耐热膜、装饰膜以及磁 性膜、光学膜、超导膜等功能膜,因而在 机械制造工业电子、电器、通讯、航空航 天、原子能、轻工等部门得到广泛的应用。
Ⅴ
金属有机化合物化学气相沉(MOCVD)
• MOCVD是利用金属有机化合物热分解反应进行 气相外延生长的方法,即把含有外延材料组分的 金属有机化合物和氢化物(或其他反应气体)作 为原料气体输运到反应室,在一定的温度下进行 外延生长形成薄膜。 • 金属有机化合物可在较低温度下热解或光解,沉 积出金属、氧化物、氮化物、硫化物等,特别是 化合物半导体无机膜(包括单晶体外延膜、多晶 膜和非晶膜)。
初始气源 CVD装置基本组成
加热反应室
废气处理系统
二、CVD的特点
CVD过程可在高温或中温下进行 CVD过程可在大气压或低于大气压(低压)下进行
镀层的密度和纯度可控制,镀层的化学成分可改变
绕镀性好,适用于在复杂形状零件上沉积薄膜 可形成多种金属、合金、陶瓷和化合物镀层
三、化学气相沉积方法
热化学气相沉积(TCVD) 低压化学气相沉积(LPCVD) 等离子体化学气相沉积(PCVD) 激光(诱导)化学气相沉积(LCVD) 金属有机化合物化学气相沉积(MOCVD)
Ⅳ
激光(诱导)化学气相沉(LCVD)
LCVD是指利用激光束的光子能量激发和促进化 学反应,实现薄膜沉积的化学气相沉积技术。 按激光作用机制,可分为激光热解沉积和激光光 解沉积两种。 热解机制:光子加热使在衬底上的气体热 解发生沉积 光解机制:靠光子能量直接使气体分解 (单光 子吸收)
要求衬底对激光 吸收系数较高
SiO2 +2H2 SiO2 + 2Cl2
Al2O3 + 6HCl
3)氧化
SiH4 + O2 SiCH2O
4)水解
5)综合 许多镀层的沉积包含上述两种或几种基本反应。 此外,还有等离子体激发、光和激光激发等反应。
4、CVD装置
CVD设备
混合气体中某些成分分解后可以 单独沉积在基体表面形成薄膜, 或混合气体中某些成分分解后与基体 表面相互作用形成化合物, 沉积在基体表面形成薄膜
1、CVD的基本条件
1)足够高的温度:气体与机体表面作用、反应沉积时 需要一定的激活能量,故CVD要在高温下进行。当然, 以等离子体、激光提过激活能量,可降低反应的温度。 2)反应物必须有足够高的蒸气压。 3)除了要得到的固态沉积物外,化学反应的生成物都 必须是气态。 4)沉积物本身的饱和蒸气压应足够低。